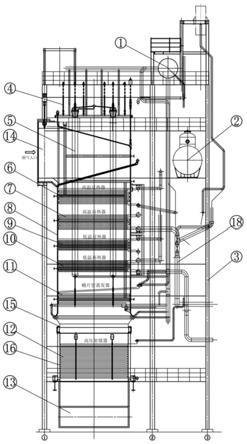
1.本发明涉及余热电站发电领域,尤其涉及一种带再热干熄焦余热锅炉。
背景技术:
2.我国大型钢铁企业吨钢能耗比发达国家高10%,中小企业吨钢能耗比发达国家高20%,极大地影响了我国钢铁工业的竞争力和可持续发展。其中我国炼焦焦炭90%以上用于高炉炼铁及冶金行业,那么针对炼焦生产中熄焦工艺提高余热利用效率对提高企业的竞争力,能源的回收利用,增加电力,减少污染有着重要的意义。熄焦工艺分干熄焦和湿熄焦,因干熄焦在节能、环保和改善焦炭质量方面均优于湿法熄焦而得到广泛的应用。在干熄炉冷却段,焦碳向下流动,惰性循环气体向上流动,焦碳通过与循环气体进行热交换而冷却。冷惰性气体主要成分为氮气,温度170~190℃在干熄炉中与炼焦炉推出的大约为1050℃的赤热焦炭逆向流动直接换热,惰性气体被加热到860~980℃,从而冷却焦炭至200℃左右,干法熄焦大约能回收红焦83%的显热。这部分烟气如不经过利用直接排放,会造成能源的浪费和环境污染,现有技术就采用了干熄焦回收红焦废热产生蒸汽,可用于发电,避免了生产等量气燃煤而对大气的污染(5-6t蒸汽需要1吨动力煤)。对规模为100万t/a焦化厂而言,采用干熄焦技术,每年可以减少8-10 万吨动力煤燃烧对大气的污染。相当于少向大气排放144吨-180吨烟尘、1280 吨-1600吨so2,尤其是每年可以减排10万吨-17.5万吨co2。
3.现阶段干熄焦工艺是惰性气体封闭的循环利用过程,干熄焦余热锅炉是其中重要的辅机设备,其主要工作原理是通过余热锅炉受热面管来吸收干熄焦排放的余热,产生蒸汽供汽轮机发电或作为供热及其它工艺用汽,但是我们国家目前的干熄焦余热锅炉的现状是企业注重前提投资成本,造成市场上干熄焦余热锅炉多为中低温,中低压余热锅炉,少部分的高温高压干熄焦余热锅炉,整体效率不高。高温高压干熄焦余热锅炉系统发电效率一般为30%~32%,中低温中低压系统效率更低,因此现有的干熄焦余热利用系统并没有对熄焦尾气的最优化利用。对企业在能耗利用层面上没有明显的可持续竞争优势。同时,应清醒地认识到,钢铁去过剩产能任务依然艰巨,作为与钢铁发展高度相关联的焦化企业,同样面临着重重挑战,采用更先进、更经济、更高效的干熄焦余热利用新工艺显得更加的必要。
技术实现要素:
4.本发明提供的一种带再热干熄焦余热锅炉系统,是国内首台双超带再热干熄焦余热锅炉,旨在解决现有技术中余热电站发电效率低下的问题,超高温超高压带再热系统总厂发电效率约35%,本系统比中温中压多发电40%左右,比高温高压多发电15%左右。本发明参数上主汽压力调整至13.9mpa,主汽温度571℃,热再热出口温度为571℃,均为超高温超高压参数。结构上增设高温再热器、低温再热器,为优化烟气换热,不设光管蒸发器,同时在锅炉结构设计都有其独特的优点。
5.为了解决上述技术问题,本发明采用如下技术方案:
6.一种带再热干熄焦余热锅炉,包括:
7.锅筒(1),除氧器(2),钢结构(3),水冷壁吊挂装置(4),吊挂管(5),高温过热器(6),高温再热器(7),水冷壁(8),低温过热器(9),低温再热器(10),鳍片管蒸发器(11),高压省煤器(12),出口烟道(13),入口烟道 (14),过滤烟道(15),省煤器墙板(16),平台扶梯(17),管道系统(18);
8.所述鳍片管蒸发器(11)固定于所述吊挂管(5)上而悬吊于锅炉顶部,锅筒(1)炉水由三根下降管引出,通过连管分别引入所述鳍片管蒸发器(11),水冷壁(8)环形集箱及吊挂管(5)下集箱。所述鳍片管蒸发器(11)错列布置,工质从底部流向顶部,与烟气逆向流动;
9.所述吊挂管(5)向上依次悬吊低温再热器(10)、低温过热器(9)、高温再热器(7)和高温过热器(6),所述吊挂管(5)进口集箱底部焊接吊板,通过销轴与所述鳍片管蒸发器(11)管夹连接,悬吊所述鳍片管蒸发器(11);
10.锅炉在循环气进口处布置有所述入口烟道(14),与熄焦系统的烟道相连,通过两根吊杆吊挂于顶部梁格下面;高压省煤器(12)布置在所述省煤器墙板 (16)内,省煤器墙板(16)与所述水冷壁(8)的环形集箱之间布置所述过渡烟道(15),中间布置膨胀节,以吸收水冷壁(8)和高压省煤器(12)之间的膨胀。
11.作为优选,所述炉系统还包括再热器系统,所述再热器系统包括冷再热进口管道系统连接至低温再热器(10)入口集箱,再到低温再热器(10)受热面,再到低温再热器(10)出口集箱,再到连接管道及再热减温器,至高温再热器 (7)进口集箱,再到高温再热器(7)受热面,再到高温再热器(7)出口集箱及热再热主汽出口管道系统。
12.作为优选,所述锅炉系统还包括过热器系统,所述过热器系统包括锅筒(1) 来的饱和蒸汽连接至低温过热器(9)入口集箱,再到低温过热器(9)受热面,再到低温过热器(9)出口集箱,再到连接管道及再热减温器,至高温过热器(6) 进口集箱,再到高温过热器(6)受热面,再到高温过热器(6)出口集箱及主汽出口管道系统。
13.作为优选,所述锅炉系统还包括鳍片管蒸发器系统,水冷壁系统,吊挂管系统,所述鳍片管蒸发器系统包括锅筒(1)连接至鳍片管蒸发器(11)的下降管到鳍片管蒸发器(11)入口集箱,再到鳍片管蒸发器(11)受热面,再到鳍片管蒸发器(11)出口集箱,再到鳍片管蒸发器(11)上升管最后回到锅筒(1)。
14.作为优选,所述水冷壁系统包括锅筒(1)连接至水冷壁(8)下降管,到水冷壁(8)入口集箱,再到水冷壁(8),再到水冷壁(8)出口集箱,再到水冷壁(8)上升管,最后再到锅筒(1)。
15.作为优选,所述吊挂管系统包括锅筒(1)连接至水冷壁(8)下降管,到吊挂管(5)入口集箱再到吊挂管(5),再到吊挂管(5)出口集箱,再到吊挂管(5)上升管,最后到锅筒(1)。
16.作为优选,所述锅筒(1)还包括多个管座,循环水通过锅筒(1)底部的三个管座进入下降管,汽水混合物通过七个横向布置的管座回到锅筒(1);所述锅筒(1)底部的其它管座分别与排污管和紧急放水管相连;压力表和安全阀的管座布置在所述锅筒(1)顶部。
17.作为优选,所述水冷壁(8)包括管子和扁钢,采用悬吊结构,通过侧墙水冷壁上集箱和后墙水冷壁折弯处的吊杆悬吊于顶部梁格上,自由向下膨胀。
18.作为优选,所述高压省煤器(12)布置在锅炉下部由省煤器墙板(16)构成的低温区域内,所述高压省煤器(12)管束为螺旋鳍片管,由多组管排向上斜向绕制成错列管束,中间用压制弯头连接,给水进入所述高压省煤器(12) 进口集箱后逆向烟气向上流动,进入所述
高压省煤器(12)出口集箱后,通过连管进入锅筒水空间;
19.高压省煤器(12)为悬吊式结构,通过螺旋鳍片管管夹将管束悬挂于横梁上,横梁两端固定在省煤器墙板(16)上,再通过省煤器墙板(16)将力传递到钢架平台。
20.作为优选,所述管道系统(18)增设高低压旁路系统,高低压旁路在本项目中起3种作用:
21.在机组启动阶段,汽机尚不能带负荷,这时通过高低压旁路使锅炉产生的蒸汽减温减压后进入冷凝器冷凝成水,再通过给水系统回到锅炉,起到避免蒸汽放空,同时回收工质的作用。
22.防止再热器干烧,在锅炉启动阶段,通过高低压旁路,可使再热器一直有蒸汽流动,从而达到保护过热器的作用。
23.在汽轮机故障时,起到停机不停炉的作用。
24.本发明的工作原理如下:
25.熄焦工艺流程中出来的烟气温度大约880~980℃,通过内衬砖墙的烟气通道从上端进入锅炉入口烟道。在入口段,气流转过90
°
,改为向下流动,首先将热量传递给由前墙水冷壁拉稀而成的预置蒸发器的受热面,然后依次流经由水冷壁包围的高温过热器、高温再热器、低温过热器、低温再热器和鳍片管蒸发器,锅炉的水冷壁设计成作为蒸发器的受热面管,吸收烟气流程中的辐射放热。随后烟气进入下部的高压省煤器,吸收烟气的剩余热量加热给水。
26.烟气经过上述的冷却过程后,烟温降到180℃以下后,转过90
°
,沿水平方向从出口烟道引出锅炉。
27.与现有技术相比,本发明具有以下有益效果:
28.余热锅炉技术具有显著的节约资源、节能和减排环保效益,它是利用工业生产中的余热来产生蒸汽的节能设备有效地解决废热利用的问题。以一年废热烟气利用量130万吨为计算基准,带来的经济环保效益如下:
29.1.资源效益
30.通过转化富能,收集余热及锅炉设备优化设计,并对余热进行梯度利用。价值极高,实现了资源循环再利用,是项目主要的经济效益来源。
31.从焦炉推出的红焦温度在950~1050℃,红焦所含显热相当于炼焦生产消耗总热量的35~45%,本项目采用干法熄焦余热回收技术比常规的湿法熄焦每年可节约水资源约126万吨(按每吨红焦耗水量0.5吨水,本项目按2台炉满负荷,年运行7000小时计算)。项目产品通过吸收余热产生高品质蒸汽用于工业生产或发电对外销售,社会经济效益显著。
32.2.节能效应
33.采用自然循环设计理念的项目产品成套设备,节能应包括以下两个方面:
34.余热回收:高温烟气从980℃被冷却到170℃,可产生92吨/小时高品质蒸汽,按年运行7000小时计,每年可产生257.6万吨蒸汽,折合节约25.76万吨标煤(按1吨标煤产生蒸汽10吨计)。
35.每年节约25.76万吨标准煤,(按每吨标准煤800元计算)折合约2亿元。
36.3.环保效益
37.项目产品减少排放环保效益分以下方面:
38.比传统的湿法熄焦技术相比,减少了大量的粉尘、酚类、氰化物、硫化物等有毒、有害气体的排放,大大减少了对环境的污染和对设备的腐蚀。
39.实现氮氧化物及其它生化物质达标排放,减少空气及水环境污染;
40.余热利用节约标煤减少排放,按每年节约25.76万吨标准煤计算,折合减排二氧化碳661182吨,减排二氧化硫5152吨,减排氮氧化合物339吨。
附图说明
41.图1是本发明一种带再热干熄焦余热锅炉的整体结构图;
42.图2是本发明一种带再热干熄焦余热锅炉的横截面图;
43.图3是本发明一种带再热干熄焦余热锅炉的过热器上防磨装置布置;
44.附图说明:1-锅筒,2-除氧器,3-钢结构,4-水冷壁吊挂装置,5-吊挂管, 6-高温过热器,7-高温再热器,8-水冷壁,9-低温过热器,10-低温再热器,11
‑ꢀ
鳍片管蒸发器,12-高压省煤器,13-出口烟道,14-入口烟道,15-过渡烟道, 16-省煤器墙板,17-平台扶梯,18-管道系统。
具体实施方式
45.下面结合具体实施例对本发明的技术方案作进一步说明。以下实施例仅在于提供一种可能的方案,并非是对本发明的限定。
46.参考图1-3,
47.熄焦工艺流程中出来的烟气温度大约880~980℃,通过内衬砖墙的烟气通道从上端进入锅炉入口烟道。在入口段,气流转过90
°
,改为向下流动,首先将热量传递给由前墙水冷壁拉稀而成的预置蒸发器的受热面,然后依次流经由水冷壁包围的高温过热器、高温再热器、低温过热器、低温再热器和鳍片管蒸发器,锅炉的水冷壁设计成作为蒸发器的受热面管,吸收烟气流程中的辐射放热。随后烟气进入下部的高压省煤器,吸收烟气的剩余热量加热给水。
48.烟气经过上述的冷却过程后,烟温降到180℃以下后,转过90
°
,沿水平方向从出口烟道引出锅炉。
49.水/蒸汽混合回路:
50.由除氧器来的除氧水送至锅炉给水泵,升压后供给高压省煤器。给水在省煤器中加热后进入锅筒。锅筒的水通过自然循环蒸发系统加热,成为汽水混合物后,再送回锅筒,自然循环蒸发系统包括如下:
51.1.鳍片管蒸发器系统:
52.锅筒—蒸发器下降管—鳍片管蒸发器入口集箱—鳍片管蒸发器受热面—鳍片管蒸发器出口集箱—鳍片管蒸发器上升管—锅筒
53.2.水冷壁系统:
54.锅筒—水冷壁下降管—水冷壁入口集箱—水冷壁—水冷壁出口集箱—水冷壁上升管—锅筒
55.3.吊挂管系统:
56.锅筒—水冷壁下降管—吊挂管入口集箱—吊挂管—吊挂管出口集箱—吊挂管上
升管—锅筒
57.汽水混合物在锅筒中进行汽水分离,饱和蒸汽送往低温过热器,而被分离出来的水作为炉水落入锅筒,再次提供给循环系统。
58.饱和蒸汽在低温过热器中经过过热后进入减温器,低温过热器和高温过热器之间设置减温器。减温水管路向减温器喷水,使锅炉出口蒸汽达到设定温度。
59.经过减温的过热蒸汽在高温过热器中进行进一步过热,达到设定温度的主蒸汽,通过主蒸汽压力调节阀控制压力,作为发电用蒸汽送往汽轮机。
60.系统组件描述:
61.锅筒:
62.锅筒材料适应超高参数的要求,封头采用球形封头,中央有φ425的入孔。
63.循环水通过锅筒底部的3个管座进入下降管,汽水混合物通过7个横向布置的管座回到锅筒。在锅筒内部,汽水混合物首先受到挡板阻隔折流以利于水位的稳定并使汽水进行初步分离。随后,初步分离出来的蒸汽经过布置在锅筒蒸汽空间的由波纹板和细密铁丝网构成的demister,使蒸汽中剩余的水分得到进一步分离,最大程度上获得干燥的饱和蒸汽。经过汽水分离后,饱和蒸汽由位于锅筒顶部一个单独的管座引出锅筒。
64.给水通过一个管座进入锅筒的水空间。
65.锅筒底部的其它管座分别与排污管和紧急放水管相连。压力表和安全阀的管座布置在锅筒顶部。在汽空间和水空间还分别装有5对横向排列的管座,用于测控水位,锅筒上共布置2只就地双色液位计,2只平衡容器,1只电接点液位计。
66.锅筒上布置有低压辅助蒸汽管座,在锅炉启动前以及锅炉短期停炉期间通入的低压饱和蒸汽或过热蒸汽,用以锅炉启动前预热和停炉时防结露。
67.锅筒通过支座支撑在顶部平台上。
68.水冷壁:
69.水冷壁由管子和扁钢组成。水冷壁采用悬吊结构,通过侧墙水冷壁上集箱和后墙水冷壁折弯处的吊杆悬吊于顶部梁格上,自由向下膨胀。
70.在烟气入口的部位,前墙水冷壁向后折弯15
°
形成预置蒸发器从后墙穿出,而后墙水冷壁在顶部向前倾斜15
°
延伸至烟气入口侧,形成炉顶。水冷壁下部为环形集箱,形成的烟气通道将包括高温过热器、高温再热器、低温过热器、低温再热器、鳍片管蒸发器和部分吊挂管在内的受热面都包围在其中,密封性能好,同时由于水冷壁内汽水混合物的冷却作用,使锅炉保温层厚度大大减小。
71.锅炉通过两根集中下降管下部的分配管向水冷壁下部环形集箱供水,水在水冷壁中受热后形成汽水混合物进入上部的集合集箱,最后由顶部的汽水连接管引入到锅筒。
72.蒸发器:
73.鳍片管蒸发器设计为悬吊式结构,通过固定在吊挂管上而悬吊于锅炉顶部。
74.锅筒炉水由两根下降管引出,通过连管分别引入蒸发器。鳍片管蒸发器错列布置,工质从蒸发器底部流向顶部,与烟气逆向流动。在鳍片管蒸发器中形成的汽水混合物进入出口集箱再由汽水连接管引入锅筒中进行汽水分离。
75.吊挂管:
76.吊挂管向上依次悬吊低温再热器、低温过热器、高温再热器和高温过热器。吊挂管
进口集箱底部焊接吊板,通过销轴与鳍片管蒸发器管夹连接,悬吊鳍片管蒸发器。
77.过热器:
78.过热器分低温过热器和高温过热器,均为光管蛇形管束,错列布置,通过吊挂管悬吊于锅炉顶部。低温过热器顺流错列布置,受热面管子为12cr1movg。高温过热器逆错列流布置,受热面管子材料sa335m-t91。
79.从锅筒上部引出的干饱和蒸汽先进入低温过热器进口集箱,与烟气逆向流动进入低温过热器出口集箱。经过减温器减温后进入高温过热器进口集箱,随后与烟气逆向流动进入高温过热器出口集箱,由主蒸汽管道引出。
80.再热器:
81.再热器分低温再热器和高温再热器,均为光管蛇形管束,错列布置,通过吊挂管悬吊于锅炉顶部。低温过热器顺流错列布置,受热面管子12cr1movg,高温过热器逆错列流布置,受热面管子sa335m-t91。
82.从汽轮机抽气来的冷再热蒸汽以360℃进入低温再热器进口集箱,与烟气逆向流动进入低温再热器出口集箱。经过减温器减温后进入高温再热器进口集箱,随后与烟气逆向流动进入高温再热器出口集箱,由再热主蒸汽管道引出。
83.高压省煤器:
84.高压省煤器布置在锅炉下部由省煤器墙板构成的低温区域内。省煤器管束为螺旋鳍片管,由多组管排向上斜向绕制成错列管束,中间用压制弯头连接。给水进入省煤器进口集箱后逆向烟气向上流动,进入省煤器出口集箱后,通过连管进入锅筒水空间。
85.省煤器为悬吊式结构,通过螺旋鳍片管管夹将管束悬挂于横梁上,横梁两端固定在省煤器墙板上,再通过省煤器墙板将力传递到钢架平台。
86.防磨装置:
87.为防止烟尘(焦粉)对锅炉受热面所造成的磨损,除了在锅炉总体设计时选择合理的烟速之外,还采取了许多防磨措施:
88.由于干熄焦的特殊工艺,对干熄焦锅炉内部二次过热器和膜式壁及吊杆的耐磨损、耐冲刷应充分考虑。在预置蒸发器和高温过热器前2排上布置有防磨盖板,同时高温过热器前四排管子采用超音速电弧喷涂,在烟气通道的四周为防止形成烟气走廊,均布置有烟气挡板(见图3)。
89.在烟气进口部位、由高温过热器及膜式壁所包围的区域。
90.锅炉烟气入口处水冷壁内表面采用耐磨浇注料进行全方位防磨;烟道和省煤器墙板:
91.锅炉在循环气进口处布置有进口烟道,与熄焦系统的烟道相连。进口烟道通过两根吊杆吊挂于顶部梁格下面。省煤器布置在省煤器墙板内,省煤器墙板与水冷壁环形集箱之间布置过渡烟道,中间布置膨胀节,以吸收水冷壁和省煤器之间的膨胀。膨胀节为非金属柔性膨胀节,具有三向补偿和吸收热膨胀推力的作用。锅炉出口烟道为防止烟气偏流,布置有导流板。
92.炉墙和保温:
93.锅炉水冷壁段为敷管炉墙,下部省煤器墙板处为框架装配式炉墙。炉墙结构用抓钉敷设保温材料,并用压板张网缩紧,外包彩钢板。除进口烟道需要耐火浇注料和异形砖料
外,其余大部分用的是保温材料。锅筒、管道的保温采用硅酸铝耐火纤维毯,外包铝合金护板。集箱及水冷壁外侧保温采用硬质无石棉硅酸钙,增加保温体的强度。
94.锅炉范围内管道:
95.锅筒设置了安全阀,就地水位计,电接点水位计,水位平衡容器,排气,压力表、疏水,连续排污,紧急放水管等管座。安全阀排汽管引至消音器。
96.在主蒸汽管道、饱和蒸汽管道、锅筒连续排污、给水等处设置取样装置。各取样点的取样管引至取样台。锅筒连续排污、紧急放水、蒸发器的定期排污、过热器和省煤器的疏放水管等均纳入排污疏水系统。加药管路接入给水总管。
97.主蒸汽管道上设置有安全阀和启动排汽管路,排汽均引至消音器。
98.在所有必须的地方装设了疏水管和排气管以保证彻底排尽积水及空气。
99.钢架和平台扶梯:
100.锅炉本体钢架和护板由h型钢和钢板焊接而成,共9根立柱,上下由横梁相连,组成一整体构架。构架按8度地震烈度要求设防。
101.平台扶梯是为适应锅炉运行和检修方便而设置的,除部分位置采用花钢板外,其余均采用栅架平台。平台、走道的端部是封闭型,走道和平台的宽度不小于1000mm,走道、平台的扶梯均带有栏杆,梯子与水平面的夹角不大于45
°
。
102.管道系统增设高低压旁路系统,高低压旁路在本项目中起3种作用:在机组启动阶段,汽机尚不能带负荷,这时通过高低压旁路使锅炉产生的蒸汽减温减压后进入冷凝器冷凝成水,再通过给水系统回到锅炉,起到避免蒸汽放空,同时回收工质的作用;防止再热器干烧,在锅炉启动阶段,通过高低压旁路,可使再热器一直有蒸汽流动,从而达到保护过热器的作用;在汽轮机故障时,起到停机不停炉的作用。
103.以上仅为本发明的优选实施方式,旨在体现本发明的突出技术效果和优势,并非是对本发明的技术方案的限制。本领域技术人员应当了解的是,一切基于发明技术内容所做出的修改、变化或者替代技术特征,皆应涵盖于本发明所附权利要求主张的技术范畴内。
再多了解一些
本文用于企业家、创业者技术爱好者查询,结果仅供参考。