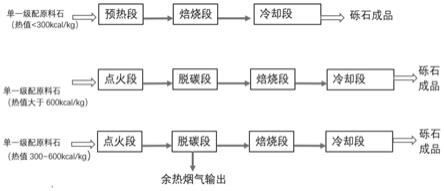
1.本发明属于固废资源化利用、节能减排和砾石制备领域,具体涉及一种利用固废制备砾石的方法。
背景技术:
2.现有利用固废制备陶粒或砂石料的技术基于原料粉磨和造粒工艺。通常对原料配料、粉磨、加水造粒、干燥、烧制等工艺。这些工艺中,原料配料过程需要加入塑性较好的原料,并充分粉磨一定细度,以保证造粒颗粒强度;同时,颗粒造粒过程加入8-15%的水,由此需要在后续烧制工艺中,首先需要干燥;干燥过程为了防止颗粒爆裂,还需要较慢的升温速度和脱水速度。这不仅消耗大量的能量,还限制了产品生产的节奏。减少工艺环节,提高生产节奏,降低能量消耗,是利用固废制备陶粒技术的关键。
技术实现要素:
3.本发明解决的技术问题是提供一种制备砾石的方法,该方法通过对原料的颗粒特性加以利用,对颗粒粒径满足砂石或陶粒标准的这部分原料,直接筛选出合格的粒径进行焙烧,能够减少粉磨和造粒环节,并获得形状不同,有棱角的砾石,从而实现对含粘土类矿物的固废原料的高效经济、节能低碳利用。
4.发明人长期研究发现,对于本发明的含有粘土类矿物的固废原料,如煤矸石、气化渣、流化床灰渣、页岩、油页岩、渣土、岩屑、含油岩屑或尾矿等,可以单独煅烧并形成强度,无需添加任何其他辅料。同时,对于造粒的陶粒,因为其形状多为圆形,这在混凝土中不利于其性能。
5.发明人还发现,这些原料如果不经过造粒工艺,其含水量低,特别是自由水含量低并且颗粒强度高,因此无需干燥过程,可以对原料快速升温,直接进入到余热或者点火燃烧阶段,颗粒并不会发生爆裂等问题。
6.为实现上述目的,本发明提供如下技术方案:
7.一种制备砾石的方法,所述方法包括:
8.将原料石进行破碎或者直接将原料石筛选后,获得粒径范围在4-90mm的原料石颗粒;然后,将所述原料石颗粒按照热值不同进行二次筛选,针对不同热值的所述原料石颗粒,采用分段焙烧进行焙烧后获得砾石。
9.作为本发明的一个实施例,所述分段焙烧包括:
10.对热值不超过300kcal/kg的原料石颗粒,使所述粒径范围在4-90mm的原料石颗粒根据砂石粒径需求进行分级,分级后原料石颗粒分批进入窑炉内进行烧制;
11.所述烧制的条件为:使分级后的单一粒级颗粒进入窑炉预热区进行布料,并在预热区内预热至300~700℃后进入焙烧区,然后在700~1180℃焙烧15-120min,随后冷却至70~150℃,即得砾石产品;
12.焙烧所用窑炉选自无需干燥工艺段的回转窑、焙烧窑、烧结窑或带式焙烧机。
13.作为本发明的一个实施例,所述分段焙烧包括:
14.对热值高于或等于300kcal/kg并且低于500kcal的原料石颗粒,使所述粒径范围在4-90mm的原料石颗粒根据砂石粒径需求进行分级,分级后原料石颗粒分批进入窑炉内进行烧制;
15.所述烧制的条件为:使分级后的单一粒级颗粒进入窑炉点火区进行布料,点火温度为1000~1200℃,然后使点火后的原料石颗粒进入脱碳区,脱碳温度为700~1000℃,脱碳时间为20~120min,脱碳后进入焙烧区并在950~1150℃下焙烧10~60min,随后冷却至70-150℃,即得砾石产品;
16.焙烧所用窑炉选自无需干燥工艺段,且增加了点火段的焙烧窑、烧结窑或带式焙烧机。
17.作为本发明的一个实施例,所述分段焙烧包括:
18.对热值高于或等于500kcal/kg的原料石,使所述粒径范围在4-90mm的原料石颗粒根据砂石粒径需求进行分级,分级后原料石颗粒分批进入窑炉内进行烧制;
19.所述烧制的条件为:使分级后的单一粒级颗粒进入窑炉点火区进行布料,点火温度1000~1200℃,然后使点火后的原料石颗粒进入脱碳区,脱碳温度为700~950℃,脱碳后进入焙烧区并在950~1150℃下焙烧10~60min,随后冷却至70-150℃;
20.优选地,在所述脱碳过程中对脱碳区的富余热量通过抽风抽出,进行余热输出利用,脱碳过程控制原料石脱碳温度低于950℃;
21.焙烧所用窑炉为无需干燥工艺段,且增加了点火段的焙烧窑、烧结窑或带式焙烧机,并且在700-950℃脱碳阶段存在余热烟气输出。
22.作为本发明的一个实施例,所述方法还包括:使所述脱碳后的原料石颗粒进入焙烧区,随后冷却至70-150℃;
23.所述焙烧区采用低温空气对原料石保温降温,而不需继续升温,不用供给燃料燃烧形成的950-1150℃高温烟气。
24.作为本发明的一个实施例,所述原料石中氧化硅的质量含量为40~70%,氧化铝的质量含量为12~30%;
25.优选地,所述原料石中氧化硅的质量含量为53~65%,氧化铝的质量含量为17~25%。
26.作为本发明的一个实施例,所述原料石包括煤矸石、气化渣、流化床灰渣、页岩、油页岩、渣土、岩屑、含油岩屑和尾矿中的一种或几种。
27.本发明提供的上述技术方案至少带来的有益效果:
28.1)、本发明无需现有陶粒制备工艺中混料、粉磨、造粒、干燥等过程,大大节省投资、降低成本;特别是避免粉磨能耗,避免造粒过程8-15%的水分消耗及烘干能耗;
29.2)、本发明制备的砾石有菱角、形状各异,改善了砾石陶粒的性能,避免了造粒过程导致的表面光滑,影响其在混凝土中的应用性能,使得制备的砾石更接近天然砂石,从而保证混凝土性能;
30.3)、本发明根据固废原料颗粒的热值分类,在焙烧过程直接将砾石送入快速升温的预热段,或者点火燃烧段,这将大大缩短制备时间,加快生产节奏;对于原来用于干燥段的热量或高热值原料焙烧形成的富裕热量,都可以进一步进行烟气余热输出利用,实现更
多的节能减排。
附图说明
31.图1为本发明的制备砾石的方法的工艺路线图。
具体实施方式
32.为使本发明的目的、技术方案和优点更加清楚,下面将对本发明实施方式作进一步地详细描述。
33.实施例1
34.采用本发明的方法制备砾石,具体步骤如下:
35.将煤矸石原料石进行破碎并筛选分级,获得粒径范围在10-30mm颗粒、30-50mm和50-70mm颗粒。这些煤矸石原料石的热值为478kcal/kg。将50-70mm颗粒送入固废焙烧窑的中间仓,然后进行布料送入窑车。窑车和原料石依次经过点火区,点火温度1100℃,点火后的原料石进入脱碳区,脱碳区出口温度为930℃,脱碳时间为30min,脱碳后进入焙烧区并在1050℃下焙烧15min,随后冷却至85℃排出。所制备的砾石筒压强度7.6mpa,满足轻集料国家标准(gb/t17431.1-2010)规定,筒压强度不得低于5.0mpa的要求。
36.实施例2
37.采用本发明的方法制备砾石,具体步骤如下:
38.将煤矸石原料石进行破碎并筛选分级,获得粒径范围在10-30mm颗粒和30-50mm颗粒。这些煤矸石原料石的热值为880kcal/kg。将10-30mm颗粒送入固废焙烧窑的中间仓,然后进行布料送入窑车。窑车和原料石依次经过点火区,点火温度1100℃,点火后的原料石进入脱碳区,脱碳区出口温度为950℃,脱碳时间为40min,脱碳后进入焙烧区并在1050℃下焙烧10min,随后冷却至85℃排出;同时从脱碳区抽出烟气温度为500~700℃,用于余热输出利用。所制备的砾石筒压强度6.6mpa,满足轻集料国家标准(gb/t17431.1-2010)规定,筒压强度不得低于5.0mpa的要求。
39.实施例3
40.将煤矸石原料石进行破碎并筛选分级,获得粒径范围在10-30mm颗粒、30-50mm和50-70mm颗粒。这些煤矸石原料石的热值为280kcal/kg。将30-50mm颗粒送入固废焙烧窑的中间仓,然后进行布料送入窑车。窑车和原料石依次经过预热区,预热至300~700℃后进入焙烧区并在1100℃焙烧40min,随后冷却至70~150℃。所制备的砾石筒压强度6.9mpa,满足轻集料国家标准(gb/t17431.1-2010)规定,筒压强度不得低于5.0mpa的要求。
41.实施例4
42.采用本发明的方法制备砾石,具体步骤如下:
43.将煤矸石原料石进行破碎并筛选分级,获得粒径范围在10-20mm颗粒和20-40mm颗粒。这些煤矸石原料石的热值为480kcal/kg。将20-40mm颗粒送入固废焙烧窑的中间仓,然后进行布料送入窑车。窑车和原料石依次经过点火区,点火温度1100℃,点火后的原料石进入脱碳区,脱碳区出口温度为930℃,脱碳时间为30min,脱碳后进入焙烧区保温并继续脱碳15min,无需高温焙烧升温,随后冷却至85℃排出。所制备的砾石筒压强度5.3mpa,满足轻集料国家标准(gb/t17431.1-2010)规定,筒压强度不得低于5.0mpa的要求。
44.以上所述仅为本发明的较佳实施例,并不用以限制本发明,凡在本发明的精神和原则之内,所作的任何修改、等同替换、改进等,均应包含在本发明的保护范围之内。
再多了解一些
本文用于企业家、创业者技术爱好者查询,结果仅供参考。