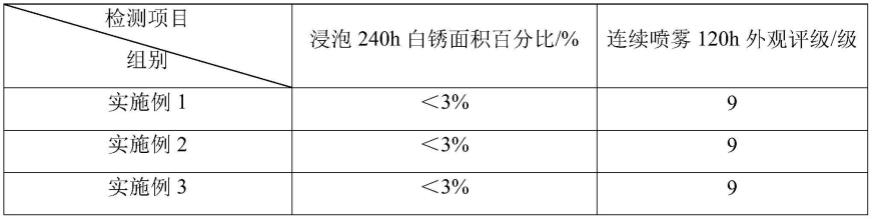
1.本技术涉及热浸镀锌技术域,更具体地说,它涉及一种金属镀件的热浸镀锌工艺。
背景技术:
2.钢铁制件表面进行热浸镀锌(简称热浸锌)处理是控制钢铁制件环境腐蚀的一种最为普遍、有效的表面防护技术。在一般的大气环境下,采用热浸镀锌所获得的热浸锌涂层可以持续几年或10多年时间保护钢铁制件不生锈。
3.然而,钢铁制件在运输和储存过程中,长期暴露于工业大气和海洋性气候的氛围之下。因此,即使钢铁制件表面进行热浸镀锌,当钢铁制件在运输和储存过程中时间较长时,钢铁制件表面还是容易发生微电池形成氢氧化锌,从而会出现白锈斑点。
技术实现要素:
4.为了改善钢铁制件在长时间运输和储存时出现白锈斑点的问题,提高钢铁制件的耐腐蚀性,本技术提供一种金属镀件的热浸镀锌工艺。
5.一种金属镀件的热浸镀锌工艺,包括如下步骤:s1:将镀件进行碱洗、酸洗和水洗后,得到清洗后的镀件;s2:将s1清洗后的镀件浸渍在助镀液中进行助镀处理后,干燥,然后再浸渍在镀锌液中进行热浸镀锌处理,得到热浸镀后的镀件;其中,镀锌液由如下重量百分比的组分组成:铝0.1-0.5%、镁0.3-0.5%、铟0.002-0.01%、镧0.1-0.3%、硅0.02-0.1%,余量为锌;s3:将s2所得热浸镀后的镀件进行冷却后,将钝化液喷射到镀件表面进行钝化处理,镀件固化后,得到钝化后的镀件;其中,钝化液由单宁酸、有机硅改性环氧树脂、磷酸和乙醇混合组成。
6.通过采用上述技术方案,由于预先将镀件进行碱洗、酸洗和水洗,除去镀件表面的铁粉、乳化液和其他污染物。因此,提高了镀件表面质量和附着力。随后,将清洗后的镀件进行助镀处理和热浸镀锌处理后,再进行钝化处理。一方面,由于采用特定合金组成的镀液。因此,镀液在清洗后的镀件表面形成的镀层分布致密、均匀,且附着力较高。另一方面,由于采用单宁酸、有机硅改性环氧树脂、磷酸和乙醇组成的钝化液,可与特定镀液形成的镀层表面发生键合作用,生成si-o-zn键,因此可紧密地覆盖在镀层表面,钝化成一定厚度的膜,进一步保护镀件,减少镀件发生腐蚀而产生白锈。
7.优选的,所述钝化液由单宁酸、有机硅改性环氧树脂、磷酸和乙醇按重量比1:(1.7-1.9):(0.06-0.09):(2.7-2.9)混合组成。
8.通过采用上述技术方案,单宁酸、有机硅改性环氧树脂、磷酸和乙醇按上述配比进行复配,一方面,有机硅改性环氧树脂作为成膜物质,与镀层表面发生键合,生成si-o-zn键,提高钝化膜与镀层的附着力,提高镀件的耐腐蚀能力。另一方面,当镀层表面产生铁锈时,钝化膜中的磷酸可与铁锈生成铁离子,单宁酸可与铁离子形成稳定性好的螯合物,附着
在镀件表面,抑制镀件的腐蚀。同时,当钝化膜中磷酸含量降低时,磷酸根离子浓度会增大并自行发生磷化成膜反应,从而在镀件表面生成磷化膜,增强了镀件的耐腐蚀性。
9.优选的,所述有机硅改性环氧树脂,采用gb1723检测的,涂-4杯,25℃的粘度是15-40s;采用盐酸-丙酮法检测的环氧值是0.02-0.08;采用gb1725检测的150℃,2h固含量是49-51%。
10.通过采用上述技术方案,由于有机硅改性环氧树脂的粘度及其他物理性能符合上述条件,所得镀件具有更好的耐腐蚀性能。经检测,浸泡820h白锈面积百分比均<2%,浸泡900h白锈面积百分比均<3%,连续喷雾340h和370h的外观评级等级高达9级。
11.优选的,所述s3中,镀件固化的温度为80-110℃,固化时间为3-5min。
12.通过采用上述技术方案,镀件在上述条件下进行固化,所得钝化膜表面致密光滑,且与镀件表面键合的能力较强,对镀件具有较好的保护效果。
13.优选的,所述s1的酸洗中,采用浓度为60-150g/l的盐酸水溶液清洗30-100min后,再进行水洗。
14.通过采用上述技术方案,由于控制镀件酸洗所采用的盐酸水溶液的浓度,以及盐酸水溶液清洗的时间,可除去基镀件表面残留的氧化皮、锈斑等其他污染物,所得镀件表面呈灰白色,光滑且均匀,有利于提高镀件后续的热浸镀锌处理和钝化处理过程中,所形成镀层与镀层的附着力。
15.优选的,所述s2助镀处理中,助镀液的温度为50-80℃,助镀处理时间为1-2min,助镀液的ph值为4-6,助镀液由氯化铵280-380g/l和氯化锌280-380g/l混合组成。
16.通过采用上述技术方案,助镀处理可以使镀件在热浸镀锌处理前具有一定的活性,增强镀层与镀件的结合,提高镀锌质量。
17.优选的,所述s2热浸镀锌处理中,镀锌液的温度为434-450℃,镀件热浸镀锌处理的时间为3-6min。
18.通过采用上述技术方案,由于控制镀件在镀锌液中的时间,可减少镀件表面的镀层出现收缩起皮,脱落等情况发生,有利于提高镀液在清洗后的镀件表面形成的镀层的致密性和均匀性。
19.虽然镀锌液中,铝、镁、铟、镧和硅的熔点较高,但是其含量较低,少于2%,所以在434-450℃的温度下依然能够形成镀液,上述镀液温度为最优温度。
20.优选的,所述s3将s2所得热浸镀后的镀件行冷却中,先将s2所得热浸镀后的镀件冷却至130-180℃,再采用蒸汽吹s2所得热浸镀后的镀件,然后再冷却至20-25℃;其中,蒸汽压力为0.5-0.7mpa,蒸汽温度为130-140℃,时间为10-20s。
21.通过采用上述技术方案,由于将s2所得热浸镀后的镀件行冷却至130-180℃,然后在上述温度和压力下,将镀件表面多余的锌粉吹落,可提高镀件表面镀层的平整性,有利于后续对镀件的钝化处理,进一步提高镀件的耐腐蚀性。
22.综上所述,本技术具有以下有益效果:本技术的方法,通过预先将镀件进行碱洗、酸洗和水洗,除去镀件表面的铁粉、乳化液和其他污染物;然后,采用特定合金组成的镀锌液对镀件进行热浸镀锌形成镀层,并结合由单宁酸、有机硅改性环氧树脂、磷酸和乙醇混合组成的钝化液进行钝化成钝化膜;钝化膜与镀层表面发生键合作用,生成si-o-zn键,因此钝化膜可紧密地覆盖在镀层表面,减少
镀件发生腐蚀而产生白锈。
具体实施方式
23.以下结合实施例对本技术作进一步详细说明。
24.本技术中所采用的原料,除以下特殊说明外,其他均为市售。
25.脱脂剂,型号为t-109,采购自浙江万众新材料有限公司。
26.对实施例和对比例所得镀件进行中性盐雾腐蚀试验和外观评级检测,试验标准如下:中性盐雾腐蚀试验:参照gb/t 10125-1997,将镀件浸泡在氯化钠溶液中,观察一定时间后镀件出现“白锈”的面积,并用划格法计算“白锈”面积百分比。
27.外观评级检测:参照gb/t 10125-1997,采用连续喷雾测试一定时间,观察出现“白锈”的面积,并参照gb/t 6461-2002中的表1,对试验后的镀件进行等级评级。评级由优至劣的评级依次为10-0。实施例
28.实施例1一种金属镀件的热浸镀锌工艺,包括如下步骤:s1:将镀件在温度为68℃、浓度为50g/l的脱脂剂的水溶液中,浸泡50min后,用水进行漂洗10min,然后再采用浓度为60g/l的盐酸水溶液清洗105min后,用水进行漂洗10min,得到清洗后的镀件;s2:将s1清洗后的镀件浸渍在助镀液中进行助镀处理后,干燥,然后再浸渍在镀锌液中进行热浸镀锌处理,得到热浸镀后的镀件;其中,助镀液的温度为50℃,助镀处理时间为1min,助镀液的ph值为4,助镀液由氯化铵270g/l和氯化锌280g/l混合组成;干燥条件为:在110-120℃水蒸汽中干燥50-80s;镀锌液液重量百分比的组成为:铝0.1%、镁0.3%、铟0.002%、镧0.1%、硅0.02%,余量为锌;镀锌液的温度为420℃,镀件热浸镀锌处理的时间为7min。
29.s3:将s2所得热浸镀后的镀件行冷却后,将钝化液喷射到镀件表面进行钝化处理,然后在115℃进行固化3min,得到钝化后的镀件;其中,s2所得热浸镀后的镀件行冷却过程中,先将s2所得热浸镀后的镀件冷却至110℃,再采用水蒸汽吹s2所得热浸镀后的镀件,然后再冷却至20-25℃;其中,水蒸汽压力为0.5mpa,蒸汽温度为130℃,时间为10s;钝化液由1.87kg单宁酸、2.99kg有机硅改性环氧树脂、0.09kg磷酸和5.05kg乙醇混合组成。
30.有机硅改性环氧树脂,采用gb1723检测的,涂-4杯,25℃的粘度是50-60s;采用盐酸-丙酮法检测的环氧值是0.02-0.08;采用gb1725检测的150℃,2h固含量是49-51%。
31.实施例2一种金属镀件的热浸镀锌工艺,与实施例1的不同之处在于,镀锌液由如下重量百分比的组分组成:铝0.3%、镁0.4%、铟0.007%、镧0.2%、硅0.07%,余量为锌。
32.实施例3
一种金属镀件的热浸镀锌工艺,与实施例1的不同之处在于,镀锌液由如下重量百分比的组分组成:铝0.5%、镁0.5%、铟0.01%、镧0.3%、硅0.1%,余量为锌。
33.对上述实施例1-3所得镀件进行中性盐雾腐蚀试验和外观评级检测,检测结果和等级评级如下表所示。
34.通过对上表进行数据分析可知,实施例1-3所得的镀件,浸泡240h白锈面积百分比均<3%,连续喷雾120h外观评级等级高达9级。由此表明,本技术实施例1-3采用金属镀件的热浸镀锌工艺所得的镀件,具有良好的耐腐蚀性。
35.实施例4-7一种金属镀件的热浸镀锌工艺,与实施例2的不同之处在于,s3中,钝化液中单宁酸、有机硅改性环氧树脂、磷酸和乙醇的重量比不同。
36.单宁酸、有机硅改性环氧树脂、磷酸和磷酸的重量如下表所示。
37.对上述实施例4-7所得镀件进行中性盐雾腐蚀试验和外观评级检测,检测结果和等级评级如下表所示。
38.通过对上表进行数据分析可知,实施例4-6所得的镀件,浸泡240h白锈面积百分比
均<2%,浸泡260h白锈面积百分比均<3%,连续喷雾120h外观评级等级高达10级,连续喷雾140h外观评级等级高达9级。
39.实施例7所得的镀件,浸泡240h白锈面积百分比均<3%,浸泡260h白锈面积百分比均<5%,连续喷雾120h外观评级等级高达9级,连续喷雾140h外观评级等级高达8级。
40.依据实施例4-6与实施例2、7进行对比可知,实施例4-6所得的镀件,浸泡240h和120h白锈面积百分比均明显小于实施例2、7浸泡240h和120h白锈面积百分比;同时,实施例4-6所得的镀件,连续喷雾120h和140h的外观评级等级均明显高于实施例2、7连续喷雾120h和140h的外观评级等级。由此表明,在本技术金属镀件的热浸镀锌工艺中,采用钝化液由单宁酸、有机硅改性环氧树脂、磷酸和乙醇按重量比1:(1.7-1.9):(0.06-0.09):(2.7-2.9)混合组成,可提高所得的镀件的耐腐蚀性。
41.实施例8一种金属镀件的热浸镀锌工艺,与实施例5的不同之处在于,有机硅改性环氧树脂,采用gb1723检测的,涂-4杯,25℃的粘度是15-40s;采用盐酸-丙酮法检测的环氧值是0.02-0.08;采用gb1725检测的150℃,2h固含量是49-51%。
42.对上述实施例8所得镀件进行中性盐雾腐蚀试验和外观评级检测,检测结果和等级评级如下表所示。
43.通过对上表进行数据分析可知,实施例8所得的镀件,浸泡260h白锈面积百分比均<2%,浸泡280h白锈面积百分比均<3%,连续喷雾140h和160h的外观评级等级高达9级。
44.依据实施例8与实施例5进行对比可知,实施例8所得的镀件,浸泡260h和280h白锈面积百分比均明显小于实施例5浸泡260h和280h白锈面积百分比;同时,实施例8所得的镀件,连续喷雾160h的外观评级等级均明显高于实施例5连续喷雾160h的外观评级等级。由此表明,在本技术金属镀件的热浸镀锌工艺中,钝化液中的有机硅改性环氧树脂,采用gb1723检测的,涂-4杯,25℃的粘度是15-40s;采用盐酸-丙酮法检测的环氧值是0.02-0.08;采用gb1725检测的150℃,2h固含量是49-51%,可提高所得的镀件的耐腐蚀性。
45.实施例9一种金属镀件的热浸镀锌工艺,与实施例8的不同之处在于,s3中,将钝化液喷射到镀件表面进行钝化处理,然后在80℃进行固化,固化时间为5min。
46.实施例10一种金属镀件的热浸镀锌工艺,与实施例8的不同之处在于,s3中,将钝化液喷射到镀件表面进行钝化处理,然后在105℃进行固化,固化时间为4min。
47.实施例11一种金属镀件的热浸镀锌工艺,与实施例8的不同之处在于,s3中,将钝化液喷射到镀件表面进行钝化处理,然后在110℃进行固化,固化时间为3min。
48.对上述实施例9-11所得镀件进行中性盐雾腐蚀试验和外观评级检测,检测结果和等级评级如下表所示。
49.通过对上表进行数据分析可知,实施例9-11所得的镀件,浸泡280h白锈面积百分比均<2%,浸泡290h白锈面积百分比均<(5-6)%,连续喷雾160h和170h的外观评级等级高达9级。
50.依据实施例9-11与实施例8进行对比可知,实施例9-11所得的镀件,浸泡280h和290h的白锈面积百分比均明显小于实施例8浸泡280h和290h白锈面积百分比;同时,实施例9-11所得的镀件,连续喷雾170h的外观评级等级均明显高于实施例8连续喷雾170h的外观评级等级。由此表明,在本技术金属镀件的热浸镀锌工艺中,镀件钝化处理后,固化的温度为80-110℃,固化时间为3-5min,所得钝化膜表面致密光滑,且与镀件表面键合的能力较强,因此提高了所得的镀件的耐腐蚀性。
51.实施例9-11中,实施例9所得镀件浸泡290h白锈面积百分比低至5%,因此实施例9所得镀件的耐腐蚀性能较好。
52.实施例12一种金属镀件的热浸镀锌工艺,与实施例9的不同之处在于,s1的酸洗中,采用浓度为150g/l的盐酸水溶液清洗30min后,再进行水洗。
53.实施例13一种金属镀件的热浸镀锌工艺,与实施例9的不同之处在于,s1的酸洗中,采用浓度为105g/l的盐酸水溶液清洗65min后,再进行水洗。
54.实施例14一种金属镀件的热浸镀锌工艺,与实施例9的不同之处在于,s1的酸洗中,采用浓度为60g/l的盐酸水溶液清洗100min后,再进行水洗。
55.对上述实施例12-14所得镀件进行中性盐雾腐蚀试验和外观评级检测,检测结果和等级评级如下表所示。
56.通过对上表进行数据分析可知,实施例12-14所得的镀件,浸泡浸泡300h白锈面积百分比均<4%,连续喷雾170h和180h的外观评级等级高达9级。
57.依据实施例12-14与实施例9进行对比可知,实施例12-14所得的镀件,浸泡300h的白锈面积百分比均明显小于实施例10浸泡300h的白锈面积百分比。由此表明,在本技术金属镀件的热浸镀锌工艺中,镀件酸洗中,采用浓度为60-150g/l的盐酸水溶液清洗30-100min后,再进行水洗,可除去基镀件表面残留的氧化皮、锈斑等其他污染物,有利于提高镀件后续的热浸镀锌处理和钝化处理过程中,所形成镀层与镀层的附着力,因此提高了所得的镀件的耐腐蚀性。
58.实施例15一种金属镀件的热浸镀锌工艺,与实施例12的不同之处在于,s2热浸镀锌处理中,镀锌液的温度为434℃,镀件热浸镀锌处理的时间为6min。
59.实施例16一种金属镀件的热浸镀锌工艺,与实施例12的不同之处在于,s2热浸镀锌处理中,镀锌液的温度为442℃,镀件热浸镀锌处理的时间为4.5min。
60.实施例17一种金属镀件的热浸镀锌工艺,与实施例12的不同之处在于,s2热浸镀锌处理中,镀锌液的温度为450℃,镀件热浸镀锌处理的走速为3min。
61.对上述实施例15-17所得镀件进行中性盐雾腐蚀试验和外观评级检测,检测结果和等级评级如下表所示。
62.通过对上表进行数据分析可知,实施例15-17所得的镀件,浸泡300h白锈面积百分比均<3%,浸泡310h白锈面积百分比均<4%,连续喷雾180h和190h的外观评级等级高达9级。
63.依据实施例15-17与实施例12进行对比可知,实施例15-17所得的镀件,浸泡300h和340h的白锈面积百分比均明显小于实施例12浸泡300h和340h的白锈面积百分比;同时,实施例15-17所得的镀件,连续喷雾190h的外观评级等级均明显高于实施例12连续喷雾190h的外观评级等级。由此表明,在本技术金属镀件的热浸镀锌工艺中,镀锌液的温度为434-450℃,镀件热浸镀锌处理的时间为3-6min,提高了镀液在清洗后的镀件表面形成的镀层的致密性和均匀性,从而提高了所得的镀件的耐腐蚀性。
64.实施例18一种金属镀件的热浸镀锌工艺,与实施例16的不同之处在于,s2助镀处理中,助镀液的温度为50℃,助镀处理时间为1min,助镀液的ph值为4,助镀液由氯化铵280g/l和氯化锌280g/l混合组成。
65.实施例19一种金属镀件的热浸镀锌工艺,与实施例16的不同之处在于,s2助镀处理中,助镀液的温度为65℃,助镀处理时间为1.5min,助镀液的ph值为5,助镀液由氯化铵330g/l和氯化锌330g/l混合组成。
66.实施例20一种金属镀件的热浸镀锌工艺,与实施例16的不同之处在于,s2助镀处理中,助镀液的温度为80℃,助镀处理时间为1min,助镀液的ph值为4,助镀液由氯化铵280g/l和氯化锌280g/l混合组成。
67.对上述实施例18-20所得镀件进行中性盐雾腐蚀试验和外观评级检测,检测结果和等级评级如下表所示。
68.实施例21一种金属镀件的热浸镀锌工艺,与实施例19的不同之处在于,s3将s2所得热浸镀后的镀件行冷却中,先将s2所得热浸镀后的镀件冷却至130℃,再采用水蒸汽吹s2所得热浸镀后的镀件,然后再冷却至20-25℃;其中,蒸汽压力为0.5mpa,水蒸汽温度为130℃,时间为10-20s。
69.实施例22一种金属镀件的热浸镀锌工艺,与实施例19的不同之处在于,s3将s2所得热浸镀后的镀件行冷却中,先将s2所得热浸镀后的镀件冷却至155℃,再采用水蒸汽吹s2所得热浸镀后的镀件,然后再冷却至20-25℃;其中,水蒸汽压力为0.6mpa,水蒸汽温度为135℃,时间为10-20s。
70.实施例23一种金属镀件的热浸镀锌工艺,与实施例19的不同之处在于,s3将s2所得热浸镀后的镀件行冷却中,先将s2所得热浸镀后的镀件冷却至180℃,再采用水蒸汽吹s2所得热浸镀后的镀件,然后再冷却至20-25℃;其中,水蒸汽压力为0.7mpa,水蒸汽温度为140℃,时间为10-20s。
71.对上述实施例21-23所得镀件进行中性盐雾腐蚀试验和外观评级检测,检测结果和等级评级如下表所示。和等级评级如下表所示。
72.通过对上表进行数据分析可知,实施例21-23所得的镀件,浸泡320h和330h的白锈面积百分比均<2%,连续喷雾200h和210h的外观评级等级高达9级。
73.依据实施例21-23与实施例19进行对比可知,实施例21-23所得的镀件,浸泡320h和330h的白锈面积百分比均明显小于实施例19浸泡320h和330h的白锈面积百分比。由此表明,在本技术金属镀件的热浸镀锌工艺中,在一定水蒸汽压力下,采用温度相近的水蒸汽将镀件表面多余的锌粉吹落,可提高镀件表面镀层的平整性,有利于后续对镀件的钝化处理,因此提高了镀件的耐腐蚀性。
74.对比例对比例1一种金属镀件的热浸镀锌工艺,与实施例22的不同之处在于,步骤s3的钝化液中,采用环氧树脂等量替换有机硅改性环氧树脂,其中,环氧树脂牌号为cesp2015,采购自广州臻析检测技术有限公司。
75.对比例2一种金属镀件的热浸镀锌工艺,与实施例22的不同之处在于,步骤s3的钝化液中,采用等量的柠檬酸替换磷酸。
76.对比例3一种金属镀件的热浸镀锌工艺,与实施例22的不同之处在于,步骤s3的钝化液中,采用等量的有机硅改性环氧树脂替换单宁酸。
77.对比例4一种金属镀件的热浸镀锌工艺,与实施例22的不同之处在于,镀液重量百分比的组成为:铝0.1%、镁0.6%、铟0.002-0.01%、镧0.1-0.3%、硅0.02-0.1%,余量为锌。
78.对比例5一种金属镀件的热浸镀锌工艺,与实施例22的不同之处在于,步骤s2中,镀液重量
百分比的组成为:铝0.6%、镁0.1%、铟0.002-0.01%、镧0.1-0.3%、硅0.02-0.1%,余量为锌。
79.对上述对比例1-5所得镀件进行中性盐雾腐蚀试验和外观评级检测,检测结果和等级评级如下表所示。等级评级如下表所示。
80.通过对上表进行数据分析可知,对比例1-3所得的镀件,浸泡240h白锈面积百分比均<22%,浸泡330h白锈面积百分比均<39%,连续喷雾120h的外观评级等级低至2级,连续喷雾210h的外观评级等级低至1级。
81.依据实施例22与对比例1-3进行对比可知,实施例22所得的镀件,浸泡240h的白锈面积百分比至少相对降低99.09%,浸泡330h的白锈面积百分比至少相对降低94.87%;连续喷雾120h的外观评级等级相对降低400%,连续喷雾210h的外观评级等级相对降低800%。
82.依据实施例22与对比例4-5进行对比可知,实施例22所得的镀件,浸泡240h的白锈面积百分比至少相对降低99.17%,浸泡330h的白锈面积百分比相对降低95.12%;连续喷雾120h的外观评级等级相对降低400%,连续喷雾210h的外观评级等级相对降低800%。
83.由此表明,在本技术金属镀件的热浸镀锌工艺中,钝化液由单宁酸、有机硅改性环氧树脂、磷酸和乙醇混合组成时,可与特定镀锌液形成的镀层表面发生键合作用,生成si-o-zn键,因此提高了所得的镀件的耐腐蚀性。
84.本具体实施例仅仅是对本技术的解释,其并不是对本技术的限制,本领域技术人员在阅读完本说明书后可以根据需要对本实施例做出没有创造性贡献的修改,但只要在本技术的权利要求范围内都受到专利法的保护。
再多了解一些
本文用于企业家、创业者技术爱好者查询,结果仅供参考。