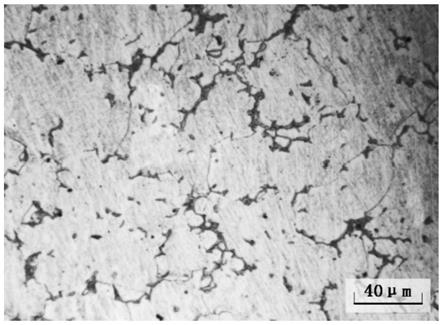
1.本发明涉及铝合金领域,具体是一种抗蠕变性耐高温铸造铝合金及制备方法。
背景技术:
2.铝型材在客车上的应用范围较广,种类较多,既有车身结构件,又有车身覆盖件和装饰件。最早应用在客车上的铝型材零部件大多对强度要求不高,但对耐腐蚀性、耐磨性以及外观质量要求甚高。随着科技的进步,客车结构也逐渐向全承载结构方向发展。目前,主要客车生产企业的全承载客车比例均已超过50%。为了提高客车的防腐性能,并延长客车的使用寿命,减少维护成本,越来越多的客车生产企业采用铝型材。在燃油经济性、安全和环保的多重要求下,国内一些知名客车制造企业已经开始考虑开发铝合金全承载客主要为装饰件向承载结构件过渡。矩形、槽形、t形等一些通用铝型材开始普遍应用到客车车身结构上。客车纵梁作为车架的重要组成部分,应具有足够的强度和刚度以承受汽车的载荷和从车轮传来的冲击,其设计既要满足实用性、耐用性、安全性等基本性能要求,更要满足实际使用工况。
3.al-zn-mg-系合金的主要强化相为mgzn2(η)与al2mg3zn(τ)。该合金如在显微组织、热处理和成分方面全面设计,可获得综合性能良好的高强度合金。提高合金中zn、mg含量,抗拉强度虽会进一步提高,但其抗应力腐蚀的能力随之下降;hf能增加固溶体的过饱和度提高时效速度,hf还能提高合金的淬火敏感性,增强抗应力腐蚀能力。gd是超高强度铝合金中常用的添加元素之一,对铝合金性能有显著的影响。根据再结晶形核机制可知弥散的al3gd质点尺寸小、密集度很高,对位错的滑移和攀沿以及晶界的移动具有很强的钉扎作用,可稳定变形组织的亚结构,阻碍加热。时位错重新排列成亚晶界及随后发展成大角度晶界的过程,从而阻碍了再结晶的形核,在al-zn-mg系合金中,元素锆的作用更为显著:抑制再结晶,提高合金再结晶温度,改善合金的强度、断裂韧性及抗应力腐蚀性能。
技术实现要素:
4.本发明的目的在于提供一种抗蠕变性耐高温铸造铝合金及制备方法,它解决现有技术中对于铝合金加工中复杂组分在使用中的相互抑制问题。
5.本发明为实现上述目的,通过以下技术方案实现:
6.一种抗蠕变性耐高温铸造铝合金,使用组分按质量百分比包含有5.0-8.0%的zn,2.5-3.5%的mg,2.0-3.0%的hf,0.3-0.6%的gd和0.2-0.5%的zr,余量为al和杂质。
7.进一步的,所述的杂质包括fe、ni、cu;
8.和/或
9.所述的杂质质量小于总质量的0.15%。
10.进一步的,所述的hf、gd与zr的质量分别记为中间合金al-hf、al-gd与al-zr中hf、gd与zr的质量。
11.进一步的,通过以下方法制得:
12.步骤一:称取铝、锌、镁和中间合金al-hf、al-gd与al-zr,并预热;
13.步骤二:将铝融化,融化完成后升温至700℃,加入锌、镁,当熔体温度达到720℃-780℃时加入中间合金al-hf、al-gd与al-zr;
14.步骤三:搅拌3分钟使所有原料其充分熔化,再升温至790℃,保温25分钟后降温,精炼6分钟后静置30分钟;
15.步骤四:冷却,去除表面浮渣,浇铸得铝合金。
16.进一步的,所述的铝、锌、镁的纯度为99.9%以上,所述的中间合金al-hf、al-gd与al-zr的纯度为99.5%以上。
17.进一步的,所述的步骤一中的预热,包括将原料送入预热釜,并基于预加热温度120-150℃条件下进行预热;
18.和/或
19.所述的步骤三中,所述保温25分钟后降温,是指将铝合金熔融物降温至730-760℃;
20.和/或
21.所述的步骤四中,在浇铸前先将模具预热至200-300℃。
22.一种抗蠕变性耐高温铸造铝合金的制备方法,作为本发明的另一个方面。
23.对比现有技术,本发明的有益效果在于:
24.本发明通过hf或gd元素的加入可产生延棱柱面生长的析出相,提高了合金的抗蠕变性能,zn的加入一方面能够起到钉扎晶界的作用,另一方面zn与hf和gd共同作用可形成大量长周期有序堆垛结构,能够阻碍位错的基面滑移,强化基体,进一步提高了合金的高温抗蠕变性能,另外,加入zr作为晶粒细化剂可显著细化晶粒,提高合金的屈服强度。
附图说明
25.图1表示实施例1所述合金的金相图;
26.图2表示实施例2所述合金的金相图;
27.图3表示实施例3所述合金的金相图;
28.图4表示实施例4所述合金的金相图;
29.图5表示对比实施例所述合金的金相图。
具体实施方式
30.下面结合具体实施例,进一步阐述本发明。应理解,这些实施例仅用于说明本发明而不用于限制本发明的范围。此外应理解,在阅读了本发明讲授的内容之后,本领域技术人员可以对本发明作各种改动或修改,这些等价形式同样。
31.下述实施例中所涉及的仪器、试剂、材料等,若无特别说明,均为现有技术中已有的常规仪器、试剂、材料等,可通过正规商业途径获得。下述实施例中所涉及的实验方法,检测方法等,若无特别说明,均为现有技术中已有的常规实验方法,检测方法等。
32.实施例1:
33.步骤一:按照5.0%的zn,2.5%的mg,2.0%的hf,0.3%的gd,和0.2%的zr,余量为al的质量百分比准确称量铝、锌、镁和中间合金al-hf、al-gd与al-zr,送入预热釜中进行预
热;
34.步骤二:将铝送入熔融釜中进行融化,融化完成后升温至700℃,加入锌、镁,当熔体温度达到720℃时加入中间合金al-hf、al-gd与al-zr;
35.步骤三:搅拌3分钟使其充分熔化,再升温至790℃,保温25分钟后降温,精炼6分钟后静置30分钟;
36.步骤四:冷却,去除表面浮渣,进行浇铸。
37.实施例2
38.步骤一:按照6.0%的zn,2.8%的mg,2.2%的hf,0.4%的gd,和0.3%的zr,余量为al的质量百分比准确称量铝、锌、镁和中间合金al-hf、al-gd与al-zr,送入预热釜中进行预热;
39.步骤二:将铝送入熔融釜中进行融化,融化完成后升温至700℃,加入锌、镁,当熔体温度达到720℃时加入中间合金al-hf、al-gd与al-zr;
40.步骤三:搅拌3分钟使其充分熔化,再升温至790℃,保温25分钟后降温,精炼6分钟后静置30分钟;
41.步骤四:冷却,去除表面浮渣,进行浇铸。
42.实施例3
43.步骤一:按照7.0%的zn,3.0%的mg,2.4%的hf,0.5%的gd,和0.4%的zr,余量为al的质量百分比准确称量铝、锌、镁和中间合金al-hf、al-gd与al-zr,送入预热釜中进行预热;
44.步骤二:将铝送入熔融釜中进行融化,融化完成后升温至700℃,加入锌、镁,当熔体温度达到720℃时加入中间合金al-hf、al-gd与al-zr;
45.步骤三:搅拌3分钟使其充分熔化,再升温至790℃,保温25分钟后降温,精炼6分钟后静置30分钟;
46.步骤四:冷却,去除表面浮渣,进行浇铸。
47.实施例4
48.步骤一:按照8.0%的zn,3.5%的mg,3.0%的hf,0.6%的gd,和0.5%的zr,余量为al的质量百分比准确称量铝、锌、镁和中间合金al-hf、al-gd与al-zr,送入预热釜中进行预热;
49.步骤二:将铝送入熔融釜中进行融化,融化完成后升温至700℃,加入锌、镁,当熔体温度达到720℃时加入中间合金al-hf、al-gd与al-zr;
50.步骤三:搅拌3分钟使其充分熔化,再升温至790℃,保温25分钟后降温,精炼6分钟后静置30分钟;
51.步骤四:冷却,去除表面浮渣,进行浇铸。
52.对照实施例
53.步骤一:按照8.0%的zn,3.5%的mg和0.5%的zr,余量为al的质量百分比准确称量铝、锌、镁和中间合金al-hf、al-gd与al-zr,送入预热釜中进行预热;
54.步骤二:将铝送入熔融釜中进行融化,融化完成后升温至700℃,加入锌、镁,当熔体温度达到720℃时加入中间合金al-hf、al-gd与al-zr;
55.步骤三:搅拌3分钟使其充分熔化,再升温至790℃,保温25分钟后降温,精炼6分钟
后静置30分钟;
56.步骤四:冷却,去除表面浮渣,进行浇铸。
57.实施例5:对实施例1-4获得的铝合金进行性能测试
58.性能测试结果如下表所示:
[0059][0060]
由表一可以看出,本发明所制备合金的高温拉伸性能和抗蠕变性能较对照组均有显著提高。这是因为hf或gd元素的加入可产生延棱柱面生长的析出相,且该析出相在在高温时具有优异的热稳定性,提高合金的抗蠕变性能,zn的加入一方面可在合金的晶界附近生成熔点较高的富zn第二相,起到钉扎晶界的作用,同时zn与hf和gd共同作用可形成大量长周期有序堆垛结构,能够阻碍位错的基面滑移,强化基体,进一步提高了合金的高温性能。
再多了解一些
本文用于企业家、创业者技术爱好者查询,结果仅供参考。