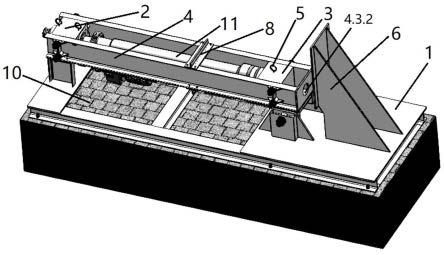
1.本发明涉及钻井装备技术领域,尤其涉及一种气体钻井冲击动力工具的测试方法。
背景技术:
2.目前国内油气井钻井提速要求越来越高,在气体钻井过程中,气体重量对井筒的作用可以忽略不计,受上覆岩层作用的影响,井底岩层所受的应力状态由压应力变为拉应力,因此气体钻井相较于常规泥浆钻井提速效果显著。此外,气体钻井在防漏、保护储层方面也具有较大的优势。以空气锤为代表的气体钻井冲击动力工具基本原理是通过改变高压气体在工具内的流道,带动活塞进行上下往复运动以一定频率冲击钎头,形成对井底岩层的冲击破碎,由于是在气体循环介质下进行,因此兼具气体钻井和冲击钻井的优势。
3.空气锤钻井是一种利用高压气体介质转换能量,实现对岩石高频率(800~1900次 /min)冲击破岩的钻井技术,兼具气体钻井和冲击钻井的优势。当使用空气锤钻井时,在空气锤活塞高频冲击动载的作用下,位于钻头底部的复合球齿可使齿尖下面的岩石瞬间达到屈服极限,同时钻头低速回转。通过不断改变球齿与岩石的接触位置,使得在接触点下面经济周围进一步形成了相连的破碎区。加之气体钻井在井底形成的“负压”,将井底岩石的压应力改变为拉应力,有利于岩石中裂纹的产生的扩展,大幅度减弱了井底岩屑的压持效应,从而使得井底岩石的“崩离”破碎充分发挥。因此与常规旋转钻井方式相比,空气锤钻井是一种以冲击、回转、动载联合破岩的高效气体钻井方式,使得火成岩等硬脆性岩石快速钻进成为现实。另外,由于空气锤钻进时所需的钻压较低(一般在10~40kn),并且空气锤活塞直接冲击纤头进行破岩,底部钻具不承受较大的轴向力,底部钻具产生的弯曲变形较小,因此在硬地层中使用空气锤钻井,在提高机械钻速的同时,也能起到良好的防斜纠斜效果。
4.冲击力、冲击功和冲击频率是评价气体钻井冲击动力工具工作状态的的关键性能参数。空气锤钻进井深最深4304.18m,单只进尺最高1945.90m,最低不足5m,个体差异明显。目前,空气锤入井前通常在钻台面注气测试,仅凭振感、声音判断工作状态是否正常,属于经验评价,存在众多的不确定性。因此,亟需一套气体钻井冲击动力工具性能参数测试方法,定量评价冲击动力工具性能,形成施工工入井标准。
技术实现要素:
5.本发明的目的在于针对上述现有技术所存在的不足,提供一种气体钻井冲击动力工具的测试方法,可以检测气体钻井冲击动力工具在运作时的冲击力、冲击功和冲击频率等主要参数进行实时采集并直观显示。同时掌握不同型号的气体钻井冲击动力工具实际性能参数,定量评价冲击动力工具性能,同时能优化气体钻井冲击动力工具的结构和使用方案。
6.具体通过以下技术方案实现:
7.一种气体钻井冲击动力工具的测试方法,其特征在于:包括安装台架装置、布设数
据处理系统、安装被测试工具、冲击参数测试;
8.所述安装测试台架包括以下步骤:s11,将有钢板焊接而成的支撑底座固定安装于水泥墩上;s12,将安装旋转机构安装于支撑底座的顶部;s13,然后将进气总成和尾座总成分别安装于安装旋转机构内部的两端;s14,向进气总成上接入供气设备;
9.所述布设数据处理系统包括以下步骤:s21,将信号采集单元、信号传输单元、数据整合单元和数据处理单元依次电性连接,构成数据处理系统;s22,将信号采集单元布设于尾座总成的内部,用以采集被测试工具作用于尾座总成上的冲击信号;
10.所述安装被测试工具包括以下步骤:s31,旋转进气总成,使进气总成旋转的中心轴垂直于安装旋转机构,然后将被测试工具放入安装旋转机构中;s32,下放进气总成,使进气总成的中心轴与被测试工具的中心轴重合,然后将被测试工具带有丝扣的一端与进气总成通气连接;s33,调整尾座总成的状态,使尾座总成与被测试工具无丝扣的一端紧密接触,并形成预紧力;s34,调整安装旋转机构,使安装旋转机构垂直于支撑底座,以使被测试工具的内活塞复位;
11.所述冲击参数测试包括以下步骤:s41,启动供气设备,使供气设备中的压缩空气通过进气总成进入被测试工具内部,以使被测试工具进入工作状态;s42,基于被测试工具与尾座总成紧密贴合,利用尾座总成将被测试工具工作状态下的冲击力传递给信号采集单元; s43,利用信号采集单元实时监测被测试工具的冲击力,并将冲击力转换成电信号通过信号传输单元上传至数据整合单元;s44,利用数据整合单元采集相关数据信号并上传至数据处理系统,数据处理单元对相应的数据信号相应的逻辑运算的处理,最终获得并实时显示被测试工具的冲击力、冲击功和冲击频率。
12.优选的,所述信号采集单元包括压电石英力传感器,所述步骤s44中,冲击功的获取包括以下步骤:s441,基于压电石英力传感器的工作原理建立被测试工具冲击压电石英力传感器的数学模型,数学模型中采用冲锤代替被测试工具,并基于该数学模型获得冲击功与冲击力的关系式
[0013][0014]
其中,w为冲锤的冲击功,fmax为冲锤的最大冲击功,a、b和c均为常数;s442,对压电石英力传感器进行标定,即,通过matlab软件对同一冲锤从不同高度自由落体所得到的数据进行曲线拟合来得到冲击力与冲击功关系曲线,结合拟合曲线结果获得常数a、b和 c的值,以完成对压电石英力传感器的标定。
[0015]
优选的,所述步骤s21中还包括数据处理系统的设计,步骤如下:s211,将数据采集卡作为数据整合单元;s212,根据系统需要配备电源适配器,并将电源适配器、信号传输单元和数据整合单元安装于数据采集箱内部;s213,在数据处理单元中,选用microsoftvisual studio软件中基于c 的的mfc模块来进行数据采集程序的编辑,数据采集程序包括基础显示模块、数据采集模块、数据回放模块和数据存储模块。
[0016]
优选的,所述步骤s11中,水泥墩由砖和水泥堆砌浇筑而成,且水泥墩上嵌入设置有若干用于连接支撑底座的连接螺柱,支撑底座上设置有与连接螺柱一一对应的安装孔,连接螺柱穿过对应的安装孔后,采用螺母与连接螺柱配合,使得支撑底座固定在水泥墩上。
[0017]
优选的,所述步骤s11中,还包括在所述进气总成的顶部和尾座总成的顶部分别设
置螺纹槽,并在螺纹槽中安装吊环,且吊环包括用于与螺纹槽配合的连接螺柱和与连接螺柱的顶部固定连接的环体。吊环的设置方便了测试台架的移动和运输。
[0018]
具体的,基于上述一种气体钻井冲击动力工具的测试方法,本技术方案公开一种气体钻井冲击动力工具的测试装置,包括数据处理系统和台架装置,台架装置包括支撑底座、进气总成、尾座总成和安装旋转机构;所述数据处理系统包括布设于台架装置上的信号采集单元以及依次电性连接的信号传输单元、数据整合单元和数据处理单元,信号采集单元电性接入信号传输单元;所述支撑底座包括定位安装架以及分别固定于定位安装架顶部的第一支撑架和第二支撑架;所述进气总成包括进气座、轴承件和进气管;进气座的内部贯穿设置有进气通道,轴承件嵌入设置于进气座内部,并与进气通道同轴设置;进气管包括受气部和受力部,受气部处于进气通道内部,并通过轴承件与进气座转动连接,且受气部的外壁与轴承件的内圈以及进气通道的内壁紧密贴合;受力部设置有与被测试工具丝扣扣型相符的螺纹扣;所述尾座总成包括安装座、冲击块、丝杆和传感器垫块;安装座的内部贯穿设置有安装通道,且安装通道包括光滑冲击部和螺纹定位部;冲击块包括承力部和传力柱,传力柱的一端处于光滑冲击部的内部,并与传感器垫块固定连接,且传力柱的外壁与光滑冲击部的内壁紧密贴合;传力柱的另一端处于安装通道的外部,并与承力部固定连接;丝杆通过螺纹定位部与安装座螺旋连接,并包含有面朝安装通道外部的调节端和面朝传感器垫块的测力端,信号采集单元设置于丝杆的测力端;所述安装旋转机构包括动力电机、传动组件和安装架体;安装架体呈顶部敞口设置的空心长方体结构,安装架体的一端可拆卸的设置于第一支架的顶部,并与第一支架可拆卸连接,安装架体的另一端与第二支架旋转连接;进气总成安装于安装架体内部靠近第一支架的一端;尾座总成的安装座处于安装架体内部靠近第二支架的一端,且尾座总成通过销轴与安装机体固定连接;动力电机处于于安装架体的底部,并与安装架体固定连接;安装架体的底部设置有用于供传动组件穿过的避让孔ⅰ,动力电机的转轴通过传动组件与进气管的受力部传动连接。
[0019]
优选的,所述传动组件为齿轮组件,包括中间齿轮以及分别与中间齿轮啮合的主动齿轮和从动齿轮,中间齿轮与安装架体转动连接,主动齿轮与动力电机的转轴同轴固定连接,从动齿轮与进气管的受力部同轴固定连接。结构较为简单,易于实现,且能确保动力的稳定传输。进一步的,所述进气座的顶部和安装座的顶部分别设置有吊环,且吊环包括连接螺柱和与连接螺柱的顶部固定连接的环体,进气座和安装座上分别设置有用于与连接螺柱配合的螺纹槽。进一步的,所述定位安装架上还设置有用于支撑安装旋转机构的侧靠支撑臂。在对气体钻井冲击动力工具进行活塞复位操作时,安装架体可斜靠在侧靠支撑臂上,避免了操作打滑造成安装架体连同气体钻井冲击动力工具一起过渡旋转,确保了测试操作的安全性。进一步的,所述进气座的进气通道内部嵌入设置有密封圈,密封圈与进气通道同轴设置,进气管受气部的外壁通过密封圈与进气通道的内壁弹性密封。
[0020]
优选的,所述丝杆的调节端设置有用于配合扳手的扳手槽,所述安装架体上与扳手槽同轴设置有供扳手穿过的避让孔ⅱ。所述步骤s32中,调整尾座总成的状态是将扳手与扳手槽配合,通过旋转扳手转动丝杆,使丝杆基于螺旋结构朝被测试工具的方向上移动,基于丝杆移动来推动冲击块,直到冲击块与被测试工具之间形成预紧力,停止旋转并取下扳手。由此一来,使调节丝杆的操作更加轻松方便,并可确保尾座总成与气体钻井冲击动力工具之间具有足够的预紧力。
[0021]
优选的,所述进气总成还包括用于防止轴承件轴向移动的环形轴承压板和用于固定环形轴承压板的压紧螺栓;环形轴承压板与轴承同轴设置,若干个压紧螺栓沿环形轴承压板的环向等距间隔设置。此结构确保了轴承件在进气座内部的稳定性,降低了轴承件与进气座之间相对固定的强度要求,方便了轴承的拆卸与安装,即,使进气总成的装配更加简单。
[0022]
优选的,所述安装架体的底部设置有连接板,所述第二支撑包括连接轴和两个相互对称并与定位安装架固定连接的耳板,连接板处于两个耳板之间,连接轴贯穿连接板,连接板通过连接轴与两个耳板转动连接。
[0023]
优选的,所述进气总成的进气座通过螺栓和销轴与安装架体旋转连接,安装架体的顶部和底部分别设置有限位横梁,限位横梁面向安装架体内侧的面设置有两个相互对称的限位滚轮组件,限位滚轮组件包括滚轮体、滚轮轴和设置于滚轮轴两端的滚轮座,滚轮座与限位横梁固定连接,滚轮轴贯穿于滚轮体的轴心处,滚轮体通过滚轮轴与滚轮座转动连接。
[0024]
本技术方案带来的有益效果:
[0025]
1)本技术方案针对现有技术中无法对气体钻井冲击动力工具的冲击力、冲击功和冲击频率进行定量测试的问题,采用布设有信号采集单元的台架装置,对气体钻井冲击动力工具的冲击力、冲击功和冲击频率进行定量测试,通过对测量的参数进行采集分析,方便了测试后期对气体钻井冲击动力工具评价、分析和改进。
[0026]
2)本技术方案针对气体钻井冲击动力工具进入工作状态后,由于冲击力较大,对测试系统和传感器的冲击震动较大的问题,通过硬连接使各部件形成一个整体,为气体钻井冲击动力工具提供稳定的工作环境,具体的,进气总成直接连接至气体钻井冲击动力工具自带的丝扣,尾座总成与气体钻井冲击动力工具之间通过可调节位置的丝杆形成预紧力,从而将气体钻井冲击动力工具固定在安装架体内;测试期间,安装架体与支撑底座相对固定,支撑底座与水泥墩相对固定,如此一来,将气体钻井冲击动力工具锤固定在安装架体架,便可减少台架振荡对试验过程的影响,即确保了气体钻井冲击动力工具工作环境的始终稳定,进一步保证测量数据的准确性。
[0027]
3)本技术方案采用安装的电机驱动被测试工具,实现模拟不同转速下被测试工具关键工作参数,测量不同工况下气体钻井冲击动力工具运作时的冲击力、冲击功和冲击频率等主要性能进行实时测量,还可通过数据处理单元直观显示。
[0028]
4)本技术方案适用性好,具体为可通过调节丝杆使安装架体内部空间适应安装不同长度的气体钻井冲击动力工具,可通过改变进气管上的螺纹扣扣型适配多种气体钻井冲击动力工具;吊环的设置方便了测试台架的移动和运输。
[0029]
5)本技术方案设置了扳手配合结构,当需要调节丝杆时,可借助扳手穿过避让孔ⅱ与扳手槽配合,使调节丝杆的操作更加轻松方便,并可确保尾座总成与气体钻井冲击动力工具之间具有足够的预紧力。
[0030]
6)采用microsoft visual studio软件中基于c 的的mfc系统设计数据采集程序,软件具有较大的灵活性,数据采集准确、可靠,界面友好,并且可以满足使用者不同的喜好。
附图说明
[0031]
本发明的前述和下文具体描述在结合以下附图阅读时变得更清楚,其中:
[0032]
图1为使用状态下的台架装置结构示意图;
[0033]
图2为使用状态下的台架装置局部放大透视结构示意图;
[0034]
图3为被测试工具活塞复位操作时的台架装置状态结构示意图;
[0035]
图4为台架装置正面结构示意图;
[0036]
图5为安装架体的正面结构示意图;
[0037]
图6为限位滚轮组件与限位横梁的连接结构示意图;
[0038]
图7为进气总成的正面剖视结构示意图;
[0039]
图8为尾座总成的正面剖视结构示意图;
[0040]
图9为冲锤冲击传感器数学模型;
[0041]
图10为一条冲击力与时间关系曲线;
[0042]
图11为传感器标定冲击力测试数据表;
[0043]
图12为传感器标定冲击功计算数据表;
[0044]
图13为冲击力与冲击功拟合曲线图;
[0045]
图14为数据处理系统的结构框图;
[0046]
图15为参数设置程序工作流程图;
[0047]
图16为单端测试装置显示的波形图;
[0048]
图17为差分测试装置显示的波形图;
[0049]
图18为1m的鉴定实验采集到的波形图;
[0050]
图19为1m的鉴定实验的活塞下落的波形图;
[0051]
图20为8次实验测得到的速度列表;
[0052]
图中:
[0053]
1、支撑底座;1.1、定位安装架;1.2、第一支撑架;1.3、第二支撑架;1.3.1、耳板; 1.3.2、连接轴;2、进气总成;2.1、进气座;2.2、轴承件;2.3、进气管;2.3.1、受气部;2.3.2、受力部;2.3.3、螺纹扣;2.4、气通道;2.5、环形轴承压板;2.6、压紧螺栓;2.7、密封圈;3、尾座总成;3.1、安装座;3.2、冲击块;3.2.1、承力部;3.2.2、传力柱;3.3、丝杆;3.4、传感器垫块;3.5、安装通道;4、安装旋转机构;4.1、动力电机;4.2、传动组件;4.2.1、主动齿轮;4.2.2、中间齿轮;4.2.3、从动齿轮;4.3、安装架体;4.3.1、避让孔ⅰ;4.3.2、避让孔ⅱ;4.4、连接板;5、吊环;5.1、连接螺柱; 5.2、环体;6、侧靠支撑臂;7、扳手槽;8、限位横梁;9、限位滚轮组件;9.1、滚轮体; 9.2、滚轮轴;9.3、滚轮座;10、水泥墩;11、被测试工具;12、信号采集单元。
具体实施方式
[0054]
下面通过几个具体的实施例来进一步说明实现本发明目的技术方案,需要说明的是,本发明要求保护的技术方案包括但不限于以下实施例。
[0055]
实施例1
[0056]
本实施例公开了一种气体钻井冲击动力工具的测试装置,作为本发明一种基本的实施方案包括数据处理系统和台架装置,台架装置包括支撑底座1、进气总成2、尾座总成3
和安装旋转机构4。数据处理系统包括布设于台架装置上的信号采集单元12以及依次电性连接的信号传输单元、数据整合单元和数据处理单元,信号采集单元12电性接入信号传输单元。支撑底座1包括定位安装架1.1以及分别固定于定位安装架1.1顶部的第一支撑架1.2 和第二支撑架1.3;进气总成2包括进气座2.1、轴承件2.2和进气管2.3;进气座2.1的内部贯穿设置有进气通道2.4,轴承件2.2嵌入设置于进气座2.1内部,并与进气通道2.4 同轴设置;进气管2.3包括受气部2.3.1和受力部2.3.2,受气部2.3.1处于进气通道2.4 内部,并通过轴承件2.2与进气座2.1转动连接,且受气部2.3.1的外壁与轴承件2.2的内圈以及进气通道2.4的内壁紧密贴合;受力部2.3.2设置有与被测试工具11丝扣扣型相符的螺纹扣2.3.3;尾座总成3包括安装座3.1、冲击块3.2、丝杆3.3和传感器垫块3.4;安装座3.1的内部贯穿设置有安装通道3.5,且安装通道3.5包括光滑冲击部和螺纹定位部;冲击块3.2包括承力部3.2.1和传力柱3.2.2,传力柱3.2.2的一端处于光滑冲击部的内部,并与传感器垫块3.4固定连接,且传力柱3.2.2的外壁与光滑冲击部的内壁紧密贴合;传力柱3.2.2的另一端处于安装通道3.5的外部,并与承力部3.2.1固定连接;丝杆3.3通过螺纹定位部与安装座3.1螺旋连接,并包含有面朝安装通道3.5外部的调节端和面朝传感器垫块3.4的测力端,信号采集单元12设置于丝杆3.3的测力端;安装旋转机构4包括动力电机4.1、传动组件4.2和安装架体4.3;安装架体4.3呈顶部敞口设置的空心长方体结构,安装架体4.3的一端可拆卸的设置于第一支架的顶部,并与第一支架可拆卸连接,安装架体4.3的另一端与第二支架旋转连接;进气总成2安装于安装架体4.3内部靠近第一支架的一端;尾座总成3的安装座3.1处于安装架体4.3内部靠近第二支架的一端,且尾座总成 3通过销轴与安装机体固定连接;动力电机4.1处于于安装架体4.3的底部,并与安装架体 4.3固定连接;安装架体4.3的底部设置有用于供传动组件4.2穿过的避让孔ⅰ4.3.1,动力电机4.1的转轴通过传动组件4.2与进气管2.3的受力部2.3.2传动连接。
[0057]
其中,数据处理系统是指基于计算机,通过测量软、硬件产品来实现用户自定义功能的测量系统。信号采集单元12通常为各种传感器,用于采集所需测量的信号;数据传输单元指用于对信号进行转换、放大、过滤和调整等初步处理的线路;数据整合单元即为数据采集卡;数据处理单元即对各种数据进行处理所使用的软件。
[0058]
在需要对气体钻井冲击动力工具进行参数测试时,可将台架装置固定于水泥墩10上,具体是采用螺栓将支撑底座1固定于水泥墩10上;然后将被测试工具11装入安装架体4.3 中,通过被测试工具11丝扣与进气管2.3受力部2.3.2的螺纹扣2.3.3配合,使被测式工具的一端与进气总成2可拆卸连接;通过调节丝杆3.3,使尾座总成3的冲击块3.2贴紧被测试工具11,将安装架体4.3沿第二支架旋转至垂直于定位安装架1.1的状态,使被测试工具11内的活塞复位,随后下放安装架体4.3到第一支架上,使安装架体4.3与定位安装架1.1相互平行,并采用销轴和螺栓使安装架体4.3与第一支架可拆卸连接;在进气总成2 的进气座2.1上连接供气设备,供气设备制备的压缩空气通过进气管2.3进入被测试工具 11,此后被测试工具11进入工作状态,并对冲击块3.2进行冲击,冲击块3.2通过传感器垫将冲击力传递给信号采集单元12,实现对冲击力的实时测量,此时,可启动电机,使电机驱动大齿轮进而带动被测试工具11,测量不同工具转速下的冲击力。测量得到冲击力后,可通过数据处理系统间接计算出冲击功和冲击频率。
[0059]
冲击力测试方法:
[0060]
通过信号采集单元12测力,基于测力需求,数据采集单元包含了压力传感器,根据各类压力传感器的工作原理,冲击力可以通过压力传感器直接测量而来。根据所测量液动冲击器的特性以及冲击力的大致范围,选用成都科大胜英科技有限公司的压电石英力传感器,其型号为511f05,其工作原理为压电效应,它可以测量的压缩力的最大值约5t,主要性能参数:量程(压)50kn、灵敏度0.1mv/n、测量范围50knpk、共振频率50khz、下线频率 1hz、输出方式m5、重量30g。
[0061]
冲击力测试获取原理:
[0062]
建立如图9所示的冲锤冲击传感器数学模型,设定冲锤下落接触到传感器时的速度为 v,压电石英力传感器是因为受到压力继而产生电荷,再通过电荷放大器对其进行一定的处理,输出电压信号。冲锤冲击传感器后会产生一定的反弹,因此冲击过程不是完全非弹性碰撞。假定传感器分为三层,传感器上层和下层设定为一个刚度很大的弹簧,中层假定为一个不变形的刚体。传感器受到冲击后传感器上层和下层都会受压,在冲击过程中,上层弹簧的形变为x1,下弹簧的形变为x2。在该数学模型中,冲锤的下落过程中,把接触时刻的动能转换为两个刚度很大的弹簧的弹性势能,达到最大形变时(xmax),传感器所受的力达到最大(fmax)。随后弹簧恢复形变,将冲锤反弹,但在弹簧恢复弹性变形的的过程中,因为传感器和支撑底座1有限位,阻滞很大,所以弹簧只把部分弹性势能转换为冲锤的反弹动能。由动能定理可得接触时刻的动能m为冲锤质量;v为冲锤与传感器刚接触时冲锤的速度,也是冲锤的最大速度。冲锤不断下落,直至传感器的弹性形变达到最大值,此时弹簧所存储的总弹性势能p为:
[0063][0064]
式(3-1)中k1与k2为两段弹簧的弹性系数,x
1max
与x
2max
为两段弹簧的最大变形量。设定冲锤速度到达最大时冲锤的的动能为冲击功w,则冲击功w与弹簧总弹性势能p相等,可得:
[0065][0066]
据胡克定理可得:
[0067]f1max
=k1x
1max
ꢀꢀꢀꢀꢀꢀꢀꢀꢀꢀꢀꢀꢀꢀꢀꢀꢀꢀꢀꢀꢀꢀꢀ
(3-3)
[0068]f2max
=k2x
2max
ꢀꢀꢀꢀꢀꢀꢀꢀꢀꢀꢀꢀꢀꢀꢀꢀꢀꢀꢀꢀꢀꢀꢀ
(3-4)
[0069]
由式(3-2)、式(3-3)和式(3-4)可得:
[0070][0071]
当弹簧达到最大形变时,传感器近似看作受力平衡,则
[0072]fmax
=f
1max
=f
2max
ꢀꢀꢀꢀꢀꢀꢀꢀꢀꢀꢀꢀꢀꢀꢀꢀꢀꢀꢀꢀ
(3-6)
[0073]
由式(3-5)和式(3-6)得
[0074][0075]
令k为上下两个弹簧的串联后的弹性系数,那么:
[0076][0077]
由于k与传感器构件自身特性相关的系数,为固定系数,所以可以得出冲击功(w)与最大冲击力的平方(f2max)成正比。冲锤通过冲击砧子完成冲击能量的传递,假定砧子为完全刚形体,冲锤为非完全刚性体,但是弹性刚度很大,且冲击过程中其变形为弹性变形。设定冲锤从开始冲击砧子至其形变至最大位置这一段时间作为研究对象,则根据冲量定理可得:
[0078]
∫fdt=mv
ꢀꢀꢀꢀꢀꢀꢀꢀꢀꢀꢀꢀꢀꢀꢀ
(3-10)
[0079]
f为冲击过程中任意一时刻冲锤的冲击力;m为冲锤质量;v为冲击接触时刻冲锤的速度;t为冲击过程中的任意一时刻。
[0080][0081]
为冲击过程的平均冲击力。由式(3-10)和式(3-11)可得:
[0082][0083]
根据动能定理,冲锤速度达到最大时冲锤的动能为冲击功,则:
[0084][0085]
任意画出一条冲击力与冲击时间的关系曲线,如图10所示,设:
[0086]
f(t)=f
max
f(t)
ꢀꢀꢀꢀꢀꢀꢀꢀꢀꢀꢀꢀꢀ
(3-14)
[0087][0088]
f(t)为任意时刻的冲击力;f
max
为冲锤的最大冲击力;f(t)为最大冲击力为单位1n时,冲锤在冲击过程中任意一时刻的冲击力。由式(3-14)和(3-15)可得:
[0089][0090][0091]
由于f(t)为最大冲击力为单位1n时,冲锤在冲击过程中任意一时刻产生的冲击
力,要产生最大冲击力为1n的冲击力,在不计下落能量损耗的情况下,则必定对应着某一确定的高度h。因下落的高度h确定,则冲锤下落接触砧子的瞬间速度唯一确定(由动量定理可得)。在最大冲击力为单位1n时,冲击过程用冲量定理可得:
[0092]
∫f(t)dt=mv'
ꢀꢀꢀꢀꢀꢀꢀꢀꢀꢀꢀꢀꢀꢀꢀꢀꢀꢀꢀꢀꢀ
(3-18)
[0093]
v'为最大冲击力为1n时冲锤的对应的速度,由式(3-17)和公式(3-18)可得:
[0094][0095]
最大冲击力为1n时冲锤的对应的速度v',冲锤的质量m和冲击时间t均为定值,令:
[0096][0097]
式中k同样为定值,则可得:
[0098][0099]
由式(3-13)和式(3-21)中,可得:
[0100][0101]
因为k、t、m均为常数,所以可以得出冲击功w与最大冲击力成正比关系。综合以上两种论证结论,可得冲击功与最大冲击力之间的呈二次曲线关系,考虑到实际情况并非理想状态,设定二者之间的的关系为:
[0102][0103]
式中,a、b、c均为常数。
[0104]
对压电石英力传感器进行标定,传感器标定的目的是找出冲击力和冲击功之间的比例系数,即由上文得到的常数a、b、c。压电石英力传感器标定方式为:采用专门的标定装置,首先将压电石英力传感器固定,将冲锤的一端与标定装置的钢丝绳相连,钢丝绳通过滑轮装置实现冲锤在不同高度的调节,冲击时直接松开钢丝绳即可;其次通过数据采集卡对传感器上传的信号进行采集;最后通过大量实验数据拟合出冲击力与冲击功之间的关系图形,并得出相应的系数来完成传感器的标定。选用最小二乘法对两组数据进行曲线拟合,利用最小二乘法曲线拟合时,以所采集到的离散数据作为标准数据,同时刻拟合曲线上的数据作为待测数据。计算标准数据与待测数据间的误差平方和,误差平方和越小,曲线拟合效果越好。拟合的曲线后可以预测其他未测量点的数据。通过matlab软件对质量为10.5kg的冲锤从不同高度自由落体所得到的数据进行曲线拟合来得到冲击力与冲击功关系曲线,实验数据如图 11和图12所示,所得到的拟合图形见图13,结合拟合曲线结果即可获得式2-23中a、b、c的值来完成传感器的标定。通过对数据进行多项式拟合得出a取值为0.00005,b取值为
‑ꢀ
0.098,c取值为5.0421。
[0105]
冲击频率测量方式:冲击频率通常不直接侧量,而是通过间接测量的方式获得。常见的有声波法和触点法。本文选用间接测量的方式,即在测量冲击力的过程中,根据最大冲
击力在单位时间内出现的次数,计算得出液动冲击器的冲击频率。
[0106]
本技术方案针对现有技术中无法对气体钻井冲击动力工具的冲击力、冲击功和冲击频率进行定量测试的问题,采用布设有信号采集单元12的台架装置,对气体钻井冲击动力工具的冲击力、冲击功和冲击频率进行定量测试,通过对测量的参数进行采集分析,方便了测试后期对气体钻井冲击动力工具评价、分析和改进。本技术方案针对气体钻井冲击动力工具进入工作状态后,由于冲击力较大,对测试系统和传感器的冲击震动较大的问题,通过硬连接使各部件形成一个整体,为气体钻井冲击动力工具提供稳定的工作环境,具体的,进气总成 2直接连接至气体钻井冲击动力工具自带的丝扣,尾座总成3与气体钻井冲击动力工具之间通过可调节位置的丝杆3.3形成预紧力,从而将气体钻井冲击动力工具固定在安装架体4.3 内;测试期间,安装架体4.3与支撑底座1相对固定,支撑底座1与水泥墩10相对固定,如此一来,将气体钻井冲击动力工具锤固定在安装架体4.3架,便可减少台架振荡对试验过程的影响,即确保了气体钻井冲击动力工具工作环境的始终稳定,进一步保证测量数据的准确性。本技术方案采用安装的电机驱动被测试工具11,实现模拟不同转速下被测试工具11 关键工作参数,测量不同工况下气体钻井冲击动力工具运作时的冲击力、冲击功和冲击频率等主要性能进行实时测量,还可通过数据处理单元直观显示。本技术方案适用性好,具体为可通过调节丝杆3.3使安装架体4.3内部空间适应安装不同长度的气体钻井冲击动力工具,可通过改变进气管2.3上的螺纹扣2.3.3扣型(具体为更换带有不同螺纹扣2.3.3扣型的进气管2.3)适配多种气体钻井冲击动力工具,具体为,本技术方案可测试直径为180~275mm 的空气锤以及直径为172~245mm的空气螺杆。
[0107]
实施例2
[0108]
本实施例公开了一种气体钻井冲击动力工具的测试方法,作为本发明一种基本的实施方案,包括安装台架装置、布设数据处理系统、安装被测试工具11、冲击参数测试;
[0109]
所述安装测试台架包括以下步骤:s11,将有钢板焊接而成的支撑底座1固定安装于水泥墩10上;s12,将安装旋转机构4安装于支撑底座1的顶部;s13,然后将进气总成2和尾座总成3分别安装于安装旋转机构4内部的两端;s14,向进气总成2上接入供气设备;
[0110]
所述布设数据处理系统包括以下步骤:s21,将信号采集单元12、信号传输单元、数据整合单元和数据处理单元依次电性连接,构成数据处理系统;s22,将信号采集单元12布设于尾座总成3的内部,用以采集被测试工具11作用于尾座总成3上的冲击信号;
[0111]
所述安装被测试工具11包括以下步骤:s31,旋转进气总成2,使进气总成2旋转的中心轴垂直于安装旋转机构4,然后将被测试工具11放入安装旋转机构4中;s32,下放进气总成2,使进气总成2的中心轴与被测试工具11的中心轴重合,然后将被测试工具11带有丝扣的一端与进气总成2通气连接;s33,调整尾座总成3的状态,使尾座总成3与被测试工具11无丝扣的一端紧密接触,并形成预紧力;s34,调整安装旋转机构4,使安装旋转机构4垂直于支撑底座1,以使被测试工具11的内活塞复位;
[0112]
所述冲击参数测试包括以下步骤:s41,启动供气设备,使供气设备中的压缩空气通过进气总成2进入被测试工具11内部,以使被测试工具11进入工作状态;s42,基于被测试工具11与尾座总成3紧密贴合,利用尾座总成3将被测试工具11工作状态下的冲击力传递给信号采集单元12;s43,利用信号采集单元12实时监测被测试工具11的冲击力,并将冲击力转换成电信号通过信号传输单元上传至数据整合单元;s44,利用数据整合单元采集相关数
据信号并上传至数据处理系统,数据处理单元对相应的数据信号相应的逻辑运算的处理,最终获得并实时显示被测试工具11的冲击力、冲击功和冲击频率。
[0113]
实施例3
[0114]
本实施例公开了一种气体钻井冲击动力工具的测试方法,作为本发明一种基本的实施方案,即基于实施例1和实施例2,信号采集单元包括压电石英力传感器,步骤s44中,冲击功的获取包括以下步骤:s441,基于压电石英力传感器的工作原理建立被测试工具冲击压电石英力传感器的数学模型,数学模型中采用冲锤代替被测试工具,并基于该数学模型获得冲击功与冲击力的关系式
[0115][0116]
其中,w为冲锤的冲击功,fmax为冲锤的最大冲击功,a、b和c均为常数;s442,对压电石英力传感器进行标定,即,通过matlab软件对同一冲锤从不同高度自由落体所得到的数据进行曲线拟合来得到冲击力与冲击功关系曲线,结合拟合曲线结果获得常数a、b和 c的值,以完成对压电石英力传感器的标定。
[0117]
实施例9
[0118]
本实施例公开了一种气体钻井冲击动力工具的测试方法,作为本发明一种基本的实施方案,即基于实施例2和实施例7,步骤s21中还包括数据处理系统的设计,步骤如下:
[0119]
s211,将数据采集卡作为数据整合单元;具体的,本次数据采集需要整合信号采集单元12上传的信号,实现气体钻井冲击动力工具(液动冲击器)的八种性能的测量,综合分析实用性以及经济性等因素,本技术方案选用由北京双诺测控技术有限公司所生产的型号为 mp4221的数据采集卡,其主要特性如下:usb2.0总线ad采集模块;8路单端输入,采样通道可以进行自动扫描;12位2mhzad,采用软件自动校正技术,并且ad输入有0~5v、0~ 10v和
±
5v三种,可以通过软件程序设置不同的增益值进行控制,所有通道的输入范围相同;采集模式包含连续采集和存储定长采集两种,mp4221启动既可以选择软件触发也可以选择外部硬件触发方式;2路24位计数器,采用减法计数的模式计数,既可以测量信号的频率也可对n个脉冲上升边沿间的间隔时间进行测量;2路20位脉冲输出,时钟频率为 10mhz。可以产生pwm方波、单次正脉冲输出、可编程脉冲个数输出;ad输入通道通过自动扫描的方式一次进行转换,用户可以任意设置转换的起始和结束通道;两路独立12位da,输出5v/
±
5v,其输出只能用作电压输出的控制,不能当做信号发生器。
[0120]
s212,根据系统需要配备电源适配器,并将电源适配器、信号传输单元和数据整合单元安装于数据采集箱内部。
[0121]
s213,在数据处理单元中,选用microsoft visual studio软件中基于c 的的mfc模块来进行数据采集程序的编辑,数据采集程序包括基础显示模块、数据采集模块、数据回放模块和数据存储模块。关于数据采集程序的编辑,具体内容如下:
[0122]
1)数据采集程序基本要求:数据采集过程首先需要通过数据采集卡同时采集六个传感器所输出的信号,其中压电石英力传感器所获取的信号还需要转换为冲击力、冲击频率以及冲击功这三种信息,其次需要在程序界面内实时显示各检测值并绘制出对应图形,同时所采集到的数据需以文本形式独立地自动保存以便后续进行数据分析。
[0123]
2)microsoft visual studio(简称vs)是由美国微软公司开发的一个基本完整的开发工具集,其包括了一个软件生命周期中所需要的大部分工具。而mfc(微软基础类库)则
是vs软件中的一个模块,它以c 为基础创建了各种类库,并且包含一个应用程序框架,目的是为了减少应用程序开发人员的工作量。使用过程中可以直接调用库中的基类、或者基于基类派生出可以实现特定功能新类,也可以自己创建新类,编辑程序过程方便,并且灵活度较高。mfc程序的编辑虽然功能千变万化,但是从本质来讲可以分为以下几个步骤:根据不同用户的使用需求进行界面的设计、对文件进行预设操作的设计、多媒体的使用以及数据库的访问等。即首先设计基础界面,而后对界面中的各个组件赋予特定的功能。比如希望界面中的唱歌按钮在触发后可以发出一段美妙的音乐,则首先需头文件中对其进行声明,而后在实现文件中设置所需播放的音乐的类型、时间、播放形式等。
[0124]
3)数据采集程序基本结构与功能:数据采集程序的结构由四部分组成包括数据显示基础设置模块,数据采集模块、数据回放模块以及数据存储模块。其中,数据显示设置包括数据显示类型设置(电压值或者直观理解值);数据显示形式设置,它包括数据显示界面中显示测量值的类型、字体、颜色、时间以及数据显示格式(动态曲线还是即时曲线)。数据采集模块实现实时采集所测量数据的功能。数据回放模块可以根据使用者的需求复现之前数据采集的过程。数据存储模块实现数据采集过程总各个测量值的实时保存以便后续分析数据,该模块数据默认保存格式为bin(二进制)格式,分析时可将需要的数据导出为文本格式。以下详细介绍每一个模块的具体内容。
[0125]
4)数据采集程序界面设计:数据采集程序的编辑前期工作为设计其主界面,主界面即为程序所要实现功能的主体框架,。界面设计基础为mfc类库,其中包括mfc类、宏以及函数,实际应用时于类库中选择继承基类并对其扩展或者创建新类以实现特定的功能。本技术方案首先选用单文档应用程序主框架窗口,系统可自动生成mfc应用的基类,其中包括应用类及全局对象、文档类、视图类、框架类以及对话框类等。然后选择或者新增对话框类并于其中设计布置各控件,主要包括各种按钮、定义各个数据名称的静态文本以及对应的可编辑文本等控件的设计,对于参数设置按钮还需设定字体、颜色、保存等对话框。
[0126]
5)数据采集程序设计:数据采集程序界面设计完成之后需对其各个控件赋予特定使命程序才能实现特定功能。界面设计完成后系统自动生成了包括对话框类、文档类、视图类以及框架类等基础类每个类中均包含头文件和实现文件。其中头文件的主要作用是为了方便各类以及程序之间的调用和各个基础变量和函数的声明。实现文件为程序主体部分,它需定义函数、变量、设定各个函数的关联方式及对应计算方式。
[0127]
6)参数设置程序:不同的使用者有不同的偏好,那么对界面中所绘制数据图形的种类、颜色、字体、横纵坐标显示形式的要求均不同。当需要更改以上参数时可通过参数设置对话框来实现。界面设计中已完成了它的基础框架,而功能的具体实现则需要编辑对应程序来完成。参数设置按钮中包含三种参数的设置功能要求,分别为坐标系参数设置、绘图参数设置以及数据回放形式设置。三种对话框所实现的功能虽然不同但是其程序的编辑模式相似,以下以坐标系统设置为例来说明:
[0128]
坐标系统设置对话框是一个新类,其功能的实现首先需要对话框中各个控件的类型、特性以及其功能实现函数于头文件中声明,而后在参数系统设置类实现文件中对函数以及算法进行具体定义来实现特定的功能。参数设置程序工作流程见图15,即首先程序开始运行,启动见面显示以后则选择参数设置按钮,参数设置按钮收到触发信息后将作出显示三个参数设置选择列表的反映,即调用列表显示函数。然后选择其中的坐标系统设置,系
统收到该选择信号后其函数功能为弹出参数设置对话框即调用坐标系统设置类。最后根据使用者的需求选择特性并确定,只有确定选择结果之后使用者在坐标系统设置类中所做的选择才能以赋值的方式将其传送至绘图工具类中,完成坐标参数的设置。
[0129]
7)开始数据采集程序:当液动冲击器运行状态稳定后,如需进行数据采集则单击开始采集按钮开始采集数据,此时所采集到各类数据值不仅要求以图形的方式显示,同时要求测量数据值以直观的数字显示于主界面的编辑框内,为了实现所设定的功能首先由界面中的开始按钮为触发源,程序设计时首先在界面类的头文件中对数据采集的各个控件、函数、变量等进行声明,然后于实现文件中赋予其具体功能。即开始采集后,系统首先更新界面,将开始采集前的界面数据清除;而后判断数据采集卡中各ad通道是否可以正常运行,当以上条件均满足时,便开始进入数据采集进程,实现数据的实时采集,当系统发出结束数据采集命令之后即结束数据采集线程停止采集。
[0130]
8)数据显示程序(绘图):由于所采集到的数据需以图形的方式实时显示那么程序实现时需先在绘图类中对其头文件进行设定,该类的头文件中需包括对显示方式的初始设置、各变量声明、函数的预定义等。然后通过绘图类实现文件中的程序达到将数据采集卡所采集到的ad值通过计算后转换为电压值或者实际值显示的目的。数据还需以实际值或者电压值得的形式实时显示于对应编辑框中,该功能通过通过函数调用的方式将对应值赋予编辑框变量即可。
[0131]
综上所述,遵循程序设计的顺序依次编辑参数设置、绘图、数据显示等类的头文件以及实现文件的程序,并将各个类的程序与数据采集卡类以特定的算法和关联方式连接起来便可实现数据采集的预设功能。
[0132]
实施例4
[0133]
本实施例公开了一种气体钻井冲击动力工具的测试方法,作为本发明一种基本的实施方案,即基于实施例3,进行相关系统实验和数据分析,具体如下:
[0134]
1)数据采集卡的测试:数据采集系统测试的核心是采集卡的测试,在实验室电脑安装测试软件,然后下载数据采集卡的驱动程序,驱动程序就好比一个“接口”,将数据采集卡和计算机连接在一起,实现它们之间的通信联系。按输入信号的方式分为单端和差分两种测试系统,进行实验观察,在完全相同的测试环境下,当没有被测金属导体靠近,平整放置探头时,根据系统校准结果,在此状态下,电压输出的波形应该是恒定的5.201v。分别采用单端和差分测试系统进行测试,其测试结果如图16和图17所示。由实验可以直观地看到差分测试系统可以有效地避免信号的干扰,而单端测试系统的显示波形有太多的噪声。
[0135]
2)冲击功测量装置的鉴定:为了验证气体钻井冲击动力工具的测试装置的可行性和精准度,需要进行鉴定实验,因为国内暂且没有明确的冲击功测量标准,而且理论计算值也会有一定的误差。因此做重物自由落体实验,对测量系统的精准度进行鉴定。将改进后的活塞挂在标定台架的导轨上,砧板和探头一起放在下面的基座上。活塞质量为10.5kg,在做鉴定实验时,在导轨上添加润滑油,活塞向下滑动的位移很短,因此等同于理想状态下的自由落体实验,可以应用自由落体速度公式:
[0136]
v2=2gh
ꢀꢀꢀꢀꢀꢀꢀꢀꢀꢀꢀꢀꢀꢀꢀꢀꢀꢀꢀꢀꢀꢀꢀ
(3-24)
[0137]
式中:v为自由落体的末速度(m/s);g为重力加速度(m/s2),重力加速度为9.81 (m/s2);h为位移(m)。因为测量气体钻井冲击动力钻具的冲击功,就相当于测量活塞冲击的
末速度,因此只需要鉴定测量装置测出的速度值,并与理论值进行比较,就可以鉴定出测量系统的精准度。将气体钻井冲击动力钻具的活塞挂在导轨上,距离固定探头的砧板为1m 的高度处下滑,根据式(3-24)可知活塞的末速度v的理论计算值为:
[0138][0139]
用气体钻井冲击动力工具的测试装置进行测量,采集到的波形图如图18所示。看到整段波形的电压上限是5.201v,可以知道活塞的下落运动进入了测量系统的线性区,也就是5mm~ 25mm,因此就把测量到的波形完好的存储下来。活塞向下落,电压就变小;活塞在被润滑后的导轨上快速提起,其电压就变大。因此测量到的波形如图18所示,有8个类似于半周的正弦波的数据波形,因此将8次测量实验结果进行计算,并取平均值,与理论计算得到的末速度值进行比较。因为测量装置的线性区为5mm~25mm,因此活塞往上提时,会超过测量的线性区,计算不到活塞回去的速度,可是这对于需要计算的冲击功是没有必要研究的,因此只需要对活塞向下落的运动,也就是对向下变化的波形进行研究就可以了。进一步的,将其中的一个周期波形的向下半个周期的波形进行放大,取其线性段进行分析,如图19所示。由图中可以看出,波形几乎呈现线性变化,根据测量系统的标定,可知位移与电压对应的关系是d=5
×
u(u为电压值),可以计算出活塞向下冲击的速度。其速度为:
[0140][0141]
式中,u1为波峰对应的电压值(v),u2为波谷对应的电压值(v),t1为波谷对应的时间(s),t2为波峰对应的时间(s)。经过单位换算,可得出v=123.4(m/s)。这是第一次实验得到的数据,然后逐一计算其他7次实验,如图20所示,列出了8次实验测得到的速度,计算出平均速度:
[0142][0143]
与理论计算到的速度4.429(m/s)进行比较,相差了0.172(m/s)。因理想状态下的自由落体实验很难达到,导轨即使有润滑,也会有误差,因此实际测量值肯定会小于理论计算值。通过多次鉴定实验,其设计的冲击功测量系统测得的末速度值略微小于理论计算值,测量到的末速度值与理论计算值的误差最大为7%。
再多了解一些
本文用于企业家、创业者技术爱好者查询,结果仅供参考。