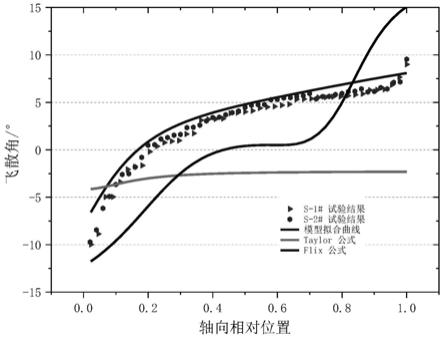
1.本发明属于弹药设计领域,特别是一种考虑破片相对位置的预制破片飞散角计算方法及系统。
背景技术:
2.填充破片的圆柱形装药战斗部是战斗部设计中常用的结构之一,被称为破片战斗部,装药爆炸后,高压爆轰产物带动破片高速运动,是主要的毁伤元。为了改进战斗部设计,需要准确的预测破片的速度及飞散角。因此,提出了一系列经验公式来估算这种典型战斗部的性能。
3.gurney公式是计算破片速度的代表性公式,考虑了装药质量与壳体质量之比,huang等人提出了一个更精确的公式来估算一端起爆的圆柱形套筒的破片速度。这是通过轴向稀疏波效应修正的gurney公式,目前应用程度较高。taylor提出了一个极具代表性的解析公式来预测战斗部的飞散角,多项试验数据表明,该公式对于破片飞散角的预测是不准确的,尤其是两端位置处的破片飞散角。flix提出了根据壳体膨胀形状构造的破片初始飞散角函数,此公式需要得知端板处破片飞散角度的折减以及最大破片速度的位置,一方面在试验中难以获得,另一方面构造的相对位置及折减精度多为假设值,修正后的函数曲线存在一定局限性。
4.考虑到轴向稀疏效应对破片飞散分布的影响研究仍有欠缺和局限之处,急需提出一种考虑轴向稀疏效应及壳体相对位置对一端起爆下的圆柱形战斗部飞散分布预测模型
技术实现要素:
5.本发明的目的在于提供一种考虑破片相对位置的预制破片飞散角计算方法及系统,考虑轴向稀疏效应及壳体相对位置对一端起爆下的圆柱形战斗部飞散分布预测,能够更精确的预测圆柱形破片战斗部的各个轴向位置处的破片飞散分布,尤其是在爆轰端与非爆轰端。
6.实现本发明目的的技术解决方案为:
7.一种考虑破片相对位置的预制破片飞散角计算系统,包括参数输入模块和破片飞散角计算模块;
8.所述参数输入模块用于输入破片飞散角计算的输入参数,包括破片距离起爆端的距离x,战斗部装药直径d,战斗部长度l,破片初速v0,炸药爆速d;
9.所述破片飞散角计算模块用于通过以下公式计算破片的飞散角:
[0010][0011]
一种考虑破片相对位置的预制破片飞散角计算方法,所述破片飞散角通过以下公式计算获得:
[0012][0013]
其中,x为破片距离起爆端的距离,d为战斗部装药直径,l为战斗部长度,v0为破片初速,d为炸药爆速,为爆轰波法线与弹体对称轴构成的夹角。
[0014]
本发明与现有技术相比,其显著优点是:
[0015]
本发明考虑了了装药质量与壳体质量之比(v0由此决定)、装药直径及长径比、轴向稀疏效应及壳体相对位置对飞散角的影响,能够更精确的预测圆柱形破片战斗部的各个轴向位置处的破片飞散分布,尤其是在爆轰端与非爆轰端。通过其他工况下的试验验证了该公式的普遍适用性并与其它经验模型进行对比。计算结果与试验数据吻合较好,表明该公式在预测一端起爆下的圆柱形壳体破片的飞散角具有较高的精度,满足工程计算的偏差要求。
附图说明
[0016]
图1是样本试验布置和样本结构示意图。
[0017]
图2是样本中一发爆炸驱动下预制破片穿靶过程。
[0018]
图3是试验后见证板上坑洞处理图。
[0019]
图4是样本破片飞散分布情况图。
[0020]
图5是样本拟合结果图,(a~c)分别为50mm口径拟合结果图、70mm口径拟合结果图、89mm口径拟合结果图。
[0021]
图6是破片飞散分布模型误差分析图,(a~c)分别为轴向相对位置误差图、飞散分布误差统计图、百分位数误差分析图。
[0022]
图7是验证试验中本发明同其它经验模型对比图。
具体实施方式
[0023]
下面结合附图及具体实施例对本发明做进一步的介绍。
[0024]
本实施例的一种考虑破片相对位置的预制破片飞散角计算系统,基于计算机系统,包括参数输入模块、破片飞散角计算模块、破片飞散分布曲线拟合模块;
[0025]
所述参数输入模块用于输入破片飞散角计算的输入参数,包括破片距离起爆端的距离x,战斗部装药直径d,战斗部长度l,破片初速v0,爆轰波法线与弹体对称轴构成的夹角由破片距离起爆端的距离x和战斗部装药直径d确定:
[0026][0027]
所述破片飞散角计算模块通过以下公式计算破片的飞散角:
[0028][0029]
所述破片飞散分布曲线拟合模块根据参数输入模块输入的多组输入参数、破片飞散角计算模块计算得到的多组输入参数对应的飞散角,拟合生成飞散角分布曲线。
[0030]
为研究爆炸驱动下破片的轴向飞散特性,在图1(a)所示的爆炸装置上进行静爆试验,由破片在见证板上的撞击穿孔位置测定破片的空间分布。将样本放置于木板平面支架上,距离地面1.5m。见证板由碳素结构钢构成,尺寸为1570mm长,3000mm高,3mm厚。战斗部与
见证板间覆盖角度为18
°
,见证板放置于战斗部距爆心外5m处。战斗部起爆方式为一端中心起爆,试验样弹立式放置,起爆端朝上。
[0031]
制备了6组内径不同,且具有不同长径比的圆柱形标本,图1(b)显示了装有jh-2炸药和装配有3mm厚45钢套管、5mm侧端盖及5mm钢球的圆柱形样品。用300吨的压制设备在300mpa的压力下压制装药,以获得大于1.69g/cm3的装药密度。内外套管间通过螺纹连接的方式进行固定,将5mm钢球破片按序放入套筒内后注入环氧树脂固定,所有样品的8701炸药密度及套管厚度相同,六组试件的长径比分别为2:1、1.8:1、1.6:1,装药口径分别为56mm,70mm,89mm。试件的c/m比分别为0.778、0.579、0.743。表样本的详细规格如下表所示。
[0032][0033][0034]
通过高速摄影拍摄破片击靶的瞬间,根据照片上的时间标记,测算出给定距离时的破片速度。试验结束后,通过与高速摄影相连接的数据采集系统,将图像转换为灰度位图并调节亮度及对比度得到破片穿靶过程,如图2所示。
[0035]
将出现火光的前一帧设为0,可以发现爆炸驱动后,见证板于30.8ms出现破片击穿产生的亮点。通过破片运动规律进行计算,假设破片的水平飞行弹道为直线,忽略空气升力和自身重力的影响,只考虑空气阻力作用,依照破片速度的衰减公式,则其运动方程为:
[0036][0037]
式中:v为破片的瞬时速度,cf为破片飞行的空气阻力系数,取球形预制破片cf=0.97,为破片的平均迎风面积,mf为破片质量,t为时间,ρ0为空气密度。对上式积分得到破片飞行速度vf与飞行时间tf之间的关系式
[0038][0039]
依据上述公式,由测速点的速度vf反推计算得出破片初速度v0。
[0040]
试验后统计破片飞散及见证板穿孔情况,利用见证板上坑洞区域边缘像素灰度值的突变,对图像进行分割、目标区域识别以及区域形状提取,利用ipp(image-pro plus)及image j图像分析软件对所获得的见证板坑洞轮廓进行测量和定位,并对其进行统计,如图3所示。
[0041]
由于破片在侵彻时着靶穿孔与破片大小形状基本一致,故可通过ipp有效提取预制破片穿孔,对六组方案下见证靶上形成的破片进行位置统计,得到破片飞散分布情况如
图4所示,相同口径相同长径比下破片飞散一致性较好,实验数据没有误差,其用于建立飞散分布估算模型。
[0042]
由上述飞散分布试验结果入手,可以明显发现,破片分散分布曲线与原始的双曲正弦(sinhx)曲线具有相同的函数变化特征,可以认为是双曲正弦曲线进行相应平移以及系数变换使得在变量0~1(轴向相对位置)之间的曲线存在正负值。因此新函数被假定为双曲正弦曲线。因为试验所得的破片飞散分布曲线存在负值,因此不能通过双曲余弦曲线来构造经验模型。起爆端修正项
[0043]
f(x)=(a1 sinh(b1·
x/d))
[0044]
非起爆端的修正项:
[0045]
f(y)=(a2 sinh(b2·
(l-x)/d))
[0046]
其中,a1和b1是来自起爆端的稀疏波影响的校正系数,a2和b2是来自非起爆端的稀疏波影响的校正系数,x是破片距离起爆端的距离,l是战斗部长度,d是战斗部装药直径。
[0047]
起爆端修正项f(x)和非起爆端修正项f(y)再加上理想破片飞散分布模型θ即为完整的飞散预测模型。将试验数据代入上述构造的飞散预测模型,可用非线性最小二乘法回归方程拟合。修正后的飞散角分布函数曲线如图5所示,4个校正系数由试验数据确定,拟合修正结果为:
[0048][0049]
其中v0是破片初速,d为炸药爆速,为爆轰波法线与弹体对称轴构成的夹角;由破片距离起爆端的距离x和战斗部装药直径d确定:
[0050][0051]
拟合参数拟合的r-square为0.9885,表明该方程很好的拟合了试验数据,能够描述不同口径、不同长径比装药下稀疏波效应影响下的破片飞散分布,尤其在起爆端和非起爆端的飞散也是合理的,极大的提高了对于战斗部毁伤能力的预测。对于x/d与(l-x)/d的参数意义,可以更精确的得到一端起爆下圆柱形破片战斗部的各个轴向位置处的破片飞散分布,这意味着此模型的结果更加准确和适用。
[0052]
图6显示了模型结果与实验结果间的相对差异。其中残差的df、平方和及均方值分别为72、12.86、0.19938,轴向相对位置与拟合y值的残差多分布于-1~1.5之间,如图6(a)(b)所示,以(-0.93,0.66)(0.93.99.33)为参照线,百分位数的常规残差不超过0.3,如图10(c),模型拟合结果较为精确,与试验结果符合较好。相对轴向位置97%的数据点的相对误差在3%以内,6组数据的平均误差计算
±
2%。较大的相对误差是因为来自起爆端和非起爆端的稀疏波影响导致破片受力不均,因此飞散分布不稳定,但此模型也较大程度的避免了误差的影响。总体来说,该模型可作为一端起爆的圆柱形装药在考虑稀疏波效应下的破片飞散分布的经验计算模型。
[0053]
为了验证上述破片飞散分布公式的一般适用性,按照样本试验设计了一组验证试验。将破片初始速度代入本发明的经验模型来预测飞散角,得到的结果同其它模型对比,得到的结果如图7,本发明模型拟合结果较为精确,与试验结果符合较好。相对轴向位置97%的数据点的相对误差在6%以内,2组数据的平均误差计算
±
7%,符合误差要求,与试验数据吻合较好,在预测一端起爆下的圆柱形壳体破片的飞散角具有较高的精度,满足工程计
算的偏差要求。
再多了解一些
本文用于企业家、创业者技术爱好者查询,结果仅供参考。