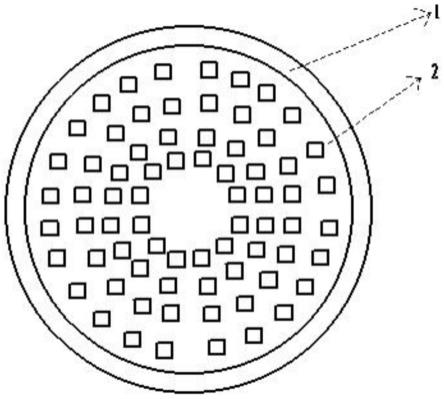
1.本发明属于特种异形涤纶复合纤维生产的技术领域,涉及一种双组分弹性复合纤维的制备方法。
背景技术:
2.近几年从nike、adidas和reebok等品牌采用功能性布料数量逐渐增加的趋势来看,具有抗菌、防臭、防火、保暖排汗、透湿防水等一系列健康性、功能性、高科技智慧型纺织品将成为未来市场主流。吸湿排汗纤维用途广泛,市场前景广阔。国际上研究起步较早,美国杜邦最早开发的coolmax、日本东洋公司开发的triactor产品被军方采购制作军服。“十”字形异形纤维的后道产品有非常好的吸湿排汗性能,但市场上的“十”字形异形纤维的生产工艺基本采用普通的“十”字形喷丝孔喷丝板,清板周期短,往往喷丝板清洁后十来个小时左右,板面就脏了,容易造成纺丝断头、飘丝,从而加大了生产成本,对后道加工也带来很多不利的影响。
3.随着合成纤维应用范围的不断扩大和纺丝技术的发展,各种具有高附加值的差别化纤维,不断地得到开发与应用,其中复合纺丝技术尤为突出。复合纤维是将两种或两种以上的高聚物熔体,利用其品种、粘度或配比的不同,分别通过各自的熔体管道,在复合组件内进行分配,从喷丝板孔挤出,形成一束纤维。现阶段的复合纤维生产基本都是生产常规的圆孔复合丝,很少有异形复合纤维的产品,其潜在卷曲性能、卷曲稳定性和弹性回复性相对较差。专利cn104726947a公开了一种双组份十字形复合纤维,潜在卷曲性能、卷曲稳定性和弹性回复性相对较好,但其喷丝孔为普通的“十”字形喷丝孔喷丝板,生产时清板周期短,往往喷丝板清洁后十来个小时左右,板面就脏了,容易造成纺丝断头、飘丝,从而加大了生产成本。
4.因此,研究一种清板周期长且潜在卷曲性能、卷曲稳定性和弹性回复性相对较好的双组分弹性复合纤维具有极其重要的意义。
技术实现要素:
5.本发明的目的是解决现有技术中存在的问题,提供一种双组分弹性复合纤维的制备方法。
6.为达到上述目的,本发明采用的技术方案如下:
7.一种双组份弹性复合纤维的制备方法,将两种不同的高聚物熔体进行复合纺丝制得双组份弹性复合纤维,复合纺丝所用的喷丝板上设有多个单位喷丝组合孔;
8.各个单位喷丝组合孔由一组相对的圆形喷丝孔i和ii以及另一组相对的圆形喷丝孔iii和iv组成,圆形喷丝孔i~iv的圆心分别位于正方形的四条边的中点上,圆形喷丝孔i~iv的直径相同都为 0.13~0.14mm,圆形喷丝孔i和ii的间距(其值等于圆形喷丝孔i和ii的中心点的距离减去圆形喷丝孔i 的半径与圆形喷丝孔ii的半径之和)为0.08~0.10mm;喷丝孔的直径小于0.13mm时,喷丝孔加工困难,而且不容易清洗,易造成堵孔现象,无法正
常生产,对本发明来说,喷丝孔的直径大于0.14mm时,剪切速率过小,熔体的流动性差,容易造成注头丝;如果圆形喷丝孔i和ii的间距(或圆形喷丝孔iii和 iv间距)过小,四个喷丝孔流出的熔体由于膨化胀大效应融合连接形成十字形状的纤维截面异形度低,其吸湿排汗性能较差;如果过大,则融合连接困难,不能形成十字形纤维截面;
9.两种不同的高聚物熔体分别是特性粘度为0.48~0.60dl/g的pet熔体和特性粘度为0.65~0.90dl/g的 pet熔体,一种从圆形喷丝孔i和ii中挤出,另一种从圆形喷丝孔iii和iv中挤出,两种高聚物熔体的特性粘度相差过小,则本发明产品的卷曲性能、卷曲稳定性和弹性回复性较差,如果相差过大,则两者熔体在流动性上的差异导致两熔体的膨化胀大效应差异大,从而难形成规则的十字形纤维截面,进而影响后道织物的吸湿排汗性能;
10.相邻两个单位喷丝组合孔的间距(即相邻两个单位喷丝组合孔中距离最近的两个圆形喷丝孔的间距,其值等于相邻两个单位喷丝组合孔中距离最近的两个圆形喷丝孔的中心点的距离减去这两个圆形喷丝孔的半径之和)大于5mm困难;
11.复合纺丝的纺丝温度(即喷丝板处熔体熔融挤出温度)为295~300℃;pet的熔点在265℃以上,为保证复合熔体的流动性,纺丝温度一般放在290℃以上,十字形纤维是异形纤维,要求温度更高,因此设定为295~300℃。
12.作为优选的技术方案:
13.如上所述的一种双组份弹性复合纤维的制备方法,所述喷丝板的清板周期为32~48h;十字形纤维在生产中,与圆形喷丝孔相比较,十字形喷丝孔使得喷丝板孔口呈矩形状,齐聚物及结焦物在喷丝孔更容易集聚而且较多,造成熔体挤出不顺,存在弯头现象,这些因素使得单纯的喷丝孔为十字形的十字纤维板面脏的快,板面难铲,清板周期最多维持在16h左右,本发明的十字形纤维在于十字纤维的形成不是依靠十字形喷丝孔,而是通过熔体流变性能即熔体流动的膨化胀大效应,由四个小圆孔流出的熔体融合连接形成十字形状的纤维,其喷丝板的喷丝孔是圆形组合孔,而非十字形喷丝孔,圆形孔孔口周长小,齐聚物及结焦物不易集聚,本发明的十字形纤维清板周期可以达到32~48h。
14.如上所述的一种双组份弹性复合纤维的制备方法,双组份弹性复合纤维的卷曲拉伸率为38~42%,卷曲弹性回复率为74~88%,断裂强度cv%为2.8~3.7,断裂伸长cv%为3.6~4.5;常规十字形纤维的卷曲拉伸率为20~30%,卷曲弹性回复率为50~70%,断裂强度cv%为5.2~6.0,断裂伸长cv%为7.0~8.2,本发明的双组份弹性复合纤维的性能能够达到高于现有技术的水平。
15.如上所述的一种双组份弹性复合纤维的制备方法,圆形喷丝孔i~iv的长径比相同都为3~4。
16.如上所述的一种双组份弹性复合纤维的制备方法,喷丝板上设有48、72或144个单位喷丝组合孔。
17.如上所述的一种双组份弹性复合纤维的制备方法,相邻两个单位喷丝组合孔的间距为6.0~8.3mm,如此设置的原因一是喷丝板的直径范围在65~88mm,二是保证从喷丝板熔融挤出的纤维丝条有效散热冷却。
18.如上所述的一种双组份弹性复合纤维的制备方法,整体工艺流程为:熔融挤出
→
冷却固化
→
集束上油
→
卷绕成型。
19.如上所述的一种双组份弹性复合纤维的制备方法,冷却固化采用环吹风装置冷却
成形,环吹风的温度为18℃~20℃,相对湿度为75~85%,压强为600~800pa。
20.如上所述的一种双组份弹性复合纤维的制备方法,集束上油采用油嘴上油,出油孔为扁平孔,可减少摩擦系数,有效提高平滑性,避免上油不均造成飘丝,异常断头。
21.有益效果
22.十字形纤维在生产中,与圆形喷丝孔相比较,十字形喷丝孔使得喷丝板孔口呈矩形状,齐聚物及结焦物在喷丝孔更容易集聚而且较多,造成熔体挤出不顺,存在弯头现象,这些因素使得单纯的喷丝孔为十字形的十字纤维板面脏的快,板面难铲,清板周期最多维持在16小时左右,本发明的十字形纤维在于十字纤维的形成不是依靠十字形喷丝孔,而是通过熔体流变性能即熔体流动的膨化胀大效应,由四个直径相同的小圆孔流出的熔体融合连接形成十字形状的纤维,其喷丝板的喷丝孔是圆形组合孔,而非十字形喷丝孔,圆形孔孔口周长小,齐聚物及结焦物不易集聚,本发明的十字形纤维清板周期可以达到32小时以上,有效地提高了纺丝喷丝板清板周期。
附图说明
23.图1为本发明的喷丝板的单位喷丝组合孔排列示意图;
24.图2为本发明的喷丝板的喷丝孔示意图;
25.图3为实施例3的喷丝组合孔与对比例3的喷丝孔的比较图;
26.其中,1-喷丝板,2-单位喷丝组合孔,3-圆形喷丝孔i,4-圆形喷丝孔ii,5-圆形喷丝孔iii,6-圆形喷丝孔iv。
具体实施方式
27.下面结合具体实施方式,进一步阐述本发明。应理解,这些实施例仅用于说明本发明而不用于限制本发明的范围。此外应理解,在阅读了本发明讲授的内容之后,本领域技术人员可以对本发明作各种改动或修改,这些等价形式同样落于本技术所附权利要求书所限定的范围。
28.实施例1
29.一种双组份弹性复合纤维的制备方法,具体过程如下:
30.将两种不同的高聚物熔体进行复合纺丝制得双组份弹性复合纤维;
31.整体工艺流程为:熔融挤出
→
冷却固化
→
集束上油
→
卷绕成型;
32.其中,如图1~2所示,复合纺丝所用的喷丝板1上设有72个单位喷丝组合孔2;各个单位喷丝组合孔2由一组相对的圆形喷丝孔i 3和圆形喷丝孔ii 4以及另一组相对的圆形喷丝孔iii 5和圆形喷丝孔iv 6组成,圆形喷丝孔i 3、圆形喷丝孔ii 4、圆形喷丝孔iii 5和圆形喷丝孔iv 6的圆心分别位于正方形的四条边的中点上,圆形喷丝孔i 3、圆形喷丝孔ii 4、圆形喷丝孔iii 5和圆形喷丝孔iv 6的直径(即图2 中的a)相同都为0.13mm,圆形喷丝孔i 3和圆形喷丝孔ii 4的间距(即图2中的b)为0.08mm;圆形喷丝孔i 3、圆形喷丝孔ii 4、圆形喷丝孔iii 5和圆形喷丝孔iv 6的长径比相同都为3;相邻两个单位喷丝组合孔2的间距为6mm;
33.两种不同的高聚物熔体分别是特性粘度为0.48dl/g的pet熔体和特性粘度为0.65dl/g的pet熔体,一种从圆形喷丝孔i 3和圆形喷丝孔ii 4中挤出,另一种从圆形喷丝
孔iii 5和圆形喷丝孔iv 6中挤出;复合纺丝的纺丝温度(即喷丝板处熔体熔融挤出温度)为295℃;
34.冷却固化采用环吹风装置冷却成形,环吹风的温度为18℃,相对湿度为75%,压强为600pa;
35.集束上油采用油嘴上油,出油孔为扁平孔。
36.最终制得的双组份弹性复合纤维的横截面为十字形;制得的双组份弹性复合纤维的卷曲拉伸率为 39.5%,卷曲弹性回复率为78.4%,断裂强度cv%为3.56,断裂伸长cv%为4.27,含油率为0.48%;喷丝板的清板周期为36h。
37.对比例1
38.一种双组份弹性复合纤维的制备方法,基本同实施例1,不同之处仅在于,圆形喷丝孔i和圆形喷丝孔ii的间距为0.06mm。
39.制得的双组份弹性复合纤维的卷曲拉伸率为32%,卷曲弹性回复率为64%,断裂强度cv%为6.87,断裂伸长cv%为9.60,含油率为0.48%;喷丝板的清板周期为18h。
40.与实施例1相比,对比例1的卷曲拉伸率、卷曲弹性回复率、断裂强度cv%、断裂伸长cv%远不如实施例1,这是因为圆形喷丝孔i和圆形喷丝孔ii的间距过小,膨化胀大融合连接时重叠面积较大,导致异形效果差。
41.对比例2
42.一种复合纤维的制备方法,基本同实施例1,不同之处仅在于,圆形喷丝孔i和圆形喷丝孔ii的间距为0.12mm。
43.无法制得复合纤维,这是因为圆形喷丝孔i和圆形喷丝孔ii的间距过大,导致无法融合连接。
44.实施例2
45.一种双组份弹性复合纤维的制备方法,具体过程如下:
46.将两种不同的高聚物熔体进行复合纺丝制得双组份弹性复合纤维;
47.整体工艺流程为:熔融挤出
→
冷却固化
→
集束上油
→
卷绕成型;
48.其中,复合纺丝所用的喷丝板上设有72个单位喷丝组合孔;各个单位喷丝组合孔由一组相对的圆形喷丝孔i和ii以及另一组相对的圆形喷丝孔iii和iv组成,圆形喷丝孔i~iv的圆心分别位于正方形的四条边的中点上,圆形喷丝孔i~iv的直径相同都为0.14mm,圆形喷丝孔i和ii的间距为0.1mm;圆形喷丝孔i~iv的长径比相同都为4;相邻两个单位喷丝组合孔的间距为6.5mm;
49.两种不同的高聚物熔体分别是特性粘度为0.5dl/g的pet熔体和特性粘度为0.7dl/g的pet熔体,一种从圆形喷丝孔i和ii中挤出,另一种从圆形喷丝孔iii和iv中挤出;复合纺丝的纺丝温度(即喷丝板处熔体熔融挤出温度)为296℃;
50.冷却固化采用环吹风装置冷却成形,环吹风的温度为19℃,相对湿度为77%,压强为700pa;
51.集束上油采用油嘴上油,出油孔为扁平孔。
52.制得的双组份弹性复合纤维的卷曲拉伸率为40.4%,卷曲弹性回复率为81.7%,断裂强度cv%为 3.27,断裂伸长cv%为4.09,含油率为0.52%;喷丝板的清板周期为36h。
53.实施例3
54.一种双组份弹性复合纤维的制备方法,具体过程如下:
55.将两种不同的高聚物熔体进行复合纺丝制得双组份弹性复合纤维;
56.整体工艺流程为:熔融挤出
→
冷却固化
→
集束上油
→
卷绕成型;
57.其中,复合纺丝所用的喷丝板上设有144个单位喷丝组合孔;各个单位喷丝组合孔由一组相对的圆形喷丝孔i和ii以及另一组相对的圆形喷丝孔iii和iv组成,圆形喷丝孔i~iv的圆心分别位于正方形的四条边的中点上,圆形喷丝孔i~iv的直径a相同都为0.13mm,圆形喷丝孔i和ii的间距c为0.1mm;圆形喷丝孔i~iv的长径比相同都为3;相邻两个单位喷丝组合孔的间距为7mm;
58.两种不同的高聚物熔体分别是特性粘度为0.53dl/g的pet熔体和特性粘度为0.75dl/g的pet熔体,一种从圆形喷丝孔i和ii中挤出,另一种从圆形喷丝孔iii和iv中挤出;复合纺丝的纺丝温度(即喷丝板处熔体熔融挤出温度)为297℃;
59.冷却固化采用环吹风装置冷却成形,环吹风的温度为20℃,相对湿度为79%,压强为800pa;
60.集束上油采用油嘴上油,出油孔为扁平孔。
61.制得的双组份弹性复合纤维的卷曲拉伸率为41.5%,卷曲弹性回复率为87.5%,断裂强度cv%为2.86,断裂伸长cv%为3.62,含油率为0.56%;喷丝板的清板周期为48h。
62.对比例3
63.一种十字形纤维的制备方法,具体过程如下:
64.将特性粘度在0.65dl/g的pet熔体进行纺丝制得字形纤维;
65.整体工艺流程为:熔融挤出
→
冷却固化
→
集束上油
→
卷绕成型;
66.其中,纺丝板上的喷丝孔为“十”字形状,由两个矩形孔重叠构成,矩形孔长0.36mm,矩形孔宽 0.13mm;
67.冷却固化采用环吹风装置冷却成形,环吹风的温度为20℃,相对湿度为79%,压强为800pa;
68.集束上油采用油嘴上油,出油孔为圆孔;
69.制得的十字形纤维卷曲拉伸率为25%,卷曲弹性恢复率为62%,强度cv%为5.7,断裂伸cv%为 7.7;清板周期为16h。
70.与实施例3相比,对比例3的清板周期远短于实施例3,这是因为十字形喷丝孔使得喷丝板孔口呈矩形状,齐聚物及结焦物在喷丝孔更容易集聚而且较多,造成熔体挤出不顺,存在弯头现象,这些因素使得单纯的喷丝孔为十字形的十字纤维板面脏的快,板面难铲。
71.如图3所示,为对比例3的喷丝孔和实施例3的喷丝组合孔的比较图,对比例3的喷丝孔(即两个矩形重叠处)中心的内接圆的直径为0.13mm,面积为0.0132mm2,以喷丝孔(即两个矩形重叠处)中心的外接圆直径为0.36mm,面积为0.1018mm2,异形度为(0.1018-0.0132)/0.1018=87%;实施例3的喷丝组合孔的4个圆形喷丝孔之间的中心内接圆的直径为0.10mm,面积为0.0078mm2,外接圆直径也为 0.36mm,面积为0.1018mm2,异形度为(0.1018-0.0078)/0.1018=92%,实施例3纤维的异形度高于对比例3纤维的异形度。
72.实施例4
73.一种双组份弹性复合纤维的制备方法,具体过程如下:
74.将两种不同的高聚物熔体进行复合纺丝制得双组份弹性复合纤维;
75.整体工艺流程为:熔融挤出
→
冷却固化
→
集束上油
→
卷绕成型;
76.其中,复合纺丝所用的喷丝板上设有48个单位喷丝组合孔;各个单位喷丝组合孔由一组相对的圆形喷丝孔i和ii以及另一组相对的圆形喷丝孔iii和iv组成,圆形喷丝孔i~iv的圆心分别位于正方形的四条边的中点上,圆形喷丝孔i~iv的直径相同都为0.14mm,圆形喷丝孔i和ii的间距为0.08mm;圆形喷丝孔i~iv的长径比相同都为4;相邻两个单位喷丝组合孔的间距为7.6mm;
77.两种不同的高聚物熔体分别是特性粘度为0.58dl/g的pet熔体和特性粘度为0.8dl/g的pet熔体,一种从圆形喷丝孔i和ii中挤出,另一种从圆形喷丝孔iii和iv中挤出;复合纺丝的纺丝温度(即喷丝板处熔体熔融挤出温度)为298℃;
78.冷却固化采用环吹风装置冷却成形,环吹风的温度为19℃,相对湿度为82%,压强为750pa;
79.集束上油采用油嘴上油,出油孔为扁平孔。
80.制得的双组份弹性复合纤维的卷曲拉伸率为38.4%,卷曲弹性回复率为75.3%,断裂强度cv%为 3.68,断裂伸长cv%为4.42,含油率为0.48%;喷丝板的清板周期为32h。
81.实施例5
82.一种双组份弹性复合纤维的制备方法,具体过程如下:
83.将两种不同的高聚物熔体进行复合纺丝制得双组份弹性复合纤维;
84.整体工艺流程为:熔融挤出
→
冷却固化
→
集束上油
→
卷绕成型;
85.其中,复合纺丝所用的喷丝板上设有72个单位喷丝组合孔;各个单位喷丝组合孔由一组相对的圆形喷丝孔i和ii以及另一组相对的圆形喷丝孔iii和iv组成,圆形喷丝孔i~iv的圆心分别位于正方形的四条边的中点上,圆形喷丝孔i~iv的直径相同都为0.13mm,圆形喷丝孔i和ii的间距为0.09mm;圆形喷丝孔i~iv的长径比相同都为3;相邻两个单位喷丝组合孔的间距为8.3mm;
86.两种不同的高聚物熔体分别是特性粘度为0.6dl/g的pet熔体和特性粘度为0.9dl/g的pet熔体,一种从圆形喷丝孔i和ii中挤出,另一种从圆形喷丝孔iii和iv中挤出;复合纺丝的纺丝温度(即喷丝板处熔体熔融挤出温度)为300℃;
87.冷却固化采用环吹风装置冷却成形,环吹风的温度为18℃,相对湿度为85%,压强为650pa;
88.集束上油采用油嘴上油,出油孔为扁平孔。
89.制得的双组份弹性复合纤维的卷曲拉伸率为41.2%,卷曲弹性回复率为84.8%,断裂强度cv%为 3.08,断裂伸长cv%为3.85,含油率为0.52%;喷丝板的清板周期为40h。
再多了解一些
本文用于企业家、创业者技术爱好者查询,结果仅供参考。