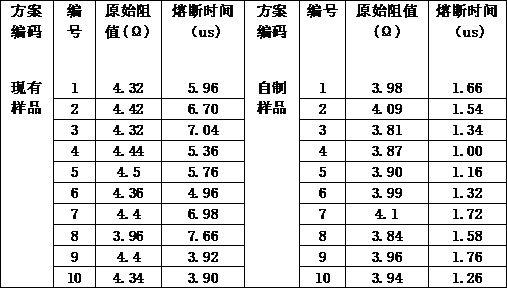
1.本发明涉及贴片保险丝设备及其制备技术领域,特别涉及采用pcb线路板工艺制备的一种小电流高分子贴片保险丝及其制备方法。
背景技术:
2.表面贴装熔断器主要应用于印刷电路板和其它电路的过流保护,其原理在于当电路发生故障或异常时,熔断器金属熔体自身熔断切断电流以实现保护电路。金属熔体的周围都被其基体部分的高分子材料或陶瓷材料所紧紧围贴着,即使是已经熔化的金属也无法向两端收缩,只能依靠向周围材料的扩散渗透或被周围材料吸收,如果在这个过程中过电流消失了(例如瞬间脉冲现象)或者产生的热量被基材迅速散掉,而扩散或吸收的过程尚在进行过程中,此时就会造成电阻变大而熔体没有完全熔断的现象。
3.此外,在表面贴装保险丝中,毫安级别的保险丝因电流低,所以发热量小,陶瓷基板的散热较快,对保险丝熔断效果有影响。再有,现有的表面贴装保险丝使用玻璃釉做隔热层会存在玻璃熔化吃银的现象,对熔断器的阻值影响比较大,所以在陶瓷基板上面生产的毫安级别的保险丝存在良率不高,性能不稳定的问题。同时毫安级别的保险丝由于银的阻值较低,所以行业多采用价格昂贵的金、铂、钯等贵金属作为熔丝材料,成本较高,良率也不好控制。从而使该类的产品价格居高不下,不利于电子行业的发展。
4.因此,在研发过程及生产中,发明人采用pcb材质的基板替代原有的陶瓷基板。但是在实现本发明的过程,发明人发现现有技术中采用pcb材质基板及采用常规工艺贴装保险丝的工艺至少还存在有以下问题:1、高分子材质的器件由于本身较轻,制备和测包过程中容易产生静电,引起返料和抛料的问题。在回流焊过程中容易出现歪焊、缺焊等不良的现象,影响客户的正常使用。为解决这种问题,往往在端电极位置打孔并灌注导电浆料,然后通过电镀ni、sn增加端头的导电性,从而造成制备成本的增加,推广性能较差。
5.2、常规表面贴装保险丝采用厚膜工艺印刷,氧化铝陶瓷为基板,金属银、金等制备成电子浆料进行印刷形成熔丝,玻璃浆料印刷在陶瓷基板表面制备成灭弧层和保护层。由于金银的导电性能较好,制备小电流的保险丝尤其是毫安级别的产品存在严重的不足,在厚膜印刷工艺中生产250ma的产品已经是极限,厚膜印刷形成的熔丝目前的技术印刷的线宽最窄只能实现50um,厚度最薄只能实现5um,而且对电子浆料的要求比较高,实现难度较大,厚度和宽度的均匀性也无法保证,对于制备毫安级别的保险丝表现的明显不足,而且生产良率较低,品质无法保证,无法满足大规模生产的需要。
6.有鉴于此,如何解决现有技术存在的问题,便成为本发明所要研究解决的课题。
技术实现要素:
7.本发明的目的是提供一种小电流高分子贴片保险丝及其制备方法以及相关的电子产品。
8.为达到上述目的,本发明的第一方面提出了一种小电流高分子贴片保险丝的制备方法,其创新点在于,该方法包括以下步骤:步骤一,制备基板采用pcb覆铜板作为基板,所述基板上具有多个能够独立分割成具备保险丝功能的单元格;步骤二,蚀刻熔丝通过蚀刻工艺在所述基板上蚀刻出熔丝,使熔丝以线条的方式呈几何形状布置于每个单元格处;步骤三,修饰熔丝采用激光对每个单元格上的熔丝进行修饰,使得每个单元格上的熔丝线条均匀,以便获得阻值一致的熔丝;步骤四,印刷助熔层选取由低温易熔金属、有机溶剂、固化剂混合制备成的助熔浆料,将助熔浆料印刷至每个单元格上熔丝表面的中央位置以形成助熔层;步骤五,印刷阻燃保护层将每个单元格的两端定义为非印刷区域,将每个单元格上熔丝和助熔层的表面定义为印刷区域,将阻燃材料印刷至印刷区域,阻燃材料固化后形成阻燃保护层;步骤六,切割基板将印刷完成的基板分割成独立的单元格,每个单元格形成器件胚体,各器件胚体具有位于两端的端头;步骤七,金属化端头在器件胚体的端头设置至少部分覆盖该端头的金属电极。
9.本发明的第二方面提出了一种小电流高分子贴片保险丝,该贴片保险丝采用如本发明第一方面所述的制备方法制成。
10.本发明的第三方面提出了一种电子产品,该电子产品包含本发明第一方面所述的贴片保险丝。
11.本发明的有关内容解释如下:1.通过本发明的上述技术方案的实施,采用pcb材质的基板替代原有的陶瓷基板,环氧材质的pcb基板的热导率在0.2w/(m.k)左右,具有很好的保温效果,通过覆铜板工艺实现熔丝,精度控制高,可以实现最细15um宽的熔丝设计,可以准确的实现熔断时间的控制;同时,针对现有技术中存在的机身问题,采用pcb材质作为基板,通过覆铜工艺、表面蚀刻工艺、厚膜印刷工艺、以及端涂工艺制备的高分子贴片保险丝,具有阻值差异小、熔断时间可控度高、外观和焊性不良率低等优点。
12.2. 在上述技术方案的第一方面中,在所述步骤一中,在所述pcb板的单面涂覆有铜层,铜层厚度为10~20mm,所述铜层的上表面电镀有防氧化层,防氧化层为表面镀金或镀银。
13.3. 在上述技术方案的第一方面中,在所述步骤二中,通过蚀刻工艺在基板上蚀刻出宽度为10~50um的熔丝,将该熔丝在每个单元格上布置成“几”字形;在所述步骤三中,采用激光将熔丝的拐弯处设置为圆角,将熔丝的直线条、曲线条的宽度修饰为一致,相较于现
有技术,熔丝存在明显的差别,本发明专利采用直线加圆角的“几”字形熔丝设计,并在中间区域加入助熔层,精度控制更高。
14.4. 在上述技术方案的第一方面中,在所述步骤四中,所述助熔浆料的重量份数配比如下:双酚a环氧树脂
ꢀꢀꢀꢀ
5~10份有机溶剂
ꢀꢀꢀꢀꢀꢀꢀꢀꢀꢀ
10~20份固化剂
ꢀꢀꢀꢀꢀꢀꢀꢀꢀꢀꢀꢀ
1~5份低温易熔金属粉体
ꢀꢀ
60~80份;按照重量份数称取上述材料混合均匀后,再通过研磨制备出所述助熔浆料。其中,有机溶剂采用dbe、松油醇、十二醇酯等,固化温度80℃~150℃,固化时间30~120min不等,温度高固化时间就短;固化剂为有机胺类固化剂,有机胺类固化剂采用有机脂肪胺、脂环胺、芳香胺和聚酰胺等,用于环氧树脂80℃~150℃的固化。且该助熔层采用厚膜印刷工艺,印刷在熔丝层的表面,通过丝印技术对图形的外观和厚度控制更好。
15.5. 在上述技术方案的第一方面中,在所述步骤四中,所述低温易熔金属粉体选取锡(sn)、锡铋合金(sn-bi)、锡-银-铜合金(sn-ag-cu)中的一种或多种形成的2~4um的球形粉体。
16.6. 在上述技术方案的第一方面中,在所述步骤五中,所述阻燃材料采用具有阻燃功能的环氧树脂,通过丝网印刷方式将阻燃材料印刷至每个单元格的所述熔丝及助熔层表面,经80~150℃固化30~120min后形成阻燃保护层,同时在基板的边缘印刷切割对位线,方便后续单元格分离,能有效的保证产品尺寸的一致性。在本发明中,阻燃材料选用具有阻燃功能的环氧树脂,其他阻燃材料不适应该产品;固化温度80~150℃,固化时间:30~120min,温度越高时间越短。
17.7. 在上述技术方案的第一方面中,所述方法还包含印刷标识步骤,印刷标识这一步骤位于制备基板和切割基板之间的工序中,所述印刷标识为在所述基板上所述熔丝的背面印刷标识字符。印刷标识是产品分类的一种方式,为产品生产的必要环节,必须在基板制备后和产品切割前完成印刷,一般情况是根据刻蚀线路的阻值确定产品的型号,然后再印刷标识。所述的标识字符是通过丝网印刷在基板的熔丝背面的白色环氧树脂,根据产品的型号,印刷不同的字符,然后经120℃温度固化1h后,形成标识字符。
18.8.在上述技术方案的第一方面中,在所述步骤七中,在器件胚体的端头位置涂覆低温固化材料以形成位于侧面的侧面电极,其中低温固化材料采用低温固化银胶,固化后电镀上导电金属材料以形成位于基板上下端面的端电极,侧面电极与端电极与熔丝电性连接。端电极采用端涂后再电镀的工艺,可以增加器件的耐焊性和降低抛料率,优化了器件的可适用性。
19.10.在上述技术方案的第一方面中,端头电极一般为对称设置,不对称实现的难度会更大一些,不实用,一般情况都是对称设计,端面电极的金属化有端涂、溅射、喷涂等工艺,根据产品不同的性能,分为不同的金属化方式,对于本发明的贴片保险丝来说端涂工艺效果最好。
20.11. 在上述技术方案的第二方面中,所述贴片保险丝具有:单元格,所述单元格为由pcb板制得的基板独立分割后具备保险丝功能的最小单
元;熔丝,所述熔丝通过蚀刻工艺设置于所述单元格表面,所述熔丝的宽度在其长度方向上均匀一致,所述熔丝呈“几”字形,在所述熔丝的拐弯处设置有圆角;助熔层,所述助熔层印刷至单元格上熔丝的中央位置;阻燃保护层,所述阻燃保护层印刷覆盖于熔丝和助熔层的表面;侧面电极,所述侧面电极位于所述单元格的至少一处端头部位,所述侧面电极与所述熔丝电性连接;端电极,所述端电极位于所述单元格的至少一处端头的上表面和下表面,所述端电极与所述熔丝电性连接。
21.12. 在上述技术方案的第三方面中,所述电子产品的型号,s1206pf系列、s0603pf系列以及s0402pf系列的贴片保险丝均可以,但是本发明不以此为限,该电子产品还包含其他能够利用本发明第一方面的制备方法方案所生产出的贴片保险丝13.在本发明中,除非另有明确的规定和限定,术语“安装”、“相连”、“连接”、“固定”等术语应做广义理解,例如,可以是固定连接,也可以是可拆卸连接,或成一体;可以是机械连接,可以是直接相连,也可以通过中间媒介间接相连,可以是两个元件内部的连通或两个元件的相互作用关系,除非另有明确的限定。对于本领域的普通技术人员而言,可以根据具体情况理解上述术语在本技术中的具体含义。
22.14.在本发明中,术语“中心”、“上”、“下”、“轴向”、“底”、“内”、“外”等指示的方位或位置关系为基于附图所示的方位或位置装配关系,仅是为了便于描述本技术和简化描述,而不是指示或暗示所指的装置或元件必须具有特定的方位、以特定的方位构造和操作,因此不能理解为对本技术的限制。
23.15. 此外,术语“第一”、“第二”等仅用于描述目的,而不能理解为指示或暗示相对重要性或者隐含指明所指示的技术特征的数量。由此,限定有“第一”、“第二”的特征可以明示或者隐含地包括至少一个该特征。在本技术的描述中,“多个”的含义是至少两个,例如两个,三个等,除非另有明确具体的限定。
24.由于上述方案的运用,本发明与现有技术相比具有以下优点和效果:1、工艺简单:采用pcb覆铜板工艺作为基板材料,整个生产过程中避免了烧结的影响,节约能源,工艺控制度高,能准确控制熔丝的宽度、厚度等参数,保证产品的性能优良;2、成本较低:在制备毫安级别的保险丝时,采用铜材质替代了价格较高的au、pt、pd等贵金属,成本具有明显的优势,同时避免了高温烧结的能耗问题,使成本更低;3、基本性能参数稳定:采用刻蚀工艺制备出的保险丝,通过激光调阻工艺对熔丝进行修饰,所制备的保险丝冷态阻值较集中,从而实现熔断时间可控性高;采用助熔层辅助熔丝在大电流下快速熔断,实现了i2t相对较小的要求,从而实现熔断过程不拉弧。由于熔丝较薄,助焊层与pcb基板浸润性较差,熔丝熔断过程断点较宽,实现了熔断后的稳定性好阻值为gω级别;4、采用低温固化材料作为阻燃层,解决了熔断过程的灭弧问题,同时避免了高温烧结产生的氧化、熔蚀对熔丝造成的影响,使熔丝更加稳定;5、通过端涂低温固化银胶再电镀镍、锡的工艺实现端头金属化,解决了焊性和抛料的风险,优化了客户的使用性。
附图说明
25.附图1为本发明实施例中贴片保险丝的正面示意图;附图2为本发明实施例中贴片保险丝的结构示意图;附图3为本发明实施例中贴片保险丝的背面示意图;附图4为本发明实施例中贴片保险丝的第一种熔丝设计方案示意图;附图5为本发明实施例中贴片保险丝的第二种熔丝设计方案示意图;附图6为本发明实施例中贴片保险丝的第三种熔丝设计方案示意图;附图7为本发明实施例中贴片保险丝的第四种熔丝设计方案示意图;附图8为本发明实施例一中的流程示意框图;附图9为本发明实施例二中的流程示意框图。
26.以上附图各部位表示如下:1 单元格101 非印刷区域102 印刷区域2 熔丝3 助熔层4 阻燃保护层5 侧面电极6 端电极7 标识字符。
具体实施方式
27.为使本技术的上述目的、特征和优点能够更加明显易懂,下面结合附图对本技术的具体实施方式做详细的说明。在下面的描述中阐述了很多具体细节以便于充分理解本技术。但是本技术能够以很多不同于在此描述的其它方式来实施,本领域技术人员可以在不违背本技术内涵的情况下做类似改进,因此本技术不受下面公开的具体实施例的限制。
28.实施例一如附图8所示的流程示意框图,本发明实施例一提出了一种小电流高分子贴片保险丝的制备方法,该方法包括以下步骤:s100,制备基板采用pcb覆铜板作为基板,所述基板上具有多个能够独立分割成具备保险丝功能的单元格(制备完成后该单个单元格即为一个保险丝);在s100中,在所述pcb板的单面涂覆有铜层,铜层厚度为20mm,所述铜层的上表面电镀有防氧化层;s200,蚀刻熔丝通过蚀刻工艺在所述基板上蚀刻出宽度为50um的熔丝熔丝,使熔丝以线条的方式呈几何形状布置于每个单元格处,且该熔丝布置成“几”字形,具有直线条和曲线条;s300,修饰熔丝采用激光对每个单元格上的熔丝进行修饰,使得每个单元格上的熔丝线条均匀,以便获得阻值一致的熔丝;在s300中,采用激光将熔丝的拐弯处设置为圆角,将熔丝的直线
条、曲线条的宽度修饰为一致;s400,印刷助熔层选取由低温易熔金属、有机溶剂、固化剂混合制备成的助熔浆料,将助熔浆料印刷至每个单元格上熔丝表面的中央位置以形成助熔层;在所述步骤s400中,按照重量份数称取双酚a环氧树脂10份、有机溶剂20份、固化剂5份、低温易熔金属粉体80份,上述材料混合均匀后,再通过研磨制备出所述助熔浆料。其中,有机溶剂采用dbe、松油醇、十二醇酯等,固化温度150℃,固化时间30min,温度高固化时间就短;固化剂为有机胺类固化剂,有机胺类固化剂采用有机脂肪胺、脂环胺、芳香胺和聚酰胺等。且该助熔层采用厚膜印刷工艺,印刷在熔丝层的表面,通过丝印技术对图形的外观和厚度控制更好;所述低温易熔金属粉体选取锡(sn)、锡铋合金(sn-bi)、锡-银-铜合金(sn-ag-cu)中的一种或多种形成的4um的球形粉体;s500,印刷阻燃保护层将每个单元格的两端定义为非印刷区域,将每个单元格上熔丝和助熔层的表面定义为印刷区域,将阻燃材料印刷至印刷区域,阻燃材料固化后形成阻燃保护层;所述阻燃材料采用具有阻燃功能的环氧树脂,通过丝网印刷方式将阻燃材料印刷至每个单元格的所述熔丝及助熔层表面,经150℃固化30min后形成阻燃保护层,同时在基板的边缘印刷切割对位线,方便后续单元格分离,能有效的保证产品尺寸的一致性。在本发明中,阻燃材料选用具有阻燃功能的环氧树脂,其他阻燃材料不适应该产品;固化温度80~150℃,固化时间30~120min,温度越高时间越短;s550,印刷标识所述印刷标识为在所述基板上所述熔丝的背面印刷标识字符。印刷标识是产品分类的一种方式,为产品生产的必要环节,必须在基板制备后和产品切割前完成印刷,一般情况是根据刻蚀线路的阻值确定产品的型号,然后再印刷标识;所述的标识字符是通过丝网印刷在基板的熔丝背面的白色环氧树脂,根据产品的型号,印刷不同的字符,然后经120℃温度固化1h后,形成标识字符;s600,切割基板将印刷完成的基板分割成独立的单元格,每个单元格形成器件胚体,各器件胚体具有位于两端的端头;切割采用机械切割的方式;s700,金属化端头在器件胚体的端头设置至少部分覆盖该端头且与熔丝电性连接的金属电极;在器件胚体的端头位置涂覆低温固化材料以形成位于侧面的侧面电极,其中低温固化材料采用低温固化银胶,固化后电镀上导电金属材料以形成位于基板上下端面的端电极,侧面电极与端电极与熔丝电性连接。
29.实施例二如附图9所示的流程示意框图,本发明实施例二提出了一种小电流高分子贴片保险丝的制备方法,该方法包括以下步骤:s100,制备基板采用pcb覆铜板作为基板,所述基板上具有多个能够独立分割成具备保险丝功能的单元格;在s100中,在所述pcb板的单面涂覆有铜层,铜层厚度为10mm,所述铜层的上表面
电镀有防氧化层;s200,蚀刻熔丝通过蚀刻工艺在所述基板上蚀刻出宽度为10um的熔丝熔丝,使熔丝以线条的方式呈几何形状布置于每个单元格处,且该熔丝布置成“几”字形,具有直线条和曲线条;s300,修饰熔丝采用激光对每个单元格上的熔丝进行修饰,使得每个单元格上的熔丝线条均匀,以便获得阻值一致的熔丝;在s300中,采用激光将熔丝的拐弯处设置为圆角,将熔丝的直线条、曲线条的宽度修饰为一致;s400,印刷助熔层选取由低温易熔金属、有机溶剂、固化剂混合制备成的助熔浆料,将助熔浆料印刷至每个单元格上熔丝表面的中央位置以形成助熔层;在所述步骤s400中,按照重量份数称取双酚a环氧树脂5份、有机溶剂10份、固化剂1份、低温易熔金属粉体60份,上述材料混合均匀后,再通过研磨制备出所述助熔浆料。其中,有机溶剂采用dbe、松油醇、十二醇酯等,固化温度80℃℃,固化时间120min;所述低温易熔金属粉体选取锡(sn)、锡铋合金(sn-bi)、锡-银-铜合金(sn-ag-cu)中的一种或多种形成的粒径2~4um的球形粉体;s450,印刷标识通过丝网印刷在基板的熔丝背面的白色环氧树脂,根据产品的型号,印刷不同的字符,然后经120℃温度固化1h后,形成标识字符;s500,印刷阻燃保护层通过丝网印刷方式将阻燃材料印刷至每个单元格的所述熔丝及助熔层表面,经80℃固化120min后形成阻燃保护层,同时在基板的边缘印刷切割对位线,方便后续单元格分离,能有效的保证产品尺寸的一致性;阻燃材料选用具有阻燃功能的绿色环氧树脂;s600,切割基板将印刷完成的基板分割成独立的单元格,每个单元格形成器件胚体,各器件胚体具有位于两端的端头;切割采用机械切割的方式;s700,金属化端头通过涂端机在器件胚体端头位置涂覆低温固化银胶,固化后形成侧电极,然后电镀ni、sn完成端头的金属化,形成成品。
30.实施例三本发明实施例三公开了一种小电流高分子贴片保险丝的制备方法,该方法包括以下步骤:s100,制备基板采用pcb覆铜板作为基板,所述基板上具有多个能够独立分割成具备保险丝功能的单元格;在s100中,在所述pcb板的单面涂覆有铜层,铜层厚度为15mm,所述铜层的上表面电镀有防氧化层;s200,蚀刻熔丝通过蚀刻工艺在所述基板上蚀刻出宽度为30um的熔丝熔丝,使熔丝以线条的方式呈几何形状布置于每个单元格处,且该熔丝布置成“几”字形,具有直线条和曲线条;
s300,修饰熔丝采用激光对每个单元格上的熔丝进行修饰,使得每个单元格上的熔丝线条均匀,以便获得阻值一致的熔丝;在s300中,采用激光将熔丝的拐弯处设置为圆角,将熔丝的直线条、曲线条的宽度修饰为一致;s400,印刷助熔层选取由低温易熔金属、有机溶剂、固化剂混合制备成的助熔浆料,将助熔浆料印刷至每个单元格上熔丝表面的中央位置以形成助熔层;在所述步骤s400中,按照重量份数称取双酚a环氧树脂7份、有机溶剂15份、固化剂3份、低温易熔金属粉体7份,上述材料混合均匀后,再通过研磨制备出所述助熔浆料。其中,有机溶剂采用dbe、松油醇、十二醇酯等,固化温度120℃,固化时间60min;所述低温易熔金属粉体选取锡(sn)、锡铋合金(sn-bi)、锡-银-铜合金(sn-ag-cu)中的一种或多种形成的粒径3um的球形粉体;s450,印刷标识通过丝网印刷在基板的熔丝背面的白色环氧树脂,根据产品的型号,印刷不同的字符,然后经120℃温度固化1h后,形成标识字符;s500,印刷阻燃保护层通过丝网印刷方式将阻燃材料印刷至每个单元格的所述熔丝及助熔层表面,经80℃固化120min后形成阻燃保护层,同时在基板的边缘印刷切割对位线,方便后续单元格分离,能有效的保证产品尺寸的一致性;阻燃材料选用具有阻燃功能的绿色环氧树脂;s600,切割基板将印刷完成的基板分割成独立的单元格,每个单元格形成器件胚体,各器件胚体具有位于两端的端头;切割采用机械切割的方式;s700,金属化端头通过涂端机在器件胚体端头位置涂覆低温固化银胶,固化后形成侧电极,然后电镀ni、sn完成端头的金属化,形成成品。
31.实施例四如附图1至附图3所示,本发明实施例四提出了一种由小电流高分子贴片保险丝的制备方法制成的贴片保险丝,所述贴片保险丝具有:单元格,所述单元格为由pcb板制得的基板独立分割后具备保险丝功能的最小单元;熔丝,所述熔丝通过蚀刻工艺设置于所述单元格表面,所述熔丝的宽度在其长度方向上均匀一致,所述熔丝呈“几”字形,在所述熔丝的拐弯处设置有圆角;助熔层,所述助熔层印刷至单元格上熔丝的中央位置;阻燃保护层,所述阻燃保护层印刷覆盖于熔丝和助熔层的表面;侧面电极,所述侧面电极位于所述单元格的至少一处端头部位,所述侧面电极与所述熔丝电性连接;端电极,所述端电极位于所述单元格的至少一处端头的上表面和下表面,所述端电极与所述熔丝电性连接。
32.在上述实施例四中,对于熔丝的线条布置方式,可参考附图4至附图7,给出了几种“几”字形设计的形状机构,但是本发明不以此为限,还可以是其他由均匀线条且包含有直线条和圆角曲线的组合。
33.在上述实施例四中,如附图3所示,需要在单元格的背面做印刷标识以做出产品分类,附图3中的“b”字仅为标识字符的一种示意,一般情况是根据刻蚀线路的阻值确定产品的型号,然后在印刷标识。
34.实施例五本发明实施例五提出了一种电子产品,该电子产品包含有由小电流高分子贴片保险丝的制备方法制成的贴片保险丝,s1206pf系列、s0603pf系列以及s0402pf系列的贴片保险丝均可以。
35.本发明技术方案为解决同类产品中存在的技术问题,采用pcb材质作为基板,通过覆铜工艺、表面蚀刻工艺、厚膜印刷工艺、以及端涂工艺制备的高分子贴片保险丝,具有阻值差异小、熔断时间可控度高、外观和焊性不良率低等优点。具体表现如下:(1)工艺简单:采用成熟的pcb板覆铜工艺,再通过刻蚀的方式,一次性制备出熔丝和电极,比传统的印刷、烧结等工序节省很多成本,节约能源;此外端电极采用低温银浆端涂工艺相对比打孔灌浆工艺简单很多,成本也比较低,可以大幅度降低器件的成本。该工艺避免了高温烧结时灭弧材料对熔丝层的影响,熔丝的状态保持较好。
36.(2)阻值稳定,pcb板表面平整度高于传统的陶瓷基板,表面覆铜后,厚度一致性好,通过表面均匀刻蚀,可使熔丝的厚度保持一致,然后利用激光对熔丝边缘进行修剪,同时避免的烧结过程中对熔丝的影响,从而形成的阻值相对稳定,良率高;(3)熔断时间可控性高,由于产品的阻值集中度高,通过激光对熔丝进行修剪,去除相关较宽的部分,熔断时产生的热量一致性高,从而实现熔断时间可控性;(4)i2t相对较小,为了使熔丝熔断时需求的热量小,本发明在熔丝表面印刷一层助熔层,该助熔层是有低温金属sn形成的一种电子浆料,利用锡的低熔点的特点,可以快速的促使熔丝较快的熔断。锡电子浆料在固化的过程中,再温度的作用下,可以对熔丝表面进行刻蚀,使表面形成类似于sn-cu合金的物质,导致熔丝在该区域的阻值高于其他部位,熔断过程中所需的热量相对较小,熔断时拉开的距离比较大,不容易产生拉弧,安全系数高;(5)额定电压较高,陶瓷基板制备的保险丝额定电压一般在72v左右,通过pcb工艺制备的保险丝,额定电压可以高达380v,可以防止熔断瞬间,以及熔断后,不会产生飞弧,对电路的保护更加可靠,使用的场合较广。
37.(6)熔断后的稳定性好,pcb板覆铜工艺制备的熔丝,与基板之间是通过粘合剂连接,熔断过程简单、熔断时拉开的距离较大,厚膜印刷工艺制备的熔丝是通过高温烧结后,通过玻璃粘结在基板表面,熔断过程散热和熔化玻璃需要吸收部分热量,熔断时通过灭弧玻璃吸收汽化的金属颗粒,拉开距离相对较小,从而容易产生在高压条件下的拉弧现象,熔断后阻值高达gω级别优于陶瓷基板工艺制备产品的mω级别,因此该发明专利设计的产品熔断后的稳定性明显优于陶瓷厚膜工艺制备的产品。
38.(7)抛料率和焊性不良率低,pcb材质的产品由于材质的原因,本身质地较轻,容易产生静电引起抛料的问题,本产品采用端涂工艺形成的电极与熔丝的端电极相连,结合电镀工艺形成完整的金属化电极,绝缘材质变为导电的器件,避免的静电的产生,同时由于本身重量的增加,从而大大降低产品的抛料率。端电极的加入又改善了产品在线路板表面的
焊性不良的问题。
39.相较现有技术,还存在有以下区别:1.熔丝存在明显的差别,本发明专利采用直线加圆角的熔丝设计,并在中间区域加入助熔层,精度控制更高;2.助熔层采用厚膜印刷工艺,印刷在熔丝层的表面,通过丝印技术对图形的外观和厚度控制更好;3.端电极采用端涂后再电镀的工艺,可以增加器件的耐焊性和降低抛料率,优化了器件的可适用于性。
40.对于本发明实施例的具体实施步骤可参考如下:本发明专利为了实现上述性能,提供的一种新型高分子贴片保险丝的制备方法,利用覆铜工艺制备pcb覆铜板、表面蚀刻工艺制备熔丝和电极、厚膜印刷工艺制备助熔层、保护层和标识,再以端涂工艺制备端电极,然后电镀ni、sn最终完成高分子贴片保险丝的制备,具有阻值差异小、熔断时间可控度高、外观和焊性不良率低等优点。具体实施如下:1、pcb覆铜板:本发明专利采用的基板为pcb覆铜板,所述的基板为单面覆铜,表面覆铜厚度为10-20um,表面镀金或银防止电极氧化,基板的尺寸按照要求制备成180*180mm的大小,方便后续单元格切割;2、所述的熔丝通过刻蚀工艺完成,熔丝的宽度为10~50um,根据产品的型号确定熔丝的宽度和长度,如图所示,长度可以根据弯曲的“几”字型个数确定(如熔丝设计图4至图7所示)。刻蚀完成后,为保证熔丝线条的均匀性,采用激光对熔丝进行修饰,从而使熔丝的图形一致性较好,拐弯处采用圆角化设计,可以减小对电流的阻碍,制备的产品阻值均匀度高,熔断时间均匀;厚膜印刷形成的熔丝目前的技术印刷的线宽最窄只能实现50um,厚度最薄只能实现5um,而且对电子浆料的要求比较高,实现难度较大,厚度和宽度的均匀性也无法保证,对于制备毫安级别的保险丝表现的明显不足。
41.3、所述的助熔层选择低温金属和合金浆料制备的浆料,通过丝网印刷在熔丝的中央位置。所述的助熔层浆料,由双酚a环氧树脂5~10份,有机溶剂dbe10~20份,固化剂1~5份,低温金属粉体sn、sn-bi或sn-ag-cu等合金的一种或多种形成的2~4um的球形粉体60-80份,通过三辊研磨机制备出的低温固化浆料,固化温度为120℃。该助熔层浆料里面的金属颗粒由于熔点比较低,在熔丝通电发热时率先熔化后融入熔丝层,从而降低熔丝的熔点,使熔丝快速断裂,有效的保护了电路。
42.4、阻燃保护层印刷,所述的保护层是通过丝网印刷在熔丝表面的绿色环氧树脂,同时经120℃温度固化1h后,形成的阻燃环氧保护层。同时在基板的边缘印刷切割对位线,方便后续单元格分离,能有效的保证产品尺寸的一致性。
43.5、标识字符的印刷,所述的标识字符是通过丝网印刷在熔丝背面的白色环氧树脂,根据产品的型号,印刷不同的字符,然后经120℃温度固化1h后,形成标识字符。
44.6、机械切割,将印刷完成的基板通过机械切割的方式分割成独立的单元,形成器件胚体。
45.7、端头金属化,通过涂端机在器件胚体端头位置涂覆低温固化银胶,固化后形成侧电极,然后电镀ni、sn完成端头的金属化,形成成品。电镀完成的器件端头的焊性较好,金属化的本身增加了产品的重量,可以减少抛料的风险。
46.同时,发明人对采用现有工艺技术制备的保险丝(称为现有样品)和由本方案制备而成的保险丝(称为自制样品)进行测量、测试,相关数据、测试结果参考如下:1、阻值对比数据见表1:表12、高电压熔断测试:现有样品,380v直流测试10%不良(不良现象为爆炸,跟拉弧性能有关);自制样品测试全部通过;其他常规产品(厚膜工艺制备)全部不良,抗拉弧能力明显较差。
47.3、成本方面:现有样品采用边缘打孔的方式,成本比较高;自制样品采用的端涂工艺制备的电极,成本相对较低。
48.上述实施例只为说明本发明的技术构思及特点,其目的在于让熟悉此项技术的人士能够了解本发明的内容并据以实施,并不能以此限制本发明的保护范围。凡根据本发明精神实质所作的等效变化或修饰,都应涵盖在本发明的保护范围之内。
再多了解一些
本文用于企业家、创业者技术爱好者查询,结果仅供参考。