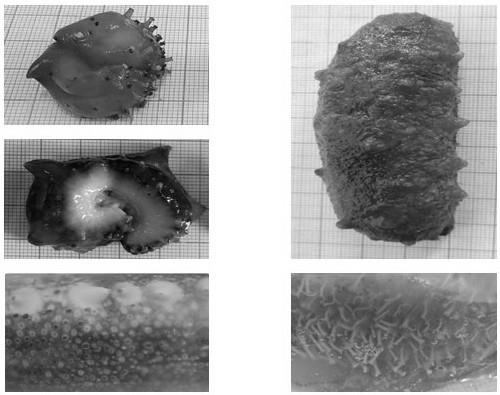
1.本发明涉及食品加工技术领域,具体涉及一种新鲜海参即食品的新型锁鲜方法。
背景技术:
2.根据2020年中国渔业统计年鉴数据显示,2019年我国海参养殖产量为17.17万吨,全产业链产值已突破500亿元,海参养殖业发展迅速,成为全球产量最高、最重要的海参生产国,人们对于海参的鲜美滋味和滋补保健效果的认可度日益加深。然而,截至目前为止,我国市面所售海参常见的产品形式主要以干制海参、盐渍海参和以干制海参或盐渍海参为原料制成的即食水发海参为主,鲜有以新鲜海参直接制作而成的即食产品。这是由于海参的生长和捕捞具有季节性,且捕捞后体壁极易在自身所含的自溶酶作用下分解溶化,难以保存,增加了运输贮藏和加工生产难度,且用新鲜海参直接加工普遍会发生口感过硬、不易食用等现象,因此90%的海参被加工成各种干制品、盐渍品和即食水发海参,鲜有新鲜状态的海参即食品在市面上出现,由此可见新鲜海参即食制品存在着巨大的发展潜力。
3.即食水发海参是由新鲜海参经干制或盐渍工艺处理后,再次经过水发工艺制作而成,其中,干海参加工过程包括去脏、清洗、煮制、腌制、烤制、拌灰和干燥等,历时21天,其水发过程也较为繁琐,需要经历三次反复高温水煮泡发过程,同时还需严格控制水发温度和时间,否则极易出现发制困难、色泽斑驳、口感差等质量问题,该过程需历时约15天,从新鲜海参到制作成即食海参共需36天之久。盐渍海参加工过程包括去脏、清洗、煮制、拌盐、腌制等,历时13天,其水分过程需经历脱盐、蒸煮、水发等步骤,用时3天,共需16天。可见,传统的即食海参加工方式生产效率低下,同时还增加了时间成本。不仅如此,传统干制和盐渍海参的加工过程还会导致新鲜海参独有的新鲜味道大量流失,大部分活性营养成分遭到破坏。新鲜味道是新鲜食材所固有的一种能够引起人身心愉悦的一系列特殊物质及其结构组成的活性刺激成分,这些物质极易因加工不当而被破坏流失。因此,保留食材新鲜味道的新型加工方式及其加工食品将成为市场的主流趋势。随着消费者对海参产品感官品质、营养保健以及食用便捷度追求的不断提升,新型海参产品所占市场的比重逐渐增加,推动了新型海参加工技术的发展。因此,以新鲜活海参为原料,开发新鲜海参锁鲜加工工艺和技术,直接利用新鲜海参开发具有独特新鲜味的营养加强型方便食品具有重要意义,存在着巨大的市场前景。
4.在研究过程中,我们发现了一项发明专利201310100683.3《海参低温真空加热蒸煮方法》,该专利旨在通过盐水漂烫、低温真空蒸煮和减压缓慢冷却等方式解决海参在低温条件下无法达到适宜口感,以及营养流失等问题。但该专利中,使用盐水漂烫会增加污水处理难度以及环境污染的风险;经蒸煮后的海参冷却温度过高,易造成口感变差和微生物超标等食品安全风险。此外,采用此方法制作出的即食海参依旧需要经过水发步骤,增加了生产用时,同时也导致部分营养物质继续流失。同时我们也发现了另一项发明专利201510738492.9《海参加工方法即食熟海参制品》的关于即食熟海参制品加工方法的发明专利,该专利指出能够通过将活海参放在清洁的暂养池或模拟海参生长环境的干净网箱中
饥饿暂养7~14天,并结合外界刺激去除活海参内脏中的泥沙,从而加工出不含泥沙并保留海参完整肠卵,同时最大程度保留海参营养和鲜度的海参即食产品。然而海参对生长环境的变化较为敏感,需要严格暂养环境的各项指标,难度较大。且暂养时间较长,停止投喂后海参会大量消耗自身营养物质,造成严重损失。此外,模拟海参生长环境所需成本较高,而暂养密度过大同样会导致海参大量死亡,因此该方法的可操作性较小,无法应用于海参即食产品的工业化生产。
5.经过多次实验研究发现,与传统的即食海参相比,本发明所述一种新鲜海参即食品的新型锁鲜方法将三重锁鲜技术通过流水线的加工方式实现了新鲜海参的锁鲜目标,最大程度地保留新鲜海参特有的新鲜味和营养物质,使海参拥有极佳的外观品质和爽脆口感,同时又可达到缩短加工周期,极大提高了生产效率、降低生产成本、提高自动化水平等效果。
技术实现要素:
6.本发明的目的在于是提供一种新鲜海参即食品的新型锁鲜方法,解决目前海参加工产品经长时间多重加工造成的新鲜味和营养物质损失的关键性技术难题。其通过小规格低温漂烫锁鲜方法、干冰真空低温临界介质快速冷却锁鲜方法或液氮真空低温介质快速冷却锁鲜方法,并辅以液氮快速速冻方法使新鲜海参在最短时间内加工为鲜食产品,加工出来的产品能够最大限度地保留海参本身的新鲜味道和营养成分,实现传统即食海参无法达到的外观、口感和海参鲜味和营养价值。本发明在加工过程中采用简便的低温漂烫、真空低温临界介质快速冷却和液氮速冻等操作步骤,取代了传统即食海参加工中的盐渍、干制、水发等繁冗耗时的加工过程,同时还能够节约大量能耗、提高生产效率、极大的缩短生产周期、提高自动化水平和产品品质。
7.本发明还提供一种使用本发明的海参加工方法得到的新鲜海参即食品。
8.为了实现上述目的和其他优点,本发明公开了上述一种新鲜海参即食品的新型锁鲜方法,其包括:第一步:将新鲜海参预处理。
9.第二步:将预处理的海参在低温条件下漂烫锁鲜。
10.第三步:将漂烫后的海参在干冰真空低温临界介质或者液氮真空介质条件下迅速冷却锁鲜。
11.第四步:将冷却后的海参进行调味包装并使用液氮进行快速速冻锁鲜。
12.其中,所述新鲜海参预处理步骤进一步包括将新鲜海参从嘴部沿腹部中线剪开,去除海参内脏、腹腔液,保留内壁筋膜并洗净泥沙。
13.其中,所述新鲜海参预处理步骤还进一步包括将洗净泥沙的海参竖直切成状,并在每块海参外壁沿中线切一道平行的切口,而在传统即食海参的制作过程以及专利201510738492.9《海参加工方法即食熟海参制品》和专利201310100683.3《海参低温真空加热蒸煮方法》中均为整个海参进行加工。本专利中每块海参的厚度为10~50mm,优选15~40 mm,优选20~30 mm。
14.其中,所述新鲜海参预处理步骤还进一步包括将切块后的海参用海参重量10%~40%的白糖去除海参粘液,优选10~30%,优选10%~20%。
15.其中,所述新鲜海参预处理步骤还进一步包括将切块后的海参用白糖搅拌硬化0.5~8 min,优选1~5 min,再优选2~3 min。
16.其中,所述第二步的低温条件下的漂烫锁鲜步骤进一步包括漂烫海参用的热水温度为70~100℃,优选80~100℃,再优选90~100℃。
17.其中,所述第二步的低温条件下的漂烫锁鲜步骤还进一步包括漂烫前海参温度为0~20℃,优选0~15℃,再优选5~15℃。
18.其中,所述第二步的低温条件下的漂烫锁鲜步骤还进一步包括将经过预处理的新鲜海参在海参重量的1~20倍的热水中低温漂烫,优选2~10倍,再优选2~4倍。
19.其中,所述第二步的低温条件下的漂烫锁鲜步骤还进一步包括将经过预处理的新鲜海参在热水中漂烫5s~120s,优选5s~60s,再优选10s~20s。
20.其中,所述第二步的低温条件下的漂烫锁鲜步骤还进一步包括将新鲜海参在热水中漂烫至温度为60~90℃,优选60~80℃。
21.其中,所述第三步的干冰真空低温临界介质条件下的冷却锁鲜步骤进一步包括可以采用第一种方式即干冰作为冷却临界介质对漂烫后的海参进行进行持续降温。
22.其中,所述第三步的干冰真空低温临界介质条件下的干冰冷却锁鲜步骤还进一步包括将漂烫后的海参在海参重量的1~10倍的冰水中进行冷却,优选1~5倍,再优选1.5~2.5倍。
23.其中,所述第三步的干冰真空低温临界介质条件下的干冰冷却锁鲜步骤还进一步包括将0.5~2倍海参重量的干冰放到水中进行持续冷却,优选0.5~1.5倍,再优选0.8~1.2倍。
24.其中,所述第三步的干冰真空低温临界介质条件下的干冰冷却锁鲜步骤还进一步包括将漂烫后的海参在真空低压条件下冷却,真空度为0~-0.1mpa,优选-0.03~-0.1mpa,再优选-0.06~-0.09mpa。
25.其中,所述第三步的干冰真空低温临界介质条件下的干冰冷却锁鲜步骤还进一步包括将漂烫后的海参在真空低温条件下冷却至温度为-2~15℃,优选-1~10℃,再优选2~4℃。
26.其中,所述第三步的干冰真空低温临界介质条件下的干冰冷却锁鲜步骤还进一步包括将漂烫后的海参在真空低温条件下冷却至2~4℃用时2~15min,优选4~12min。
27.其中,所述第三步的真空低温临界介质条件下的冷却锁鲜步骤还可以采用第二种方式即液氮真空作为冷却介质对漂烫后的海参进行进行持续降温。
28.其中,所述第三步的真空低温临界介质或者液氮真空低温临界介质条件下的液氮冷却锁鲜步骤还进一步包括将漂烫后的海参放入海参重量1~10倍的液氮中进行冷却,优选1~5倍,再优选1~3倍。
29.其中,所述第三步的真空低温临界介质条件下的液氮冷却锁鲜步骤还进一步包括将漂烫后的海参在液氮真空中冷却1~60s,优选3~30s,再优选5~15s。
30.其中,所述第三步的真空低温临界介质条件下的液氮冷却锁鲜步骤还进一步包括将漂烫后的海参在液氮中冷却至温度为-2~15℃,优选-1~10℃,再优选2~4℃。
31.其中,所述第四步的液氮条件下的速冻锁鲜步骤进一步包括将冷却后的海参进行调味,密封包装。
32.其中,所述第四步的液氮条件下的速冻锁鲜步骤还进一步包括将包装后的海参采用液氮进行速冻。
33.其中,所述第四步的液氮条件下的速冻锁鲜步骤还进一步包括将包装后的海参在0.5~10倍用量的液氮中进行快速速冻,优选0.5~5倍,再优选1~3倍。
34.其中,所述第四步的液氮条件下的速冻锁鲜步骤还进一步包括将包装后的海参在液氮速冻过程中的环境温度为-80~-196℃,优选-80~-100℃,再优选-85~-95℃。
35.其中,所述第四步的液氮条件下的速冻锁鲜步骤还进一步包括将包装后的海参在液氮中冷却1~30min,优选3~15min,再优选5~10min。
36.较现有技术而言,本发明至少包括以下有益效果:本发明与传统即食海参相比,通过干冰真空临界介质冷却锁鲜技术或液氮真空快速冷却锁鲜技术,辅以小规格低温漂烫锁鲜技术和液氮快速速冻锁鲜技术对新鲜海参即食品进行了锁鲜加工,最大限度的保留了海参的新鲜味和营养物质,解决了新鲜海参经干制或盐渍后再次水发的传统即食海参繁琐加工过程,以及对海参新鲜味和营养物质的破坏问题,提高海参外观和口感品质。
37.从图1可以看出,新鲜活海参的可溶性固形物含量为7%,传统即食海参中的可溶性固形物含量为0.4%~1.0%,专利201310100683.3《海参低温真空加热蒸煮方法》中新鲜海参经漂烫和冷却处理再发制7天后的可溶性固形物含量为1.8%,而通过本专利加工得到的即食海参由于细胞壁破坏程度较低,因此可溶性固形物含量高达5.8%,本发明与新鲜海参相比损失率较小,锁住了80%以上的可溶性鲜味和营养物质。通过进一步检测发现(表3),传统即食海参中的蛋白质含量为3.2~4.0g/100g,而本发明制备的新鲜海参即食品中的蛋白质含量达到了5.6g/100g,比统即食水发海参高出40%以上。此外,感官评定结果显示(表1和表2),采用本发明制备的新鲜海参即食品的新鲜味和口感也明显优于传统即食海参,极大地锁住了海参原有的鲜味,提升了新鲜海参即食品的外观和口感品质。
38.2、本发明在新鲜海参预处理步骤中,将海参切成厚度为20~30mm块状以辅助锁鲜效果。经本专利实验研究发现,将海参切成20~30mm厚度的块状能够将表面积增加1.5倍,使其在低温漂烫锁鲜步骤中能够在15s内快速完成熟化,减少在水中的停留时间,用最短的时间锁住海参的鲜味和营养。且漂烫后的大小便于人们直接食用,无需再加工处理。此外,以此厚度切块后的海参经锁鲜加工为成品后的口感和风味能够达到最佳品质。而在传统即食海参的制作过程以及专利201510738492.9《海参加工方法即食熟海参制品》和专利201310100683.3《海参低温真空加热蒸煮方法》中均为完整海参进行加工,在食用前还需进行切块等后续处理,不够便捷,且采用完整海参进行加工易造成内部和表面熟化程度不同,造成口感不一、微生物含量不稳定等问题。
39.3、本发明在新鲜海参预处理步骤中,通过添加白糖与新鲜海参混合搅拌,能够快速有效地去除掉海参中的苦腥味物质,凸显出新鲜海参中独有的新鲜味道,同时中和海参本身的咸度,并促使排出海参中的一部分粘液,将海参的肉壁结构变得更加紧致,有利于新鲜海参在漂烫后达到脆嫩爽口的感官效果。
40.4、本发明将加工前的海参暂养温度和加工过程中的环境温度控制在0~15℃,优选10℃。这是因为海参的最佳生长温度为5~15℃,超出此温度范围后海参通常会进行冬眠/夏眠,且海参捕捞季节也通常选在该温度范围内,此时的海参肉质及营养品质均保持在最佳
状态。
41.5、本发明采用中和漂烫技术对新鲜海参进行轻熟化,灭活新鲜海参中的自溶酶,防止海参因自溶导致的口感变差。漂烫前热水温度为90~100℃,新鲜海参温度为0~15℃,两者混合后能够使中心温度达到60~80℃。与传统即食海参及专利201510738492.9《海参加工方法即食熟海参制品》加工过程中采用高温高压方式蒸煮海参相比,本发明中采用低温漂烫加工出的海参不仅可以保持海参中含有的水分及原有的新鲜味道和色泽,使海参更加脆嫩鲜美,还能减少营养物质和生物活性成分的破坏流失,尤其是热敏感性和水溶性成分,避免有害物质生成。此外,利用该方法同样能够有效控制微生物含量,保证新鲜海参即食品的食用安全性,使锁鲜后的新鲜海参即食品符合gb 10136食品安全国家标准动物性水产制品中对于微生物的限定标准。
42.6、本专利中在小规格低温漂烫锁鲜步骤中,采用不含盐的自来水进行漂烫,而传统即食海参及专利201310100683.3《海参低温真空加热蒸煮方法》的漂烫加工中大多使用0.5~5%的盐水进行漂烫。研究表明,当污水中盐度超过0.6%时会抑制微生物对污水的处理效果,甚至高盐度的污水会致其死亡,增加了污水处理难度和成本,极易造成环境污染,危及生态环境。
43.7、本发明中在低温漂烫锁鲜步骤中,漂烫时间仅为5 s~120 s,优选5 s~60s,再优选10 s~20 s,最优选15s。而在传统即食海参以及专利201510738492.9《海参加工方法即食熟海参制品》和专利201310100683.3《海参低温真空加热蒸煮方法》中均需漂烫/蒸煮10~60min。与传统即食海参及上述专利相比,本发明在漂烫锁鲜步骤中具有更强的环保性和先进性,能够节省大量能源资源,减少碳排放量。
44.8、本发明在真空低温临界介质冷却锁鲜步骤中的第一种方法选用干冰水作为降温介质。干冰放入水中会形成固相、气相和液相三相介质,其中,固相的干冰分散在液相中,能够在干冰周围快速形成一种低温团,并能够持续吸热以达到稳定维持低温的效果,解决传统即食海参及专利201510738492.9《海参加工方法即食熟海参制品》加工过程中采用冰水冷却导致温度不稳定、降温效果持续性差的问题。而干冰挥发形成的气相能够在水中产生持续振动效果,推动了液相的水不断流动,加速温度达到平衡状态,同时防止海参块相互速冻粘结,影响产品品质。
45.9、本发明在真空低温临界介质冷却锁鲜步骤中的第一种方法选用干冰水作为降温介质能够将水温逐渐恒定在-2~15℃,改进专利201310100683.3《海参低温真空加热蒸煮方法》中仅将蒸煮后的海参冷却至20~50℃的条件。食品领域技术人员皆知微生物的最佳繁殖温度为21.1~52.7℃,在该温度范围内微生物繁殖能力旺盛,新鲜海参极易发生口感变差、腐败变质等不利影响,因此本发明在冷却锁鲜步骤中避开了该温度范围,选择将海参冷却至-2~15℃抑菌温度,能够避免微生物的大量繁殖破坏海参风味和口感等品质,产生食品安全问题。同时该温度范围也是海参的最适生长温度,在此温度下海参的品质最好。
46.10、本发明在真空低温临界介质快速冷却锁鲜过程中的第一种方法采用干冰水进行冷却时还能够快速在新鲜海参表面形成一种致密保护层,将新鲜味和营养物质牢牢地包裹在海参中,防止大量流失。同时,海参在真空状态下,借助海参内外压力差的作用能够迅速将海参表面的肉刺和触手激发出来,令海参中的蛋白质形成致密有序的结构,产生愉悦的爽脆口感。
47.11、本发明在真空低温临界介质快速冷却锁鲜过程中的第二种方法选用液氮作为降温介质。液氮能够更加快速地在海参表面形成一层冰晶层,将新鲜味和营养物质牢牢地锁在海参内部,防止鲜味和营养物质流失。
48.12、本发明在液氮快速速冻步骤中利用液氮将密封包装好的新鲜海参即食品进行快速速冻。液氮温度为-196℃,在使用液氮进行速冻时,环境温度可控制为-80~-196℃,优选-80~-100℃,再优选-85~-95℃。在此环境温度下,产品的中心温度能够迅速降至冻结温度以下,达到快速速冻的效果,防止鲜味物质损伤以及蛋白质网络结构发生改变而导致的水分流失、口感变差,从而提高海参品质。此外,由于本发明中速冻环境温度较低,产品完全冻结仅需用时7min。而在常规-18℃速冻条件下则至少需要12h,在-30~-40℃速冻条件下也需要2~4h。因此,采用液氮进行速冻不仅可以大大缩短生产时间,显著提高生产效率,还能够减少缓慢速冻对海参蛋白质结构和细胞壁的损伤,防止海参鲜食品在解冻后丧失脆嫩的口感,同时也将新鲜海参的解冻损耗率降低了1~5%,海参原料利用率提高了5~10%。并且,与传统即食海参相比,从新鲜海参到即食产品的成品出成率也提高了10%以上。
49.14、本发明区别于传统即食海参加工及专利201310100683.3《海参低温真空加热蒸煮方法》之处在于,本发明的新鲜海参经第一步和第二步处理后即可鲜食,无需再经历发制过程,该方法能够减少营养物质的进一步流失,有效提高生产效率,同时避免造成资源浪费。而传统即食海参及上述专利制作的海参即食品均需经过水发步骤,采用干海参进行发制需经15天左右,采用盐渍海参进行发制也需3~5天,但在盐渍海参的脱盐水发阶段将会产生10~20倍污水,加重了环境污染风险和污水处理难度,同时也减少了可饮用水的总量。在专利201310100683.3《海参低温真空加热蒸煮方法》中所述的新鲜海参同样需在0~4℃环境进行发制。
50.15、从外观上,由图2可以看出,本发明的锁鲜海参表皮形成致密保护层,内部组织状态弹嫩紧致,表皮触角颗粒分布密集,肉刺坚挺且腹足清晰可见,颜色与新鲜海参相差无几。而传统即食海参的外观则表现为软烂松散的状态,皮肤破损程度明显,几乎看不到清晰完整的表皮颗粒,放入水中甚至出现絮状分布的表皮组织,颜色与本发明的即食海参相比明显较淡,外层皮肤出现透明质感。从内部结构上,由图3可以看出,本发明的即食海参表皮边缘轮廓无破损,表皮组织纹理清晰,结构致密,内部切片结构状态细腻均匀,总体看来肉质结构紧密完整。而传统即食海参的表皮边缘破损严重,表皮组织纹理松散,组织结构呈蜂窝状,内部切片结构状态具有明显的颗粒感且分布不均匀,总体肉质结构较差。
51.16、本发明与专利201510738492.9《海参加工方法即食熟海参制品》区别在于,上述专利在进行海参加工前需将海参在模拟生长环境中饥饿暂养7~14天,并通过一系列外界刺激进行吐沙,但海参对生长环境变化较为敏感,模拟生长环境时需严格把控水温、盐度、含氧量及养殖密度,稍有不慎极易造成海参自溶死亡,一旦在暂养池中出现自溶海参则会导致周边与之接触的海参相继自溶死亡。且暂养过程中为了使海参能够吐净泥沙需停止喂食,为了维持生命,海参会大量消耗自身的营养物质,造成10%~30%的损失。此外,模拟海参生长环境所需成本极高,而海参生长环境过密同样会导致海参死亡,因此该方法的可操作性较差,无法应用于大规模的工业化生产。而本专利中的鲜活海参能够立即进行加工,无需进行暂养或吐沙等手段,避免了海参在暂养和吐沙过程中由于环境把控问题和无法进食导致的海参吐肠、死亡溶解及营养流失,影响海参的新鲜程度、完整性和产品品质。本发明提
供的方法可操作性较强,具有直接的实际生产价值。
附图说明
52.图1为新鲜海参、本发明加工得到的即食海参、专利201310100683.3《海参低温真空加热蒸煮方法》制备的即食海参和商购的四个品牌传统即食海参可溶性固形物含量对比图;注:a为新鲜海参,b为本发明加工得到的即食海参,c为专利201310100683.3《海参低温真空加热蒸煮方法》制备的即食海参,d为晓芹海参,e为棒棰岛即食海参,f为獐子岛即食海参,g为好当家即食海参。
53.图2为本发明加工得到的即食海参与传统即食海参的外观对比图(左为本发明锁鲜海参,右为传统即食海参)。
54.图3为本发明加工得到的即食海参与传统即食海参的纵切面在显微镜下的结构对比图(左为本发明锁鲜海参,右为传统即食海参)。
55.图4为本发明b与市售即食品及活海参可溶性营养物质检测图;注:a为新鲜海参,b为本发明加工得到的即食海参,c为专利201310100683.3《海参低温真空加热蒸煮方法》制备的即食海参,d为晓芹海参,e为棒棰岛即食海参,f为獐子岛即食海参,g为好当家即食海参。
具体实施方式
56.下面结合实施例对本发明内容进行详细说明:《实施例1》将5kg新鲜海参从嘴部沿腹部中线剪开,去除海参内脏、腹腔液,保留内壁筋膜并洗净泥沙,竖直切成20mm厚的块状,并在每块海参外壁沿中线切一道平行的切口;将海参块用15%白糖搅拌硬化3min;将预处理后的海参用2倍海参重量的100℃热水漂烫15s,将烫后中心温度控制在68℃;然后将海参迅速放入2倍海参重量的冷水中,冷水中同时含有海参同等重量的干冰,并在-0.08mpa条件下冷却8min。结束后将海参进行调味并密封包装,随后放入1.25倍重量的液氮中速冻7min。最终得到锁鲜海参出成率为54%。
57.《实施例2》将5kg新鲜海参从嘴部沿腹部中线剪开,去除海参内脏、腹腔液,保留内壁筋膜并洗净泥沙,竖直切成30mm厚的块状,并在每块海参外壁沿中线切一道平行的切口;将海参块用15%白糖搅拌硬化2min;将预处理后的海参用3倍海参重量的90℃热水漂烫30s,将烫后中心温度控制在71℃;然后将海参迅速放入2倍海参重量的冷水中,冷水中同时含有海参同等重量的干冰,并在-0.06mpa条件下冷却12min。结束后将海参进行调味并密封包装,随后放入2倍重量的液氮中速冻10min。最终得到锁鲜海参出成率为52%。
58.《实施例3》将5kg新鲜海参从嘴部沿腹部中线剪开,去除海参内脏、腹腔液,保留内壁筋膜并洗净泥沙,竖直切成40mm厚的块状,并在每块海参外壁沿中线切一道平行的切口;将海参块用20%白糖搅拌硬化3min;将预处理后的海参用4倍海参重量的95℃热水漂烫45s,将烫后中心温度控制在74℃;然后将海参迅速放入2.5倍海参重量的冷水中,冷水中同时含有海参2倍重量的干冰,并在-0.09mpa条件下冷却10min。结束后将海参进行调味并密封包装,随后
放入3倍重量的液氮中速冻5min。最终得到锁鲜出成率为51%。
59.从图1~图4可以看出,根据本发明的新鲜海参即食品与传统即食海参的各项优势差异明显。
60.使用实施例1中制造的锁鲜海参以及四种市场上商购的即食海参进行感官评定。
61.从日常购买并食用海参的消费人群中随机挑选10名志愿者,对每名志愿者提供编号为1~5的上述五种海参制品进行试吃,但是事先不告知志愿者海参制品来源。试吃结束后要求每名志愿者对于每种海参的鲜味和口感做出评价。根据志愿者评价完成以下表1~2,其中每个表中报告了做出每种评价的志愿者的人数。
62.表4海参鲜味的评价结果表5海参口感的评价结果从表4-5可以看出,根据实施例1生产的锁鲜海参制品味道鲜美,软硬适中,相对于其他商购海参制品,实施例1的海参能够给予消费者更加优质的食用体验。
63.表6海参营养的检测结果
64.以上所述仅为本发明的优选实施方式而已,并不用于限制本发明,对于本领域的技术人员来说,本发明可以有各种更改和变化。凡在本发明的精神和原则之内,所作的任何修改、等同替换、改进等,均应包含在本发明的保护范围之内。
再多了解一些
本文用于企业家、创业者技术爱好者查询,结果仅供参考。