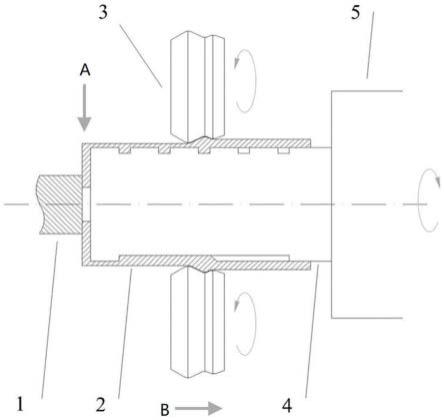
1.本发明涉及金属塑性加工技术领域,具体涉及一种带内筋筒形件的多级旋轮式随动约束旋压成形方法。
背景技术:
2.超高速飞行器和大型运载火箭等航空航天重大装备的制造水平是衡量国家高精尖科技水平的关键标志之一。带内筋薄壁筒形件因兼具轻量高效、高性能和高可靠性等优点,往往被用作这些重大装备的关键主体结构。基于当前重大装备的极端服役要求,亟需发展带内筋薄壁筒形件的高筋薄腹整体成形方法,以减轻构件重量、提高构件的承载性能。流动旋压成形技术是一种先进的点加载增量精确塑性成形技术,有利于实现带内筋薄壁筒形件的一体化制造。而在此类构件的成形过程中,由于模具结构、加载工具及轨迹等条件的约束作用,构件内筋区域的材料流入不足,从而使得成形过程中常出现内筋充填高度不足的问题。一般来说,此类构件的筋高对筒体的结构刚度和服役性能影响较大,故而在工程应用中提高内筋充填高度是亟需解决的关键问题。
3.目前,针对带内筋筒形件内筋充填高度不足的难题,能够有效改善内筋充填高度的有效方法鲜有报道。期刊文献(张利鹏,刘智冲.带内筋铝合金筒形件强力旋压成形工艺研究[j].2007,14(6):109-113.)针对铝合金带纵向内筋筒形件筋高不足的问题,采用小减薄率多道次成形的工艺,结果发现在纵筋内表面出现了周向裂纹。专利文献cn 109940079 b公开了一种提高带内筋筒形件旋压成形内筋充填高度的方法及装置,通过在现有带筋槽芯模的基础上增加一个固定环和轴向约束环,从而增大材料流动的轴向阻力。然而该方法的轴向载荷参数化调控困难,且对构件的长程加载适应性差,容易产生局部扩径等缺陷。期刊文献(夏琴香,胡昱,孙凌燕,等.旋轮型面对矩形内齿旋压成形影响的数值模拟[j].2007,35(8):1-6.)比较了不同旋轮工作型面对内筋成形质量的影响,发现台阶型旋轮成形的平均筋高低于圆弧型旋轮。现有技术中,期刊文献(m.zhan,j.guo,m.w.fu,et al.formation mechanism and control of flaring in forward tube spinning[j].international journal of advanced manufacturing technology,2018,94:59-72.)针对无筋筒形件流动旋压成形过程中的尾部扩口现象,公开了一种控制装置,主要通过在已有旋轮上加装压圈实现;然而该装置与台阶型旋轮结构相似,对带内筋薄壁筒形件的充填高度作用不明显。
[0004]
因此,提出一种能有效提高带内筋薄壁筒形件内筋充填高度的方法,对于深入及拓展此类构件的应用很有必要。
技术实现要素:
[0005]
为了解决现有技术存在的上述技术问题,本发明提供了一种带内筋筒形件的多级旋轮式随动约束旋压成形方法,该成形方法操作简单方便,且便于匹配不同的旋压工艺参数,且易于组装,在一定程度上节省了生产成本。
[0006]
为实现上述目的,本发明提供了一种带内筋筒形件的多级旋轮式随动约束旋压成形方法,其包括以下步骤:
[0007]
s1,将带有筋槽的芯模安装至旋压机床的芯模主轴上,芯模上涂刷润滑剂,取中空的筒坯,并通过芯模前端的尾顶机构将筒坯固定在芯模上,然后组装多级旋轮并安装在旋压机床的旋轮架上;
[0008]
s2,调整多级旋轮位置,以使多级旋轮在旋压时随芯模的旋转而被动旋转,同时控制多级旋轮轴向进给至筒坯的起始旋压位置,多级旋轮对筒坯先进行径向压下直至预设的减薄率ψ,然后根据设定的轴向进给量控制多级旋轮轴向进给,从而使筒坯产生筋区和腹板区,以得到带内筋筒形件;
[0009]
s3,将多级旋轮沿其径向进给的反方向退出,将多级旋轮更换为双锥形旋轮,再次径向进给直至双锥形旋轮与筒坯的终旋端接触,利用双锥形旋轮的退出角卸出芯模,最后取出成形的带内筋筒形件。
[0010]
作为本发明的进一步优选技术方案,所述筒坯为挤压筒坯或板材卷焊筒坯。
[0011]
作为本发明的进一步优选技术方案,所述芯模上设有以下任意一种形式的筋槽:a1、环向横筋槽;a2、轴向纵筋槽;a3、正交筋槽;a4、非正交筋槽。
[0012]
作为本发明的进一步优选技术方案,所述芯模上设置的筋槽具有有拔模斜度或无拔模斜度。
[0013]
作为本发明的进一步优选技术方案,所述多级旋轮为一体式回转体结构或分体式回转结构中的任意一种,且为一体式回转体结构或分体式回转结构的多级旋轮均包括一级旋轮和二级旋轮,其中:
[0014]
当多级旋轮为一体式回转体结构时,该多级旋轮上设有用于其安装位置的确定以及对其一体式回转体结构进行固定用的定位安装孔;
[0015]
当多级旋轮为分体回转体结构时,该多级旋轮的一级旋轮和二级旋轮均设有用于其安装位置的确定以及对其分体回转体结构进行固定用的定位安装孔,且该多级旋轮的一级旋轮和二级旋轮上的定位安装孔数量相等。
[0016]
作为本发明的进一步优选技术方案,所述多级旋轮的一级旋轮和二级旋轮的最大直径分别为d
m1
和d
m2
,二者的半径差δr满足以下公式:
[0017][0018]
其中,c为二级旋轮最大直径与坯料的间隙控制系数,满足以下公式:
[0019]
c∈[0,0.2]。
ꢀꢀꢀꢀꢀꢀꢀꢀꢀ
(5)
[0020]
作为本发明的进一步优选技术方案,所述多级旋轮中一级旋轮的厚度为h1,其进给侧和退出侧的厚度分别为h
a1
和h
r1
;二级旋轮的厚度为h2,其进给侧和退出侧的厚度分别为h
a2
和h
r2
;一级旋轮和二级旋轮最大直径的轴向级差为s
12
,满足以下公式:
[0021][0022]
其中,c2为单级旋轮进给侧和退出侧的厚度比例系数。
[0023]
作为本发明的进一步优选技术方案,所述多级旋轮的一级旋轮为圆弧型旋轮或双锥型旋轮;二级旋轮为圆弧型旋轮或双锥型旋轮。
[0024]
作为本发明的进一步优选技术方案,所述多级旋轮数量为nm,nm≥1,若nm大于1,则其沿筒坯周向等角度分布。
[0025]
作为本发明的进一步优选技术方案,步骤s2中处于起始旋压位置的多级旋轮法线平行于芯模的轴线。
[0026]
本发明的带内筋筒形件的多级旋轮式随动约束旋压成形方法,通过采用上述技术方案,可以达到如下有益效果:
[0027]
1)本发明提出的一种带内筋筒形件的多级旋轮式随动约束旋压成形方法,其主要改进点在于对旋压成形加载工具几何结构的改变,即将多个旋轮的几何结构进行复合形成多级旋轮,利用旋轮不同级间的工作角与退出角构成的凹槽实现旋轮前方隆起材料的进一步聚集,从而促进筋槽区域材料的径向流动,改善构件的内筋充填高度,为带内筋筒形件的高筋薄腹成形提供了新思路;
[0028]
2)本发明提出的一种带带内筋筒形件的多级旋轮式随动约束旋压成形方法,通过改进旋轮结构为多级旋轮提供了一种随动约束,且是一种局部加载整体成形技术,操作简单方便;
[0029]
3)本发明提出的多级旋轮分为一体结构和分体结构,便于匹配不同的旋压工艺参数,且易于组装,在一定程度上节省了生产成本。
附图说明
[0030]
下面结合附图和具体实施方式对本发明作进一步详细的说明。
[0031]
图1为本发明实施例中的旋轮安装位置示意图;
[0032]
图2为本发明实施例中一体式双锥-双锥型多级旋轮结构示意图;其中,图2中(a)为一体式多级旋轮的剖面结构示意图,图2中(b)为一体式多级旋轮的俯视图;
[0033]
图3为分体式多级旋轮的剖面结构示意图;
[0034]
图4为分体式多级旋轮中一级旋轮的结构示意图;其中,图4中(a)为一级旋轮的剖面结构示意图,图4中(b)为一级旋轮的俯视图;
[0035]
图5为分体式多级旋轮中二级旋轮的结构示意图;其中,图5中(a)为二级旋轮的剖面结构示意图,图5中(b)为二级旋轮的俯视图;
[0036]
图6为除本发明实施例外多级旋轮的组合形式;其中,图6中(a)为双锥-圆弧型,图6中(b)为圆弧-圆弧型,图6中(c)为圆弧-双锥型;
[0037]
图7为本发明实施例中,沿周向不同测量角度的横筋高度分布情况及横筋高度相对提升率;
[0038]
图8为本发明实施例中,沿轴向不同测量距离的纵筋高度分布情况及纵筋高度相对提升率;
[0039]
图中:1、尾顶机构;2、筒坯;3、多级旋轮;4、芯模;5、芯模主轴;6、一级旋轮;7、二级旋轮;8、定位安装孔。
[0040]
本发明目的实现、功能特点及优点将结合实施例,参照附图做进一步说明。
具体实施方式
[0041]
下面将结合附图以及具体实施方式,对本发明做进一步描述。较佳实施例中所引用的如“上”、“下”、“左”、“右”、“中间”及“一”等用语,仅为便于叙述的明了,而非用以限定本发明可实施的范围,其相对关系的改变或调整,在无实质变更技术内容下,当亦视为本发明可实施的范畴。
[0042]
本发明提供了一种带内筋筒形件的多级旋轮式随动约束旋压成形方法,通过多级旋轮3的多个旋轮几何结构的复合,利用旋轮级间的凹槽实现旋压过程中旋轮前方隆起材料的进一步聚集,从而促进筋槽区域材料的径向流动,实现内筋充填高度的增加,其方法包括以下步骤:
[0043]
步骤s1,制备中空的筒坯2,其外径和厚度分别为d和t。
[0044]
在本发明的一实施例中,所述筒坯2为挤压筒坯,其外径d=214mm,厚度t=7mm。当然,在具体实施中,所述筒坯2还可以为板材卷焊筒坯。
[0045]
步骤s2,将带有筋槽的芯模4安装至芯模主轴5上,芯模4上涂刷润滑剂,并通过芯模4前端的尾顶机构1将s1步骤中制备的筒坯2固定在芯模4上,组装多级旋轮3并安装在旋轮架上,筒坯2、芯模4及多级旋轮3的装配结构参阅图1所示。
[0046]
在本发明的实施例中,步骤s2中的芯模4上设有正交筋槽,芯模4上设置的筋槽具有有拔模斜度,且拔模斜度为3
°
。
[0047]
在本发明的实施例中,步骤s2中的多级旋轮3为一体式回转体结构,又称作一体式多级旋轮,该多级旋轮3的定位安装孔8设置有8个,该定位安装孔8用于一体式多级旋轮3的安装位置的确定以及对其一体式回转体结构进行固定,一体式多级旋轮的一级旋轮6和二级旋轮7均采用双锥型旋轮(双锥-双锥型),该一体式双锥-双锥型多级旋轮结构参阅图2所示。当然,多级旋轮3还可以根据加工需求选择为分体式回转结构,该分体式回转结构的多级旋轮3的剖面结构参阅图3所示,该多级旋轮3的一级旋轮6上和二级旋轮7上分别设置有相同数量的定位安装孔8,该定位安装孔8用于分体式回转结构的多级旋轮3安装位置的确定以及对其分体式回转结构进行固定。分体式回转结构的多级旋轮3中一级旋轮6的结构参阅图4所示,分体式回转结构的多级旋轮3中二级旋轮7的结构参阅图5所示。多级旋轮3的一级旋轮6和二级旋轮7均可根据需要选择圆弧型旋轮或双锥型旋轮中的任意一种,一级旋轮6和二级旋轮7的结构形成除本实例的双锥-双锥型,还可根据需求选择为双锥-圆弧型、圆弧-圆弧型、圆弧-圆弧型,具体参阅图6所示。该实施例中的多级旋轮3分为一体结构和分体结构,这样不仅便于匹配不同的旋压工艺参数,而且易于组装,且在一定程度上节省了生产成本。
[0048]
在本发明的实施例中,所述多级旋轮3的一级旋轮6和二级旋轮7的最大直径分别为d
m1
和d
m2
,二者的半径差δr满足公式:
[0049][0050]
其中,c为二级旋轮7最大直径与坯料的间隙控制系数,满足公式:
[0051]
c∈[0,0.2]
ꢀꢀꢀꢀꢀꢀꢀꢀ
(8)
[0052]
该实施例中d
m1
=250mm,间隙控制系数c=0,d
m2
=244mm。
[0053]
优选地,多级旋轮3装置中的一级旋轮6的厚度为h1,其进给侧和退出侧的厚度分别为h
a1
和h
r1
;二级旋轮7的厚度为h2,其进给侧和退出侧的厚度分别为h
a2
和h
r2
;一级旋轮6和二级旋轮7最大直径的轴向级差为s
12
,满足公式:
[0054][0055]
其中,c2为单级旋轮进给侧和退出侧的厚度比例系数。在本实施例中,一级旋轮6的厚度为h1=35mm,厚度比例系数c2=4/3,其进给侧和退出侧的厚度分别为h
a1
=15mm和h
r1
=20mm;二级旋轮7的厚度为h2=15mm,厚度比例系数c2=1,其进给侧和退出侧的厚度分别为h
a2
=7.5mm和h
r2
=7.5mm;一级旋轮6和二级旋轮7最大直径的轴向级差为s
12
=22.5mm。
[0056]
具体实施中,多级旋轮3的数量为nm=2,两个多级旋轮3沿筒坯2周向等角度分布。
[0057]
步骤s3,调整多级旋轮3位置,以使多级旋轮3在旋压时随芯模4的旋转而被动旋转,同时控制多级旋轮3轴向进给至筒坯2的起旋位置(参阅图1中箭头a所指位置),多级旋轮3对筒坯2先进行径向压下直至预设的减薄率ψ,然后根据设定的轴向进给量控制多级旋轮3轴向进给(参阅图1中箭头b所指方向),从而使筒坯2产生筋区和腹板区,以得到带内筋筒形件。
[0058]
本发明实施例中,步骤s3中的随动旋压过程的多级旋轮3运动轨迹为,先进行径向压下直至预设的减薄率ψ=42.86%,然后根据设定的轴向进给量控制多级旋轮3进行轴向进给。需要说明的,依据本实施例提供的多级旋轮3式随动约束旋压成形方法,在步骤s3中,多级旋轮3的径向进给速度为1mm/s,轴向进给的进给比为1mm/r,芯模4上的纵横筋槽宽度为10mm、深度为4mm,内基槽的圆角半径为2mm。
[0059]
具体实施中,步骤s3中多级旋轮3安装起始位置为多级旋轮3法线平行于旋压芯模4的轴线。
[0060]
步骤s4,将多级旋轮3沿其径向进给的反方向退出,将多级旋轮3更换为双锥形旋轮,再次径向进给直至双锥形旋轮与筒坯2的终旋端接触,利用双锥形旋轮的退出角卸出芯模4,最后取出成形的带内筋筒形件,完成加工。
[0061]
本发明提出的一种带内筋筒形件的多级旋轮式随动约束旋压成形方法,其主要改进点在于对旋压成形加载工具几何结构的改变,即将多个旋轮的几何结构进行复合形成多级旋轮3,利用旋轮不同级间的工作角与退出角构成的凹槽实现旋轮前方隆起材料的进一步聚集,从而促进筋槽区域材料的径向流动,改善构件的内筋充填高度,为带内筋筒形件的高筋薄腹成形提供了新思路。
[0062]
对本发明加工成形的带内筋筒形件进行几何特征测量,利用激光扫描设备获取带内筋筒形件的几何数据,通过三维软件重构该构件的几何形状,并对构件的几何特征进行测量,获取筋高。获取的筋高数据如图7和图8所示。根据图7-8的数据结果可以看出,采用本发明提供的多级旋轮3式旋压成形方法能有效提升带内筋筒形件的纵横筋高,因此,该方法对带内筋筒形件的高筋薄壁制造具有重要的意义。
[0063]
在本发明申请的描述中,需要理解的是,术语“前”、“上”、“下”、、“径向”、“轴向”、“横”、“纵”等指代的方向或位置关系均基于附图实现,仅是为了便于本发明申请描述的简
化,而不是限定所指的装置或构件必须以特定的方向或位置运行。
[0064]
虽然以上描述了本发明的具体实施方式,但是本领域熟练技术人员应当理解,这些仅是举例说明,可以对本实施方式做出多种变更或修改,而不背离本发明的原理和实质,本发明的保护范围仅由所附权利要求书限定。
再多了解一些
本文用于企业家、创业者技术爱好者查询,结果仅供参考。