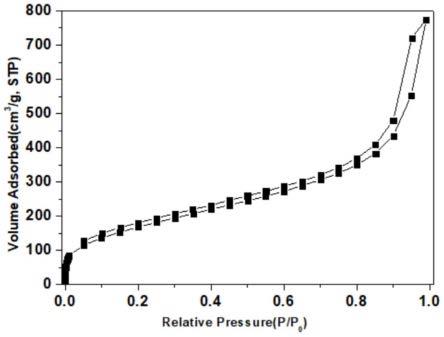
1.本发明属于多相催化领域,具体涉及一种采用蛋壳型催化剂进行丙烯氢甲酰化反应的方法。
背景技术:
2.烯烃氢甲酰化反应是烯烃与合成气(co h2)在过渡金属络合物催化剂的作用下在烯烃双键上同时加上氢原子和甲酰基生成比原来烯烃多一个碳原子的醛的反应过程。该反应是典型的原子经济反应,对反应原料的利用率达到100%(chem.rev.,2012,112(11):5675-5732.)。在所有烯烃的氢甲酰化反应中,丙烯氢甲酰化是最重要的。丙烯氢甲酰化的产品丁醛占全世界所有醛消耗量的50%以上(1500万吨/年的需求量),丙烯氢甲酰化的产品有正丁醛和异丁醛两种,都是用量较大的重要化学品(式1)。
[0003][0004]
式1.丙烯氢甲酰化反应合成正丁醛和异丁醛的路线
[0005]
丙烯氢甲酰化反应的其中一个产品异丁醛加氢可制备异丁醇;异丁醛与甲醛和三乙胺催化加氢缩合可制得重要化工原料新戊二醇;还可用于制备甲基丙烯酸甲酯(mma)及可降解塑料聚酯共单体2,2,4,4-四甲基-1,3-环丁二醇(式2,cbdo)等(石化技术与应用,2013,31(4):342-346)。
[0006][0007]
式2.异丁醛制备可降解塑料聚酯共单体cbdo路线
[0008]
丙烯氢甲酰化的工业生产目前采用的主要是均相催化工艺,在工业丙烯氢甲酰化反应的发展历史中,一共经历了五代催化剂的变革,分别为羰基co催化剂、叔膦配体改性的羰基co催化剂、羰基rh催化剂、油溶性rh-p 络合物催化剂、水溶性的rh-p络合物催化剂。除了wilkinson开发的经典的 hrhco(pph3)3油溶性均相催化剂(第四代催化剂)之外,丙烯的氢甲酰化主要采用的是1984年ruhrchemie和rhone-poulence公司开发的rch/rp水油两相工艺(第五代催化工艺)。第五代催化工艺,使用rh-tppts催化剂,主要的代表公司为basf,dow化学等(adv catal,2002,47:1-64)。两相催化工艺体系虽然用较简单的方法实现了催化剂的回收使用,但是丙烯的水溶性问题也使得应用两相技术的丙烯氢甲酰化反应被动力学控制,同时两相催化技术使得操作工艺变得较为繁琐。在实际的工业生产中,由于要维持铑膦络合物的稳定性,工业操作中配体通常是过量加入的,这样就导致丁醛产品中正构醛和异构醛的调节比例范围很窄(正异比调节范围局限在 9~15左右),产品醛中正丁醛的选择性在90%以上,限制了企业生产的机动化和利润最大化。另外工业上目前使用的均相和两相工艺都面临着贵金属 rh流失的问题,需要不断地补充新鲜催化剂以维持装置的平稳运行,增加了额外的生产成本(appl catal a:gen,2001,221(1):219-225.)。在实现丙烯氢
甲酰化均相催化剂多相化的同时,提升产品醛中的异丁醛的选择性一直是很有挑战性的工作。
技术实现要素:
[0009]
为了解决上述问题,本发明的目的在于提供一种采用蛋壳型催化剂进行丙烯氢甲酰化反应的方法,实现绿色无溶剂的丙烯氢甲酰化制备丁醛的过程,提升产品丁醛中异丁醛的比例。
[0010]
本发明的技术方案为:
[0011]
一种采用蛋壳型催化剂进行丙烯氢甲酰化反应的方法,将蛋壳型催化剂装入反应器,通入丙烯及合成气进行丙烯氢甲酰化反应;
[0012]
所述的蛋壳型催化剂以具有载体和配体双重功能的膦配体聚合物小球作为载体,以金属rh、co、ir、ru、pt、pd和fe中的一种、两种或三种以上作为活性组分;
[0013]
膦配体聚合物小球由含有烯烃基的单膦配体、含有烯烃基的二级氧化膦配体中的一种自聚或者中的两种以上共聚而成;膦配体聚合物小球的粒径范围为1-8mm(优选为1-5mm),活性组分均匀配位于聚合物小球的表面层形成催化剂蛋壳层,含有金属活性组分的载体表面层称之为蛋壳层,催化剂蛋壳层厚度(金属活性由载体表面配位至载体内的的深度)为 0.01-0.1mm(优选为0.01-0.05mm)。
[0014]
2、按照权利要求1所述的采用蛋壳型催化剂进行丙烯氢甲酰化反应的方法,其特征在于:反应过程为将蛋壳型装入反应器中,通入原料丙烯及合成气进行氢甲酰化反应,所述的反应器为径向反应器、列管式反应器,浆态床、滴流床或釜式反应器,优选为列管式反应器。
[0015]
合成气的主要组分为h2和co,h2 co的体积含量为10~100%(优选为 80~100%),h2/co体积比为0.1~10.0(优选为0.8~1.2),其余气体组分为 co2、n2、he和ar气中的一种或两种以上;原料丙烯纯度为5~100%(优选为80~100%),其余气体组分为co2、n2、he和ar气中的一种或两种以上;反应温度313~453k(优选为343~403k),反应压力0.1~6.0mpa(优选 0.5~3.0mpa),合成气气体空速100~10000h-1
(优选500~5000h-1
),丙烯空速0.01~40.0h-1
(优选为0.1~10.0)。
[0016]
蛋壳型催化剂的制备方法为:将rh、co、ir、ru、pt、pd和fe中的一种或二种以上的活性金属前驱体配成浸渍液,采用等体积浸渍的方法使得活性金属与膦配体聚合物小球表面层的膦配体配位,即可得到蛋壳型催化剂;所述的蛋壳型催化剂中金属担载量范围为0.01-15wt%,优选范围为 0.1-3wt%。
[0017]
蛋壳型催化剂的膦配体聚合物小球聚合用到的含有烯烃基的单齿膦配体、二级氧化膦配体的烯烃基优选为乙烯基官能团;
[0018]
所述含有烯烃基的单齿膦配体、含有烯烃基的二级氧化膦配体为下述中的一种或二种以上:
[0019]
[0020]
[0021][0022]
l1-l18为含有烯烃基的单膦配体,l19-l42为含有烯烃基的二级氧化膦配体。
[0023]
所述的膦配体聚合物小球孔容为0.1-5.0cm3/g,优选为0.1-1.5cm3/g,孔径分布在
0.01-100.0nm,优选为0.1-5.0nm,比表面积为10-1000m2/g,优选范围为20-650m2/g。
[0024]
膦配体聚合物小球的制备过程为:
[0025]
将含有烯烃基的单齿膦配体、二级氧化膦配体中的一种或二种以上充分溶解后,添加或不添加交联剂,采用乳液聚合或悬浮聚合的方法,经自由基引发剂引发有机膦配体中的烯烃基发生聚合反应,生成具有多级孔结构膦配体聚合物小球;
[0026]
蛋壳型催化剂制备过程为:
[0027]
将活性金属前驱体配成浸渍液,采用等体积浸渍的方法使得活性金属与氧化膦聚合物小球表面层的膦配体配位,除去溶剂,即可得到蛋壳型催化剂。蛋壳型催化剂的具体制备步骤为:
[0028]
a)惰性气体气氛273-393k(优选为273-353k)下,在有机溶剂中加入烯烃基的单齿膦配体和/或烯烃基的二级氧化膦配体中的一种或二种以上,添加或不添加交联剂,再加入悬浮乳化剂,搅拌均匀,配成均一待聚合油相;
[0029]
b)惰性气体气氛273-393k(优选为273-353k)下,搅拌状态下将上述油相分散到水相中,再加入自由基引发剂,采用自由基聚合的方法将膦配体聚合成聚合物小球;
[0030]
c)过滤出步骤b)中的固体颗粒物,固体颗粒物体积10-1000(优选为20-500) 倍的溶剂清洗,后在273-423k(优选为273-403k)下真空抽除溶剂,即得到膦配体聚合物小球,即用于丙烯氢甲酰化反应的蛋壳型催化剂的载体;
[0031]
d)惰性气体气氛298-403k(优选为298-373k)下,采用等体积浸渍的方法,将含有活性金属组分前驱体的溶液,浸渍入膦配体聚合物小球中,后在 298-453k(优选为298-403k)保温0.1-20小时,273-453k(优选为273-403k) 下真空去除溶剂,得到丙烯氢甲酰化反应的蛋壳型催化剂;活性金属在前驱体溶液中的浓度范围为0.001-10mol l-1
(优选为0.001-1mol l-1
)。
[0032]
步骤a)中的有机溶剂为苯、甲苯、二甲苯、联苯、多氯联苯、环己烷、正辛烷和十二烷中一种或两种以上;
[0033]
步骤a)中的交联剂为下述中中的一种或两种以上:
[0034][0035]
步骤b)中所述的悬浮乳化剂选为聚乙烯醇、聚乙烯吡咯烷酮、对辛基苯酚聚氧乙烯醚、n-十二烷基二甲胺、硬脂酸钠盐和十二烷基苯磺酸钙中的一种或两种以上;所述的自由基引发剂为过氧化环己酮、过氧化二苯甲酰、叔丁基过氧化氢或偶氮二异丁腈中的一种或两种以上;自由基聚合时油相和水相的体积比为10000:1-1:10000(优选为1000:1-1:1000);
[0036]
步骤c)中所述的用于清洗聚合物小球的溶剂为苯、甲苯、二甲苯、甲醇、乙醇、二氯
甲烷、三氯甲烷、水、或四氢呋喃中一种或两种以上;
[0037]
步骤a)中,聚合成有机聚合物小球前,含有烯烃基的单膦配体或二级氧化膦配体在溶剂中的浓度范围为0.01-1000g/l,优选为0.1-100g/l,单膦配体与二级氧化膦配体同时添加时,含有烃基的单齿膦配体和二级氧化膦配体的摩尔比为0.0001:1-10000:1(优选为0.001:1-1000:1),
[0038]
在交联剂添加的情况下,烯烃基单齿膦配体和/或含有烯烃基的二级氧化膦配体原料与交联剂的摩尔比为0.001:1~1000:1(优选为0.01:1~100:1),含有烯烃基的单齿膦配体和/或含有烯烃基的二级氧化膦配体原料与自由基引发剂的摩尔比为500:1-10:1,优选为100:1-10:1;
[0039]
步骤a)、b)和d)中所述惰性气体选自ar、he、n2和co2中的一种或两种以上。
[0040]
所述的活性组分为rh、co、ir、ru、pt、pd或fe中的一种或两种以上,其中rh的前驱体为rhh(co)(pph3)3、rh(co)2(acac)、rhcl3和rh(ch3coo)2中的一种或两种以上;co的前驱体为co(ch3coo)2、co(co)2(acac)、co (acac)2和cocl2中的一种或两种以上;ir的前驱体为ir(co)3(acac)、 ir(ch3coo)3、ir(acac)3和ircl4中的一种或两种以上;ru的前驱体为二氯(环辛基-1,5-二烯)钌(ii)、rucl3、ru(acac)3、十二羰基三钌、[ruar2(benzene)]2、 [ruar2(p-cymene)]2,[ruar2(mesitylene)]2、[(π-ally)ru(cod)]2和 [(π-ally)ru(nbd)]2;pt的前驱体为pt(acac)2、ptcl4和ptcl2(nh3)2中的一种或两种以上;pd的前驱体为pd(ch3coo)2、pd(acac)2、pdcl2、pd(pph3)4和 pdcl2(ch3cn)2中的一种或两种以上;fe的前驱体为fe(acac)3、fecl3、fecl2、 fes、二茂铁和九羰基二铁中的一种或两种以上,催化剂中金属担载量范围为0.01-15wt%,优选为0.1-3wt%。
[0041]
本发明的反应原理:
[0042]
本发明在蛋壳型催化剂制备时,通过控制聚合物小球的孔道结构,控制蛋壳型催化剂制备过程等手段,使得制备出的蛋壳型催化剂活性中心位于蛋壳型催化剂的表层,活性中心在催化剂中的特定分布使得制备出的蛋壳型催化剂应用于丙烯氢甲酰化反应时,催化剂活性高,产品醛中异丁醛选择性好,同时催化剂具有较好的稳定性,显现出良好的工业应用前景。
[0043]
本发明的有益效果为:
[0044]
目前工业上应用广泛的丙烯氢甲酰化催化工艺,面临着金属和配体流失的问题,本发明提供的一种采用蛋壳型催化剂进行丙烯氢甲酰化反应的方法,蛋壳型催化剂的载体是具有载体和配体双重功效的膦配体聚合物小球,聚合物小球中的膦配体与贵金属间存在着较强的配位作用力,从而解决了金属和配体流失的问题。同时,聚合物小球特定的孔道结构和金属在小球表层的蛋壳型分布状态,使得制备出的蛋壳型催化剂应用于丙烯氢甲酰化反应时,催化剂活性高,产品醛中异丁醛选择性好,可以达到50%以上,而目前工业上的丙烯氢甲酰化工艺,异丁醛的选择性只能做到10%以下。
附图说明
[0045]
图1是实施例1获得的膦配体聚合物小球的液氮温度下的n2物理吸附曲线。
[0046]
图2是实施例1获得的膦配体聚合物小球的孔径分布曲线。
[0047]
图3是膦配体聚合物小球制备时用到的交联剂结构式。
具体实施方式
[0048]
下述实施例对本发明进行更好的说明,但不限制本发明所要保护的范围。
[0049]
实施例1
[0050]
膦配体聚合物小球制备方法为:
[0051]
在10℃和惰性气体n2氛围保护下,称取10g二(4-乙烯基苯基)苯基膦(配体l1)、2g聚乙烯基吡咯烷酮(乳化剂)溶于100ml甲苯,搅拌均匀待用。30℃,n2保护下,将溶有膦配体的甲苯溶液搅拌状态(机械搅拌,搅拌速度100r/min)下加入40ml去离子水中,再加入0.3g过氧化苯甲酰(引发剂),后在75℃下继续搅拌(机械搅拌,搅拌速度100r/min)聚合18小时。
[0052]
降温至室温后,将颗粒物过滤后用500ml去离子水洗涤后在60℃下真空干燥5小时,得膦配体聚合物小球,小球直径范围为0.2mm-3.0mm,平均粒径1.2mm。图1为制备出的聚合物小球的n2物理吸附曲线,计算得知聚合物小球的比表面积为610m2/g,孔容为1.20cm3/g。图2是膦配体聚合物小球的孔径分布曲线,从图中可看出聚合物小球的孔主要分布在0.5-2nm 之间。
[0053]
蛋壳型催化剂制备方法为:
[0054]
筛分出1.0-1.4mm的聚合物小球,在50℃和惰性气体ar气保护氛围下,称取23.0毫克rhh(co)(pph3)3(cas号17185-29-4)溶于2.0ml正庚烷中,加入1.0克上述筛分出的膦配体聚合物小球载体,使浸渍液被膦配体聚合物小球全部吸入,后再60℃下保温10小时。
[0055]
降温至室温,20℃下真空除去溶剂,即获得应用于丙烯氢甲酰化反应的蛋壳型催化剂,经电镜观察剖面,活性组分rh均匀配位于聚合物小球的表面层,含有金属rh的催化剂层(壳层)厚度为0.01mm,蛋壳层rh分布均匀。实测催化剂金属负载量为0.25%。
[0056]
实施例2
[0057]
在实施例2中,除了用相同摩尔数二级氧化膦配体l19替代10g配体 l1外,其余膦配体小球及蛋壳型催化剂合成过程与实施例1相同。经电镜观察剖面,活性组分rh均匀配位于聚合物小球的表面层,含有金属rh的催化剂层(壳层)厚度为0.01mm,蛋壳层rh分布均匀。实测催化剂金属负载量为0.25%。
[0058]
实施例3
[0059]
在实施例3中,膦配体小球制备时,除了用150ml环己烷代替100ml 甲苯外,其余膦配体小球及蛋壳型催化剂合成过程与实施例1相同。经电镜观察剖面,活性组分rh均匀配位于聚合物小球的表面层,含有金属rh 的催化剂层(壳层)厚度为0.01mm,蛋壳层rh分布均匀。实测催化剂金属负载量为0.25%。
[0060]
实施例4
[0061]
在实施例4中,膦配体小球制备时,机械搅拌速度调整至30r/min,其余膦配体小球及蛋壳型催化剂合成过程与实施例1相同。经电镜观察剖面,活性组分rh均匀配位于聚合物小球的表面层,含有金属rh的催化剂层(壳层)厚度为0.01mm,蛋壳层rh分布均匀。实测催化剂金属负载量为0.25%。
[0062]
实施例5
[0063]
在实施例5中,膦配体小球制备时,除了再加入2.0g附图2中的col2 苯乙烯作为交联剂外,其余膦配体小球及蛋壳型催化剂合成过程与实施例1 相同,经电镜观察剖面,活性组分rh均匀配位于聚合物小球的表面层,含有金属rh的催化剂层(壳层)厚度为0.01mm,蛋
壳层rh分布均匀。实测催化剂金属负载量为0.25%。
[0064]
实施例6
[0065]
在实施例6中,膦配体小球制备时,除了用5g配体l13和5g配体l22 代替10g二(4-乙烯基苯基)苯基膦(配体l1)外,其余膦配体小球及蛋壳型催化剂合成过程与实施例1相同,经电镜观察剖面,活性组分rh均匀配位于聚合物小球的表面层,含有金属rh的催化剂层(壳层)厚度为 0.01mm,蛋壳层rh分布均匀。实测催化剂金属负载量为0.25%。
[0066]
实施例7
[0067]
在实施例7中,蛋壳型催化剂制备时的浸渍步骤,除了用2.0ml四氢呋喃代替2ml正庚烷外,其余膦配体小球及蛋壳型催化剂合成过程与实施例1相同。经电镜观察剖面,活性组分rh均匀配位于聚合物小球的表面层,含有金属rh的催化剂层(壳层)厚度为0.01mm,蛋壳层rh分布均匀。实测催化剂金属负载量为0.25%
[0068]
实施例8
[0069]
在实施例8中,除了用相同摩尔数rhcl3替代rhh(co)(pph3)3外,其余合成过程和条件与实施例1相同,经电镜观察剖面,活性组分rh均匀配位于聚合物小球的表面层,含有金属rh的催化剂层(壳层)厚度为0.01mm,蛋壳层rh分布均匀。实测催化剂金属负载量为0.25%
[0070]
实施例9
[0071]
在实施例9中,除了用相同摩尔数cocl2替代rhh(co)(pph3)3外,其余合成过程和条件与实施例1相同,可得co基蛋壳型催化剂,催化剂层(壳层)厚度为0.02mm。
[0072]
实施例10
[0073]
在实施例10中,除了用相同摩尔数ir(acac)3替代rhh(co)(pph3)3外,其余合成过程和条件与实施例1相同,可得高分散型ir基催化剂,催化剂层(壳层)厚度为0.015mm。
[0074]
实施例11
[0075]
在实施例11中,除了用相同摩尔数pdcl2(ch3cn)2替代rhh(co)(pph3)3外,其余合成过程和条件与实施例1相同,催化剂层(壳层)厚度为0.01mm。
[0076]
实施例12
[0077]
在实施例12中,除了用相同摩尔数ptcl2(nh3)2替代rhh(co)(pph3)3外,其余合成过程和条件与实施例1相同,催化剂层(壳层)厚度为0.01mm。
[0078]
对比例1
[0079]
在对比例1中,除了用前期专利cn104707660b中提到的溶剂热聚合法制备均一的催化剂外,浸渍过程金属rh前驱体种类和用量等与实施1相同。
[0080]
具体实施方法为:1000ml的搪瓷高压反应釜中,将10g膦配体l1和 1g过氧化苯甲酰溶解于100ml甲苯,搅拌2小时,373k氮气保护下静止 24小时发生聚合反应。后降温至室温,室温抽除溶剂,得到膦配体粉状聚合物。
[0081]
在298k和惰性气体保护氛围下,称取23.0毫克rhh(co)(pph3)3溶于 30.0ml四氢呋喃中,加入1.0克膦配体粉状聚合物载体(碾碎至200-300目),将此混合物在298k和惰性气体保护氛围下搅拌24小时,然后在室温条件下真空抽走溶剂,即获得rh分布均匀的粉状催化剂。
[0082]
对比例2
[0083]
在对比例2中,膦配体小球制备时,除了用10g乙烯基单齿膦配体
[0084][0085]
代替10g配体l1外,其余的合成过程与实施例1相同。用其余膦配体小球及蛋壳型催化剂合成过程与实施例1相同。经电镜观察剖面,活性组分rh 均匀配位于聚合物小球的表面层,含有金属rh的催化剂层(壳层)厚度为 0.01mm,蛋壳层rh分布均匀。实测催化剂金属负载量为0.25%。
[0086]
对比例3
[0087]
在对比例3中,蛋壳型催化剂制备时浸渍步骤,除了用1.0ml正庚烷替代2.0ml正庚烷来溶解金属前驱体外,其余合成过程和条件与实施例1 相同,经电镜观察剖面,活性组分rh均匀配位于聚合物小球的表面层,含有金属rh的催化剂层(壳层)厚度为0.005mm,蛋壳层rh分布均匀。实测催化剂金属负载量为0.25%
[0088]
对比例4
[0089]
在对比例4中,蛋壳型催化剂制备时浸渍步骤更改如下:
[0090]
筛分出1.0-1.4mm的聚合物小球,在70℃和惰性气体ar气保护氛围下,称取23.0毫克rhh(co)(pph3)3(cas号17185-29-4)溶于150ml 2-甲基四氢呋喃中,加入1.0克上述筛分出的膦配体聚合物小球载体,70℃,搅拌速度120r/min下充分搅拌配位48小时。
[0091]
降温至室温,20℃下真空除去溶剂,即获得应用于丙烯氢甲酰化反应的蛋壳型催化剂,经电镜观察剖面,活性组分rh均匀配位于聚合物小球的表面层,含有金属rh的催化剂层(壳层)厚度为0.12mm,蛋壳层rh分布均匀。实测催化剂金属负载量为0.25%。
[0092]
对比例5
[0093]
在对比例5中,蛋壳型催化剂制备时浸渍步骤更改如下:
[0094]
筛分出1.0-1.4mm的聚合物小球,在70℃和惰性气体ar气保护氛围下,称取23.0毫克rhh(co)(pph3)3(cas号17185-29-4)和1.0g mgcl2溶于 100ml四氢呋喃和水的混合溶液(v:v=1:1),加入1.0克上述筛分出的膦配体聚合物小球载体,70℃,搅拌速度120r/min下充分搅拌配位48小时。
[0095]
降温至室温,20℃下真空除去溶剂,即获得应用于丙烯氢甲酰化反应的蛋壳型催化剂,经电镜观察剖面,活性组分rh均匀配位于聚合物小球的表面层,含有金属rh的催化剂层(壳层)厚度为0.14mm,蛋壳层rh分布均匀。实测催化剂金属负载量为0.25%。
[0096]
实施例13
[0097]
将实施例1-12及对比例1-5制备的催化剂1.0g装入到固定床列管式反应器中部,通入反应混合气(h2:co:c3h6=1:1:1),在398k,1.5mpa,反应混合气空速1000h-1
条件下进行氢甲酰化反应。反应经一个恒温-20℃体积 100ml的收集罐吸收收集,反应产物全部收集于收集罐中。所获得产品采用配有hp-5毛细管柱和fid检测器的hp-7890n气相色谱分析,反应
尾气采用hp-7890n气相色谱的tcd检测器进行在线分析,反应结果列于表1。
[0098]
表1.实施例1-12及对比例催化剂的丙烯氢甲酰化性能
[0099][0100][0101]
实施例1-12使用的是蛋壳型催化剂,当采用单膦配体的聚合物小球蛋壳型催化剂时,产品醛中的正异比基本可以在1.0左右。采用二级氧化膦的聚合物小球蛋壳型催化剂,产品醛中异丁醛的选择性还可以进一步升高。实施例9,10,11和12活性金属分别为co、ir、pd和pt,反应性能低于活性金属为rh的催化剂但是co、ir、pd和pt等的价格比较低,对于工业某些场合非rh金属更适用)。当活性中心为rh时,可以看出蛋壳型的催化剂的异丁醛选择性明显高于相应的对比例均一型的催化剂(对比例1),同时丙烯氢甲酰化反应活性也要更高。对比例2采用的是三个乙烯基的单膦配体,交联后制备的蛋壳型催化剂比表面积比实施例1-12要大一些,孔道也和实施例1-12有所区别,最终导致产品醛中异丁醛的选择性低于实施例1-12的方案,这可能是由于三个乙烯基的单膦配体做出的聚合物小球的孔道限域效
应,不利于诱导立体位阻更大的异丁醛产生造成的。对比例3中做出的蛋壳型催化剂蛋壳层厚度为0.005mm,虽然也能维持较高的异丁醛选择性,但是丙烯tof值比实施例1要低,而对比例4和对比例5的方案做出的蛋壳层厚度分别为0.12mm和0.14mm,产品中异丁醛选择性出现了明显的下降,并且丙烯的tof值比实施例1要低不少,这可能是由于rh浸渍深度较深,聚合物小球的载体孔道限制位阻更大的异丁醛产生造成的,同时较深的浸渍深度不利于反应物与活性中心rh的接触。综上,合适的蛋壳层厚度可以保证较高异丁醛选择性(丁醛正异比在1左右)的同时,保证较高的丙烯氢甲酰化反应活性(除了非rh金属外,丙烯tof值基本在1000h-1 以上)。我们通过控制聚合物小球的孔道结构,控制蛋壳型催化剂制备过程等手段,使得制备出的蛋壳型催化剂活性中心位于蛋壳型催化剂的表层,活性中心在催化剂中的特定分布使得制备出的蛋壳型催化剂应用于丙烯氢甲酰化反应时,催化剂活性高,产品醛中异丁醛选择性好。
再多了解一些
本文用于企业家、创业者技术爱好者查询,结果仅供参考。