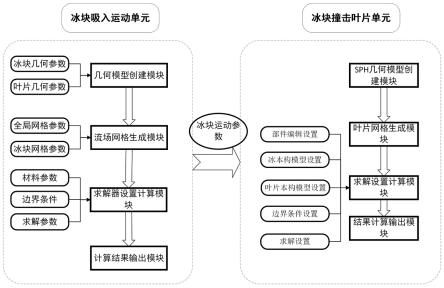
1.本发明属于返发动机叶片损伤评估技术领域,具体涉及一种航空发动机叶片冰撞击损伤高精度智能评估系统。
背景技术:
2.现有针对发动机冰脱落运动轨迹及撞击壁面、叶片过程的仿真计算方法的主要以人为判断和迭代为主,还没有采用人工智能算法,依靠多工具接口开发实现联合仿真系统。其可靠性预测只能做定性判断,定量判断误差较大,误差在正负50%之间。
3.现有针对航空发动机叶片冰撞击损伤计算方法的主要缺陷是:航空发动机叶片冰撞击损伤现有的计算方法只考虑了冰块撞击叶片的单一过程,没有实现和冰块在脱落飞行中的运动姿态数据耦合,并且计算精度不够高。现有航空发动机叶片冰撞击损伤计算流程仅仅依赖于单个商业化软件工具,不具备专业化工程仿真软件系统,没有嵌入可操作性的仿真规范标准,不利于仿真经验及仿真知识的固化传递,且仿真效率较低。
技术实现要素:
4.本发明的目的在于提供一种航空发动机叶片冰撞击损伤高精度智能评估系统,该系统实现航空发动机冰块吸入姿态变化和撞击过程耦合过程的高精度仿真分析,冰撞击叶片计算损伤精度控制在10%以内,并能够自动生成仿真报告。
5.为实现上述目的,本发明采用如下技术方案:航空发动机叶片冰撞击损伤高精度智能评估系统,包括:冰块吸入运动单元,用于根据输入参数计算出冰块运动参数并根据报告模板生成仿真报告;冰块撞击叶片单元,根据所述冰块运动参数和叶片几何三维模型进行冰块撞击叶片计算,并形成仿真报告;其中,所述冰块吸入运动单元包括几何模型创建模块、流场网格生成模块、求解器设置计算模块和计算结果输出模块;所述几何模型创建模块用于根据冰块几何参数、通道几何参数和叶片几何参数生成仿真所需的几何三维模型;所述流场网格生成模块用于设置冰块和通道的网格参数生成高质量的三维流场重叠计算网格,并根据三维流场重叠计算网格对冰块仿真所需的几何三维模型网格化处理;所述求解器设置计算模块用于根据材料参数、边界条件和计算要求计算出冰块运动参数;所述计算结果输出模块用于根据设置的报告模板生成仿真报告;所述冰块撞击叶片单元包括sph几何模型创建模块、叶片网格生成模块、求解设置计算模块和结果计算输出模块;所述sph几何模型创建模块用于导入叶片几何模型并根据所述冰块运动参数、以及输入的冰块重心坐标、冰块密度和不同方向的粒子数量形成sph几何模型;所述叶片网格生成模块用于导入网格并根据选择的精度参数将sph几何模型中的冰块参数网格化形成新的sph几何模型;所述求解设置计算模块用于根据设置的不同选项
参数设置启动冰块撞击叶片计算,并提取数据和动画最后生成仿真动画,选项参数设置包括部件编辑设置、冰本构模型设置、叶片本构模型设置、边界条件设置和求解设置;所述结果计算输出模块用于根据设置的报告模板生成仿真报告。
6.进一步地,所述冰块几何参数包括冰块形状和冰块尺寸,通道几何参数包括涵道型线数据,叶片几何参数包括叶轮厚度、叶轮半径和整流锥度。
7.进一步地,所述网格参数包括网格单元尺寸、边界层首层、边界层增长率和边界层层数。
8.进一步地,所述材料参数包括冰块密度、冰块分别绕xyz轴重心坐标的转动惯量和初始释放速度;环境压力、重力加速度、流动速度、温度和叶片参数;计算设置包括初始稳态迭代步、库朗特数、时间步长、时间步数、子循环迭代、自动保存时间步和并行线程数。
9.进一步地,所述部件编辑设置包括冰块参数和叶片参数,冰块参数和叶片参数均包括对应的单元号、材料号和状态方程号;冰本构模型设置包括冰本构模型参数和冰材料参数定义曲线,所述冰本构模型参数包括弹性模量、泊松比、压缩截止压力和拉伸截止压力,冰材料参数定义曲线外部导入;叶片本构模型设置包括叶片本构模型参数和真实有效塑性应力应变曲线,叶片本构模型参数包括材料类型、密度、弹性模量和泊松比,真实有效塑性应力应变曲线外部导入;所述边界条件设置包括边界条件id和自由度定义;所述求解设置包括冰初始速度、求解总时间和并行线程数。
10.本发明通过系统研究冰体的本构模型及叶片损伤模型,基于冰撞击过程计算过程建立了一套叶片吞冰损伤规范化分析方法和流程,可以为航空发动机进气条件下的吞冰损伤物理试验提供多方案快速优化的数值参考,具备可靠精度,可有效节约试验成本、提升试验效率。
附图说明
11.图1为本发明的系统结构框图。
12.图2为本发明的铝合金靶板中心位置处位移时间历程曲线图。
具体实施方式
13.如图1所示,本实施例提供的航空发动机叶片冰撞击损伤高精度智能评估系统包括冰块吸入运动单元和冰块撞击叶片单元,冰块吸入运动单元用于根据输入参数计算出冰块运动参数并根据报告模板生成仿真报告;同时还将计算的冰块运动参数发送给冰块撞击叶片单元,冰块撞击叶片单元根据冰块运动参数和叶片几何三维模型进行冰块撞击叶片计算,并形成仿真报告。
14.所述冰块吸入运动单元包括几何模型创建模块、流场网格生成模块、求解器设置计算模块和计算结果输出模块。
15.所述几何模型创建模块用于根据输入的参数生成仿真所需的几何三维模型;输入参数包括冰块几何参数、通道几何参数和叶片几何参数,冰块几何参数包括冰块形状和冰块尺寸,其中,冰块形状可选择球形或方形,通过输入具体的数据实现冰块尺寸的设定,球形输入直径大小,方形输入长宽高等参数,冰块形状和尺寸构成冰块几何参数,根据冰块几何参数自动生成冰块几何三维模型。所述通道几何参数采用外部导入涵道型线数据,根据
导入的涵道型线数据生成涵道几何三维模型,本地保存航空发送机常用的所有涵道型线数据。所述叶片几何参数包括叶轮厚度、叶轮半径和整流锥度,通过输入对应的叶轮几何参数数据设定叶片的形状进而生成对应的叶片几何三维模型。所述冰块几何三维模型、涵道几何三维模块和叶片几何三维模型构成了冰块仿真所需的几何三维模型。
16.所述流场网格生成模块用于设置冰块和通道的网格参数生成高质量的三维流场重叠计算网格,并根据三维流场重叠计算网格对冰块仿真所需的几何三维模型网格化操作,其中,冰块网格参数包括边界层首层、边界层增长率和边界层层数;通道网格参数包括面网格单元尺寸、边界层首层、边界层增长率和边界层层数。
17.所述求解器设置计算模块用于输入材料参数设置、边界条件设置和计算设置三个选项计算出冰块运动参数。所述材料参数设置包括冰块密度、冰块分别绕xyz轴重心坐标的转动惯量和初始释放速度。所述边界条件包括环境压力、重力加速度、流动速度(初始流动速度、最终流动速度、流动变化时间)、温度、叶片参数(转速、剪切拐点、压降)。所述计算设置包括初始稳态迭代步、库朗特数、时间步长、时间步数、子循环迭代、自动保存时间步和并行线程数。
18.所述计算结果输出模块用于根据用户提供的报告模板自动插入数据,在特定目录下生成仿真报告。为有效地组织和管理本地仿真数据,系统通过创建一个项目文件夹和一系列子目录来管理所有相关文件,工程文件夹内按树形结构的方式组织各类数据和文件使其保存到合适的位置方便用户查找。
19.所述冰块撞击叶片单元包括sph几何模型创建模块、叶片网格生成模块、求解设置计算模块和结果计算输出模块。
20.所述sph几何模型创建模块用于导入叶片几何模型并根据所述冰块运动参数和冰块重心坐标、冰块密度、不同方向的粒子数量形成sph几何模型,冰块运动参数包括冰块姿态和速度参数。
21.所述叶片网格生成模块用于导入网格并根据选择的精度参数将sph几何模型中的冰块参数网格化形成新的sph几何模型。
22.所述求解设置计算模块用于根据设置的不同选项参数设置启动冰块撞击叶片计算,并提取数据和动画最后生成仿真报告。不同选项设置包括部件编辑、冰本构模型设置、叶片本构模型设置、边界条件设置和求解设置,快速完成复杂非线性问题的求解计算设置过程。所述部件设置包括冰块参数和叶片参数,冰块参数和叶片参数均包括对应的单元号、材料号和状态方程号。冰本构模型设置包括冰本构模型参数和冰材料参数定义曲线,所述冰本构模型参数包括弹性模量、泊松比、压缩截止压力和拉伸截止压力,冰材料参数定义曲线外部导入。叶片本构模型设置包括叶片本构模型参数和真实有效塑性应力应变曲线,叶片本构模型参数包括材料类型、密度、弹性模量和泊松比,真实有效塑性应力应变曲线外部导入。所述边界条件设置包括边界条件id和自由度定义(平移和转动)。所述求解设置包括冰初始速度、求解总时间和并行线程数。
23.所述结果计算输出模块用于根据用户提供的报告模板自动插入数据,在特定目录下生成仿真报告。
24.对本实施例提供的系统精度进行验证:1、铝合金模型及材料参数标定
铝合金材料模型采用分段线性硬化弹塑性材料模型,对直径25.3mm的冰球以192m/s速度撞击铝合金靶板工况进行计算,靶板边界处设置位移约束。铝合金靶板中心位置处位移时间历程曲线如图2所示,铝板中心位置处最大位移为11.98mm,针对不同速度冰撞击工况进行仿真模型标定,验证适用于航空发动机风扇叶片冰撞击数值仿真的冰本构参数和仿真建模方法;从表1可知仿真与试验测试最高误差为8%,计算和试验结果吻合,证明上述验证模型具备良好的可靠性。
25.表1 冰球撞击铝合金靶板数值模拟结果2、冰撞击发动机风扇叶片数值仿真分析在工程实践中为了降低试验的复杂度和设计迭代周期,可以在设计初期根据撞击点处速度等效原则采用静止风扇叶片代替旋转风扇叶片开展冰撞击试验,以获得风扇叶片动态应变。试验所用冰弹直径为25.4mm,实测发射速度为151.5m/s,冲击位置为叶高75%。冰弹采用sph几何模型模拟,sph几何模型建模方法与冰的材料本构与前述刚性靶板冰撞击仿真相同。冰球以151.5m/s的速度撞击单个风扇叶片,撞击过程中的sph粒子破碎和等效应力从0.2毫秒到0.8毫秒。
26.基于单个冰球真实撞击风扇叶片多个试验结果开展仿真多工况模拟校核计算,选取了不同半径、不同质量冰球和撞击速度组合的三种不同试验工况并对结果进行对比分析,试验条件及叶片损伤模拟结果比较见下表2所示。
27.表2 不同试验条件下叶片损伤模拟比较从表2数据对比可以看出,仿真模型计算结果显示撞击区域叶片前缘卷曲、叶身凹陷等变形的位置和面积与试验趋势吻合,各工况变形量平均误差小于10%,通过冰撞击过程理论研究和试验对比,验证了冰撞击理论模型的准确性。
28.本实施例基于冰轨迹预测和冰撞击仿真研究,构建了吞冰流场计算和冰撞击过程计算一体化耦合过程,在仿真计算研究成果的基础上,开发出航空发动机冰块撞击损伤评估软件系统。该系统集成冰块运动、冰块撞击叶片过程的仿真流程和仿真规范,基于三维虚拟仿真系统快速实现发动机吞冰过程中的冰块运动、冰块撞击叶片破碎过程及破碎后轨迹预测的一体化仿真流程。基于专业应用app智能向导可以快速实现几何建模及导入、网格智能划分、物理模型及边界条件设定、仿真自动求解、报告自动生成等一系列复杂仿真流程的
智能压缩,基于规范化流程和专业app大大降低复杂问题的仿真门槛,数十倍地提高技术人员的仿真效率,填补了航空发动机叶片冰撞击损伤高精度智能化、工程化评估手段的空白。
29.以上所述仅是本发明优选的实施方式,但本发明的保护范围并不局限于此,任何基于本发明所提供的技术方案和发明构思进行的改造和替换都应涵盖在本发明的保护范围内。
再多了解一些
本文用于企业家、创业者技术爱好者查询,结果仅供参考。