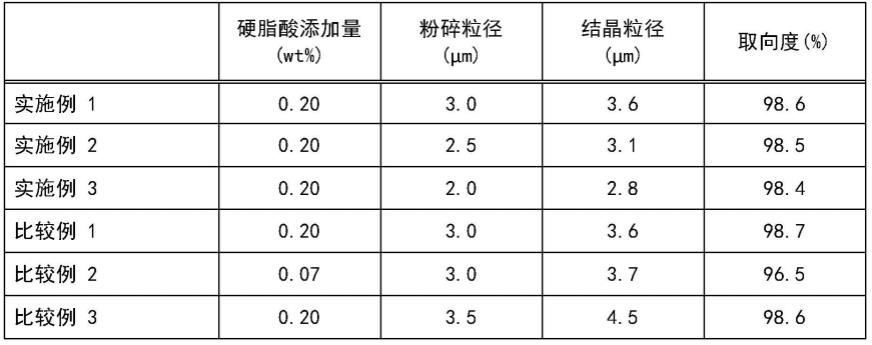
1.本发明涉及具有兼具高br和高h
cj
的优异的磁特性的稀土烧结磁体及其制造方法。
背景技术:
2.稀土烧结磁体作为节能化、高功能化所不可或缺的功能性材料,其应用范围和生产量逐年扩大。在稀土烧结磁体中,特别是nd系烧结磁体(以下称为“nd磁体”)具有高的剩余磁通密度(以下称为“br”),例如用于混合动力汽车、电动汽车的驱动用马达、电动动力转向用马达、空调的压缩机用马达、硬盘驱动器的音圈马达(vcm)等。如此,在多种用途的马达中,使用了具有高br的nd磁体,但例如为了使马达进一步小型化,对于nd磁体要求更高的br。
3.另一方面,在高温下,稀土烧结磁体的矫顽力(以下称为“h
cj”)降低,因此发生不可逆热退磁。因此,特别是在电动汽车用马达等面向汽车使用的稀土烧结磁体中,要求具有高的h
cj
。
4.以往,作为提高nd磁体的br的方法,有组成上的方法和制作工序上的方法,作为组成上的方法,已知有为了增加nd磁体中的r2t
14
x相的比例而减少r的含量的方法、减少固溶在r2t
14
x相中而使br降低的添加元素的量的方法。
5.然而,已知通过减少r、其他添加元素的量,与稀土烧结磁体的耐热性有关的h
cj
降低。特别是在减少r量的情况下,在随着液相的生成而引起致密化的nd磁体的烧结工序中,其烧结性降低,并且还存在发生异常晶粒生长的风险。因此,为了得到更高特性的nd磁体,抑制减少r、其他添加元素的量而导致的h
cj
降低,并且实现高的br是重要的。在该情况下,为了抑制h
cj
的降低或增大h
cj
,通常已知添加dy、tb等重稀土元素,但由于其添加而导致br的降低,且dy、tb等重稀土元素在资源方面也是稀有的,价格昂贵,因此该方法未必优选。
6.另外,作为制作工序上的方法,已知有为了提高r2t
14
x相的取向度而使添加于成型前的粉末的润滑剂(饱和脂肪酸、其酯等)增量的方法、使成型时的施加磁场增大等进行条件调整的方法。
7.然而,已知在使添加到成型前的粉末中的润滑剂增量的情况下,虽然通过取向度的提高而得到br的增大,但一般而言,从此得到的nd磁体因大量存在来自润滑剂的c而使h
cj
大幅降低。另外,为了增大成型时使r2t
14
x相取向的施加磁场,需要用于产生磁场的电磁体的大型化,进而需要设备的大型化、以及减小磁场空间,无法实现工业上的效率化。
8.另一方面,作为增大nd磁体的h
cj
的方法,已知有结晶粒径的微细化。已知其主要是在成型前对原料合金进行微粉碎时通过使微粉粒度变细从而进行烧结后的晶体粒径的微细化(细化),在某一定的粒径范围内,随着粒径微细化,h
cj
线性地增大。
9.但是,在进行一定以上的微细化的情况下,由于微粉碎时的粉碎能力降低、微粉的反应性提高等,微粉的杂质(主要是氧、氮)浓度增大,因此nd磁体的h
cj
降低、或者即使h
cj
增大也难以应用后述的晶界扩散法。为了对此进行改善,提出了将微粉碎时的粉碎气体变为he、ar等惰性气体的方法(专利文献1)。
10.作为其他的nd磁体的h
cj
增加方法,已知有选择性地使重稀土元素(dy、tb等)聚集于nd磁体中的晶界相的方法(以下称为“晶界扩散法”)(专利文献2、3)。该方法是在利用涂布等方法使dy、tb等重稀土元素化合物附着于磁体表面后,在高温下进行加热处理的方法,仅在极接近nd磁体中的主相粒子的晶界的区域形成dy、tb的浓度高的组织,从而能够在抑制br降低的同时得到高的h
cj
增大效果。
11.现有技术文献
12.专利文献
13.专利文献1:国际公开第2014/142137号
14.专利文献2:国际公开第2006/044348号
15.专利文献3:国际公开第2013/100010号
技术实现要素:
16.发明所要解决的课题
17.然而,在上述专利文献1所记载的方法、上述专利文献1、2等中记载的晶界扩散法中,存在以下的课题。
18.即,在将上述专利文献1中提出的微粉碎时的粉碎气体变为he、ar等惰性气体的方法中,若考虑与氮气的价格差,则工业上的生产困难。另外,晶界扩散法虽然对于高矫顽力化非常有用,但是在为了提高nd磁体的br,减少磁体中的添加元素、多余的r量的情况下、或者在由于进行润滑剂的增量而带来的取向提高等而使杂质元素(碳、氧、氮)增大的情况下,存在h
cj
增大效果显著降低的问题。另外,由于h
cj
增大效果量也有限度,因此,对于电动汽车等要求高耐热性的用途,需要提高进行晶界扩散法之前的磁体原材料自身的h
cj
矫顽力。
19.本发明是鉴于上述课题而完成的,目的在于提供一种稀土烧结磁体,其通过与以往提出的制造时的微细化、晶界扩散的实施不同的方法,实现高的br和高的h
cj
。
20.用于解决课题的手段
21.本发明人为了实现上述目的,着眼于稀土烧结磁体中的杂质量、平均结晶粒径以及取向度,进行了深入研究,结果发现,在降低通常在稀土烧结磁体中被评价为杂质的o、n、c量的基础上,将稀土烧结磁体的平均结晶粒径抑制为4.0μm以下,并且使取向度相对于平均结晶粒径满足特定的关系的情况下,可得到兼具高的br和高的h
cj
的具有优异的磁特性的稀土烧结磁体,完成了本发明。
22.因此,本发明提供下述的稀土烧结磁体。
23.[1]稀土烧结磁体,是包含r(r为选自稀土元素中的1种以上的元素,以nd为必需元素)、t(t为选自铁族元素中的1种以上的元素,以fe为必需元素)、x(x为选自b、c中的1种或2种元素,以b为必需元素)、m1(m1为选自al、si、cr、mn、cu、zn、ga、ge、mo、sn、w、pb、bi中的1种以上的元素)的稀土烧结磁体,其特征在于,包含0.1质量%以下的o、0.05质量%以下的n、0.07质量%以下的c,该稀土烧结磁体的平均结晶粒径为4.0μm以下,并且,对于取向度,在将取向度设为or[%]、将平均结晶粒径设为d[μm]的情况下,满足以下的关系式(1):
[0024]
0.26
×
d 97≦or≦0.26
×
d 99
···
(1)。
[0025]
[2][1]的稀土烧结磁体,其中,作为所述r的一部分,包含通过晶界扩散而引入至烧结后的磁体的r元素。
[0026]
[3][2]的稀土烧结磁体,其中,通过所述晶界扩散而引入的r元素为选自dy、tb及ho中的1种以上的元素。
[0027]
[4][1]~[3]中任一项的稀土烧结磁体,其中,在将所述r、t、x的原子百分率分别设为[r]、[t]、[x]的情况下,满足以下的关系式(2):
[0028]
[t]/14≦[x]≦[r]/2
···
(2)。
[0029]
[5][1]~[3]中任一项的稀土烧结磁体,其中,还包含m2(m2为选自ti、v、zr、nb、hf、ta中的1种以上的元素),在将所述r、t、x、m2的原子百分率分别设为[r]、[t]、[x]、[m2]的情况下,满足以下的关系式(3):
[0030]
([t]/14) ([m2]
×
2)≦[x]≦([r]/2) ([m2]
×
2)
···
(3)。
[0031]
[6][5]的稀土烧结磁体,其中,所述m2为0.5原子%以下。
[0032]
[7][1]~[6]中任一项的稀土烧结磁体,其中,r为12.5原子%~16.0原子%,m1为0.1原子%~2.0原子%。
[0033]
发明效果
[0034]
根据本发明的稀土烧结磁体,通过将稀土烧结磁体中的o量、n量、c量、平均结晶粒径、取向度调整在特定的范围,并且优化平均结晶粒径与取向度的关系,能够得到兼具高的br和高的h
cj
的优异的磁特性。
具体实施方式
[0035]
如上所述,本发明的稀土烧结磁体具有包含r(r为选自稀土元素中的1种以上的元素,以nd为必需)、t(t为选自铁族元素中的1种以上的元素,以fe为必需)、x(x为选自b、c中的1种或2种元素,以b为必需)、m1(m1为选自al、si、cr、mn、cu、zn、ga、ge、mo、sn、w、pb、bi中的1种以上的元素)的组成,并且含有o、c、n和不可避免的杂质。
[0036]
如上所述,上述r是选自稀土元素中的1种以上的元素,以nd为必需。对r的含量没有特别限制,从抑制溶解的合金的α-fe的结晶析出、烧结时促进正常的致密化的观点出发,优选为12.5原子%以上,更优选为13.0原子%以上。另外,从得到高br的观点出发,优选为16.0原子%以下,更优选为15.5原子%以下。
[0037]
对r中的nd的比例没有特别限定,优选为全部r元素的60原子%以上,更优选为75原子%以上。另外,作为nd以外的r元素,没有特别限制,可以优选含有pr、dy、tb、ho、ce、y等。
[0038]
如上所述,上述t是选自铁族元素、即fe、co、ni中的1种以上的元素,以fe为必需。t的含量为上述r、x、m1、o、c、n及后述的m2以外的剩余部分,优选为70原子%以上且80原子%以下。应予说明,fe的含有比例优选为稀土磁体整体的70原子%以上且85原子%以下,更优选为75原子%以上且80原子%以下。
[0039]
如上所述,上述x为选自b、c中的1种或2种,以b为必需。从充分地形成主相从而确保充分的br的观点出发,x的含量优选为5.0原子%以上,更优选为5.5原子%以上。另外,考虑到x的含量过高的情况下的nd1fe4x4相的析出对br的影响,优选为8.0原子%以下,更优选为7.0原子%以下。
[0040]
在此,虽没有特别限制,上述r、t和x的含量在将它们的原子百分率分别设为[r]、[t]和[x]的情况下,优选满足以下的关系式(2)。
[0041]
[t]/14≦[x]≦[r]/2
···
(2)
[0042]
即,从r2t
14
x相比率的减少对br的影响、形成r2t
17
相带来的对h
cj
的影响的观点出发,x的含量优选为[t]/14以上,另外,考虑到r
1.1
fe4b4相这样的富x相的形成引起的r2t
14
x相比率的变动对br的影响,优选为[r]/2以下。
[0043]
如上所述,上述m1为选自al、si、cr、mn、cu、zn、ga、ge、mo、sn、w、pb、bi中的1种以上的元素。从确保用于确保良好的生产率的热处理中的最佳温度具有充分的宽度的观点、进而抑制h
cj
的降低的观点出发,m1的含量优选为0.1原子%以上,更优选为0.3原子%以上,进一步优选为0.5原子%以上。另外,从得到高br的观点出发,优选为2.0原子%以下,更优选为1.5原子%以下。
[0044]
上述o的含量为0.1质量%以下,优选为0.08质量%以下。在o的含量超过0.1质量%的情况下,磁特性、特别是h
cj
降低。另外,上述n的含量为0.05质量%以下,优选为0.03质量%以下。在n的含量超过0.05质量%的情况下,h
cj
降低。进而,上述c的含量包含作为上述x元素的一部分而含有的情况在内为0.07质量%以下,优选为0.05质量%以下。c的含量超过0.07质量%时,h
cj
降低。应予说明,在本发明中,这些o、n、c的含量越少越好,但通常这些元素是难以完全排除的不可避免的元素。
[0045]
另外,在本发明的稀土烧结磁体中,使平均结晶粒径为4μm以下,更优选平均结晶粒径为3.5μm以下。在平均结晶粒径超过4μm的情况下,难以得到高的h
cj
,有时无法实现本发明的目的。应予说明,平均结晶粒径的测定例如可以通过以下的步骤进行。首先,将烧结磁体的截面研磨至成为镜面后,利用激光显微镜观察浸渍于例如vilella腐蚀液(例如,混合比为甘油:硝酸:盐酸=3:1:2的混合液)等蚀刻液中而选择性地蚀刻晶界相的截面。接着,基于所得到的观察图像,通过图像解析来测定各个粒子的截面积,计算作为等价圆的直径。然后,基于各粒度所占的面积分数的数据,求出平均直径。应予说明,平均直径优选为多个部位的图像中的多个粒子的平均,例如虽没有特别限制,优选通过设为不同的20处以上的图像中的总计约2000个以上的粒子的平均等的方法来测定平均直径。
[0046]
进而,在本发明的稀土烧结磁体中,关于取向度,在将取向度设为or[%]、将上述平均结晶粒径设为d[μm]时,以满足以下的关系式(1)的方式进行调整。
[0047]
0.26
×
d 97≦or≦0.26
×
d 99
···
(1)
[0048]
通过满足这样的关系,能够得到高的br和高的h
cj
。其理由未必明确,可以推测如下。一般而言,结晶粒径的微细化通过成型、烧结前的微粉粒径的微细化而进行,但微粉粒径越微细化,微粉的表面积比例越大,因此微粉间的摩擦阻力增大,因此在磁场成型时微粉难以取向。关于该变化量,本发明人的实验表明,相对于平均结晶粒径成为4μm以下的微粉粒度,相对于1μm的结晶粒径微细化,变差0.26%。另外,已知微粉的取向度低时无法实现高的br,而另一方面,取向度过高时,h
cj
急剧降低。本发明人对它们进行综合研究,发现取向度为上述关系式(1)的范围时,可稳定地得到高的br和高的h
cj
。
[0049]
在此,对上述取向度or[%]没有特别限制,从激发原料的潜力(potential)、得到良好的br的观点出发,优选为96%以上,进一步优选为97%以上,在满足该优选的取向度和上述平均结晶粒径4μm以下的必要条件的范围内,优选实现上述关系式(1)的关系。应予说明,取向度or[%]能够通过电子束背散射衍射法(ebsd)等公知的方法进行测定。
[0050]
在本发明的稀土烧结磁体中,作为m2,可以含有选自ti、v、zr、nb、hf、ta中的1种以
上的元素。通过含有该m2,能够抑制烧结过程中的晶粒的异常晶粒生长,得到防止br降低的效果。该m2的含量没有特别限制,优选为0.5原子%以下,更优选为0.3原子%以下,进一步优选为0.2原子%以下。若m2含量超过0.5原子%,则根据情况有时m2元素形成的m
2-x相使r2t
14
x相的比率减少,从而导致br的降低。
[0051]
在含有该m2元素的情况下,没有特别限制,关于上述r、t、x和该m2的含量,在将这些原子百分率分别设为[r]、[t]、[x]和[m2]的情况下,优选满足以下的关系(3)。
[0052]
([t]/14) ([m2]
×
2)≦[x]≦([r]/2) ([m2]
×
2)
···
(3)
[0053]
即,从r2t
14
x相比率的减少对br的影响、形成r2t
17
相带来的对h
cj
的影响的观点出发,含有m2时的x的含量优选为([t]/14) ([m2]
×
2)以上,另外,考虑到r
1.1
fe4b4相这样的富x相的形成带来的r2t
14
x相比率的变动对br的影响,优选为([r]/2) ([m2]
×
2)以下。
[0054]
本发明的稀土烧结磁体除了上述元素以外,作为不可避免的杂质,有时含有h、f、mg、p、s、cl、ca等元素。在该情况下,这些不可避免的杂质的含量相对于上述磁体的构成元素和不可避免的杂质的合计,作为不可避免的杂质的合计,容许至0.1质量%以下,但优选这些不可避免的杂质的含量少。
[0055]
接着,对制造本发明的稀土烧结磁体的方法进行说明。
[0056]
制作本发明的稀土烧结磁体的工序基本上与通常的粉末冶金法相同,没有特别限制,通常包括:将原料熔解从而得到具有规定组成的原料合金的熔解工序;将原料合金粉碎从而制备合金微粉末的粉碎工序;在磁场施加中对合金微粉末进行压粉成型从而得到成型体的成型工序;和对成型体进行热处理从而得到烧结体的热处理工序。
[0057]
首先,在熔解工序中,以成为规定的组成的方式称量成为各元素的原料的金属或合金。称量至规定的组成后,例如通过高频熔解将原料熔解,进行冷却从而制造原料合金。原料合金的铸造一般采用浇铸到平模或书型模(book mold)中的熔解铸造法、或者薄带连铸法。另外,本发明也可以应用分别制作接近作为主相的r2fe
14
b化合物组成的合金和在烧结温度下成为液相助剂的富r合金,在粗粉碎后称量混合的所谓的二合金法。但是,接近主相组成的合金依赖于铸造时的冷却速度和合金组成而容易结晶α-fe相,因此,为了使组织均匀化、消除α-fe相,优选根据需要在真空或ar气氛中在700~1200℃下实施1小时以上的均质化处理。应予说明,在利用薄带连铸法制作接近主相组成的合金的情况下,也可以省略均质化。对于成为液相助剂的富r合金,除了上述铸造法以外,还可以应用所谓的液体急冷法。
[0058]
上述粉碎工序例如可以是包括粗粉碎工序和微粉碎工序的多个阶段的工序。在粗粉碎工序中,例如可以使用颚式破碎机、布朗粉碎机、针磨机或氢粉碎。在该情况下,在本发明中,没有特别限制,从实现o、n、c量的降低、得到优异的磁特性的观点出发,优选采用氢粉碎。特别是,在通过薄带连铸制作合金的情况下,优选应用氢粉碎,通常可以得到粗粉碎至0.05mm~3mm、特别是0.05mm~1.5mm的粗粉。
[0059]
在上述微粉碎工序中,可以采用使用例如n2、he、ar等非氧化性气体气流的喷射磨对上述粗粉进行粉碎的方法。在本发明中,在该微粉碎工序中,将上述粗粉微粉碎至优选0.2μm~15μm、更优选为0.5μm~10μm。稀土烧结磁体的o、n主要在微粉碎工序中混入,因此为了调整稀土烧结磁体中的o、n的含量,需要控制喷射磨气氛。稀土烧结磁体中的o含量的调整通过喷射磨气氛中的o量和露点的控制来进行,粉碎时的气氛中的o量优选为1ppm以
下,露点优选为-60℃以下。
[0060]
另外,稀土烧结磁体中的n含量例如可以利用(a)采用he、ar气体气流的喷射磨进行微粉碎的方法、(b)在n2气气流的喷射磨中引入氢来进行微粉碎的方法、或者(c)使用含有氢的粗粉用n2气气流的喷射磨进行微粉碎的方法来进行调整。在该情况下,在(b)或(c)的方法中,通过引入氢气或使用含有氢的粗粉,从而氢优先吸附于通过粉碎而产生的活性面,阻碍氮的吸附,由此能够减少稀土烧结磁体中的n量。
[0061]
在此,在原料合金的粗粉碎、微粉碎中的一者或两者的工序中,为了在作为下一工序的磁场中的成型中提高粉末的取向性,例如可以适当添加由饱和脂肪酸或其酯构成的润滑剂。此时,通常增加润滑剂的添加量对于提高取向是有效的,但通过来自润滑剂的c在稀土烧结磁体中形成大量的r-con相,从而产生h
cj
显著降低的困境。因此,在期望提高取向时,优选对采用上述(c)的方法使用含有氢的粗粉进行了微粉碎的微粉进行润滑剂的增量。认为在由该微粉制作的稀土烧结磁体中,在热处理时,内部含有的氢脱离时,通过该氢,化学吸附于微粉表面的润滑剂通过羰基还原反应等而分解,进而通过基于氢气的裂解反应而分解为挥发性高的低级醇,通过解离的作用,能够减少残留于稀土烧结磁体中的c含量。
[0062]
在上述成型工序中,施加400~1600ka/m的磁场,一边使合金粉末在易磁化轴方向上取向,一边用压缩成型机进行压粉成型。此时,优选使成型体密度为2.8~4.2g/cm3。即,从确保成型体的强度而得到良好的操作性的观点出发,成型体密度优选为2.8g/cm3以上。另外,为了提高成型后的成型体的强度,也可以添加pva、脂肪酸等粘合剂。另一方面,从得到充分的成型体强度的同时,抑制加压时的粒子的取向的紊乱而得到优选的br的观点出发,成型体密度优选为4.2g/cm3以下。另外,为了抑制合金微粉的氧化,优选在氮气、ar气等非活性气体气氛中进行成型。
[0063]
在上述热处理工序中,将在成型工序中得到的成型体在ar气等非氧化性气氛中或高真空中烧结。在通过上述(c)的方法使用含有氢的粗粉的情况下,为了抑制伴随着成型体中的氢气的放出(吸热反应)的成型体的温度降低、以及因温度差而产生的裂纹的产生,优选在非氧化性气氛或低真空气氛中在200~600℃下保持5分钟~10小时之后进行烧成。通常所述烧结优选在950℃~1200℃的温度范围内保持0.5~10小时来进行。接着,为了提高h
cj
,可以在比所述烧结温度低的温度下对得到的烧结体实施热处理。就该烧结后的热处理而言,可以进行高温热处理和低温热处理这2阶段的热处理,也可以仅进行低温热处理。对于高温热处理而言,优选在600~950℃的温度下对烧结体进行热处理,对于低温热处理而言,优选在400~600℃的温度下进行热处理。
[0064]
由此可以得到本发明的稀土烧结磁体。该稀土烧结磁体的平均结晶粒径如上所述,例如可以通过利用激光显微镜进行观察而容易地测定。具体而言,例如能够在对磁体进行磨削、镜面加工后,用nital腐蚀液或vilella腐蚀液等腐蚀液腐蚀表面后,由该面的反射电子图像通过图像解析来求出。另外,如上所述,得到的稀土烧结磁体的取向度可以通过电子束背散射衍射法(ebsd)来测定。
[0065]
另外,将所得到的稀土烧结磁体磨削成规定形状后,可以实施所谓的晶界扩散处理,即,在选自r1的氧化物、r2的氟化物、r3的氧氟化物、r4的氢氧化物、r5的碳酸盐、r6的碱性碳酸盐、r7的单质金属或合金中的1种或2种以上(r1~r7为选自稀土元素中的1种以上)的扩散源存在于上述稀土烧结磁体表面的状态下进行热处理。上述扩散源向磁体表面的固定方
法可以采用在包含粉末状的扩散源的浆料中浸渍烧结磁体从而涂布该浆料并进行干燥的浸涂法、丝网印刷法、或者溅射、pld等干式成膜法等。晶界扩散热处理的温度是比烧结温度低的温度,优选为700℃以上,对于时间没有特别限制,从得到良好的烧结磁体的组织、磁特性的观点出发,优选为5分钟~80小时,更优选为10分钟~50小时。通过该晶界扩散处理,使粉末中所含的上述r1~r7扩散到磁体中,能够实现h
cj
的进一步增大。应予说明,通过该晶界扩散而引入的稀土元素,为了便于说明,虽如上所述设为r1~r7,但在晶界扩散后,均包含在本发明稀土烧结磁体中的上述r成分中。另外,虽无特别限制,作为包含该r1~r7的上述扩散源,优选使用含有hr(hr为选自dy、tb及ho中的1种以上的元素)的金属、化合物或金属间化合物,由此能够更有效地实现h
cj
的增大。
[0066]
应予说明,本发明的稀土烧结磁体只要满足上述元素组成和上述关系式(1)即可,优选进一步满足上述关系式(2)或(3),作为上述r元素,不一定需要包含通过上述晶界扩散而引入的r,但由于可以得到更良好的h
cj
,可以更良好地实现兼顾高br和高h
cj
的本发明的目的,因此优选包含通过上述晶界扩散而引入的r。在该情况下,通过晶界扩散而引入上述r1~r7,已知由此得到的磁体中,r浓度显示出特征性的浓度分布。具体而言,已知赋予了扩散源的磁体表面处的上述r元素的浓度(re)与磁体中心部的上述r的浓度(rc)为re>rc的关系。
[0067]
实施例
[0068]
以下,示出实施例、比较例,更具体地说明本发明,但本发明并不限定于下述实施例。
[0069]
[实施例1~3]
[0070]
将nd金属、pr金属、dy金属、硼铁合金、电解co、al金属、cu金属、ga金属、si金属、锆金属及电解铁(金属均为纯度99%以上)以成为规定的比例的方式称量
·
配合,熔解,通过薄带连铸法进行铸造,得到厚度0.2~0.4mm的薄片状的原料合金。使得到的薄片状的原料合金在氢加压气氛下氢脆化,由此得到粗粉碎粉。接着,在得到的粗粉碎粉中,相对于粗粉碎粉100质量%以表1所示的比例添加、混合作为润滑剂的硬脂酸后,使用气流式粉碎机(喷射磨装置),在氮气流中进行干式粉碎,得到表1所示的粉碎粒径(d
50
)的微粉碎粉(合金粉末)。应予说明,粉碎粒径(d
50
)为利用气流分散法的激光衍射法得到的体积基准中值粒径。
[0071]
将该微粉碎粉在非活性气体气氛中填充到成型装置的模具中,在15koe(1.19ma/m)的磁场中进行取向,同时在与磁场垂直的方向上进行加压成型。此时的成型体密度为3.0~4.0g/cm3。将得到的成型体在ar气氛中、600℃下保持2小时后,在真空中、1040℃以上且1080℃以下(对于每个样品,选定由烧结引起的致密化充分发生的温度)进行5小时烧结,得到nd磁体原材料。得到的nd磁体原材料的密度为7.5g/cm3以上。
[0072]
对于该烧结后的磁体组织,进行利用激光显微镜的观察,测定平均结晶粒径。另外,通过ebsd测定来测定该磁体中的结晶组织的取向度。将它们的结果示于表1。另外,对于得到的nd磁体原材料,使用高频电感耦合等离子体发光分光分析法(icp-oes)进行金属成分分析,同时通过红外线吸收气体分析进行氧、碳、氮的分析。将结果示于表2。应予说明,表2中记载的值为质量%。另外,将该nd磁体原材料加工为15mm
×
7mm
×
12mm的尺寸的长方体形状,制成样品,通过bh示踪仪测定br、h
cj
。将结果示于表3。
[0073]
将该nd磁体原材料加工成20mm
×
20mm
×
2.2mm的尺寸的长方体形状后,浸渍于平
均粒径0.5μm的氧化铽粒子以质量分数50%与乙醇混合而成的浆料中,涂布该浆料,使其干燥,在nd磁体原材料表面形成氧化铽的涂膜。接着,将形成有涂膜的nd磁体原材料在真空中以950℃加热5小时后,实施以20℃/分钟的冷却速度冷却至200℃的高温热处理,使铽晶界扩散。接着,在450℃下加热2小时后,实施以20℃/分钟的冷却速度冷却至200℃的低温热处理,得到nd烧结磁体。将得到的nd烧结磁体的中心部切成6mm
×
6mm
×
2mm的尺寸的长方体形状,通过脉冲示踪器进行h
cj
的测定。将结果示于表3。应予说明,在表3中,将满足本发明的规定的要素表示为
○
,将不满足的要素表示为
×
。
[0074]
[比较例1]
[0075]
以与实施例1同样的步骤制作薄片状的原料合金。使该合金在氢加压气氛下氢脆化之后,进行400℃、4小时的加热处理,进行合金的脱氢化处理。由得到的粗粉碎粉以与实施例1同样的步骤进行微粉碎、成型、烧结、扩散处理,与实施例1同样地测定粉碎粒径、晶体粒径、取向度、组成、晶界扩散处理前的br和h
cj
、晶界扩散处理后的h
cj
。将结果示于表1~3。
[0076]
[对比例2、3]
[0077]
以与实施例1同样的步骤进行磁体的制作。此时,如表1所示改变润滑剂(硬脂酸)的添加量和粉碎粒径。与实施例1同样地,将粉碎粒径、结晶粒径、取向度、组成、晶界扩散处理前的br和h
cj
、晶界扩散处理后的h
cj
的测定结果示于表1~3。
[0078]
[表1]
[0079][0080]
[表2]
[0081] ndprfecocualzrsigabonc实施例124.16.566.30.50.20.10.20.10.810.080.020.05实施例224.26.566.20.50.20.10.20.10.810.080.030.05实施例324.36.566.10.50.20.10.20.10.810.080.030.05比较例124.16.566.30.50.20.10.20.10.810.150.060.13比较例224.36.666.10.50.20.10.20.10.810.060.040.03比较例324.36.666.10.50.20.10.20.10.810.060.030.04
[0082]
(wt%)
[0083]
[表3]
[0084][0085]
如表3中所示,满足本发明的氧、氮、碳的含有率以及上述关系式(1)的条件的实施例1~3的磁体均得到高的br、h
cj
、晶界扩散后h
cj
。另一方面,如表2中所示,比较例1的磁体的氧、氮、碳的含有率高,因此烧结后的h
cj
小,另外,晶界扩散处理带来的h
cj
增大效果也小,未得到充分的h
cj
矫顽力。另外,比较例2的磁体不满足上述关系式(1),润滑剂添加量少,因此磁体的取向低,未得到充分的br。进而,比较例3的磁体的结晶粒径大,晶界扩散处理前磁体的h
cj
低,因此虽然晶界扩散处理带来的h
cj
增大效果大,但与实施例1~3相比,h
cj
差。
[0086]
如上所述,实施例1~3中得到的本发明涉及的稀土烧结磁体的晶界扩散后的h
cj
超过27koe,能够用于例如电动汽车等要求高耐热性的用途。另外,得到了br也超过13.7kg的特性,能够使例如马达等小型化。
再多了解一些
本文用于企业家、创业者技术爱好者查询,结果仅供参考。