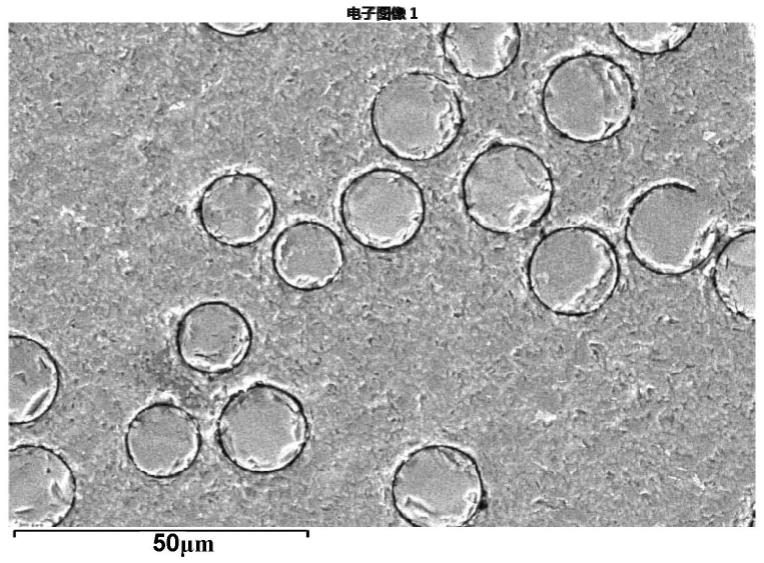
1.本发明涉及一种基于浆料组分设计的纤维增强碳化硅陶瓷基复合材料的制备方法,属于航空航天热结构陶瓷基复合材料技术领域。
背景技术:
2.与常规高温结构材料如镍基、钛基合金相比,纤维增强碳化硅陶瓷基复合材料具有更高的比强度和比刚度,更加突出的耐温/抗氧化性能,是航空航天动力系统减重提效的关键热结构材料。
3.孔隙是陶瓷基复合材料裂纹萌生进而触发断裂失效的主要诱因,因此高致密是高性能陶瓷基复合材料的首要前提。纤维是碳化硅陶瓷基复合材料具备非脆性断裂特性的关键组元,然而,因传质受纤维阻碍,碳化硅陶瓷基复合材料实现致密化制备比较困难。反应烧结(或称反应熔渗)是目前该类材料致密化制备的主要技术途径之一,其通常先制备含碳的多孔预成型体,借助外渗硅(或硅合金)熔体完成反应烧结,主要原理是利用硅熔体在毛细作用下渗入纤维预制体孔隙并与内部碳源反应生成碳化硅,从而获得致密材料。然而这种制备方法存在两个非常显著的问题:一方面,受纤维预制体孔隙结构的限制,硅熔体渗透深度是有限的,因此该方法不适合制备厚壁部件(kumar s,et al.capillary infiltration studies of liquids into 3d-stitched c-c preforms:part b:kinetics of silicon infiltration.j eur ceram soc.2009;29(12):2651-2657.)。另一方面,硅与碳的反应受扩散控制,随着反应进行碳和硅之间形成碳化硅反应层阻碍扩散进行,使得材料不可避免存在未反应的硅残留,这对材料高温性能带来不利影响(wang j,et al.microstructure and mechanical properties of c/c-sic composites fabricated by a rapid processing method.j eur ceram soc.2009;29(14):3091-3097.)。为克服现有反应烧结技术在制备碳化硅陶瓷基复合材料的不足,亟需从熔体渗透与反应原理角度对整个制备过程进行优化设计。
技术实现要素:
4.为解决反应烧结在制备碳化硅陶瓷基复合材料存在硅熔体渗透深度不足与熔体残留的问题,本发明提供一种全新的基于浆料叠层设计的纤维增强碳化硅陶瓷基复合材料的制备方法,包括:(1)将硅粉和硅合金粉中至少一种以及碳化硅粉体作为原料粉体,加入粘结剂和溶剂进行混合后,通过流延成型和干燥,得到碳化硅坯片;(2)将纤维布浸渍在含有碳化硅粉和碳源的混合浆料中或将含有碳化硅粉和碳源的混合浆料覆在纤维布的上下表面,再经干燥后,得到纤维浸渍片;(3)将所得碳化硅坯片和纤维浸渍片交替叠层后置于模具中进行加压固化,得到固化成型体;
(4)将所得固化成型体进行排胶和反应烧结,得到所述基于浆料叠层设计的纤维增强碳化硅陶瓷基复合材料。
5.在前期研究过程中,本发明人先是通过将纤维布(碳纤维布、碳化硅纤维布或氮化硅纤维布)直接浸渍在含有碳源 硅粉(或/和硅合金粉) sic粉的混合溶液中,但是此时虽然可以实现硅熔体渗透深度的降低,但由于硅源和碳源距离纤维布的距离都很近,不可避免的使得硅源和碳源反应的同时,不可避免的存在部分硅源与纤维布之间存在腐蚀反应;为此,本发明人进一步地将含有硅粉和硅合金粉中至少一种以及碳化硅粉体的碳化硅坯片和含有碳化硅粉和碳源的纤维浸渍片交替叠层,再依次经固化、热解和反应烧结。其在反应烧结过程中,由于硅源(硅粉和硅合金粉)和碳源之间分离且与纤维布之间存在特定的距离,在实现微距渗硅反应的同时有效避免了对于纤维布的腐蚀,最终获得纤维增强碳化硅陶瓷基复合材料。
6.较佳的,所述含有碳化硅粉和碳源的混合浆料是将碳化硅粉体、碳源、粘结剂和溶剂混合后得到。
7.较佳的,所述碳源为无机碳源或/和有机碳源;所述无机碳源为碳粉;所述有机碳源为酚醛树脂、环氧树脂和糖醇树脂中的至少一种;优选地,所述碳源的加入量为碳源和碳化硅粉总体质量的20~75wt%;更优选地,所述碳粉的粒径为0.1~20μm,优选为1~10μm。
8.较佳的,步骤(1)中,所述硅粉和硅合金粉中至少一种占原料粉体总质量的为40~80wt%。在此范围内,有利于后续烧结反应充分进行。若是硅粉和硅合金粉的含量过少或过多,则难以保证烧结反应充分进行,导致材料内部有残留碳或硅,进一步降低力学性能和高温热性能。
9.较佳的,所述固化成型体中硅粉和硅合金粉中至少一种和碳源的质量比为(50~80):(20~40)。在此范围内,能够保证材料内部无显著碳或硅残留。
10.较佳的,所述碳化硅粉体的粒径为0.1~50μm,优选为2~20μm;所述硅粉或/和硅合金粉的粒径为0.5~50μm,优选为1~20μm。
11.较佳的,所述粘结剂选自聚乙烯醇、聚乙烯醇缩丁醛、聚甲基丙烯酸甲酯中的至少一种,优选为聚乙烯醇和聚乙烯醇缩丁醛;所述溶剂选自乙醇、异丙醇和二甲苯中的至少一种。
12.较佳的,所述碳化硅坯片的厚度为0.1~5mm,优选为0.3~1mm;所述纤维浸渍片的厚度为0.1~3mm,优选为0.5~1mm。
13.较佳的,所述纤维布的材质为碳纤维布、碳化硅纤维布或氮化硅纤维布。
14.较佳的,所述加压固化的固化温度为80~250℃,固化压力0.1~20mpa。
15.较佳的,所述排胶的温度为600~1000℃,保温时间0.5~2小时;所述反应烧结的温度为1400~1800℃,保温时间为0.1~2小时。
16.有益效果:与现有的反应烧结技术相比,本发明专利提出碳化硅流延片/纤维浸渍片交替叠层并结合反应烧结原理制备陶瓷基复合材料的新思路(图2):在流延片(碳化硅坯片)/纤维浸渍片中分别引入硅源和碳源,降低硅源的渗透距离,同时缩短烧结反应硅/碳扩散距离;其次,通过灵活调控硅源/碳源粒径、组分比例,可促进原位反应充分、完全进行,抑制甚至完全消除材料内部游离硅/碳的残留;另外,由于硅熔体渗透/扩散距离缩短,反应烧结温度
和时间也可显著降低,这将缓解硅熔体对纤维的热/化学损伤,从而大幅提升材料综合性能。
附图说明
17.图1为本发明纤维增强碳化硅陶瓷基复合材料的制备过程示意图;图2为本发明纤维增强碳化硅陶瓷基复合材料的浆料叠层设计和反应烧结原理图,从图中可知,通过分别在纤维布和流延层中引入碳源和硅源,可以利用碳源和硅源的反应烧结效应实现材料致密化;图3为本发明实施例1制备的纤维增强碳化硅陶瓷基复合材料的微观结构sem照片,从图中可知,材料孔隙率较低,无显著残留硅和碳,纤维本身无损伤,说明利用这种浆料叠层设计可以实现材料高效制备;图4为实施例2制备的纤维增强碳化硅陶瓷基复合材料的微观结构sem照片,从图中可知复合材料孔隙率较低,无显著残留硅和碳,纤维本身无损伤;图5为实施例3制备的纤维增强碳化硅陶瓷基复合材料的微观结构sem照片,从图中可知复合材料孔隙率较低,无显著残留硅和碳,纤维本身无损伤;图6为对比例1制备的纤维增强碳化硅陶瓷基复合材料的微观结构sem照片,从图中可知存在大颗粒的碳残留和si残留;图7为对比例2制备的纤维增强碳化硅陶瓷基复合材料的微观结构sem照片,从图中可知纤维本身存在比较严重的腐蚀;图8为对比例3制备的纤维增强碳化硅陶瓷基复合材料的微观结构sem照片,从图中可知存在大颗粒的碳残留和si残留。
具体实施方式
18.以下通过下述实施方式进一步说明本发明,应理解,下述实施方式仅用于说明本发明,而非限制本发明。
19.在本公开中,分别配制两种碳化硅浆料:一种主要成分为碳化硅粉、硅或/和硅合金粉中至少一种、溶剂和粘结剂,并以流延方式获得碳化硅坯片(或称碳化硅坯体);另一种主要成分为碳化硅粉、碳粉(或有机树脂)、溶剂和粘结剂,将纤维布(由碳纤维或碳化硅纤维组成)浸渍其中获得纤维浸渍片。将流延所得碳化硅坯片与纤维浸渍片交替叠层,依次经固化、热解和反应烧结获得纤维增强碳化硅陶瓷基复合材料(图1)。
20.碳化硅坯体的流延成型。具体来说,将掺入硅(或硅合金)粉的浆料通过流延方式获得碳化硅坯片。作为一个示例,将一定配比的硅粉和硅合金粉中至少一种、碳化硅粉和粘结剂(例如,聚乙烯醇、聚乙烯醇缩丁醛或聚甲基丙烯酸甲酯等)加入至适量溶剂(例如,乙醇、异丙醇或二甲苯等)中,机械搅拌均匀后倒入球磨罐进行球磨(其中,球磨的转速为60~120转/分钟,时间为12~48小时),获得第一稳定浆料。将第一稳定浆料通过流延技术和干燥,获得碳化硅坯片。其中,粘结剂的加入量可为原料粉体(硅粉和硅合金粉中至少一种和碳化硅粉)总质量的5~20wt%。所得第一稳定浆料中原料粉体的固含量可为25~50wt%。所得碳化硅坯体的厚度可为0.1~5μm,优选为0.3~1mm。
21.在可选的实施方式中,流延用第一稳定浆料中硅粉和硅合金粉中至少一种占原料
粉体总质量的为40~80wt%。
22.纤维浸渍片的制备。在浆料中掺入碳源(碳粉或有机树脂等),并将该浆料浸渍纤维布(碳纤维布或碳化硅纤维布),获得纤维浸渍片。作为一个示例,将一定配比的碳化硅粉体、碳源(例如,碳粉、酚醛树脂、环氧树脂、糖醇树脂等有机碳源或/和无机碳源)和粘结剂(例如,聚乙烯醇、聚乙烯醇缩丁醛或聚甲基丙烯酸甲酯等)加入至适量溶剂(例如,乙醇、异丙醇或二甲苯等)中,机械搅拌均匀后倒入球磨罐中进行球磨(球磨数小时),获得第二稳定浆料。再通过涂刷或浸渍等方式将浆料引入纤维布中,并进行干燥,得到纤维浸渍片。其中,粘结剂的加入量可为碳化硅粉体质量的5~20wt%。所得第二稳定浆料中碳化硅粉体和碳源的固含量可为30~60wt%。其中,纤维布可为碳纤维布或碳化硅纤维布。所得纤维浸渍片的厚度可为0.1~3mm,优选为0.5~1mm。
23.在可选的实施方式中,当碳源为无机碳源(例如,碳粉)时,纤维浸渍用第二稳定浆料中碳化硅粉体和碳粉质量比为50~80:20~50。若以酚醛树脂、环氧树脂、糖醇树脂等为碳源,可依据其热解残炭率确定碳化硅粉体/树脂的质量百分比。作为一个示例,以酚醛树脂、环氧树脂、糖醇树脂等为有机碳源,则碳化硅粉体/有机碳源的质量比可为25~65:35~75。
24.在可选的实施方式中,碳化硅粉体粒径可为0.1~50μm,优选可为2~20μm。硅粉或硅合金粉体粒径可为0.5~50μm,优选可为1~20μm。碳粉的粒径可为0.1~20μm,优选可为1~10μm。上述干燥的过程一般是置于室温通风环境下晾干。
25.将流延所得碳化硅坯片纤维浸渍片经过裁剪并交替叠层,置于模具中保温加压固化,得到固化成型体。其中,固化温度可为80~250℃,固化压力可为0.1~20mpa。优选,控制固化成型体中硅源(硅粉或/和硅合金粉)和碳源质量比为(50~80):(20~40)。
26.将固化成型体置于碳管炉中进行中温排胶处理,然后升高温度进行反应烧结过程,完成材料的致密化制备。其中,排胶的温度可为600~1000℃,保温时间0.5~2小时。反应烧结温度可为1400~1800℃,保温时间可为0.1~2小时。
27.综上所述,本发明通过在交替叠层的流延片/纤维浸渍片中分别引入硅源和碳源,降低硅源的渗透与扩散距离,缩短反应烧结时间;另外,通过灵活调控硅源/碳源比例,可促进原位反应充分、完全进行,抑制材料内部硅残留并缓解硅熔体对纤维的热/化学损伤,从而大幅提升材料综合性能。
28.下面进一步例举实施例以详细说明本发明。同样应理解,以下实施例只用于对本发明进行进一步说明,不能理解为对本发明保护范围的限制,本领域的技术人员根据本发明的上述内容作出的一些非本质的改进和调整均属于本发明的保护范围。下述示例具体的工艺参数等也仅是合适范围中的一个示例,即本领域技术人员可以通过本文的说明做合适的范围内选择,而并非要限定于下文示例的具体数值。
29.实施例1(1)碳化硅坯体流延:将碳化硅粉(粒径为5μm)、硅粉(粒径为10μm)、聚乙烯醇缩丁醛加入到乙醇中,碳化硅粉、硅粉、聚乙烯醇缩丁醛和乙醇的质量比为20:25:10:45,机械搅拌均匀后放倒入球磨罐球磨24小时,获得均匀的第一稳定碳化硅浆料。再利用流延设备将浆料制成厚度均匀的流延片,流延片厚度为0.5mm。最后平铺置于室温通风环境晾干,得到碳化硅坯片(厚度为0.4mm);
(2)纤维浸渍片制备:将碳化硅粉(粒径为2μm)、碳粉(粒径为1μm)、聚乙烯醇缩丁醛加入到乙醇中,碳化硅粉、碳粉、聚乙烯醇缩丁醛和乙醇的质量比为30:20:10:40,机械搅拌均匀后放倒入球磨罐球磨24小时,获得均匀的第二稳定浆料。再通过涂刷方式将浆料引入平纹碳纤维布(厚度0.4mm),获得未干燥的纤维浸渍片,浸渍片厚度为0.5mm。最后平铺置于室温通风环境晾干,得到纤维浸渍片(厚度为0.4mm);(3)预制体成型:将步骤(1)获得的碳化硅坯片与步骤(2)获得的干燥后的纤维浸渍片进行裁剪并交替叠层(总共8层),置于模具中保温加压固化,得到固化成型体。所得固化成型体中硅源(硅粉)和碳源质量比为50:40。其中固化温度为150℃,固化压力为1.5mpa;(4)成型体排胶与烧结:将步骤(3)中获得的固化成型体置于碳管炉中进行排胶处理(排胶温度为700℃,保温时间为1小时)然后升至1450℃,保温0.5小时,进行反应烧结过程,完成材料制备,材料微观结构如图3所示。
30.实施例2(1)碳化硅坯体流延:将碳化硅粉(粒径为10μm)、硅粉(粒径为5μm)、聚乙烯醇加入到异丙醇中,碳化硅粉、硅粉、聚乙烯醇和异丙醇的质量比为25:25:5:45,机械搅拌均匀后放倒入球磨罐球磨36小时,获得均匀的第一稳定碳化硅浆料。再利用流延设备将浆料制成厚度均匀的流延片,流延片厚度为2mm。最后平铺置于室温通风环境晾干,得到碳化硅坯片(厚度为1.5mm);(2)纤维浸渍片制备:将碳化硅粉(粒径为5μm)、酚醛树脂、聚乙烯醇加入到异丙醇中,碳化硅粉、酚醛树脂、聚乙烯醇和异丙醇的质量比为25:30:5:40,机械搅拌均匀后放倒入球磨罐球磨36小时,获得均匀的第二稳定浆料。再通过浸渍方式将浆料引入缎纹碳化硅纤维布(厚度0.5mm),获得未干燥的纤维浸渍片,浸渍片厚度为1mm。最后平铺置于室温通风环境晾干,得到纤维浸渍片(厚度为0.8mm);(3)预制体成型:将步骤(1)获得的流延坯片与步骤(2)获得的纤维浸渍片进行裁剪并交替叠层(总共8层),置于模具中保温加压固化,得到固化成型体。所得固化成型体中硅源(硅粉)和碳源质量比为60:30。其中固化温度为120℃,固化压力为5mpa;(4)成型体排胶与烧结:将(3)中获得的固化成型体置于碳管炉中进行排胶处理(排胶温度为800℃,保温时间为0.5小时),然后升至1500℃,保温0.2小时,进行反应烧结过程,完成材料制备。
31.实施例3(1)酯加入到乙醇中,碳化硅粉、硅粉、聚甲基丙烯酸甲酯和乙醇的质量比为30:25:5:40,机械搅拌均匀后放倒入球磨罐球磨24小时,获得均匀的第一稳定碳化硅浆料。再利用流延设备将浆料制成厚度均匀的流延片,流延片厚度为0.5mm。最后平铺置于室温通风环境晾干,得到碳化硅坯片(厚度为0.4mm);(2)纤维浸渍片制备:将碳化硅粉(粒径为2μm)、环氧树脂、聚乙烯醇加入到乙醇中,碳化硅粉、环氧树脂、聚乙烯醇和乙醇的质量比为25:25:10:40,机械搅拌均匀后放倒入球磨罐中球磨24小时,获得均匀的第二稳定浆料。再通过浸渍方式将浆料引入单向碳化硅纤维布(厚度0.5mm),获得未干燥的纤维浸渍片,厚度为0.3mm。最后平铺置于室温通风环境晾干,得到纤维浸渍片(厚度为0.25mm);(3)预制体成型:将步骤(1)获得的流延坯片与步骤(2)获得的纤维浸渍片进行裁
剪并交替叠层(总共8层),置于模具中保温加压固化,得到固化成型体。所得固化成型体中硅源(硅粉)和碳源质量比为70:30。其中固化温度为100℃,固化压力为10mpa;(4)成型体排胶与烧结:将(3)中获得的固化成型体置于碳管炉中进行排胶处理(排胶温度为900℃,保温时间为1小时),然后升至1600℃,保温0.1小时,进行反应烧结过程,完成材料制备。
32.实施例4本实施例4的制备过程参照实施例2,区别在于:第一稳定碳化硅浆料中碳化硅粉、硅粉、聚乙烯醇和异丙醇的质量比为10:40:5:45。所得碳化硅坯片的厚度为0.6mm。
33.实施例5本实施例5的制备过程参照实施例2,区别在于:第一稳定碳化硅浆料中碳化硅粉、硅粉、聚乙烯醇和异丙醇的质量比为30:20:5:45,机械搅拌均匀后放倒入球磨罐球磨36小时,获得均匀的第一稳定碳化硅浆料。所得碳化硅坯片的厚度为0.8mm。
34.实施例6本实施例6的制备过程参照实施例1,区别在于:碳化硅坯片的厚度为3mm,干燥后的纤维浸渍片的厚度为1.6mm。
35.对比例1本对比例1的制备过程参照实施例1,区别在于:直接采用三维平纹碳纤维预制体(厚度为20mm)直接浸渍在同时含有碳化硅粉、硅源和碳源的前驱体溶液中,再经干燥、排胶和反应烧结。其中,碳化硅粉、硅源和碳源的前驱体按质量比40:20:40进行球磨混合24小时,获得稳定浆料。
36.对比例2本对比例2的制备过程参照实施例1,区别在于:采用平纹碳纤维布,直接浸渍在同时含有碳化硅粉、硅源和碳源的前驱体溶液中,再进行干燥、叠层、热固化和反应烧结。其中,将碳化硅粉、硅源和碳源的前驱体溶液按质量比50:30:20进行球磨混合24小时,获得稳定浆料,其与步骤参照实施例1。
37.对比例3本对比例3的制备过程参照实施例1,区别在于:碳化硅坯片的厚度为6mm,干燥后的纤维浸渍片的厚度为3.2mm。
38.需要说明的是,以上列举的仅仅是本发明的若干具体实施例,远远没有体现出本发明的全部内涵。应该意识到:只要不偏离本发明的范围和实质,本领域的技术人员从本发明公开内容直接导出或间接引申的所有变形,均被认为是本发明的保护范围。
再多了解一些
本文用于企业家、创业者技术爱好者查询,结果仅供参考。