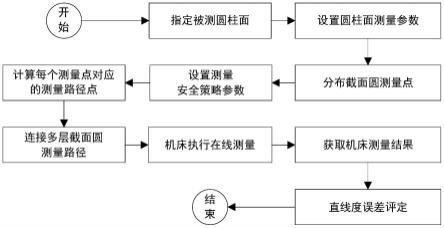
1.本发明涉及机械测量技术领域,具体涉及一种基于在线测量的圆柱面直线度误差评定方法及系统。
背景技术:
2.圆柱面作为机械产品上常见的几何特征,其加工质量影响到产品整体的装配精度或运动精度,在多数情况下需要对其轴线的直线度误差进行评定,判断圆柱面的加工质量是否满足设计的公差要求。
3.目前对机械产品上圆柱面的直线度测量及评定大多由专业测量技术人员借助相关量具或测量仪器进行手工测量或半自动化测量,后续再对测量数据进行分析计算,得到评定结果。对于测量精度要求更高的产品往往采用三坐标测量机床进行检测,直接获取误差评定结果。人工检测和三坐标检测方式分别存在着效率低下和成本过高的问题。对于大型、不宜搬运的工件采用摄影测量的方法进行直线度误差评定。
4.人工测量及误差评定较高地依赖专业人员的技能水平和经验积累,测量过程存在较大的测量不确定度,并且测量精度和效率都不高,甚至在某些情况下操作者的失误会造成对产品合格与否的误判;而三坐标测量机作为专业的检测设备,其价格昂贵、测量成本较高,并且对于加工工序集中的机械产品若交由三坐标测量,不可避免地存在工件在加工机床与测量机床之间反复拆卸、装夹定位的情况,从而影响产品整体的生产效率。此外,摄像测量技术主要应用于一些特殊对象,不适宜对机加工产品进行高精度的检测。
技术实现要素:
5.本发明的目的是提供一种基于在线测量的圆柱面直线度误差评定方法及系统,精度高,且无需反复拆卸、装夹,大大提高生产效率。
6.为了解决上述技术问题,本发明提供了基于在线测量的圆柱面直线度误差评定方法,包括以下步骤:
7.s1、导入包含圆柱面特征的工件三维模型,指定欲评定其直线度误差的被测圆柱面;
8.s2、设置被测圆柱面测量参数,所述测量参数包括截面圆的层数和每层截面圆测量点的个数;
9.s3、分布截面圆测量点:计算每层截面圆相对于圆柱上端面的距离,根据设置的每层截面圆测量点的个数,对每个截面圆圆弧曲线进行等距采样,得到离散在截面圆上的测量点;
10.s4、设置测针参数和安全策略参数,计算所有测量点对应的测量路径及其测量路径之间的连接顺序;
11.s5、驱动机床按规划好的测量路径对目标圆柱面进行在线测量;
12.s6、获取每层截面圆测量点的实测值,并对实测值进行拟合操作,得到直线度误差
评定结果。
13.作为本发明的进一步改进,所述步骤s2中设置被测圆柱面测量参数还包括以下步骤:
14.设置该被测圆柱面是内圆柱面还是外圆柱面;
15.设置测量点截面圆的层数la,每层截面圆测量点的个数n,首层测量点截面圆到圆柱上端面的距离df,末层截面圆测量点到圆柱下端面的距离db。
16.作为本发明的进一步改进,所述步骤s3中分布截面圆测量点具体包括以下步骤:
17.s31、根据圆柱的长度l和设置的截面圆的层数la、首层测量点截面圆到圆柱上端面的距离df、末层截面圆测量点到圆柱下端面的距离db,计算每层截面圆到圆柱上端面的距离di,计算公式为:di=df (i-1)
×
(h-d
f-db)/(l
a-1),i=1,2,
…
,la;
18.s32、提取圆柱面的上端面圆的圆弧线,依次将其沿圆柱面的轴线方向平移di距离,得到每层截面圆的测量曲线ci,i=1,2,
…
la;
19.s33、根据设置的每层截面圆测量点的个数n,在测量曲线ci上等间距分布设置测量点。
20.作为本发明的进一步改进,所述测针参数包括测头半径r,所述安全策略参数包括每层截面圆测量点的安全距离d和回退距离e。
21.作为本发明的进一步改进,所述步骤s4还包括根据测针参数和安全策略参数计算测量路径点,连接测量路径点得到所有测量点对应的测量路径。
22.作为本发明的进一步改进,所述计算测量路径点具体包括以下步骤:
23.s411、将每层截面圆的测量点pi投影到圆柱面上,根据设置的圆柱面是内圆柱面还是外圆柱面取所在位置的圆柱面法矢ni,根据测头半径r,计算测量点pi对应的测头球心点p
ci
,计算公式为p
ci
=pi r
×
ni;
24.s412、根据设置的测量安全距离d,计算该测量点pi对应的测量安全点p
di
,计算公式为p
di
=p
ci
d
×
ni;
25.s413、依次对所有的截面圆测量点执行所述步骤s411和步骤s412,得到所有测量点对应的测头球心点和安全点。
26.作为本发明的进一步改进,所述连接测量路径点具体包括以下步骤:
27.s421、对于每层截面圆的测量点,其测量时测针方向矢量固定为v,根据设置的回退距离e、计算测量路径中的回退点p
ei
,计算公式为p
ei
=p
di
e
×
v;
28.s422、按照进入点-安全点-测量点-安全点-回退点的顺序连接,得到测量点pi的测量路径,即p
ei-p
di-p
ci-p
di-p
ei
;
29.s423、重复执行步骤s421、s422计算所有截面圆测量点的测量路径,每层截面圆的内部的测量点的测量路径按顺时针或逆时针方向依次连接,除末层截面圆外,每层截面圆的末尾测量点的测量路径与下方邻近层的截面圆的首测量点的测量路径连接,即形成所有截面圆的测量路径。
30.作为本发明的进一步改进,所述步骤s6具体包括以下步骤:
31.s61、通过最小二乘法分别对每层截面圆测量点的实测值进行拟合,得到最小二乘拟合圆;
32.s62、提取每层截面圆对应的最小二乘圆的圆心点,通过最小区域法将这些圆心点
拟合成最小区域直线;
33.s63、分别计算每层截面圆对应的最小二乘圆的圆心点到最小区域直线的距离di,求得这些距离的最大值d
max
,则所测量的圆柱面的直线度误差dev=2
×dmax
;
34.s64、将计算得到的直线度误差值dev与设计公差值进行比较,计算超差值,若超差值等于0则判定该圆柱面的直线度合格,否则判定为不合格。
35.一种基于在线测量的圆柱面直线度误差评定系统,采用如上所述的基于在线测量的圆柱面直线度误差评定方法进行圆柱面直线度误差评定。
36.作为本发明的进一步改进,所述系统包括机床,所述的基于在线测量的圆柱面直线度误差评定方法在机床上执行。
37.本发明的有益效果:本发明基于在线测量的圆柱面直线度误差评定方法,在现有的机床加工及测量系统的基础上拓展几何特征测量功能,自动规划被测圆柱面的测量路径,根据机床在线测量结果对被测圆柱面的直线度误差进行快速评定,有效地降低了人工在检测过程中引入的误差,并且避免了被测工件在加工机床与专用测量设备之间的反复搬运、拆装过程带来的时间损耗,为机械产品的直线度检测提供了一种新的低成本、高效率、高精度解决方案。
附图说明
38.图1是本发明基于在线测量的圆柱面直线度误差评定方法流程图;
39.图2是本发明分层截面圆测量点分布示意图;
40.图3是本发明分层截面圆测量路径示意图;
41.图中标号说明:1、圆柱面;11、首层测量点截面圆;12、末层截面圆。
具体实施方式
42.下面结合附图和具体实施例对本发明作进一步说明,以使本领域的技术人员可以更好地理解本发明并能予以实施,但所举实施例不作为对本发明的限定。
43.参考图1,本发明提供了一种基于在线测量的圆柱面直线度误差评定方法,包括以下步骤:
44.s1、导入包含圆柱面1特征的工件三维模型,指定欲评定其直线度误差的被测圆柱面;
45.s2、设置被测圆柱面测量参数,所述测量参数包括截面圆的层数和每层截面圆测量点的个数;
46.s3、分布截面圆测量点:计算每层截面圆相对于圆柱上端面的距离,根据设置的每层截面圆测量点的个数,对每个截面圆圆弧曲线进行等距采样,得到离散在截面圆上的测量点;
47.s4、设置测针参数和安全策略参数,计算所有测量点对应的测量路径及其测量路径之间的连接顺序;
48.s5、驱动机床按规划好的测量路径对目标圆柱面进行在线测量;
49.s6、获取每层截面圆测量点的实测值,并对实测值进行拟合操作,得到直线度误差评定结果。
50.本发明基于在线测量的圆柱面直线度误差评定技术能够对机械产品上的圆柱面进行自动测量路径规划,由软件计算测量点的分布位置和连接顺序,并生成测量程序,在与数控机床建立实时通信的基础上,将测量程序发送给机床,驱动机床对工件进行实时测量后自动获取测量数据进行分析,对直线度误差进行计算并输出评定结果。整个测量及数据分析的过程由在线测量系统完成,效率较高,无需人工干预,减轻了测量操作人员的负担。另外,产品在加工及测量过程中无需反复拆卸、装夹,大大提高了生产效率。
51.具体地,本发明包括以下步骤:
52.(1)导入step格式的并包含圆柱面1特征的工件三维模型,指定欲评定其直线度误差的圆柱面1;
53.(2)设置圆柱面1测量参数:
54.a.设置该圆柱面1是内圆柱面还是外圆柱面;
55.b.设置测量点截面圆的层数la,每层截面圆测量点的个数n,首层测量点截面圆11到圆柱上端面的距离df,末层截面圆12测量点到圆柱下端面的距离db;
56.(3)分布截面圆测量点:
57.a.根据圆柱的长度l和设置的截面圆的层数la、首层测量点截面圆11到圆柱上端面的距离df、末层截面圆12测量点到圆柱下端面的距离db,计算每层截面圆到圆柱上端面的距离di,计算公式为:di=df (i-1)
×
(h-d
f-db)/(l
a-1),i=1,2,
…
,la;
58.b.提取圆柱面1的上端面圆的圆弧线,依次将其沿圆柱面1的轴线方向平移di距离,得到每层截面圆的测量曲线ci,i=1,2,
…
la;
59.c.根据设置的每层截面圆测量点的个数n,在测量曲线ci上等间距分布测量点。如图2所示;
60.(4)设置测针参数和测量安全策略参数,包括测头半径r,每层截面圆测量点的安全距离d、回退距离e等参数;
61.(5)计算测量路径点:
62.a.将每层截面圆的测量点pi投影到圆柱面1上,根据设置的圆柱面1是内圆柱面还是外圆柱面取所在位置的圆柱面法矢ni。根据测头半径r,计算测量点pi对应的测头球心点p
ci
,计算公式为p
ci
=pi r
×
ni;
63.b.根据设置的测量安全距离d,计算该测量点pi对应的测量安全点p
di
,计算公式为p
di
=p
ci
d
×
ni;
64.c.依次对所有的截面圆测量点执行上述a、b步骤,得到所有测量点对应的测头球心点和安全点。
65.(6)连接测量路径点:
66.a.对于每层截面圆的测量点,其测量时测针方向矢量固定为v。根据设置的回退距离e、计算测量路径中的回退点p
ei
,计算公式为p
ei
=p
di
e
×
v;
67.b.按照进入点-安全点-测量点-安全点-回退点的顺序连接,得到测量点pi的测量路径,即p
ei-p
di-p
ci-p
di-p
ei
;
68.c.执行上述步骤计算所有截面圆测量点的测量路径,每层截面圆的内部的测量点的测量路径按顺时针或逆时针方向依次连接,除末层截面圆12外,每层截面圆的末尾测量点的测量路径与下方邻近层的截面圆的首测量点的测量路径连接,即形成所有截面圆的测
量路径,如图3所示;
69.(7)启动机床,按照前面步骤所规划的测量路径对目标圆柱面进行在线测量;
70.(8)机床在线测量完成后,获取每层截面圆测量点的实测值,然后进行直线度误差评定:
71.a.通过最小二乘法分别对每层截面圆测量点的实测值进行拟合,得到最小二乘拟合圆;
72.b.提取每层截面圆对应的最小二乘圆的圆心点,通过最小区域法将这些圆心点拟合成最小区域直线;
73.c.分别计算每层截面圆对应的最小二乘圆的圆心点到最小区域直线的距离di,求得这些距离的最大值d
max
,则所测量的圆柱面的直线度误差dev=2
×dmax
;
74.d.将计算得到的直线度误差值dev与设计公差值进行比较,计算超差值,若超差值等于0则判定该圆柱面的直线度合格,否则判定为不合格。
75.实施例
76.如图1-图3所示,本实施例提供一种基于在线测量的圆柱面直线度误差评定方法,对包含圆柱面1进行误差测评,具体包括以下步骤:
77.(1)导入step格式的并包含圆柱面1特征的工件三维模型1;
78.(2)设置圆柱面1测量参数:
79.a.设置该圆柱面1为外圆柱面;
80.b.设置测量点截面圆的层数la=3,每层截面圆测量点的个数n=6,首层测量点截面圆11到圆柱上端面的距离df=4mm,末层截面圆12测量点到圆柱下端面的距离db=5mm;
81.通过上述具体实施方式步骤(3)-(6),得到各测量点的测量路径及形成所有截面圆的测量路径,如图3所示;
82.(7)启动机床,按照前面步骤所规划的测量路径对目标圆柱面进行在线测量;
83.(8)机床在线测量完成后,获取每层截面圆测量点的实测值如下表1所示,然后进行直线度误差评定:
84.表1:
[0085][0086]
a.通过最小二乘法分别对每层截面圆测量点的实测值进行拟合,得到最小二乘拟合圆;
[0087]
b.提取每层截面圆对应的最小二乘圆的圆心点,通过最小区域法将这些圆心点拟合成最小区域直线;
[0088]
c.分别计算每层截面圆对应的最小二乘圆的圆心点到最小区域直线的距离di,求得这些距离的最大值d
max
,则所测量的圆柱面的直线度误差dev=2
×dmax
=0.0029mm;
[0089]
d.将计算得到的直线度误差值dev与设计公差值0.01mm进行比较,计算超差值,若超差值等于0,则判定该圆柱面的直线度合格,否则判定为不合格。
[0090]
本发明还提供了一种基于在线测量的圆柱面直线度误差评定系统,采用如上所述的基于在线测量的圆柱面直线度误差评定方法进行圆柱面直线度误差评定。
[0091]
进一步地,所述系统包括机床,所述的基于在线测量的圆柱面直线度误差评定方法在机床上执行,借助在机床上对机械产品进行在线检测的方法来改善前面所述问题,原理相同,重复之处不再赘述,即在现有的机床加工及测量系统的基础上拓展几何特征测量
功能,自动规划被测圆柱面的测量路径,根据机床在线测量结果对被测圆柱面的直线度误差进行快速评定,有效地降低了人工在检测过程中引入的误差,并且避免了被测工件在加工机床与专用测量设备之间的反复搬运、拆装过程带来的时间损耗,为机械产品的直线度检测提供了一种新的低成本、高效率、高精度解决方案。
[0092]
以上所述实施例仅是为充分说明本发明而所举的较佳的实施例,本发明的保护范围不限于此。本技术领域的技术人员在本发明基础上所作的等同替代或变换,均在本发明的保护范围之内。本发明的保护范围以权利要求书为准。
再多了解一些
本文用于企业家、创业者技术爱好者查询,结果仅供参考。