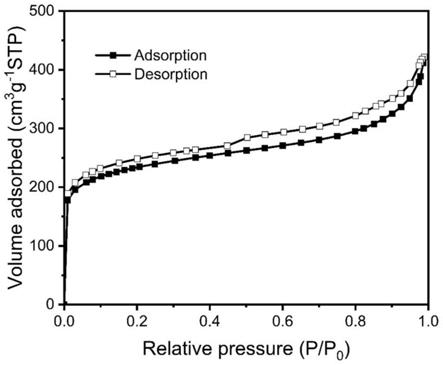
1.本发明属于材料制备技术领域,涉及一种基于聚苯醚生产工程废料的再利用制备多孔吸附材料的合成方法,具体为一种基于傅-克烷基化反应来实现超交联,回收利用聚苯醚生产过程中的副产品之一的醇溶性废料,制备多孔吸附材料。
背景技术:
2.聚苯醚因具有无毒无害、相对密度小、机械性能和电性能优异等特点,在电子电器、汽车工业、工程器械等方面具有较强的适用性。在现有的聚苯醚生产过程中,最后一道工序是用甲醇将聚合物沉淀出来,将聚苯醚产品过滤分离出来后,留在甲醇中的少量残余废料中含有铜氨催化剂、黑色的副反应化合物、二甲基酚的低聚物、甲苯等等废料。国内聚苯醚产能是每年4-5万吨,所产生的这些废料每年有5000吨左右,目前全部进行焚烧处理或将其填充到沥青中进行再利用。然而,沥青中毒性较大污染水体的部分就是酚类,向沥青中添加酚类则更增加了沥青的毒性,使其更易污染环境。因此,需要找到更好的方法进行回收利用,以提升企业发展,促进可持续发展。
3.超交联聚合物是一种基于傅-克烷基化反应制备的多孔材料。由于采用苯、萘等刚性结构物质,使得超交联聚合物中的网络结构呈现出高度刚性,形成稳定的孔隙。超交联微孔聚合物材料一般具有较高的比表面积和较大的微孔体积,在气体吸附、分离等方面具有优异的性能。
4.本发明将聚苯醚生产过程中的工程废料进行回收,利用过滤萃取的方法将可回收利用的部分分离出来,然后运用超交联聚合物理论体系,基于傅-克烷基化反应,使用外交联剂编织法,将废料交联起来,合成高比表面积多孔吸附材料。
技术实现要素:
5.本发明的目的是提供一种基于聚苯醚生产过程中的醇溶废料的再利用制备多孔吸附材料的合成方法。
6.为实现上述目的,提供以下技术方案:
7.一种基于聚苯醚生产过程中醇溶废料再利用的多孔吸附材料合成方法,包括以下步骤:
8.(1)将聚苯醚生产过程中的醇溶废料溶于溶剂中,过滤去除不溶物,蒸出溶剂后干燥,得到回收料;
9.(2)将步骤(1)制得的回收料溶解在反应溶剂中,依次加入交联剂和催化剂,在氮气气氛下搅拌反应,减压抽滤,得到固体产物;
10.(3)将所述固体产物用沉淀剂洗涤,再经沉淀剂抽提,干燥,得到所述多孔吸附材料。
11.上述技术方案中,进一步的,步骤(1)中所述的溶剂为二氯甲烷或三氯甲烷。
12.进一步的,步骤(2)中所述的反应溶剂为1,2-二氯乙烷或二硫化碳。
13.进一步的,所述交联剂和催化剂的添加量为:每1g回收料添加0.0041mol-0.0208mol交联剂和0.0083mol-0.0417mol催化剂。
14.进一步的,所述的交联剂为对二氯苄、间二氯苄、邻二氯苯、4,4’二氯甲基-1,1’联苯、9,10-二(氯甲基)蒽、1,4-二氯甲基萘、1,5-二氯甲基萘、2,6-双(氯甲基)吡啶或4,4'-二氯甲基-2,2'-联吡啶,但不限于此。
15.进一步的,所述的催化剂为路易斯酸,包括无水氯化铁、无水氯化铝、无水氯化锌或无水氯化锡,但不限于此。
16.进一步的,所述的搅拌反应条件为:在60-80℃搅拌反应12-36小时。
17.进一步的,所述的沉淀剂为甲醇、乙醇、二氯甲烷或三氯甲烷。
18.本发明的有益效果是,
19.本发明采用聚苯醚生产中的工业废料,对其进行有效利用制得多孔吸附材料,实现可持续发展,对世界环境的保护至关重要。该聚苯醚基多孔材料,由于采用含苯、萘等刚性结构的交联剂,使得其网络结构呈现出高度刚性,具有较高的比表面积和较大的微孔体积,在气体吸附、分离等方面具有优异的性能。
附图说明
20.图1是本发明中所得多孔吸附材料的氮气吸脱附曲线;
21.图2是本发明中所得多孔吸附材料的孔径分布;
22.图3是本发明中所得多孔吸附材料的外观照片。
23.具体实施方法
24.本发明的原理是利用提纯废料的刚性结构单元,与对二氯苄等交联剂发生傅-克烷基化反应,形成多孔网络结构。下面根据附图和实施例进一步说明本发明,本发明的目的和效果将变得更加明显。
25.以下实施例中所使用的提纯废料是将聚苯醚生产工业废料(10g)溶于氯仿(120ml)中,经超声和高速搅拌2-4小时,减压抽滤去除不溶物,收集的滤液蒸除氯仿,将产物置于60℃下真空干燥24小时,得到制备多孔材料的原料,即提纯废料。
26.实施例1:
27.在反应器中依次加入提纯废料(1g)、1,2-二氯乙烷(20ml)、无水氯化铁(1.3517g,0.0083mol),搅拌至充分溶解,再加入对二氯苄(0.7294g,0.0042mol),氮气-真空抽排3次后氮气鼓泡15min,在60℃下反应12小时。
28.反应结束后,减压抽滤得到棕色固体产物,再用甲醇反复洗涤3次,并在索氏抽提器中用甲醇萃取24h。最后,在80℃下真空干燥24h,即得最终产物。
29.实施例2:
30.在反应器中依次加入提纯废料(1g)、1,2-二氯乙烷(20ml)、无水氯化铁(6.7583g,0.0417mol),搅拌至充分溶解,再加入对二氯苄(3.6471g,0.0208mol),氮气-真空抽排3次后氮气鼓泡15min,在80℃下反应36小时。
31.反应结束后,减压抽滤得到棕色固体产物,再用甲醇反复洗涤3次,并在索氏抽提器中用甲醇萃取24h。最后,在80℃下真空干燥24h,即得最终产物
32.实施例3:
33.在反应器中依次加入提纯废料(1g)、1,2-二氯乙烷(20ml)、无水氯化铁(4.055g,0.025mol),搅拌至充分溶解,再加入对二氯苄(2.1883g,0.0125mol),氮气-真空抽排3次后氮气鼓泡15min,在80℃下反应24小时。
34.反应结束后,减压抽滤得到棕色固体产物,再用甲醇反复洗涤3次,并在索氏抽提器中用甲醇萃取24h。最后,在80℃下真空干燥24h,即得最终产物。
35.实施例4:
36.在反应器中依次加入提纯废料(1g)、1,2-二氯乙烷(20ml)、无水氯化铁(5.4067g,0.0333mol),搅拌至充分溶解,再加入对二氯苄(2.9177g,0.0167mol),氮气-真空抽排3次后氮气鼓泡15min,在80℃下反应24小时。
37.反应结束后,减压抽滤得到棕色固体产物,再用甲醇反复洗涤3次,并在索氏抽提器中用甲醇萃取24h。最后,在80℃下真空干燥24h,即得最终产物。
38.实施例5:
39.在反应器中依次加入提纯废料(1g)、1,2-二氯乙烷(20ml)、无水氯化铁(2.7033g,0.0167mol),搅拌至充分溶解,再加入对二氯苄(1.4588g,0.0083mol),氮气-真空抽排3次后氮气鼓泡15min,在80℃下反应24小时。
40.反应结束后,减压抽滤得到棕色固体产物,再用甲醇反复洗涤3次,并在索氏抽提器中用甲醇萃取24h。最后,在80℃下真空干燥24h,即得最终产物。
41.实施例6:
42.在反应器中依次加入提纯废料(1g)、1,2-二氯乙烷(20ml)、无水氯化铝(2.2223g,0.0167mol),搅拌至充分溶解,再加入对二氯苄(1.4588g,0.0083mol),氮气-真空抽排3次后氮气鼓泡15min,在80℃下反应24小时。
43.反应结束后,减压抽滤得到棕色固体产物,再用甲醇反复洗涤3次,并在索氏抽提器中用甲醇萃取24h。最后,在80℃下真空干燥24h,即得最终产物。
44.实施例7:
45.在反应器中依次加入提纯废料(1g)、1,2-二氯乙烷(20ml)、无水氯化铝(4.4447g,0.0333mol),搅拌至充分溶解,再加入对二氯苄(2.9177g,0.0167mol),氮气-真空抽排3次后氮气鼓泡15min,在80℃下反应24小时。
46.反应结束后,减压抽滤得到棕色固体产物,再用甲醇反复洗涤3次,并在索氏抽提器中用甲醇萃取24h。最后,在80℃下真空干燥24h,即得最终产物。
47.实施例8:
48.在反应器中依次加入提纯废料(1g)、1,2-二氯乙烷(20ml)、无水氯化铁(2.7033g,0.0167mol),搅拌至充分溶解,再加入4,4’二氯甲基-1,1’联苯(2.0929g,0.0083mol),氮气-真空抽排3次后氮气鼓泡15min,在80℃下反应24小时。
49.反应结束后,减压抽滤得到棕色固体产物,再用甲醇反复洗涤3次,并在索氏抽提器中用甲醇萃取24h。最后,在80℃下真空干燥24h,即得最终产物。
50.实施例9:
51.在反应器中依次加入提纯废料(1g)、1,2-二氯乙烷(20ml)、无水氯化铁(5.4067g,0.0333mol),搅拌至充分溶解,再加入4,4’二氯甲基-1,1’联苯(4.1858g,0.0167mol),氮
气-真空抽排3次后氮气鼓泡15min,在80℃下反应24小时。
52.反应结束后,减压抽滤得到棕色固体产物,再用甲醇反复洗涤3次,并在索氏抽提器中用甲醇萃取24h。最后,在80℃下真空干燥24h,即得最终产物。
53.实施例10:
54.在反应器中依次加入提纯废料(1g)、1,2-二氯乙烷(20ml)、无水氯化铝(4.4447g,0.0333mol),搅拌至充分溶解,再加入4,4’二氯甲基-1,1’联苯(4.1858g,0.0167mol),氮气-真空抽排3次后氮气鼓泡15min,在80℃下反应24小时。
55.反应结束后,减压抽滤得到棕色固体产物,再用甲醇反复洗涤3次,并在索氏抽提器中用甲醇萃取24h。最后,在80℃下真空干燥24h,即得最终产物。
56.实施例11:
57.在反应器中依次加入提纯废料(1g)、1,2-二氯乙烷(20ml)、无水氯化铁(2.7033g,0.0167mol),搅拌至充分溶解,再加入9,10-二(氯甲基)蒽(2.2931g,0.0083mol),氮气-真空抽排3次后氮气鼓泡15min,在80℃下反应24小时。
58.反应结束后,减压抽滤得到棕色固体产物,再用甲醇反复洗涤3次,并在索氏抽提器中用甲醇萃取24h。最后,在80℃下真空干燥24h,即得最终产物。
59.实施例12:
60.在反应器中依次加入提纯废料(1g)、1,2-二氯乙烷(20ml)、无水氯化铁(5.4067g,0.0333mol),搅拌至充分溶解,再加入9,10-二(氯甲基)蒽(4.5862g,0.0167mol),氮气-真空抽排3次后氮气鼓泡15min,在80℃下反应24小时。
61.反应结束后,减压抽滤得到棕色固体产物,再用甲醇反复洗涤3次,并在索氏抽提器中用甲醇萃取24h。最后,在80℃下真空干燥24h,即得最终产物。
62.实施例13:
63.在反应器中依次加入提纯废料(1g)、1,2-二氯乙烷(20ml)、无水氯化铝(2.2223g,0.0167mol),搅拌至充分溶解,再加入9,10-二(氯甲基)蒽(2.2931g,0.0167mol),氮气-真空抽排3次后氮气鼓泡15min,在80℃下反应24小时。
64.反应结束后,减压抽滤得到棕色固体产物,再用甲醇反复洗涤3次,并在索氏抽提器中用甲醇萃取24h。最后,在80℃下真空干燥24h,即得最终产物。
65.所制得的产物为多孔吸附材料,其氮气吸脱附曲线及孔径分布如图1、2所示,根据iupac分类,所制备的多孔材料均表现为ⅰ型等温线。在低气压(p/p0<0.1)下就表现出较高的氮气吸附量,则表明该聚合物具有丰富的微孔。而在中压区(p/p0=0.4-0.7)的滞后回线表明材料具有部分介孔。此外,在多个吸附等温线的高压区(p/p0=0.8-1)又开始急剧上升,这表明这些聚合物中存在大孔。孔径分布证实了上述结论,各个多孔材料均具有此类不均匀多孔结构。其具有较高的比表面积和较大的微孔体积,在气体吸附、分离等方面具有优异的性能;本发明通过对聚苯醚生产中的工业废料进行再利用,成功制得具有吸附功能的多孔材料,实现废物再利用,绿色环保有利于可持续发展。
66.上述具体实施方式用来解释说明本发明,而不是对本发明进行限制,在本发明的精神和权利要求的保护范围内,对本发明做出的任何修改和改变,都落入本发明的保护范围。
再多了解一些
本文用于企业家、创业者技术爱好者查询,结果仅供参考。