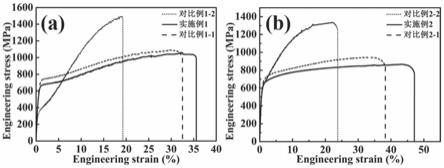
一种cu-al合金化高强中锰钢热轧板及其制备方法
技术领域
1.本发明涉及中锰钢技术领域,尤其涉及一种cu-al合金化高强中锰钢热轧板及其制备方法。
背景技术:
2.中锰钢(锰质量分数为3%-12%)作为第三代先进汽车高强钢,因其优异的强塑积(20-70gpa%)、轻量化和低成本等特点,具有非常广阔的应用前景。中锰钢中奥氏体含量是保证相变诱导塑性(trip)效应发生的主要因素,通过变形诱导马氏体相变使局部强度提高,使得变形向未发生马氏体相变区域转移,推迟颈缩,从而得到优异力学性能。此外,奥氏体稳定性对于中锰钢力学性能提升极为重要,若奥氏体稳定性太差,大量奥氏体在变形初期发生马氏体相变,剩余奥氏体无法保证有效的trip效应发生以维持整个塑性变形阶段,从而导致过早的断裂。因此,制备奥氏体含量及稳定性兼具的中锰钢是当今中锰钢工业应用主流发展趋势。
3.近年来,国内外学者一般通过在中锰钢中添加微合金元素的方式调节奥氏体含量及稳定性。如中锰钢中铝的加入可以使得钢的密度降低大幅减重;可以显著扩大奥氏体 铁素体两相区范围,缩短工业退火时间,节约成本;同时铝作为铁素体形成元素,一定程度上抑制退火过程中过量奥氏体形成,促进奥氏体中锰含量的富集从而提高奥氏体稳定性;此外,铝不溶于渗碳体,抑制渗碳体析出,促进碳在奥氏体中富集,提高奥氏体稳定性;最后,铝可以促进退火过程中再结晶的发生从而细化晶粒。铜本身作为一种奥氏体稳定元素,固溶在奥氏体中的铜就可以显著提高奥氏体含量及稳定性。析出的富铜纳米粒子可以作为第二相进一步起到析出强化作用,不同于中锰钢中传统的碳化铌、碳化钒等析出强化粒子,消耗固溶在奥氏体中的c原子,而削弱奥氏体含量及稳定性。但现有技术中未有关于cu-al复合添加以调整中锰钢中奥氏体含量及稳定性,制备高强中锰钢的报道。综上所述,如何在普通热轧中锰钢研发基础上,不显著提高生产成本的前提下,通过复合添加cu-al微合金元素和调整相应热处理工艺,制备出一种奥氏体含量及稳定性兼具的新型中锰钢具有很大的实际意义。
技术实现要素:
4.为解决上述问题,本发明在中锰钢的设计理念基础上,通过复合添加cu-al合金元素对中锰钢奥氏体逆转变影响,合理的成分控制以及优化热处理工艺,开发出了一种性能优异的高强韧汽车钢板,满足不同汽车零件使用指标,所述cu-al合金化中锰钢热轧板的制备方法,包括以下步骤:
5.(1)熔炼:将钢锭进行真空熔炼浇铸得到炮弹状钢锭;
6.(2)锻造:将步骤(1)得到的钢锭加热至1200℃-1250℃,保温2-3h,锻造成横截面100mm
×
30mm的板坯,随后空冷至室温;
7.(3)热轧:将步骤(2)得到的板坯加热至1200℃-1250℃,保温2-3h,开轧温度为
1150℃-1250℃,终轧温度≥900℃,经过轧制得到厚度为4
±
0.5mm的薄板,随后空冷至室温;
8.(4)轧后热处理:将步骤(3)得到的薄板进行900℃奥氏体化淬火,保温0-30min,随后水冷至室温,将水淬后热轧板进行临界退火,随后水冷至室温,得到成品cu-al合金化中锰钢热轧板。
9.进一步地,所述步骤(1)中,钢锭中各元素的质量百分比如下:c:0.15-0.18%,mn:10.0-10.32%,al:1.9-2.1%,cu:1.8-2.2%,其余为fe及不可避免的杂质。
10.进一步地,所述步骤(2)中钢锭加热温度为1200℃,保温时间为2h。
11.进一步地,所述步骤(3)中板坯加热温度为1200℃,保温时间为2h。
12.进一步地,所述步骤(3)中板坯开轧温度为1200℃,终轧温度为1000℃进一步地,所述步骤(3)中的轧制为5-7道次轧制。
13.进一步地,所述步骤(4)中退火温度为600℃,保温时间为30min。
14.本发明还提供了一种根据上述方法制备而成的cu-al合金化中锰钢热轧板,所述cu-al合金化中锰钢热轧板可应用于汽车工业中。
15.与现有技术相比,本发明的有益技术效果:
16.本发明将微合金元素cu-al及热处理工艺相结合,使中锰钢兼备了适宜的奥氏体含量和良好的稳定性,使其在变形过程中能够充足协调的发生trip效应,使产品具有优异的力学性能。本发明的cu-al合金化中锰钢热轧板抗拉强度可达866-1061mpa,延伸率为35.2%-47.1%,强塑积为35-40gpa%,在不显著提高生产成本的前提下,有效地提高了中锰钢的力学性能,促进中锰钢工业化生产和应用。
附图说明
17.下面结合附图说明对本发明作进一步说明。
18.图1(a)为实施例1和对比例1-1/2的工程应力应变曲线;
19.图1(b)为实施例2和对比例2-1/2的工程应力应变曲线;
20.图2(a)为实施例1和对比例1-1/2的拉伸前后奥氏体含量图;
21.图2(b)为实施例2和对比例2-1/2的拉伸前后奥氏体含量图。
具体实施方式
22.本发明提供了一种性能优异的高强韧汽车钢板,满足不同汽车零件使用指标。所述cu-al合金化中锰钢热轧板的制备方法,包括以下步骤:
23.(1)熔炼:将钢锭进行真空熔炼浇铸得到炮弹状钢锭;
24.(2)锻造:将步骤(1)得到的钢锭加热至1200℃-1250℃,保温2-3h,锻造成横截面100mm
×
30mm的板坯,随后空冷至室温;
25.(3)热轧:将步骤(2)得到的板坯加热至1200℃-1250℃,保温2-3h,开轧温度为1150℃-1250℃,终轧温度≥900℃,经过轧制得到厚度为4
±
0.5mm的薄板,随后空冷至室温;
26.(4)轧后热处理:将步骤(3)得到的薄板进行900℃奥氏体化淬火,保温0-30min,随后水冷至室温,将水淬后热轧板进行临界退火,随后水冷至室温,得到成品cu-al合金化中
锰钢热轧板。
27.进一步地,所述步骤(1)中,钢锭中各元素的质量百分比如下:c:0.15-0.18%,mn:10.0-10.32%,al:1.9-2.1%,cu:1.8-2.2%,其余为fe及不可避免的杂质。
28.在一个实施例中,所述步骤(2)中钢锭加热温度为1200℃,保温时间为2h。
29.在一个实施例中,所述步骤(3)中板坯加热温度为1200℃,保温时间为2h。
30.在一个实施例中,所述步骤(3)中板坯开轧温度为1200℃,终轧温度为1000℃
31.在一个实施例中,所述步骤(3)中的轧制为5-7道次轧制。
32.在一个实施例中,所述步骤(4)中退火温度为600℃,保温时间为30min。
33.本发明所述cu-al合金化中锰钢热轧板可应用于汽车工业中。
34.以下结合实施例对本发明提供的技术方案进行进一步说明。
35.实施例1
36.钢锭的化学成分及质量百分比如下:c:0.15%,mn:10.32%,al:2.01%,cu:1.98%,余量为fe及不可避免的杂质;
37.钢锭采用真空感应炉冶炼,将钢锭加热至1200℃保温2h,锻造成钢坯;将钢坯加热至1200℃保温2h,经6道次热轧成厚度为4mm的薄板,终轧温度900℃,随后空冷至室温;将热轧后的钢板在加热炉中,加热至600℃保温30min后水淬至室温,得到cu-al合金化中锰钢热轧板;
38.根据gb/t228-2002“金属材料室温拉伸试验方法”将热处理后钢板加工成拉伸试样进行性能测试,应力应变曲线如图1a所示;拉伸前后奥氏体含量如图2a所示。
39.对比例1-1
40.钢锭的化学成分及质量百分比如下:c:0.18%,mn:10.25%,al:2.11%,余量为fe及不可避免的杂质;
41.钢锭采用真空感应炉冶炼,将钢锭加热至1200℃保温2h,锻造成钢坯;将钢坯加热至1200℃保温2h,经6道次热轧成厚度为4mm的薄板,终轧温度900℃,随后空冷至室温;将热轧后的钢板在加热炉中,加热至600℃保温30min后水淬至室温,得到中锰钢热轧板;
42.根据gb/t228-2002“金属材料室温拉伸试验方法”将热处理后钢板加工成拉伸试样进行性能测试,应力应变曲线如图1a所示;拉伸前后奥氏体含量如图2a所示。
43.对比例1-2
44.钢锭的化学成分及质量百分比如下:c:0.15%,mn:10.09%,cu:1.99%,余量为fe及不可避免的杂质;
45.钢锭采用真空感应炉冶炼,将钢锭加热至1200℃保温2h,锻造成钢坯。将钢坯加热至1200℃保温2h,经6道次热轧成厚度为4mm的薄板,终轧温度900℃,随后空冷至室温;将热轧后的钢板在加热炉中,加热至600℃保温30min后水淬至室温,得到中锰钢热轧板;
46.根据gb/t228-2002“金属材料室温拉伸试验方法”将热处理后钢板加工成拉伸试样进行性能测试,应力应变曲线如图1a所示;拉伸前后奥氏体含量如图2a所示。
47.退火工艺下工程应力应变曲线(图1a)和力学性能(表1)比较发现,相对于对比例1-1(单添加al)以及对比例1-2(单添加cu),实施例1(复合添加cu-al)具有最优的强度-塑性的结合,强塑积达到37.4gpa%。其中,抗拉强度达到1061mpa,延伸率为35.2%,且从图2a可以看出实施例1中拉伸前奥氏体含量为68.3%,断后奥氏体含量为34.3%,奥氏体转化率
为49.7%,兼备奥氏体含量和稳定性,满足现代汽车钢使用要求和未来阶段化的发展需求。
48.实施例2
49.钢锭的化学成分及质量百分比如下:c:0.15%,mn:10.32%,al:2.01%,cu:1.98%,余量为fe及不可避免的杂质;
50.钢锭采用真空感应炉冶炼,将钢锭加热至1200℃保温2h,锻造成钢坯。将钢坯加热至1200℃保温2h,经6道次热轧成厚度为4mm的薄板,终轧温度900℃,随后空冷至室温;将热轧后的钢板在加热炉中重新加热至900℃进行奥氏体化水淬保温30min,随后水淬至室温;将奥氏体化水淬后热轧板加热至600℃保温30min,随后水淬至室温,得到中锰钢热轧板,得到cu-al合金化中锰钢热轧板。
51.根据gb/t228-2002“金属材料室温拉伸试验方法”将热处理后钢板加工成拉伸试样进行性能测试,应力应变曲线如图1b所示;拉伸前后奥氏体含量如图2b所示。
52.对比例2-1
53.钢锭的化学成分及质量百分比如下:c:0.18%,mn:10.25%,al:2.11%,余量为fe及不可避免的杂质;
54.钢锭采用真空感应炉冶炼,将钢锭加热至1200℃保温2h,锻造成钢坯。将钢坯加热至1200℃保温2h,经6道次热轧成厚度为4mm的薄板,终轧温度900℃,随后空冷至室温;将热轧后的钢板在加热炉中重新加热至900℃进行奥氏体化水淬保温30min,随后水淬至室温。将奥氏体化水淬后热轧板加热至600℃保温30min,随后水淬至室温,得到中锰钢热轧板;
55.根据gb/t228-2002“金属材料室温拉伸试验方法”将热处理后钢板加工成拉伸试样进行性能测试,应力应变曲线如图1b所示;拉伸前后奥氏体含量如图2b所示。
56.对比例2-2
57.钢锭的化学成分及质量百分比如下:c:0.15%,mn:10.09%,cu:1.99%,余量为fe及不可避免的杂质;
58.钢锭采用真空感应炉冶炼,将钢锭加热至1200℃保温2h,锻造成钢坯;将钢坯加热至1200℃保温2h,经6道次热轧成厚度为4mm的薄板,终轧温度900℃,随后空冷至室温;将热轧后的钢板在加热炉中重新加热至900℃进行奥氏体化水淬保温30min,随后水淬至室温。将奥氏体化水淬后热轧板加热至600℃保温30min,随后水淬至室温,得到中锰钢热轧板。
59.根据gb/t228-2002“金属材料室温拉伸试验方法”将热处理后钢板加工成拉伸试样进行性能测试,应力应变曲线如图1b所示;拉伸前后奥氏体含量如图2b所示。
60.在淬火-退火工艺下工程应力应变曲线(图1b)和力学性能(表1)比较发现,相对于对比例2-1(单添加al)以及对比例2-2(单添加cu),实施例2(复合添加cu-al)具有最优的强度-塑性的结合,强塑积达到40.8gpa%。其中,抗拉强度达到866mpa,延伸率为47.1%,且从图2b可以看出实施例2中拉伸前奥氏体含量为52.5%,断后奥氏体含量为28.4%,奥氏体转化率为45.9%,兼备奥氏体含量和稳定性,均满足现代汽车钢使用要求和未来阶段化的发展需求。
61.表1力学性能检测结果
[0062][0063]
本文中应用了具体个例对本发明的原理及实施方式进行了阐述,以上实施例的说明只是用于帮助理解本发明的方法及其核心思想;同时,对于本领域的一般技术人员,依据本发明的思想,在具体实施方式及应用范围上均会有改变之处。综上所述,本说明书内容不应理解为对本发明的限制。
再多了解一些
本文用于企业家、创业者技术爱好者查询,结果仅供参考。