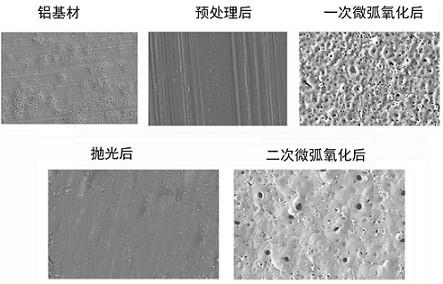
1.本发明属于铝或铝合金材料表面处理技术领域。
背景技术:
2.铝、镁、钛及其合金具有密度小,比强度高且易成型加工等优点,被广泛应用于航空、航天、交通运输和其他工业领域。但由于其耐磨性、耐蚀性差,应用受到限制,通过对其进行表面改性处理在不改变基体材料整体性能的条件下,提高耐磨性、耐蚀性对于扩大其应用领域具有重要意义。
3.微弧氧化技术(microarc oxidation mao)又称为液相等离子体电解氧化技术(plasma electrolytic oxidation, peo)是指利用微弧放电区域的瞬间高温烧结作用,在铝、镁、钛、及其复合材料表面制备陶瓷膜层的表面强化技术。其工作过程一般为:铝、镁、钛及其合金材料作为阳极试样,将其连结固定好放入特定的电解质溶液中,用钢质电解槽作为氧化系统的阴极材料,通过在阳极和阴极之间施加较高的电压值,打破传统阳极氧化电压的限制性,以期在金属表面原位生长出陶瓷基防护涂层,在此过程中,会在合金基板上形成一层高结合力和致密的韧性纳米陶瓷氧化物层。这是一种用于镁、钛、和铝金属及其合金的高压阳极氧化工艺。该方法所研制的氧化膜具有良好的介电、磨损、热、机械和抗腐蚀性能。
4.一般将 mao 膜层分为内部致密层、中间致密层和外部多孔层的三层结构,或外部多孔层和内部致密层的双层结构。微弧氧化过程中,击穿放电使得内部熔融氧化物和气体向外逸出,导致 mao 膜具有多微孔的结构。外部多孔层粗糙、多孔,比表面积较大;内部致密层决定着陶瓷膜的性能,与基体为原位结合,结合强度大,为主要强化层,可提高微弧氧化-水性聚氨酯复合膜层的抗腐蚀性能。电解液组成,浓度,反应时间以及电流密度,电压,频率等电参数的改变将会影响mao 膜层的厚度,粗糙度等,改变膜层多孔层以及致密层的厚度及结构,最终改变 mao 膜层的抗腐蚀性能与其和表面所涂装涂料的结合强度。
5.
技术实现要素:
6.本发明提供了一种微弧氧化铝合金的制备方法,通过在一次微弧氧化后进行抛光处理有效的平整待处理金属表面,保留微弧氧化层中的过渡层和部分致密层,并将其作为二次微弧氧化的基质,获得的微弧氧化膜表面形态主要为火山熔岩口的内凹形态,有效的避免了无定型或者杂孔表面形态,明显减少了表面多孔层的形成,获得的微弧氧化表面的硬度高,粗糙度ra和摩擦系数μ低,表面微弧氧化层的孔隙率低,孔道分布较为规整,稳定性高于传统微弧氧化铝合金涂层,具体而言:一种铝合金涂层,所述涂层的厚度为40-50μm,所述涂层通过两次微弧氧化处理获得,涂层表面粗糙度ra为1.5-2.5μm,厚度为40-50μm,硬度为1700-1800hv
0.5
,摩擦系数μ为0.45-0.57,所述两次微弧氧化前包括有预处理,两次微弧氧中包括有抛光蜡打磨,两次微
弧氧化后包括有后处理,所述两次微弧氧化使用的电解液成分相同,组成配比不同,包括有naoh、na2sio3、naf和p123表面活性剂和乙炔基甲醇。
7.进一步的,预处理包括有热处理、机械抛光、脱脂除油、水洗、干燥处理;所述热处理为将铝合金置于350-360℃的惰性气氛中,恒温静置处理30-40min;所述机械抛光为将铝合金依次在 60#,300#,1000#,2000#砂纸条件下逐级打磨;所述脱脂除油为使用碱性脱脂液进行脱脂除油处理,所述碱性脱脂液的成分如下:碳酸氢钠42g/l,碳酸钠38g/l,edta 5g/l,温度43℃,时间5min;所述水洗为使用45℃的去离子水冲洗;所述干燥处理为空气吹扫。
8.进一步的,两次微弧氧化过程中,一次微弧氧化参数为:微弧氧化电解液为naoh 5-7g/l、na2sio
3 11-12 g/l、naf 1-2g/l和0.2-0.5 g/lp123表面活性剂和0.7-0.9 g/l乙炔基甲醇,采用恒流模式下的双极脉冲电源,正向电流为35-37 a/dm2和负向电流为17-19 a/dm2,正向脉冲时间3-5ms,正向脉冲关停时间0.4-0.6ms,负向脉冲0.7-0.9ms,负向脉冲关停时间0.2-0.4ms,温度为15-20℃,总时长为3-5min。
9.进一步的,两次微弧氧化过程中,二次微弧氧化参数为::微弧氧化电解液为naoh 4-6g/l、na2sio
3 8-9 g/l、naf 4-5g/l和0.2-0.5 g/lp123表面活性剂和0.7-0.9 g/l乙炔基甲醇,采用恒流模式下的双极脉冲电源,正向电流为25-27 a/dm2和负向电流为8-10 a/dm2,正向脉冲时间3-5ms,正向脉冲关停时间0.8-1.2ms,负向脉冲0.9-1.1ms,负向脉冲关停时间0.3-0.5ms,温度为15-20℃,总时长为15-35min。
10.进一步的,抛光蜡打磨使用的抛光蜡由三压硬脂酸13.2wt.%、二压硬脂酸10.8wt.%、脂肪酸8.2wt.%、油酸0.9wt.%、氧化铬66.9wt.%组成。
11.进一步的,抛光蜡打磨过程中,打磨移除厚度为一次微弧氧化涂层厚度的3/4。
12.进一步的,后处理:依次用乙醇、超声清洗,和冷风吹干。
13.进一步的,铝合金的质量成分如下:si 0.7-1.1wt.%、fe 0.7-0.8wt.%、cu1.8-2.5 wt.%、mn0.4-0.8 wt.%、mg0.4-0.8 wt.%、ni 0.1-0.2wt.%、zn 0.3-0.35wt.%、ti 0.15wt.%、平衡铝。
14.铝合金整体处理步骤如下:(1)铝合金表面预处理:热处理、机械抛光、脱脂除油、水洗、干燥处理。
15.所述热处理为将铝合金置于350-360℃的惰性气氛中,恒温静置处理30-40min。
16.所述机械抛光为将铝合金依次在 60#,300#,1000#,2000#砂纸条件下逐级打磨。
17.所述脱脂除油为使用碱性脱脂液进行脱脂除油处理,所述碱性脱脂液的成分如下:碳酸氢钠42g/l,碳酸钠38g/l,edta 5g/l,温度43℃,时间5min。
18.所述水洗为使用45℃的去离子水冲洗。
19.所述干燥处理为空气吹扫。
20.(2)一次微弧氧化处理:微弧氧化电解液为naoh 5-7g/l、na2sio3 11-12 g/l、naf 1-2g/l和0.2-0.5 g/lp123表面活性剂和0.7-0.9 g/l乙炔基甲醇,采用恒流模式下的双极脉冲电源,正向电流为35-37 a/dm2和负向电流为17-19 a/dm2,正向脉冲时间3-5ms,正向脉冲关停时间0.4-0.6ms,负向脉冲0.7-0.9ms,正向脉冲关停时间0.2-0.4ms,温度为15-20℃,总时长为3-5min,获得的厚度为20-25μm。
21.(3)抛光蜡打磨、除油脱脂、热水洗、干燥:所述抛光蜡由三压硬脂酸13.2wt.%、二压硬脂酸10.8wt.%、脂肪酸8.2wt.%、油酸0.9wt.%、氧化铬66.9wt.%组成,抛光移除厚度为一次微弧氧化厚度的3/4;所述除油脱脂为使用碱性脱脂液进行脱脂除油处理,所述碱性脱脂液的成分如下:碳酸氢钠42g/l,碳酸钠38g/l,edta 5g/l,温度43℃,时间15min。
22.所述干燥为空气吹扫。
23.(4)二次微弧氧化处理:微弧氧化电解液为naoh 4-6g/l、na2sio3 8-9 g/l、naf 4-5g/l和0.2-0.5 g/lp123表面活性剂和0.7-0.9 g/l乙炔基甲醇,采用恒流模式下的双极脉冲电源,正向电流为25-27 a/dm2和负向电流为8-10 a/dm2,正向脉冲时间3-5ms,正向脉冲关停时间0.8-1.2ms,负向脉冲0.9-1.1ms,正向脉冲关停时间0.3-0.5ms,温度为15-20℃,总时长为15-35min。
24.(5)后处理:依次用乙醇、超声清洗,和冷风吹干。
25.所述铝合金的质量成分如下:si 0.7-1.1wt.%、fe 0.7-0.8wt.%、cu1.8-2.5 wt.%、mn0.4-0.8 wt.%、mg0.4-0.8 wt.%、ni 0.1-0.2wt.%、zn 0.3-0.35wt.%、ti 0.15wt.%、平衡铝。
26.本发明首先对铝合金进行表面预处理:处理方式依次包括有热处理、机械抛光、脱脂除油、水洗、干燥处理,其目的主要为释放热应力,提高涂层与基材的结合力,减少金属晶粒缺陷;平整金属基材表面,除去氧化膜;表面油脂导致的电解液与基材的接触不良,导致氧化层厚度上凹凸不平,最终获得平整、应力低、晶型高、洁净的待处理基材。
27.然后对经过表面处理的铝合金进行一次微弧氧化:微弧氧化电解液为naoh 5-7g/l、na2sio
3 8-12 g/l、naf 1-2g/l和0.2-0.5 g/lp123表面活性剂和0.7-0.9 g/l乙炔基甲醇,采用恒流模式下的双极脉冲电源,正向电流为35-37 a/dm2和负向电流为17-19 a/dm2,正向脉冲时间3-5ms,正向脉冲关停时间0.4-0.6ms,负向脉冲0.7-0.9ms,正向脉冲关停时间0.2-0.4ms,温度为15-20℃,总时长为3-5min,获得的厚度为20-25μm。
28.不论是一次微弧氧化,还是二次微弧氧化,均是对电解参数的调节,其中电解液的成分、正向电流、关停时间等都、微弧氧化处理时间,决定了微弧氧化过程中的能量供应情况,将大程度的影响微弧氧化膜层形成过程中膜层的击穿频率,放电通道的持续时间以及放电过程中的最高温度等,从而进一步影响微弧氧化膜层的孔隙率,相组成,粗糙度以及耐蚀性等等。
29.微弧氧化使用的碱性电解液体系主要为硅酸盐,磷酸盐以及铝酸盐等硅酸钠在各种电解液体系下膜层的生长速率最快,而不同添加剂的加入也可以影响微弧氧化膜层的组成及抗腐蚀性能,浓度变化会导致电解液导电性酸碱性,稳定性等的改变,影响的起弧时间,起弧电压,火花的尺寸,数量,寿命及分布等从而影响微弧氧化膜层的厚度,结构,影响双膜层体系的结合强度及抗腐蚀性能。硅酸钠浓度的增大能够促进铝合金样品表面发生弧光放电,降低微弧氧化起弧过程的能量消耗。硅酸钠的浓度越高,其获得的表面粗糙度越高,因为一次微弧氧化膜会后续抛光移除,总体上一次微弧氧化液中的硅酸钠的浓度na2sio3 11-12 g/l要高于二次微弧氧化的na2sio3 8-9 g/l浓度,经过一次微弧氧化后,表面的粗糙度ra为7-8μm。
30.氟化钠的加入能够使膜厚增加,这是因为加入氟化钠后,可以更容易产生火花放电现象,前期电压上升速率增加,起弧电压下降,并且可以抑制阳极的过度溶解,使得膜厚
增加,总体上一次微弧氧化液中的氟化钠naf 1-2g/l的浓度要低于二次微弧氧化氟化钠naf 4-5g/l的浓度。
31.电解液中主成膜剂的浓度对陶瓷膜层的厚度影响显著。主成膜剂浓度较低时,容易在铝合金表面形成钝化膜,电击穿将会变得十分困难,对膜层的生长不利;当拥有较高浓度的主成膜剂时,会增强溶液导电性能,产生更多的放电中心通道,在电子不断进入微孔下会使得膜层厚度不断增加;但主成膜剂浓度达过高时,电击穿也会变得更加困难,从而引起起弧电压降低,导致弧光放电现象,抑制微弧氧化效果,甚至引起局部电流过大而造成烧蚀情况。当 naoh 浓度增大时,粗糙度和孔隙率也在略微增大。随着 naoh 浓度的增加,离子浓度增加,溶液的电导率增大,导电性增强,分配在试样表面的电压峰值就大,电流击穿能力增强,导致成膜速率增加。同时,oh-参与阳极化学反应,浓度增大时,会促进阳极电子转移,从而增加氧化物生成速率,增大成膜速率。
32.p123表面活性剂为非离子表面活性剂,主要是改善电解液的表面张力,改善基材与电解液的接触形态,乙炔基甲醇为缓蚀剂,表面对基材的腐蚀,同时有一定的涂层平整作用。
33.微弧氧化时间:反应时间增加时,膜层厚度的增加速率也会增大,推测可能与随着反应的进行,孔隙率和粗糙度在逐渐增加,使得同样氧化物生成速率条件下膜层厚度速率生长加快有关。微弧氧化的处理时间,在微弧氧化处理过程中,随着时间的增加,微弧氧化膜层的厚度不断增大,由此带来膜层阻抗的升高将导致膜层放电通道减少,并且在单次放电过程中的电荷量增大,击穿电压不断提高。随着单次击穿愈发变得困难,膜层生长的能耗也不断增加。而且平均每次放电会产生更多的热量,反应生成的熔融物质和高热量使得原膜层融化了的更多的熔融物质从放电通道内喷涌而出,在与电解液接触冷却后形成更加粗糙的表面积和较大的孔隙率。
34.关停时间:一次微弧氧化中正向脉冲关停时间0.4-0.6ms,负向脉冲关停时间0.2-0.4ms,二次微弧氧化中正向脉冲关停时间0.8-1.2ms,负向脉冲关停时间0.3-0.5ms,可以看出二次微弧氧化的关停时间大于一次微弧氧化的关停时间,因为一次微弧氧化的时间短,因此一次微弧氧化膜层表面放电现象相对较弱,而二次微弧氧化的膜层表面放电现象相对更为剧烈,增加关停时间可以使得喷射出的氧化物更充分冷却而不是被下次放电所熔融,有利于形成规整的,平整的孔道,避免形成无定型的,疏松的,粗糙的孔道。
35.电流密度对膜层的微观形貌,宏观特征等影响较大,电流密度增大时微弧氧化膜层生长速率加快,放电通道中出现更加剧烈的放电现象,熔融氧化物更剧烈的熔融,冷却并堆积到放电通道的“火山口”周围,如需使得微弧氧化膜层的疏松层较少,应采用较小电流密度下制备微弧氧化膜层。因此一次微弧氧化的电流密度要明显高于二次微弧氧化的电流密度。
36.抛光蜡打磨的目的:如前述,微弧氧化膜的由下至上为过渡层-致密层和多孔层,在微弧氧化过程中,微弧氧化膜层厚度增加,粗糙度增加,并且放电通道会减少,单次放电的电流增大随着单次击穿变得困难,膜层生长的能耗增加,膜层变粗糙,其中主要的内阻能耗源于致密层和过渡层,当致密层和过渡层不平整时,会导致热量释放不均一,放电不统
一,如较厚的位置难以击穿放电,而较薄的位置容易发生氧化,通过一次微弧氧化后的抛光处理,完全除去多孔层,切削部分的致密层,使得获得的表面微弧氧化层厚度在截面方向明显平整,在后续微弧过程中均化放电通道,有利于获得平坦均匀的微弧氧化火山口,外围氧化物积累少,无定型或者粗糙孔道较少,裂纹少,整体空隙率较低,因此对应的致密度和耐腐蚀、硬度效果好, 抛光移除厚度为一次微弧氧化厚度的3/4。
37.这里,需要注意一篇专利文献:cn107604411a公开了一种铝合金微弧氧化处理方法,其特征在于,包括以下步骤:(1)对铝合金进行表面打磨抛光后,依次用乙醇超声清洗15-20min,蒸馏水超声清洗15-20min,然后用洁净干燥的压缩空气吹干;(2)将步骤(1)处理后的铝合金放入稀土微弧氧化电解液中,进行第一次微弧氧化处理,在铝合金表面原位生长一层陶瓷膜层;(3)将步骤(2)微弧氧化后的铝合金进行第二次表面打磨抛光,用蒸馏水超声清洗至水膜连续均匀、不断裂为止,然后用洁净干燥的压缩空气吹干;(4)将步骤(3)处理后的铝合金放入稀土微弧氧化电解液中,进行第二次微弧氧化处理,继续在铝合金表面原位生长一层均匀致密陶瓷膜层。
38.该文献的有益技术效果为“通过将铝合金在稀土混合盐溶液中进行微弧氧化,可以在铝合金表面生长出均匀致密的陶瓷膜层。该方法的处理过程简单,制备的陶瓷膜层的硬度高。”所述文献没有任何的附图记载,对于其技术效果是源于一次微弧氧化后的抛光处理,还是源于稀土混合盐也没有记载,此外,对于抛光程度也没有记载,因此本发明将该文献实施例1作为对比例1进行试验,对其效果进行sem表征。
39.有益技术效果(1)本发明通过在一次微弧氧化后进行抛光处理,有效的获得平整的、低粗糙度表面,低摩擦系数表面。
40.(2)通过在电镀液中增加p123和乙炔基甲醇进一步改善微弧氧化表面形态,获得的规整表面,助于膜层质量的提升,膜层更加致密、平整,参见附图2。
附图说明
41.附图1 本发明实施例2不同处理步骤对应的铝材的sem图。
42.附图2本发明实施例和对比例对应铝材的sem图。
具体实施方式
43.下面结合具体实施例进一步说明本发明的技术方案,本发明实施例和对比例使用的待处理铝合金的质量成分如下:si 0.7-1.1wt.%、fe 0.7-0.8wt.%、cu1.8-2.5 wt.%、mn0.4-0.8 wt.%、mg0.4-0.8 wt.%、ni 0.1-0.2wt.%、zn 0.3-0.35wt.%、ti 0.15wt.%、平衡铝,对于部分极低浓度杂质不进行标记,不代表不存在。
44.实施例1一种铝合金涂层通过如下步骤制备获得:(1)铝合金表面预处理:热处理、机械抛光、脱脂除油、水洗、干燥处理;所述热处理为将铝合金置于350℃的惰性气氛中,恒温静置处理30min;
所述机械抛光为将铝合金依次在 60#,300#,1000#,2000#砂纸条件下逐级打磨;所述脱脂除油为使用碱性脱脂液进行脱脂除油处理,所述碱性脱脂液的成分如下:碳酸氢钠42g/l,碳酸钠38g/l,edta 5g/l,温度43℃,时间5min。
45.所述水洗为使用45℃的去离子水冲洗;所述干燥处理为空气吹扫;(2)一次微弧氧化处理:微弧氧化电解液为naoh 5g/l、na2sio3 11 g/l、naf 1g/l和0.2g/l p123表面活性剂和0.7 g/l乙炔基甲醇,采用恒流模式下的双极脉冲电源,正向电流为35a/dm2和负向电流为17 a/dm2,正向脉冲时间3ms,正向脉冲关停时间0.4ms,负向脉冲0.7ms,负向脉冲关停时间0.2ms,温度为15℃,总时长为3min。
46.(3)抛光蜡打磨、除油脱脂、热水洗、干燥:所述抛光蜡由三压硬脂酸13.2wt.%、二压硬脂酸10.8wt.%、脂肪酸8.2wt.%、油酸0.9wt.%、氧化铬66.9wt.%组成,抛光移除厚度为一次微弧氧化厚度的3/4;所述除油脱脂为使用碱性脱脂液进行脱脂除油处理,所述碱性脱脂液的成分如下:碳酸氢钠42g/l,碳酸钠38g/l,edta 5g/l,温度43℃,时间15min。
47.所述干燥为空气吹扫。
48.(4)二次微弧氧化处理:微弧氧化电解液为naoh 4g/l、na2sio3 8g/l、naf 4g/l和0.2g/lp123表面活性剂和0.7g/l乙炔基甲醇,采用恒流模式下的双极脉冲电源,正向电流为25 a/dm2和负向电流为8 a/dm2,正向脉冲时间3ms,正向脉冲关停时间0.8ms,负向脉冲0.9ms,负向脉冲关停时间0.3ms,温度为15℃,总时长为15min。
49.(5)后处理:依次用乙醇、超声清洗,和冷风吹干。
50.实施例2一种铝合金涂层通过如下步骤制备获得:(1)铝合金表面预处理:热处理、机械抛光、脱脂除油、水洗、干燥处理;所述热处理为将铝合金置于355℃的惰性气氛中,恒温静置处理35min。
51.所述机械抛光为将铝合金依次在 60#,300#,1000#,2000#砂纸条件下逐级打磨。
52.所述脱脂除油为使用碱性脱脂液进行脱脂除油处理,所述碱性脱脂液的成分如下:碳酸氢钠42g/l,碳酸钠38g/l,edta 5g/l,温度43℃,时间5min。
53.所述水洗为使用45℃的去离子水冲洗。
54.所述干燥处理为空气吹扫。
55.(2)一次微弧氧化处理:微弧氧化电解液为naoh 6g/l、na2sio3 11.5 g/l、naf 1.5g/l和0.35 g/lp123表面活性剂和0.8 g/l乙炔基甲醇,采用恒流模式下的双极脉冲电源,正向电流为36 a/dm2和负向电流为18a/dm2,正向脉冲时间4ms,正向脉冲关停时间0.5ms,负向脉冲0.8ms,负向脉冲关停时间0.3ms,温度为17.5℃,总时长为4min。
56.(3)抛光蜡打磨、除油脱脂、热水洗、干燥:所述抛光蜡由三压硬脂酸13.2wt.%、二压硬脂酸10.8wt.%、脂肪酸8.2wt.%、油酸0.9wt.%、氧化铬66.9wt.%组成,抛光移除厚度为一次微弧氧化厚度的3/4;所述除油脱脂为使用碱性脱脂液进行脱脂除油处理,所述碱性脱脂液的成分如下:碳酸氢钠42g/l,碳酸钠38g/l,edta 5g/l,温度43℃,时间15min。
57.所述干燥为空气吹扫。
58.(4)二次微弧氧化处理:微弧氧化电解液为naoh 5g/l、na2sio3 8.9 g/l、naf 4.5g/l和0.35g/lp123表面活性剂和0.8 g/l乙炔基甲醇,采用恒流模式下的双极脉冲电
源,正向电流为26 a/dm2和负向电流为9 a/dm2,正向脉冲时间4ms,正向脉冲关停时间1ms,负向脉冲1ms,负向脉冲关停时间0.4ms,温度为17.5℃,总时长为20min。
59.(5)后处理:依次用乙醇、超声清洗,和冷风吹干。
60.实施例3一种铝合金涂层通过如下步骤制备获得:(1)铝合金表面预处理:热处理、机械抛光、脱脂除油、水洗、干燥处理;所述热处理为将铝合金置于360℃的惰性气氛中,恒温静置处理40min;所述机械抛光为将铝合金依次在 60#,300#,1000#,2000#砂纸条件下逐级打磨;所述脱脂除油为使用碱性脱脂液进行脱脂除油处理,所述碱性脱脂液的成分如下:碳酸氢钠42g/l,碳酸钠38g/l,edta 5g/l,温度43℃,时间5min。
61.所述水洗为使用45℃的去离子水冲洗;所述干燥处理为空气吹扫;(2)一次微弧氧化处理:微弧氧化电解液为naoh7g/l、na2sio3 12 g/l、naf 2g/l和0.5 g/lp123表面活性剂和0.9 g/l乙炔基甲醇,采用恒流模式下的双极脉冲电源,正向电流为37 a/dm2和负向电流为19 a/dm2,正向脉冲时间5ms,正向脉冲关停时间0.6ms,负向脉冲0.9ms,负向脉冲关停时间0.4ms,温度为20℃,总时长为5min。
62.(3)抛光蜡打磨、除油脱脂、热水洗、干燥:所述抛光蜡由三压硬脂酸13.2wt.%、二压硬脂酸10.8wt.%、脂肪酸8.2wt.%、油酸0.9wt.%、氧化铬66.9wt.%组成,抛光移除厚度为一次微弧氧化厚度的3/4;所述除油脱脂为使用碱性脱脂液进行脱脂除油处理,所述碱性脱脂液的成分如下:碳酸氢钠42g/l,碳酸钠38g/l,edta 5g/l,温度43℃,时间15min。
63.所述干燥为空气吹扫。
64.(4)二次微弧氧化处理:微弧氧化电解液为naoh 6g/l、na2sio3 9 g/l、naf 5g/l和0.5 g/lp123表面活性剂和0.9 g/l乙炔基甲醇,采用恒流模式下的双极脉冲电源,正向电流为27 a/dm2和负向电流为10 a/dm2,正向脉冲时间5ms,正向脉冲关停时间1.2ms,负向脉冲1.1ms,负向脉冲关停时间0.5ms,温度为17.5℃,总时长为30min。
65.(5)后处理:依次用乙醇、超声清洗,和冷风吹干。
66.对比例1一种铝合金涂层通过如下步骤制备获得: (1)对铝合金进行表面打磨抛光后,依次用乙醇超声清洗15min,蒸馏水超声清洗15min,然后用洁净干燥的压缩空气吹干;(2)将步骤(1)处理后的铝合金放入稀土微弧氧化电解液中,进行第一次微弧氧化处理,处理温度为35℃,时间为25min,在铝合金表面原位生长一层20μm厚的陶瓷膜层,所述稀土微弧氧化电解液的成分为:12g/l硅酸钠、2g/l氟化钾、4g/l氢氧化钠、2.5g/l硝酸铈;(3)将步骤(2)微弧氧化后的铝合金进行第二次表面打磨抛光,用蒸馏水超声清洗至水膜连续均匀、不断裂为止,然后用洁净干燥的压缩空气吹干;(4)将步骤(3)处理后的铝合金放入稀土微弧氧化电解液中,进行第二次微弧氧化处理,处理温度为35℃,时间为25min,继续在铝合金表面原位生长一层20μm厚的瓷膜层,所述稀土微弧氧化电解液的成分为:12g/l硅酸钠、2g/l氟化钾、4g/l氢氧化钠、2.5g/l硝酸铈。
67.对比例2一种铝合金涂层通过如下步骤制备获得:(1)铝合金表面预处理:热处理、机械抛光、脱脂除油、水洗、干燥处理;所述热处理为将铝合金置于355℃的惰性气氛中,恒温静置处理35min。
68.所述机械抛光为将铝合金依次在 60#,300#,1000#,2000#砂纸条件下逐级打磨。
69.所述脱脂除油为使用碱性脱脂液进行脱脂除油处理,所述碱性脱脂液的成分如下:碳酸氢钠42g/l,碳酸钠38g/l,edta 5g/l,温度43℃,时间5min。
70.所述水洗为使用45℃的去离子水冲洗。
71.所述干燥处理为空气吹扫。
72.(2)一次微弧氧化处理:微弧氧化电解液为naoh 6g/l、na2sio3 11.5 g/l、naf 1.5g/l,采用恒流模式下的双极脉冲电源,正向电流为36 a/dm2和负向电流为18a/dm2,正向脉冲时间4ms,正向脉冲关停时间0.5ms,负向脉冲0.8ms,负向脉冲关停时间0.3ms,温度为17.5℃,总时长为4min。
73.(3)抛光蜡打磨、除油脱脂、热水洗、干燥:所述抛光蜡由三压硬脂酸13.2wt.%、二压硬脂酸10.8wt.%、脂肪酸8.2wt.%、油酸0.9wt.%、氧化铬66.9wt.%组成,抛光移除厚度为一次微弧氧化厚度的3/4;所述除油脱脂为使用碱性脱脂液进行脱脂除油处理,所述碱性脱脂液的成分如下:碳酸氢钠42g/l,碳酸钠38g/l,edta 5g/l,温度43℃,时间15min。
74.所述干燥为空气吹扫。
75.(4)二次微弧氧化处理:微弧氧化电解液为naoh 5g/l、na2sio3 8.9 g/l、naf 4.5g/l,采用恒流模式下的双极脉冲电源,正向电流为26 a/dm2和负向电流为9 a/dm2,正向脉冲时间4ms,正向脉冲关停时间1ms,负向脉冲1ms,负向脉冲关停时间0.4ms,温度为17.5℃,总时长为20min。
76.(5)后处理:依次用乙醇、超声清洗,和冷风吹干。
77.对比例3一种铝合金涂层通过如下步骤制备获得:(1)铝合金表面预处理:热处理、机械抛光、脱脂除油、水洗、干燥处理;所述热处理为将铝合金置于355℃的惰性气氛中,恒温静置处理35min。
78.所述机械抛光为将铝合金依次在 60#,300#,1000#,2000#砂纸条件下逐级打磨。
79.所述脱脂除油为使用碱性脱脂液进行脱脂除油处理,所述碱性脱脂液的成分如下:碳酸氢钠42g/l,碳酸钠38g/l,edta 5g/l,温度43℃,时间5min。
80.所述水洗为使用45℃的去离子水冲洗。
81.所述干燥处理为空气吹扫。
82.(2)一次微弧氧化处理:微弧氧化电解液为naoh 6g/l、na2sio3 11.5 g/l、naf 1.5g/l和0.35 g/lp123表面活性剂和0.8 g/l乙炔基甲醇,采用恒流模式下的双极脉冲电源,正向电流为36 a/dm2和负向电流为18a/dm2,正向脉冲时间4ms,正向脉冲关停时间0.5ms,负向脉冲0.8ms,负向脉冲关停时间0.3ms,温度为17.5℃,总时长为4min。
83.(3)二次微弧氧化处理:微弧氧化电解液为naoh 5g/l、na2sio3 8.9 g/l、naf 4.5g/l和0.35g/lp123表面活性剂和0.8 g/l乙炔基甲醇,采用恒流模式下的双极脉冲电源,正向电流为26 a/dm2和负向电流为9 a/dm2,正向脉冲时间4ms,正向脉冲关停时间1ms,
负向脉冲1ms,负向脉冲关停时间0.4ms,温度为17.5℃,总时长为20min。
84.(4)后处理:依次用乙醇、超声清洗,和冷风吹干。
85.对比例4一种铝合金涂层通过如下步骤制备获得:(1)铝合金表面预处理:热处理、机械抛光、脱脂除油、水洗、干燥处理;所述热处理为将铝合金置于355℃的惰性气氛中,恒温静置处理35min。
86.所述机械抛光为将铝合金依次在 60#,300#,1000#,2000#砂纸条件下逐级打磨。
87.所述脱脂除油为使用碱性脱脂液进行脱脂除油处理,所述碱性脱脂液的成分如下:碳酸氢钠42g/l,碳酸钠38g/l,edta 5g/l,温度43℃,时间5min。
88.所述水洗为使用45℃的去离子水冲洗。
89.所述干燥处理为空气吹扫。
90.(2)一次微弧氧化处理:微弧氧化电解液为naoh 6g/l、na2sio3 11.5 g/l、naf 1.5g/l和0.35 g/lp123表面活性剂和0.8 g/l乙炔基甲醇,采用恒流模式下的电源,电流为36 a/dm2,温度为17.5℃,总时长为4min。
91.(3)抛光蜡打磨、除油脱脂、热水洗、干燥:所述抛光蜡由三压硬脂酸13.2wt.%、二压硬脂酸10.8wt.%、脂肪酸8.2wt.%、油酸0.9wt.%、氧化铬66.9wt.%组成,抛光移除厚度为一次微弧氧化厚度的3/4;所述除油脱脂为使用碱性脱脂液进行脱脂除油处理,所述碱性脱脂液的成分如下:碳酸氢钠42g/l,碳酸钠38g/l,edta 5g/l,温度43℃,时间15min。
92.所述干燥为空气吹扫。
93.(4)二次微弧氧化处理:微弧氧化电解液为naoh 5g/l、na2sio3 8.9 g/l、naf 4.5g/l和0.35g/lp123表面活性剂和0.8 g/l乙炔基甲醇,采用恒流模式电源,电流为26 a/dm2,温度为17.5℃,总时长为20min。
94.(5)后处理:依次用乙醇、超声清洗,和冷风吹干。
95.如附图1所示,其中分别对应铝基材、预处理后、一次微弧氧化后、抛光后和二次微弧氧化后对应铝材的sem图,其中铝基材表面含有大量的天然多孔氧化铝,预处理后露出金属光泽,然后在其表面进行一次微弧氧化,氧化后获得的铝材表面微米孔和疏松孔道,通过抛光除去一次微弧氧化膜表面的疏松多孔层和部分致密层,留下致密层和过渡层,表面平坦,然后进行二次微弧氧化,获得的微弧氧化膜表面膜平整,孔道较为规整,尤其没有疏松的多孔孔道。如附图2所示,对比例1-4获得的微弧氧化膜表面含有众多疏松多孔孔道,表面粗糙,相比而言,实施例2获得额的微弧氧化膜表面为致密的微弧氧化层,没有疏松孔道,即相比于对比例1-4,本发明获得的微弧氧化涂层的效果更好。
96.对上述实施例2和对比例1-4进行对应的测试,对对比例1-4进行简述,其中对比例1采用的是参考文件的实施例1,对比例2与实施例2的区别在于电解液的不同,两者在表面
粗糙度、摩擦系数、磨损量(磨损量的单位为10-10
cm3(n
.
m)-1
)上没有本质区别,但是由于其中的表面活性剂和缓蚀剂的加入,一定程度上改善了微弧氧化膜表面形貌,具有对应的积极效果,对比例3中没有抛光,表面粗糙度、摩擦系数、磨损量明显恶化,进一步证明了一次微弧氧化对后续规整微弧氧化膜的积极作用,对比例4中电流恒定的电源,进一步证明了双极脉冲电流对微弧氧化膜的影响,本发明实施例2是最佳实验效果,对应的表面粗糙度、摩擦系数、磨损量、硬度分别为1.67μm、0.48、2.1310-10
cm3(n
.
m)-1
、1786 hv
0.5
。
97.以上,虽然通过优选的实施例对本发明进行了例示性的说明,但本发明并不局限于这种特定的实施例,可以在记载于本发明的保护范围的范畴内实施适当的变更。
再多了解一些
本文用于企业家、创业者技术爱好者查询,结果仅供参考。