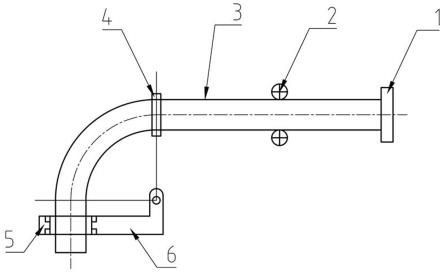
1.本发明涉及金属材料塑性加工成形领域,具体的说是一种大直径钛合金弯头成形方法。
背景技术:
2.钛合金材料具有密度小、强度高、耐蚀性强、焊接性好等优异性能,尤其在海水中的耐蚀性十分突出,被称为“海洋金属”,是海洋工程与船舶的理想金属材料。钛合金应用于船舶海水管路,可以减少管路壁厚的腐蚀设计余量,从而实现管路系统的整体减重,对于船舶系统的轻量化设计具有重要意义。
3.弯头是管系附件重要组成部分,在管路系统中应用广泛。纯钛(ta1、ta2等)材质的弯头,由于材料延伸性能好,常采用组合模具推制成形的方法。而对于钛合金材料,因其室温下强度高,流动性差,延伸率低,一般需要加热成形。在现有技术中,扩径推弯是钛合金弯头成形的主要方法。它是在专用弯头推制机上,利用加热装置对管坯加热,使管坯在轴向推力的作用下通过牛角芯棒,管坯在向前移动的过程实现扩径并弯曲成形。这一方法具有工艺简单、批量生产相同规格弯头时效率高的优点,但是成形所需的牛角芯棒模具制造困难,在弯头公称直径和弯曲半径相同的情况下,壁厚不同就必须使用不同尺寸的牛角芯棒。在实际生产不同规格/壁厚的弯头时,需要频繁更换牛角芯棒,效率低下;而对于大直径钛合金弯头的成形来说,模具的制造周期尤其长,并且成本高昂。
技术实现要素:
4.本发明的技术目的为:提供一种工序简单、成本低廉,能够快速、高效地实现直径190~457mm、壁厚5~20mm,最小相对弯曲半径为1.5d的钛合金弯头成形的工艺方法,在保证弯头成形质量的前提下,实现效率提升,成本降低。
5.本发明为解决上述技术问题所采用的技术方案为:一种大直径钛合金弯头的成形方法,具体包括以下步骤:步骤一、选取外径和壁厚与成品钛合金弯头相同,且长度比成品钛合金弯头的弧长大2~3m的钛合金管材作为基础管材;步骤二、在所选钛合金管材的内外表面均匀涂刷防氧化涂料,并对其进行晾干;步骤三、设定钛合金管材的一端为夹持端,另一端为推进端,在夹持端预留出夹持长度,并在该预留长度处沿钛合金管材的外圆周划定折弯起始线,之后,按照公式计算出理论折弯长度,在钛合金管材的推进端距离折弯起始线理论折弯长度 (10~20mm)处划定折弯终止线,制成待弯制管材,备用;公式中:l为理论折弯长度,r为成品钛合金弯头的弯曲半径,θ为成品钛合金弯头的弯曲角度;步骤四、将步骤三制得的待弯制管材装配在中频弯管机上,使中频弯管机中的夹
头夹紧待弯制管材的夹持端,中频弯管机中的顶杆顶紧待弯制管材的推进端,中频弯管机中的感应线圈与待弯制管材上的折弯起始线内外对应,开启中频弯管机,使待弯制管材的加热部位升温至720~760℃,在保持该温度条件下,利用中频弯管机中的液压驱动装置推动顶杆,使待弯制管材以25~35mm/min的推进速度不断向感应线圈方向运动,直至待弯制管材上的折弯终止线通过感应线圈,在对待弯制管材进行加热的过程中,还通过感应线圈上的小孔对其进行喷水冷却,之后,关闭中频弯管机,制得初弯制管件,备用;步骤五、将步骤四制得的初弯制管件冷却至室温,然后,沿初弯制管件上划定的折弯起始线和折弯终止线进行管材切割,并对切割后产生的端口进行修磨,制得弯制管坯,备用;步骤六、将步骤五制得的弯制管坯放入加热炉内,设置炉内加热温度为820~850℃,到达设定温度后进行保温15~20min;步骤七、取热压模具,并将其预热至200~300℃,之后,将完成预热的热压模具装配于压力机上,并保证热压模具中上模和下模的中心线对齐;步骤八、取步骤六中已完成加热的弯制管坯置于步骤七中的下模中,在弯制管坯的中部和两端口处分别装入用于辅助弯头成形的芯棒和马蹄模,之后,启动压力机,使热压模具中的上模缓慢下压,直至上模与下模完全贴合,弯制管坯于上模和下模共同组构成的型腔内被热压成目标形态,在热压的过程中,应保证弯制管坯的表面温度不低于720℃,制得热压成形管件,备用;步骤九、对步骤八制得的热压成形管件进行两端口处的机加工,之后,对热压成形管件的表面进行喷砂去除防氧化涂料处理,即得成品钛合金弯头。
6.优选的,在步骤三中,所述的夹持长度为200~500mm。
7.优选的,在步骤四中,所述感应线圈的内侧与待弯制管材的外侧之间的间隙宽度为10~15mm。
8.优选的,在步骤四中,所述的感应线圈由矩形铜管弯制而成。
9.优选的,在步骤四中,采用现场红外测温的方式,对待弯制管材加热部位的温度进行测定。
10.优选的,在步骤六中,所述的加热炉为电阻加热炉。
11.优选的,在步骤八中,采用现场红外测温的方式,对弯制管坯的表面温度进行测定。
12.优选的,在步骤八中,当弯制管坯的表面温度低于720℃时,应将其放回加热炉内进行二次加热,且整个热压过程中,弯制管坯的回炉次数需不超过2次。
13.优选的,在步骤九中,喷砂处理时采用40目的石英砂。
14.有益效果:本发明的一种大直径钛合金弯头成形方法,通过“中频预弯 模具热压”的工艺路线,解决了现有大直径钛合金弯头成形方法生产效率低、模具成本高的问题。能够实现直径190~457mm、壁厚5~20mm,最小相对弯曲半径1.5d的钛合金弯头的成形。模具工装制造简单,成本低,生产效率得到了显著提升,工业可操作性强,实用效果好。
附图说明
15.图1为采用中频弯管机制备初弯制管件时的结构示意图;图2为热压制备热压成形管件时的结构示意图;附图标记:1、顶杆;2、导辊;3、待弯制管材;4、感应线圈;5、夹头;6、弯臂;7、上模;8、马蹄模;9、下模;10、热压成形管件;11、芯棒。
具体实施方式
16.下面结合附图和具体实施例对本发明的技术方案做进一步详细的阐述和说明。公开本发明的目的旨在保护本发明范围内的一切变化和改进,本发明并不局限于下面的实施例。
17.本发明的一种大直径钛合金弯头成形方法,先利用中频弯管机对大直径钛合金管材进行加热弯制,弯制完成后进行划线和切割,然后对其进行加热,根据管材直径和壁厚,设定加热温度,到达温度后保温15~20分钟出炉,使管件温度均匀。根据目标钛合金弯头的弯曲角度θ、弯曲半径r选择相应规格热压模具,管件出炉后迅速放入下模,装入马蹄模和芯棒,利用压力机使上模下压,至上、下模具贴合为止,完成所需钛合金弯头的成形。
18.具体操作步骤的实现如下:(1)模具准备:本发明涉及的模具分为中频弯制机和热压模具两部分。中频弯制机主要包括感应线圈、夹头、弯臂、顶杆等,如图1所示。感应线圈由矩形铜管弯制而成,感应线圈上均匀分布小孔,用于中频弯制机在弯制时喷水冷却;夹头与弯臂连接,决定初步成形的初弯制管件的弯曲半径。
19.热压模具主要由上模、下模、马蹄模和芯棒组成,见图2所示。上模与下模形成型腔,根据成品钛合金弯头的直径和弯曲半径来制造加工,芯棒用于支撑成品钛合金弯头的内壁,马蹄模用于支撑成品钛合金弯头的两个端口,芯棒和马蹄模共同作用保障成品钛合金弯头的内径尺寸。
20.(2)涂刷防氧化涂料: 钛合金管材内外表面均匀涂刷防氧化涂料,晾干。
21.(3)管材划线:根据成品钛合金弯头的弯曲角度和弯曲半径,按照以下公式计算划线长度:其中:l为理论折弯长度,r为成品钛合金弯头的弯曲半径,θ为成品钛合金弯头的弯曲角度。
22.在管材夹持端预留出夹持长度后划第一条线,然后在距第一条线长度l处划第二条线(可增加10~20mm切割/修磨余量)。
23.(4)中频弯制:按照图1将待弯制管材装配到中频弯管机上,感应线圈放置于管材第一条划线处,感应线圈内侧与管材外部间距以10~15mm为宜。调整中频弯管机电流参数,结合现场红外测温,使待弯制管材加热部位温度维持在720~760℃范围。中频弯管机中的液压驱动装置推动顶杆使待弯制管材向前运动,推进速度为25~35mm/min,加热同时由感应线圈上的小孔喷水冷却,使待弯制管材获得足够刚度,确保弯曲段截面圆度。当待弯制管材上的第二条划线处通过感应线圈时,弯制结束,制得初弯制管件,关闭中频弯管机开关。
24.(5)切割:待初弯制管件冷却至室温后,沿两条划线处切割管材,修磨切割端口,去除毛刺,制得弯制管坯,备用。
25.(6)加热:将制得的弯制管坯放入加热炉内,优先选用电阻加热炉,设置炉内加热温度为820~850℃,到达设定温度后进行保温15~20min出炉,保证整个管段加热均匀。
26.(7)模具预热:提前预热热压模具至200~300℃,这样能够有效减缓钛合金弯管压制过程的温降,给压制过程留出更多的操作时间。
27.(8)热压模具装配:按照图2所示,将热压模具装配于压力机上,保证上模和下模的中心线对齐。
28.(9)热压成型:弯制管坯在加热炉内加热出炉后,快速放置于热压模具中的下模内,在弯制管坯的中部和两端口处装入芯棒和马蹄模,然后操作压力机,使上模缓慢下压,直至上、下模贴合为止。这一过程需配合红外测温,若弯制管坯表面温度低于720℃,应停止压制,对弯制管坯回炉进行二次加热,整个模具的热压过程允许回炉不超过2次。
29.(10)机加工:按照产品图纸对热压成形管件的两端口进行机加工,包括平口、开坡口等。
30.(11)表面处理:喷砂去除热压成形管件表面防氧化涂料,建议使用40目石英砂,即制得成品钛合金弯头。
31.实施例1本实施例对直径d426mm,壁厚12mm,弯曲半径r=640mm(即r=1.5d),弯曲角度θ=52
°
的钛合金弯头进行成形,具体操作步骤为:模具准备:
①
设定中频弯管机中感应线圈的内径为450mm,调节弯臂长度为1278mm(r=3d),管材表面涂刷防氧化涂料,晾干。将管材一端穿过感应线圈,端部用夹头夹紧,夹持长度400mm,另一端用顶杆顶紧。
②
热压模具上模和下模腔内径为427mm,弯曲半径为640mm,马蹄外径ф402mm。
32.划线:第一条线划线位置位于夹头夹持处,然后在距第一条线长度l=590mm处划第二条线。
33.中频弯制:启动中频弯管机,然后调节电流参数,将红外测温枪对准钛合金管材加热处(呈高温红色),温度显示750
±
10℃时保持电流参数稳定,液压驱动装置推动顶杆使钛合金管材向前运动,推进速度设置为30mm/min,同时由感应线圈上的小孔喷水冷却弯曲管材,当管材第二条划线通过感应线圈时弯制结束。
34.切割:沿两条划线处切割弯管,修磨端口毛刺。
35.加热:采用电阻加热炉对钛合金弯管进行加热,设置炉温850℃,到温后保温20分钟出炉。
36.模具预热:提前预热模具至250℃左右,利用红外测温进行监测。
37.热压成型:钛合金弯管出炉后,快速放置于热压下模,装入芯棒和两端马蹄模,然后操作压力机使上模下压,在距离上、下模贴合还有20mm距离时,红外测温显示弯管表面温度低于720℃,停止压制,弯管回炉二次加热,加热温度保持850℃不变。出炉后进行二次压制,至上下模贴合,压制完成。
38.机加工及表面处理:弯头两端机加工平口,然后喷砂去除内外表面防氧化涂料,成形完成,制得成品钛合金弯头。
39.实施例2本实施例对直径d273mm,壁厚8mm,弯曲半径r=500mm(即r=1.8d),弯曲角度θ=60
°
的钛合金弯头进行成形,具体操作步骤为:模具准备:
①
设定中频弯管机中感应线圈的内径为295mm,调节弯臂长度为819mm(r=3d),管材表面涂刷防氧化涂料,晾干。将管材一端穿过感应线圈,端部用夹头夹紧,夹持长度250mm,另一端用顶杆顶紧。
②
热压模具上模和下模腔内径为274mm,弯曲半径为500mm,马蹄外径ф257mm。
40.划线:第一条线划线位置位于夹头夹持处,然后在距第一条线长度l=533mm处划第二条线。
41.中频弯制:启动中频弯管机,调节电流参数,将红外测温枪对准钛合金管材加热处(呈高温红色),温度显示730
±
10℃时保持电流参数稳定,液压驱动装置推动钛合金管材向前运动,推进速度为25mm/min,同时由感应线圈上的小孔喷水冷却加热弯曲管材,当第二条划线通过感应线圈时弯制结束。
42.切割:沿两条划线处切割弯管,修磨端口毛刺。
43.加热:采用电阻加热炉对钛合金弯管进行加热,设置炉温830℃,到温后保温15分钟出炉。
44.模具预热:提前预热模具至250℃左右,利用红外测温进行监测。
45.热压成型:钛合金弯管出炉后,快速放置于热压下模,装入芯棒和两端马蹄模,然后操作压力机使上模下压,过程中通过红外测温显示弯管表面温度始终高于720℃,持续下压至上、下模贴合,压制完成。
46.机加工及表面处理:端部机加工平口,然后喷砂去除弯头内外表面防氧化涂料涂料,弯头成形完成,制得成品钛合金弯头。
再多了解一些
本文用于企业家、创业者技术爱好者查询,结果仅供参考。