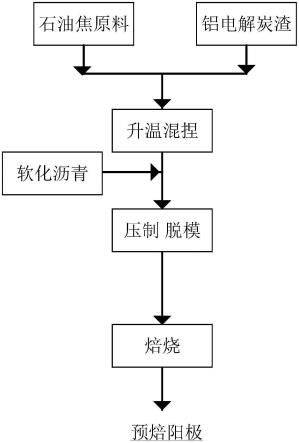
1.本发明属于有色冶金环保技术领域,具体涉及一种铝电解炭渣资源化利用的方法。
背景技术:
2.na3alf
6-al2o3熔盐电解法作为当代工业唯一的金属铝生产方法,普遍采用预焙阳极电解槽,炭阳极在承担着导电作用的同时也参与反应。目前国际上每生产1t铝消耗大约400kg阳极,这与理论消耗值334kg有着巨大的差距;多消耗的阳极一部分进入电解质体系形成炭渣。据统计每生产1t铝产生大约10kg炭渣。这些炭渣影响电解质体系,造成电能消耗增加,因此不得不将其打捞出来。打捞后的炭渣也是含有较多的氟化物,被列为危险废弃物,对环境有着巨大危害。铝电解炭渣处理和资源化利用成为亟待解决的问题。
3.炭渣的处理问题是铝工业发展中不可忽视的问题,对于炭渣的处理问题目前普遍采用的方法的思路都是将其中的碳质与氟化物分离,分离后分别利用;目前主要采用的炭渣处理方法有以下几种:浮选法、焙烧法、真空蒸馏法;炭渣中碳质和电解质结合方式有多种,有简单的结合、有互相包裹、还有一部分炭渣来自阴极,其中碳质部分石墨化程度高,碳质与电解质结合方式为电解质渗透进入碳质,较难分离。浮选法可将两种简单结合的炭渣分离,但存在电解质回收率低,回收的电解质含碳量高的缺点;焙烧法利用高温将炭渣中的碳质氧化生成气体排出,留下电解质部分,但会伴随着氟化物的排放,和碳质部分无法利用的两大问题;真空蒸馏法相较于浮选法能够较好的将碳质与电解质分离,但依然会有部分al2o3留在未被蒸馏的碳质之中,且成本较高,大规模利用依然需要进一步研究。无论是直接焙烧法、浮选法都有着分离效果较差,循环利用难度大的缺点。真空蒸馏法虽分离效果较好但成本远高于资源重新利用产生的价值。阳极添加剂的研究取得了一定进展,有研究表明na2co3、naf、na3alf6、caf2对氧化有催化作用。这些组分在炭渣中都可以找到,这也是炭渣组分较难分离的原因之一。中国专利(cn110284157b)公开了一种阳极炭渣和铝电解质回收利用方法,在上述方法中,将炭渣与含钙含碱物质混合后研磨焙烧,再对焙烧产物碱液浸出。回收了电解质中的钠、氟、铝、锂等元素,但对于炭渣中的碳质部分没有很好回收利用。
4.中国专利(cn111217356a)公开了一种从铝电解阳极炭渣中回收多孔炭的方法,在上述方法中,将铝电解阳极炭渣、浓硫酸和氧化剂按照一定比例混合后经过2次焙烧最终得到多孔炭材料,该方法对于炭渣中的电解质部分利用不充分。
5.炭渣作为铝电解体系产生的废弃物,其主要组成与铝电解体系完全相同,主要成分为碳质与电解质,电解质与碳质结合较为紧密完全分离难度大,作为主要组分的碳质部分有相当的潜力回归铝电解预焙阳极的制造当中;含氟化盐的炭渣替代部分石油焦用于阳极生产,碳质部分继续起到导电和还原铝的作用,电解质部分进入铝电解体系不污染电解质的同时,还能补充部分电解质的消耗,其中含有的部分具有催化氧化反应的组分,可以催化石油焦和炭渣中碳质部分的氧化,减小不同组分间的氧化性差异,减少阳极掉渣情况的发生。
技术实现要素:
6.本发明的目的是提供一种铝电解炭渣资源化利用的方法,采用不同粒度的石油焦与铝电解炭渣混合加热,再加入沥青,浸润后取出压制,释放内应力后焙烧制成预焙阳极。
7.本发明的方法按以下步骤进行:
8.(1)准备大颗粒石油焦、中颗粒石油焦、小颗粒石油焦和细粉石油焦作为石油焦原料;
9.(2)准备铝电解炭渣;
10.(3)将沥青加热至软化点温度,制成软化沥青;
11.(4)将石油焦原料与铝电解炭渣混合后,置于混捏机中开始升温搅拌;当温度升至120
±
1℃时,加入软化沥青,继续升温搅拌;当温度升至125
±
1℃时,将混捏机中的物料取出,置于模具中进行压制,然后脱模静置释放内应力,获得生坯料;
12.(5)将生坯料焙烧制成预焙阳极。
13.上述的步骤(1)中,大颗粒石油焦的粒径d1为3.9mm≤d1≤7.8mm,中颗粒石油焦的粒径d2为2.17mm≤d2《3.9mm,小颗粒石油焦的粒径d3为1.63mm≤d3《2.17mm,细粉石油焦的粒径d3《1.63mm。
14.上述的步骤(1)中,石油焦原料中按质量百分比大颗粒石油焦占20~30%,中颗粒石油焦占20~30%,小颗粒石油焦占10~15%,细粉石油焦占25~50%。
15.上述的步骤(4)中,石油焦原料与含氟炭渣的混合比例按质量比为石油焦原料:含氟炭渣=(8~12):1。
16.上述的步骤(4)中,软化沥青的加入量为石油焦原料总质量的15~20%。
17.上述的步骤(4)中,进行压制时,控制压制压力35~45mpa,保压时间4~8min。
18.上述的步骤(4)中,脱模静置时间至少10h。
19.上述的步骤(5)中,将生坯料置于坩埚电阻炉内,再用石油焦原料将生坯料和坩埚电阻炉之间的空隙填满压实,以防止生坯料被氧化,并减少重力作用下的变形。
20.上述的步骤(5)中,焙烧温度为1050
±
20℃,时间为12~16h。
21.上述的步骤(1)中,大颗粒石油焦、中颗粒石油焦、小颗粒石油焦和细粉石油焦为煅后石油焦。
22.上述的步骤(2)中,铝电解炭渣按质量百分比含c 28~33%、氟盐55~59%、al2o
3 5~7%、其中氟盐的主要成分为na3alf6,或者为na3alf6和caf2。
23.上述的步骤(3)中,沥青为改制煤沥青。
24.本发明的方法有效解决了对于炭渣的回收利用困难的问题,添加含氟的铝电解炭渣,使阳极充分利用炭渣中的碳质和电解质组分,两者各司其职,产生有益效果。
附图说明
25.图1为本发明的铝电解炭渣资源化利用的方法流程示意图。
具体实施方案
26.本发明实施例中采用的煅后石油焦按质量百分比含s 0.22%,灰分0.2%,挥发分0.6%,v 0.012%;真比重2.6、比电阻430ω
·
cm。
27.本发明实施例中的改制煤沥青的软化温度为110℃。
28.下面结合实施例来说明本发明的具体实施方式,实施例仅用来解释本发明,不以任何方式限制本发明,本发明的保护范围应包括权利要求的全部内容。
29.实施例1
30.流程如图1所示;
31.准备大颗粒石油焦、中颗粒石油焦、小颗粒石油焦和细粉石油焦作为石油焦原料;大颗粒石油焦、中颗粒石油焦、小颗粒石油焦和细粉石油焦为煅后石油焦;石油焦原料中按质量百分比大颗粒石油焦占25%,中颗粒石油焦占25%,小颗粒石油焦占13%,细粉石油焦占37%;大颗粒石油焦的粒径d1为3.9mm≤d1≤7.8mm,中颗粒石油焦的粒径d2为2.17mm≤d2《3.9mm,小颗粒石油焦的粒径d3为1.63mm≤d3《2.17mm,细粉石油焦的粒径d3《1.63mm;
32.准备铝电解炭渣;铝电解炭渣按质量百分比含c 30%、氟盐56%、al2o
3 6%、其中氟盐的主要成分为na3alf6,或者为na3alf6和caf2;
33.将沥青加热至软化点温度,制成软化沥青;沥青为改制煤沥青;
34.将石油焦原料与铝电解炭渣混合后,置于混捏机中开始升温搅拌;当温度升至120
±
1℃时,加入软化沥青,继续升温搅拌;当温度升至125
±
1℃时,将混捏机中的物料取出,置于模具中进行压制,然后脱模静置释放内应力,获得生坯料;石油焦原料与含氟炭渣的混合比例按质量比为石油焦原料:含氟炭渣=10:1;软化沥青的加入量为石油焦原料总质量的15%;进行压制时,控制压制压力40mpa,保压时间6min;脱模静置时间10h;
35.将生坯料置于坩埚电阻炉内,再用石油焦原料将生坯料和坩埚电阻炉之间的空隙填满压实,以防止生坯料被氧化,并减少重力作用下的变形;将生坯料焙烧制成预焙阳极,焙烧温度为1050
±
20℃,时间为12h。
36.实施例2
37.方法同实施例1,不同点在于:
38.(1)石油焦原料中按质量百分比大颗粒石油焦占30%,中颗粒石油焦占30%,小颗粒石油焦占15%,细粉石油焦占25%;
39.(2)铝电解炭渣按质量百分比含c 28%、氟盐57%、al2o
3 5%、其中氟盐的主要成分为na3alf6,或者为na3alf6和caf2;
40.(3)石油焦原料与含氟炭渣的混合比例按质量比为石油焦原料:含氟炭渣=11:1;软化沥青的加入量为石油焦原料总质量的16%;进行压制时,控制压制压力35mpa,保压时间8min;脱模静置时间11h;
41.(4)焙烧时间为13h。
42.实施例3
43.方法同实施例1,不同点在于:
44.(1)石油焦原料中按质量百分比大颗粒石油焦占20%,中颗粒石油焦占20%,小颗粒石油焦占10%,细粉石油焦占50%;
45.(2)铝电解炭渣按质量百分比含c 33%、氟盐59%、al2o
3 5%、其中氟盐的主要成分为na3alf6,或者为na3alf6和caf2;
46.(3)石油焦原料与含氟炭渣的混合比例按质量比为石油焦原料:含氟炭渣=9:1;软化沥青的加入量为石油焦原料总质量的17%;进行压制时,控制压制压力45mpa,保压时
间4min;脱模静置时间12h;
47.(4)焙烧时间为14h。
48.实施例4
49.方法同实施例1,不同点在于:
50.(1)石油焦原料中按质量百分比大颗粒石油焦占22%,中颗粒石油焦占26%,小颗粒石油焦占14%,细粉石油焦占38%;
51.(2)铝电解炭渣按质量百分比含c 31%、氟盐55%、al2o
3 5%、其中氟盐的主要成分为na3alf6,或者为na3alf6和caf2;
52.(3)石油焦原料与含氟炭渣的混合比例按质量比为石油焦原料:含氟炭渣=12:1;软化沥青的加入量为石油焦原料总质量的18%;进行压制时,控制压制压力35mpa,保压时间8min;脱模静置时间12h;
53.(4)焙烧温时间为15h。
54.实施例5
55.方法同实施例1,不同点在于:
56.(1)石油焦原料中按质量百分比大颗粒石油焦占27%,中颗粒石油焦占24%,小颗粒石油焦占12%,细粉石油焦占37%;
57.(2)铝电解炭渣按质量百分比含c 29%、氟盐58%、al2o
3 7%、其中氟盐的主要成分为na3alf6,或者为na3alf6和caf2;
58.(3)石油焦原料与含氟炭渣的混合比例按质量比为石油焦原料:含氟炭渣=8:1;软化沥青的加入量为石油焦原料总质量的19%;进行压制时,控制压制压力45mpa,保压时间4min;脱模静置时间12h;
59.(4)焙烧时间为16h。
60.实施例6
61.方法同实施例1,不同点在于:
62.(1)石油焦原料中按质量百分比大颗粒石油焦占21%,中颗粒石油焦占21%,小颗粒石油焦占11%,细粉石油焦占47%;
63.(2)铝电解炭渣按质量百分比含c 32%、氟盐58%、al2o
3 7%、其中氟盐的主要成分为na3alf6,或者为na3alf6和caf2;
64.(3)石油焦原料与含氟炭渣的混合比例按质量比为石油焦原料:含氟炭渣=11:1;软化沥青的加入量为石油焦原料总质量的20%;进行压制时,控制压制压力35mpa,保压时间8min;脱模静置时间11h;
65.(4)焙烧时间为16h。
66.实施例7
67.采用实施例1和实施例2的预焙阳极进行co2反应性试验,并采用不含有含氟炭渣的阳极作为对比例进行co2反应性试验;反应中阳极中的部分碳质会与co2发生反应生成co,表现为阳极消耗和部分阳极组分掉渣现象;
68.试验结果,对比例的阳极w
rar
(残极率)73.12%,w
rad
(脱落率)10.42%,w
ral
(损失比)16.45%;
69.实施例2的阳极w
rar
(残极率)85.32%,w
rad
(脱落率)4.11%,w
ral
(损失比)10.57%;
70.实施例1的阳极w
rar
(残极率)90.76%,w
rad
(脱落率)4.0%,w
ral
(损失比)5.2%;
71.证明炭渣的加入使得阳极的co2反应性有所下降,这是因为炭渣中的碳质相较于石油焦和沥青石墨化程度更高,炭渣的加入使得预焙阳极的整体co2反应性降低,在电解过程中会更少掉渣,使得阳极寿命更长。
72.实施例8
73.采用实施例2的预焙阳极进行熔盐电解,熔盐为na3alf
6-al2o3熔盐,采用分子比2.3的电解质体系;将阳极利用螺纹导杆连接到电解体系,电解温度为960℃,电流密度0.6a/cm2,极距2cm;待到体系稳定,将直流稳压电源接通开始铝电解;电解进行一段时间之后将数字万用表接入电解体系,利用数字万用表对电解时的电流和槽电压进行监测;
74.结果显示,电解过程槽电压较为稳定,只在小范围内波动,说明阳极在电解过程中较为稳定;证明阳极在铝电解生产中性能较为良好。
75.以上结合具体实施方式描述了本发明的技术原理,用于解释本发明,不能解释为对本发明保护范围的限制;本领域技术人员不需要付出创造性劳动即可联想到本发明的其它方式,都将落入本发明保护范围之内。
再多了解一些
本文用于企业家、创业者技术爱好者查询,结果仅供参考。