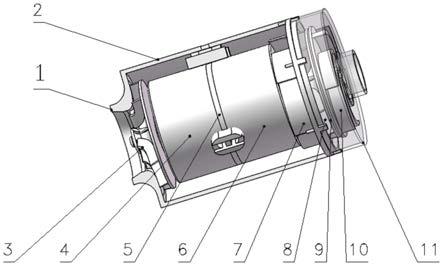
1.本发明涉及呼吸机技术领域,尤其涉及一种用于呼吸机空气增压系统的两级离心叶轮风机,是一种产生轴向强正压差的轴流双转子离心叶轮风机。
背景技术:
2.现代呼吸机最早出现于1915年哥本哈根的mol-gaard与lund,和1916年斯德哥尔摩的外科医师giertz,他们的成就缺乏资料记载,仅见于科学通讯报道。1934年frenkner研制出第一台气动限压呼吸机——“spiropulsator”,这台呼吸机的气源来自于钢筒,在吸气时气体经过两只减压阀,产生出50cm水柱的压力。1940年,frenkner和crafoord合作,在“spiropulsator”的基础上进行了改进,使它能够与环丙烷同时使用,做出了第一台麻醉呼吸机。1942年,美国工程师bennett发明了一种利用按需阀的供氧装置,供高空飞行使用。此后又加以改进,在1948年研制出间歇式正压呼吸机tv-2p,用来治疗急、慢性呼吸衰竭。1955年jefferson、morch、stephenson、bennett和鸟牌等呼吸机品牌是美国市场上使用最广的呼吸机。进入60年代,随着电子产品的快速发展,呼吸机也步入了电子化时代。呼吸机的应用更加广泛,其控制也更加的精准。1964年emerson的术后呼吸机,就是一台电动控制呼吸机,呼吸时间可以随意调节,配备压缩空气泵,各种功能均可以通过电子调节,从根本上改变了过去呼吸机纯属简单的机械运动的时代,跨入了精密的电子时代。到1970年又出现了利用射流原理控制的气动呼吸机,它是以气流控制的呼吸机,传感器、逻辑元件、放大器和调节功能等都是采用射流原理,而没有任何活动的部件,却具有与电路相同的效应。20世纪70年代由于科学技术的发展,许多尖端技术尤其是电子技术被引进到呼吸机的设计中,一大批新型呼吸机面世。新的通气理念以及技术得到发展和应用,呼气末正压、持续气道正压、间歇指令通气和t形管技术得到应用。80年代以来随着计算机技术的迅猛发展,新一代多功能电脑型呼吸机更是具备了以往不可能实现的功能,如监测、报警、记录等。进入90年代,呼吸机不断朝着智能化发展,计算机技术的应用使呼吸机的功能更加完善,性能大大提高。
3.空气增压系统为呼吸机提供正压气源,是呼吸机设计的重要关键技术。国内外的呼吸机生产商均在空气增压系统投入大量人力和物力进行研发,力图掌握其关键技术。通常的增压系统风机包括两个主要部分:旋转部,即搅动空气提升气压的电机和旋转扇叶;固定部,储存限制流体方向的外壳和导流扇叶。风机结构大多是电机带动包裹在风仓内的一个风叶高速转动做功,依靠风叶和壳体之间的间隙差达到增加气体压力和流速的目的。
4.现有空气增压系统总压比通常是1.025倍,等熵效率指标为50%。大多数无创呼吸机使用的都是端面进风、侧面出风的单叶轮鼓风机,端面进来的风通过叶轮高速加压循环敲击鼓风罩直至通过出风口输出,这个过程中总压比超过1.025倍时对电机转速要求更高,循环敲击鼓风罩导致多方位的噪音叠加。通过空气增压系统的风机叶片的几何造型、叶片数量、直径和转速等参数的优化设计,使空气增压系统与无刷电机的轴功率相匹配,以获得更大的压比和更高的效率是空气增压系统设计的主要技术难点。因此呼吸机空气系统的气
动外形优化设计必须依靠大型计算流体力学数值模拟软件平台和高性能计算机进行数值计算,结合计算流体力学技术、地面试验测试技术、材料技术和制造技术等以获得性能优异的呼吸机空气增压系统。
技术实现要素:
5.本发明的技术解决问题是:克服现有呼吸机空气增压系统的性能不足,提出了适用于低转速、高压升和大量流量的空气增压系统。
6.为实现上述目的,本发明提供一种用于呼吸机空气增压系统的两级离心叶轮风机,其包括有两个对置的离心叶轮(3,9)。
7.进一步的,其包括一级进气道(1)、外罩(2)、一级离心叶轮(3)、电机a(4)、一体支撑端盖(5)、电机b(6)、级间导气叶轮(7)、二级进气道(8)、二级离心叶轮(9)、出口导气叶轮(10)和尾罩(11);其中,所述一级进气道(1)的尾部安装在所述外罩(2)上,所述一级离心叶轮(3)安装在所述电机a(4)的前端轴上,所属一体支撑端盖(5)安装在所述外罩(2)上,所述电机a(4)和所述电机b(6)分别安装在所述一体支撑端盖(5)两端,用于驱动叶轮转动;所述级间导气轮(7)安装在所述电机b(6)上,所述二级进气道(8)安装在所述级间导气轮(7)上,所述二级离心叶轮(9)安装在所述电机b(6)尾段轴上,所述出口导气叶轮(10)安装在所述尾罩(11)上,所述尾罩(11)与所述外罩(2)连接,并进行密封。主要包括包括一级进气道(1)、外罩(2)、一级离心叶轮(3)、电机a(4)、一体支撑端盖(5)、电机b(6)、级间导气叶轮(7)、二级进气道(8)、二级离心叶轮(9)、出口导气叶轮(10)和尾罩(11)。
8.本发明摈弃了传统的电机结构,采用独有的一体支撑端盖结构,该一体支撑端盖是整个风机的支撑系统,以一体支撑端盖为中心支撑,支撑着外罩、支撑着电机a(4)和电机b(6),两端电机机壳的轴承位与一体支撑端盖轴承位分别同轴对齐;两转子通过轴承内圈固定于定子线圈内端;电机a和电机b及一体支撑端盖将转子和轴承包围在电机内部,这样的设计安全,可靠性高,既能保证转子同心度且轴承油脂不容易被风干。
9.本发明采用一体双转子的内转子无刷电机,双转子和线圈可同时或独立通电工作,(一般的鼓风机只有单一的电机),一旦其中一组线圈或者一组转子出现故障,可以快速断开故障端供电,另一组电机仍然可以有限地继续旋转以提供气压(应急作用),这样的设定在特殊的场合下能起到挽救性的作用。
10.双转子同时也是内转子,内转子结构形式可方便安放离心叶轮,转子轴伸端固定离心叶轮,安装方便。双转子各匹配一个离心叶轮,两个内转子通过两组线圈产生的磁场运转做功,内转子电机转速高,转动惯量小的优势使得离心叶轮可以尽可能的获得平稳的高转速,与此同时,在电机振动和噪音方面有更好的效果。
11.无刷电机驱动离心叶轮转动,转速范围为0~36000rpm(revolutions per minute转每分),空气经过一级进气道加速达到一级离心叶轮的进口速度,离心叶轮吸入空气并对其进行做功,使空气的动压增大,空气经过扩压后,动压降低,静压升高,流过电机罩外侧与外罩内侧间的气路进入级间导气叶轮,由径向流动再变成轴向流动;空气进入二级进气道后,二级离心叶轮吸入空气并对空气再次做功,使空气的动压再次增大,空气经过出口导气叶轮增速后输出。
12.一级进气道主要用于进气和整流,引导气流加速,抑制分离和减小流动损失。气流
经过一级进气道后达到一定速度与一级离心叶轮转速进行匹配,避免离心叶轮在进口处出现失速现象。
13.进一步的,呈“√”形的一级进气道,进气道喉道面积与进口面积比为1:1.1~1:1.4,进气道半锥角为5
°
~15
°
,进气道长度5mm~10mm。一级进气道直接固定在外罩的前端。
14.进一步的,一级离心叶轮和二级离心叶轮均采用离心式增压叶轮,离心叶轮呈扭曲状后掠型的气动外形,离心叶轮的叶片安装角和弦长沿离心叶轮的轴向逐渐减小。一级离心叶轮与外罩前段的距离0.1~1mm。
15.进一步的,一级离心叶轮叶片个数8~14,叶轮直径38mm~50mm,进口高度5mm~10mm,出口高度2mm~4mm;采用美国国家航空咨询委员会开发的naca系列翼型,厚度10%~30%;叶片的前缘和后缘半径为0.25mm~1mm。叶根螺旋角沿弦长(0~1)为0
°
~50
°
,叶根前缘气流角优选值10
°
~20
°
,叶根后缘气流角0
°
~15
°
;叶稍螺旋角沿弦长(0~1)为10
°
~50
°
,叶稍前缘气流角30
°
~50
°
,叶稍后缘气流角为5
°
~20
°
。
16.进一步的,级间导气叶轮采用90
°
螺旋“花瓣式”设计,叶片个数4~10;导气叶轮为漩流器,将径向气流改为轴向气流。级间导气叶轮通道面积是呈现逐渐增大的规律,设计为减速通道,气流进入导气轮后通过减速扩压,由此降低流动换向带来的压力损失,再进入二级进气道。级间导气叶轮的高度为6mm~16mm。为减小导气叶轮进口气流分离,导气叶轮叶片的前缘和后缘半径为0.25mm~0.5mm,叶稍与叶根的螺旋角和气流角保持一致,螺旋角均为0。采用naca系列翼型,厚度5%~15%。
17.进一步的,二级离心叶轮和一级离心叶轮构型相同。
18.进一步的,出口导气叶轮采用125
°
螺旋“花瓣式”设计,叶片个数4~8;出口导气叶轮为漩流器,将径向气流改为轴向气流。出口导气轮通道面积是呈现逐渐减小的规律,设计为加速通道,气流进入导气轮后通过加速排出。出口导气叶轮的高度为3mm~8mm。为减小导气叶轮进口气流分离,导气叶轮叶片的前缘和后缘半径取为0.1mm~0.5mm。导气叶轮叶片叶根部螺旋角沿弦长(0~1)为0~150
°
,叶根前缘气流角40
°
~75
°
,叶根后缘气流角10
°
~30
°
。叶稍与叶根的螺旋角和气流角保持一致。采用naca系列翼型,厚度5%~15%。
19.进一步的,离心叶轮径向截面位置的螺旋角和气流角具体为:
20.离心叶轮径向截面与轮毂之间的距离为0时,该径向截面位置的前缘螺旋角和气流角分别为0
°
和20
°
,后缘螺旋角和气流角分别为30
°
和10
°
,其中b为离心叶轮叶片的展长;
21.离心叶轮径向截面与轮毂之间的距离为0.5b时,该径向截面位置的前缘螺旋角和气流角分别为6
°
和24
°
,后缘螺旋角和气流角分别为30
°
和11
°
,其中b为离心叶轮叶片的展长;
22.离心叶轮径向截面与轮毂之间的距离为0.75b时,该径向截面位置的前缘螺旋角和气流角分别为10
°
和29
°
,后缘螺旋角和气流角分别为32
°
和12
°
,其中b为离心叶轮叶片的展长;
23.离心叶轮径向截面与轮毂之间的距离为1b时,该径向截面位置的前缘螺旋角和气流角分别为14
°
和40
°
,后缘螺旋角和气流角分别为33
°
和14
°
,其中b为离心叶轮叶片的展长。
24.本发明针对呼吸机空气增压系统的工作条件,利用cfd进行数值模拟和几何参数优化设计获得了高压比、高等熵效率的离心叶轮、级间导气轮和出口导气轮的气动外形。采
用独有的一体支撑结构,以一体支撑端盖为中心支撑,分别设有2个轴承位,设有两组转子,双转子各匹配一个离心叶轮。两组转子和线圈可同时也可独立通电工作。内转子结构紧凑、使电机整机布局更好,转子和离心叶轮融合一体更有利于风道设计,双转子结构使电机转速高,转动惯量小,从而可以设计气压更高、流量更大的风机,更好地解决了空气流动风腔的设计问题。
附图说明
25.图1为本发明中空气增压风机的尺寸示意图;
26.图2为本发明中空气增压风机组件示意图;
27.图3为本发明中增压风机结构部件示意图;
28.图4为本发明实施例中离心叶轮尺寸示意图;
29.图5为本发明实施例中级间导气叶轮尺寸示意图;
30.图6为本发明实施例中出口导气叶轮尺寸示意图;
31.图7为本发明中一体双转子无刷电机组件示意图;
32.图8为本发明中叶片前缘后缘示意图;
33.包括一级进气道(1)、外罩(2)、一级离心叶轮(3)、电机a(4)、一体支撑端盖(5)、电机b(6)、级间导气叶轮(7)、二级进气道(8)、二级离心叶轮(9)、出口导气叶轮(10)和尾罩(11);
34.12-气体流动路径;
35.511-电机前端轴,512-电机a前端轴承,513一级绕组-,514-电机a转子磁钢,515-电机a定子硅钢片,516-电机a机壳,517-电机a后端轴承;
36.521-二级绕组,522-电机b后端轴承,523-电机b磁钢,524-电机b定子硅钢片,525-电机b前端轴承,526-电机b机壳,527-电机后端轴
37.531-一体支撑端盖,
具体实施方式
38.应当理解,此处所描述的具体实施例仅仅用以解释本发明,并不用于限定本发明。
39.参照图1和图2,本发明提供一种用于呼吸机空气增压系统的两级离心叶轮风机,主要包括一级进气道(1)、外罩(2)、一级离心叶轮(3)、电机a(4)、一体支撑端盖(5)、电机b(6)、级间导气叶轮(7)、二级进气道(8)、二级离心叶轮(9)、出口导气叶轮(10)和尾罩(11)。
40.一级进气道(1)的尾部安装在外罩(2)上,一级离心叶轮(3)安装在电机a(4)的前端轴上,一体支撑端盖(5)安装在外罩(2)上,电机a(4)和电机b(6)分别安装在一体支撑端盖两端,用于驱动叶轮转动。
41.级间导气轮7安装在电机罩6上,二级进气道8安装在级间导气轮7上,二级离心叶轮9安装在电机5尾段轴上,出口导气叶轮10安装在尾罩11上,尾罩11与外罩2连接,并进行密封。
42.本发明摈弃了传统的电机结构,采用独有的一体支撑端盖结构,该一体支撑端盖是整个风机的支撑系统,以一体支撑端盖为中心支撑,支撑着外罩、支撑着电机a(4)和电机b(6),两端电机机壳的轴承位与一体支撑端盖轴承位分别同轴对齐;两转子通过轴承内圈
固定于定子线圈内端;电机a和电机b及一体支撑端盖将转子和轴承包围在电机内部,这样的设计安全,可靠性高,既能保证转子同心度且轴承油脂不容易被风干。
43.本发明采用一体双转子的内转子无刷电机,双转子和线圈可同时或独立通电工作,(一般的鼓风机只有单一的电机),一旦其中一组线圈或者一组转子出现故障,可以快速断开故障端供电,另一组电机仍然可以有限地继续旋转以提供气压(应急作用),这样的设定在特殊的场合下能起到挽救性的作用。
44.双转子同时也是内转子,内转子结构形式可方便安放离心叶轮,转子轴伸端固定离心叶轮,安装方便。双转子各匹配一个离心叶轮,两个内转子通过两组线圈产生的磁场运转做功,内转子电机转速高,转动惯量小的优势使得离心叶轮可以尽可能的获得平稳的高转速,与此同时,在电机振动和噪音方面有更好的效果。
45.呼吸机空气增压系统的气体流动路径如图3所示。无刷电机驱动离心叶轮转动,转速范围为0~36000rpm(revolutions per minute转每分),空气经过一级进气道加速达到一级离心叶轮的进口速度,离心叶轮吸入空气并对其进行做功,使空气的动压增大,空气经过扩压后,动压降低,静压升高,流过机壳外侧与外罩内侧间的气路进入级间导气叶轮,由径向流动再变成轴向流动;空气进入二级进气道后,二级离心叶轮吸入空气并对空气再次做功,使空气的动压再次增大;空气进入出口导气叶轮后,动压降低,静压升高,气流再次由径向变成轴向流动,最后气流通过尾罩出气口喷出。
46.一级进气道主要用于进气和整流,引导气流加速,抑制分离和减小流动损失。气流经过一级进气道后达到一定速度与一级离心叶轮转速进行匹配,避免离心叶轮在进口处出现失速现象。
47.进一步的,呈“√”形的一级进气道,进气道喉道面积与进口面积比为1:1.1~1:1.4,进气道半锥角为5
°
~15
°
,进气道长度5mm~10mm。
48.进一步的,一级离心叶轮和二级离心叶轮均采用离心式增压叶轮,离心叶轮呈扭曲状后掠型的气动外形,离心叶轮的叶片安装角和弦长沿离心叶轮的轴向逐渐减小。一级离心叶轮与外罩前段的距离0.1~1mm。
49.进一步的,如图4所示,一级离心叶轮叶片个数8~14,叶轮直径38mm~50mm,进口高度5mm~10mm,出口高度2mm~4mm;采用美国国家航空咨询委员会开发的naca系列翼型,厚度10%~30%;叶片的前缘和后缘半径为0.25mm~1mm。叶根螺旋角沿弦长(0~1)为0
°
~50
°
,叶根前缘气流角优选值10
°
~20
°
,叶根后缘气流角0
°
~15
°
;叶稍螺旋角沿弦长(0~1)为10
°
~50
°
,叶稍前缘气流角30
°
~50
°
,叶稍后缘气流角为5
°
~20
°
。
50.进一步的,级间导气叶轮采用90
°
螺旋“花瓣式”设计,叶片个数4~10,如图5所示;级间导气叶轮为漩流器,将径向气流改为轴向气流。级间导气叶轮通道面积是呈现逐渐增大的规律,设计为减速通道,气流进入导气轮后通过减速扩压,由此降低流动换向带来的压力损失,再进入二级进气道。级间导气叶轮的高度为6mm~16mm。为减小导气叶轮进口气流分离,导气叶轮叶片的前缘和后缘半径为0.25mm~0.5mm,级间导气轮叶片叶根部螺旋角沿弦长(0~1)优选值为0~90
°
,叶稍与叶根的螺旋角和气流角保持一致,螺旋角均为0。采用naca系列翼型,厚度5%~15%。
51.进一步的,二级离心叶轮和一级离心叶轮几何构型相同。
52.进一步的,出口导气叶轮采用125
°
螺旋“花瓣式”设计,如图6所示,叶片个数4~8;
出口导气叶轮为漩流器,将径向气流改为轴向气流。出口导气轮通道面积是呈现逐渐减小的规律,设计为加速通道,气流进入导气轮后通过加速排出。出口导气叶轮的高度为3mm~8mm。为减小导气叶轮进口气流分离,导气叶轮叶片的前缘和后缘半径取为0.1mm~0.5mm。导气叶轮叶片叶根部螺旋角沿弦长(0~1)为0~150
°
,叶根前缘气流角40
°
~75
°
,叶根后缘气流角10
°
~30
°
。叶稍与叶根的螺旋角和气流角保持一致。采用naca系列翼型,厚度5%~15%。
53.进一步的,离心叶轮径向截面位置的螺旋角和气流角具体为:
54.离心叶轮径向截面与轮毂之间的距离为0时,该径向截面位置的前缘螺旋角和气流角分别为0
°
和20
°
,后缘螺旋角和气流角分别为30
°
和10
°
,其中b为离心叶轮叶片的展长;
55.离心叶轮径向截面与轮毂之间的距离为0.5b时,该径向截面位置的前缘螺旋角和气流角分别为6
°
和24
°
,后缘螺旋角和气流角分别为30
°
和11
°
,其中b为离心叶轮叶片的展长;
56.离心叶轮径向截面与轮毂之间的距离为0.75b时,该径向截面位置的前缘螺旋角和气流角分别为10
°
和29
°
,后缘螺旋角和气流角分别为32
°
和12
°
,其中b为离心叶轮叶片的展长;
57.离心叶轮径向截面与轮毂之间的距离为1b时,该径向截面位置的前缘螺旋角和气流角分别为14
°
和40
°
,后缘螺旋角和气流角分别为33
°
和14
°
,其中b为离心叶轮叶片的展长。
58.具体实施例1
59.本发明针对呼吸机空气增压系统的工作条件,利用流体动力学仿真软件cfd进行数值模拟和几何参数优化设计获得了高压比、高等熵效率的离心叶轮、级间导气轮和出口导气叶轮的气动外形。
60.增压风机进气道喉道面积与进口面积比为优选为1:1.15,进气道半锥角为10
°
,进气道长度优选值为6mm,一级离心叶轮与外罩前段的距离为0.2mm。
61.增压风机长度为91mm,直径为52mm。离心叶轮叶片数为10,叶轮直径41mm,叶轮进口高度6.8mm;级间导气叶轮叶片数为6,叶轮直径52mm,叶轮进口高度14mm,叶轮前缘半径0.25mm,后缘半径0.1mm。出口导气叶轮叶片数为6,叶轮直径42mm,叶轮进口高度6mm,叶轮前缘半径0.25mm,后缘半径0.1mm。
62.离心叶轮叶根前缘气流角优选值20
°
,叶根后缘气流角优选值为10
°
;叶稍前缘气流角优选值为40
°
,叶根后缘气流角优选值为13
°
63.级间导气叶轮叶根前缘气流角优选值为78
°
,叶根后缘气流优选值为0
°
。叶稍与叶根的螺旋角和气流角保持一致。
64.叶根前缘气流角优选值为69
°
,叶根后缘气流优选值为20
°
。叶稍与叶根的螺旋角和气流角保持一致。
65.离心叶轮、级间导气叶轮和出口导气叶轮厚度优选值为15%、10%、10%。
66.在无刷电机转速为25000rpm的条件下,空气增压系统的总压比和等熵效率均达到最大,能获得总压比1.033倍(压升≥3300pa),空气质量流量2.4g/s,空气体积流量117l/s,等熵效率55%,空气适用温度-10℃~50℃。
67.测试结果表明,在无刷电机转速≥25000rpm的条件下,能获得更高空气增压系统
的总压比和等熵效率,获得总压比≥1.033,等熵效率≥55%,完全可以满足呼吸机空气增压系统的技术要求。
68.相比现有的呼吸机空气增压系统本发明的设计有很大的提升。本发明的增压叶轮采用离心式设计,采用航天空气动力学技术建立呼吸机增压系统流动模型,在高性能大型超级计算机平台上对离心叶轮进行气动数值模拟仿真和优化设计,确定叶轮的几何参数和叶片个数、获得更高压比的离心叶轮构型。本发明采用呈“√”形的一级进气道,并且对进气道内部外形进行优化,与离心叶轮设计结合起来,能极大提高流动效率,减小流道内离心叶轮的噪声,结合轴流双转子设计使离心叶轮风机的系统总压比大,适用温度范围广,效率高和可靠性高。
69.以上仅为本发明的优选实施例,并非因此限制本发明的专利范围,凡是利用本发明说明书及附图内容所作的等效结构或等效流程变换,或直接或间接运用在其他相关的技术领域,均同理包括在本发明的专利保护范围内。
再多了解一些
本文用于企业家、创业者技术爱好者查询,结果仅供参考。