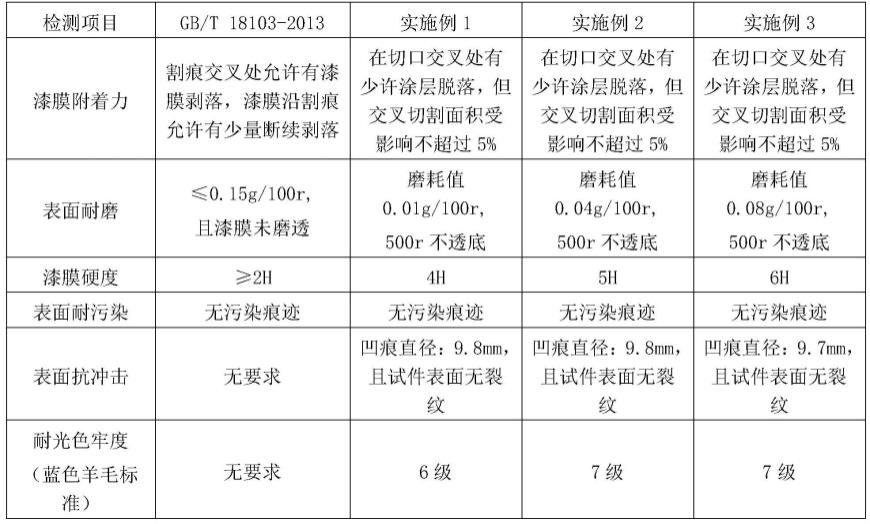
1.本发明涉及一种高稳定性实木复合地板的制备方法,应用在实木复合地板生产领域。
背景技术:
2.实木复合地板是采用不同树种的板材交错层压而成的,其一定程度上克服了实木地板(非层压)存在的湿胀干缩的缺点,干缩湿胀率小,具有较好的尺寸稳定性,同时其也保留了实木地板的自然木纹和舒适的脚感,因此实木复合地板兼具了强化地板的稳定性与实木地板的美观性,还具有环保的优势。
3.实木复合地板具体结构包括面层和基材,该面层为单层板,基材为胶合板,制备过程包括基材准备、开槽榫、表面涂饰、封边处理等。然而在实木复合地板的使用过程中,由于基材锻压制备过程中,胶合板中间层板芯中的水分出不来,中间层板芯的水分偏高,使得地板容易变形、离缝,尤其是使用地暖的环境下,往往地板会出现开裂、翘曲变形等问题,其尺寸稳定性差。
4.如申请号cn201710192121.4的专利申请公开了一种奇偶对称组坯分层锻压制备高稳定性实木复合地板的方法,其通过奇偶对称结构组坯,严格控制基材的参数以消除应力变形,维持基材尺寸及结构的稳定;具体其是采用了“三层锻压”的二次压合工艺来将板材中的含水率调整至均匀稳定,最大化释放板坯中的甲醛以及释放单板内应力,力学性能更加稳定,同时其采用包含聚乙烯和蜂胶的封边剂处理,如此获得甲醛释放放量低、含水率均匀、尺寸稳定性好、防水性能优异且稳定的地板。但申请人对其进行内胶合强度测定、防潮性能测定以及表面耐龟裂性能测定中发现,该产品仍然会出现了尺寸稳定性不佳的问题。
5.目前,我们使用的实木地板或实木复合地板在安装时,其榫和槽间都存在一定的间隙,且随着板材受季节性湿度变化,板材出现干缩湿胀后,地板容易出现端头拔缝,踩踏后会产生刺耳的噪音,其尺寸稳定性不佳,且不能做出大规格的地板,其地板宽度无法做到1.65m以上。
6.因此,提供一种不易出现开裂、卷曲变形等问题,产品规格更大的高稳定性实木复合地板的制备方法己成为当务之亟。
技术实现要素:
7.为了克服现有实木地板或实木复合地板等容易出现尺寸稳定性不佳等问题的缺点,本发明提供一种高稳定性实木复合地板的制备方法,通过优选单板,使用9层对称结构、三次成型的工艺,并配合多次砂光定厚,保证了各层单板含水率均匀稳定、板坯应力性能好,避免了实木复合地板尺寸稳定性不佳的问题,减小了各层单板间的应力以及胶水使用量,降低了成本且环保等级高,还让该地板产品可以做出更大规格(地板宽度可达1.65m以上)。
8.本发明的技术方案如下:
9.一种高稳定性实木复合地板的制备方法,主要包括以下依序进行的步骤:
10.(一)选材:
11.选用含水率为8-12%,厚度为2.2-2.6mm的桉木单板和含水率为8-14%,厚度为0.4-0.6mm的杂木单板;
12.(二)分层热压:
13.(1)第一次成型:
14.①
布胶:将三棵树无醛胶以单面布胶方式涂布于两两相邻的桉木单板之间,且布胶量为250-350g/m2;
15.②
板材组坯:将桉木单板叠放在一起,且该两两相邻的桉木单板之间的桉木单板的延伸方向相互垂直;
16.③
冷压:组坯完成于常温下陈放至少10min,再以压力0.6-0.8mpa/m2保压28-32min,之后对重叠部分进行修割,空缺部分进行填补;
17.④
热压:于125-130℃以压力0.8-1.0mpa/m2保压6-8min后,再缓慢将压力降至0.15-0.25mpa/m2,保压2-3min,之后再缓慢将压力降至常压,即获得板材坯料;
18.(2)养生、砂光定厚:将板材坯料堆垛,并以≥200kg的重物平压3-5天进行养生,之后对板材坯料的两面均匀砂光定厚,以砂平为准,且公差控制在
±
0.2mm;
19.(3)第二次成型:
20.①
布胶:将三棵树无醛胶以单面布胶方式涂布于两两相邻的桉木单板或桉木单板与板材坯料之间,且布胶量为210-230g/m2;
21.②
板材组坯:将两层桉木单板、板材坯料以及两层桉木单板自下而上依次叠放在一起,且两两相邻的桉木单板或桉木单板与板材坯料之间的延伸方向相互垂直;
22.③
冷压:组坯完成于常温下陈放至少10min,再以压力0.6-0.8mpa/m2保压28-32min;之后对重叠部分进行修割,空缺部分进行填补;
23.④
热压:于125-130℃以压力0.8-1.0mpa/m2保压12-15min后,先缓慢将压力降至0.45-0.55mpa/m2,保压2-3min,之后再缓慢将压力降至常压,即获得基板;
24.(4)养生、修边、砂光定厚:将基板堆垛,并以≥200kg的重物平压5-7天进行养生,之后先对基板组坯进行修补,再对基板组坯的两面均匀砂光定厚,以砂平为准,且公差控制在
±
0.2mm;
25.(5)第三次成型:
26.将杂木单板、基板组坯以及杂木单板自下而上依次叠放贴合在一起,每层杂木单板由相互平行的杂木单板组成,且两两相邻的杂木单板与基板组坯之间的延伸方向相互垂直,即获得所述高稳定性实木复合地板组坯;
27.(三)封闭、隔离涂饰:对高稳定性实木复合地板组坯的表面涂布标准色底层和数码喷涂装饰层;
28.(四)开槽榫:在高稳定性实木复合地板组坯的相对的端面上分别开设槽和榫,相邻高稳定性实木复合地板间能通过槽和榫相互配合连接;
29.(五)表面涂饰:对高稳定性实木复合地板组坯进行表面涂饰;
30.(六)封边处理:对表面涂饰后的高稳定性实木复合地板组坯进行封边处理,即获
得高稳定性实木复合地板。
31.本技术的高稳定性实木复合地板的制备方法通过优选单板,使用9层对称结构、三次成型的工艺,并配合多次砂光定厚,保证了各层单板含水率均匀稳定、板坯应力性能好,减小了各层单板间的应力以及胶水使用量,降低了成本且环保等级高,其不仅尺寸、颜色、表面的稳定性佳,还让该地板产品可以做出更大规格(地板宽度可达1.65m以上)。
32.其中,通过严格控制优选单板的含水率、纹理、树种、厚度四个要素,以此来消除应力变形,维持基材尺寸及结构的稳定。采用板材坯料为中间层,既有利于保证地板的支撑强度,又易于配合其他层单板使得含水率均匀稳定,且三次成型均在每次热压后使单板含水率得到平衡,之后各次成型工艺之间穿插又对板坯进行充分的养生、砂光定厚的工艺,如此各单板内的应力能够得到充分地释放,以此获得更加稳定的力学性能,在板材强度提升的同时,又充分减少了胶水的使用量,环保性能得到提升。第一次成型和第二次成型的布胶步骤中使用的三棵树无醛胶均为sk-wqy1a或sk-wqy1b;热压步骤中的分段降压使得板材能缓慢排湿,能有效避免地板鼓包。养生工序使得板材的温度和水分能得到缓慢的释放;第一次成型和第二次成型的冷压步骤中的对重叠部分进行修割,空缺部分进行填补的工序以及分别设在第一次成型和第二次成型后的两次养生、砂光定厚工序,使得板材的压力均匀,有效降低了板材内应力,有效提升了板材的加工幅面,即地板宽度可达1.65m以上(现有的地板长度一般都在1.2m左右,而宽度一般无法做到1.65m以上),减少锯路损耗,提升了出材率,使得产品性能更加稳定,不易变形。
33.步骤(四)开槽榫的步骤具体为:高稳定性实木复合地板组坯间长边相对的端面上的槽和榫以平扣方式相互配合,短边相对的端面上的槽和榫以锁扣方式相互配合。
34.长边采用平扣技术,减少材料损耗;短边采用锁扣技术,提供锁合力。现有同类实木复合地板的加工余量为11-14%,而本技术高稳定性实木复合地板的加工余量为7-10%,出材率提升1.4%。加工出材率增长是源于产品尺寸的自由变化,材料边角损失小,则利用率高,能节约大量成本。
35.步骤(四)开槽榫的步骤具体为:在高稳定性实木复合地板组坯两长边端面上分别开设长边凹槽和设置长边凸榫,该长边凹槽和长边凸榫均沿长边延伸,该长边凸榫向长边端面外旁侧伸出且与长边延伸方向相垂直,相邻高稳定性实木复合地板件的长边凹槽和长边凸榫能相互配合;
36.高稳定性实木复合地板组坯的一个短边端面顶部为二层台阶状结构,该台阶a沿短边延伸方向延伸,且上层台阶a较下层台阶a突出高稳定性实木复合地板组坯外部,短边端面底部设有向短边端面外旁侧突出的短边凸榫,该短边凸榫沿短边延伸方向延伸,短边凸榫朝向台阶a一侧面的外边沿处设有向上层台阶a方向凸起且沿短边延伸的凸条a;台阶a与短边凸榫之间形成卡槽a;另一个短边端面顶部为二层台阶状结构,该台阶b沿短边延伸,且下层台阶b较上层台阶b突出高稳定性实木复合地板组坯外部,该下层台阶b背向的上层台阶b一侧面外边沿处设有背向上层台阶b方向凸起且沿短边延伸的凸条b,凸条b与短边端面之间形成卡槽b;相邻的高稳定性实木复合地板组坯间通过下层台阶b、凸条b与卡槽a的卡接,以及凸条a与卡槽b的卡接相互配合。
37.优选的长边平扣、短边锁扣方式,连接更加快速、牢固。
38.步骤(二)分层热压中还包括:第一次成型、第二次成型和第三次成型中,使板材坯
料、基板组坯和高稳定性实木复合地板组坯的长边和短边端面处的桉木单板或杂木单板的顺纹一面朝外。
39.板材顺纹朝外的设计使得地板吸湿能力降低,尺寸稳定性及防水性能得到提高。
40.步骤(三)的步骤具体为:
41.(1)涂布标准色底层:对高稳定性实木复合地板组坯表面进行处理,之后通过辊涂方式将腻子涂布于高稳定性实木复合地板组坯表面,并过红外线迅速干燥;
42.(2)数码喷涂装饰层:采用智能数码打印机和高保色油墨,将数码装饰图直接喷印在经涂布标准色底层处理后的高稳定性实木复合地板组坯表面。
43.涂布标准色底层步骤为后继的数码喷涂装饰层步骤和表面涂饰工艺打下基础,数码喷涂装饰层赋予地板更丰富的色彩和图案。其中,所述腻子优选三棵树优威(uv)附着腻子ung221-hp 、三棵树优威(uv)辊涂腻子ung244 。
44.步骤(五)表面涂饰的步骤具体为:
45.(1)涂布高透明性uv底漆:通过滚涂或淋涂的方式在经过开槽榫后的高稳定性实木复合地板组坯表面涂布至少4层的高透明性uv底漆;
46.(2)涂布耐黄变uv面漆:通过滚涂或淋涂的方式在涂布高透明性uv底漆后的高稳定性实木复合地板组坯表面涂布至少4层的耐黄变uv面漆。
47.现有地板表面涂饰时多采用单层涂布耐磨底漆的做法,通过增大耐磨底漆涂布量来提升漆膜强度,但其存在容易起脆问题。本案优选的表面涂饰步骤采用复式增强工艺,采用多层涂布高透明性uv底漆和耐黄变uv面漆的做法,侵入式渗透地板,漆膜固定式互联,解决了目前实木复合地板的油漆涂饰加工容易起脆的问题,其使漆膜具有耐磨、高色牢度、高表面强度、高表面耐冲击力的优点。其中,高透明性uv底漆起到填充、隔离作用,使漆膜更耐磨、高硬度、高保色等性能,耐黄变uv面漆起到表面保护作用。所述高透明性uv底漆优选三棵树优威(uv)透明附着底漆udg213 、三棵树优威(uv)透明底漆udg245 。
48.步骤(六)封边处理的具体步骤为:向表面涂饰后的高稳定性实木复合地板组坯的四个端面喷涂熔融的防水蜜蜡,喷涂量为40-60g/m2,即获得高稳定性实木复合地板。
49.通过对实木复合地板的封边处理,当蜡被喷射至端面时,一部分蜡能够渗入至单板毛孔并固化封闭毛孔,另一部分蜡位于端面并固化以在端面形成蜡膜。因此,封边处理能够防止外界水汽进入地板内部,防止地板受潮变形及吸湿膨胀,提升地板使用寿命。
50.所述熔融的防水蜜蜡的温度为70-80℃。
51.优选防水蜜蜡使得喷涂更加均匀。
52.与现有技术相比,本发明申请具有以下优点:
53.1)本技术的高稳定性实木复合地板的制备方法通过优选单板,使用9层对称结构、三次成型的工艺,并配合多次砂光定厚,保证了各层单板含水率均匀稳定、板坯应力性能好,减小了各层单板间的应力以及胶水使用量,降低了成本且环保等级高,其不仅尺寸、颜色、表面的稳定性佳,还让该地板产品可以做出更大规格(地板宽度可达1.65m以上);
54.2)长边采用平扣技术,减少材料损耗;短边采用锁扣技术,提供锁合力;
55.3)板材顺纹朝外的设计使得地板吸湿能力降低,尺寸稳定性及防水性能得到提高;
56.4)表面涂饰步骤采用复式增强工艺,采用多层涂布高透明性uv底漆和耐黄变uv面
漆的做法,使漆膜具有耐磨、高色牢度、高表面强度、高表面耐冲击力的优点;
57.5)通过对实木复合地板的封边处理能够防止外界水汽进入地板内部,防止地板受潮变形及吸湿膨胀,提升地板使用寿命。
附图说明
58.图1是本发明所述的高稳定性实木复合地板的制备方法的高稳定性实木复合地板长边卡接示意图;
59.图2是本发明所述的高稳定性实木复合地板的制备方法的高稳定性实木复合地板短边卡接示意图。
60.标号说明:
61.长边凹槽1、长边凸榫2、台阶a3、台阶b4、短边凸榫5、卡槽a6、卡槽b7、上层台阶a3-1、下层台阶a3-2、上层台阶b4-1、下层台阶b4-2、凸条a5-1、凸条b4-2-1。
具体实施方式
62.下面结合说明书附图1-2对本发明的技术方案进行详细说明。
63.实施例1
64.如图1-2所示,本发明所述的一种高稳定性实木复合地板的制备方法,主要包括以下依序进行的步骤:
65.(一)选材:
66.选用含水率为10%,厚度为2.4mm的桉木单板和含水率为10%,厚度为0.5mm的杂木单板;
67.(二)分层热压:
68.(1)第一次成型:
69.①
布胶:将三棵树无醛胶以单面布胶方式涂布于两两相邻的桉木单板之间,且布胶量为300g/m2;
70.②
板材组坯:将桉木单板叠放在一起,且该两两相邻的桉木单板之间的桉木单板的延伸方向相互垂直;
71.③
冷压:组坯完成于常温下陈放10min,再以压力0.7mpa/m2保压30min,之后对重叠部分进行修割,空缺部分进行填补;
72.④
热压:于128℃以压力0.9mpa/m2保压7min后,再缓慢将压力降至0.2mpa/m2,保压2.5min,之后再缓慢将压力降至常压,即获得板材坯料;
73.(2)养生、砂光定厚:将板材坯料堆垛,并以200kg的重物平压4天进行养生,之后对板材坯料的两面均匀砂光定厚,以砂平为准,且公差控制在
±
0.2mm;
74.(3)第二次成型:
75.①
布胶:将三棵树无醛胶以单面布胶方式涂布于两两相邻的桉木单板或桉木单板与板材坯料之间,且布胶量为220g/m2;
76.②
板材组坯:将两层桉木单板、板材坯料以及两层桉木单板自下而上依次叠放在一起,且两两相邻的桉木单板或桉木单板与板材坯料之间的延伸方向相互垂直;
77.③
冷压:组坯完成于常温下陈放10min,再以压力0.7mpa/m2保压30min;之后对重
叠部分进行修割,空缺部分进行填补;
78.④
热压:于128℃以压力0.9mpa/m2保压13min后,先缓慢将压力降至0.5mpa/m2,保压2.5min,之后再缓慢将压力降至常压,即获得基板;
79.(4)养生、修边、砂光定厚:将基板堆垛,并以200kg的重物平压6天进行养生,之后先对基板组坯进行修补,再对基板组坯的两面均匀砂光定厚,以砂平为准,且公差控制在
±
0.2mm;
80.(5)第三次成型:
81.将杂木单板、基板组坯以及杂木单板自下而上依次叠放贴合在一起,每层杂木单板由相互平行的杂木单板组成,且两两相邻的杂木单板与基板组坯之间的延伸方向相互垂直,即获得所述高稳定性实木复合地板组坯;
82.(三)封闭、隔离涂饰:对高稳定性实木复合地板组坯的表面涂布标准色底层和数码喷涂装饰层;
83.(四)开槽榫:在高稳定性实木复合地板组坯的相对的端面上分别开设槽和榫,相邻高稳定性实木复合地板间能通过槽和榫相互配合连接;
84.(五)表面涂饰:对高稳定性实木复合地板组坯进行表面涂饰;
85.(六)封边处理:对表面涂饰后的高稳定性实木复合地板组坯进行封边处理,即获得高稳定性实木复合地板。
86.步骤(四)开槽榫的步骤具体为:高稳定性实木复合地板组坯间长边相对的端面上的槽和榫以平扣方式相互配合,短边相对的端面上的槽和榫以锁扣方式相互配合。
87.步骤(四)开槽榫的步骤具体为:在高稳定性实木复合地板组坯两长边端面上分别开设长边凹槽1和设置长边凸榫2,该长边凹槽1和长边凸榫2均沿长边延伸,该长边凸榫2向长边端面外旁侧伸出且与长边延伸方向相垂直,相邻高稳定性实木复合地板件的长边凹槽1和长边凸榫2能相互配合;
88.高稳定性实木复合地板组坯的一个短边端面顶部为二层台阶状结构,该台阶a3沿短边延伸方向延伸,且上层台阶a3-1较下层台阶a3-2突出高稳定性实木复合地板组坯外部,短边端面底部设有向短边端面外旁侧突出的短边凸榫5,该短边凸榫5沿短边延伸方向延伸,短边凸榫5朝向台阶a3一侧面的外边沿处设有向上层台阶a3-1方向凸起且沿短边延伸的凸条a5-1;台阶a3与短边凸榫5之间形成卡槽a6;另一个短边端面顶部为二层台阶状结构,该台阶b4沿短边延伸,且下层台阶b4-2较上层台阶b4-1突出高稳定性实木复合地板组坯外部,该下层台阶b4-2背向的上层台阶b4-1一侧面外边沿处设有背向上层台阶b4-1方向凸起且沿短边延伸的凸条b4-2-1,凸条b4-2-1与短边端面之间形成卡槽b7;相邻的高稳定性实木复合地板组坯间通过下层台阶b4-2、凸条b4-2-1与卡槽a6的卡接,以及凸条a5-1与卡槽b7的卡接相互配合。
89.步骤(二)分层热压中还包括:第一次成型、第二次成型和第三次成型中,使板材坯料、基板组坯和高稳定性实木复合地板组坯的长边和短边端面处的桉木单板或杂木单板的顺纹一面朝外。
90.步骤(三)的步骤具体为:
91.(1)涂布标准色底层:对高稳定性实木复合地板组坯表面进行处理,之后通过辊涂方式将腻子涂布于高稳定性实木复合地板组坯表面,并过红外线迅速干燥;
92.(2)数码喷涂装饰层:采用智能数码打印机和高保色油墨,将数码装饰图直接喷印在经涂布标准色底层处理后的高稳定性实木复合地板组坯表面。
93.步骤(五)表面涂饰的步骤具体为:
94.(1)涂布高透明性uv底漆:通过滚涂或淋涂的方式在经过开槽榫后的高稳定性实木复合地板组坯表面涂布4层的高透明性uv底漆;
95.(2)涂布耐黄变uv面漆:通过滚涂或淋涂的方式在涂布高透明性uv底漆后的高稳定性实木复合地板组坯表面涂布4层的耐黄变uv面漆。
96.步骤(六)封边处理的具体步骤为:向表面涂饰后的高稳定性实木复合地板组坯的四个端面喷涂熔融的防水蜜蜡,喷涂量为50g/m2,即获得高稳定性实木复合地板。
97.所述熔融的防水蜜蜡的温度为75℃。
98.实施例2
99.如图1-2所示,本发明所述的一种高稳定性实木复合地板的制备方法,主要包括以下依序进行的步骤:
100.(一)选材:
101.选用含水率为8%,厚度为2.6mm的桉木单板和含水率为8%,厚度为0.6mm的杂木单板;
102.(二)分层热压:
103.(1)第一次成型:
104.①
布胶:将三棵树无醛胶以单面布胶方式涂布于两两相邻的桉木单板之间,且布胶量为250g/m2;
105.②
板材组坯:将桉木单板叠放在一起,且该两两相邻的桉木单板之间的桉木单板的延伸方向相互垂直;
106.③
冷压:组坯完成于常温下陈放12min,再以压力0.8mpa/m2保压28min,之后对重叠部分进行修割,空缺部分进行填补;
107.④
热压:于130℃以压力0.8mpa/m2保压8min后,再缓慢将压力降至0.15mpa/m2,保压3min,之后再缓慢将压力降至常压,即获得板材坯料;
108.(2)养生、砂光定厚:将板材坯料堆垛,并以250kg的重物平压3天进行养生,之后对板材坯料的两面均匀砂光定厚,以砂平为准,且公差控制在
±
0.2mm;
109.(3)第二次成型:
110.①
布胶:将三棵树无醛胶以单面布胶方式涂布于两两相邻的桉木单板或桉木单板与板材坯料之间,且布胶量为230g/m2;
111.②
板材组坯:将两层桉木单板、板材坯料以及两层桉木单板自下而上依次叠放在一起,且两两相邻的桉木单板或桉木单板与板材坯料之间的延伸方向相互垂直;
112.③
冷压:组坯完成于常温下陈放13min,再以压力0.6mpa/m2保压32min;之后对重叠部分进行修割,空缺部分进行填补;
113.④
热压:于125℃以压力1.0mpa/m2保压12min后,先缓慢将压力降至0.55mpa/m2,保压2min,之后再缓慢将压力降至常压,即获得基板;
114.(4)养生、修边、砂光定厚:将基板堆垛,并以250kg的重物平压7天进行养生,之后先对基板组坯进行修补,再对基板组坯的两面均匀砂光定厚,以砂平为准,且公差控制在
±
0.2mm;
115.(5)第三次成型:
116.将杂木单板、基板组坯以及杂木单板自下而上依次叠放贴合在一起,每层杂木单板由相互平行的杂木单板组成,且两两相邻的杂木单板与基板组坯之间的延伸方向相互垂直,即获得所述高稳定性实木复合地板组坯;
117.(三)封闭、隔离涂饰:对高稳定性实木复合地板组坯的表面涂布标准色底层和数码喷涂装饰层;
118.(四)开槽榫:在高稳定性实木复合地板组坯的相对的端面上分别开设槽和榫,相邻高稳定性实木复合地板间能通过槽和榫相互配合连接;
119.(五)表面涂饰:对高稳定性实木复合地板组坯进行表面涂饰;
120.(六)封边处理:对表面涂饰后的高稳定性实木复合地板组坯进行封边处理,即获得高稳定性实木复合地板。
121.步骤(四)开槽榫的步骤具体为:高稳定性实木复合地板组坯间长边相对的端面上的槽和榫以平扣方式相互配合,短边相对的端面上的槽和榫以锁扣方式相互配合。
122.步骤(四)开槽榫的步骤具体为:在高稳定性实木复合地板组坯两长边端面上分别开设长边凹槽1和设置长边凸榫2,该长边凹槽1和长边凸榫2均沿长边延伸,该长边凸榫2向长边端面外旁侧伸出且与长边延伸方向相垂直,相邻高稳定性实木复合地板件的长边凹槽1和长边凸榫2能相互配合;
123.高稳定性实木复合地板组坯的一个短边端面顶部为二层台阶状结构,该台阶a3沿短边延伸方向延伸,且上层台阶a3-1较下层台阶a3-2突出高稳定性实木复合地板组坯外部,短边端面底部设有向短边端面外旁侧突出的短边凸榫5,该短边凸榫5沿短边延伸方向延伸,短边凸榫5朝向台阶a3一侧面的外边沿处设有向上层台阶a3-1方向凸起且沿短边延伸的凸条a5-1;台阶a3与短边凸榫5之间形成卡槽a6;另一个短边端面顶部为二层台阶状结构,该台阶b4沿短边延伸,且下层台阶b4-2较上层台阶b4-1突出高稳定性实木复合地板组坯外部,该下层台阶b4-2背向的上层台阶b4-1一侧面外边沿处设有背向上层台阶b4-1方向凸起且沿短边延伸的凸条b4-2-1,凸条b4-2-1与短边端面之间形成卡槽b7;相邻的高稳定性实木复合地板组坯间通过下层台阶b4-2、凸条b4-2-1与卡槽a6的卡接,以及凸条a5-1与卡槽b7的卡接相互配合。
124.步骤(二)分层热压中还包括:第一次成型、第二次成型和第三次成型中,使板材坯料、基板组坯和高稳定性实木复合地板组坯的长边和短边端面处的桉木单板或杂木单板的顺纹一面朝外。
125.步骤(三)的步骤具体为:
126.(1)涂布标准色底层:对高稳定性实木复合地板组坯表面进行处理,之后通过辊涂方式将腻子涂布于高稳定性实木复合地板组坯表面,并过红外线迅速干燥;
127.(2)数码喷涂装饰层:采用智能数码打印机和高保色油墨,将数码装饰图直接喷印在经涂布标准色底层处理后的高稳定性实木复合地板组坯表面。
128.步骤(五)表面涂饰的步骤具体为:
129.(1)涂布高透明性uv底漆:通过滚涂或淋涂的方式在经过开槽榫后的高稳定性实木复合地板组坯表面涂布5层的高透明性uv底漆;
130.(2)涂布耐黄变uv面漆:通过滚涂或淋涂的方式在涂布高透明性uv底漆后的高稳定性实木复合地板组坯表面涂布5层的耐黄变uv面漆。
131.步骤(六)封边处理的具体步骤为:向表面涂饰后的高稳定性实木复合地板组坯的四个端面喷涂熔融的防水蜜蜡,喷涂量为40g/m2,即获得高稳定性实木复合地板。
132.所述熔融的防水蜜蜡的温度为70℃。
133.实施例3
134.如图1-2所示,本发明所述的一种高稳定性实木复合地板的制备方法,主要包括以下依序进行的步骤:
135.(一)选材:
136.选用含水率为12%,厚度为2.2mm的桉木单板和含水率为14%,厚度为0.4mm的杂木单板;
137.(二)分层热压:
138.(1)第一次成型:
139.①
布胶:将三棵树无醛胶以单面布胶方式涂布于两两相邻的桉木单板之间,且布胶量为350g/m2;
140.②
板材组坯:将桉木单板叠放在一起,且该两两相邻的桉木单板之间的桉木单板的延伸方向相互垂直;
141.③
冷压:组坯完成于常温下陈放15min,再以压力0.6mpa/m2保压32min,之后对重叠部分进行修割,空缺部分进行填补;
142.④
热压:于125℃以压力1.0mpa/m2保压6min后,再缓慢将压力降至0.25mpa/m2,保压2min,之后再缓慢将压力降至常压,即获得板材坯料;
143.(2)养生、砂光定厚:将板材坯料堆垛,并以220kg的重物平压5天进行养生,之后对板材坯料的两面均匀砂光定厚,以砂平为准,且公差控制在
±
0.2mm;
144.(3)第二次成型:
145.①
布胶:将三棵树无醛胶以单面布胶方式涂布于两两相邻的桉木单板或桉木单板与板材坯料之间,且布胶量为210g/m2;
146.②
板材组坯:将两层桉木单板、板材坯料以及两层桉木单板自下而上依次叠放在一起,且两两相邻的桉木单板或桉木单板与板材坯料之间的延伸方向相互垂直;
147.③
冷压:组坯完成于常温下陈放15min,再以压力0.8mpa/m2保压28min;之后对重叠部分进行修割,空缺部分进行填补;
148.④
热压:于130℃以压力0.8mpa/m2保压15min后,先缓慢将压力降至0.45mpa/m2,保压3min,之后再缓慢将压力降至常压,即获得基板;
149.(4)养生、修边、砂光定厚:将基板堆垛,并以220kg的重物平压5天进行养生,之后先对基板组坯进行修补,再对基板组坯的两面均匀砂光定厚,以砂平为准,且公差控制在
±
0.2mm;
150.(5)第三次成型:
151.将杂木单板、基板组坯以及杂木单板自下而上依次叠放贴合在一起,每层杂木单板由相互平行的杂木单板组成,且两两相邻的杂木单板与基板组坯之间的延伸方向相互垂直,即获得所述高稳定性实木复合地板组坯;
152.(三)封闭、隔离涂饰:对高稳定性实木复合地板组坯的表面涂布标准色底层和数码喷涂装饰层;
153.(四)开槽榫:在高稳定性实木复合地板组坯的相对的端面上分别开设槽和榫,相邻高稳定性实木复合地板间能通过槽和榫相互配合连接;
154.(五)表面涂饰:对高稳定性实木复合地板组坯进行表面涂饰;
155.(六)封边处理:对表面涂饰后的高稳定性实木复合地板组坯进行封边处理,即获得高稳定性实木复合地板。
156.步骤(四)开槽榫的步骤具体为:高稳定性实木复合地板组坯间长边相对的端面上的槽和榫以平扣方式相互配合,短边相对的端面上的槽和榫以锁扣方式相互配合。
157.步骤(四)开槽榫的步骤具体为:在高稳定性实木复合地板组坯两长边端面上分别开设长边凹槽1和设置长边凸榫2,该长边凹槽1和长边凸榫2均沿长边延伸,该长边凸榫2向长边端面外旁侧伸出且与长边延伸方向相垂直,相邻高稳定性实木复合地板件的长边凹槽1和长边凸榫2能相互配合;
158.高稳定性实木复合地板组坯的一个短边端面顶部为二层台阶状结构,该台阶a3沿短边延伸方向延伸,且上层台阶a3-1较下层台阶a3-2突出高稳定性实木复合地板组坯外部,短边端面底部设有向短边端面外旁侧突出的短边凸榫5,该短边凸榫5沿短边延伸方向延伸,短边凸榫5朝向台阶a3一侧面的外边沿处设有向上层台阶a3-1方向凸起且沿短边延伸的凸条a5-1;台阶a3与短边凸榫5之间形成卡槽a6;另一个短边端面顶部为二层台阶状结构,该台阶b4沿短边延伸,且下层台阶b4-2较上层台阶b4-1突出高稳定性实木复合地板组坯外部,该下层台阶b4-2背向的上层台阶b4-1一侧面外边沿处设有背向上层台阶b4-1方向凸起且沿短边延伸的凸条b4-2-1,凸条b4-2-1与短边端面之间形成卡槽b7;相邻的高稳定性实木复合地板组坯间通过下层台阶b4-2、凸条b4-2-1与卡槽a6的卡接,以及凸条a5-1与卡槽b7的卡接相互配合。
159.步骤(二)分层热压中还包括:第一次成型、第二次成型和第三次成型中,使板材坯料、基板组坯和高稳定性实木复合地板组坯的长边和短边端面处的桉木单板或杂木单板的顺纹一面朝外。
160.步骤(三)的步骤具体为:
161.(1)涂布标准色底层:对高稳定性实木复合地板组坯表面进行处理,之后通过辊涂方式将腻子涂布于高稳定性实木复合地板组坯表面,并过红外线迅速干燥;
162.(2)数码喷涂装饰层:采用智能数码打印机和高保色油墨,将数码装饰图直接喷印在经涂布标准色底层处理后的高稳定性实木复合地板组坯表面。
163.步骤(五)表面涂饰的步骤具体为:
164.(1)涂布高透明性uv底漆:通过滚涂或淋涂的方式在经过开槽榫后的高稳定性实木复合地板组坯表面涂布6层的高透明性uv底漆;
165.(2)涂布耐黄变uv面漆:通过滚涂或淋涂的方式在涂布高透明性uv底漆后的高稳定性实木复合地板组坯表面涂布6层的耐黄变uv面漆。
166.步骤(六)封边处理的具体步骤为:向表面涂饰后的高稳定性实木复合地板组坯的四个端面喷涂熔融的防水蜜蜡,喷涂量为60g/m2,即获得高稳定性实木复合地板。
167.所述熔融的防水蜜蜡的温度为80℃。
168.实验数据:
169.一、高稳定性实木复合地板漆膜主要性能检测
170.检测方法:依据gb/t 18103-2013进行检测
171.检测结果如下:
172.表1高稳定性实木复合地板漆膜主要性能检测结果
[0173][0174]
二、高稳定性实木复合地板性能检测
[0175]
检测方法:
[0176]
1.耐热尺寸稳定性:将试件放入温度为(80
±
2)℃的鼓风干燥箱内,保证空气循环,处理试件(24
±
0.25)h后,取出试件置于室温条件,并在10min内测量原画线位置处试件中心线的长度;
[0177]
2.耐湿尺寸稳定性:把试件放入温度为(40
±
2)℃、相对湿度(90
±
3)%的恒温恒湿箱中处理(24
±
0.25)h后,取出试件置于室温条件,并在10min内测量原画线位置处试件中心线的长度;
[0178]
3.耐光色牢度:按gb/t 19657-2013中4.30的规定进行。
[0179]
检测结果如下:
[0180]
表2高稳定性实木复合地板性能检测结果
[0181][0182]
由表1、2可知,本技术高稳定性实木复合地板的制备方法制备的高稳定性实木复合地板漆膜的漆膜附着力性能符合国标gb/t 18103-2013,表面耐磨、漆膜硬度、表面耐污染、表面抗冲击、耐光色牢度(蓝色羊毛标准)等性能均优于国标gb/t 18103-2013,且该高稳定性实木复合地板的耐热尺寸稳定性、耐湿尺寸稳定性、耐光色牢度均综合性能优于炭化木、胶合板、纤维板等木质板材,可见其能有效避免了尺寸稳定性不佳的问题。
[0183]
本发明所述的高稳定性实木复合地板的制备方法并不只仅仅局限于上述实施例,凡是依据本发明原理的任何改进或替换,均应在本发明的保护范围之内。
再多了解一些
本文用于企业家、创业者技术爱好者查询,结果仅供参考。