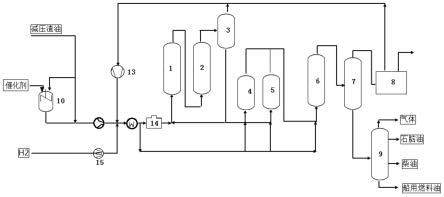
1.本发明方法涉及船用燃料油的制备领域,尤其涉及一种加氢制备船用燃料油的方法,特别是高金属(ni v≥150μg.g-1
)、高残炭(ccr≥16wt%)的重质馏分油、渣油和油砂沥青经过加氢裂化和加氢处理制备船用燃料油的方法。
背景技术:
2.目前,国内外油品市场对轻、重质油品的需求仍将呈持续上升的趋势,国ⅵ标准对油品加工提出了更高的要求。船用燃料油的标准也在进一步提升。在上述市场趋势下,既能以较经济合理的代价实现重油轻质化、又能使所得到的产品满足不断苛刻的汽柴油产品规格的炼油技术成了国内外炼油技术开发商重点开发的技术之一。
3.加氢是最有效的重质油原料预处理技术。通过加氢,显著降低这些原料中的金属、硫、氮、沥青质含量,提高氢碳比,进而为催化裂化和延迟焦化等装置提供优良的原料。目前实现工业应用的主要的加氢工艺是固定床工艺,该工艺具有成本低、操作简单,技术成熟等特点,是加工常规油品最重要的技术。但在固定床催化加氢处理中,如果原料黏度较大、金属杂质或沥青质较高,在加氢过程中,金属和焦炭会逐渐沉积在催化剂上,容易使催化剂快速失活,床层堵塞,压力升高,使装置操作频繁停工。加氢处理这类原料必须保证尽可能长的循环操作,无需停止设备。许多研究者提出了多种解决方法。
4.cn1322097c公开了一种采用可置换反应器和可短路反应器加氢处理重烃馏分的方法。先在第一加氢脱金属段中,然后在第二加氢脱硫段中加氢处理,其中加氢脱金属段前至少有一个保护区。所述的加氢处理方法包括下述步骤:a)—个步骤,其中使用保护区;b)一个步骤,在这个步骤期间该保护区短路,并且再生和/或更换该区段所含的催化剂;c)一个步骤,在这个步骤期间再接已再生和/或更换催化剂的保护区;d)—个步骤,其中至少一个加氢脱金属段和/或加氢脱硫段的反应器可以短路,并且再生和/或更换该区段所含的催化剂。但是这样的方法需要更高的初始投资。
5.cn1349554公开了一种带层状催化剂床层的上流式反应器系统加氢处理重质原料的方法。用至少两个不同加氢活性的催化剂的上流式固定床反应器加氢处理金属、硫和含碳残质污染的重质原料。但该方法运行周期短,一般不超过1年。
6.cn1144860公开了一种渣油加氢处理的方法。在重渣油加氢反应系统中的第一个反应器增设一个或多个进料口,同时改变原有的催化剂级配,当一反催化剂床层压降为装置设计最大压降的0.4-0.8倍时,依次改用下一个进料口,同时原有进料口可进循环油或循环油与原料油的混合物。该工艺能有效地防止床层压降和延长渣油加氢催化剂的使用寿命,而且可以增加装置的处理能力。
7.cn00110714.3公开了一种渣油处理方法。通过在重渣油加氢反应系统之前,采用一段吸附过滤剂床层或一段吸附过滤剂床层和一段吸附过滤催化剂床层同时使用,不仅可以最大程度地脱除原料油中携带的悬浮颗粒,而且还可以脱除掉原油中的环烷酸铁生成的硫化亚铁及大部分易生焦的物质,最大程度减少渣油加氢反应系统反应器的结垢,减少装
置运转周期内的因结垢造成的开停工次数。
8.cn1144863c公开了一种重质烃类催化加氢处理方法。将渣油临氢热裂化和固定床渣油加氢处理技术有机结合,重质烃类原料首先在悬浮床或类似的反应器中使原料进行缓和临氢热裂化预处理,然后再进入固定床加氢处理装置进行加氢处理,其特点是能适应固定床渣油加氢原料的重质化和劣质化,提高固定床渣油加氢装置运转寿命、降低其操作苛刻度。
9.cn1609176a公开了一种劣质重、渣油改质方法,特别是使用悬浮床加氢裂解和固定床加氢处理相组合生产优质重油催化裂化的方法。重、渣油先经过悬浮床缓和加氢裂解,使绝大部分或全部金属杂质从胶质和沥青质中游离出来;该加氢产物通过可切换操作或可在线置换添料的金属吸附反应器,吸附脱除悬浮床加氢裂解油中游离的金属杂质吸附脱金属后的产物送入渣油固定床加氢处理装置深度加氢脱除其它杂质,生产优质重油催化裂化原料。
技术实现要素:
10.本发明的目的是提供一种浆态床、滴流固定床、上流式液相加氢的组合工艺,浆态床加氢裂化可以对渣油进行深度转化,滴流固定床加氢前处理反应器可以对浆态床反应器携带的催化剂粉末有效截留,同时脱除金属。上流式液相加氢处理反应器进一步脱硫、脱氮,对油品深度精制,通过组合工艺,并恰当地选择有效的加氢催化剂,可以生产船用燃料油,兼产石脑油、柴油。
11.为此,本发明提供一种加氢制备船用燃料油的方法,所述方法包括:
12.2个浆态床加氢裂化反应器r1、r2,
13.2个滴流固定床加氢前处理反应器r3、r4,
14.1个上流式液相加氢处理反应器r5;
15.原料油与加氢裂化催化剂混合后,和氢气一起进入所述r1和/或r2,产物进入气液分离器s1进行分离得到气体产物和液体产物,气体产物循环回压缩机与新氢混合再次进入所述r1、r2,液体产物一部分作为循环油与新鲜原料混合后进入所述r1、r2,另一部分进入所述r3和/或r4,进行脱金属反应以及油浆中催化剂粉末的脱除,随后所得产物进入所述r5,进行进一步的加氢精制,所得产物进入分馏塔进行分馏得到气体、石脑油、柴油和船用燃料油。
16.本发明所述的加氢制备船用燃料油的方法,其中优选的是,所述原料油为重质油或/和渣油。
17.本发明所述的加氢制备船用燃料油的方法,其中优选的是,所述r1、r2为直筒式浆态床加氢裂化反应器。
18.本发明所述的加氢制备船用燃料油的方法,其中优选的是,所述气液分离器s1进行气液分离后产物循环比为5%~40%。
19.本发明所述的加氢制备船用燃料油的方法,其中优选的是,所述r5采取在反应器多点设置注氢,以补充r5的氢气消耗。
20.本发明所述的加氢制备船用燃料油的方法,其中优选的是,所述r1、r2可串联或并联或只使用其中一个,所述r3、r4可并联使用或只使用其中一个。
21.相应地,该方法所包含的流程有:(1)、(r1 r2) r3 r5;(2)、(r1 r2) r4 r5;(3)、(r1 r2) (r3//r4) r5;(4)、r1 r3 r5;(5)、r1 r4 r5;(6)、r2 r4 r5(7)、(r1) (r3//r4) r5;(8)(r2) (r3//r4) r5;(9)(r1//r2) r3 r5;(10)(r1//r2) r4 r5;(10)(r1//r2) (r3//r4) r5。一共十种工艺流程,各工艺流程可根据所加工原料的轻重,以及生产的实际需求来切换,通常在加工劣质渣油或对原料的加氢程度度较深时,可采用r1、r2串联,在加工较轻原料时,可只使用r1或r2。r3、r4为并联反应器,当其中一个催化剂粉末或油浆沉积严重造成反应器压差过高时,可将其切出反应流程,进行处理。该组合工艺的多样性,可提高生产灵活性。
22.本发明所述的加氢制备船用燃料油的方法,其中优选的是,所述r1、r2内装填非负载催化剂,所述非负载催化剂为水溶性或油溶性mo和/或ni和/或co的盐。
23.本发明所述的加氢制备船用燃料油的方法,其中优选的是,所述r3、r4内装填加氢脱金属催化剂。
24.本发明所述的加氢制备船用燃料油的方法,其中优选的是,所述r3、r4内还装填有加氢保护剂。
25.本发明所述的加氢制备船用燃料油的方法,其中优选的是,所述r5内装填加氢脱硫、加氢脱氮催化剂。
26.本发明所述的加氢制备船用燃料油的方法,其中优选的是,为了提高杂质、粉尘和颗粒的捕捉能力,所述加氢脱金属催化剂采用级配方式,中下部为大粒度、高孔隙率的蜂窝形、球形催化剂。
27.本发明所述的加氢制备船用燃料油的方法,其中优选的是,所述加氢脱金属催化剂以多孔无机氧化物氧化铝为载体,第vi b族和/或viii族金属为活性组分。
28.本发明所述的加氢制备船用燃料油的方法,其中优选的是,所述加氢脱金属催化剂组成为:以al2o3或含有k2o、mgo、sio2、tio2、zro2、p2o5的al2o3作为载体;
29.所述加氢脱金属催化剂孔容为0.3~1.3ml/g,比表面为80~150m2/g,孔隙率为50-65%;
30.催化剂以对应金属氧化物质量计为5.0~20.0%的第vi b族金属,和/或1.0~2.0%的vⅲ族金属。
31.本发明所述的加氢制备船用燃料油的方法,其中优选的是,所述第vi b族金属为w或/和mo,所述viii族金属为co或/和ni。
32.本发明所述的加氢制备船用燃料油的方法,其中优选的是,所述非负载催化剂、加氢脱金属催化剂、加氢脱硫以及加氢脱氮催化剂中催化剂使用的载体为滴球成型、滚球造粒、挤压成型或压片成型;
33.所述非负载催化剂、加氢脱金属催化剂、加氢脱硫以及加氢脱氮催化剂形状为蜂窝形、球形、条形(包括圆柱形、三叶草形、四叶草形)、片形。进一步优选蜂窝形、球形和四叶草条形。
34.本发明所述的加氢制备船用燃料油的方法,其中优选的是,所述r1、r2的反应条件为:氢压8.0mpa~18.0mpa,温度400℃~440℃,液时体积空速0.3h-1
~2h-1
,氢油体积比500~1000,在原料油中浆态床加氢催化剂加入量为100~3000μg/g。
35.本发明所述的加氢制备船用燃料油的方法,其中优选的是,所述r3、r4、r5的反应
条件为:氢压10.0mpa~16.0mpa,温度360℃~430℃,液时体积空速0.2h-1
~lh-1
,氢油体积比500~1000。
36.本发明所述的加氢制备船用燃料油的方法,重油和/或渣油等原料油与加氢裂化催化剂混合后与氢气先经过浆态床进行加氢裂化,进行深度转化。之后裂化后产品经气液分离,液相产品进入滴流固定床加氢前处理反应器,反应器内装填加氢保护剂以及脱金属催化剂,主要脱除原料中的ni、v等金属,并除去油浆中的浆态床加氢催化剂粉末。其反应生成物不经分离直接进入加氢处理反应器进行深度地加氢精制,进一步脱除硫氮,最后反应生成物经分馏塔分馏得到气体、石脑油、柴油、船用燃料油。
37.本发明所述的加氢制备船用燃料油的方法,尤其适用于高金属(ni v≥150μg.g-1
)、高残炭(ccr≥16wt%)的重质馏分油、渣油和油砂沥青的加氢裂化和加氢处理。本发明通过浆态床加氢裂化和液相加氢处理的组合工艺,实现渣油的深度转化,转化率在30%~95%,并能够进一步加氢脱硫、脱氮,来生产硫含量不大于0.1%的船用燃料油,同时兼产石脑油、柴油。
38.具体地,为了提高杂质、粉尘和颗粒的捕捉能力,本发明中使用的加氢脱金属催化剂优选采用级配方式,中下部为大粒度、高孔隙率的蜂窝形、球形催化剂,最好以多孔无机氧化物如氧化铝为载体,第vi b族金属(如w或/和mo)和/或viii族金属(如co或/和ni)氧化物为活性组分,催化剂的组成优选为:
39.1)以al2o3或含有k2o、mgo、sio2、tio2、zro2、p2o5的al2o3作为载体;
40.2)孔容为0.1~3.0ml/g,最好为0.3~1.3ml/g;
41.3)比表面为50~200m2/g,最好为80~150m2/g;
42.4)孔隙率为40%~75%,最好为50-65%;
43.5)催化剂以对应金属氧化物质量计(以下同),含有1.0~10.0%,最好为5.0~20.0%的第vi b族金属(如moo和/或wo3),和/或0.5~3.0%,最好为1.0~2.0%的vⅲ族金属(如coo和/或nio)。
44.具体地,本发明的方法,各反应器可以采用任何适合本领域的加氢处理工艺条件,一般的工艺条件如下:浆态床预处理反应器反应条件为:氢压2.0mpa~20.0mpa,较好的是8.0mpa~18.0mpa;温度300℃~500℃,较好的是400℃~440℃;液时体积空速0.2-1
~3h-1
,较好的是0.3h-1
~2h-1
,氢油体积比100~3000,较好的是500~1000。在原料油中浆态床加氢催化剂加入量一般为10~10000μg/g(以金属计),优选为100~3000μg/g。除此之外,所有上流式反应器和其它固定床反应器的反应条件为:氢压5.0mpa~20.0mpa,较好的是8.0mpa~18.0mpa,最好的是10.0mpa~16.0mpa;温度300℃~450℃,较好的是360℃~440℃,最好的是360℃~430℃;液时体积空速0.2h-1
~3h-1
,较好的是0.2h-1
~2h-1
,最好的是0.2h-1
~lh-1
,氢油体积比300~2000,较好的是400~1500,最好的是500~1000。
45.具体地,本发明中的加氢处理催化剂(即加氢脱金属催化剂、加氢脱硫催化剂、加氢脱氮催化剂),都是本领域专业人员熟知的常规催化剂,一般以多孔无机氧化物如氧化铝为载体,第vib族金属(如w或/和mo)和/或vⅲ族金属(如co或/和ni)氧化物为活性组分,催化剂的物性、组成最好是:
46.1)以al2o3或含有k2o、mgo、sio2、tio2、zro2、p2o5的al2o3作为载体;
47.2)孔容为0.1~3.0ml/g,最好为0.3~1.3ml/g;
48.3)比表面为20~400m2/g,最好为100~240m2/g;
49.4)催化剂以对应金属氧化物质量计(以下同),含有1.0~20.0%,最好为3.0~12%的第vi b族金属(如moo或wo3),和/或0.5~8.0%,最好为1.0~5.5%的vⅲ族金属(如coo和/或nio)。
50.本发明中涉及到的催化剂可采用现有技术中的常规方法来制备。
51.本发明所提供的方法可以处理高硫、高金属含量、高沥青质的劣质重油、渣油,转化率在60%~95%,能够对渣油深度转化。
52.综上所述,本发明可以充分结合浆态床加氢裂化反应器、滴流固定床、上流式液相加氢固定床反应器的优势,浆态床加氢裂化原料适应性好,同时具有高转化率,可以减少未转化油。液相加氢具有能耗低,操作成本低的优点。将它们结合起来,为生产满足要求的船用燃料油提供了一种新方法。
附图说明
53.图1为本发明的加氢制备船用燃料油的方法的流程示意图。
54.其中:
55.1、桨态床加氢裂化反应器r1,2、桨态床加氢裂化反应器r2,3、气液分离器s1,4、滴流固定床加氢前处理反应器r3,5、滴流固定床加氢前处理反应器r4,6、上流式液相加氢处理反应器r5,7、高分装置,8、气体净化器,9、分馏塔,10、搅拌装置,13、循环氢压缩机,14、加热器,15、新氢压缩机。
具体实施方式
56.以下对本发明的实施例作详细说明:本实施例在以本发明技术方案为前提下进行实施,给出了详细的实施方式和过程,但本发明的保护范围不限于下述的实施例,下列实施例中未注明具体条件的实验方法,通常按照常规条件。
57.实施例1和实施例2均使用图1所示的工艺流程。参见图1所示,原料油如减压渣油的一部分与加氢裂化催化剂通过搅拌装置10混合后,与油减压渣油的剩余部分,以及由新氢压缩机15输送而来的氢气经由加热器14预热后一起依次进入桨态床加氢裂化反应器r1 1、桨态床加氢裂化反应器r22进行加氢裂化,加氢裂化产物进入气液分离器s1 3进行气液分离,其中,所得气体经由循环氢压缩机13与新氢混合再次进入桨态床加氢裂化反应器r1 1、桨态床加氢裂化反应器r2 2;所得液体产物一部分作为循环油与新鲜原料混合后再进入桨态床加氢裂化反应器r1 1、桨态床加氢裂化反应器r2 2,另一部分进入滴流固定床加氢前处理反应器r3 4和/或滴流固定床加氢前处理反应器r4 5,在加氢保护剂和加氢脱金属催化剂的作用下进行脱金属处理以及脱除油浆中的催化剂粉末,前处理产物进入上流式液相加氢处理反应器r5 6,在加氢精制催化剂的作用下进一步进行加氢精制包括脱硫脱氮等,随后所得加氢精制产物进入高分装置7进行气液分离,所得气体产物经过气体净化器8一部分作为循环氢循环回系统,一部分排出系统;所得液体产物进入分馏塔9进行分馏得到气体、石脑油、柴油、船用燃料油。
58.实施例1
59.本实施例中所用原料油为原料油a,原料油a的主要性质列于表1。试验过程中的浆
态床加氢裂化催化剂为油溶性钼催化剂,催化剂加入量为400μg/g。液相加氢前处理反应器中脱金属催化剂采用cn101928593a中实施例1中方法制得;液相加氢处理反应器中的加氢精制催化剂(包括加氢脱金属剂、加氢脱硫剂、加氢脱氮剂,三者在液相加氢处理反应器中随物流方向依次按照1:1:1的质量比装填),催化剂性质见表2。各部分反应条件和产品结果见表3、4。
60.结合图1所示,本实施例中原料油a的一半与加氢裂化催化剂通过搅拌装置10混合后,与原料油a的剩余部分,以及由新氢压缩机15输送而来的氢气经由加热器14预热后一起依次进入桨态床加氢裂化反应器r1 1、桨态床加氢裂化反应器r2 2进行加氢裂化,加氢裂化产物进入气液分离器s1 3进行气液分离,其中,所得气体经由循环氢压缩机13与新氢混合再次进入桨态床加氢裂化反应器r1 1、桨态床加氢裂化反应器r2 2;所得液体产物一半作为循环油与新鲜原料混合后再进入桨态床加氢裂化反应器r1 1、桨态床加氢裂化反应器r2 2,另一半均分后分别进入上流式液相加氢前处理反应器r3 4和上流式液相加氢前处理反应器r4 5,在加氢保护剂和加氢脱金属催化剂的作用下进行脱金属处理以及脱除油浆中的催化剂粉末,前处理产物进入上流式液相加氢处理反应器r5 6,在加氢精制催化剂的作用下进一步进行加氢精制包括脱硫脱氮等,随后所得加氢精制产物进入高分装置7进行气液分离,所得气体产物经过气体净化器8一半作为循环氢循环回系统,一半排出系统;所得液体产物进入分馏塔9进行分馏得到气体、石脑油、柴油、船用燃料油。
61.实施例2
62.本实施例与实施例1不同之处在于,将原料油a替换为原料油b,原料油b的主要性质列于表1,浆态床加氢裂化催化剂加入量为600μg/g,具体工艺过程与实施例1相同,其中改变条件如表3和表4所示。
63.实施例3
64.本实施例操作流程与实施例1不同之处为:原料油a的一半与加氢裂化催化剂通过搅拌装置10混合后,与原料油a的剩余部分,以及由新氢压缩机15输送而来的氢气经由加热器14预热后一起依次进入桨态床加氢裂化反应器r1 1进行加氢裂化,加氢裂化产物进入气液分离器s1 3进行气液分离,其中,所得气体经由循环氢压缩机13与新氢混合再次进入桨态床加氢裂化反应器r1 1;所得液体产物一半作为循环油与新鲜原料混合后再进入桨态床加氢裂化反应器r1 1,另一半进入上流式液相加氢前处理反应器r3 4,在加氢保护剂和加氢脱金属催化剂的作用下进行脱金属处理以及脱除油浆中的催化剂粉末,前处理产物进入上流式液相加氢处理反应器r5 6,在加氢精制催化剂的作用下进一步进行加氢精制包括脱硫脱氮等,随后所得加氢精制产物进入高分装置7进行气液分离,所得气体产物经过气体净化器8一半作为循环氢循环回系统,一半排出系统;所得液体产物进入分馏塔9进行分馏得到气体、石脑油、柴油、船用燃料油。
65.对比例1
66.本对比例为本发明的一个对比实施方案,其工艺过程与实施例1基本相同,不同之处在于没有浆态床加氢裂化反应器r1、r2,原料油a直接进入液相加氢前处理反应器r3,产物进入上流式液相加氢处理反应器r5,进行进一步的脱硫脱氮,产物进入分馏塔进行分馏。试验过程使用的下流式反应器催化剂、加氢脱硫催化剂和加氢脱氮催化剂均与实施例1相同,具体工艺条件和试验结果见表4。
67.对比例2
68.本对比例为本发明的一个对比实施方案,其工艺过程与实施例1不同之处在于只设置了一个浆态床加氢裂化反应器r1,由r1出来后进入下流式加氢前处理反应器r3、r4,产物进入上流式液相加氢处理反应器r5,进行进一步的脱硫脱氮,产物进入分馏塔进行分馏。试验过程使用的下流式反应器催化剂、加氢脱硫催化剂和加氢脱氮催化剂均与实施例1相同,具体工艺条件和试验结果见表4。
69.对比例3
70.本对比例其工艺过程与实施例1不同之处在于物料只通过了浆态床加氢裂化反应器r1、r2,没有进入后续加氢反应器r3、r4、r5,由r2出来后直接进入分馏,具体工艺条件和试验结果见表4。
71.对比例4
72.本对比例其工艺过程与实施例1不同之处在于物料通过浆态床加氢裂化反应器r1、r2后,没有进入后续加氢处理反应器r3、r4,由r2出来后直接进入r5,具体工艺条件和试验结果见表4。
73.对比例5
74.本对比例其工艺过程与实施例1不同之处在于物料通过浆态床加氢裂化反应器r1、r2后,进入下流式加氢处理反应器r3、r4,由r4出来后没有进入r5,直接进入分馏,具体工艺条件和试验结果见表4。
75.表1试验原料油主要性质
76.原料名称ab密度(20℃),kg/m31.00640.9664(ni v),μg/g120.6230硫,%0.452.54氮,%0.860.43残炭,%16.3212沥青质,%4.195.77粘度(100℃),mm2/s1443.692.4
77.表2催化剂性质
[0078][0079]
表3浆态床加氢工艺条件
[0080][0081][0082]
表4固定床加氢工艺条件和产品性质
[0083]
[0084]
由表4的试验结果可以看出,采用本发明的工艺过程可对劣质重油原料高效加氢处理,同时,增加了装置稳定性,提高了脱杂质活性。
[0085]
当然,本发明还可有其它多种实施例,在不背离本发明精神及其实质的情况下,熟悉本领域的技术人员可根据本发明作出各种相应的改变和变形,但这些相应的改变和变形都应属于本发明的保护范围。
再多了解一些
本文用于企业家、创业者技术爱好者查询,结果仅供参考。