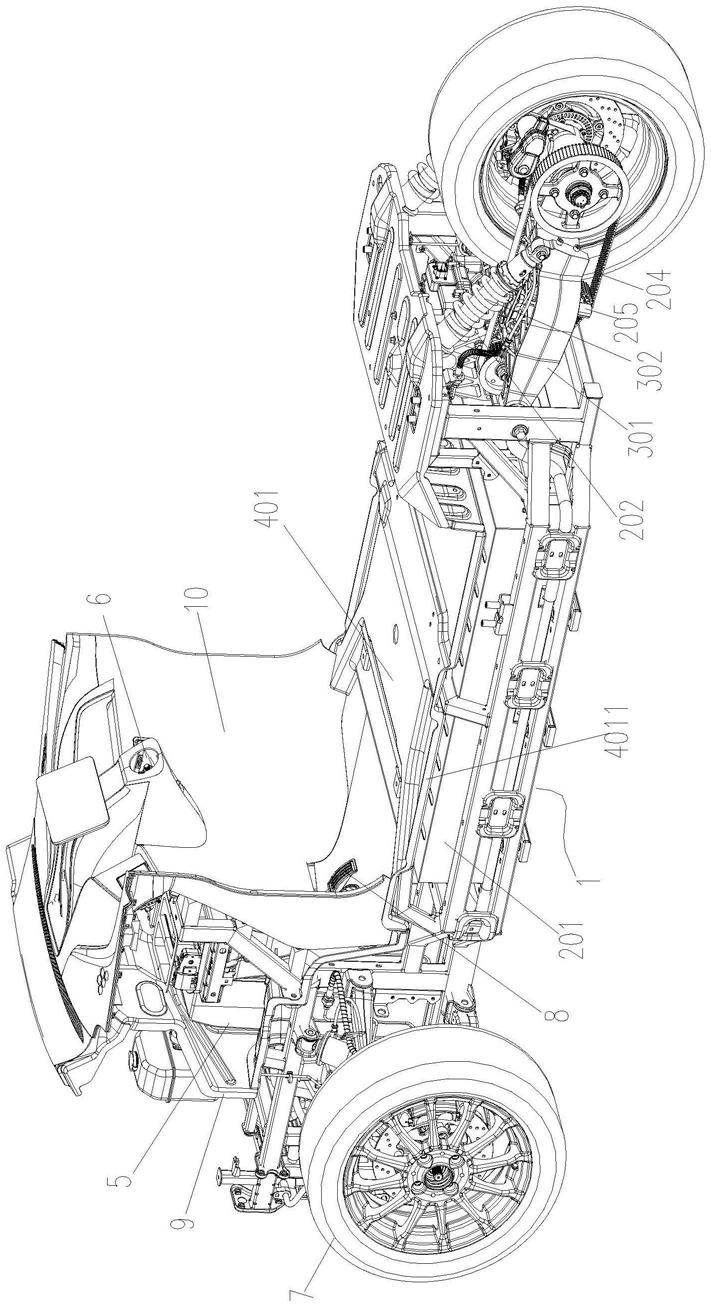
1.本发明涉及电动机动车技术领域,具体涉及一种倒三轮摩托车动力系统及倒三轮电动摩托车。
背景技术:
2.倒三轮摩托车与两轮摩托车或正三轮摩托车相比,不易侧翻,行驶稳定性更优秀,可为用户提供更安全舒适的驾驶体验。
3.现有技术的倒三轮摩托车由于前部具有两个车轮,动力系统一般包括控制器、驱动电机和变速器,安装底座一般在电机上,底座与车架通过若干相对于动力系统输出轴对称布置的螺栓进行固定,输出轴与底座形成悬臂结构;由于动力系统输出轴处于底座法兰面中心,在驱动时自身会产生以较大的扭矩施加在底座上,然后再传导于车架;需要实现大扭矩动力输出时,就需要增加动力系统壳体、底座以及车架相关安装结构的强度,这会造成零件重量增加,从而造成簧下重量增加,结构工艺复杂,装配工艺复杂和成本过高等问题。
4.因此,需要一种动力系统的安装结构,能够在驱动时分散扭矩作用于车架的作用点,避免大扭矩直接的集中的作用于车架,可有效减小动力系统安装点及车架的变形量,提高动力系统寿命;降低对结构强度的依赖,有助于产品轻量化;简化车架生产工艺,提升生产效率。
技术实现要素:
5.有鉴于此,本发明的目的是克服现有技术中的缺陷,能够在驱动时分散扭矩作用于车架的作用点,避免大扭矩直接的集中的作用于车架,可有效减小动力系统安装点及车架的变形量,提高动力系统寿命;降低对结构强度的依赖,有助于产品轻量化;简化车架生产工艺,提升生产效率。
6.本发明的倒三轮摩托车动力系统,所述动力系统安装在倒三轮摩托车的车架上,所述动力系统具有一将动力输出至摩托车后轮的动力输出轴,靠近动力输出轴设有轴侧安装座,尾侧设有尾侧安装座,且通过轴侧安装座和尾侧安装座安装在车架上;动力系统安装在车架上可避免现有技术的安装结构导致的簧下(悬挂)质量的增加,利于保证操控性和舒适性;
7.现有技术中,动力系统底座与车架通过若干相对于动力系统输出轴对称布置的螺栓进行固定,输出轴与底座形成悬臂结构;由于动力系统输出轴处于底座法兰面中心,在驱动时自身会产生以较大的扭矩施加在底座上,然后再传导于车架;需要实现大扭矩动力输出时,就需要增加动力系统壳体、底座以及车架相关安装结构的强度,这会造成零件重量增加,结构工艺复杂,装配工艺复杂和成本过高等问题;本发明中,轴侧和尾侧通过分开的安装座安装,可在驱动时分散扭矩作用于车架的作用点,避免大扭矩直接的集中的作用于车架,可有效减小动力系统安装点及车架的变形量,提高动力系统寿命;降低结构强度,有助于产品轻量化;简化车架生产工艺,提升装配效率。
8.进一步,所述轴侧安装座通过两个安装点与车架固定连接,尾侧安装座通过一个安装点与车架固定连接;所述轴侧安装座的两个安装点之间为非对称布置;通过非对称的且分开的安装座进行安装,可根据动力输出方向合理分配所产生的扭矩,从而具有针对性的受力,进一步减小安装座及车架相关位置的变形量,提高动力系统和车架寿命;进一步降低结构强度,有助于产品轻量化;简化车架生产工艺,提升装配效率。
9.进一步,所述轴侧安装座的两个安装点中,一个为下安装点靠下与车架固定连接,另一个为上安装点靠上与车架固定连接,尾侧安装座的安装点靠下与车架固定连接;分为上安装点和下安装点,将安装点分散至动力系统的周围,改变了现有的全部集中在底座上的结构,保证了安装支撑强度,避免了车架以及底座承受较大扭矩的技术问题。
10.进一步,所述动力系统安装于车架上靠后形成的后框架结构内,所述下安装点和尾侧安装座固定安装在后框架结构的下部,上安装点固定安装在后框架结构的上部;采用后框架结构用于安装动力系统,提升整体的承载强度,在支撑乘坐位的同时,提供动力系统的安装空间,并为动力系统的安装点分散提供条件
11.进一步,所述动力系统包括控制器、驱动电机和变速器,所述控制器、驱动电机和变速器集成为一体;所述控制器固定在所述驱动电机的顶部;所述变速器的输出轴为动力输出轴;集成为一体指的是控制器的外壳、驱动电机和变速器的外壳固定连接为一体,而且在设定条件下,外壳可部分一体成形形成共用,在此不再赘述;
12.所述轴侧安装座位于变速器的壳体,尾侧安装座靠下位于驱动电机壳体,且所述下安装点和尾侧安装座的安装点相对于所述动力输出轴的轴线靠后设置;
13.现有技术中,控制器与驱动电机一般采用分体式结构,采用线束控制连接,损耗高,降低系统效率;并且,使得整车装配复杂,布线问题以及由此产生电磁屏蔽问题;当然,现有技术也存在将电机控制器侧面装配在驱动电机上的技术方案,但安装在侧面的结构对于散热问题以及由于重心问题增加的震动等问题较难解决;本发明的结构避免驱动电机与控制器长距离连线而引起的电机相电阻增大,驱动系统效率低下的问题;电磁屏蔽在驱动电机与电机控制器的壳体上即可实现,隔绝外部异常信号对控制器本体的干扰,使得动力系统具有更高的体积密度,更低的效率损耗;将控制器位于电机正上方,优化了组件的重心,避免车辆振动导致的共振,从而避免电器部件的脱落,还利于整体的防水设计;
14.本发明的倒三轮的驱动轮为后轮驱动,在以后轮为驱动的结构中,下安装点和尾侧安装座位于轴线的一侧,动力输出轴的外圆高点的线速度背离该位置,输出动力的反作用扭矩对该安装点形成压力,保证安装的稳定性;同时,结合上安装点的设置,形成杠杆式约束,减轻动力扭矩对安装点的作用,从而保证了动力系统本身和车架的安装稳定性。
15.本发明还公开了一种倒三轮电动摩托车,所述倒三轮摩托车采用所述的倒三轮摩托车动力系统
16.本发明的有益效果是:本发明公开的一种倒三轮摩托车动力系统及倒三轮电动摩托车,动力系统安装在车架上可避免现有技术的安装结构导致的簧下(悬挂)质量的增加,利于保证操控性和舒适性;轴侧和尾侧通过分开的安装座安装,可在驱动时分散扭矩作用于车架的作用点,避免大扭矩直接的集中的作用于车架,可有效减小动力系统安装点及车架的变形量,提高动力系统寿命;降低结构强度,有助于产品轻量化;简化车架生产工艺,提升生产效率。
附图说明
17.下面结合附图和实施例对本发明作进一步描述:
18.图1为本发明的整车结构示意图;
19.图2为本发明的整车侧视图;
20.图3为动力系统安装结构示意图;
21.图4为动力系统轴向的立面剖视图;
22.图5为控制器的横向剖视图;
23.图6为动力系统轴测图(箭头所示为冷却液流向);
24.图7为控制器冷却流道示意图(俯视所看到的箭头所示为冷却液流向);
25.图8为驱动电机的轴测图(箭头所示为冷却液流向);
26.图9为车架爆炸图;
27.图10后摆臂结构示意图;
28.图11为后摆臂安装于车架结构示意图;
29.图12为张紧装置而机构示意图;
30.图13为张紧装置剖视图。
具体实施方式
31.如图1至图13所示,本发明的倒三轮摩托车动力系统,所述动力系统安装在倒三轮摩托车的车架1上,所述动力系统202具有一将动力输出至摩托车后轮的动力输出轴202a,靠近动力输出轴202a设有轴侧安装座,尾侧设有尾侧安装座,且通过轴侧安装座和尾侧安装座安装在车架1上;动力系统安装在车架上可避免现有技术的安装结构导致的簧下(悬挂)质量的增加,利于保证操控性和舒适性;
32.现有技术中,动力系统底座与车架通过若干相对于动力系统输出轴对称布置的螺栓进行固定,输出轴与底座形成悬臂结构;由于动力系统输出轴处于底座法兰面中心,在驱动时自身会产生以较大的扭矩施加在底座上,然后再传导于车架;需要实现大扭矩动力输出时,就需要增加动力系统壳体、底座以及车架相关安装结构的强度,这会造成零件重量增加,结构工艺复杂,装配工艺复杂和成本过高等问题;本发明中,轴侧和尾侧通过分开的安装座安装,可在驱动时分散扭矩作用于车架的作用点,避免大扭矩直接的集中的作用于车架,可有效减小动力系统安装点及车架的变形量,提高动力系统寿命;降低结构强度,有助于产品轻量化;简化车架生产工艺,提升装配效率。
33.如图所示,本发明还公开一种倒三轮电动摩托车,采用本实施例的动力系统,倒三轮包括车架1、悬挂系统和电驱动系统,所述车架1上设有驾驶位401,与所述驾驶位401相对应在摩托车上设置有操控踏板8,所述操控踏板8位于摩托车前轮7的横向投影的范围内;
34.当然,倒三轮电动摩托车还包括转向系统6、制动系统、电器仪表以及其他附属系统等,属于现有技术的系统结构,在此不再赘述;由于本发明采用将操控踏板8设置于前轮所在的范围的结构,则使得驾驶位相对于现有技术靠前,从而可缩短整车长度,利于提高整车的操控灵活性;操控踏板8一般包括刹车踏板、油门踏板(如果有)等,在此不再赘述。
35.所述电驱动系统布置于倒三轮的车架上,包括电池组201和本实施例的动力系统202,所述电池组201布置在车架1的中部位置,所述动力系统202布置于车架靠后的位置;电
池组201和动力系统202的布置结构,分散了整车的各个系统质心,从而在保证离地间隙的条件下调低整车质心,使得整车的灵活性、操控性和稳定性得到保证;动力系统靠后布置,可大大缩短传动驱动距离,提高传动效率。
36.本实施例中,所述操控踏板8位于摩托车前轮7轴线的后方,可以是后上、平齐或后下,结构上与驾驶位匹配度最高,更易于布置;同时,需要对车内仪表台10下方进行处理,即在操控踏板处形成向前的凹陷,该凹陷需要留出必要的操控空间,在此不再赘述。
37.如图1和图2所示,本实施例中,位于所述驾驶位401的后部还设有乘坐位402,拓展车辆使用范围的同时,由于驾驶位前移,使得整车的长度相对于现有同标准的车辆缩短,设置乘坐位能够保证双人驾乘时的重心相对靠前,从而保证操控灵活性、稳定性和安全性。
38.如图1和图2所示,本实施例中,所述驱动系统包括电池组201和动力系统202,所述动力系统202布置于车架1靠后的位置,且位于乘坐位的下部;动力系统202靠后布置,可大大缩短传动驱动距离,提高传动效率;位于乘坐位下部的布置方式,使得整车的布置具有较好的集中效果,利于保证整车的结构紧凑性,可有效控制整车长度,人机体验效果较好,同时,对于调整整车的质心位置提供了较好的前提条件。
39.如图1和图2所示,本实施例中,所述电池组201布置在车架1的中部位置,且电池组201靠前的部分位于所述驾驶位401的下部;驾驶位401、电池组201、动力系统202以及乘坐位402的布置结构,分散了整车的各个系统质心,从而在保证离地间隙的条件下调低整车质心,使得整车的灵活性、操控性和稳定性得到保证。
40.如图3所示,本实施例中,所述动力系统202具有一将动力输出至摩托车后轮的动力输出轴202a,靠近动力输出轴202a设有轴侧安装座,尾侧设有尾侧安装座,且通过轴侧安装座和尾侧安装座安装在车架1上,这里的尾侧指的是动力系统在轴向上远离动力输出轴的一侧(尾部);动力系统202安装在车架1上可避免现有技术的安装结构导致的簧下(悬挂)质量的增加,利于保证操控性和舒适性;
41.现有技术中,动力系统底座与车架通过若干相对于动力系统输出轴对称布置的螺栓进行固定,输出轴与底座形成悬臂结构;由于动力系统输出轴处于底座法兰面中心,在驱动时自身会产生以较大的扭矩施加在底座上,然后再传导于车架;需要实现大扭矩动力输出时,就需要增加动力系统壳体、底座以及车架相关安装结构的强度,这会造成零件重量增加,结构工艺复杂,装配工艺复杂和成本过高等问题;本发明中,轴侧和尾侧通过分开的安装座安装,可在驱动时分散扭矩作用于车架的作用点,避免大扭矩直接的集中的作用于车架,可有效减小动力系统安装点及车架的变形量,提高动力系统寿命;降低结构强度,有助于产品轻量化;简化车架生产工艺,提升装配效率。
42.如图3所示,本实施例中,所述轴侧安装座通过两个安装点2024、2026与车架1固定连接,尾侧安装座通过一个安装点2025与车架固定连接;所述轴侧安装座的两个安装点2024、2026之间为非对称布置(相对于动力输出轴202a的轴线);通过非对称的且分开的安装座进行安装,可根据动力输出方向合理分配所产生的扭矩,从而具有针对性的受力,进一步减小安装座及车架相关位置的变形量,提高动力系统和车架寿命;进一步降低结构强度,有助于产品轻量化;简化车架生产工艺,提升装配效率。
43.本实施例中,所述车架1用于安装动力系统的位置形成后框架结构,所述动力系统位于所述后框架结构内,轴侧安装座的两个安装点2024、2026中,一个为下安装点2024靠下
与车架1固定连接,另一个为上安装点2026靠上与车架1固定连接,尾侧安装座的安装点2025靠下与车架固定连接;分为上安装点和下安装点,将安装点分散至动力系统的周围,改变了现有的全部集中在底座上的结构,保证了安装支撑强度,避免了车架以及底座承受较大扭矩的技术问题。
44.所述乘坐位402安装于所述后框架结构的上部;
45.采用后框架结构用于支撑乘坐位并安装动力系统202,提升整体的承载强度,在支撑乘坐位的同时,提供动力系统的安装空间,并为动力系统的安装点分散提供条件。
46.如图6所示,本实施例中,所述动力系统202包括控制器2023、驱动电机2021和变速器2023,所述控制器2023、驱动电机2021和变速器2022集成为一体,集成为一体指的是控制器的外壳、驱动电机的外壳和变速器的外壳固定连接为一体,而且在设定条件下,外壳可部分一体成形形成共用,在此不再赘述;所述控制器2023固定在所述驱动电机2021的顶部;所述变速器2022的输出轴为动力输出轴202a(图中附图标记指的是传动配合设置于发动力输出轴的皮带轮,在此不再赘述);
47.现有技术中,控制器与驱动电机一般采用分体式结构,采用线束控制连接,损耗高,降低系统效率;并且,使得整车装配复杂,布线问题以及由此产生电磁屏蔽问题;当然,现有技术也存在将电机控制器侧面装配在驱动电机上的技术方案,但安装在侧面的结构对于散热问题以及由于重心问题增加的震动等问题较难解决;本发明的结构避免驱动电机与控制器长距离连线而引起的电机相电阻增大,驱动系统效率低下的问题;电磁屏蔽在驱动电机与电机控制器的壳体上即可实现,隔绝外部异常信号对控制器本体的干扰,使得动力系统具有更高的体积密度,更低的效率损耗;将控制器位于电机正上方,优化了组件的重心,避免车辆振动导致的共振,从而避免电器部件的脱落,还利于整体的防水设计;
48.所述轴侧安装座位于变速器2022的壳体,尾侧安装座靠下位于驱动电机壳体,且所述下安装点2024和尾侧安装座的安装点2025相对于所述动力输出轴202a的轴线靠后设置;本发明的倒三轮的驱动轮为后轮驱动,在以后轮为驱动的结构中,下安装点和尾侧安装座位于轴线的一侧,动力输出轴的外圆高点的线速度背离该位置,输出动力的反作用扭矩对该安装点形成压力,保证安装的稳定性;同时,结合上安装点的设置,形成杠杆式约束,减轻动力扭矩对安装点的作用,从而保证了动力系统本身和车架的安装稳定性。
49.如图4和图5所示,本实施例中,所述控制器2023包括防水外壳,所述防水外壳内形成主控腔20231和接线腔20232,所述主控腔20231用于安装控制电路板202310(一般为印刷电路板加上元器件,在此不再赘述),接线腔20232用于接入外部线路,所述控制电路板202310通过铜排20237与驱动电机2021电连接并控制驱动电机2021的运行状态;双腔的结构,可合理规划接线以及控制电路的布置,避免接线位置对控制电路的干扰影响;如图所示,接线腔20232位于靠上的位置,方便接线操作;主控腔20231位于靠下的位置,方便通过铜排与驱动电机电连接;控制器内的控制电路板上设有必要的电器元件,最终通过接线腔内接入外部线路,并通过铜排电连接驱动电机完成控制,在电学原理上属于现有技术,在此不再赘述。
50.如图4和图5所示,本实施例中,所述防水外壳包括底座20233、壳体20238和上盖20234,所述壳体20238密封固定于底座20233,密封的方式及根据不同的连接结构采用现有的静密封结构即可,比如密封垫、密封圈等,在此不再赘述;所述上盖20234密封固定于壳体
20238形成的接线腔20232的上部开口;所述控制器2023通过底座20233固定于驱动电机2021上部;所述控制电路板202310上的发热电器元件与壳体20238之间通过导热垫形成热传导过渡,如图5所示,控制电路板202310上设有电容202311,上部与壳体20238之间设有导热垫(一般为导热橡胶),一是可以利于散热,二是可以在振动时保护电容;所述主控腔20231与接线腔20232之间形成密封,形成独立的两个腔,避免互相干扰,特别是避免接线腔内进行操作的时候对主控腔20231内的控制电路板造成损坏或进水,密封的方式依然是采用现有技术的静密封方式,在接线柱穿出的位置形成密封;驱动电机2021的导线与铜排20237之间形成电连接并通过灌胶方式固定,属于现有技术的灌封方式,在此不再赘述;
51.如图4和图5所示,接线腔20232由壳体20238一体成形的隔板形成,接线腔20232底部设有用于通过接线柱20236的过孔(根据需要可以是一个或者若干个,一般为两个),接线柱20236设有一护套20235,护套20235穿过过孔且护套形成紧压过孔边缘的密封台阶面,可通过密封垫或密封圈形成密封,接线柱20236由下向上密封穿过护套20235,通过o型圈形成密封(本发明为沿轴向设置的两个),接线柱20236则用于连接控制电路202310和外部导线,在此不再赘述;密封方式则采用通常的密封圈、密封垫的结构,属于现有的密封结构,在此不再赘述。
52.如图10、图11、图12所示,本实施例中,所述驱动系统还包括后驱动轮203,所述驱动电机2021的驱动动力通过变速器2022由动力输出轴202a输出至后驱动轮203,所述后驱动轮203通过后悬挂组件3安装于车架1,所述后悬挂组件3包括后摆臂301和后减震组件,所述后摆臂301包括主摆臂3011,所述主摆臂3011前端以可使主摆臂3011单自由度上下摆动的方式铰接于车架1,主摆臂3011的后端向横向的内侧弯曲并形成用于安装后驱动轮的轴座3015;
53.后驱动轮203通过主摆臂3011安装在车架1上,主摆臂3011的主体位于车轮左侧,形成对后驱动轮203的连接支撑,前端铰接车架的方式可采用现有的平叉头管的交接方式,也可以是分为多个铰接点的铰接方式,在此不再赘述;主摆臂3011后端向内侧弯曲使得其端部靠近后驱动轮203,通过轴座支撑安装后驱动轮203,轴座安装后驱动轮的方式、结构以及润滑方式属于现有技术,在此不再赘述;向内侧弯曲指的是向摩托车中部弯曲,在此不再赘述;同时,由于其端部向内侧弯曲,还是得其端部可用于安装一些附属装置,比如刹车钳等等,在此不再赘述。
54.如图10、图11、图12所示,本实施例中,所述后摆臂301还包括在横向上与主摆臂并列的副摆臂3016,所述主摆臂3011上形成一横向水平延伸的摆臂横梁3014,所述副摆臂3016固定连接在摆臂横梁3014的水平延伸端部;所述减振组件包括两个减震器302、3021,两个所述减震器302、3021的下端分别对应铰接于主摆臂3011和副摆臂3016,上端分别铰接于车架1;
55.现有技术中,摩托车后摆臂为双臂结构或者单臂结构,对于质量较大的车型,维护后轮时的拆装工作,通常不易进行;单臂结构形式尺寸精度要求高,且因只能在单侧布置减震器,对结构设计及悬架匹配要求高,容易出现车辆左右支撑感不一致的情况;
56.主摆臂3011上位于摆臂横梁3014的前端形成两个横向并列的摆臂铰接点3012、3013,所述主摆臂3011通过两个所述摆臂铰接点3012、3013以可使主摆臂3011单自由度上下摆动的方式铰接于车架1,如图所示,两个摆臂铰接点3012、3013同轴且分列摩托车纵向
中心线的横向两侧,形成稳定的铰接结构;
57.本发明采用副摆臂3016固定在主摆臂3011上的结构,副摆臂位于车轮右侧,形成相对近似于对称安装减震器的两部分,可安装两个减震器302、3021,实现双后减震器布置,从而保证后悬架对车辆的左右支撑一致性,从而达到驾乘的舒适性和安全性的目的;同时,结合车辆轮胎作为易损件,其维护频次较高的问题,本发明对维护频次最高的后轮可单独拆卸,而不需对制动、传动部分进行操作。同时,通过设置辅助摆臂,避免了双摆臂的重量较大、维护后轮时的拆装复杂的问题,对于质量较大的摩托车,本发明不但能够起到双摆臂结构的稳定性、舒适性效果,还具有单摆臂的灵活性和后轮维护的拆装便利性。
58.如图10所示,本实施例中,所述轴座3015上设有功能性安装位30151,功能性安装位30151主要用于制动系统的部件安装(制动钳等);两个所述摆臂铰接点3012、3013的铰接轴线与所述变速器2022的动力输出轴202a同轴,在摆臂摆动过程中可使得传动链条或者皮带的传动轴心距离不变,避免长度变化,从而保持传动的稳定性,以及提升零件使用寿命;所述动力输出轴通过同步带传动或者链传动将动力传递至后轮203,本实施例中,采用同步带传动,则具有同步带副204,包括传动设置于动力输出轴202a上的主动皮带轮、同步带和传动设置于后驱动轮上的从动皮带轮,在此不再赘述;
59.两个所述减震器302、3021上端铰接于车架1的后框架结构,如图11所示,整体上结构简单紧凑,设计较为巧妙,后框架结构用于支撑乘坐位、安装动力系统并且还为减震器提供安装基础,避免了现有技术的复杂结构,降低车架重量。
60.如图12、图13所示,本实施例中,所述后摆臂301上设有用于同步带或链张紧的张紧组件205;
61.所述张紧组件205包括张紧座2054、张紧螺杆2053、张紧件2052和张紧轮2051,所述张紧座2054固定设置于主摆臂3011,张紧螺杆2053以可在圆周方向单自由度往复转动的方式设置在张紧座2054,如图所示,张紧螺杆在长度方向上被限定在张紧座2054上,采用限位凸台20531限制其向上的结构,且螺杆上端转动配合穿出张紧座2054上的过孔,利于张紧操作,在此不再赘述;所述张紧件2052螺纹配合设置于张紧螺杆2053且可被张紧螺杆2053驱动沿同步带或链张紧的方向往复运动,当然,张紧件2052需要被限定横向(螺杆的横向)的自由度;所述张紧轮2051通过一与其转动配合的张紧轮轴2055设置于张紧件2052并与同步带或链形成张紧配合,本实施例采用的为同步带,则张紧轮从内侧对同步带形成张紧,当然,张紧轮也需采用同步带轮的结构,带有啮合齿,在此不再赘述;
62.现有技术中,张紧件多为自张紧形式,如压簧式、扭簧式、偏心轴套式等,此类张紧装置结构相对复杂,成本相对较高,长期使用后易出现张紧力变化,不能保证皮带在最佳条件下工作;本发明采用上述结构,张紧装置安装在主摆臂上,通过螺纹连接并调整张紧状态,稳定而调整方便;
63.本发明中,张紧轮设计在主摆臂,在维修拆卸轮胎时,皮带或链条保持张紧状态,更换轮胎时不需要再次调节张紧力。
64.如图12、图13所示,本实施例中,所述主摆臂3011的内侧设有竖直的张紧槽30111,所述张紧座2054可拆卸式固定设置于所述张紧槽30111的上端,所述张紧件2052与所述张紧槽30111之间形成可单自由度往复运动的滑块配合副,本实施例中张紧槽与张紧件2052(一般为条形,具有足够的张紧距离)之间采用滑块配合副,(可采用燕尾槽或者t形槽结构
配合);所述张紧轮轴2055沿水平方向向内侧延伸,即向着同步带所在的方向延伸,(这里的内侧指的是摩托车车架的纵向中线的一侧);利用主摆臂3011设置张紧槽30111和张紧件2052的配合,形成导向机构及顶部张紧座形成限位机构(螺杆上的限位凸台),通过简单稳定的螺纹连接,实现皮带张紧力的调节,结构简单,调节方便且成本较低。
65.本实施例中,所述车架1由前部车架101、中部车架102和后部车架103依次固定连接形成,所述前部车架101形成前框架结构,中部车架102形成中框架结构,所述后部车架103形成后框架结构;
66.现有技术中,三轮摩托车车架多为含有车门框架和车顶框架的整体焊接结构,其生产工艺复杂,尺寸保证困难,装配精度较低,且车架结构多无法满足大容量电池带来的强度、刚度等需求,只有增加尺寸来满足要求,导致车辆重量大,能耗较高;本发明采用三段式结构,通过三个模块连接成整体车架,合理布置各个系统所在的车架模块,从而受力承载形成有效地分散,使得整车重心得到较好的调整,从而实现轻量化车架的同时保证支撑强度,降低能源消耗。
67.本实施例中,所述前部车架101设有多个前部功能安装位,至少包括用于安装前轮悬架、转向机构和空调组件的安装位;中部车架102设有多个中部功能安装位,至少包括用于安装所述电池组201和驾驶位401的安装位;所述后部车架103设有多个后部功能安装位,至少包括用于安装所述动力系统202和乘坐位402的安装位。
68.如图1、图2和图9所示,前部车架101设置有前悬架、转向、制动、散热、电器等系统的安装机构;中部车架102安装大容量动力电池组201,电池组201由下向上装配在中部车架,能够得到有效保护,并能降低整车质心高度,保证车辆行驶稳定性;同时驾驶位位于中部车架靠前的位置,上下部分与电池组重叠;后部框架设置有驱动系统及后悬架安装部位,从而使得整车的各个系统以及部件有针对性的分散在车架1上,有效调整车架的受力承载,保证整车的稳定性和安全性。
69.如图9所示,本实施例中,所述前部车架101包括两个横向并列的下部前纵梁1011、1012和分别对应位于两个下部前纵梁上部的两个上部前纵梁1013、1014,两个上部前纵梁1013、1014和两个下部前纵梁1011、1012之间通过固定连接形成前框架结构,当然,两个上部前纵梁和两个下部前纵梁为主体,通过设定的竖向及横向支撑形成框架结构,整体具有较高的稳定性;所述中部车架102包括两个横向并列的下部中纵梁1021、1022和分别对应位于两个下部中纵梁1021、1022上部的两个上部中纵梁1023、1024,两个上部中纵梁1023、1024和两个下部中纵梁1021、1022之间通过固定连接形成中框架结构,同理,形成框架则需要设定合理的竖向和横向支撑,在此不再赘述;所述后部车架103包括两个横向并列的下部后纵梁1031、1032和分别对应位于两个下部后纵梁1031、1032上部的两个上部后纵梁1033、1034,两个上部后纵梁1033、1034和两个下部后纵梁1031、1032之间通过固定连接形成所述后框架结构,同理,形成框架则需要设定合理的竖向和横向支撑,在此不再赘述;
70.所述电池组201固定安装在中框架结构内;如图所示,电池组201向下不超过两个下部中纵梁1021、1022底边,对电池组形成有效保护,并有效降低整车质心,利于保证行驶安全性;当然,所述中框架结构内设有用于安装摩托车电池组的安装位,且所述安装位靠前的部分位于驾驶位支撑架下部,在此不再赘述。
71.车架1整体上分为三段式框架结构,其结构强度刚度高,增加了车架的稳定性和承
1036;
81.两个所述上部后纵梁1031、1032的前端之间通过后上横梁ⅰ10315固定连接,后端之间通过后上横梁ⅱ10314固定连接;后上横梁ⅰ10315和后上横梁ⅱ10314之间固定连接设有功能性纵梁1037,所述动力系统的上安装点安装于所述功能性纵梁,下安装点2024以及尾侧安装座的安装点2025安装于所述后下横梁ⅱ1036;
82.所述后下横梁ⅰ1035与两个所述后竖梁1039、10310之间分别对应设有一个后斜撑10313、10314;后上横梁ⅰ10315与后下横梁ⅰ1035之间在靠近两端的位置分别固定连接设有一个后竖撑10311、10312;
83.两个所述上部中纵梁1023、1024的上部固定设有驾驶位支撑架4011,所述驾驶位支撑架4011为横跨两个所述上部中纵梁的框架结构且通过四脚固定连接于两个所述上部中纵梁1023、1024;用于安装驾驶位401,同时对中部车架起到加固作用;
84.两个所述减震器302、3021上端铰接于所述后上横梁ⅱ10314;主摆臂3011的两个所述摆臂铰接点3012、3013分别对应铰接于两个所述后竖梁1039、10310;
85.通过上述结构设定,前部车架、中部车架和后部车架分别形成完整的框架结构模式,且连接成车架后整体上也为框架结构,框架结构不但具有加强功能,还具有安装其他部件的功能性结构,从而使得车架不但在较为简单的结构上实现加强功能,还整齐有序的安装车身部件,获得较高的结构强度及刚度,框架结构还是得被安装的设备部件能够得到有效保护,比如电池组和动力系统等,并能降低整车质心高度,保证车辆行驶稳定性。
86.如图1、图2所示,本实施例中,所述空调组件5位于摩托车前围板9与摩托车仪表台10之间设置于前部车架101;
87.所述空调组件5位于前部车架101偏左的位置;
88.现有技术中,封闭式三轮摩托车的制冷装置多布置于车辆顶棚,此种方式会影响人员头部空间,且带来外观商品性较差的问题;本发明将空调装置布置于前部车架,当然,在仪表台上需设置出风口;从结构上看,空调组件布置于车辆内部,通过密闭管路与压缩机、冷凝器等零部件连接,避免防水防尘问题;
89.空调组件5布置于车辆前围板9与仪表台10之间,空调箱由内外饰零件完全遮挡,不对外观商品性造成影响;
90.空调组件5布置于操纵踏板8靠前的上部(前部车架左侧,位于操纵踏板上部),不影响人员操作,获得舒适的人机体验。
91.本实施例中,所述动力系统202为水冷动力系统;
92.所述控制器2023和驱动电机2021分别设有各自的冷却水流道,且控制器2023的冷却流道与驱动电机2021的冷却流道相连通;相互连通整体上形成串联或者并联的冷却通道,利于形成冷却循环,从而实现较好的冷却效果。
93.本实施例中,如图6所示,所述控制器2023的冷却流道与驱动电机2021的冷却流道串联,冷却液由控制器的冷却流道流入,最终由驱动电机的冷却流道流出;整体上形成大循环,较好的提高冷却效果,简化水路连接;结合驱动电机布置于控制器正下方的结构,在考虑散热性能的同时,冷却液从控制器流入,驱动电机流出,有效避免电机的高温冷却液对电机控制器的热辐射,提升系统热稳定性;
94.如图6、图7所示,控制器2023的冷却流道包括控制器冷却液进口20241、控制器冷
却区域20242和控制器冷却液出口20243,所述控制器冷却区域20242为多条水道散射状并联或串联加宽的冷却结构,多条水道的冷却液汇集于控制器冷却液出口流出;散射状指的是由进口形成呈放射状分布的多条分支且分散拓宽,可由并联和串联结构相结合的结构形式形成;如图所示,控制器结构内部冷却区域采用串并联均流设计,在冷却区域可形成分流或者汇流,调整水道宽度做最大限度得覆盖,且在分流水道之间做平滑过渡处理,使得内部冷却液流量分配合理,改善控制器内发热部件得温度均匀性,从而提升控制器稳定性与可靠性。
95.如图6、图8所示,本实施例中,驱动电机2021的冷却流道包括电机冷却液进口20251、电机冷却区域20252和电机冷却液出口20253,所述电机冷却液进口20251连通于控制器冷却液出口20243,控制器的底座固定于驱动电机后所述电机冷却液进口20251与控制器冷却液出口20243之间即形成连通,当然,连通处的周围需要形成一定的密封,在此不再赘述;电机冷却区域20252为一条或者多条在纵向上u形回转的冷却结构;驱动电机采用u型循环水路,通过对电机冷却水套的水道数量、水道宽度、水道厚度的优化组合调整,使得电机冷却散热性能提高的同时,还改善了水套内部回流,使其流通更为顺畅,降低了水套的流动阻力,有效提升驱动系统功率密度体积密度,降低了整车的能量损耗;纵向上的u形回转水道指的是在驱动电机的轴向上往复回转形成一条或者多条水道,在此不再赘述;
96.为减小驱动电机冷却结构水道内的流动死区面积,将电机水套u型流道拐角处做倒圆角处理,做好平滑过渡,保证冷却液流经过的区域不存在局部涡旋或零速度的区域。
97.本实施例中,控制器2023的冷却流道加工在底座20233,所述冷却区域覆盖发热部件安装的位置,冷却效果较好;驱动电机的冷却流道加工于驱动电机壳体;
98.控制器2023冷却液进口20241靠近驱动电机2021的尾部,控制器2023冷却液出口20243和电机冷却液进口20251的位置靠近驱动电机2021的头部;
99.该集成式水冷结构,在考虑散热性能与水阻性能的同时,还结合了水套进口和水套出口方式及布局,不但不会影响搭载终端产品后的安装位置。还考虑到设备本身的散热分布,达到较高的冷却效率。
100.最后说明的是,以上实施例仅用以说明本发明的技术方案而非限制,尽管参照较佳实施例对本发明进行了详细说明,本领域的普通技术人员应当理解,可以对本发明的技术方案进行修改或者等同替换,而不脱离本发明技术方案的宗旨和范围,其均应涵盖在本发明的权利要求范围当中。
再多了解一些
本文用于企业家、创业者技术爱好者查询,结果仅供参考。