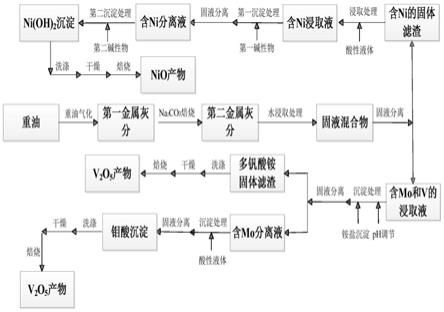
1.本发明涉及一种金属回收的重油利用方法。
背景技术:
2.含钼催化剂广泛应用于各种石油产品特别是重油加氢过程,随着炼油工业的大规模发展,对钼催化剂的用量也日益增大。但是钼金属资源相对短缺,在冶金、国防等领域也有很大需求。因此,从废催化剂中回收钼,实现金属的循环利用,既能减少环境污染,又具有重要的经济价值。
3.cn101724758a提出从含钼废催化剂中湿法回收钼的方法。该方法是将废催化剂粉碎后与碱性物质混合焙烧得到灰渣,灰渣经过硫酸,硝酸和柠檬酸混酸溶液溶解后,再加入氨水调节ph值获得钼酸铵沉淀。
4.但上述流程存在操作流程复杂,还存在加氢尾油粘度高导致溶剂萃取分离固体难度大,以及萃余油性质差需要解决加工去向等问题。
技术实现要素:
5.本发明的目的是提供一种实现金属回收的重油处理方法,本发明的回收方法效果好,产品质量稳定,副产氢气,经济性好。
6.为了实现上述目的,本发明提供一种实现金属回收的重油利用方法,该方法包括:
7.1)将含mo、ni和v的重油在含氧气体和水蒸气存在下进行气化反应,得到含mo、ni和v的第一金属灰分;
8.2)将所述第一金属灰分与碱金属盐进行混合后,在含氧气体存在下在焙烧装置中进行焙烧处理,得到含mo、v的碱金属盐和nio的第二金属灰分;
9.3)对所得第二金属灰分进行浸取,得到含mo和v浸取液,以及含ni滤渣;
10.4)对含mo和v浸取液进行分离处理,得到moo3和v2o5产品;
11.5)对含ni滤渣进行提取处理,得到nio产品。
12.优选地,步骤1)中,所述气化反应条件包括:
13.温度为1200-1500℃;和/或压力为2.0-8.5mpa;和/或时间为1-10s;和/或
14.所述含氧气体为空气和/或氧气,优选为氧气;和/或
15.以含氧气体中氧气的体积为基准,所述含氧气体物流与重油比例为600-1200ml(氧)/g(油);和/或
16.水蒸气物流与重油质量比为0.3-0.8。
17.优选地,其中,步骤2)中,
18.所述碱金属盐选自碳酸钠、碳酸钾、氢氧化钠和氢氧化钾中的一种或多种;和/或
19.所述碱金属盐中的碱金属离子与第一金属灰分中mo和v的物质的量的总物质的量的比例为1-6;和/或
20.所述焙烧条件包括:温度为450-850℃,和/或时间为30-240min;和/或
21.所述含氧气体为空气和/或氧气,优选为氧气;和/或
22.以含氧气体中氧气的体积为基准,相对于1g的所述第一金属灰分,所述含氧气体物流为3-150ml/min。
23.优选地,其中,步骤3)中所述浸渍条件包括:
24.第二金属灰分与水的比例为3-10g(灰)/ml(水);和/或
25.温度为10-90℃,和/或时间为20-180min。
26.优选地,其中,步骤4)中所述分离处理步骤包括:
27.a.将所述含v和mo的浸取液采用酸性调节剂调整ph值后,加入铵盐沉淀出多钒酸铵,得到固液混合物;将所得固液混合物进行固液分离,得到多钒酸铵沉淀物和含mo分离液;
28.b.将所得多钒酸铵沉淀物依次进行洗涤、干燥和焙烧,得到所述v2o5产物;
29.c.将所得含mo分离液与酸性调节剂混合进行沉淀处理,将钼酸沉淀过滤洗涤后,进行烘干焙烧后得到moo3产物。
30.优选地,步骤a中,
31.所述酸性调节剂选自盐酸、硫酸和硝酸中的一种或多种;和/或
32.采用酸性调节剂所调节悬浊液的ph值为5-10;和/或
33.所述铵盐选自氯化铵、硫酸铵、碳酸铵、硝酸铵和醋酸铵中的一种或多种;和/或
34.所述铵盐中的nh
4
与含有mo和v的浸取液中v的物质的量之比为0.01-10,和/或
35.进行所述沉淀的温度为5-90℃,和/或时间为1-300min。
36.优选地,步骤b中,所述焙烧的温度为300-600℃,和/或时间为60-600min。
37.优选地,步骤c中,
38.所述酸性调节剂选自盐酸、硫酸和硝酸中的一种或多种;和/或
39.采用酸性调节剂所调节悬浊液的ph值为0.1-1,沉淀的温度为10-90℃,时间为60-600min;和/或
40.所述焙烧的温度为300-550℃,和/或时间为60-600min,和/或焙烧气氛为空气气氛。
41.优选地,其中,步骤5)中所述提取处理的步骤包括:
42.(i)将所述含ni滤渣与酸液接触并进行浸取处理,得到含ni的浸取液;
43.(ii)将所得含ni的浸取液与第一碱性物混合进行第一沉淀处理,然后进行固液分离,得到含ni的分离液;
44.(iii)将含ni的分离液与第二碱性物混合并进行第二沉淀处理,然后进行固液分离,得到ni(oh)2沉淀;
45.(iv)将所得ni(oh)2沉淀依次进行洗涤、干燥和焙烧,得到所述nio产物。
46.优选地,步骤(i)中,所述浸取处理的条件包括:
47.所述酸液包括选自盐酸、硫酸和硝酸中的一种或多种;和/或
48.酸液与含ni滤渣的重量比为1-20;和/或
49.温度为5-95℃,和/或时间为1-300分钟;和/或
50.所述含ni的浸取液的ph值为0-6。
51.优选地,步骤(ii)中,所述第一沉淀处理的条件包括:
52.所述第一碱性物选自碳酸钠和氢氧化钠中的一种或多种;和/或
53.温度为5-90℃,和/或时间为1-300分钟;和/或
54.进行第一沉淀处理时含ni的浸取液的ph值为3-8。
55.优选地,步骤(iii)中,所述第二沉淀处理的条件包括:
56.所述第二碱性物选自碳酸钠和氢氧化钠中的一种或多种;和/或
57.温度为5-90℃,和/或时间为1-300分钟;和/或
58.进行第二沉淀处理时含ni的分离液的ph值为8.5-12。
59.优选地,步骤(iv)中,所述焙烧的温度为400-650℃,和/或时间为60-600min。
60.优选地,其中,以重油的重量为基准,所述重油中mo的含量为0.1-5重量%,ni的含量为0.1-5重量%,v的含量为0.1-5重量%,c的含量为85-92重量%,h的含量为5-12重量%。
61.优选地,其中,所述重油选自渣油和尾油中的一种或多种。
62.本发明具有如下优点:
63.1、本发明采用重油气化、碱式焙烧和湿法分离联合方式实现从重油中选择性分离回收钼、镍和钒等金属。钼、镍和钒收率和纯度高,产物质量稳定,工艺成熟可靠,且副产氢气,经济性好,环保性强。
64.2、重油中回收的钼可作浆态床重油加氢催化剂的合成原料,并且重油中的镍和钒等金属也能回收用作其他催化剂或者冶金原料,具有很大的经济效益。
65.3、重油气化反应时间短,转化效率高,生成合成气,再经co变化后生产氢气,为炼厂加氢装置提供氢气原料,附加价值高。并且重油中的s和n在气化过程中转化为h2s和n2,相比燃烧释放的so
x
和no
x
处理成本更低,环保性更强。
66.本发明的其他特征和优点将在随后的具体实施方式部分予以详细说明。
附图说明
67.附图是用来提供对本发明的进一步理解,并且构成说明书的一部分,与下面的具体实施方式一起用于解释本发明,但并不构成对本发明的限制。在附图中:
68.图1是本发明分离方法一种具体实施方式的流程示意图。
具体实施方式
69.在本文中所披露的范围的端点和任何值都不限于该精确的范围或值,这些范围或值应当理解为包含接近这些范围或值的值。对于数值范围来说,各个范围的端点值之间、各个范围的端点值和单独的点值之间,以及单独的点值之间可以彼此组合而得到一个或多个新的数值范围,这些数值范围应被视为在本文中具体公开。
70.以下对本发明的具体实施方式进行详细说明。应当理解的是,此处所描述的具体实施方式仅用于说明和解释本发明,并不用于限制本发明。
71.如图1所示,本发明提供一种金属回收的重油利用方法,该方法包括:
72.将含mo、ni和v的重油在含氧气体和水蒸气存在下在气化装置中进行气化反应,得到含mo、ni和v的第一金属灰分;
73.将所述第一金属灰分与碱金属盐进行混合后,在含氧气体存在下在焙烧装置中进
行焙烧处理,得到含mo、v的碱金属盐和nio的第二金属灰分;
74.对所得第二金属灰分进行水浸取,得到含mo和v浸取液,以及含ni滤渣;
75.对含mo和v浸取液进行分离处理,得到moo3和v2o5产品;
76.对含ni滤渣进行提取处理,得到nio产品。
77.本发明采用重油气化、碱式焙烧和湿法分离联合方式实现从重油中选择性分离回收钼、镍和钒等金属。钼、镍和钒收率和纯度高,产物质量稳定,工艺成熟可靠,且副产氢气,经济性好,环保性强。
78.本发明,步骤1)中所述气化反应条件包括:温度为1200-1500℃;和/或压力为2.0-8.5mpa;和/或时间为1-20s。
79.本发明,步骤1)中所述含氧气体为空气和/或氧气,优选为氧气。
80.本发明,步骤1)中以含氧气体中氧气的标准体积为基准,所述含氧气物流与重油比例为600-1200ml(氧)/g(油)。
81.本发明,步骤1)中水蒸气物流与重油质量比为0.3-0.8。所述重油与含氧气体和蒸汽可以同时向气化装置中进料。
82.本发明,步骤1)中所述气化装置是本领域技术人员所熟知的,例如是气化炉等。
83.根据本发明,碱金属焙烧用于除去第一金属灰分中残存的炭,此外还用于生成含mo和v的水溶性碱金属盐。
84.根据本发明,步骤2)中,所述碱金属盐中的碱金属离子的物质的量与第一金属灰分中mo和v的总物质的量的比例为1-6。
85.根据本发明,步骤2)中,所述焙烧条件包括:温度为450-850℃,和/或时间为30-240min。
86.根据本发明,步骤2)中,所述含氧气体为空气和/或氧气,优选为氧气。
87.根据本发明,步骤2)中,以含氧气体中氧气的体积为基准,相对于1g的所述第一金属灰分,所述含氧气体物流为3-150ml/min。
88.根据本发明,步骤2)中,所述含氧气体可以与重油同时向焙烧装置中进料,也可以将重油一次性加入焙烧装置中,然后再连续或分批次地通入含氧气体。所述焙烧装置是本领域技术人员所熟知的,例如是焙烧炉等。
89.根据本发明,对所得第二金属灰分中进行水浸取用于将含mo、v和ni的第一金属灰分分离出含mo和v浸取液以及含nio滤渣。步骤3)中,所述水浸取条件包括:第二金属灰分与水的比例为3-10g(灰)/ml(水)。
90.根据本发明,步骤3)中,温度为10-90℃,和/或时间为20-180min。时间可以依据温度进行调整,具体根据目标产物进行调配。
91.根据本发明,分离处理用于进一步将含有mo和v浸渍液中分离出moo3和v2o5。如图1所示,步骤4)中所述分离处理步骤包括:a.将所述含v和mo的浸取液采用酸性调节剂调整ph值后,加入铵盐沉淀出多钒酸铵,得到固液混合物;将所得固液混合物进行固液分离,得到多钒酸铵沉淀物和含mo分离液;b.将所得多钒酸铵沉淀物依次进行洗涤、干燥和焙烧,得到所述v2o5产物;c.将所得含mo分离液与酸性调节剂混合进行沉淀处理,将钼酸沉淀过滤洗涤后,进行烘干焙烧后得到moo3产物。
92.根据本发明,步骤a是用于使v以多钒酸铵的形式沉淀,从而与mo分离,所述混合反
应条件可以包括:采用酸性调节剂所调节悬浊液的ph值为5-10。
93.根据本发明,步骤a中,所述铵盐选自氯化铵、硫酸铵、碳酸铵、硝酸铵和醋酸铵中的一种或多种。
94.根据本发明,步骤a中,所述铵盐中的nh
4
与含有mo和v的浸取液中v的物质的量之比为0.01-10。
95.根据本发明,步骤a中,进行所述沉淀的温度为5-90℃,和/或时间为1-300min。根据本发明,所述v2o5产物中v2o5的含量可以在90重量%以上,优选在95重量%以上。
96.根据本发明,步骤b是使多钒酸铵沉淀物热解转化为v2o5产物,步骤b中所述焙烧的温度可以为300-600℃,和/或时间可以为60-600min,和/或焙烧气氛可以为空气气氛。
97.根据本发明,步骤c使钼酸铵溶液与酸性液体反应转变为钼酸沉淀,然后热解转化为moo3产物,步骤c中,所述酸性调节剂选自盐酸、硫酸和硝酸中的一种或多种。
98.根据本发明,步骤c中,采用酸性调节剂所调节悬浊液的ph值为0.1-1,和/或沉淀的温度为10-90℃,和/或时间为60-600min。
99.根据本发明,步骤c中,所述焙烧的温度可以为300-550℃,和/或时间可以为60-600min,和/或焙烧气氛可以为空气气氛,所述moo3产物中moo3的含量可以在90重量%以上,优选在95重量%以上。
100.根据本发明,提取处理用于将含ni浸取液转化为nio产物。如图1所示,所述提取处理的步骤可以包括:(i)将所述含ni滤渣与酸液接触并进行浸取处理,得到含ni的浸取液;(ii)将所得含ni的浸取液与第一碱性物混合进行第一沉淀处理,然后进行固液分离,得到含ni的分离液;(iii)将含ni的分离液与第二碱性物混合并进行第二沉淀处理,然后进行固液分离,得到ni(oh)2沉淀;(iv)将所得ni(oh)2沉淀依次进行洗涤、干燥和焙烧,得到所述nio产物。
101.根据本发明,步骤(i)中的浸取处理用于使含ni的灰分中的nio溶解,所述浸取处理的条件可以包括:所述酸性液体包括选自盐酸、硫酸和硝酸中的一种或多种。
102.根据本发明,步骤(i)中的浸取处理用于使含ni的灰分中的nio溶解,所述浸取处理的条件可以包括:酸性液体与含ni的灰分的重量比为1-20。
103.根据本发明,步骤(i)中的浸取处理用于使含ni的灰分中的nio溶解,所述浸取处理的条件可以包括:温度为5-95℃,和/或时间为1-300min,和/或所述含ni的浸取液的ph值为0-6。
104.根据本发明,步骤(ii)中的第一沉淀处理用于去除fe和al等杂质,其条件并无特殊限制,例如所述第一沉淀处理的条件可以包括:所述第一碱性物选自碳酸钠和氢氧化钠中的一种或多种。
105.根据本发明,步骤(ii)中的第一沉淀处理用于去除fe和al等杂质,其条件并无特殊限制,例如所述第一沉淀处理的条件可以包括:温度为5-90℃,和/或时间为1-300min,和/或进行第一沉淀处理时含ni的浸取液的ph值为3-8。
106.根据本发明,步骤(iii)中的第二沉淀处理用于生产ni(oh)2,所述第二沉淀处理的条件可以包括:第二碱性物选自碳酸钠和氢氧化钠中的一种或多种。
107.根据本发明,步骤(iii)中的第二沉淀处理用于生产ni(oh)2,所述第二沉淀处理的条件可以包括:温度为5-90℃,和/或时间为1-300min,和/或进行第二沉淀处理时含ni的
分离液的ph值为8.5-12。
108.根据本发明,优选该方法还包括:
109.(i)将步骤(4)得到的moo3产品、溶剂和c1-c6含氧有机酸混合并在20-150℃下反应得到反应混合物,调节反应混合物的ph值为2.5-5,得到第一产物;
110.(ii)使所述第一产物与c6-c18含氧有机酸混合并在145-300℃下反应,所得产物经分离纯化得到有机油溶性含钼化合物。
111.根据本发明,优选地,步骤(i)中,以钼元素计的所述moo3产品和所述溶剂的重量比为1:(1-20);以钼元素计的所述moo3产品与所述c1-c6含氧有机酸的摩尔比为1:(0.5-4)。
112.根据本发明,优选地,步骤(ii)中,以钼元素计的所述moo3产品与所述c6-c18含氧有机酸的摩尔比为1:(1-10)。
113.根据本发明,优选地,步骤(i)中反应的时间为0.3-9小时。
114.根据本发明,优选地,步骤(ii)中反应的时间为1-12小时。
115.根据本发明,优选地,步骤(i)中所述溶剂选自水和/或有机溶剂;所述有机溶剂选自苯、甲苯、乙醇或石油醚。
116.根据本发明,优选地,所述c1-c6含氧有机酸选自甲酸、乙酸、丙酸、2-甲基丁酸、羟基乙酸、异丁酸、戊酸、乙二酸、丙二酸、丁二酸、戊二酸、2-羟基丁二酸、3-羟基丙三羧酸或柠檬酸。
117.根据本发明,优选地,所述c6-c18含氧有机酸选自己酸、庚酸、2-丙基庚酸、辛酸、2-乙基己酸、壬酸、癸酸、油酸、软脂酸、硬脂酸或碳原子数为6-18的环烷酸。
118.根据本发明,优选地,步骤(i)和/或步骤(ii)在惰性气氛中进行。
119.根据本发明的方法,其中,所述的有机油溶性含钼化合物具有式(1)所示的结构:
[0120][0121]
其中,a b为2、3、4、5或6,m n为0、1、2、3、4、5或6,r1为c1-c6含氧有机酸根,r2为c6-c18含氧有机酸根。
[0122]
根据本发明的方法,优选地,a与b相等,且a b为2、4或6;m与n相等,且m n为0、2或4。
[0123]
根据本发明的方法,更优选地,所述c1-c6含氧有机酸根为一元羧酸根、二元羧酸根或多元羧酸根,优选为二元羧酸根或多元羧酸根,更优选为甲酸根、乙酸根、丙酸根、2-甲基丁酸根、羟基乙酸根、异丁酸根、戊酸根、乙二酸根、丙二酸根、丁二酸根、戊二酸根、2-羟基丁二酸根、3-羟基丙三羧酸根或柠檬酸根。
[0124]
根据本发明的方法,更优选地,所述c6-c18含氧有机酸根为一元羧酸根、二元羧酸根、多元羧酸根、硫羧酸根、磺酸根或亚磺酸根,优选为一元羧酸根、二元羧酸根或磺酸根,更优选为己酸根、庚酸根、2-丙基庚酸根、辛酸根、2-乙基己酸根、壬酸根、癸酸根、油酸根、软脂酸根、硬脂酸根或碳原子数为6-18的环烷酸根。
[0125]
根据本发明的方法,更优选地,所述的有机油溶性含钼化合物含有2-23重量%的钼金属元素。
[0126]
按照本发明方法合成的有机油溶性含钼化合物具有优异的加氢、抑焦、脱氮效果。
[0127]
根据本发明,步骤(iv)中用于使ni(oh)2热解转化为nio产物,其条件并无特殊限制,例如所述焙烧的温度可以为300-650℃,优选为300-550℃,和/或时间可以为60-600min,和/或焙烧气氛可以为空气气氛。所述nio产物中nio的含量可以在90重量%以上,优选在95重量%以上。
[0128]
根据本发明,重油是本领域技术人员所熟知的,例如,以重油的重量为基准,所述重油中mo的含量为0.1-5重量%,ni的含量为0.1-5重量%,v的含量为0.1-5重量%,c的含量为85-92重量%,h的含量为5-12重量%。
[0129]
根据本发明,所述重油可以选自渣油和尾油中的一种或多种,优选自渣油临氢热转化所生产的尾油,更优选为含mo催化剂和含ni、v金属的低品质重油加氢所得尾油。
[0130]
本发明方法的其他操作,如所述的过滤和干燥等,可以采用本领域技术人员熟知的操作条件,本发明不再具体赘述。
[0131]
下面通过实施例来进一步说明本发明,但是本发明并不因此而受到任何限制。
[0132]
本发明实施例和对比例所用rmx尾油为石油化工科学研究院开发多产改质油的渣油临氢热转化工艺所得的尾油,以rmx尾油的重量为基准,rmx尾油中mo的含量为0.50重量%,ni的含量为0.23重量%,v的含量为0.74重量%,c的含量为87.18重量%,h的含量为6.84重量%。
[0133]
产物的某种金属收率为产物中某种金属的重量与重油中某种金属的重量的比例。
[0134]
本发明的实施例以及对比例中:所使用的化学试剂均国药集团化学试剂有限公司产品。
[0135]
金属含量分析在perkinelmer nexion 300x电感耦合等离子体发射光谱仪上依据icp-other方法测定。
[0136]
红外光谱在nicolet 6700型号傅立叶红外光谱仪上进行测试。
[0137]
采用质谱测定有机钼化合物的相对分子质量。
[0138]
实施例1
[0139]
(1)将rmx尾油、氧气和水蒸气分别以30g/min、20000ml/min和18g/min的进料量喷入焙烧炉中进行气化反应,反应温度为1350℃,压力为6mpa,时间为3s。气化反应产生合成气夹带着燃烧含mo、v和ni的第一金属灰分进入水池中激冷处理。冷却的合成气由水池中侧顶部流入下游水洗单元。而第一金属灰分随水池中水由底部泵流出装置,再经过滤烘干收集。分析第一金属灰分中钼、钒和镍含量(以金属计)分别为8.3重量%、7.2重量%和2.4重量%。
[0140]
(2)取第一金属灰分300g和6.4g碳酸钠混合后,加入到焙烧炉中,在650℃、1600ml/min气速下进行空气焙烧75min。焙烧结束后冷却焙烧炉,含mo、v和ni的第二金属灰分由过滤器反吹至收集塔中收集。此时moo3和v2o5与碳酸钠反应生成钠盐,而nio则不发生变化。分析焙烧灰分中钼、钒和镍含量(以金属计)分别为20.9重量%、18.1重量%和6.0重量%。
[0141]
(3)取20g步骤(2)焙烧所得第二金属灰分粉碎至100目后,用水在35℃下浸取
60min,其中水与含有所述金属灰分的重量比为5g(灰)/ml(水)。此时mo和v的钠盐溶于水经过滤进入浸取液中,而nio的溶解度小,经过滤进入滤渣中,将含ni滤渣用水洗涤待用。
[0142]
(4)向步骤(3)所得含mo和v浸取液中加入重量分数为37%的盐酸将浸取液的ph值调节为8.0后,再加入14.9g氯化铵,沉淀温度为50℃,沉淀时间为30min。将所得将固液混合物进行固液分离,得到多钒酸铵沉淀物和含mo分离液。向所得多钒酸铵沉淀物加入1重量%稀氨水洗涤后进行干燥,然后在600℃下空气焙烧120min,得到v2o5产物中v的收率为97.3重量%,v2o5重量分数为98.7%。
[0143]
(5)向步骤(4)所得mo滤液中加入重量分数65%的硝酸将滤液ph值调整为0.6,在80℃下反应180min,以钼酸作为沉淀的形式进行沉钼。将所得钼酸沉淀用蒸馏水洗涤后进行干燥,然后在500℃下空气焙烧180min,得到moo3产物,mo的收率为96.2重量%,moo3产物中moo3重量分数为98.5%。
[0144]
(6)取步骤(3)分离所得含ni滤渣向其中加入重量分数为10%盐酸溶液16.2g。将混合物加热到90℃后,搅拌浸取30min。降温冷却后用naoh将ph值调整为6.0使得浸取液中的fe和al沉淀30min,将沉淀过滤。然后用naoh将过滤后的含ni滤液的ph值调整为9.0,使得ni(oh)2沉淀。将ni(oh)2晶体用蒸馏水洗涤后进行干燥,然后在600℃下空气焙烧120min,得到nio产物,计算得ni收率为98.2重量%,nio产物中nio重量分数为99.1%。
[0145]
实施例2
[0146]
(1)将rmx尾油、氧气和水蒸气分别以30g/min、25000ml/min和12g/min的进料量喷入焙烧炉中进行气化反应,反应温度为1400℃,压力为7mpa,时间为5s。气化反应产生合成气夹带着燃烧含mo、v和ni的第一金属灰分进入水池中激冷处理。冷却的合成气由水池中侧顶部流入下游水洗单元。而第一金属灰分随水池中水由底部泵流出装置,再经过滤烘干收集。分析第一金属灰分中钼、钒和镍含量(以金属计)分别为12.4重量%、10.8重量%和3.6重量%。
[0147]
(2)取第一金属灰分30g和碳酸钠8.0g。加入到焙烧炉中,750℃、2500ml/min气速下进行空气焙烧60min。焙烧结束后冷却焙烧炉,含mo、v和ni的第二金属灰分由过滤器反吹至收集塔中收集。此时moo3和v2o5与碳酸钠反应生成钠盐,而nio则不发生变化。分析焙烧灰分中钼、钒和镍含量(以金属计)分别为19.7重量%、17.1重量%和5.6重量%。
[0148]
(3)同实施例1。
[0149]
(4)向步骤(3)所得含mo和v浸取液中加入重量分数为65%的硝酸将浸取液的ph值调节为7.6后,再加入26.3g硝酸铵,沉淀温度为40℃,沉淀时间为50min。将所得将固液混合物进行固液分离,得到多钒酸铵沉淀物和含mo分离液。向所得多钒酸铵沉淀物加入1重量%稀氨水洗涤后进行干燥,然后在650℃下空气焙烧90min,得到v2o5产物,计算得v收率为98.1重量%,v2o5产物中v2o5重量分数为98.4%。
[0150]
(5)向步骤(4)所得mo滤液中加入重量分数65%的硝酸将滤液ph值调整为0.8,在80℃下反应180min,以钼酸作为沉淀的形式进行沉钼。将所得钼酸沉淀用蒸馏水洗涤后进行干燥,然后在550℃下空气焙烧120min,得moo3产物,mo的收率为95.0重量%,moo3产物中moo3重量分数为98.2%。
[0151]
(6)同实施例1,得到nio产物,计算得ni收率为98.7重量%,nio产物中nio重量分数为96.1%。
[0152]
实施例3
[0153]
(1)将rmx尾油、氧气和水蒸气分别以30g/min、29000ml/min和12g/min的进料量喷入焙烧炉中进行气化反应,反应温度为1450℃,压力为6mpa,时间为3s。气化反应产生合成气夹带着燃烧含mo、v和ni的第一金属灰分进入水池中激冷处理。冷却的合成气由水池中侧顶部流入下游水洗单元。而第一金属灰分随水池中水由底部泵流出装置,再经过滤烘干收集。分析第一金属灰分中钼、钒和镍含量(以金属计)分别为15.5重量%、13.4重量%和4.6重量%。
[0154]
(2)同实施例1。
[0155]
(3)同实施例1。
[0156]
(4)向步骤(3)所得含mo和v浸取液中加入重量分数为37%的盐酸将浸取液的ph值调节为8.2后,再加入11.9g硫酸铵,沉淀温度为30℃,沉淀时间为60min。将所得将固液混合物进行固液分离,得到多钒酸铵沉淀物和含mo分离液。向所得多钒酸铵沉淀物加入1重量%稀氨水洗涤后进行干燥,然后在600℃下空气焙烧120min,得到v2o5产物中v的收率为95.9重量%,v2o5重量分数为98.1%。
[0157]
(5)同实施例1,得到moo3产物,mo的收率为94.7重量%,moo3产物中moo3重量分数为97.5%。
[0158]
(6)同实施例1,得到nio产物,计算得ni收率为96.6重量%,nio产物中nio重量分数为98.2%。
[0159]
实施例4
[0160]
(1)将rmx尾油、氧气和水蒸气分别以30g/min、18000ml/min和15g/min的进料量喷入焙烧炉中进行气化反应,反应温度为1300℃,压力为5mpa,时间为7s。气化反应产生合成气夹带着燃烧含mo、v和ni的第一金属灰分进入水池中激冷处理。冷却的合成气由水池中侧顶部流入下游水洗单元。而第一金属灰分随水池中水由底部泵流出装置,再经过滤烘干收集。分析第一金属灰分中钼、钒和镍含量(以金属计)分别为7.1重量%、6.2重量%和2.0重量%。
[0161]
(2)同实施例1。
[0162]
(3)取20g步骤(2)焙烧所得第二金属灰分粉碎至100目后,用水在65℃下浸取30min,其中水与含有所述金属灰分的重量比为7g(灰)/ml(水)。此时mo和v的钠盐溶于水经过滤进入浸取液中,而nio的溶解度小,经过滤进入滤渣中,将含ni滤渣用水洗涤待用。
[0163]
(4)同实施例1,得到v2o5产物,计算得v收率为95.1量%,v2o5产物中v2o5重量分数为98.1%。
[0164]
(5)同实施例1,得到moo3产物,mo的收率为93.9重量%,moo3产物中moo3重量分数为98.4%。
[0165]
(6)取步骤(3)分离所得含ni滤渣向其中加入重量分数为5%盐酸溶液12.5g。将混合物加热到90℃后,搅拌浸取30min。降温冷却后用naoh将ph值调整为6.5使得浸取液中的fe和al沉淀60min,将沉淀过滤。然后用naoh将过滤后的含ni滤液的ph值调整为9.5,使得ni(oh)2沉淀。将ni(oh)2晶体用蒸馏水洗涤后进行干燥,然后在550℃下空气焙烧180min,得到nio产物,计算得ni收率为95.2量%,nio产物中nio重量分数为98.6%。
[0166]
实施例5
[0167]
与实施例1的步骤(1)-(7)基本相同,不同之处在于步骤(1)中氧气和水蒸气分别为16000ml/min和21g/min,反应温度为1250℃,压力为4mpa,时间为10s。
[0168]
所得到v2o5产物,计算得v收率为95.2重量%,v2o5产物中v2o5重量分数为98.2%。所得到moo3产物,计算得mo收率为94.0重量%,moo3产物中moo3重量分数为97.5%。所得到nio产物,计算得ni收率为97.2重量%,nio产物中nio重量分数为98.2%。
[0169]
对比例1
[0170]
(1)用1200g甲苯将300g rmx尾油在120℃萃取1h,然后经过滤得到萃取相和金属残渣,将萃取相中的甲苯蒸出后得到改质油。。
[0171]
(2)将金属残渣在140℃、0.01mpa下干燥4h,然后经过粉碎机处理将金属残渣粒径粉碎至100目。
[0172]
(3)重复步骤(1)-(2)的过程,将累积得到的金属残渣30g(mo、ni和v的质量分数分别为5.2%、1.6%和4.8%)与8.3g碳酸钠混合。将混合后的粉末在600℃下进行空气焙烧120min。
[0173]
(4)将步骤(3)所得焙烧产物在90℃下用35g水浸取90min,此时v和mo的钠盐溶于水中经过滤后进入浸取液,将含ni滤渣用水洗涤后烘干待用。
[0174]
(5)向含v和mo的浸取液中加入重量分数为37%的盐酸将浸取液的ph值调节为8.2后,再加入6.1g氯化铵,沉淀温度为50℃,沉淀时间为30min。将沉淀过滤洗涤后,烘干焙烧后得到v2o5产物,v的收率为95.2重量%,v2o5产物中v2o5重量分数为93.6%。向含mo滤液中加入重量分数为37%的盐酸将滤液ph值调整为0.8,反应时间为30min,以钼酸作为沉淀的形式进行沉钼。将钼酸沉淀过滤洗涤后,进行烘干焙烧后得到moo3产物,mo的收率为92.5重量%,moo3产物中moo3重量分数为93.7%。
[0175]
(6)取步骤(5)分离所得含ni滤渣,向其中加入重量分数为5%盐酸溶液16.2g。将混合物加热到90℃后,搅拌浸取30min。降温冷却后用naoh将ph值调整为6.0使得浸取液中的fe和al沉淀30min,将沉淀过滤。然后用naoh将过滤后的含ni滤液的ph值调整为9.0,使得ni(oh)2沉淀。将ni(oh)2晶体用蒸馏水洗涤后进行干燥,然后在600℃下空气焙烧120min,得到nio产物,计算得ni收率为97.6重量%,nio产物中nio重量分数为98.1%。
[0176]
将实施例1-5与对比例1进行比较可知,本发明可以高效分离钼、镍和钒,钼、镍和钒收率和纯度高,产物质量稳定,且简化工艺步骤,具有重要的环保价值。本发明采用重油气化方式将尾渣转化为含金属的气化灰渣,同时可以产生合成气为下游制氢原料或锅炉燃料。而对比例采用溶剂萃取的方式将金属残渣从尾渣中分离出来回收金属。与对比例相比,本发明在第一步金属富集方式更简化,且合成气的利用相比于尾渣中除渣重油利用更简单。
[0177]
实施例6
[0178]
(i)将实施例1回收的三氧化钼与溶剂(水和乙醇的混合溶液,水与乙醇的重量比为1:1)在烧瓶中分散,三氧化钼和溶剂的重量比为1:20。惰性气体吹扫,在温度100℃下加入丁二酸反应8小时,丁二酸与三氧化钼(以钼元素计)的摩尔比为3:1;反应结束后,利用稀氨水调整溶液ph值为4.5,得到第一产物。
[0179]
(ii)在溶液中加入预热的壬酸,按照三氧化钼(以钼元素计)与壬酸摩尔比为1:4.5混合,壬酸预热温度100℃,混合完毕后,在温度为245℃条件反应3小时,反应结束分离
溶剂得到有机油溶性含钼化合物。
[0180]
采用红外光谱对有机钼化合物的结构进行测试,红外光谱:γ=2962cm-1
、1708cm-1
、1534cm-1
、1462cm-1
、1423cm-1
、1289cm-1
、986cm-1
、780cm-1
、731cm-1
。
[0181]
由红外光谱数据可知,690-790cm-1
附近出现了归属于mo-o-mo的吸收峰,2961cm-1
,1462cm-1
分别为有机酸烷基上ch3的c—h键反对称伸缩振动、反对称变形振动峰,1534cm-1
、1462cm-1
分别为配位羧基的不对称伸缩振动和对称伸缩振动峰,说明有机油溶性含钼化合物为具有式(1)所示的结构。
[0182]
实施例7
[0183]
采用与实施例6相同的方法制备有机钼化合物,不同之处仅在于,步骤(i)中调节反应混合物的ph值为0.5。反应结束将反应产物分离除尽溶剂相,水洗油相,减压蒸馏脱除轻组分后得到有机钼化合物。
[0184]
红外光谱:γ=2956cm-1
,1708cm-1
,1509cm-1
,1421cm-1
,1297cm-1
,1118cm-1
,983cm-1
,684cm-1
。
[0185]
红外谱图分析690cm-1-790cm-1
处没有mo-o-mo的吸收峰,说明有机钼化合物不具有式(1)所示的结构。
[0186]
按照本发明方法合成的具有式(1)结构的有机油溶性含钼化合物具有优异的加氢、抑焦、脱氮效果。
[0187]
以上详细描述了本发明的优选实施方式,但是,本发明并不限于上述实施方式中的具体细节,在本发明的技术构思范围内,可以对本发明的技术方案进行多种简单变型,这些简单变型均属于本发明的保护范围。
[0188]
另外需要说明的是,在上述具体实施方式中所描述的各个具体技术特征,在不矛盾的情况下,可以通过任何合适的方式进行组合,为了避免不必要的重复,本发明对各种可能的组合方式不再另行说明。
[0189]
此外,本发明的各种不同的实施方式之间也可以进行任意组合,只要其不违背本发明的思想,其同样应当视为本发明所发明的内容。
[0190]
以上详细描述了本发明的优选实施方式,但是,本发明并不限于此。在本发明的技术构思范围内,可以对本发明的技术方案进行多种简单变型,包括各个技术特征以任何其它的合适方式进行组合,这些简单变型和组合同样应当视为本发明所公开的内容,均属于本发明的保护范围。
再多了解一些
本文用于企业家、创业者技术爱好者查询,结果仅供参考。