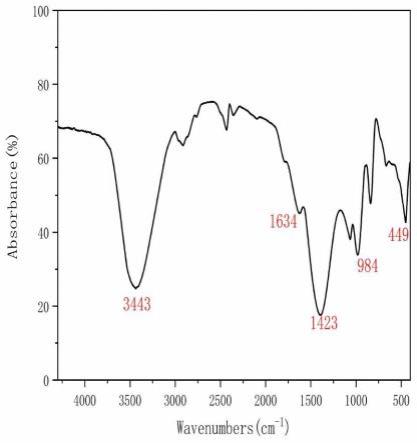
1.本发明涉及混凝土外加剂技术领域,具体而言,涉及一种水化硅酸钙晶核早强剂及其制备方法。
背景技术:
2.随着我国在工程建设方面的高速发展,混凝土在低温下的早期强度问题一直备受关注。通常当温度降低至5-8℃时,水泥的水化速率仅为20℃时的1/5-1/4。因此在冬季为了提高混凝土构件的早期强度,通常需要采用蒸汽养护,需要消耗大量的化石燃料。
3.研究表明,水化硅酸钙(c-s-h)早强剂能够有效促进混凝土在低温下的强度发展。c-s-h晶种的制备方法,目前主要有水热法和溶液合成。水热法需要使用氢氧化钙和二氧化硅在高温和高压下进行反应,其产品纯度高,基本无三废产生,但是存在工艺复杂、成本高的缺点。而单纯的溶液法又存在合成周期长,不利于量产的缺点。因此研究一种工艺简单且能够显著提升混凝土制品早期抗压强度的水化硅酸钙晶核早强剂具有非常重要的意义。
技术实现要素:
4.本发明的目的在于提供一种水化硅酸钙晶核早强剂的制备方法,该制备方法工艺流程简单,操作方便,整个制备过程不需要额外调节ph和加入稀有气体进行保护,省去了繁琐的步骤,且有效的降低了成本。
5.本发明的另一目的在于提供一种由上述水化硅酸钙早强剂的制备方法所制得的早强剂;该早强剂中钙源和硅源中cao与sio2的摩尔比为1.9~2.3,较高的钙硅比可以降低产品的碱含量,避免在混凝土中加入产品后出现反碱现象,且该早强剂能够显著提升混凝土在高温和低温下的早期强度。
6.本发明解决其技术问题是采用以下技术方案来实现的。
7.一方面,本技术实施例提供一种水化硅酸钙晶核早强剂的制备方法,其特征在于,包括以下步骤:
8.水化硅酸钙晶种悬浮液的制备:将钙源的水溶液和硅源的水溶液分别滴加至聚羧酸减水剂溶液中,并进行加热和搅拌反应,得到水化硅酸钙晶种悬浮液,所述钙源和硅源中cao与sio2的摩尔比为1.9~2.3;
9.早强剂的制备:向质量分数为0.5-1.5%的水化硅酸钙晶种悬浮液中加入硝酸盐,再滴加硅源的水溶液,待溶液滴加完全后,保温反应2-5h,最后加入防沉剂搅拌即得到早强剂产品。
10.另一方面,本技术实施例提供一种由上述水化硅酸钙晶核早强剂的制备方法所制备的早强剂。
11.相对于现有技术,本发明的实施例至少具有如下优点或有益效果:
12.1、制备工艺流程简单,操作方便,整个制备过程不需要额外调节ph和加入稀有气体进行保护,省去了繁琐的步骤,且有效的降低了成本。
13.2、该早强剂中钙源和硅源中cao与sio2的摩尔比为1.9~2.3,较高的钙硅比可以降低产品的碱含量,避免在混凝土中加入产品后出现反碱现象。
14.3、在该早强剂的制备材料中,用硝酸镁替代了传统的硝酸铝,mg
2
可以少量取代硅氧四面体中的si
4
,形成镁氧八面体结构,镶嵌在硅氧四面体之间。mg
2
对si
4
取代将多出2个负电荷,多出的电荷由带正电荷的mg
2
或ca
2
进行平衡,因此镁氧八面体表面将吸附较多的正电荷,这将为减水剂分子提供更多的吸附点,可以提高水化硅酸钙的分散性,降低其颗粒粒径,有助于提升产品的稳定性。较低的颗粒粒径可以更好的分散在混凝土中,为水泥的水化提供更多的水化点,从而有助于提升抗压强度,使混凝土在短时间里达到更高的强度,以满足承受外力的要求。
附图说明
15.为了更清楚地说明本发明实施例的技术方案,下面将对实施例中所需要使用的附图作简单地介绍,应当理解,以下附图仅示出了本发明的某些实施例,因此不应被看作是对范围的限定,对于本领域普通技术人员来讲,在不付出创造性劳动的前提下,还可以根据这些附图获得其他相关的附图。
16.图1为本发明实施例中水化硅酸钙晶核早强剂红外测试结果。
具体实施方式
17.为使本发明实施例的目的、技术方案和优点更加清楚,下面将对本发明实施例中的技术方案进行清楚、完整地描述。实施例中未注明具体条件者,按照常规条件或制造商建议的条件进行。所用试剂或仪器未注明生产厂商者,均为可以通过市售购买获得的常规产品。
18.需要说明的是,在不冲突的情况下,本技术中的实施例及实施例中的特征可以相互组合。下面将参考具体实施例来详细说明本发明。
19.一种水化硅酸钙晶核早强剂的制备方法,包括以下步骤:
20.水化硅酸钙晶种悬浮液的制备:将钙源的水溶液和硅源的水溶液分别滴加至聚羧酸减水剂溶液中,并进行加热和搅拌反应,得到水化硅酸钙晶种悬浮液,所述钙源和硅源中cao与sio2的摩尔比为1.9~2.3。
21.早强剂的制备:向质量分数为0.5-1.5%的水化硅酸钙晶种悬浮液中加入硝酸盐,再滴加硅源的水溶液,待溶液滴加完全后,保温反应2-5h,最后加入防沉剂搅拌即得到早强剂产品。
22.本发明采用晶种聚合技术制备水化硅酸钙晶核早强剂,合成工艺简单,可以显著缩短合成周期,易于量产。该早强剂中钙源和硅源中cao与sio2的摩尔比为1.9~2.3,较高的钙硅比可以降低产品的碱含量,避免在混凝土中加入产品后出现反碱现象。整个制备过程不需要额外调节ph和加入稀有气体进行保护,省去了繁琐的步骤,且有效的降低了成本。
23.在本发明的一些实施例中,上述钙源为硝酸钙。要在溶液中合成水化硅酸钙,就需要提供钙离子,原料必须可溶可电离,同时不能引入氯离子,以免腐蚀钢筋。再考虑成本因素,因此最满足条件的原料就是硝酸钙。
24.在本发明的一些实施例中,上述硅源为硅酸钠。要在溶液中合成水化硅酸钙,就需
要提供硅酸根离子,原料必须可溶可电离,再考虑成本因素,因此最满足条件的原料就是硅酸钠。使用硅酸钠还可以调节溶液的ph,使溶液呈碱性。
25.在本发明的一些实施例中,上述硅酸钠的模数为1.4-1.8。硅酸钠易溶于水,且碱性较高,选择模数较低的硅酸钠能够满足水化硅酸钙的合成条件,所以无需外加碱性物质来调节ph。
26.在本发明的一些实施例中,上述聚羧酸减水剂溶液的质量分数为0.1-0.3%。掺入少量聚羧酸减水剂的目的是起到分散效果,让钙离子吸附在聚羧酸分子上,与硅酸盐结合生成水化硅酸钙,使产物颗粒均匀。这个比例下,减水剂可以充分溶解分散。比例太低减水剂分子不足,水化硅酸钙颗粒不均匀,导致所制备的水化硅酸钙晶核早强剂对混凝土的抗压强度降低,比例太大会增加成本。
27.在本发明的一些实施例中,上述硝酸盐为硝酸钙、硝酸镁和硝酸钠的混合物。硝酸盐中主要选用的硝酸钙,以给反应提供足够的钙离子,掺入少量硝酸镁的目的是在合成过程中少量的镁离子可以取代水化硅酸钙中硅氧四面体中的硅,生成镁氧八面体,为减水剂的吸附提供更多位点,提高水化硅酸钙颗粒的分散性,使产品更稳定。掺入少量硝酸钠有辅助增强的作用,可以提高产品的增强效果。
28.在本发明的一些实施例中,上述硝酸钙、硝酸钠、硝酸镁的质量比为15-20∶0.8-1∶0.5-0.8。三种硝酸盐以硝酸钙为主,以提供足够的钙离子。硝酸钠在此比例下具有较好的增强作用,比例太高会在产品中引入过多的碱,影响产品使用效果。而硝酸镁在此比例下,镁可以少量取代水化硅酸钙中硅氧四面体中的硅,生成镁氧八面体。剩下的镁离子将取代部分钙离子,用于中和硅氧四面体和镁氧八面体的负电荷。比例过高会影响混凝土强度,太低达不到目的。
29.在本发明的一些实施例中,上述加热温度为50-65℃,所述搅拌转速为500-600r/min。这个温度范围是合成水化硅酸钙的最佳温度范围,高转速下,可以起到良好的剪切作用,使生成的水化硅酸钙颗粒细少,便于分散在水中,形成稳定的悬浮液。
30.在本发明的一些实施例中,上述防沉剂为耐盐性黄原胶。为了使水化硅酸钙颗粒均分散在水中,不发生分层现象产生沉淀,需要提高悬浮液的粘度。但产品含有大量的盐类物质,多数增稠剂在高盐溶液中会失去增稠作用,所以必须选择耐盐性胶,比如耐盐黄原胶。
31.一种由上述水化硅酸钙晶核早强剂的制备方法所制备的早强剂。
32.采用本发明提供的一种水化硅酸钙晶核早强剂的制备方法所制备的早强剂能够显著提升混凝土的早期抗压强度。
33.以下结合实施例对本发明的特征和性能作进一步的详细描述。
34.实施例1
35.一种水化硅酸钙晶核早强剂的制备方法,包括以下步骤:
36.水化硅酸钙晶种悬浮液的制备:配制硝酸盐溶液,用洁净的自来水配制质量分数为0.1%的聚羧酸减水剂溶液,再加入ca(no3)2·
4h2o并进行搅拌使其充分溶解,溶液的含固量控制在20%。配制硅酸盐溶液,用洁净的自来水配制0.1%的聚羧酸减水剂溶液,再加入na2sio3,并进行搅拌使其充分溶解,na2sio3的模数为1.4。在带有搅拌机的双层反应釜中加入计量的硝酸盐溶液,控制釜内温度为50℃,调节搅拌转速为500r/min。采用滴加的方式
向上述加入硝酸盐溶液的反应釜内滴加上述硅酸盐溶液,滴加速率为60ml/min。滴加结束后,保温反应72h,以生成足够量的c-s-h晶粒。硝酸盐和硅酸盐溶液的用量按等效cao/sio2的摩尔比例为1.9计量。反应所得产品为含有大量c-s-h晶种的悬浮液,密封保存备用。
37.水化硅酸钙晶核早强剂的制备:配制反应底液,用上述制备好的水化硅酸钙晶种悬浮液和洁净的自来水配制0.5%的反应底液,并在反应釜中高速搅拌分散45min,搅拌速度为850r/min。然后调低搅拌速度至100r/min,向上述反应釜中依次投入经计量的ca(no3)2·
4h2o、nano3、mg(no3)2·
6h2o,三种硝酸盐的质量比为15:0.8:0.5,总质量按釜内底液的20%计。配制硅酸盐溶液,用洁净的自来水配制0.1%的聚羧酸减水剂溶液,将na2sio3加入至配制好的聚羧酸减水剂溶液,并进行搅拌使其充分溶解,na2sio3的模数为1.4。待反应釜内硝酸盐溶解完全后,向釜内滴加硅酸盐溶液,滴加速率为60ml/min,待溶液滴加完全后,再保温反应3.5h。反应结束并冷却至室温后,再按产物总质量的0.05%添加耐盐性黄原胶,继续搅拌25min,即得到早强剂产品。
38.实施例2
39.本实施例与实施例1的制备方法基本相同,区别在于:1、聚羧酸减水剂溶液的质量分数为0.3%;2、na2sio3的模数为1.8;3、在带有搅拌机的双层反应釜中加入计量的硝酸盐溶液,控制釜内温度为65℃,调节搅拌转速为600r/min;4、硝酸盐和硅酸盐溶液的用量按等效cao/sio2的摩尔比例为2.3计量;5、反应底液的质量分数为1.5%;6、ca(no3)2·
4h2o、nano3、mg(no3)2·
6h2o,三种硝酸盐的质量比为20∶1∶0.8;7、耐盐性黄原胶按产物总质量的0.08%掺入。
40.实施例3
41.本实施例与实施例1的制备方法基本相同,区别在于:1、聚羧酸减水剂溶液的质量分数为0.2%;2、na2sio3的模数为1.5;3、在带有搅拌机的双层反应釜中加入计量的硝酸盐溶液,控制釜内温度为55℃,调节搅拌转速为550r/min;4、硝酸盐和硅酸盐溶液的用量按等效cao/sio2的摩尔比例为2.1计量;5、反应底液的质量分数为1.0%;6、ca(no3)2·
4h2o、nano3、mg(no3)2·
6h2o,三种硝酸盐的质量比为18∶0.9∶0.6;7、耐盐性黄原胶的按产物总质量的0.06%掺入。
42.实施例4
43.本实施例与实施例1的制备方法基本相同,区别在于:1、聚羧酸减水剂溶液的质量分数为0.2%;2、na2sio3的模数为1.7;4、硝酸盐和硅酸盐溶液的用量按等效cao/sio2的摩尔比例为2.2计量;5、反应底液的质量分数为1.2%;6、ca(no3)2·
4h2o、nano3、mg(no3)2·
6h2o,三种硝酸盐的质量比为16∶0.8∶0.7。
44.实施例5
45.本实施例与实施例1的制备方法基本相同,区别在于:1、聚羧酸减水剂溶液的质量分数为0.2%;2、na2sio3的模数为1.5;2、硝酸盐和硅酸盐溶液的用量按等效cao/sio2的摩尔比例为2.0计量;3、反应底液的质量分数为1.0%;4、ca(no3)2·
4h2o、nano3、mg(no3)2·
6h2o,三种硝酸盐的质量比为17∶0.9∶0.7;5、耐盐性黄原胶按产物总质量的0.07%掺入。
46.实验例1
47.将实施例1-5中制备好的水化硅酸钙晶核早强剂取样使用红外测试仪进行产物检测,其测定结果如图1所示。
48.由图1可以得出,449cm-1
和984cm-1
处分别为si-o-si(q1)的弯曲振动吸收峰和si-o(q2)的弹性振动吸收峰,1423cm-1
为ca-o-ca的振动吸收峰,1634cm-1
为结晶水的振动吸收峰,3443cm-1
为-oh的振动吸收峰,上述结果表明该早强剂产品成分为水化硅酸钙。
49.实验例2
50.为了测试实施例1中制得的水化硅酸钙晶核早强剂在高温蒸养混凝土中的作用效果,将水泥、砂子、碎石、水和减水剂分别按照表1中的量进行配比混合形成混凝土,将上述制得的早强剂分别加入至45℃蒸养温度的混凝土中,并分别设置了2h、3h、4h三个蒸养时间梯度,每组实验设定一个对照组(未添加早强剂)和一个实验组(早强剂添加量为3%)。上述3个实验组仅改变了上述硝酸盐和硅酸盐的比例,其他条件不变,用钙硅比来表示改变的硝酸盐和硅酸盐的比例,上述三个实验组钙硅比分别设定为1.9、2.1和2.3。各组均在混凝土拌合后12小时进行强度测试,其测定结果如表1所示。
51.表1早强剂在高温蒸养混凝土中的测试结果
[0052][0053][0054]
由表1的结果分析可知,上述早强剂在45℃蒸养温度的混凝土中,对于蒸养时间2h、3h、4h的混凝土,加入上述早强剂后,12h的抗压强度分别提升了48.2%、38.5%、17.6%。上述实验结果表明上述早强剂对于蒸养时间较短的混凝土作用较好,且能够显著提升45℃蒸养混凝土的早期抗压强度。
[0055]
实验例3
[0056]
为了测试实施例1中制得的水化硅酸钙晶核早强剂在高温蒸养混凝土中的作用效果,将水泥、砂子、碎石、水和减水剂分别按照表1中的量进行配比混合形成混凝土,将上述制得的早强剂分别加入至60℃蒸养温度的混凝土中,并分别设置了1.5h、2.5h、3.5h三个蒸养时间梯度,每组实验设定一个对照组(未添加早强剂)和一个实验组(早强剂添加量为
3%)。上述3个实验组仅改变了上述硝酸盐和硅酸盐的比例,其他条件不变,用钙硅比来表示改变的硝酸盐和硅酸盐的比例,上述三个实验组钙硅比分别设定为1.9、2.1和2.3。在60℃蒸养温度下,各组均在混凝土拌合后12小时进行强度测试,其测定结果如表1所示。
[0057]
由表1的结果分析可知,上述早强剂在60℃蒸养温度的混凝土反应中,对于蒸养时间1.5h、2.5h、3.5h的混凝土,加入上述早强剂后,12h的抗压强度分别提升了64.4%、15.8%、13.1%。上述实验结果表明上述早强剂对于蒸养时间较短的混凝土作用较好,且能够显著提升60℃蒸养混凝土的早期抗压强度。
[0058]
实验例4
[0059]
为了测试实施例1中制得的水化硅酸钙晶核早强剂在低温养护混凝土中的作用效果,将粉煤灰、砂子、碎石、水和减水剂分别按照表2中的量进行配比混合形成混凝土,将上述制得的早强剂加入平均养护温度为8℃、5-6℃、10-12℃的混凝土中进行反应,每组实验设定一个对照组(未添加早强剂)和三个实验组(早强剂添加量为3%),三个实验组中的钙硅比分别为1.9、2.1、2.3。各组均在混凝土拌合后24h进行抗压强度测定,其测定结果如表3所示。
[0060]
表2混凝土配比
[0061][0062][0063]
表3早强剂在低温养护混凝土中的测试结果
[0064][0065][0066]
由表3分析可知,本实施例中的水化硅酸钙晶核早强剂可以显著提升平均养护温度为8℃、5-6℃、10-12℃的的混凝土的抗压强度,且抗压强度随着上述早强剂中钙硅比的增大而增大。较高的钙硅比可以降低产品的碱含量,避免在混凝土中加入产品后出现反碱现象。
[0067]
对比例1
[0068]
本实施例中所用早强剂为实施例1中所制备的水化硅酸钙晶核早强剂。
[0069]
本实施例中,为了进一步说明本发明提供的一种水化硅酸钙晶核早强剂的性能效
果,对市售的两个厂家:上海三瑞高分子材料有限公司、上海炽为新材料有限公司制备的晶核早强剂进行了对比实验。将水泥、砂子、碎石、水和减水剂分别按照表4中的配比进行混合形成混凝土,将实施例1制得的早强剂按照3%的添加量加入上述混凝土中进行反应,在反应时间18h、1d、3d、7d、28d取样进行混凝土抗压强度测定。其测定结果如表5所示。第1组为空白对照,第2组是实验组,第3、4组为上述两个不同厂家的晶核早强剂。
[0070]
表4配合比设计
[0071]
编号水泥/kg.m-3
砂子/kg.m-3
碎石/kg.m-3
水/kg.m-3
减水剂/kg.m-3
早强剂/%136083010601456.40236083010601456.43336083010601456.43436083010601456.43
[0072]
表5早强剂在混凝土中的测试结果
[0073]
编号18h/mpa1d/mpa3d/mpa7d/mpa28d/mpa15.912.346.554.477.2213.528.654.364.480.1310.924.750.459.475.6411.922.149.261.476.2
[0074]
由表5分析可知,本实施例中提供的一种水化硅酸钙晶核早强剂对比市售的其他厂家的晶核早强剂可以显著提升混凝土的抗压强度,加入上述早强剂1d后,混凝土的抗压强度可以达到28.6mpa,3d后的混凝土的抗压强度可以达到54.3mpa,均高于市售的其他两个厂家的晶核早强剂。
[0075]
综上所述,本发明实施例的一种水化硅酸钙晶核早强剂及其制备方法,本发明采用晶种引发聚合技术,合成工艺简单,可以显著缩短合成周期,易于量产。本发明选择的硅酸钠模数较低,低模数的硅酸钠易溶于水且碱性较高,能够满足水化硅酸钙的合成条件,所以无需外加碱性物质来调节ph。在已有的晶核早强剂制备过程中普遍需要加入稀有气体进行保护,目的是为了防止水化硅酸钙在合成过程中碳化,但并不能避免产品在贮存、运输和使用过程中的碳化,所以加入稀有气体进行保护对实际生产和使用无意义。另外,水化硅酸钙产品的碳化可以将产品中的少量氢氧化钙转变为碳酸钙,后者也可以起到晶种的作用,诱导水泥水化,具有积极的作用。因此本发明提供的一种水化硅酸钙晶核早强剂的制备方法中未加入稀有气体进行保护。整个制备过程不需要额外调节ph和加入稀有气体进行保护,省去了繁琐的步骤,且有效的降低了成本。该早强剂中钙源和硅源中钙cao与sio2的摩尔比为1.9~2.3,实验结果表明较高的钙硅比可以降低产品的碱含量,避免在混凝土中加入产品后出现反碱现象。在该早强剂的制备材料中,用硝酸镁替代了传统的硝酸铝,mg
2
可以少量取代硅氧四面体中的si
4
,形成镁氧八面体结构,镶嵌在硅氧四面体之间。mg
2
对si
4
取代将多出2个负电荷,多出的电荷由带正电荷的mg
2
或ca
2
进行平衡,因此镁氧八面体表面将吸附较多的正电荷,这将为减水剂分子提供更多的吸附点,可以提高水化硅酸钙的分散性,降低其颗粒粒径,有助于提升产品的稳定性。较低的颗粒粒径可以更好的分散在混凝土中,为水泥的水化提供更多的水化点,从而有助于提升抗压强度,使混凝土在短时间里达到更高的强度,以满足承受外力的要求。
[0076]
本发明提供的一种水化硅酸钙晶核早强剂在45℃蒸养混凝中,对于蒸养时间2h、3h、4h的混凝土,加入上述早强剂后,12h的抗压强度分别提升了48.2%、38.5%、17.6%。上述早强剂在60℃蒸养混凝土中,对于蒸养时间1.5h、2.5h、3.5h的混凝土,加入上述早强剂后,12h的抗压强度分别提升了64.4%、15.8%、13.1%。上述实验结果表明上述早强剂对于蒸养时间较短的混凝土作用较好,且能够显著提升高温蒸养混凝土的早期抗压强度。
[0077]
本发明提供的一种水化硅酸钙晶核早强剂可以显著提升平均养护温度为5-12℃的混凝土的抗压强度,且抗压强度随着上述早强剂中钙硅比的增大而增大。
[0078]
本发明提供的一种水化硅酸钙晶核早强剂与市售的其他厂家的晶核早强剂的对比实验结果表明,本发明提供的一种水化硅酸钙晶核早强剂可以显著提升混凝土的抗压强度,加入该早强剂1d后,混凝土的抗压强度可以达到28.6mpa,3d后的混凝土的抗压强度可以达到54.3mpa,均高于市售的其他两个厂家的晶核早强剂,具有市场竞争力。
[0079]
以上所描述的实施例是本发明一部分实施例,而不是全部的实施例。本发明的实施例的详细描述并非旨在限制要求保护的本发明的范围,而是仅仅表示本发明的选定实施例。基于本发明中的实施例,本领域普通技术人员在没有作出创造性劳动前提下所获得的所有其他实施例,都属于本发明保护的范围。
再多了解一些
本文用于企业家、创业者技术爱好者查询,结果仅供参考。