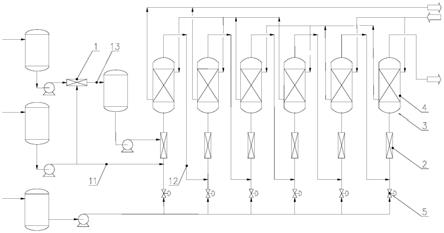
1.本发明涉及化工领域,特别涉及一种异丙醇胺的合成系统及方法。
背景技术:
2.ipa(异丙醇胺)是一种具有氨基和醇性羟基的醇胺类化合物,具有胺和醇的综合性能。根据其结构中羟基的个数进行划分,可以分为一异丙醇胺(mipa)、二异丙醇胺(dipa)、三异丙醇胺(tipa)。
3.一异丙醇胺主要用于合成表面活性剂,洗涤剂,润湿剂,医药和农药的中间体以及金色加工液等;
4.二异丙醇胺主要用于油气脱硫剂,橡胶防老化剂,纤维助剂,中间体等;
5.三异丙醇胺主要用作水泥添加剂,帮助降低水泥研磨过程中的能耗,同时对于提高水泥后期的强度有较大的帮助。水泥外加剂主要应用于水泥生产过程中,其作用是有利于水泥生产企业降低生产能耗、提高产品品质和生产效率。国外发达国家和地区的水泥生产企业已广泛使用水泥外加剂。
6.异丙醇胺的合成方法较多,由环氧丙烷和氨合成异丙醇胺是主流方法,合成异丙醇胺的过程中,一异丙醇胺、二异丙醇胺、三异丙醇胺是联产的,部分工艺对三种产品的比例可调,可以选择性的进行生产。异丙醇胺由于结构不同,其化学性质和用途也有所不同。由于异丙醇胺系列产品具有毒性小,安全无副作用及环保等优点,广泛应用于表面活性剂、医药农药中间体、金属加工液、石油及天然气等气体处理、工业与民用清洗剂、水泥行业、涂料、日化、聚氨酯等领域,具有广阔的市场前景。因此,如何低消耗、高效率的生产ipa,是本领域技术人员亟待解决的问题。
技术实现要素:
7.本发明的目的之一是针对现有技术的不足,提供一种异丙醇胺的合成系统,其结构简单、操作方便,运行效率大幅提高,可有效降低异丙醇铵的合成成本,满足市场的需求。
8.本发明的目的之二是提供一种利用上述合成系统合成异丙醇铵的方法,可有效提高原料环氧丙烷的选择性达到99.9%以上,且降低反应压力、温度,缩短反应时间,还具有节能、降耗的优点。
9.实现本发明目的之一的技术方案是:一种异丙醇胺的合成系统,包括第一混合器、微界面反应装置,所述微界面反应装置的数量至少为两个,微界面反应装置包括微界面反应器、阀门,阀门位于微界面反应器的上游,至少两个微界面反应装置通过串联相连,上游端的微界面反应装置的微界面反应器的进料口通过第一管路与液氨源相连,位于上游的微界面反应装置的微界面反应器的出料口通过第二管路连接在位于下游的微界面反应装置的微界面反应器和阀门之间,各微界面反应装置的阀门进口均与环氧丙烷源相连,所述第一混合器的进料口与催化剂源、液氨源相连,且其出料口通过第三管路连接在上游端的微界面反应装置的微界面反应器和阀门之间。
10.优选的,所述微界面反应装置的微界面反应器和阀门之间设置第二混合器。
11.进一步的,所述微界面反应器包括封闭的壳体,壳体内的绕管管内为物料通道,物料通道和壳体之间的空间为介质通道。
12.优选的,所述物料通道分为两段,两段物料通道分别呈往复折弯延伸形成第一绕管、第二绕管,且第二绕管相对第一绕管所在平面转动90
°
。
13.进一步的,所述微界面反应装置的数量六个。
14.实现本发明目的之二的技术方案是:采用任一上述异丙醇胺的合成系统合成异丙醇铵的方法,包括以下步骤:
15.1)以脱盐水作为催化剂,经第一混合器与液氨混合,得到催化剂溶液,催化剂与氨的摩尔比为0.5-1:1;
16.2)催化剂氨溶液经第三管路、液氨经第一管路、环氧丙烷经对应的阀门进入上游端的微界面反应器,催化剂溶液、液氨、环氧丙烷的流量比为0.82-0.58:0.7-0.51:1,控制上游端的微界面反应器的压力为5-10mpa,温度为150℃;
17.3)上游端的微界面反应器排出的混合物料依次经第二管路向下游的微界面反应器供料,且通过对应的阀门向下游的微界面反应器补充环氧丙烷,补充的环氧丙烷与上游端微界面反应器加入的环氧丙烷的流量比为0.95-1.05:1,控制下游的微界面反应器的压力为5-10mpa,温度为125-145℃;
18.4)下游端的微界面反应器排料口排出含有一异丙醇胺、二异丙醇胺、三异丙醇胺、氨的混合物料,送至精馏工序经分离得到目标产品。
19.优选的,步骤1)催化剂与氨的摩尔比为0.5:1。
20.优选的,步骤2)催化剂溶液、液氨、环氧丙烷的流量比为0.82:0.7:1,或者为0.58:0.51:1。
21.优选的,步骤3)补充的环氧丙烷与上游端微界面反应器加入的环氧丙烷的流量比为1:1。
22.采用上述技术方案具有以下有益效果:
23.1、本发明异丙醇胺的合成系统,包括第一混合器、微界面反应装置,其中,第一混合器用于混合催化剂和液氨,得到催化剂的液氨溶液,微界面反应装置作为原料的反应空间。所述微界面反应装置的数量至少为两个,微界面反应装置包括微界面反应器、阀门,阀门位于微界面反应器的上游,至少两个微界面反应装置通过串联相连。上游端的微界面反应装置的微界面反应器的进料口通过第一管路与液氨源相连,用于对上游端的微界面反应器提供液氨,作为原料。位于上游的微界面反应装置的微界面反应器的出料口通过第二管路连接在位于下游的微界面反应装置的微界面反应器和阀门之间,也即,在上游的微界面反应装置反应后的物料连续进入下游的微界面反应装置继续进行反应,保证其中的原料反应彻底,且充分利用上游的微界面反应装置生成的反应热。各微界面反应装置的阀门进口均与环氧丙烷源相连,用于向对应的微界面反应器提供、补充环氧丙烷,作为原料。所述第一混合器的进料口与催化剂源、液氨源相连,且其出料口通过第三管路连接在上游端的微界面反应装置的微界面反应器和阀门之间,先利用液氨作为溶剂,制备得到催化剂的液氨溶液,再与作为合成原料的液氨、环氧丙烷混合进入反应器。
24.2、本发明异丙醇胺的合成系统,其微界面反应器包括封闭的壳体,壳体内的绕管
管内为物料通道,物料通道和壳体之间的空间为介质通道,合成原料及催化剂的液氨溶液经微界面发生器处理后进入单向流动的物料通道,进行典型的界面反应,可有效提高液氨和环氧丙烷的合成效率,使得环氧丙烷的转化率达到100%,选择性达到99.9%以上,且降低反应所需压力和温度,反应更加温和,有效缩短了反应所需时间。
25.3、本发明异丙醇胺的合成系统,物料通道分为两段,两段物料通道分别呈往复折弯延伸形成第一绕管、第二绕管,且第二绕管相对第一绕管所在平面转动90
°
,极大提高了反应器的空间利用率,特定结构的物料通道使合成原料在单向流经物料通道过程中,持续掺混,新鲜的液氨及环氧丙烷交换到界面的表层,而合成产物不断去除,达到“推陈出新”的目的,仅需要使液氨轻微过量即可保证环氧丙烷的转化率达到100%,选择性达到99.9%以上。
26.4、本发明合成方法,先利用第一混合器混合制备催化剂溶液,再与合成原料的液氨、环氧丙烷混合,而不直接将催化剂与液氨、环氧丙烷混合,其原因为:由于氨与环氧丙烷反应过程十分缓慢,工业化生产难以进行,因此,本发明首先在常压条件下将液氨与催化剂(脱盐水)反应生成一水合氨,环氧丙烷再与一水合氨发生反应开环生成一异丙醇胺,若取消催化剂溶液制备过程,而直接将催化剂(脱盐水)、液氨、环氧丙烷一起混合进入反应器,则在反应器内需进行两种化学反应,首先是水合氨反应,需要较长停留时间,之后进行环氧丙烷的开环反应,导致环氧丙烷在反应器内的停留时间延长,反应器体积增大,且高压设备投资增多,同时大量游离液氨还会大大降低二异丙醇胺和三异丙醇胺产品比例,因此,从节约投资考虑,在常压设备完成催化剂溶液的制备。
27.5、本发明合成方法,在常压设备中制备催化会溶液时控制催化剂和液氨的摩尔比为0.5:1,其原因是,催化剂和液氨反应生成一水合氨,遇环氧丙烷即可发生反应并副产水,副产水与过量的液氨继续生成一水合氨,进入下游的反应器与补充的环氧丙烷反应,形成良性循环,如此可充分利用上游反应器副产的水,既满足生产需要,减少催化剂添加量50%,可有效减少催化剂循环量,节约能源,降低脱水塔设备投资及运行费用。且控制催化剂溶液、液氨、环氧丙烷的流量比为为0.82-0.58:0.7-0.51:1,根据异丙醇胺的反应原理可以得知,提高氨的摩尔比有利于一异丙醇铵的比例,提高环氧丙烷的摩尔比有利于二异丙醇胺和三异丙醇胺的比例。当需要以一异丙醇胺作为主要产品时,控制氨过量,有助于减少环氧丙烷与生成的一异丙醇胺反应,进而提高一异丙醇胺的产量,该工况下,液氨的摩尔比为0.7,既能满足提高一异丙醇胺产品比例,又能减少后续精馏系统氨回收塔的运行负荷,降低能耗;当需要以二异丙醇胺作为主要产品时,通过减少氨添加量并增加环氧丙烷的比例,使生成的一异丙醇胺与过量的环氧丙烷继续反应生成二异丙醇胺,进而达到降低一异丙醇胺比例而提高二异丙醇胺比例的目的。
28.下面结合附图和具体实施方式作进一步的说明。
附图说明
29.图1为本发明异丙醇铵合成系统的连接示意图。
30.附图中,1为第一混合器,2为第二混合器,3为微界面反应装置,4为微界面反应器,5为阀门,11为第一管路,12为第二管路,13为第三管路。
具体实施方式
31.本发明中,使用的原料为液氨和环氧丙烷,所需原料指标如下:
32.环氧丙烷质量指标(gb/t 14491-2015)
[0033][0034]
液氨质量指标(gb/t 536-2017)
[0035][0036][0037]
实施例1
[0038]
异丙醇胺的合成系统包括第一混合器1、微界面反应装置3。所述微界面反应装置3的数量为六个,微界面反应装置3包括微界面反应器4、阀门5,阀门5位于微界面反应器4的上游,本实施例中,微界面反应器包括竖直延伸的封闭壳体,壳体内的绕管管内为物料通道,且物料通道的进口位于壳体的下端,物料通道的出口位于壳体的上端,物料通道分为两段,两段物料通道分别呈往复折弯延伸形成第一绕管、第二绕管,且第二绕管相对第一绕管所在平面转动90
°
,物料通道和壳体之间的空间为介质通道,微界面反应器和阀门之间设置有第二混合器2,六个微界面反应装置通过串联相连,上游端的微界面反应装置的微界面反应器的进料口通过第一管路11与液氨源相连,具体的,液氮源连接在上游端微界面反应装置的第二混合器上游,且通常的,液氮源通过泵提供驱动力。位于上游的微界面反应装置的微界面反应器的出料口通过第二管路12连接在位于下游的微界面反应装置的微界面反应器和阀门之间,本实施例中,第二管路的下游端连接在下游的微界面反应器装置的第二混合器上游,也即,保证进入各微界面反应器的物料经过充分混合。各微界面反应装置的阀门进口均与环氧3丙烷源相连。所述第一混合器1的进料口与催化剂源、液氨源相连,且其出料口通过第三管路13连接在上游端的微界面反应装置的微界面反应器和阀门之间,显然的,第三管路的下游端连接在上游端微界面反应装置的第二混合器的上游,通常的,需要在第三管路上设置泵提供驱动力。
[0039]
实施例2
[0040]
利用实施例1的合成系统合成异丙醇铵,以年产2万吨异丙醇铵为例,包括以下步骤:
[0041]
1)以脱盐水作为催化剂,流量为0.36-0.49吨/小时,用于配制的液氨流量为0.42
吨/小时,经第一混合器混合,得到催化剂溶液;
[0042]
2)催化剂溶液经第三管路泵至上游端的第二混合器(对应图1最左侧的微界面反应装置),液氨经第一管路泵至上游端的第二混合器,液氨的流量为0.36-0.5吨/小时,环氧丙烷经上游端的阀门(对应图1最左侧的微界面反应装置)泵至上游端的第二混合器,环氧丙烷的流量为0.35吨/小时,经混合后,进入上游端的微界面反应器(对应图1最左侧)的物料通道,控制上游端的微界面反应器的压力为5-10mpag,且利用90℃的脱盐水作为冷媒介质,控制物料通道内的物料为150℃;
[0043]
3)上游端的微界面反应器排出的混合物料依次经第二管路向下游的微界面反应器供料(对应图1由左向右),且通过对应的阀门向下游的微界面反应器补充环氧丙烷,补充的环氧丙烷的流量0.35吨/小时,其中,由左向右第二个微界面反应器的温度控制为145℃,由左向右第三个微界面反应器的温度控制为140℃,由左向右第四个微界面反应器的温度控制为135℃,由左向右第五个微界面反应器的温度控制为130℃,由左向右第六个微界面反应器的温度控制为125℃,这五个微界面反应器的压力控制在5-10mpag;
[0044]
4)下游端的微界面反应器(对应图1最右侧的微界面反应器)排料口排出含有一异丙醇胺、二异丙醇胺、三异丙醇胺、氨的混合物料。
[0045]
在工况1条件下经检测:mipa1.25吨/小时,dipa1.0吨/小时,tipa0.25吨/小时,nh30.29吨/小时,h2o0.5吨/小时,其它0.04吨/小时。
[0046]
在工况2条件下经检测:mipa0.5吨/小时,dipa1.75吨/小时,tipa0.25吨/小时,nh30.2吨/小时,h2o0.36吨/小时,其它重组分0.04吨/小时,送至精馏工序经分离得到目标产品。
再多了解一些
本文用于企业家、创业者技术爱好者查询,结果仅供参考。