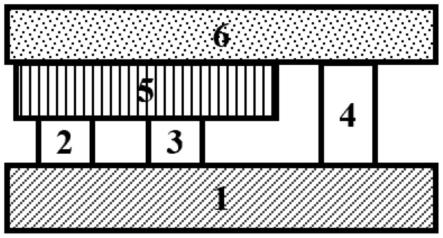
1.本发明涉及柔性有机电化学晶体管或突触电子学领域,具体涉及一种全固态有机电化学晶体管及其制备方法。
背景技术:
2.在过去的几十年里,由于计算机的计算能力的大幅提高,人工智能,大数据以及物联网不断发展与更新。但是,基于冯
·
诺依曼架构的现代互补金属氧化物半导体(cmos)硬件受到物理分离的逻辑和存储单元(冯
·
诺依曼效率瓶颈)的阻碍,严重影响了计算机的能耗、访问速度、带宽和响应时间。
3.突触神经元连接形成控制人类所有先天和学习行为的神经网络。作为大脑中最小的计算单元,它们能够大规模并行信息处理和分布式计算,以响应各种各样的刺激,且能耗仅为20w左右。受此启发,通过模仿生物突触行为进行神经形态计算的电子突触器件,包括传统的硅基cmos模拟电路和具有非线性传输和低离子运动的可调谐模拟器件逐渐成为人们关注的焦点。自推出以来,基于cmos的模拟电路因难大规模集成和低效率而处于不利地位。双端可调谐忆阻器已被证明可以适用于模拟突触可塑性行为的非易失性存储器,例如突触的短期可塑性(stp)和长期可塑性(ltp)。然而,由于噪声过大而导致器件操作不稳定,并且在集成时需要额外的电路元件会阻碍它们在人工突触领域的发展前景。。
4.三端神经形态晶体管使我们能够通过同时传输信息和自我学习来更有效地应对上述的挑战。三端有机电化学晶体管的工作机制取决于有机薄膜中的电解质离子对电化学晶体管沟道进行掺杂或去掺杂的电化学反应(离子-电子耦合),其中“写入”和“读取”操作分别由栅电压和源-漏电压严格控制。因此,三端电化学晶体管是一种具有非易失性记忆性能的人工突触器件,其中信息传输和自学习过程可以在同一人工突触中同时实现。事实上,我们可以把离子通过沟道时的动态跨导的更新比作生物突触中突触权重(w)的调整。像水溶液电解质这样的液态电解质可能具有生物相容性,但是,当涉及到可扩展性,集成性,小型化和长期操作时,固体电解质是一种更好的选择。目前,使用固态聚合物电解质,凝胶聚合物电解质和复合聚合物电解质等固体电解质已经成为一种常见的策略。聚合物自组装离子凝胶电解质材料是一类有前途的固态电解质,由离子液体(ils)或其他功能组分组成,通过使用化学或物理(优先光化学)方法交联聚合物组分来实现溶胀聚合物网络,这不仅保持了聚合物的机械柔韧性和离子液体的大比电容,也允许通过光图案化来制造复杂和高密度的器件。然而,有研究证实很难兼顾活性层中电子传输和离子渗透/传输。有人提出用极性基团功能化半导体聚合物主链以促进水合电解质离子的渗透和流动。也有研究表明通过简单呼吸图制备多孔半导体聚合物薄膜的电化学晶体管器件可实现快速离子掺杂、高跨导。
技术实现要素:
5.本发明的目的在于:如何提供一种基于多层多孔半导体层的全固态有机可拉伸电化学晶体管及其制备方法,旨在解决电化学晶体管中由于液态电解质导致的器件不便大规
模集成、长期应用和便携的缺点,同时利用固体电解质渗入多层多孔有机半导体层来平衡半导体层中电子传输和离子渗透/传输,提高器件的总体性能。
6.本发明采用的技术方案如下:
7.一种全固态有机电化学晶体管,从下到上依次包括柔性衬底层,电极层和离子凝胶电解质层;所述电极包括源电极、漏电极和栅电极;所述源电极、漏电极的上方设置多层多孔半导体层,栅电极上方为离子凝胶电解质层;
8.所述多层多孔半导体层由半导体材料与sebs按比例溶解于混合的有机溶剂氯仿与甲醇中,且经过旋涂和水转印后形成可拉伸的多层多孔固体半导体的薄膜。
9.作为一种优选的技术方案,所述柔性衬底层的材料为sebs、pdms或pu的一种或多种。
10.作为一种优选的技术方案,所述电极层的材料为碳浆,具有延展性,薄膜厚度范围为80~150nm。
11.作为一种优选的技术方案,所述多层多孔半导体层的材料为p3ht或dpp-dtt中的一种与sebs的混合配制而成,薄膜厚度范围为200~300nm。
12.作为一种优选的技术方案,所述离子凝胶电解质层的材料为由聚合物与离子液体混合配制而成离子凝胶,所述聚合物为ps-pmma-ps、ps-peo-ps、p(vdf-trfe)、p(vdf-hfp)或p(vdf-trfe-ctfe)中的一种,所述离子液体为[emim][tfsi]、[emim][fsi]、[emim][dca]、[bmim][pf6]或[emim][bf4]中的一种或多种。
[0013]
一种全固态有机电化学晶体管的制备方法,制备过程包括以下步骤:
[0014]
步骤1:对透明玻璃基板进行清洗,清洗后用氮气吹干或经恒温箱热烘干6h以上;
[0015]
步骤2:将sebs、pdms或pu倾倒于涂有洗洁精的玻璃基板上,待溶液铺平后,置于真空干燥箱中烘干,烘干后用刀片将柔性基板从玻璃基板上剥离;
[0016]
步骤3:将碳浆的电极(80~150nm)喷涂在pu基板上;
[0017]
步骤4:对显微镜载玻片进行清洗,清洗后用氮气吹干或经恒温箱热烘干6h以上;
[0018]
步骤5:将配制好的pva溶液旋涂至显微镜载玻片上,并将旋涂后的基片进行烘干处理,得到pva牺牲层;
[0019]
步骤6:在湿度为88%rh条件下,将配制好的p3ht混合溶液或dpp-dtt混合溶液旋涂至pva牺牲层上;
[0020]
步骤7:将基片置于装有60℃去离子水的培养皿中,使pva牺牲层溶解于去离子水中,得到单层多孔半导体层,将第一层多孔半导体层转印至柔性基板pu上,并用氮气吹干,重复将第二层多孔半导体层转印至第一层多孔半导体层上,并用氮气吹干,重复将第三层多孔半导体层转印至第二层多孔半导体层上,并用氮气吹干;
[0021]
步骤8:在半导体沟道上滴覆离子凝胶电解质。
[0022]
作为一种优选的技术方案,所述步骤2中,所述烘干的温度在30℃,时间范围为12h。
[0023]
作为一种优选的技术方案,所述步骤5中,所述烘干的温度在110℃,时间范围为2min。
[0024]
作为一种优选的技术方案,所述烘干方式采用恒温热台加热、烘箱加热、远红外加热、热风加热的一种或多种。
[0025]
本发明的有益效果如下:
[0026]
1、通过使用简单的呼吸图方法,制备多孔半导体层,有效地增大半导体层与电解质层的接触面积,更有利于电解质离子注入到沟道中,增强沟道中离子-电子电容耦合,实现低电压工作,减小器件功耗损失。
[0027]
2、通过简单叠加多层多孔半导体薄膜,能够有效增多半导体中的电化学掺杂的反应位点,加强电解质离子与半导体层的电化学掺杂,提高器件输出漏电流,增强输入栅电压对输出的调控。
[0028]
3、通过将离子凝胶电解质滴覆在具有可拉伸性半导体沟道上,能够避免液体电解质具有的不便于大规模集成与长期应用的弊端,同时,离子凝胶电解质不仅保持了离子液体的大部分电学性能,具有聚合物的机械强度,而且在物理、化学和电化学上是稳定的,与不同的半导体材料相兼容,适用于大规模集成,用于突触电子学,为后摩尔时代的到来提供一个思路。
[0029]
4、通过在多层多孔半导体薄上滴覆由聚合物和离子液体按比例混合的离子凝胶电解质层,能够在保证半导体活性层与离子凝胶电解质层具有较大的接触面积的同时,增加电解质离子的注入率,优化器件的跨导。这种全固态的有机电化学晶体管避免了液态电解质带来的不便储存与应用,且适合于柔性电子的大规模集成,可适用于模拟生物突触的突触行为。
附图说明
[0030]
为了更清楚地说明本发明实施例的技术方案,下面将对实施例中所需要使用的附图作简单地介绍,应当理解,本说明书附图中的各个部件的比例关系不代表实际选材设计时的比例关系,其仅仅为结构或者位置的示意图,其中:
[0031]
图1是本发明的结构示意图;
[0032]
图2是本发明的使用旋涂工艺制备的多层多孔半导体层示意图;
[0033]
附图中标号说明:
[0034]
1-柔性衬底层,2-源电极,3-漏电极,4-栅电极,5-多层多孔半导体层,6-离子凝胶电解质层,11-多孔半导体薄膜、22-致密半导体薄膜。
具体实施方式
[0035]
为了使本发明的目的、技术方案及优点更加清楚明白,以下结合附图及实施例,对本发明进行进一步详细说明。应当理解,此处所描述的具体实施例仅用以解释本发明,并不用于限定本发明,即所描述的实施例仅仅是本发明一部分实施例,而不是全部的实施例。
[0036]
下面结合图1至图2,对本发明作详细说明。
[0037]
实施例1(对照组):
[0038]
1.对表面粗糙度小于1nm的透明玻璃基板进行清洗,清洗后经恒温箱热烘干6h以上;
[0039]
2.在玻璃基板上涂一层洗洁精,将pu倾倒于涂有洗洁精的玻璃基板上,微微振动,将溶液铺平,铺平后置于真空干燥箱中烘干(30℃,12h),烘干后用刀片将柔性基板小心从玻璃基板上剥离;
[0040]
3.将碳浆的电极(80~150nm)喷涂在pu基板上;
[0041]
4.对表面粗糙度小于1nm的显微镜载玻片进行清洗,清洗后经恒温箱热烘干6h以上;
[0042]
5.将配制好的pva溶液旋涂至显微镜载玻片上(3000rpm,60s),并将旋涂后的载玻片进行烘干处理(110℃,2min),得到pva牺牲层;
[0043]
6.在湿度为10%rh条件下,将配制好的p3ht混合溶液(p3ht:sebs=2:1)旋涂至pva牺牲层(5000rpm,10s);
[0044]
7.在显微镜下观察p3ht薄膜,观察得p3ht薄膜表面平整致密,得到图2所示的致密半导体膜22;
[0045]
8.将旋涂后的载玻片置于装有去离子水的培养皿中,培养皿置于热台上(60℃),使pva牺牲层溶解于去离子水中,得到半导体活性层,将一层半导体活性层转印至柔性基板上,并用氮气吹干;
[0046]
9.测试条件下:漏电压(vd)=-0.5v,栅电压(vg)扫描区间为1~-1.5v,在半导体沟道上方滴覆[emim][tfsi]离子液体,测得开关比(ion/ioff)
[0047]
=5.6
×
103,跨导(gm)=0.38ms,若不经封装器件不易长期存储且直接拉伸会损坏器件。
[0048]
实施例2:
[0049]
1.对表面粗糙度小于1nm的透明玻璃基板进行清洗,清洗后经恒温箱热烘干6h以上;
[0050]
2.在玻璃基板上涂一层洗洁精,将pu倾倒于涂有洗洁精的玻璃基板上,微微振动,将溶液铺平,铺平后置于真空干燥箱中烘干(30℃,12h),烘干后用刀片将柔性基板小心从玻璃基板上剥离;
[0051]
3.将碳浆的电极(80~150nm)喷涂在pu基板上;
[0052]
4.对表面粗糙度小于1nm的显微镜载玻片进行清洗,清洗后经恒温箱热烘干6h以上;
[0053]
5.将配制好的pva溶液旋涂至显微镜载玻片上(3000rpm,60s),并将旋涂后的载玻片进行烘干处理(110℃,2min),得到pva牺牲层;
[0054]
6.在湿度为88%rh条件下,将配制好的p3ht混合溶液(p3ht:sebs=2:1)旋涂至pva牺牲层(5000rpm,10s);
[0055]
7.在显微镜下观察p3ht薄膜,观察得p3ht薄膜表面有分布均匀的多孔,得到图2所示的多孔半导体膜11;
[0056]
8.将旋涂后的载玻片置于装有去离子水的培养皿中,培养皿置于热台上(60℃),使pva牺牲层溶解于去离子水中,得到半导体活性层,将一层半导体活性层转印至柔性基板上,并用氮气吹干;
[0057]
9.测试条件下:漏电压(vd)=-0.5v,栅电压(vg)扫描区间为1~-1.5v,在半导体沟道上方滴覆[emim][tfsi]离子液体,测得开关比(ion/ioff)
[0058]
=4.4
×
103,薄膜厚度归一化跨导(gm)=0.54ms,若不经封装器件不易长期存储且直接拉伸会损坏器件。
[0059]
实施例3:
[0060]
1.对表面粗糙度小于1nm的透明玻璃基板进行清洗,清洗后经恒温箱热烘干6h以上;
[0061]
2.在玻璃基板上涂一层洗洁精,将pu倾倒于涂有洗洁精的玻璃基板上,微微振动,将溶液铺平,铺平后置于真空干燥箱中烘干(30℃,12h),烘干后用刀片将柔性基板小心从玻璃基板上剥离;
[0062]
3.将碳浆的电极(80~150nm)喷涂在pu基板上;
[0063]
4.对表面粗糙度小于1nm的显微镜载玻片进行清洗,清洗后经恒温箱热烘干6h以上;
[0064]
5.将配制好的pva溶液旋涂至显微镜载玻片上(3000rpm,60s),并将旋涂后的载玻片进行烘干处理(110℃,2min),得到pva牺牲层;
[0065]
6.在湿度为10%rh条件下,将配制好的p3ht混合溶液(p3ht:sebs=2:1)旋涂至pva牺牲层(5000rpm,10s);
[0066]
7.在显微镜下观察p3ht薄膜,观察得p3ht薄膜表面平整致密,得到图2所示的致密半导体膜22;
[0067]
8.将旋涂后的载玻片置于装有去离子水的培养皿中,培养皿置于热台上(60℃),使pva牺牲层溶解于去离子水中,得到半导体活性层,将一层半导体活性层转印至柔性基板上,并用氮气吹干;
[0068]
9.在半导体沟道上方滴覆ps-peo-ps:[emim][tfsi]离子凝胶,滴覆后置于40℃真空干燥箱烘干;
[0069]
10.测试条件下:漏电压(vd)=-0.5v,栅电压(vg)扫描区间为1~-1.5v,测得开关比(ion/ioff)=3.7
×
103,跨导(gm)=0.29ms;
[0070]
11.在将器件拉伸至120%300次后测得器件跨导(gm)=0.23ms,保留79.3%的跨导。
[0071]
实施例4:
[0072]
1.对表面粗糙度小于1nm的透明玻璃基板进行清洗,清洗后经恒温箱热烘干6h以上;
[0073]
2.在玻璃基板上涂一层洗洁精,将pu倾倒于涂有洗洁精的玻璃基板上,微微振动,将溶液铺平,铺平后置于真空干燥箱中烘干(30℃,12h),烘干后用刀片将柔性基板小心从玻璃基板上剥离;
[0074]
3.将碳浆的电极(80~150nm)喷涂在pu基板上;
[0075]
4.对表面粗糙度小于1nm的显微镜载玻片进行清洗,清洗后经恒温箱热烘干6h以上;
[0076]
5.将配制好的pva溶液旋涂至显微镜载玻片上(3000rpm,60s),并将旋涂后的载玻片进行烘干处理(110℃,2min),得到pva牺牲层;
[0077]
6.在湿度为88%rh条件下,将配制好的p3ht混合溶液(p3ht:sebs=2:1)旋涂至pva牺牲层(5000rpm,10s);
[0078]
7.在显微镜下观察p3ht薄膜,观察得p3ht薄膜表面有分布均匀的多孔,得到图2所示的多孔半导体膜11;
[0079]
8.将旋涂后的载玻片置于装有去离子水的培养皿中,培养皿置于热台上(60℃),
使pva牺牲层溶解于去离子水中,得到半导体活性层,将一层半导体活性层转印至柔性基板上,并用氮气吹干;
[0080]
9.在半导体沟道上方滴覆ps-peo-ps:[emim][tfsi]离子凝胶,滴覆后置于40℃真空干燥箱烘干;
[0081]
10.测试条件下:漏电压(vd)=-0.5v,栅电压(vg)扫描区间为1~-1.5v,测得开关比(ion/ioff)=4.1
×
103,薄膜厚度归一化跨导(gm)=0.61ms;
[0082]
11.在将器件拉伸至120%300次后测得器件薄膜厚度归一化跨导(gm)
[0083]
=0.54ms,保留88.52%的跨导。
[0084]
实施例5:
[0085]
1.对表面粗糙度小于1nm的透明玻璃基板进行清洗,清洗后经恒温箱热烘干6h以上;
[0086]
2.在玻璃基板上涂一层洗洁精,将pu倾倒于涂有洗洁精的玻璃基板上,微微振动,将溶液铺平,铺平后置于真空干燥箱中烘干(30℃,12h),烘干后用刀片将柔性基板小心从玻璃基板上剥离;
[0087]
3.将碳浆的电极(80~150nm)喷涂在pu基板上;
[0088]
4.对表面粗糙度小于1nm的显微镜载玻片进行清洗,清洗后经恒温箱热烘干6h以上;
[0089]
5.将配制好的pva溶液旋涂至显微镜载玻片上(3000rpm,60s),并将旋涂后的载玻片进行烘干处理(110℃,2min),得到pva牺牲层;
[0090]
6.在湿度为88%rh条件下,将配制好的p3ht混合溶液(p3ht:sebs=2:1)旋涂至pva牺牲层(5000rpm,10s);
[0091]
7.在显微镜下观察p3ht薄膜,观察得p3ht薄膜表面有分布均匀的多孔,得到图2所示的多孔半导体膜11;
[0092]
8.将旋涂后的载玻片置于装有去离子水的培养皿中,培养皿置于热台上(60℃),使pva牺牲层溶解于去离子水中,得到半导体活性层,依次将两层半导体活性层转印至柔性基板上,并用氮气吹干;
[0093]
9.在半导体沟道上方滴覆ps-peo-ps:[emim][tfsi]离子凝胶,滴覆后置于40℃真空干燥箱烘干;
[0094]
10.测试条件下:漏电压(vd)=-0.5v,栅电压(vg)扫描区间为1~-1.5v,测得开关比(ion/ioff)=4.5
×
103,薄膜厚度归一化跨导(gm)=1.02ms;
[0095]
11.在将器件拉伸至120%300次后测得器件薄膜厚度归一化跨导(gm)
[0096]
=0.89ms,保留87.25%的跨导。
[0097]
实施例6:
[0098]
1.对表面粗糙度小于1nm的透明玻璃基板进行清洗,清洗后经恒温箱热烘干6h以上;
[0099]
2.在玻璃基板上涂一层洗洁精,将pu倾倒于涂有洗洁精的玻璃基板上,微微振动,将溶液铺平,铺平后置于真空干燥箱中烘干(30℃,12h),烘干后用刀片将柔性基板小心从玻璃基板上剥离;
[0100]
3.将碳浆的电极(80~150nm)喷涂在pu基板上;
[0101]
4.对表面粗糙度小于1nm的显微镜载玻片进行清洗,清洗后经恒温箱热烘干6h以上;
[0102]
5.将配制好的pva溶液旋涂至显微镜载玻片上(3000rpm,60s),并将旋涂后的载玻片进行烘干处理(110℃,2min),得到pva牺牲层;
[0103]
6.在湿度为88%rh条件下,将配制好的p3ht混合溶液(p3ht:sebs=2:1)旋涂至pva牺牲层(5000rpm,10s);
[0104]
7.在显微镜下观察p3ht薄膜,观察得p3ht薄膜表面有分布均匀的多孔,得到图2所示的多孔半导体膜11;
[0105]
8.将旋涂后的载玻片置于装有去离子水的培养皿中,培养皿置于热台上(60℃),使pva牺牲层溶解于去离子水中,得到半导体活性层,依次将三层半导体活性层转印至柔性基板上,并用氮气吹干;
[0106]
9.在半导体沟道上方滴覆ps-peo-ps:[emim][tfsi]离子凝胶,滴覆后置于40℃真空干燥箱烘干;
[0107]
10.测试条件下:漏电压(vd)=-0.5v,栅电压(vg)扫描区间为1~-1.5v,测得开关比(ion/ioff)=3.7
×
103,薄膜厚度归一化跨导(gm)=1.49ms;
[0108]
11.在将器件拉伸至120%300次后测得器件薄膜厚度归一化跨导(gm)
[0109]
=1.26ms,保留84.56%的跨导。
[0110]
通过实施例1-6可以看出可以看出:按照一种全固态有机电化学晶体管,从下到上依次包括柔性衬底层1,电极层和离子凝胶电解质层6;所述电极包括源电极2、漏电极3和栅电极4;所述源电极2、漏电极3的上方设置多层多孔半导体层5,栅电极4上方为离子凝胶电解质层6;所述多层多孔半导体层5由半导体材料与sebs按比例溶解于混合的有机溶剂氯仿与甲醇中,且经过旋涂和水转印后形成可拉伸的多层多孔固体半导体的薄膜。
[0111]
通过引入多层多孔半导体活性层的全固态有机可拉伸电化学晶体管的制备方法制备的有机电化学晶体管(即实例2~6制备而成的有机电化学晶体管),相比于未经处理制备的电化学晶体管(即实例1制备而成的有机电化学晶体管),其薄膜厚度均一化跨导gm提高,整体器件的机械柔性及长期稳定性增强。这是由于滴覆在p3ht多孔膜上的离子凝胶电解质渗入进如图2左图所示的多孔半导体薄膜11中,该多孔半导体层有利于增大电解质与半导体的接触面积,在栅压调制下,电解质离子有效地注入半导体层,调控漏电流,同时,离子凝胶固体电解质与多层多孔半导体层界面兼容,解决了液体电解质不能大规模扩展、整合和小型化的弊端。该全固态可拉伸电化学晶体管不仅具有一定的机械强度,而且在物理、化学和电化学上是稳定的,可用于突触电子学,为后摩尔时代的到来提供一个思路。
[0112]
以上所述仅为本发明的较佳实施例而已,并不用以限制本发明,凡在本发明的精神和原则之内所作的任何修改、等同替换和改进等,均应包含在本发明的保护范围之内。
再多了解一些
本文用于企业家、创业者技术爱好者查询,结果仅供参考。