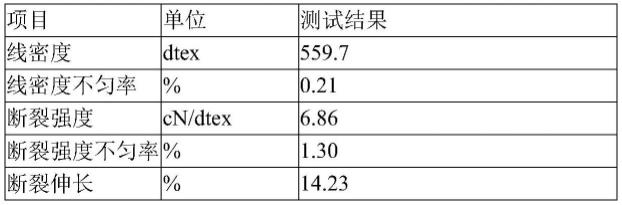
1.本发明涉及涤纶丝的制备方法领域,尤其是涉及一种基于熔体直纺的涤纶中强丝制备方法。
背景技术:
2.中强丝是一种断裂强度介于民用涤纶fdy丝(3.8cn/dtex≦强度≦4.5cn/dtex)和细旦工业丝(强度≧7cn/dtex)之间的纤维,一般断裂强度为6.2cn/dtex~7.2cn/dtex,主要用于绣花线、缝纫线、渔网线、包带、灯箱基布等下游生产。
3.目前,传统中强丝制备采用切片纺生产,原料采用高粘切片(特性粘度一般为0.85~1.10dl/g),由切片熔融后经过螺杆挤压机挤出,经纺丝、冷却、上油、多级拉伸热定型后所制得。例如,公开号为cn109722734b的中国发明专利公开了一种超亮光涤纶中强丝及其制备方法,其将改性聚酯熔体经计量、三角形或一字形喷丝板挤出、冷却、上油、二道拉伸、一道热定型和卷绕制得改性聚酯fdy丝,即得超亮光涤纶中强丝。该方法需要使用pta为主原料生产特定的高粘度切片,再用高粘度切片去制备中强丝,存在制造成本高、工艺流程长的弊端。因高粘切片的流动性较常规熔体差,容易造成管壁料的滞留从而导致中强丝物性不匀,螺杆挤出机需要定期清理造成物料浪费大,制得的中强丝品质易受原料高粘切片批次的不同而存在质量波动等不利因素。同时,因高品质中强丝产品为民用丝和普通工业丝之间的拓展产品,属于细分市场,而现有中强丝和民用丝因生产工艺不同,需用两种不同的生产线生产,不能利用一种生产线制造两种产品,缺乏灵活性。
技术实现要素:
4.本发明的目的在于提供了一种基于熔体直纺的涤纶中强丝制备方法,克服传统中强丝制备中受高粘切片纺工艺导致的制造成本高、工艺流程长、质量偏差等问题,直接使用民用丝常规熔体进行熔体直纺,得到生产纺况稳定、纤维物理力学性能优良的中强丝。
5.本发明的目的通过以下技术方案予以实现。
6.本发明提供了一种基于熔体直纺的涤纶中强丝制备方法,包括如下步骤:(1)pet熔体输送:将原料通过聚酯装置制得民用丝熔体pet,通过保温熔体管道进行输送;(2)涤纶中强丝制备:将熔体输送至纺丝箱体后,挤出形成初生纤维;依次经过冷却、上油、预网络处理后,进行多级拉伸热定型,经卷绕后得到涤纶中强丝。
7.较目前使用高粘切片为原料在切片纺上生产的中强丝,使用本发明中的制备方法得到的中强丝具有熔体输送稳定、物性指标优良的特点。尤其是常规民用丝熔体较高粘熔体的管壁滞留料会大大减少,从而提高中强丝的制成率。目前市场上的中强丝优等品制成率在85~90%之间,而本发明的中强丝优等品制成率可达到95%以上。
8.其次,本发明不再使用“从pta制成高粘切片,再将高粘切片熔融进入螺杆挤出机”这一工序,直接将pta(精对苯二甲酸)通过聚酯装置制得民用丝熔体pet,通过保温管道输送至纺丝箱体进行制备。减少的这道工序使得本发明不再需要定期清理螺杆挤出机,减少
物料的浪费,同时也减少螺杆挤出机、干燥塔、切片仓等设备的投入成本,缩短工艺流程,能够更快、更好、更稳定地制得中强丝产品。该制备方法使制造成本较切片纺制备下降30~50%,同时解决使用高粘切片存在的因批次供应的质量偏差造成中强丝成品性能不稳定的问题,使得中强丝的断裂强度不匀率控制在2%以内,断裂伸长不匀率控制在6%以内。
9.另外,本发明使用常规民用丝熔体,采用常规熔体直纺方式,因此可在民用丝生产线上直接进行中强丝制备。因高品质中强丝产品为民用丝和普通工业丝之间的拓展产品,属于细分市场,因此在实际生产中,可以根据市场需求,在民用丝生产线上直接进行中强丝和民用丝的品种切换,大大增加了民用丝生产线产品的灵活性。
10.作为优选,步骤(1)中,所述民用丝熔体pet的熔体粘度为0.60~0.70dl/g;所述保温熔体管道的温度设定为250~300℃。
11.作为优选,步骤(1)的pet熔体输送具体为:将原料通过聚酯反应制得民用丝熔体pet,经过保温熔体管道输送至纺丝增压泵,pet熔体经过纺丝增压泵后继续通过保温熔体管道输送至熔体冷却器,通过熔体冷却器后经过静态混合器进入各生产线的纺丝箱体中。
12.作为优选,步骤(2)中,所述多级拉伸热定型为依次进入第一对辊、第二对辊、第三对辊进行拉伸和热定型,丝束在第一对辊和第二对辊之间完成第一次拉伸,丝束在第三对辊处完成第二次拉伸以及热定型。
13.丝束在第一对辊处进行预加热至玻璃化温度点以上,可以充分的被软化,便于下一步工序的拉伸。第二对辊与第一对辊之间有一定的速差,从而使丝束进行第一次拉伸,第三对辊与第二对辊有一定的速差,使丝束进行第二次拉伸,同时第二对辊的两根辊均产生高温对丝束进行加热定型。此时丝束经过两道拉伸,且第二次拉伸同时经过高温热定型后形成稳定的内部结构,获得所需中强丝的断裂强度以及稳定的沸水收缩率。
14.作为优选,所述第一对辊的温度设定为不小于熔体的玻璃化转变温度,辊速设定为500~1000m/min;所述第二对辊的温度设定为与第一对辊的设定温度相同或偏高1~10℃,辊速设定为2500~3000m/min;所述第三对辊的温度设定为200℃~220℃,辊速设定为3500~4000m/min。
15.作为优选,所述第一次拉伸的拉伸比为3~4;所述第二次拉伸的拉伸比为1~2。
16.作为优选,步骤(2)的涤纶中强丝制备具体为:熔体输送进入纺丝箱体,经过计量泵计量后将熔体由分配管分配至喷丝板中挤出,熔体经由喷丝板挤出后形成初生纤维,其经过纺丝侧吹风装置吹风冷却后,形成丝束进入油嘴进行上油,上油后的丝束经过纺丝甬道进入卷绕预网络器装置进行预网络处理,之后依次进入第一对辊、第二对辊、第三对辊进行拉伸和热定型,并分别设置保温箱对辊和丝束进行保温;之后丝束进入主网络器装置完成网络点处理,最后进行卷绕,得到涤纶中强丝。
17.作为优选,所述纺丝箱体和分配管的温度均设定为250~300℃。
18.作为优选,所述民用丝熔体pet为改性的民用丝熔体pet,其制备方法包括如下步骤:将烯丙基缩水甘油醚、烷基-1-醇和开环催化剂加热反应,使用的烷基-1-醇为无支链且碳原子个数为4~10;之后加入pta和高密度聚乙烯进行预混熔融,反应后加入乙二醇聚合,得到改性的民用丝熔体pet。
19.烯丙基缩水甘油醚分子内既含有碳碳双键又有环氧键,可作为一种良好的合成偶联剂,使其先与烷基-1-醇反应开环,在分子链一端得到羟基和烷基醚。接着加入pta(对苯
二甲酸)和高密度聚乙烯,此时反应后的烯丙基缩水甘油醚将作为中间物将高密度聚乙烯接枝到pta上,具体为pta与羟基发生酯化反应,而高密度聚乙烯的端双键与碳碳双键反应。具有端双键的高密度聚乙烯在预混熔融加工时会生成自由基,而且加工温度越高,加工时间越长,产生的自由基越多,生成的自由基会使高密度聚乙烯与烯丙基缩水甘油醚生成支链。加入乙二醇是与pta反应聚合生成pet熔体,但此时生成的pet接枝有高密度聚乙烯,高密度聚乙烯的高拉伸强度和蠕变性能可以提高改性后涤纶的断裂强度。
20.另外,在烯丙基缩水甘油醚与烷基-1-醇反应开环生成的烷基醚支链提高高密度聚乙烯和pet间空间位阻,在提高改性pet熔体强度的同时,有效抑制剪切粘度的增长,使其保持良好的加工性能。控制烷基-1-醇的无支链及碳链长度是为了避免支链及长碳链会影响中强丝产品的强度。该改性方法得到的改性pet熔体同样可以使用民用丝熔体直纺工艺,且改善因取代高粘切片纺而降低的断裂强度,得到性能更好的中强丝产品。
21.作为优选,所述开环催化剂为氯化锡;所述烷基-1-醇为正丁醇、戊醇、1-己醇或正辛醇;所述加热反应为在70~90℃下反应3~5h;所述高密度聚乙烯的分子量范围为8*104~1.5*105;分子量分布范围为12~20;所述预混熔融为200~240℃下反应2~8min;所述烯丙基缩水甘油醚、烷基-1-醇、高密度聚乙烯、pta和乙二醇的质量比为5~8:5~12;20~35:100~130:120~150;所述聚合为在225~250℃且氮气气氛下反应,压力为4~5kg/cm2。
22.控制高密度聚乙烯的分子量及分子量分布范围,都是为了使高密度聚乙烯的粘度及熔点维持在一个合理范围内,不影响原有的加工工艺。预混熔融的时间过长会导致高密度聚乙烯自身自由基产长支链过多,不利于后续的pet聚合,时间过短则反应不充分。
23.与现有技术相比,本发明具有以下有益效果:(1)采用民用丝熔体直纺,减少物料的浪费及设备投入成本,缩短工艺流程;(2)得到中强丝产品的制成率提高,解决使用高粘切片存在的因批次供应的质量偏差造成中强丝成品性能不稳定的问题;(3)在实际生产中,可以根据市场需求,在民用丝生产线上直接进行中强丝和民用丝的品种切换,大大增加了民用丝生产线产品的灵活性;(4)改性的民用丝熔体pet在提高熔体强度的同时,有效抑制剪切粘度的增长,使其保持良好的加工性能,且提高断裂强度。
具体实施方式
24.以下用具体实施例来说明本发明的技术方案,但本发明的保护范围不限于此:总实施例一种基于熔体直纺的涤纶中强丝制备方法,包括如下步骤:(1)pet熔体输送:将pta、乙二醇通过聚酯装置制得民用丝pet熔体(熔体粘度为0.60~0.70dl/g),通过温度设定为250~300℃的保温熔体管道进行输送至纺丝增压泵,熔体pet经过纺丝增压泵后继续通过保温熔体管道输送至熔体冷却器,通过熔体冷却器后经过静态混合器进入各生产线的纺丝箱体中,每条生产线配备24个纺丝箱体,每个纺丝箱体分为2个生产位;(2)涤纶中强丝制备:熔体输送进入温度设定为250~300℃的纺丝箱体,经过计量泵计量后将熔体由分配管分配至喷丝板中挤出,分配管与纺丝箱体的温度一致,计量泵供
料量为58~62g/min;熔体经由喷丝板挤出后形成初生纤维,喷丝板孔数48f,孔规格为0.8*0.28mm,其经过风速为0.4~0.5m/s的纺丝侧吹风装置吹风冷却后,形成丝束进入油嘴进行上油,集束点高度1300~1500mm,油剂使用型号为hlm-100,油剂浓度为15~20%,上油后的丝束经过纺丝甬道进入卷绕预网络器装置进行预网络处理;之后依次进入第一对辊、第二对辊、第三对辊进行拉伸和热定型,第一对辊的温度设定为不小于熔体的玻璃化转变温度,丝束在第一对辊的两根辊之间进行一定角度的多圈缠绕,便于调整丝束角度以及充分的被软化,辊速设定为500~1000m/min;第二对辊的温度设定为与第一对辊的设定温度相同或偏高1~10℃,同样丝束在第一对辊的两根辊之间进行一定角度的多圈缠绕,辊速设定为2500~3000m/min,丝束在第一对辊和第二对辊之间完成第一次拉伸,第一次拉伸的拉伸比为3~4;第三对辊的温度设定为200℃~220℃,辊速设定为3500~4000m/min,丝束在第三对辊处完成第二次拉伸以及热定型,丝束在第三对辊处进行一定角度的多圈缠绕后,拉伸定型工序完成,第二次拉伸的拉伸比为1~2,第一对辊、第二对辊、第三对辊均分别设置保温箱对辊和丝束进行保温;之后丝束进入主网络器装置完成网络点处理,最后进入卷绕装置进行卷绕,得到涤纶中强丝。
25.上述使用的民用丝pet熔体还可为改性的民用丝pet熔体,其制备方法包括如下步骤:将烯丙基缩水甘油醚、烷基-1-醇和氯化锡在70~90℃下加热反应3~5h,使用的烷基-1-醇为无支链且碳原子个数为4~10,可为正丁醇、戊醇、1-己醇或正辛醇,优选为戊醇;之后加入pta和高密度聚乙烯在200~240℃下预混熔融2~8min,反应后加入乙二醇,在氮气气氛下225~250℃聚合,压力为4~5kg/cm2,得到改性的民用丝熔体pet。其中,烯丙基缩水甘油醚、烷基-1-醇、高密度聚乙烯、pta和乙二醇的质量比为5~8:5~12;20~35:100~130:120~150。
26.实施例1(涤纶中强丝167dtex/48f)本实施例中使用的是常规民用丝pet熔体,熔体粘度为0.65dl/g,其通过分配管后将熔体分至不同的生产线,被分配的部分民用丝熔体进入中强丝生产线中生产中强丝,另一部分则进入民用丝生产线生产常规民用丝。
27.具体包括如下步骤:(1)pet熔体输送:将pta、乙二醇通过聚酯装置制得民用丝pet熔体,通过温度设定为285℃的保温熔体管道进行输送至纺丝增压泵,熔体pet经过纺丝增压泵后继续通过保温熔体管道输送至熔体冷却器,通过熔体冷却器后经过静态混合器进入各生产线的纺丝箱体中,每条生产线配备24个纺丝箱体,每个纺丝箱体分为2个生产位;(2)涤纶中强丝制备:熔体输送进入温度设定为288℃的纺丝箱体,经过计量泵计量后将熔体由分配管分配至喷丝板中挤出,分配管与纺丝箱体的温度一致,计量泵供料量为60.12g/min;熔体经由喷丝板挤出后形成初生纤维,喷丝板孔数48f,孔规格为0.8*0.28mm,其经过风速为0.47m/s的纺丝侧吹风装置吹风冷却后,形成丝束进入油嘴进行上油,集束点高度1300mm,油剂使用型号为hlm-100,油剂浓度18%,上油后的丝束经过纺丝甬道进入卷绕预网络器装置进行预网络处理;之后依次进入第一对辊、第二对辊、第三对辊进行拉伸和热定型,第一对辊的温度设定为115℃,丝束在第一对辊的两根辊之间进行一定角度的多圈缠绕,便于调整丝束角度以及充分的被软化,辊速设定为700m/min;第二对辊的温
度设定为118℃,同样丝束在第一对辊的两根辊之间进行一定角度的多圈缠绕,辊速设定为2700m/min,丝束在第一对辊和第二对辊之间完成第一次拉伸,第一次拉伸的拉伸比为3.85;第三对辊的温度设定为215℃,辊速设定为3800m/min,丝束在第三对辊处完成第二次拉伸以及热定型,丝束在第三对辊处进行一定角度的多圈缠绕后,拉伸定型工序完成,第二次拉伸的拉伸比为1.4,第一对辊、第二对辊、第三对辊均分别设置保温箱对辊和丝束进行保温;之后丝束进入主网络器装置完成网络点处理,最后进入卷绕装置进行卷绕,卷绕速度3750m/min,得到涤纶中强丝167dtex/48f。
28.表1实施例1的涤纶中强丝物性指标汇总表项目单位测试结果线密度dtex167.9线密度不匀率%0.29断裂强度cn/dtex6.47断裂强度不匀率%1.12断裂伸长%14.97断裂伸长不匀率%5.90沸水收缩率%2.50网络度a/m6.3含油率%0.8如表1所示,实施例1制备得到中强丝产品物性满足下游客户使用需求,且不匀率较切片纺中强丝产品低,制备方法简单,工艺流程短,生产纺况优。
29.实施例2(涤纶中强丝278dtex/72f)与实施例1的区别在于:使用常规民用丝熔体,特性粘度为0.65dl/g,计量泵供料量为100.08g/min,喷丝板孔数72f,孔规格为0.72*0.24mm,纺丝侧吹风冷却装置风速0.52m/s,集束点高度1300mm,油剂使用型号为hlm-100,油剂浓度18%;第一对辊的辊温设定为115℃,辊速设定650m/min,第二对辊的辊温设定为118℃,辊速设定2650m/min,第一次拉伸的拉伸比为4.07,第三对辊的辊温设定为220℃,辊速设定3700m/min,第二次拉伸的拉伸比为1.39,卷绕速度为3650m/min;得到涤纶中强丝278dtex/72f。
30.表2实施例2的涤纶中强丝物性指标汇总表项目单位测试结果线密度dtex277.2线密度不匀率%0.36断裂强度cn/dtex6.33断裂强度不匀率%1.76断裂伸长%15.13断裂伸长不匀率%5.82沸水收缩率%2.43网络度a/m5.6含油率%0.92实施例3(涤纶中强丝560dtex/96f)
与实施例1的区别在于:实施例3使用的纺丝计量泵为民用丝计量泵,计量泵供料量有限,因此560dtex/96f规格的中强丝制备需要使用合股的方式进行。仍使用常规民用丝熔体,特性粘度为0.65dl/g。
31.具体包括如下步骤:(1)pet熔体输送:将pta、乙二醇通过聚酯装置制得民用丝pet熔体,通过温度设定为285℃的保温熔体管道进行输送至纺丝增压泵,熔体pet经过纺丝增压泵后继续通过保温熔体管道输送至熔体冷却器,通过熔体冷却器后经过静态混合器进入各生产线的纺丝箱体中,每条生产线配备24个纺丝箱体,每个纺丝箱体分为2个生产位;(2)涤纶中强丝制备:熔体输送进入温度设定为288℃的纺丝箱体,经过计量泵计量后将熔体由分配管分配至喷丝板中挤出,分配管与纺丝箱体的温度一致,计量泵供料量为100.80g/min;熔体经由喷丝板挤出后形成初生纤维,喷丝板孔数48f,孔规格为0.8*0.28mm,280dtex/48f的单束丝从喷丝板出来,其经过风速为0.50m/s的纺丝侧吹风装置吹风冷却后,形成丝束进入油嘴进行上油,集束点高度1300mm,油剂使用型号为hlm-100,油剂浓度18%,在纺丝上油装置下方增加一排纺丝集束导丝钩,将两束单丝合并成一束丝后进入纺丝甬道至预网络装置进行预网络处理;之后依次进入第一对辊、第二对辊、第三对辊进行拉伸和热定型,第一对辊的温度设定为120℃,丝束在第一对辊的两根辊之间进行一定角度的多圈缠绕,便于调整丝束角度以及充分的被软化,辊速设定为680m/min;第二对辊的温度设定为120℃,同样丝束在第一对辊的两根辊之间进行一定角度的多圈缠绕,辊速设定为2550m/min,丝束在第一对辊和第二对辊之间完成第一次拉伸,第一次拉伸的拉伸比为3.75;第三对辊的温度设定为220℃,辊速设定为3800m/min,丝束在第三对辊处完成第二次拉伸以及热定型,丝束在第三对辊处进行一定角度的多圈缠绕后,拉伸定型工序完成,第二次拉伸的拉伸比为1.49,第一对辊、第二对辊、第三对辊均分别设置保温箱对辊和丝束进行保温;之后丝束进入主网络器装置完成网络点处理,最后进入卷绕装置进行卷绕,卷绕速度3650m/min,得到涤纶中强丝560dtex/96f。
32.表3实施例3的涤纶中强丝物性指标汇总表表3实施例3的涤纶中强丝物性指标汇总表实施例4与实施例1的区别在于:使用改性的民用丝pet熔体;其制备方法包括如下步骤:将烯丙基缩水甘油醚、戊醇和氯化锡在80℃下加热反应4h;之后加入pta和高密度
聚乙烯在235℃下预混熔融3min,反应后加入乙二醇,在氮气气氛下240℃聚合,压力为4.4kg/cm2,得到改性的民用丝熔体pet,特性粘度为0.68dl/g。其中,烯丙基缩水甘油醚、戊醇、高密度聚乙烯、pta和乙二醇的质量比为6:9;25:115:130。
33.实施例5与实施例1的区别在于:使用改性的民用丝pet熔体;其制备方法包括如下步骤:将烯丙基缩水甘油醚、戊醇和氯化锡在85℃下加热反应3.5h;之后加入pta和高密度聚乙烯在227℃下预混熔融4min,反应后加入乙二醇,在氮气气氛下240℃聚合,压力为4.5kg/cm2,得到改性的民用丝熔体pet,特性粘度为0.68dl/g。其中,烯丙基缩水甘油醚、戊醇、高密度聚乙烯、pta和乙二醇的质量比为7:9;27:120:130。
34.对比例1与实施例4的区别在于:使用乙醇代替戊醇;其制备方法包括如下步骤:将烯丙基缩水甘油醚、乙醇和氯化锡在80℃下加热反应4h;之后加入pta和高密度聚乙烯在235℃下预混熔融3min,反应后加入乙二醇,在氮气气氛下240℃聚合,压力为4.4kg/cm2,得到改性的民用丝熔体pet,特性粘度为0.75dl/g。其中,烯丙基缩水甘油醚、乙醇、高密度聚乙烯、pta和乙二醇的质量比为6:9;25:115:130。
35.对比例2与实施例4的区别在于:使用1-十八醇代替戊醇;其制备方法包括如下步骤:将烯丙基缩水甘油醚、1-十八醇和氯化锡在80℃下加热反应4h;之后加入pta和高密度聚乙烯在235℃下预混熔融3min,反应后加入乙二醇,在氮气气氛下240℃聚合,压力为4.4kg/cm2,得到改性的民用丝熔体pet,特性粘度为0.66dl/g。其中,烯丙基缩水甘油醚、1-十八醇、高密度聚乙烯、pta和乙二醇的质量比为6:9;25:115:130。
36.对比例3与实施例4的区别在于:预混熔融的时间为20min;其制备方法包括如下步骤:将烯丙基缩水甘油醚、戊醇和氯化锡在80℃下加热反应4h;之后加入pta和高密度聚乙烯在235℃下预混熔融20min,反应后加入乙二醇,在氮气气氛下240℃聚合,压力为4.4kg/cm2,得到改性的民用丝熔体pet,特性粘度为0.73dl/g。其中,烯丙基缩水甘油醚、戊醇、高密度聚乙烯、pta和乙二醇的质量比为6:9;25:115:130。
37.表4各组别的熔体pet粘度以及中强丝断裂强度 实施例1实施例4对比例1对比例2对比例3特性粘度(dl/g)0.650.680.750.660.73断裂强度(cn/dtex)6.476.756.776.536.64由表1-3可知,采用民用丝熔体直接通过熔体直纺的制备方式已经得到充分验证实施,制备得的中强丝具有生产纺况稳定,优等品制成率高,工艺流程短,制造成本低,同时其物性不匀率低,能够更好的满足下游客户的需求。目前该方法适合生产50d-500d的中强丝制备,同时可直接在中强丝和民用丝之间直接进行品种切换。
38.由表4可知,本发明中使用的改性pet熔体可以将特性粘度维持在民用丝范围内,并且提高中强丝产品的断裂强度,得到性能更优的涤纶中强丝。结合实施例4和对比例1-2,可知烷基-1-醇的长碳链长度决定高分子链中支链的长度,进而影响熔体的特性粘度及中强丝的断裂强度。结合实施例4和对比例3,预混熔融的时间越长,高密度聚乙烯自身自由基产长支链过多,不利于后续的pet聚合,且会使粘度变大,不利于加工。
39.以上仅为本发明的优选实施例,并非因此限制本发明的专利范围,凡是利用本发明说明书所作的等效结构或等效流程变换,或直接或间接运用在其他相关的技术领域,均同理包括在本发明的专利保护范围内。
再多了解一些
本文用于企业家、创业者技术爱好者查询,结果仅供参考。