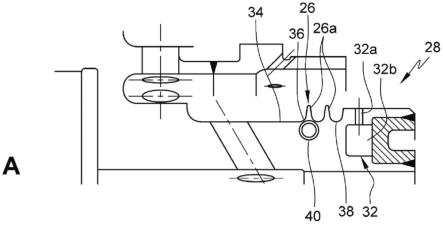
1.技术领域为飞机的引擎的燃烧室中的燃料注入装置。
背景技术:
2.参考图1,例如涡轮引擎等一些涡轮机1包括气体发生器10,所述气体发生器包括在上面安装注入轮14的旋转轴杆12,因此注入轮本身是可旋转的。
3.注入轮具有通向燃烧室18的多个孔口16。以此方式,注入轮在旋转时将燃料离心地喷射到燃烧室18中。参考图2,涡轮机还包含燃料供应轨道20,其是具有安装在气体发生器10的轴杆12周围的旋转形状的固定部分。燃料供应轨道20将燃料递送到注入轮。因此,燃料供应轨道20包括通向腔24或环形喷射腔室的内部燃料回路22。为了确保注入轮14和燃料供应轨道20之间的密封,提供例如曲径密封件26等多个动态密封件26。现有技术水平众所周知的此类型的密封件26包括环形齿26a,其由燃料供应轨道20和注入轮14中的一个承载且在注入轮14和燃料供应轨道20中的另一个的可磨耗环形部分上摩擦。
4.然而,常常发生在环形齿26a之间形成焦炭的固体沉积物的情况,因此导致注入轮14和燃料供应轨道20之间的摩擦。摩擦可能增加直至气体发生器轴杆完全被阻挡且引擎无法启动。
5.如果启动困难,则操作者执行涡轮机械维护手册中描述的故障处理操作。这些研究通常冗长且不太有效,因为检测启动困难的原因(在此情况下,动态接头中的焦化,实际上许多其它原因也是可能的)可能要花费很长时间。一旦已找到原因,就清洁引擎上的轨道,或移除轨道以进行清洁或更换。这些操作意味着涡轮机及因此其所安装的飞机始料未及地无法使用,这可能进一步需要取消一个或多个所规划的飞行任务。因此,这些操作意味着相当大的成本。
6.因此,重要的是,限制焦炭在环形密封件中形成从而提供注入轮和燃料供应轨道之间的密封件。
7.本发明旨在以简单、可靠且便宜的方式弥补这些缺点。
技术实现要素:
8.因此,本文涉及一种用于将燃料供应到气体发生器的燃烧室的装置,其包括:
[0009]-燃料注入轮,其用于将燃料注入到燃烧室中,
[0010]-燃料供应轨道,其包括内部燃料回路,所述内部燃料回路具有将燃料供应到形成于轨道和注入轮之间的环形喷射腔室的燃料排出构件,
[0011]-至少一个动态环形密封件,其适于提供燃料供应轨道的环形面和注入轮之间的密封件,
[0012]
特征在于,燃料供应轨道的燃料回路包括径向布置在动态环形密封件处的环形燃料流部分。
[0013]
不同于现有技术,所述燃料回路具备正好布置在动态环形密封件处的环形部分,
这允许通过环形密封件处的燃料循环降低温度(通常在150℃以下)且因此防止焦炭的形成。当密封件包括环形齿时,防止形成于环形齿之间的环形空间中的焦炭积聚。因此可维持涡轮机的标称操作条件,因为不存在马达轴杆阻滞的风险。术语“环形部分”不指代360
°
成型部分,如将从具体实施方式显而易见。
[0014]
在一个实施例中,所述环形部分包括至少第一匝,其径向布置在动态密封件内部且向下游连接到燃料排出构件。此第一匝具有连接到上游燃料通道的上游端,且向下游连接到燃料排出构件。
[0015]
并且,所述第一匝可形成于动态密封件的第一轴向端附近,所述第一轴向端沿着密封件与布置于燃料排出构件附近的第二端相对地布置。第一匝的此定位允许环形密封件的第一端(其是最容易形成焦炭的部分)冷却。
[0016]
此外,所述环形部分可包括至少一个第二匝,其轴向布置在第一匝和环形密封件的第二端之间,且在气流方向上遵循第一匝。
[0017]
环形密封件可具有轴向范围l,所述第一匝在-l/2和l之间轴向延伸,其中在密封件的第一轴向端处取为原点,且从第一端朝向第二端取为正方向。
[0018]
所述环形部分可连接到燃料排出构件,所述燃料排出构件包括喷射腔室中的多个燃料排出端口。
[0019]
所述燃料排出构件可包括向上游连接到所述环形部分的一个或多个周向延伸管道。
[0020]
轨道的环形面可以是径向外环形面,燃料回路的所述环形部分径向布置在所述径向环形面内。
[0021]
根据另一特征,所述环形燃料流部分可径向布置在环形密封件内部或径向布置在环形密封件外部。
[0022]
环形密封件可包括彼此轴向间隔的环形齿,所述环形齿由燃料供应轨道和注入轮中的一个承载且适于摩擦地啮合注入轮和燃料供应轨道中的另一个的可磨耗环形部分。
[0023]
所述径向环形部分可径向布置在环形齿的内部或外部。
[0024]
本发明还涉及一种包括例如上文描述的装置的涡轮机。
附图说明
[0025]
[图1]是涡轮机的总图,其中注入轮“14”与引擎轴线“12”和环形燃烧室“18”集成,以及
[0026]
在装备有燃料注入轮的燃气涡轮机的情况下,在[图2]中展示工作原理的示意性表示,如上文所描述,
[0027]
[图3]表示根据本公开的第一实施例,此图包括分别标注为图3a和图3b的两个部分a和b,图3a和图3b分别展示轨道的轴向截面和外部视图,箭头示意性地示出燃料流,
[0028]
[图4]是图3的替代实施例的3d表示(燃料回路的椭圆形横截面),
[0029]
[图5]表示根据本公开的第二实施例,此图包括分别标注为图5a和图5b的两个部分a和b,图5a和图5b分别呈现轨道的轴向截面(部分a)和外部视图(部分b),箭头示意性地表示燃料流,
[0030]
[图6]以轴向截面展示第三实施例(红色矩形示意性地表示燃料可在其中流动的
腔),
[0031]
[图7]表示根据本公开的第四实施例,此图包括分别标注为图7a和图7b的两个部分a和b,图7a和图7b分别展示轨道的轴向截面和外部视图,箭头示意性地表示燃料流。
具体实施方式
[0032]
现在参考图3,其展示与图2中所展示相同或类似的既定与注入轮14协作的燃料供应轨道28。燃料供应轨道28包括内部燃料回路30,所述内部燃料回路具有将燃料供应到喷射腔室的燃料排出构件32。燃料回路由粗线表示,且流动方向由箭头表示。燃料排出构件32包括不能延伸经过360
°
的环形管道32b,此管道连接到在涡轮机的轴线周围均匀间隔开的燃料排出端口32a。环形管道32b包括第一周向管道32b1和第二周向管道32b2。燃料回路30在图3b中示意性地展示。
[0033]
燃料供应轨道28包括既定与由可磨耗材料制成的环(未图示)协作的径向外环形面34,径向环形齿或舌状物26a从所述径向外环形面延伸。如此形成的动态密封件包括第一端36和第二端38,第二端38布置在燃料排出构件32附近,而第一端36相对地定位。
[0034]
为了避免在第一端处形成焦炭,燃料回路30包括环形部分40,其正好形成在环形密封件26处,即,轴向位于环形密封件26处,且在此情况下,径向位于环形密封件26内部(示意性地,燃料回路展示为具有圆形横截面,但椭圆形横截面也是可能的,如图4中所展示)。更确切地说,此环形部分40由第一匝形成,其上游端连接到燃料供应通道42,且其下游端连接到环形部分40或第一匝。可以看到,第一匝40的下游端和环形管道32b之间的连接以大体上处于后者的中间的角度作出以便减少环形管道中的压力损失。此第一匝40形成于环形密封件26的第一端36附近。因此,来自喷射腔室24的任何潜在燃料反流不会导致焦炭形成,因为环形密封件26的第一端36的环形齿26a处的温度相比于现有技术降低。
[0035]
图4展示根据图3中展示的实施例的替代实施例的燃料供应轨道44的三维视图。在此视图中,第一匝46具有轴向或纵向维度(即,椭圆形且非圆形横截面),即,沿着燃气涡轮机的轴线。在此情况下,在环形密封件26具有轴向范围l的情况下,第一匝46轴向位于-l/2和l之间,其中在密封件26的第一轴向端36处取为原点,且从第一端36朝向第二端38取为正方向。此匝46向上游从密封件26的第一端36轴向延伸到其下游端。
[0036]
图5a是供应轨道48的第二实施例,其中环形部分50包括在气流方向中向下游连接到第二匝50b的第一匝50a,此第二匝50b径向形成在环形密封件26内。第二匝50b的下游端连接到燃料排出构件32。如前所述,第二匝50b的下游端和环形管道32b之间的连接以大体上处于后者的中间的角度作出以便减少管道中的压力损失。
[0037]
在操作中,燃料流经第一匝50a且接着流经第二匝50b,且接着同时流经第一周向管道32b1和第二周向管道32b2,如图5b中所示出。在此第二实施例中,应了解,第一匝50b1和第二匝50b2一起形成环形燃料流部分50,用于降低动态环形密封件26的温度。
[0038]
图6展示燃料供应轨道52的第三实施例,其中环形密封件26的冷却环形部分54由环形燃料排出管道32的一部分的径向位于环形密封件26内的轴向延伸部形成。
[0039]
图7展示燃料供应轨道56的第四实施例,其中燃料供应通道42的下游端连接在包括第一周向管道60a和第二周向管道60b的环形管道60的中点58处,所述第一周向管道和第二周向管道在操作中形成环形密封件26的冷却环形部分。第一周向管道60a的下游端连接
到周向地延伸到中点58的第三周向管道62。第二周向管道60b的下游端连接到周向地延伸到中点58的第四周向管道64。
[0040]
应了解,第一60a和第二60b周向管道的下游端不彼此连通。在操作中,燃料流经燃料供应通道42,且接着分成第一周向管道60a中且接着第三周向管道62中的第一燃料流,并分成在周向管道60b中且接着在第四周向管道64中流动的第二燃料流。
再多了解一些
本文用于企业家、创业者技术爱好者查询,结果仅供参考。