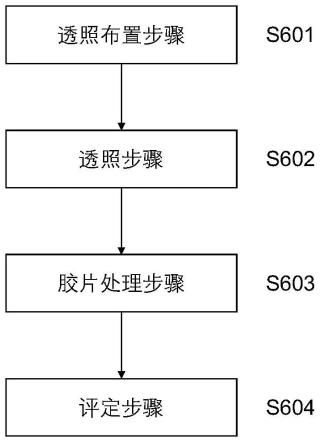
1.本发明属于聚变、加速器工程等应用领域,涉及一种焊缝无损检测方法,更具体而言涉及一种小尺寸跑道型焊缝无损检测方法。
背景技术:
2.随着世界人口和经济增长,各国对于能源的需求急剧增加,目前使用的能源主要包括煤、石油、天然气等化石能源以及裂变能源等。但化石能源存在储量有限、排放温室气体、污染环境的问题,而裂变能源会产生长寿命放射性强的核废料,一旦出现安全事故后果将很严重。
3.对此,聚变能源具有经济和清洁、安全的优点,是未来世界主要的能源。目前,磁约束核聚变装置是最有希望实现可控核聚变反应堆的装置,对于我国经济社会的可持续发展具有重要的战略意义。
4.磁约束核聚变装置利用磁场来约束温度极高的等离子体的核燃料,使其发生聚变反应释放出能量。在这样的聚变装置中,磁体系统是核心部件,由若干个超导导体(pf)线圈串联连接后套装在一起。超导导体采用了管内电缆导体cicc(cable-in-conduit conductors)结构,将超导电缆用不锈钢等材料的铠甲(jacket)包裹,使用铠甲起到承力和液氦冷却剂容器的功能。
5.超导电缆用4.5k的液氦冷却,为了将液氦引入线圈绕组内部,需要在线圈内侧或外侧的铠甲上开凿氦进出孔,然后将氦进出口凸台与铠甲、液氦管焊接在一起。
6.氦进出口是线圈上应力最大的区域之一,其焊缝为i类焊缝,因此对焊缝质量有着极高的高求。焊缝质量不仅要满足大电流及高磁场的物理运行要求,也应具有较高的力学强度,因此氦进出口焊缝的结构设计以及检测工艺研究极具挑战性及现实工程意义。
技术实现要素:
7.现有技术中存在的问题
8.基于对铠甲及超导电缆的保护,氦进出口焊缝设计为异型的跑道型焊缝,制备流程分为:铠甲上堆焊凸台、铠甲上制造氦孔以及焊接坡口、焊接氦进出口凸台。由于其结构的特殊性以及操作现场空间局限,传统的焊缝无损检测方法,例如超声检测技术、射线检测技术、电磁检测技术等无法直接应用于异型的跑道型焊缝中,给无损检测技术的研发及实施带来了很大的难度。
9.本发明为解决现有技术中存在的问题而提出,其目的是提供一种针对小尺寸异型焊缝的无损检测技术,能够适用于核聚变装置的磁体制备过程中批量氦进出口焊缝的检测。
10.解决问题的技术手段
11.具体而言,本发明提供一种焊缝无损检测方法,通过射线检测法对被检测工件的小尺寸异型焊缝进行缺陷检测,其包括:透照布置步骤,其中准备与焊缝的尺寸匹配的多个
胶片;透照步骤,其中使用所述多个胶片分别沿所述焊缝整周照射射线进行多次透照;胶片处理步骤,其中对经过所述透照步骤的所述多个胶片进行洗片、烘干处理;和评定步骤,其中对经过所述胶片处理步骤得到的多个胶片进行评定分析,确定所述焊缝整周的缺陷的大小和类型,其中,在所述透照步骤中,利用支承板支承各所述胶片,使各所述胶片紧贴所述焊缝的根部进行透照,所述焊缝是跑道型焊缝,包括两个彼此平行的直线段焊缝和两个将所述直线段焊缝彼此连接的180
°
的弧形段焊缝,对各所述直线段焊缝分别使用一个所述胶片进行一次透照,对各所述弧形段焊缝分别使用多个所述胶片在多个部位进行多次透照。
12.更具体而言,在本发明的焊缝无损检测方法中,在所述透照步骤中,使射线源的辐射中心方向与焊缝中心所在平面之间的夹角为10~15
°
。
13.更具体而言,在本发明的焊缝无损检测方法中,在所述透照布置步骤中准备12个胶片,所述12个胶片各自的宽度与所述焊缝的尺寸匹配,在所述透照步骤中,对各所述弧形段焊缝分别使用5个所述胶片在5个部位进行5次透照。
14.更具体而言,在本发明的焊缝无损检测方法中,所述12个胶片包括以所述直线段焊缝为对应的有效透照部位的第一胶片和第七胶片,还包括各自以所述弧形段焊缝上的不同局部部位为对应的有效透照部位的第二胶片~第六胶片以及第八胶片~第十二胶片,所述第二胶片~第六胶片各自的对应的有效透照部位彼此不重叠且各自首尾相连覆盖一个弧形段焊缝,所述第八胶片~第十二胶片各自的对应的有效透照部位彼此不重叠且各自首尾相连覆盖另一个弧形段焊缝,各所述胶片在所述焊缝周向上的宽度大于各自的对应的有效透照部位的长度。
15.更具体而言,在本发明的焊缝无损检测方法中,各所述胶片在所述焊缝周向上的宽度相比各自的对应的有效透照部位的长度在两侧各附加0.5mm。
16.更具体而言,在本发明的焊缝无损检测方法中,所述焊缝是在cicc的铠甲上开口并以双钝边对接的坡口形式焊接凸台而形成的焊缝,所述凸台具有与所述开口对应的内孔,在所述透照步骤中,使各所述胶片在所述开口和所述内孔内紧贴所述焊缝的根部,并且胶片的进入所述开口内的端部抵接所述cicc内的导体来进行透照。
17.更具体而言,在本发明的焊缝无损检测方法中,各所述胶片是厚度小于1mm且带屏蔽物质的工业胶片。
18.更具体而言,在本发明的焊缝无损检测方法中,采用单壁成像技术进行透照。
19.发明效果
20.于是,如上所述,本发明针对小尺寸(此处的小尺寸例如在跑道型焊缝的情况下指弧形段直径小于30mm,或者,在椭圆型焊缝的情况下指短轴尺寸小于30mm,或者,也可以对于任意的闭合形状焊缝,表示其短尺寸方向上的尺寸小于30mm)的跑道型焊缝提出一个多次透照曝光的x射线检测技术,通过增加曝光次数,实现焊缝的100%检测。
21.从而,通过采用本发明的焊缝无损检测方法,对于小尺寸的异型焊缝能够保证多角度的缺陷完全检出,即,使用平面的胶片绕异型焊缝一周在不同的位置紧贴焊缝进行多次x射线透照,能够采用单壁成像技术实现焊缝全体积检测。其具有操作过程简便、成本低、易控制、信号易于定位识别的优点,为核聚变装置的磁体制备过程中批量氦进出口焊缝的检测提供了有效可行的方法。
附图说明
22.图1是应用本发明的焊缝无损检测方法的cicc的示意图,其表示的是尚未开凿开口以及焊接凸台的状态,(a)示意性地表示了cicc中超导线缆在铠甲中插通的状态,(b)为(a)的截面图,(c)示意性地表示了单根铠甲的结构。
23.图2是表示氦进出口凸台的结构的示意图,其中,(a)是立体图,(b)是正视示意图,(c)是俯视示意图。
24.图3是表示焊缝的图,其中(a)示意性地表示了凸台200焊接在cicc100的铠甲103上的焊缝的位置,(b)示意性地表示了焊缝的形状。
25.图4是表示本发明的焊缝无损检测方法中的布置方式的示意图。
26.图5是表示本发明的焊缝无损检测方法的透照次数的说明图。
27.图6是本发明的焊缝无损检测方法的流程图。
具体实施方式
28.下面结合附图,对本发明的具体实施方式进行说明。
29.应当理解,所有附图都只是代表性的示意图,它们用于辅助理解发明的技术思想,并不限定具体的形状、尺寸、位置关系。
30.以下实施方式中,在提及要素的数字等(包括个数、数值、量、范围等)的情况下,除了特别明确说明的情况和从原理上明显限定为特定数字的情况之外,并不限定于该特定数字,可为特定数字以上或以下。本技术中,“使用
……
构成”或“由
……
构成”这样的表述仅表示了主要的构成部件,并不排除包括其他的部件。
31.另外,在以下的实施方式中,其结构要素(包括步骤要素等)除了特别明确说明的情况和从原理上明显理解为是必须的情况之外,都不一定是必须的,并且也可以包括说明书中未明确提及的要素。
32.本说明书中描述的实施方式仅为一个完整描述的示例,并不限定本发明的保护范围,基于本发明的实施方式,本领域技术人员在没有付出创造性劳动前提下能够获得的所有其他实施方式,都属于本发明保护的范围。
33.[实施方式]
[0034]
本实施方式的焊缝无损检测方法所针对的是,在管内电缆导体cicc的铠甲上开凿开口(例如氦进出口)并形成坡口然后在该开口处焊接凸台(例如氦进出凸台)而形成的焊缝(例如是跑道型焊缝)。
[0035]
图1是应用本发明的焊缝无损检测方法的cicc100的示意图,其表示的是尚未开凿开口以及焊接凸台的状态。图1中,(a)示意性地表示了cicc中超导线缆在铠甲中插通的状态,(b)为(a)的截面图,(c)示意性地表示了单根铠甲的结构。
[0036]
图1所示的cicc100包括中心螺旋管101、超导电缆102和铠甲103。其中,中心螺旋管101为金属例如不锈钢制成的管道,在工作过程中可供液氦等低温流体流动以降低超导电缆102的温度,维持超导电缆102的超导状态。
[0037]
超导电缆102由各向同性的超导线与其它金属线(例如铜线)多级绞制而成,例如图1所示,超导电缆102包括6根子缆,各子缆可进一步包括多个次级子缆,而各次级子缆可以进一步包括多个次次级子缆,如此类推,构成了具有低空隙率、多股、多层级的不规则螺
旋结构。如图1中(a)、(b)所示,超导电缆102被包裹在中心螺旋管101的周围,因此下文中有时也将超导电缆102和中心螺旋管101整体称作“超导电缆102”。
[0038]
单根铠甲103整体外形为方管状,截面接近正方形,内部形成有管腔104从而具有外方内圆的结构。管腔104供超导电缆102插通,起到承力和液氦冷却剂容器的功能。
[0039]
铠甲103由金属例如316l不锈钢构成,外形尺寸例如是54.2mm
×
54.2mm,管腔104直径例如为38mm,管腔直径接近超导电缆102的外径。在聚变装置中,构成超导磁体的cicc100整根长度接近上千米,其铠甲由多个图1中(c)所示的单根的铠甲103焊接构成。
[0040]
在工作过程中,为了使超导电缆102的材料(例如nb3sn、nbti等)呈现超导态,对cicc100的中心螺旋管101内和超导电缆102所处的管腔104中均供给液氦,并可以进一步通过分配中心区和电缆区的液氦流速、流量等参数,调整cicc100的冷却效果。
[0041]
为了对铠甲103的管腔104内供给液氦,需要在铠甲103上开凿开口(例如液氦进口和液氦出口)并在开口处焊接凸台,再将与液氦源或液氦回收部连接的液氦管焊接在凸台上。并且,使来自液氦源的液氦从液氦进口流入管腔104内,液氦在管腔104内流动并冷却超导电缆102,然后从液氦出口流出到液氦回收部,流出到液氦回收部的液氦可以在经过冷却处理后重新返回液氦源。由此,位于铠甲103的管腔104内的超导电缆102能够被冷却到液氦温度,使超导电缆的材料呈现超导态。
[0042]
基于对铠甲及超导电缆的保护,经过力学分析、安全系数分析等,将氦进出口的焊缝设计为异型的跑道型焊缝。制备流程分为:铠甲上堆焊凸台、铠甲上制造氦孔以及焊接坡口、焊接氦进出口凸台。这里的氦进出口凸台当然是与异型的跑道型焊缝对应的形状。
[0043]
具体地,图2是表示氦进出口凸台200的结构的示意图,其中,(a)是立体图,(b)是正视示意图,(c)是俯视示意图。为便于说明,图中标注了x、y、z方向,但这些方向并不代表实际的水平、垂直方向。
[0044]
凸台200由金属例如与铠甲103相同的316l不锈钢构成,形状近似为中空的筒状,内孔的形状、尺寸与铠甲上开设的氦进出口的形状、尺寸相当。凸台200在cicc100的铠甲上可以设置有多个,例如至少2个,也可以根据需要大量设置。凸台200的沿内孔轴向的一端201(称作“铠甲端”)与铠甲焊接,另一端202(称作“氦管端”)与液氦管连接。如图2中(c)所示,凸台200的截面(俯视形状)为跑道型,包括两个平行的直线段203和两个将直线段彼此连接的弧形段204。
[0045]
另外,凸台200的形状不受图2示意图的限定。在本发明中,凸台200可以通过双钝边对接的形式焊接到铠甲上,因此如图2中(b)所示在铠甲端201和氦管端202处均形成了坡口,不过,氦管端202的形状只要能够适合于与液氦管连接即可,不限于图2所示形状。
[0046]
图3是表示焊缝的图,其中(a)示意性地表示了凸台200焊接在cicc100的铠甲103上的焊缝的位置,(b)示意性地表示了焊缝的形状。图3中(a)例如是沿cicc100的长度方向的截面图(例如是yz面),凸台内孔205与cicc100的铠甲103上的氦进出口105的形状、尺寸相当。用黑色区域表示了焊缝300,其为不等厚焊缝。焊缝300形成在凸台200的铠甲端201的坡口处,如图3中(b)所示,沿z方向观察时焊缝为跑道型,其形状与凸台200的截面形状对应,包括两个彼此平行的直线段焊缝301、303和两个将直线段焊缝彼此连接的180
°
的弧形段焊缝302、304。
[0047]
图4是表示本发明的焊缝无损检测方法中的布置方式的示意图。
[0048]
本发明的焊缝无损检测方法使用x射线检测技术。具体而言,使射线源产生的x射线穿过被检工件,由于工件中有缺陷的部位(如气孔、非金属夹杂等)与无缺陷部位对射线的吸收能力不同,一般情况是透过有缺陷部位的射线强度高于无缺陷部位的射线强度,因此可以通过检测透过被检工件后的射线强度差异,来判断被检工件中是否存在缺陷。
[0049]
于是,通过使x射线穿过被检工件后在例如工业胶片上成像,能够通过胶片上的影像,实现被检工件内部体积型及面积型缺陷的识别,具有直观,高灵敏度等优点。
[0050]
图4是沿cicc100的长度方向观察到的例如xz面的截面图。图中400是射线源,向焊缝300上的透照部位以倾斜角α出射射线,该倾斜角α例如可以定义为射线辐射中心方向与焊缝中心所在平面(图中为xy面)之间的夹角。
[0051]
发明人经过研究发现,当该倾斜角α为10~15
°
时,胶片黑度差异较小,清晰度较高,故优选为该角度。
[0052]
如图4所示,凸台200被焊接在cicc100的铠甲103上开设了氦进出口105的位置。使用例如铅制的支承板401支承胶片402,将胶片402经凸台内孔205插入氦进出口105中,使胶片紧贴焊缝300的根部(对应于径向内侧),并且使胶片402的插入到氦进出口105内的端部抵接超导导体102,由此确保透照时胶片能够可靠地、完整地呈现透照部位的像。
[0053]
图5是表示本发明的焊缝无损检测方法的透照次数的说明图。图5的视图与图3中(b)相同,表示了沿z方向观察焊缝300的状态(省去了凸台200)。图中沿焊缝300的周向标注了次数1~12,但顺序并不限定于此,可以相反或为任意的顺序。
[0054]
如图5所示,本发明的焊缝无损检测方法对跑道型焊缝300进行检测时采用了12次透照。每次透照使用不同的胶片,具体而言,发明人经过研究发现,在焊缝300满足本发明作为前提的“小尺寸”(例如,在跑道型焊缝的情况下指弧形段直径小于30mm,或者,在椭圆型焊缝的情况下指短轴尺寸小于30mm,或者,也可以对于任意的闭合形状焊缝,表示其短尺寸方向上的尺寸小于30mm)的情况下,在焊缝300的直线段焊缝301、303处可以各使用1个胶片进行一次透照,在180
°
的弧形段焊缝302、304处可以各使用5个胶片在不同部位进行五次透照,由此能够保证多角度的缺陷完全检出。即,使用平面的胶片绕异型的焊缝一周,在不同的位置紧贴焊缝进行多次(直线段1次,弧形段多次)x射线透照,能够采用单壁成像技术实现焊缝全体积检测。
[0055]
所使用的12个胶片的尺寸与焊缝300的尺寸对应。为方便起见,与图5所示的透照次数对应地将各次透照使用的胶片分别称作“胶片1”、“胶片2
”……“
胶片12”。胶片1和胶片7的宽度(这里指焊缝周向上的长度)可以相同,以直线段焊缝301、303为对应的有效透照部位,它们的宽度满足的条件是大于该对应的有效透照部位的长度,例如可配置成在两侧各附加长度0.5mm。同样的,胶片2~胶片6各自以弧形段焊缝303上的局部焊缝为对应的有效透照部位,各自的对应的有效透照部位彼此不重叠,且它们首尾相连起来能够覆盖整个弧形段焊缝303,各胶片的宽度同样大于各自对应的有效透照部位的长度,例如可配置成在两侧各附加长度0.5mm。胶片8~胶片12与胶片2~胶片6同理。
[0056]
使用图6说明本发明的焊缝无损检测方法的流程。图6是本发明的焊缝无损检测方法的流程图。
[0057]
本发明中,针对小尺寸(例如,在跑道型焊缝的情况下指弧形段直径小于30mm,或者,在椭圆型焊缝的情况下指短轴尺寸小于30mm,或者,也可以对于任意的闭合形状焊缝,
表示其短尺寸方向上的尺寸小于30mm)的跑道型焊缝提出一个多次透照曝光的x射线检测技术,通过增加透照次数,实现焊缝的100%检测。
[0058]
具体而言,如图6所示,首先在步骤s601的透照布置步骤中,准备与cicc100的铠甲103与凸台200间的焊缝300的尺寸匹配的多个胶片,该胶片例如是厚度小于1mm且自带屏蔽物质的工业胶片。更具体而言,准备多个与焊缝300的直线段、弧形段分别对应的例如12个胶片。各胶片的宽度根据焊缝的周长确定,具体宽度如前文所述。
[0059]
接着,在步骤s602的透照步骤中,通过支承板401支承胶片402将其经凸台内孔205插入氦进出口105内,使胶片紧贴焊缝300的根部,并且使胶片402的插入到氦进出口105内的端部抵接超导导体102,使用射线源400发射射线进行透照。12个胶片分别用于焊缝300上不同部位的透照曝光,按照图5所示,在焊缝300的直线段焊缝301、303处各使用1个胶片进行一次透照,在180
°
的弧形段焊缝302、304处各使用5个胶片在不同部位进行五次透照,共进行12次透照。并且,在透照时如图4所示,使射线源400向焊缝300上的透照部位以倾斜角α出射射线,该倾斜角α为10~15
°
。
[0060]
结束了步骤s602的12次透照后,在步骤s603的胶片处理步骤中,将曝光后的胶片放置在自动洗片机中处理,确保焊缝影像清晰呈现。胶片处理完成后将其放置在烘干箱中,用于后一步的缺陷评定。
[0061]
然后,在s604的评定步骤中,在评定室中对完成了胶片处理的胶片进行评定。评定的方法可以采用任意的现有方法,例如可以目视评定,也可以将胶片上的影像数据化,使用经过例如机器学习等方法训练得到的评定模型来进行评定。
[0062]
通过对影像的评定分析,确定焊缝300整周上的缺陷的大小及类型,并对焊缝300最终的等级进行综合评定。
[0063]
通过采用本发明的焊缝无损检测方法,对于小尺寸的异型焊缝能够保证多角度的缺陷完全检出,即,使用平面的胶片绕异型焊缝一周在不同的位置紧贴焊缝进行多次x射线透照,能够采用单壁成像技术实现焊缝全体积检测。其具有操作过程简便、成本低、易控制、信号易于定位识别的优点,为核聚变装置的磁体制备过程中批量氦进出口焊缝的检测提供了有效可行的方法。
[0064]
以上对本发明的焊缝无损检测方法应用于cicc导体的氦进出口凸台的焊缝检测的情况进行了说明,但应当理解,本发明不限于该情况,例如,焊缝可以不必形成于外方内圆结构的铠甲上,也可以是其他形状例如小方管等,被检测工件也可以不必是焊接了凸台的cicc导体,事实上,本发明可以应用于任意小尺寸不规则的孔形焊缝的无损检测。
再多了解一些
本文用于企业家、创业者技术爱好者查询,结果仅供参考。