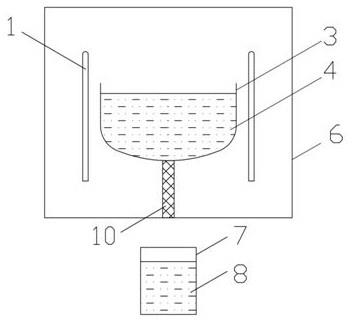
1.本发明涉及极低电阻率的硅负极材料及其制备方法。
背景技术:
2.车用动力电池要解决的两个关键问题是缩短充电时间、延长续航里程。
3.当前,动力电池的能量密度还未能完全解决电动汽车续航短的问题,同时随着未来电动汽车智能化功能的增加,车辆用电必然会持续增长。
4.从电池本身来看,提升电池能量密度可从正极、负极、电解液、隔膜等方面入手。现阶段提升电池能量密度的关键问题在于负极材料。目前动力电池负极材料普遍采用石墨材料,石墨负极材料克容量已经做到360mah/g,接近372mah/g的理论克容量,想再提升已经比较困难,开发新型的锂电池负极材料及技术迫在眉睫。
5.目前业界认为硅负极材料是石墨负极材料的理想替代产品。硅材料的理论克容量高达4200mah/g,远高于石墨材料的372mah/g,是目前已知能用于负极的材料中理论克容量最高的材料。低嵌锂电位、低原子质量、高能量密度,环境友好、储量丰富、成本较低等也都是硅负极的优势。
6.硅负极材料最突出的缺点就是在电化学反应中体积膨胀率高达320%,远高于现有的石墨材料10%左右的膨胀率。膨胀和收缩频繁发生,会使材料结构的崩塌几率显著加大,缩短电池的循环寿命,导致其难以满足电动汽车的使用需求。
7.现在纯硅负极材料的使用技术瓶颈还没有突破,目前都是通过掺入约10%的硅负极材料加工成硅碳负极材料,达到能量密度提升与寿命不衰减的某种平衡。
8.常温下石墨的电阻率为0.0008-0.0013
ω
cm。平衡或通常的随炉冷却速度条件下,p型掺硼硅最大的硼浓度为6
×
10
20
atoms/cm3,对应的电阻率为0.00021
ω
cm,n型掺磷硅最大的磷浓度为1.5
×
10
21
atoms/cm3,对应的电阻率为0.000105
ω
cm,还不能满足快速充电对硅碳负极电阻率的要求。为了尽可能降低硅碳负极的电阻、缩短充电时间、减少充电放热量,用于硅碳负极的硅材料的电阻率必须降低。
9.为了尽可能降低硅负极材料的电阻率,必须大幅度提高纯硅负极材料的掺杂浓度。这可以通过提高硅中掺杂原子(p型掺杂时单独或同时掺入硼、铝、镓等p型掺杂元素,n型掺杂时单独和或同时掺入磷、砷、锑等n型掺杂元素)的浓度来实现,使硅中掺杂原子的原子浓度尽可能远地超过3%。这样的掺杂原子浓度已经超过了这些原子在硅中的平衡固溶度(熔点温度),通常的熔化加随炉冷却方法已经不能满足要求。
10.采用等离子体加工方法可以满足要求但存在成本高产量低的问题。
技术实现要素:
11.为了克服现有技术的不足,本发明提供了极低电阻率的硅负极材料及其制备方法。
12.一种极低电阻率的p型掺杂硅负极材料的制备方法,包括如下步骤:
1)制备高掺杂浓度的p型硅熔体;2)控制硅熔体的温度在设定温度1420-2000℃;3)快速冷却硅熔体,得到直径1-10毫米的颗粒。
13.步骤1)制备高掺杂浓度的p型硅熔体步骤如下:将多晶硅和p型掺杂剂同时装入坩埚内;通过加热器将炉内温度提高到1420℃以上使坩埚内的多晶硅和p型掺杂剂转变成熔体;或者将多晶硅装入坩埚内,通过加热器将炉内温度提高到1420℃以上使坩埚内的多晶硅转变成熔体;在多晶硅熔化过程中将p型掺杂剂装入坩埚内;或者将多晶硅装入坩埚内;通过加热器将炉内温度提高到1420℃以上使坩埚内的多晶硅转变成熔体;在多晶硅完全熔化后将p型掺杂剂装入坩埚内,使掺杂剂在熔体中熔化;所述的p型掺杂剂为硼、铝、镓p型掺杂剂中的一种或几种;所述高掺杂浓度为所述的设定温度下掺杂剂达到的饱和浓度,p型掺杂剂的加入量满足在所述的设定温度下得到掺杂剂的饱和溶液的要求。
14.步骤2)如下:调节加热器的输入功率,将硅熔体的温度稳定在设定温度,设定温度是1420-2000℃范围内的选定温度;根据所需的硅负极材料的电阻率确定设定温度,选择的设定温度越高,硅熔体中掺杂剂的饱和浓度就越高,得到的硅负极材料的电阻率就越低;掺杂剂在硅熔体中达到溶解平衡并形成饱和溶液所需时间就是温度稳定的时间。
15.步骤3)如下:坩埚底部或侧面设有直径1-5毫米的流液管,打开流液管通道使硅熔体通过流液管在重力作用下流入急冷器内的急冷剂里快速冷却,熔体离开坩埚到在急冷剂中急冷成硅固体的总时间小于1秒;或者硅熔体从坩埚通过移液器或移出机构移出,移液器或移出机构将硅熔体转变成直径1-10毫米的液滴或流束并在重力作用下转移到急冷器中的急冷剂里快速冷却,熔体离开移液体器到在急冷剂中急冷成硅固体的总时间小于1秒;或者将硅熔体从所述的坩埚通过移液器或移出机构转移到熔体洒落器,洒落器将硅熔体转变成直径1-10毫米的液滴或流束再在重力作用下洒落到急冷器中的急冷剂里快速冷却,熔体离开洒落器到在急冷剂中急冷成硅固体的总时间小于1秒;所述的急冷剂包括水、干冰、液氮。
16.步骤3)如下:硅熔体进入急冷器采用风冷冷却。
17.另一种极低电阻率的n型掺杂硅负极材料的制备方法,包括如下步骤:1)制备无掺杂剂的硅熔体;2)控制硅熔体的温度在设定温度1420-2000℃;3)掺入n型掺杂剂;温度达到设定温度后,将n型掺杂剂掺入硅熔体内,同时保持设定温度到形成掺杂剂的饱和溶液,掺杂剂为磷、砷、锑中的一种或几种;4)快速冷却硅熔体,得到直径1-10毫米的颗粒。
18.步骤2)如下:调节加热器的输入功率,将硅熔体的温度稳定在设定温度,设定温度是1420-2000℃范围内的选定温度;根据所需的硅负极材料的电阻率确定设定温度,选择的设定温度越高,硅熔体中掺杂剂的饱和浓度就越高,得到的硅负极材料的电阻率就越低;掺杂剂在硅熔体中达到溶解平衡并形成饱和溶液所需时间就是温度稳定的时间。
19.步骤4)如下:所述的坩埚底部或侧面设有直径1-5毫米的流液管,打开流液管通道使硅熔体通过流液管在重力作用下流入急冷器内的急冷剂里快速冷却,熔体离开坩埚到在急冷剂中急冷成硅固体的总时间小于1秒;或者硅熔体从所述的坩埚通过移液器移出,移液器将硅熔体转变成直径1-10毫米的液滴或流束并在重力作用下转移到急冷器中的急冷剂里快速冷却,熔体离开移液体器到在急冷剂中急冷成硅固体的总时间小于1秒;或者将硅熔体从所述的坩埚通过移液器转移到熔体洒落器,洒落器将硅熔体转变成直径1-10毫米的液滴或流束再在重力作用下洒落到急冷器中的急冷剂里快速冷却,熔体离开洒落器到在急冷剂中急冷成硅固体的总时间小于1秒;所述的急冷剂包括水、干冰、液氮。
20.步骤4)如下:硅熔体进入急冷器采用风冷冷却。
21.所述的制备方法,得到直径1-10毫米的颗粒后进一步粉碎至硅负极材料需要的纳米级粒径。
22.一种极低电阻率的硅负极材料,掺杂剂原子的浓度高于硅熔点温度下该原子的热力学平衡固溶度的n型或p型硅固体材料;高掺杂浓度的p型或n型硅熔体快速冷却制备得到,所述的快速冷却是指,硅熔体急冷成硅固体的整个过程中掺杂剂原子来不及从硅晶格中析出,硅熔体转变成固体所需的时间少于1秒;所述的高掺杂浓度是指对应的硅熔体中掺杂剂的浓度,该硅熔体急冷得到的硅固体中掺杂剂原子的浓度高于该原子的热力学平衡固溶度。
23.本发明的有益效果是:掺杂浓度高,工艺可靠,成本低,产量高。
附图说明
24.图1是通过熔体移液器和熔体洒落器将硅熔体导入急冷器实现熔体急冷的一个示意图。
25.图2是通过熔体移液器和熔体洒落器将硅熔体导入急冷器实现熔体急冷的另一个示意图。
26.图3是通过熔体移液器直接将硅熔体导入急冷器实现熔体急冷的一个示意图。
27.图4是通过熔体移液器直接将硅熔体导入急冷器实现熔体急冷的另一个示意图。
28.图5是通过流液管接将硅熔体导入急冷器实现熔体急冷的一个示意图。
29.图中,加热器1、移液器2、坩埚3、硅熔体4、洒落器5、炉体6、急冷器7、急冷剂8、硅块9、流液管10。
具体实施方式
30.下面结合附图和实施例对本发明做进一步阐述。
31.实施例1如图1所示,炉体6内设有坩埚3和加热器1,设定温度分别取1450℃、1500℃、1650℃、1750℃。坩埚3的底部设有流液管10,内径取3毫米。用来制备硅碳负极的石墨的电阻率为12
×
10-4
ω
cm,硅碳负极中的硅碳比取1:9。
32.将多晶硅和硼粉装入坩埚3内,硼粉的量能确保在设定温度下形成硼的饱和溶液即可;通过加热器1将炉内温度提高到1420℃以上使坩埚3内的多晶硅和硼粉转变成硅熔体4;化料过程中控制流液管10的温度使流入其中的硅熔体保持凝固状态;调节加热器1的输入功率,将硅熔体的温度稳定在设定温度足够长的时间,使硼粉继续溶解在硅熔体中达到溶解平衡并形成饱和溶液;提高流液管10的温度使堵塞其中的硅块熔化,硅熔体4通过流液管10在重力作用下流入坩埚3下部的急冷器7内,急冷器7具有急冷剂8,硅熔体4快速冷却成硅块9,硅熔体4离开坩埚3到在急冷剂8中急冷成硅块9的总时间小于1秒。
33.将得到的直径1-10毫米的硅块9颗粒进一步粉碎至硅负极材料需要的纳米级粒径的硅粉,硅粉与碳粉比例1:9制备硅碳负极,分别测量纳米硅粉和硅碳负极的电阻率。数据对比列在表1,在硅熔点温度平衡结晶时能得到的最大硼浓度为6
×
10
20
atoms/cm3,对应电阻率为2.1
×
10-4
ω
cm,显示本发明能显著降低硅粉的电阻率,进而降低硅碳负极的电阻率,降低充电时的电极放热。
34.表1
温度(℃)硼的质量浓度(%)纳米硅粉电阻率(10-4
ω
cm)硅碳负极电阻率(10-4
ω
cm)14501.50.6310.8715002.30.4210.8416503.00.3110.8217505.00.2110.79
实施例2采用图1所示的方案,以具体实施例对本发明做进一步说明。设定温度取1500℃,流液管10的内径分别取1毫米、3毫米、5毫米、8毫米,用来制备硅碳负极的石墨的电阻率为12
×
10-4
ω
cm,硅碳负极中的硅碳比取1:9。
35.将多晶硅和硼粉装入坩埚3内,硼粉的量能确保在设定温度下形成硼的饱和溶液即可;通过加热器1将炉内温度提高到1420℃以上使坩埚3内的多晶硅和硼粉转变成硅熔体4;化料过程中控制流液管10的温度使流入其中的硅熔体保持凝固状态;调节加热器1的输入功率,将硅熔体的温度稳定在设定温度足够长的时间,使硼粉继续溶解在硅熔体中达到溶解平衡并形成饱和溶液;提高流液管10的温度使堵塞其中的硅块熔化,硅熔体4通过流液管10在重力作用下流入急冷器7内的急冷剂8里快速冷却成硅块9,硅熔体4离开坩埚3到在急冷剂8中急冷成硅块9的总时间小于1秒。
36.将得到的直径1-10毫米的硅块9颗粒进一步粉碎至硅负极材料需要的纳米级粒径的硅粉,硅粉与碳粉比例1:9制备硅碳负极,分别测量纳米硅粉和硅碳负极的电阻率。数据对比列在表2,显示本发明选定流液管内径范围1-10毫米,能确保硅熔体的急冷效果,使硼原子留在晶格中。
37.表2
流液管内径(mm)硼的质量浓度(%)纳米硅粉电阻率(10-4
ω
cm)硅碳负极电阻率(10-4
ω
cm)12.30.4210.8432.30.4210.8452.30.4210.8482.10.4610.85
实施例3
采用图2、3所示的方案,以具体实施例对本发明做进一步说明。设定温度分别取1450℃、1500℃、1650℃、1750℃。用来制备硅碳负极的石墨的电阻率为12
×
10-4
ω
cm,硅碳负极中的硅碳比取1:9。
38.将多晶硅装入坩埚3内,通过加热器1将炉内温度提高到1420℃以上使坩埚3内的多晶硅转变成硅熔体4;调节加热器1的输入功率,将硅熔体4的温度稳定在设定温度足够长的时间,同时将掺杂剂磷掺入硅熔体4内,直至形成磷的饱和溶液;将硅熔体从所述的坩埚3内通过移液器2(或移出机构,比如虹吸装置或者其它有动力或者无动力的移出装置等)转移到熔体洒落器5内,洒落器5将硅熔体转变成直径1-10毫米的液滴或流束再在重力作用下洒落到急冷器7中的急冷剂8内快速冷却,熔体离开洒落器5到在急冷剂8内急冷成硅块9的总时间小于1秒。
39.将得到的直径1-10毫米的硅块9颗粒进一步粉碎至硅负极材料需要的纳米级粒径的硅粉,硅粉与碳粉比例1:9制备硅碳负极,分别测量纳米硅粉和硅碳负极的电阻率。数据对比列在表3,在硅熔点温度平衡结晶时能得到的最大磷浓度为1.5
×
10
21
atoms/cm3,对应电阻率为1.05
×
10-4
ω
cm,显示本发明能显著降低硅粉的电阻率,进而降低硅碳负极的电阻率,降低充电时的电极放热。
40.表3
温度(℃)磷的质量浓度(%)纳米硅粉电阻率(10-4
ω
cm)硅碳负极电阻率(10-4
ω
cm)145050.7910.88150070.5210.85165090.3910.841750150.2610.82
实施例4采用图4、5所示的方案,以具体实施例对本发明做进一步说明。设定温度取1650℃用来制备硅碳负极的石墨的电阻率为12
×
10-4
ω
cm,硅碳负极中的硅碳比取1:9。
41.将多晶硅装入坩埚3内,通过加热器1将炉内温度提高到1420℃以上使坩埚3内的多晶硅转变成硅熔体4;调节加热器1的输入功率,将硅熔体4的温度稳定在设定温度足够长的时间,同时将掺杂剂磷掺入硅熔体4内,直至形成磷的饱和溶液;将硅熔体从所述的坩埚3内通过移液器2转移到急冷器7的正上方,移液器2直接将硅熔体转变成直径1-10毫米的液滴或流束再在重力作用下洒落到急冷器7中的急冷剂8内快速冷却,熔体离开洒落器5到在急冷剂8内急冷成硅块9的总时间小于1秒。
42.将得到的直径1-10毫米的硅块9颗粒进一步粉碎至硅负极材料需要的纳米级粒径的硅粉,硅粉与碳粉比例1:9制备硅碳负极,分别测量纳米硅粉和硅碳负极的电阻率。数据对比列在表4,在硅熔点温度平衡结晶时能得到的最大磷浓度为1.5
×
10
21
atoms/cm3,对应电阻率为1.05
×
10-4
ω
cm,显示本发明能显著降低硅粉的电阻率,进而降低硅碳负极的电阻率,降低充电时的电极放热。
43.表4
温度(℃)磷的质量浓度(%)纳米硅粉电阻率(10-4
ω
cm)硅碳负极电阻率(10-4
ω
cm)16509.50.3610.83
上述描述中的实施方案可以进一步组合或者替换,且实施方案仅仅是对本发明的
优选实施例进行描述,并非对本发明的构思和范围进行限定,在不脱离本发明设计思想的前提下,本领域普通技术人员对本发明的技术方案做出的各种变化和改进,均属于本发明的保护范围。本发明的保护范围由所附权利要求及其任何等同物给出。
再多了解一些
本文用于企业家、创业者技术爱好者查询,结果仅供参考。