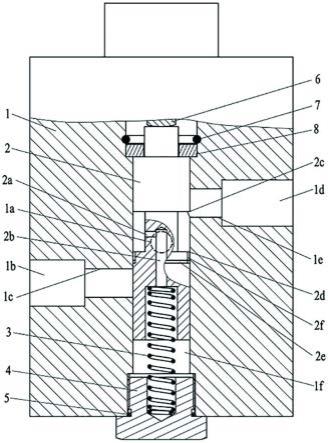
1.本实用新型涉及液压滑阀技术,具体为阀芯带有预升压槽的三通压力控制阀技术。
背景技术:
2.液压滑阀是液压控制阀最常见的阀芯结构形式,在液压系统中具有广泛的应用。液压滑阀的阀芯和阀体之间通过圆柱面滑动配合间隙形成非接触密封,阀芯上具有若干沉割槽,阀芯在阀孔中相对位置的改变使得沉割槽连通不同的油口,实现油路的通断控制。
3.三通减压阀的阀芯为全周开口滑阀式,初始状态压力油口截止,负载油口与回油口连通,快速换向时,回油口截止,压力油口与负载油口快速接通,接通瞬间高压油液经节流边以射流形式充入与负载油口接通的零压沉割槽腔,会产生气泡的析出,随着油液的继续充入,沉割槽腔压力升高,析出的气泡在高压区被压破,产生噪声,当气泡在近壁面处被压破时还会对固体壁面产生剥蚀,这会对阀的控制性能产生严重影响。另外,o型、y型、u型、n型、j型中位机能的换向阀在换向时也存在上述问题。
4.检索现有公开文献专利发现关于液压滑阀换向时的冲击和空化噪声的研究主要有:文献“电液换向阀换向阀冲击研究”(孙军,哈尔滨工业大学,2019)建立了液压滑阀流场三维cfd模型,仿真分析了u形、v形节流槽对阀口打开瞬间压力冲击的消减作用,为液压滑阀设计和优化提供了参考。文献“减少液控换向阀换向冲击的方法”(周志强.重型机械,2005(05):55-56.)分析了液压滑阀换向瞬间产生液压液压冲击并造成振动和噪声的原因与危害,提出在换向阀p口安装减压阀可以有效减少冲击。专利“一种起重机液压系统及其抗冲击阀”(cn202023785u)提出在阀芯节流边设置截面积逐渐变化的节流槽来达到抗冲击的作用。
5.上述研究及专利,为液压滑阀换向冲击与噪声的消减在理论机理方面提供了一定的参考,专利中提出的在阀芯节流边设置两个以上节流槽的技术适用于p口与阀孔交界处具有环形沉割槽的滑阀结构,具有一定的局限性。
技术实现要素:
6.本实用新型的目的是提供一种阀芯带有预升压槽的三通压力控制阀。
7.本实用新型是一种阀芯带有预升压槽的三通压力控制阀,包括阀体1,阀芯2,弹簧3,螺堵4,o形密封圈5,驱动杆6,孔用开口挡圈7,挡圈8,所述阀芯2装在阀体1的阀孔1f中,阀芯2的一端与驱动杆6接触,并由挡圈8与孔用开口挡圈7限位,阀芯2的另一端通过弹簧3与螺堵4限位,阀孔1f的一端由驱动杆6的驱动装置封闭,阀孔1f的另一端由螺堵4和o形密封圈5进行封闭和密封;阀体1设有负载油口1a、压力油口1b和回油口1d,阀芯2在阀孔1f中的初始安装位置形成负载油口1a与回油口1d连通、压力油口1b封闭的状态。
8.与现有技术相比,本实用新型的有益效果是:保证阀肩足够密封长度的前提下,在阀芯的压力油口节流边阀肩处设置尺寸合理的环形槽和直槽,或螺旋槽和直槽,使得压力
油在压力油口与负载油口接通之间小流量充入负载腔,实现负载腔的预升压,实现抗液压冲击的效果,消减气泡的析出,进而消减空化、气蚀及噪声;另外,环形槽和螺旋槽的设置可以提高阀芯阀体的间隙润滑,减小阀芯侧向力。
附图说明
9.图1是本实用新型的结构示意图,图2是本实用新型阀芯开设“环形槽+直槽”结构示意图,图3是本实用新型阀芯开设“螺旋槽+直槽”结构示意图。图中:1-阀体;1a-负载油口;1b-压力油口;1c-压力油口节流边;1d-回油口;1e-回油口节流边;1f-阀孔;2-阀芯;2a-径向小孔;2b-中心盲孔;2c-节流边1;2d-节流边2;2e-环形槽;2f-直槽1;2ee-螺旋槽;2ff-直槽2。
具体实施方式
10.本实用新型是一种阀芯带有预升压槽的三通压力控制阀,包括阀体1,阀芯2,弹簧3,螺堵4,o形密封圈5,驱动杆6,孔用开口挡圈7,挡圈8,所述阀芯2装在阀体1的阀孔1f中,阀芯2的一端与驱动杆6接触,并由挡圈8与孔用开口挡圈7限位,阀芯2的另一端通过弹簧3与螺堵4限位,阀孔1f的一端由驱动杆6的驱动装置封闭,阀孔1f的另一端由螺堵4和o形密封圈5进行封闭和密封;阀体1设有负载油口1a、压力油口1b和回油口1d,阀芯2在阀孔1f中的初始安装位置形成负载油口1a与回油口1d连通、压力油口1b封闭的状态。
11.以上所述的阀芯带有预升压槽的三通压力控制阀,所述阀芯2的节流边2 2d所在阀肩处设有环形槽2e和直槽1 2f,直槽1 2f连通环形槽2e和负载油口1a所在的阀杆腔,直槽1 2f的数量为1~2个,初始状态时,直槽1 2f的长度与环形槽2e的宽度之和为d1,压力油口节流边1c到节流边2 2d的距离为d2,回油口节流边1e到节流边1 2c的距离为d3,在满足d2-d3≥d1的条件下直槽1 2f长度取大值。
12.以上所述的阀芯带有预升压槽的三通压力控制阀,所述阀芯2的另一种形式为节流边2 2d所在阀肩处设有螺旋槽2ee和直槽2 2ff,螺旋槽2ee靠近节流边2 2d的一端为起始端,另一端为末端,直槽2 2ff与螺旋槽2ee起始端连通,接通螺旋槽2ee和负载油口1a所在的阀杆腔,螺旋槽2ee的螺距不小于宽度的5倍,末端一圈的螺距可以小于其它段的螺距,初始状态时,螺旋槽2ee末端与节流边2 2d的距离为d4,要满足d2-d3≥d4。
13.以上所述的阀芯带有预升压槽的三通压力控制阀,所述阀体1的压力油口1b与阀孔1f相交处无环形沉割槽。
14.以上所述的阀芯带有预升压槽的三通压力控制阀,所述驱动杆6的驱动方式包括液动、机械驱动和电磁驱动。
15.下面将结合本实用新型实施例中的附图,对本实用新型实实施例中的技术方案进行清楚、完整的描述,显然,所描述的实施例仅仅是本实用新型一部分实施例,而不是全部的实施例。基于本实用新型的实施例,本领域普通技术人员在没有做出创造性劳动前提下所获得的所有其他实施例,都属于本实用新型保护的范围。
16.如图1~图3所示,本实用新型是一种阀芯带有预升压槽的三通压力控制阀,阀芯2装在阀体1的阀孔1f中,阀芯2的一端与驱动杆6接触,并由挡圈8与孔用开口挡圈7限位,阀芯2的另一端通过弹簧3与螺堵4限位,阀孔1f的一端由驱动杆6的驱动装置封闭,阀孔1f的
另一端由螺堵4和o形密封圈5进行封闭和密封;阀体1设有负载油口1a、压力油口1b和回油口1d,阀芯2在阀孔1f中的初始安装位置形成负载油口1a与回油口1d连通、压力油口1b封闭的状态。
17.进一步的,所述阀芯2的节流边2 2d所在阀肩处设有环形槽2e和直槽1 2f,直槽1 2f连通环形槽2e和负载油口1a所在的阀杆腔,环形槽2e的宽度和深度为0.4~1mm,直槽1 2f的宽度为1~2mm,深度为0.4~1mm,直槽1 2f的数量为1~2个,2个直槽对称布置,初始状态时,直槽1 2f的长度与环形槽2e的宽度之和为d1,压力油口节流边1c到节流边2 2d的距离为d2,回油口节流边1e到节流边1 2c的距离为d3,在满足d2-d3≥d1的条件下直槽1 2f长度取大值。
18.进一步的,所述阀芯2的另一种形式为节流边2 2d所在阀肩处设有螺旋槽2ee和直槽2 2ff,螺旋槽2ee靠近节流边2 2d的一端为起始端,另一端为末端,直槽2 2ff与螺旋槽2ee起始端连通,接通螺旋槽2ee和负载油口1a所在的阀杆腔,螺旋槽2ee的深度和宽度为0.4~1mm,圈数为1.5~3圈,螺距不小于宽度的5倍,末端一圈的螺距可以小于其它段的螺距,直槽2 2ff的宽度为1~2mm,深度为0.4~1mm,长度为2~3mm,初始状态时,螺旋槽2ee末端与节流边2 2d的距离为d4,要满足d2-d3≥d4。
19.进一步的,所述阀体1的压力油口1b与阀孔1f相交处无环形沉割槽。
20.进一步的,所述驱动杆6的驱动方式包括液动、机械驱动和电磁驱动。
21.本实用新型的工作过程为:阀体上各油口的初始状态为压力油口截止为有压,负载油口与回油口连通为零压;当驱动杆在外力作用下推动阀芯沿阀孔向下位移时,d2和d3会逐渐减小,且d2大于d3,因此负载油口与回油口会先断开,由于d2-d3≥d1,故负载油口与回油口断开时压力油口与负载油口未连通,压力油口节流边与阀芯节流边2的距离不小于d1,形成了过渡位置的三口截止状态;阀芯继续向下位移,则压力油口先与环形槽(或螺旋槽末端一圈)某处连通,压力油会依次流经环形槽(或螺旋槽)与直槽1(或直槽2)充入与负载油口连通的阀腔;阀芯再向下位移d1的距离后,压力油口与负载腔连通,油液大量流向负载腔。在阀芯向下位移d1过程中,压力油口与负载腔之间通过预升压槽(环形槽 直槽,或螺旋槽 直槽)连通,使得负载腔中的压力在油口大开之前逐渐升高,实现抗液压冲击的效果,消减气泡的析出,进而消减空化、气蚀及噪声;另外,环形槽和螺旋槽的设置可以提高阀芯阀体的间隙润滑,减小阀芯侧向力。
22.尽管已经示出和描述了本实用新型的实施例,对于本领域的普通技术人员而言,可以理解在不脱离本实用新型的原理和精神的情况下可以对这些实施例进行多种变化、修改、替换和变型,本实用新型的范围由所附权利要求及其等同物限定。
再多了解一些
本文用于企业家、创业者技术爱好者查询,结果仅供参考。