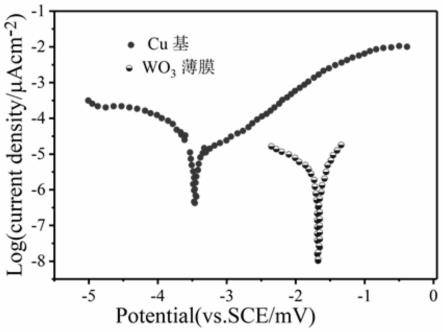
1.本发明涉及物理及功能材料技术领域,具体涉及一种耐蚀抗铜基超疏水表面的制备方法与应用。涉及在铜基表面上制备氧化钨(wo3)薄膜超疏水表面的方法,特别是具有耐蚀和超疏水性能表面。
背景技术:
2.铜具有优异的热性能、电气性能和良好的延展性,被广泛应用于军事装备、船舶建筑、汽车制造和航空航天等领域。然而,铜对氯离子(cl-)非常敏感,容易造成腐蚀,降低了相关设施的耐久性和性能。此外,铜离子的排放对也会环境造成严重的影响,阻碍了其广泛的应用。因此,在铜表面构造耐腐蚀超疏水膜以防止铜腐蚀是十分必要的。超疏水性是一种特殊的润湿性行为,接触角(ca)大于150
°
,滑动角(sa)小于10
°
,超疏水表面具有拒水性、耐腐蚀性和自洁性等特点,引起了人们的广泛关注。
3.目前,铜基制备超疏水材料主要是通过电沉积、化学刻蚀、化学沉积以及热氧化等方法,在铜片表面构筑能够产生超疏水性能的粗糙结构,利用化学修饰后降低表面能从而得到超疏水表面。但是,一方面,这些方法通常都存在处理工序复杂,成本较高,稳定性较差等缺点,根本无法大面积工业化生产。另一方面,也是最重要的,现存的很多超疏水表面只对外加宏观水滴呈低黏附超疏水状态(即cassie态),对潮湿环境中原位形成的微小液滴或雾化液滴则呈非超疏水态(即超疏水特性在水蒸气凝结条件下发生失效)或高黏附的超疏状态(即wenzel态),很难脱落,基本无法实现工业化应用。
技术实现要素:
4.针对现有制备超疏水材料的工艺存在处理工序复杂、成本高、稳定性差以及针对现有工艺制备的超疏水表面存在只对宏观水滴呈低黏附超疏状态,而对潮湿环境中的微小液滴或雾化液滴则呈非超疏水态的问题;本发明提供了一种绿色环保、处理工序简单、条件温和、易操作、成本低、稳定性好的氧化钨薄膜超疏水表面的制备方法,该方法制备的超疏水表面水滴接触角(ca)>150
°
,滚动角(sa)<10
°
,水滴呈稳定的低黏附超疏水状态(cassie态)。
5.本发明是通过如下技术方案实现的:
6.一种耐蚀抗铜基超疏水表面的制备方法,其特征在于,该方法依次包括如下步骤:
7.s1、基底预处理:将铜箔基底清洗,去除表面脏污;
8.s2、去除氧化皮:将清洗后的铜箔置于酸中浸泡,去除所述铜箔表面的氧化皮;
9.s3、基底清洗:去除氧化皮后洗去铜箔表面残留的酸,然后用有机溶剂淋洗,吹干,备用;
10.s4、沉积氧化钨膜:在所述铜箔的表面溅射沉积氧化钨薄膜;
11.s5、表面氟化改性:将步骤s4制备好的试样浸入含有氟硅烷的溶液中浸泡进行氟化改性,干燥,得到耐蚀抗铜基超疏水表面。
12.具体的,本发明的耐蚀抗铜基超疏水表面的制备方法,涉及在铜基表面上制备氧化钨(wo3)薄膜超疏水表面的方法,本发明的制备方法是以丙酮、无水乙醇和离子水超声清洗,将铜先进行预处理除去表面粉尘、油污;以稀盐酸浸泡去除表面氧化皮;随后利用离子束溅射工艺在铜基表面构建纳米级粗糙结构氧化钨(wo3);最后利用十七氟癸基三甲氧基硅烷(fas-17)对具有粗糙结构的氧化钨(wo3)进行常温氟化改性,即制得氧化钨超疏水表面。
13.进一步的,一种耐蚀抗铜基超疏水表面的制备方法:步骤s1、基底预处理:将所述铜箔基底依次用丙酮、无水乙醇和去离子水超声清洗5-10分钟,去除表面粉尘和油污。
14.进一步的,一种耐蚀抗铜基超疏水表面的制备方法:步骤s2、去除氧化皮:将清洗后的铜箔置于稀盐酸中浸泡20-90秒,去除所述铜箔表面的氧化皮。
15.进一步的,一种耐蚀抗铜基超疏水表面的制备方法:所述稀盐酸的浓度为0.01-0.5mol/l。
16.进一步的,一种耐蚀抗铜基超疏水表面的制备方法:步骤s3、基底清洗:去除氧化皮后依次用自来水和去离子水冲洗去除所述铜箔表面残留的酸,然后用无水乙醇淋洗,冷风吹干,备用。具体的,为了防止铜箔干燥过程中的再次氧化,而采用了无水乙醇淋洗,冷风吹干的方法。
17.进一步的,一种耐蚀抗铜基超疏水表面的制备方法:步骤s4、沉积氧化钨膜:在室温下,在所述铜箔的表面采用离子束溅射工艺沉积氧化钨薄膜;溅射前,将腔室抽真空至压力为3
×
10-3
~4.5
×
10-3
pa;然后注入氩气,确保溅射压力为1.0
×
10-2
~1.8
×
10-2
pa;然后在加速电压为1000-2500v,电流为10-50ma的条件下溅射沉积1-3小时,即可得到氧化钨薄膜。
18.进一步的,一种耐蚀抗铜基超疏水表面的制备方法:步骤s5、表面氟化改性:将步骤s4制备好的试样浸入含有氟硅烷的乙醇溶液中浸泡2-5小时进行氟化改性,然后在50-60℃下干燥,即可得到耐蚀抗铜基超疏水表面。
19.进一步的,一种耐蚀抗铜基超疏水表面的制备方法:所述的氟硅烷为十七氟癸基三甲氧基硅烷。具体的,采用了修饰效果好且修饰后几乎不改变样品形貌的低表面能物质氟硅烷进行低温氟化,并且在本发明的工艺中采用的是将试样浸入含有氟硅烷的乙醇溶液中浸泡进行氟化,该方法可以使得氟化更均匀,有利于进一步提升超疏水效果。
20.一种耐蚀抗铜基超疏水表面的应用,其特征在于,上述的制备方法制得的耐蚀抗铜基超疏水表面在航空航天、低温存储、空调热泵、制冷和低温工程材料中的应用。
21.本发明工艺制备的耐蚀抗铜基超疏水表面(即铜基氧化钨薄膜超疏水表面)其稳定性好,在航空航天、低温存储、空调热泵、制冷和低温工程等领域有广阔的应用前景和巨大的市场效益。
22.本发明提供的耐蚀抗铜基超疏水表面的制备方法是以丙酮、无水乙醇和离子水超声清洗,将铜先进行预处理除去表面粉尘、油污;以稀盐酸浸泡去除表面氧化皮;随后,把清洗后的铜基放入离子束溅射沉积系统中,溅射沉积1-3小时,得到了氧化钨(wo3)薄膜。然后将得到的氧化钨膜在常温下浸入含有十七氟癸基三甲氧基硅烷的稀释乙醇溶液中浸泡2-5小时,最后干燥,得到了改性后的氧化钨超疏水表面;制备的氧化钨表面具有优异的超疏水性能和耐蚀性能。所制备的具有纳米级粗糙结构的氧化钨铜基超疏水表面在模拟海水溶液
中浸泡表现出非常好的耐蚀性能。
23.本发明的有益效果:
24.(1)本发明公开了一种在铜基表面上制备氧化钨薄膜超疏水表面的制备方法(指宏观水滴接触角>150
°
,滚动角<10
°
,水滴呈稳定cassie态的超疏水表面),本发明的方法工艺简单、条件温和、易操作、成本低等;制备所得的铜基超疏水表面具有优异的宏观疏水性能,水静态接触角可达161
°
,滚动角6.8
°
,且有优异的耐蚀性能,在模拟海水溶液中浸泡表现出非常好的耐蚀性能。本发明在铜基表面制备出的超疏水表面,稳定性好,在航空航天、低温存储、空调热泵、制冷和低温工程等领域有广阔的应用前景和巨大的市场效益。
25.(2)本发明方法制备的耐蚀抗铜基超疏水表面在模拟海水溶液中浸泡一周后,其表面对水的接触角可保持在161
°
,缓蚀率能达到97.3%;继续浸泡到15天后,仍表现出非常好的耐蚀性能,其缓蚀率达到了90%,具有优异的耐蚀性能。
26.(3)本发明采用离子束溅射法在室温条件下在铜基表面构建了纳米级粗糙结构氧化钨薄膜,再经过常温氟硅烷修饰氟化改性,从而使所得的超疏水表面具有较强的耐腐蚀性能和超疏水性能;本发明的方法是一种比较简单、廉价易控制的方法,通过本发明的制备方法最终所得的铜基超疏水表面具有较高的防腐性能。
27.(4)本发明的制备方法,工艺简单、条件温和、成本低廉、稳定性高、绿色环保,制备所得的超疏水表面,具有优异的耐腐蚀性能。
附图说明
28.为了更清楚地说明本发明实施例的技术方案,下面将对实施例描述中所需要使用的附图作简单地介绍,显而易见地,下面描述中的附图仅仅是本发明的一些实施例,对于本领域的技术人员来讲,在不付出创造性劳动的前提下,还可以根据这些附图获得其他附图。
29.图1为本发明实施例1中氧化钨薄膜的fesem图;
30.图2为本发明实施例1制备的耐蚀抗铜基超疏水表面的水静态接触角图;
31.图3为本发明实施例1制备的耐蚀抗铜基超疏水表面的极化曲线。
具体实施方式
32.下面将结合本发明实施例中的附图,对本发明实施例中的技术方案进行清楚、完整地描述,显然,所描述的实施例仅仅是本发明的一部分实施例,而不是全部的实施例。以下对至少一个示例性实施例的描述实际上仅仅是说明性的,决不作为对本发明及其应用或使用的任何限制。基于本发明中的实施例,本领域普通技术人员在没有作出创造性劳动前提下所获得的所有其他实施例,都属于本发明保护的范围。
33.实施例1
34.一种耐蚀抗铜基超疏水表面的制备方法,依次包括如下步骤:
35.s1、铜箔基底预处理:将20.0mm
×
20.0mm
×
0.24mm的铜箔基底依次用丙酮、无水乙醇和去离子水超声清洗5分钟,去除表面的粉尘和油污;
36.s2、去除氧化皮:将清洗后的铜箔置于0.1mol/l的稀盐酸中浸泡30秒,以去除铜箔表面的氧化皮;
37.s3、基底清洗:去除氧化皮后依次用自来水和去离子水冲洗去除铜箔表面残留的
盐酸,然后用无水乙醇淋洗,冷风吹干,备用;采用无水乙醇淋洗和冷风吹干可以防止铜箔干燥过程中的再次氧化;
38.s4、沉积氧化钨膜:在室温下,在所述铜箔的表面采用离子束溅射工艺沉积氧化钨薄膜;具体的工艺为:把清洗后的铜箔放入离子束溅射沉积系统中,且在溅射前将腔室抽真空至压力为4.5
×
10-3
pa;然后注入氩气(99.999wt%),确保溅射压力为1.8
×
10-2
pa;然后在加速电压为2500v,电流为50ma的条件下溅射沉积2小时,即可得到氧化钨(wo3)薄膜;
39.s5、表面氟化改性:将步骤s4制备好的试样浸入含有十七氟癸基三甲氧基硅烷(fas-17)的乙醇溶液中浸泡2小时进行氟化改性,然后在60℃下烘干,得到耐蚀抗铜基超疏水表面。
40.实施例2
41.一种耐蚀抗铜基超疏水表面的制备方法,依次包括如下步骤:
42.s1、铜箔基底预处理:将20.0mm
×
20.0mm
×
0.24mm的铜箔基底依次用丙酮、无水乙醇和去离子水超声清洗10分钟,去除表面的粉尘和油污;
43.s2、去除氧化皮:将清洗后的铜箔置于0.05mol/l的稀盐酸中浸泡50秒,以去除铜箔表面的氧化皮;
44.s3、基底清洗:去除氧化皮后依次用自来水和去离子水冲洗去除铜箔表面残留的盐酸,然后用无水乙醇淋洗,冷风吹干,备用;采用无水乙醇淋洗和冷风吹干可以防止铜箔干燥过程中的再次氧化;
45.s4、沉积氧化钨膜:在室温下,在所述铜箔的表面采用离子束溅射工艺沉积氧化钨薄膜;具体的工艺为:把清洗后的铜箔放入离子束溅射沉积系统中,且在溅射前将腔室抽真空至压力为3.5
×
10-3
pa;然后注入氩气(99.999wt%),确保溅射压力为1.5
×
10-2
pa;然后在加速电压为1500v,电流为30ma的条件下溅射沉积4小时,即可得到氧化钨(wo3)薄膜;
46.s5、表面氟化改性:将步骤s4制备好的试样浸入含有十七氟癸基三甲氧基硅烷的乙醇溶液中浸泡3小时进行氟化改性,然后在50℃下烘干,得到耐蚀抗铜基超疏水表面。
47.对上述实施例1步骤s4沉积的氧化钨薄膜用场发射扫描电子显微镜进行微观形貌观察,如图1所示;从图1中可以看出本发明利用离子束溅射工艺在铜基表面构建了纳米级粗糙结构氧化钨薄膜。
48.通过接触角测量仪对上述实施例1制备的耐蚀抗铜基超疏水表面进行接触角检测,如图2所示;可以看出采用本发明的方法制备铜基氧化钨薄膜超疏水表面水静态接触角可达163
°
,具有明显的超疏水性能。
49.通过电化学测试系统对上述实施例1制备的耐蚀抗铜基超疏水表面(氧化钨超疏水表面)进行极化曲线测量,如图3所示;从图3中可以看出本发明制备的超疏水表面具有优异的耐腐蚀性能。综上,本发明制备的超疏水表面具有优异的疏水性能和耐腐蚀性能。本发明在铜基表面制备出的氧化钨薄膜超疏水表面,稳定性好,在航空航天、低温存储、空调热泵、制冷和低温工程等领域有广阔的应用前景和巨大的市场效益。
50.上述为本发明的较佳实施例仅用于解释本发明,并不用于限定本发明。凡由本发明的技术方案所引伸出的显而易见的变化或变动仍处于本发明的保护范围之中。
再多了解一些
本文用于企业家、创业者技术爱好者查询,结果仅供参考。