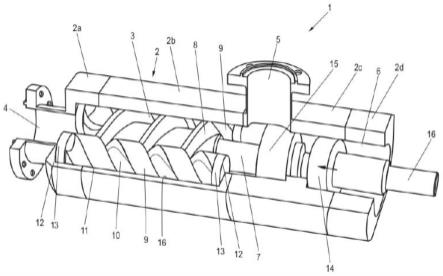
1.本发明涉及一种螺杆泵,所述螺杆泵包括壳体和容置于其中的驱动主轴以及至少一个与所述驱动主轴啮合的从动主轴,其分别具有两个末端端面。
背景技术:
2.螺杆泵用于输送各种物质,主要是流体介质。众所周知,螺杆泵包括壳体,其中容置有包括从壳体引出并且与驱动电机(视情况在中间连接传动装置的情况下)耦合的驱动主轴以及一个或多个从动主轴的主轴组,从动主轴的主轴型线与驱动主轴的主轴型线啮合并通过驱动主轴而被驱动。其中容置有主轴组的壳体可以是同样朝外封闭的泵壳体或设计为插入外壳中的嵌件的壳体。
3.通常轴向地对以平行且错开180
°
的方式布置在驱动主轴旁边的一个或多个(在大多数情况下是两个)从动主轴进行液压支撑,为此可以以与各个从动主轴的端面相邻的方式设置一个喷嘴孔口,通过喷嘴孔口,待输送的流体的被馈送分量流向主轴端面,以便建立轴向支撑压力,通过该支撑压力对各个从动主轴进行轴向支撑。这取决于壳体的相应设计,其中必须设有通过适当的通道进行的相应流体供应以及相应的喷嘴孔口,这些喷嘴孔口也必须在几何形状上相应地进行设计以产生相应的流体压力。
4.螺杆泵还越来越多地用于食品和制药领域,即借助螺杆泵来输送相应的流体食品或药物。采用此类物质进行工作需要高度的卫生,因此,也必须以相应短的间隔对所使用的螺杆泵进行清洁。基于螺杆泵在用于对包括相应通道等的从动主轴进行轴向支撑的流体导引方面的复杂设计等,为了进行清洁,需要对螺杆泵进行拆除和拆卸以进行清洗,以便确保对所有区域进行清洁。因为基于附加通道、喷嘴孔口等的集成,会产生相当大的容积,其不参与实际输送过程,即类似地作为死区而存在,但仍然会暴露于流体。
技术实现要素:
5.因此,本发明基于以下问题:提出一种改进的螺杆泵。
6.为了解决该问题,就开篇所述及的类型的螺杆泵而言,本发明提出,以与从动主轴的至少一个端面轴向相邻的方式设有止推面,其中所述从动主轴借助轴向间隙以可垂直于止推面移动的方式容置。
7.在根据本发明的螺杆泵中,未设有液压轴向推力平衡。确切而言,或者例如在设有两个从动主轴的情况下,每个从动主轴至少在一侧上轴向地分别对应有一个止推面,其中所述从动主轴以与所述止推面形成较小的轴向间隙的方式容置。因此,所述止推面处于实际的泵室中。在工作期间驱动驱动主轴。基于型线卡合或液压压力,所述一个或两个从动主轴也随驱动主轴一同旋转,从而输送流体通过泵室。驱动主轴自身在很大程度上是液压平衡的,亦即,由于工作原因,没有或仅有可忽略不计的轴向力作用于驱动主轴。具体实现方式在于,相对于壳体对驱动主轴进行密封的密封元件的受压表面,即处于压力作用下的表面与驱动主轴型线的受压型线表面基本相同。沿不同方向轴向地对两个表面进行加压,因
此产生了力的平衡,从而使得驱动主轴液压平衡。在工作过程中,从动主轴在这些止推面或其中之一的方向上仅经历由泵压力而引起的轻微轴向偏移。如果泵是不可逆的,则止推面设置在从动主轴的吸入侧或吸入侧末端上,因为从动主轴在工作期间会略微向吸入侧移动。如果泵是可逆的,则每个从动主轴设有两个止推面,以便根据输送方向和从动主轴的运动方向在两侧设置止推面。如果驱动主轴泵在输送方向上是可逆的,则视具体工作方向而言,以朝向一个止推面或另一止推面的方式进行偏移。基于较小的轴向间隙,可以进行偏移,其中可以针对产生的最大偏移来设计轴向间隙。在工作期间,从动主轴的各个端面可以向各个轴向止推垫圈移动,在该处,端面理想地通过薄液压润滑膜进行支承,或者,如果端面向推力面移动,则摩擦力是可忽略不计的。亦即,尽管朝向止推面进行止推,一方面,在止推面如上所述处于泵室中之后,还是通过待输送的流体实现相应的支承和润滑,另一方面,也不会发生磨损。
8.因此,根据本发明的螺杆泵一方面能够对从动主轴进行相应的轴向支撑,但除了集成两个止推垫圈之外,没有为此采用任何特定措施。待输送的流体流经的唯一容积是泵室,其几乎是优化了死区。这又意味着,在进行清洁的情况下,不必对根据本发明的螺杆泵进行拆卸,因为在清洁流体可以毫无问题地相应地冲洗泵室之后,可以在安装状态下进行该清洁过程。也就是说,借助根据本发明的螺杆泵可以实现所谓的“原位清洗(cip)”。
9.如已描述过的那样,在采用不可逆的泵的情况下,只有所述从动主轴或每个从动主轴的吸入侧端面可以对应有一个止推面。在采用可逆的泵的情况下,可以以与所述从动主轴的两个端面轴向相邻的方式设置止推面,其中在此情况下,所述从动主轴借助轴向间隙容置在两个止推面之间。
10.如上所述,主轴组是液压同步的,也就是说,其在操作过程中自动进行调节。特别是在驱动主轴与从动主轴之间不存在机械力传递或仅存在可忽略不计的机械力传递,从而引起从动主轴在工作期间的最小轴向偏移。因此,从动主轴与轴向止推面之间的轴向间隙也可以相应地设计得较小,当然这取决于螺杆泵的给定的结构尺寸。轴向间隙优选在0.3mm(就结构尺寸较小的螺杆泵而言)与5.0mm(就结构尺寸特别大的螺杆泵而言)之间,优选在1.0-3.0mm之间的范围内。针对从动主轴的给定的轴向偏移对间隙进行设计,其中这些给定的值是指各个从动主轴在两个止推垫圈之间的总间隙。
11.就实现止推面而言,设有不同的方案。因此,所述止推面或每个止推面可以借助壳体上的涂层而形成。在此,在壳体侧设有一个或多个相应的壳体凸肩,其形成止推面的基础,所述止推面借助所述壳体凸肩的涂层而实现。作为替代方案,所述止推面或每个止推面也可以借助止推垫圈而实现。在此,为例实现止推面,将特定的止推垫圈插入壳体的相应位置处。通过止推垫圈的厚度可以非常精确地调节该间隙。
12.优选将极耐磨的表面设置为止推面,亦即,使用相应的耐磨材料。为此适用由陶瓷或碳化材料或者由包含陶瓷或碳化材料的复合材料制成的涂层或止推垫圈。也就是说,原则上使用工业陶瓷,其视需要可以借助玻璃或碳纤维加以增强。有利的是,使用基于硅的陶瓷材料或工业陶瓷,其中为此特别是适用sic或si3n4,或者使用wc,如上所述,该材料也可以视需要进行纤维增强。也可以采用cr2o3。作为替代方案,也可以使用硬质合金来形成涂层,止推垫圈也可以由硬质合金制成或者可以具有硬化表面。该硬度应至少为1000hv。因此,类似于由钢制成且优选经特殊表面硬化技术(科尔斯特林技术kolsterising)处理或经低温
氮化的从动主轴,这些止推面或涂层或轴向垫圈不易磨损,这些从动主轴如上所述理想地通过液体静压的润滑膜滑动支承在这些止推面或涂层或止推垫圈上。
13.所述或每个从动主轴容置在相应的从动主轴钻孔中,所述从动主轴钻孔与容置所述驱动主轴的驱动主轴钻孔重叠,其中所述一个或两个从动主轴钻孔被一个或两个轴向壳体台肩轴向限制,各个止推面构建在所述壳体台肩上或者止推垫圈支撑在所述壳体台肩上。因此,在壳体中设有定义的台肩,其用作涂层的载体或止推垫圈的轴向支撑点。也就是说,直接在这种壳体凸肩上施覆涂层,或者,止推垫圈贴靠在这种壳体凸肩上。在此情况下,可以非常精确地对两个壳体台肩之间的轴向距离进行定义和调节,从而可以建立定义的几何关系并且也可以在使用单独的止推垫圈时,通过选择相应的止推垫圈厚度来相应地对各个从动主轴的轴向间隙进行精确调节。
14.如上所述,所述驱动主轴优选液压平衡,因此,不会有沿某一方向推动所述驱动主轴的显著轴向力作用于所述驱动主轴,所述轴向力又会引起所述从动主轴的位移。只要型线卡合允许,就能在利用轴向间隙的情况下,仅通过泵壳体中产生的压力略微轴向地移动几乎轴向悬臂式支承的从动主轴。在此情况下,驱动主轴和从动主轴容置在泵室中,泵室通过在驱动主轴与壳体之间进行密封的密封元件,优选单个密封元件,相对于驱动主轴的驱动侧进行密封。也就是说,泵室的一侧仅通过一个密封元件进行密封。根据本发明,针对驱动主轴的尺寸和几何形状,所述密封元件选择或设计为使得所述密封元件的轴向受压表面基本上对应于所述驱动主轴或所述驱动主轴型线的轴向受压表面。为此进行轴向液压平衡,其在主轴组的液压同步和工作期间产生的轴向从动主轴偏移的最小化方面经证实是特别有利的。被驱动主轴贯穿的环形密封元件的受压表面最终相当于其朝向泵室的轴向环面。沿主轴纵向来看,驱动主轴的受压表面如已知的那样由从主轴芯部径向突出的主轴型线的多个部分呈镰刀形的表面区段组成,这是由主轴型线与从动主轴的两个主轴形成的卡合而引起的。两个受压表面之间的差异应最大为10%,优选最大仅为5%,当然,在理想情况下为零,因此,即使有的话,也只会产生非常小的轴向力,其既不会致使驱动主轴发生轴向偏移,也不会引起主轴轴承结构上的显著负载。
15.所述密封元件自身优选是机械密封件,其优选布置在所述驱动主轴上并且相对于所述壳体上的相应密封区段或密封座进行密封。
16.所述驱动主轴自身有利地在具有所述工作和从动主轴的泵室外部的仅一侧上径向旋转支承在所述壳体中,所述驱动主轴以一个区段从所述泵室引出。为此,有利地使用径向轴承,其中优选仅使用单个径向轴承。径向轴承可以是形式为球轴承、滚子轴承或球面滚子轴承等的单排或多排轴承,即滚动轴承。基于驱动主轴的给定的液压平衡亦即两个从动主轴以错开180
°
的方式布置在驱动主轴旁边的布局,可以仅使用一个简单的径向轴承,因为径向轴承基于相应的力平衡在工作过程中几乎是无负载的。
17.本发明的一种有利的改进方案提出,至少所述或每个从动主轴钻孔内衬有一个滑动衬垫,其中所述从动主轴以与所述滑动衬垫形成径向间隙的方式布置。借助滑动衬垫对从动主轴钻孔进行内衬也用于缩小可能的死区。因为在正常工作中,从动主轴不会发生径向运动,确切而言,在主轴侧面与从动主轴钻孔或滑动衬垫之间同样产生对从动主轴进行支承的薄液压润滑膜。这样便又能通过滑动衬垫相应地实现径向从动主轴间隙的最小化,进而也相应地缩小死区。
18.有利地将塑料衬垫,特别是由氢化丁腈橡胶(hnbr)、三氟氯乙烯、三元乙丙橡胶(epdm)、聚四氟乙烯(ptfe)、全氟烷氧基聚合物、氟橡胶(fkm)或全氟橡胶(ffkm)构成的塑料衬垫,用作这种滑动衬垫。然而,所列并不是详尽无遗的,确切而言,也可以使用其他合适的塑料材料,只要这些塑料材料适用于待输送的介质。
19.优选地调节所述滑动衬垫的厚度,使得所述径向间隙在0.01-1.00mm之间,特别是在0.05-0.5mm之间。亦即,在此设有极小的径向间隙,其原因在于,在工作期间不会发生明显的径向运动。
20.除了螺杆泵的死区优化设计之外,所述螺杆泵在轴向间隙和径向间隙的最小化方面的设计还具有以下优点:与迄今为止常用的螺杆泵相比,可以大幅提高螺杆泵的效率,至多可以提高数个10%。因为基于这些最小的间隙,体积流量在较大的压力范围内保持恒定,其中几乎不会发生所输送介质的回流,因为这些给定的间隙是最小的。也就是说,结合螺杆泵的从卫生角度来看非常有利的技术方案,可以实现显著更高效的输送工作。
21.如上所述,所述螺杆泵特别是用于输送需要极高清洁度的关键物质。因此,将根据本发明的螺杆泵用于输送粘性或糊状食品、药品、化妆品或化学品。粘性或糊状食品例如可以是乳制品,如鲜奶酪、奶油、乳脂、凝乳、黄油或酸奶。也可以输送明显更加粘稠的或糊状的食品,例如番茄酱、蛋黄酱、芥末和类似食品、辣根、精制软干酪、植物油、液态蛋、生面团或果酱以及明胶、糖浆、坚果或牛轧糖奶油,巧克力、蜂蜜、杏仁膏或其他脂肪或油。在制药和化妆品领域,例如液体皂、乳霜或乳液等可被称为可输送介质。在化学领域,示例包括液体洗涤剂、洗洁精、清洁剂以及油漆等。在此,所列当然也不是详尽无遗的,但其表明可输送的材料的粘度范围非常大。可以使用根据本发明的螺杆泵进行输送的可输送物质的粘度在0.5-1百万kg
·
m-1
·
s-1
的范围内。
附图说明
22.本发明的其他优点和细节参见下面所描述的实施例和附图。其中:
23.图1为示出根据本发明的螺杆泵的第一实施方式的原理的四分之一剖视图,以及
24.图2为示出根据本发明的螺杆泵的第二实施方式的原理的四分之一剖视图。
具体实施方式
25.图1以局部剖视图示出根据本发明的螺杆泵1,其包括壳体2壳体在此示例性地由四个壳体部件2a、2b、2c和2d组成。亦即,壳体采用模块化结构。在壳体内部构建有泵室3,其具有轴向通路4和径向通路5。螺杆泵1的输送方向是可逆的,即具体视输送方向而定,通路4可以是吸入连接,通路5可以是压力连接,反之亦然。尽管在此示出了轴向通路5和径向通路4,但也可以采用不同的通路配置,例如具有两个径向通路,其也可以围绕壳体纵轴有所偏移。
26.除了压力室3之外,壳体2还具有轴承室6,如下文将描述的那样,在轴承室中对驱动主轴进行支承。
27.螺杆泵1还包括主轴组,其包括具有驱动主轴型线8的居中布置的驱动主轴7以及侧向相邻且相对彼此错开180
°
地布置的两个从动主轴9,这两个从动主轴分别具有从动主轴型线10,其中驱动主轴型线8与从动主轴型线10啮合。在该示例中示出了两个从动主轴9,
作为替代方案,也可以仅设有一个从动主轴9或者设有三个从动主轴9。
28.驱动主轴7或驱动主轴型线8容置在壳体2或壳体部件2b中的在此未示出的相应驱动主轴钻孔中,而两个从动主轴9则容置在壳体2或壳体部件2b中的相应从动主轴钻孔11中。两个从动主轴钻孔11以已知方式与驱动主轴钻孔9重叠,其中这些钻孔形成泵室3的主要部分。
29.两个壳体部件2a和2c在两个从动主轴钻孔11的区域内具有相应的壳体凸肩12,其用作分别针对于一个止推垫圈13的支撑面,这些止推垫圈彼此轴向地间隔一定距离并且在其间分别容置有一个从动主轴9。每个止推垫圈13形成一个针对轴向相邻的从动主轴9的端面的止推面或者具有这种止推面。这些止推垫圈在两侧是平面的,即平面地贴靠在相应的壳体凸肩12上,正如这些止推垫圈也平面平行于从动主轴9的相应平面端面而延伸那样。每个从动主轴9以较小的轴向间隙容置在两个止推垫圈13之间,也就是说,可以轴向地略微移动每个从动主轴,具体视螺杆泵的结构尺寸而定,轴向间隙在0.3-5.0mm之间,特别是在1.0-3.0mm之间。通过所使用的止推垫圈13的厚度来设定最大轴向间隙,从而可以实现轴向间隙的最小化并且可以实现该处的死区的最小化。
30.止推垫圈13例如为由陶瓷材料或包含陶瓷材料的复合材料制成、优选由工业陶瓷制成的垫圈。优选采用硅基材料,特别是sic或si3n4。作为替代方案,每个止推垫圈13也可以由碳化物材料制成,例如由wc制成。也可以采用由硬质合金制成的止推垫圈13。这些止推垫圈是极耐磨的止推垫圈13,其中由相应的例如经特殊表面硬化技术(科尔斯特林技术kolsterising)处理的不锈钢或经低温氮化的不锈钢制成的各个从动主轴9也相应地具有耐磨性。主轴和壳体均由防锈的不锈钢制成,其特别是适用于食品、医疗、制药和化学工业。
31.如局部剖视图所示,驱动主轴7从泵室3被导引至轴承室6中,在这个轴承室中,驱动主轴通过径向轴承14、优选形式为单排或多排球轴承或者滚子轴承或球面滚子轴承的滚动轴承支承在壳体2中。借此在单个轴承平面中实现驱动主轴7的旋转支承。这种单个轴承平面是足够的,因为(下文还将对此进行讨论)驱动主轴7在轴向上液压平衡,所以在泵工作过程中,没有或仅有可忽略不计的轴向力作用于驱动主轴7,也没有或仅有可忽略不计的由两个从动主轴7的双侧对称布局而产生的径向力作用于驱动主轴,这两个从动主轴在轴向和径向上以液压的方式受到支撑或者通过润滑膜进行支承,下面还将对此进行讨论。
32.此外,设有单个密封元件15,密封元件优选为径向机械密封件,其布置在驱动主轴7上并且相对于壳体2中的相应密封座而进行密封。整个泵室3朝向这一侧,即朝向驱动侧,通过该主轴密封件或密封平面进行密封。亦即,流体或介质只能从通路4流向通路5或反之,排除了朝向轴承侧或驱动侧的通流(实际的泵驱动器连接在相应的端部主轴接头16上)。
33.如上所述,驱动主轴7在轴向上液压平衡,因此,没有或仅有完全可忽略不计的轴向力作用于驱动主轴7。具体实现方式在于,针对驱动主轴型线8相应地对密封元件15进行设计。该设计使得密封元件15的被介质施压的面,即朝向泵室3的面,基本上与工作主轴型线8的轴向受压表面相同。沿主轴纵向来看,工作主轴型线8的轴向受压表面因工作主轴型线8与从动主轴型线10的啮合接合而以已知的方式通过工作主轴型线7的多个部分呈镰刀形的表面区段而产生,这些表面区段合计得出一个总面积。这个总面积几乎或理想地与密封元件15的朝向泵室的轴向受压的环状表面的大小完全相同。可能的面积差异应最大为10%,优选最大为5%。作用于各个面的压力彼此方向相反,因此,由于两个面都被施加相同
的压力,在理想情况下会产生完全的压力平衡,因此,驱动主轴7几乎无压力或者液压平衡,使得在理想情况下,没有或仅有可忽略不计的轴向力作用于驱动主轴。
34.但由此也不会发生从驱动主轴7到两个从动主轴的机械的力传递,因为驱动主轴在工作期间轴向位置固定。由于工作压力,从动主轴9仅发生轻微的轴向位移,这导致从动主轴9在从动主轴钻孔11中的轻微轴向运动并且致使各个从动主轴9的相应端面碰撞到各个止推垫圈13。两个相对的表面优选通过待输送的介质的薄润滑膜以液体静压的方式进行滑动支承,从而不会在该区域中产生磨损。
35.此外,为了进一步最小化死区并提高效率,由于通过给定间隙的介质回流的最小化,各个从动主轴钻孔11还配设有滑动衬垫16,其优选为由诸如hnbr、epdm、ptfe、ctfe、pfa、fkm或ffkm等塑料制成的滑动衬垫16。滑动衬垫16的厚度选择为使得在各个从动主轴9(即其外侧面)与滑动衬垫16之间仅存在最小的径向间隙,其中该径向间隙应在0.01-1.0mm之间,特别是在0.05-0.5mm之间。亦即,在此仅给定最小的间隙,因此,可以实现可能的回流的最小化,同时提高效率。在此也类似地设置相应的介质润滑膜,从动主轴9通过介质润滑膜朝向滑动衬垫16进行滑动支承,因此,此处也不会发生磨损。
36.在工作过程中,通过驱动器以已知方式驱动驱动主轴7,驱动主轴发生旋转。通过型线接合不可避免地引起从动主轴9的旋转以及介质从通路4到通路5或反之亦然(即从吸入接头到压力接头)的相应传输,取决于驱动主轴的旋转方向7。在启动期间,两个从动主轴9均如上所述因工作压力的增大和型线接合内的最小轴向间隙而最小程度地轴向移动,这两个从动主轴分别向止推垫圈13中的一个移动,在该处,这两个从动主轴优选通过待输送的介质中的润滑膜进行滑动支承。由于最小的间隙,仅产生极少的回流,从而提高效率。
37.根据图2的螺杆泵1的实施例的基本结构对应于图1所示基本结构。在此也设有示例性地包括三个壳体部件2a、2b、2c和2d的模块化壳体2。在壳体内部构建有泵室3,其具有轴向通路4和径向通路5。螺杆泵1的输送方向在此也是可逆的。除了压力室3之外,壳体2还具有轴承室6,如下文将描述的那样,在轴承室中对驱动主轴进行支承。
38.螺杆泵1在此还包括主轴组,主轴组包括具有驱动主轴型线8的中心驱动主轴7和各具有一个从动主轴型线10的两个侧向相邻且相对彼此错开180
°
地布置的从动主轴9,其中驱动主轴型线8与从动主轴型线10啮合。在该示例中示出了两个从动主轴9,作为替代方案,也可以仅设有一个从动主轴9或者设有三个从动主轴9。
39.驱动主轴7容置在壳体2中的相应驱动主轴钻孔中,而两个从动主轴9则容置在壳体2中的相应从动主轴钻孔11中。两个从动主轴钻孔11以已知方式与驱动主轴钻孔9重叠,其中这些钻孔又形成泵室3的主要部分。
40.两个壳体部件2a和2c在两个从动主轴钻孔11的区域中具有相应的壳体凸肩12。这些壳体凸肩12彼此轴向地间隔一定距离。在这些壳体凸肩之间分别容置有一个从动主轴9。每个壳体凸肩12均配设有涂层17,涂层形成针对轴向相邻的从动主轴9的端面的止推面。涂层17例如由si3n4、sic、wc或cr2o3制成并且直接施覆到各个壳体凸肩12上。从动主轴9的端面是平面的,即平面地贴靠在壳体凸肩12的相应涂层17上。每个从动主轴9以较小的轴向间隙容置在两个壳体凸肩12或耐磨的涂层17之间,也就是说,可以轴向地略微移动每个从动主轴,具体视螺杆泵的结构尺寸而定,轴向间隙在0.3-5.0mm之间,特别是在1.0-3.0mm之间。在工作过程中,从动主轴9在此也向止推面或涂层17移动并且理想地在该处通过液压润
滑膜进行支撑或滑动支承。在任何情况下,这些涂层都非常耐磨,这些从动主轴自身也是如此,以便确保长久工作。
41.在此,借助涂层17直接在壳体自身上实现止推面。在此不需要如图1所示的实施例那样布置单独的止推垫圈。但还是实现了与图1所示实施例相同的优点。
42.此外,图2所示的螺杆泵1的结构相当于图1所示示例,即在此也设有用于对驱动主轴7进行支承的径向轴承15,并且至少从动主轴钻孔11也覆盖有滑动衬垫16。因此,参考针对图1所示泵的实施方案,这些实施方案同样适用于图2所示泵。
43.在螺杆泵1不可逆的情况下,在从动主轴9在工作过程中最小程度地朝向吸入侧运动之后,每个从动主轴钻孔11仅在各个从动主轴钻孔的吸入侧末端上设有一个形成止推面的止推垫圈13或涂层17。
44.显然,根据本发明的螺杆泵采用简单的设计,因为螺杆泵不具有用于对从动主轴7的进行液压推力平衡的装置,该装置在输送食物或其他卫生敏感介质时是不利的。确切而言,螺杆泵的技术方案允许在组装状态下对其进行清洁,因为除了泵室之外没有其他可以容纳待输送的介质的容积。这样就能在安装状态下对螺杆泵进行简单的冲洗,即“原位清洗”。通过止推垫圈13的集成可以实现从动主轴9的允许轴向间隙的最小化,其中如上所述,实现直接的垫圈止推,因此,在泵室区域中不存在不利的死区。
45.通过使用三个主轴,即驱动主轴7和两个从动主轴9,能够实现更抗压的输送特性曲线,因为螺杆泵1具有非常密集的型线。这样就能以较高的计量精度进行应用。通过密集的型线还产生更好的吸入性能,从而提高效率。此外,螺杆泵1或主轴组也是液压同步的,即在工作期间自动进行调节,其中在驱动主轴7与从动主轴9之间不会发生机械的力传递。
再多了解一些
本文用于企业家、创业者技术爱好者查询,结果仅供参考。