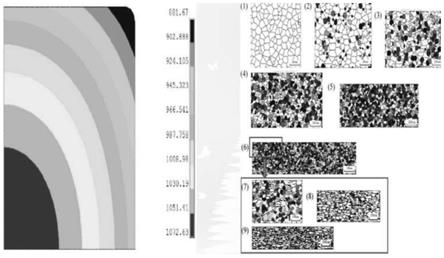
1.本发明属于冶金领域的一种轧钢工艺,具体涉及中板轧制过程中的头尾角部裂纹消除方法。
背景技术:
2.钢板裂纹是指钢板表面形成一条或者多条裂纹,依据其形态和发生部位不同可分为多种类型,其中钢板角裂是热轧态钢板表面常见的一种表面质量缺陷,根据轧制变形理论,在坯料展宽过程中,坯料宽向两侧棱边被咬入轧辊,变形后咬入侧上下棱边的角部将有一部分随着轧辊压下转移到板材上下表面,在轧制过程中此部分破裂、延伸和扩展,形成一定宽度的细密边部裂纹。此裂纹无法做到完全剪切避让,会降低成品合格率。
3.中板轧制过程中随着金属的延伸,在8-20mm厚度规格产品头尾圆弧处发生角部微裂纹的概率较高。其主要原因在于加热过程中的氧化脱碳和轧制过程中边角温度过低导致的应力裂纹,是钢在第ⅲ脆性区产生的一种沿晶开裂,裂纹形貌与圆弧形状相对应,此类裂纹需要切除,造成成材率损失。据统计,中板厂每年因角部裂纹浪费的头部金属重量为2000吨,造成成本浪费约800万元。
技术实现要素:
4.针对角部裂纹缺陷问题,本发明的目的在于提供一种用于中板产线的角部裂纹的控制方法,降低中板厂角部裂纹缺陷发生率。
5.本发明具体采用如下技术方案:
6.一种轧制过程中头尾角部裂纹的控制方法,其特征在于包括:
7.控制加热过程温度和时间,控制残氧量;具体如下:加热炉分三段,加热段温度设定1230
±
20℃,加热段时间保证>0.4h;均热段温度设定1220
±
20℃,均热段时间保证>0.25h;下表温度设定较上表低10℃,炉膛残氧量控制1%以下;
8.粗轧过程根据坯料厚度和展宽比对轧制道次、展宽道次和道次压下量进行控制;
9.根据总轧制道次的不同选择粗轧、精轧过程除鳞道次;
10.终轧温度控制在820-840℃;
11.根据轧制成品厚度选择合适的中间坯厚度;
12.根据中间坯厚度选择合适的中间坯冷却时间。
13.本发明有益效果:
14.本发明通过对中板头尾部角部裂纹的影响因素进行分析,对加热制度、轧制工艺进行优化,最终得出合适的控制工艺。通过跟踪角裂控制法实验效果,利用本发明的控制方法进行生产,轧制过程稳定,可大幅减少此类角部裂纹的发生,中板厂角部裂纹缺陷发生率由5%降低至0.2%以内,提高了中板产线表面一次合格率,减少了头尾切损量,经济效益显著。
附图说明
15.图1为现有轧制方法轧后头尾角裂的金相组织;
16.图2为现有轧制方法轧后角裂部位nd/td/rd三维方向金相组织;
17.图3为现有轧制方法轧后角裂部位存在脱碳现象;
18.图4为现有轧制方法轧后角裂部位为组织不均导致的应力裂纹;
19.图5为仿真模拟轧制过程采用本发明控制方法得到的边角部的组织转变规律示意图。
具体实施方式
20.如图1、图2所示,从轧后角裂组织形貌看,除nd面组织差异较大外,其他两个面组织均为带状组织,且内部均无裂纹,表明原材料并无问题,其中nd面中存在粗大再结晶、混晶以及大量铁素体,表明板坯发生严重再结晶和脱碳,推床裂纹产生的原因是应力裂纹。通过图3、图4发现裂纹产生的原因一方面是由于加热温度过高导致脱碳,另一方面是由于轧制过程中精轧阶段边角部组织差异性大导致应力裂纹。
21.基于上述分析,本发明通过调整参数改善组织差异性,具体是通过调整加热区域氧化氛围,控制在炉时间,使钢板奥氏体化后又不过分氧化脱碳;同时控制粗轧展宽阶段压下量均匀性晶粒大小,针对不同道次选择合理的除鳞时间,减少局部区域温度过低现象;精轧区域控制中间坯厚度,合理分配精轧压下量,采用高终轧,控制中间坯控温时间,使晶粒再完全再结晶后高温轧制,可减少边部组织差异,角部裂纹发生率可由3.2%降低至0.2%以内。如图5所示为模拟仿真轧制过程中边角部的组织转变规律。
22.具体地,本发明的一种轧制过程中头尾角部裂纹的控制方法,通过对加热制度、轧制工艺、中间坯料控制优化,减少中板角部裂纹情况,具体包括:
23.1、加热制度优化
24.控制加热过程温度和时间,控制残氧量;具体如下:加热炉分三段,加热段温度设定1230
±
20℃,加热段时间保证>0.4h;均热段温度设定1220
±
20℃,均热段时间保证>0.25h;下表温度设定较上表低10℃,炉膛残氧量控制1%以下,总在炉时间<1.5min/mm;
25.2、粗轧过程优化:
26.根据坯料厚度和展宽比对轧制道次、展宽道次和道次压下量进行控制,具体如下表所示:
27.展宽比展宽道次总轧制道次单道次压下量≤1.21、27、915%-20%1.2-≤1.539、1116%-23%1.5-≤2.041118%-25%
28.3、除磷道次优化:
29.根据总轧制道次的不同选择粗轧、精轧过程除鳞道次,具体如下表所示:
30.粗精轧轧制道次粗轧除鳞精轧除鳞7 5第1、3道次第1道次9 5第1、5道次第1道次11 5第1、5道次第1道次
9 7第1、5道次第1、3道次11 7第1、5道次第1、3道次
31.4、终轧温度控制在820-840℃。
32.5、根据轧制成品厚度选择合适的中间坯厚度。中间坯厚度具体控制如下表:
33.轧制成品厚度中间坯厚度6-≤103.6
±
0.2h10-≤123.4
±
0.2h12-≤163.2
±
0.2h16-≤203.0
±
0.2h20-≤252.8
±
0.2h25-≤302.4
±
0.2h30-≤402.0
±
0.2h40-≤501.8
±
0.2h50-≤601.6
±
0.2h
34.6、根据中间坯厚度选择合适的中间坯冷却时间,具体控温时间如下表所示:
35.中间坯厚度(mm)中间坯控温时间(s)30-≤40≤8040-≤50≤9050-≤60≤10060-≤70≤12070-≤80≤14080-≤90≤16090-≤100≤200100-≤110≤240
技术特征:
1.一种轧制过程中头尾角部裂纹的控制方法,其特征在于包括:控制加热过程温度和时间,控制残氧量;具体如下:加热炉分三段,加热段温度设定1230
±
20℃,加热段时间保证>0.4h;均热段温度设定1220
±
20℃,均热段时间保证>0.25h;下表温度设定较上表低10℃,炉膛残氧量控制1%以下,总在炉时间<1.5min/mm;粗轧过程根据坯料厚度和展宽比对轧制道次、展宽道次和道次压下量进行控制;根据总轧制道次的不同选择粗轧、精轧过程除鳞道次;终轧温度控制在820-840℃;根据轧制成品厚度选择合适的中间坯厚度;根据中间坯厚度选择合适的中间坯冷却时间。2.如权利要求1所述的轧制过程中头尾角部裂纹的控制方法,其特征在于粗轧过程根据坯料厚度和展宽比对轧制道次、展宽道次和道次压下量进行控制如下表所示:展宽比展宽道次总轧制道次单道次压下量≤1.21、27、915%
‑‑
20%1.2-≤1.539、1116%-23%1.5-≤2.041118%-25%。3.如权利要求1所述的轧制过程中头尾角部裂纹的控制方法,其特征在于根据总轧制道次的不同选择粗轧、精轧过程除鳞道次如下表所示:粗精轧轧制道次粗轧除鳞精轧除鳞7 5第1、3道次第1道次9 5第1、5道次第1道次11 5第1、5道次第1道次9 7第1、5道次第1、3道次11 7第1、5道次第1、3道次。4.如权利要求1所述的轧制过程中头尾角部裂纹的控制方法,其特征在于根据轧制成品厚度选择合适的中间坯厚度如下表所示:轧制成品厚度中间坯厚度6-≤103.6
±
0.2h10-≤123.4
±
0.2h12-≤163.2
±
0.2h16-≤203.0
±
0.2h20-≤252.8
±
0.2h25-≤302.4
±
0.2h30-≤402.0
±
0.2h40-≤501.8
±
0.2h50-≤601.6
±
0.2h。5.如权利要求1所述的轧制过程中头尾角部裂纹的控制方法,其特征在于根据中间坯
厚度选择合适的中间坯冷却时间如下表所示:中间坯厚度(mm)中间坯控温时间(s)30-≤40≤8040-≤50≤9050-≤60≤10060-≤70≤12070-≤80≤14080-≤90≤16090-≤100≤200100-≤110≤240。
技术总结
本发明公开了一种轧制过程中头尾角部裂纹的控制方法,通过对中板头尾部角部裂纹的影响因素进行分析,对加热制度、轧制工艺进行优化,最终得出合适的控制工艺。通过跟踪角裂控制法实验效果,利用本发明的控制方法进行生产,轧制过程稳定,可大幅减少此类角部裂纹的发生,中板厂角部裂纹缺陷发生率由5%降低至0.2%以内,提高了中板产线表面一次合格率,减少了头尾切损量,经济效益显著。经济效益显著。经济效益显著。
技术研发人员:黄灿 徐益平 李灿 杨晓东 张波 单金涛 丁小恒 温红
受保护的技术使用者:南京钢铁股份有限公司
技术研发日:2022.02.08
技术公布日:2022/5/17
再多了解一些
本文用于企业家、创业者技术爱好者查询,结果仅供参考。