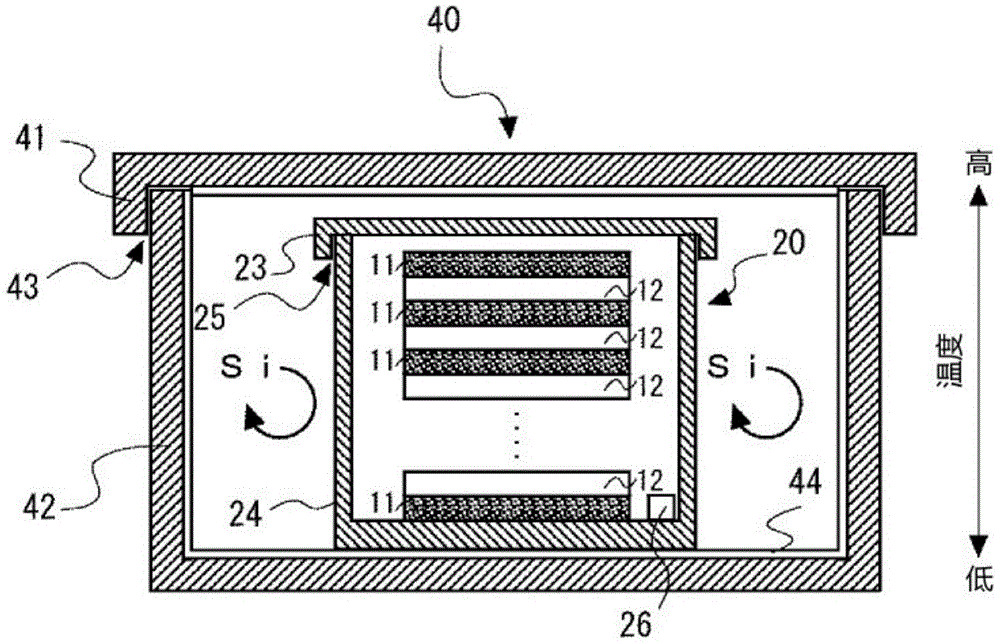
本发明涉及半导体衬底的制造方法和半导体衬底的制造装置。
背景技术
作为替代Si(硅)、GaAs(砷化镓)的下一代半导体材料,SiC(碳化硅)、GaN(氮化镓)、Ga2O3(氧化镓)等材料受到关注。
例如,SiC与Si相比,绝缘击穿电场大一个数量级,带隙大三倍,热导率高三倍左右。因此,SiC有望应用于功率器件、高频器件、高温工作器件等。
通常,用于制造SiC半导体器件的SiC衬底是通过对单晶SiC晶锭进行切片来制造的。作为该晶锭的生长方法,主要采用升华再结晶法(改良瑞利法)(参照专利文献1等)。
现有技术文献
专利文献
专利文献1:日本特开平3-295898号公报
技术实现要素:
发明所要解决的技术问题
但是,在改良瑞利法中,通过使SiC原材料的升华气体在单晶衬底(籽晶)的表面上进行再结晶,进行晶锭的生长。因此,再结晶(生长)后的表面成为新的生长表面,通过重复进行该操作来实现晶锭的加长。
然而,在该升华再结晶法中,存在的问题是,伴随生长表面的移动,生长条件时刻发生变化,由此单晶SiC的质量根据晶锭的部位而产生偏差。即,难以在整个晶锭上生长高质量的单晶SiC。
具体而言,由于晶锭的生长表面伴随晶锭生长而移动,因而生长表面与SiC原材料的距离、生长表面与加热器的相对位置发生变化。由此,在晶锭生长的初期阶段和后期阶段,生长表面附近的生长条件不同。
结果,在晶锭的某个部位处,通过期望的生长条件获得高质量的单晶SiC,而在该晶锭的别的部位处,偏离了优选的生长条件,造成位错的发生、其他多晶型的混入、亚晶界的发生等,存在无法获得高质量的单晶SiC的问题。
鉴于上述问题,本发明所要解决的技术问题是提供一种能够使高质量的半导体衬底生长的新技术。
用于解决问题的手段
为了解决上述问题,本发明是一种半导体衬底的制造方法,其包括:设置步骤,交替设置原衬底和原料体;以及加热步骤,加热所述原衬底和所述原料体并在所述原衬底上形成生长层。通过采用这样的结构,本发明可以在多个原衬底的各自中同时实现期望的生长条件,因而可以提供一种能够生长高质量的半导体衬底的新技术。
在本发明的优选方式中,在所述设置步骤中,将所述原衬底和所述原料体设置在准封闭空间中。通过采用这样的结构,本发明可以在期望的蒸气压环境下实现原衬底和原料体之间的原料输送。
在本发明的优选方式中,在所述加热步骤中进行加热,以在所述原衬底和所述原料体之间形成温度差。通过采用这样的结构,本发明可以在原衬底和原料体之间实现将原衬底和原料体之间的温度梯度作为驱动力的原料输送。
在本发明的优选方式中,还包括分离步骤,分离具有所述生长层的所述原衬底的一部分。通过采用这样的结构,本发明可以将高质量的半导体衬底从包括生长层的衬底分离。
在本发明的优选方式中,所述分离步骤包括:引入步骤,将损伤层引入到具有所述生长层的所述原衬底中;以及剥离步骤,剥离具有所述生长层的所述原衬底的一部分。通过采用这样的结构,本发明可以将损伤层引入到距原衬底的表面的期望深度,并可以从具有生长层的原衬底分离高质量的半导体衬底。
在本发明的优选方式中,在所述设置步骤中,将所述原衬底和所述原料体设置成紧密结合。本发明可以提供一种可以增大形成生长层的原衬底的数量、能够生长高质量的半导体衬底的、经济性优异的新技术。
在本发明的优选方式中,在所述设置步骤中,在包括所述原衬底和所述原料体的单位处理体之间设置防止所述原衬底和所述原料体之间的原料输送的原料输送防止体。通过采用这样的结构,本发明可以实现在原衬底的主表面或背表面中形成生长层的晶体生长。
在本发明的优选方式中,所述原衬底和所述原料体包括SiC材料。通过采用这样的结构,本发明可以提供一种能够生长高质量的SiC半导体衬底的新技术。
为了解决上述问题,本发明是一种衬底的制造装置,其中,具有:主体容器,能够交替设置原衬底和原料体;以及加热炉,能够加热所述原衬底和所述原料体并能够在所述原衬底上形成生长层。通过采用这样的结构,本发明可以在多个原衬底各自中同时实现期望的生长条件,因而可以提供一种能够生长高质量的半导体衬底的新技术。
在本发明的优选方式中,所述主体容器在内部具有准封闭空间。通过采用这样的结构,本发明可以在期望的蒸气压环境下实现原衬底和原料体之间的原料输送。
在本发明的优选方式中,所述主体容器将所述原衬底、所述原料体、原料输送防止体、所述原衬底和所述原料体依次层叠,并能够设置所述原衬底、原料体、原料输送防止体、原衬底和原料体。通过采用这样的结构,本发明可以实现仅在原衬底的主表面或背表面中形成生长层的晶体生长。
在本发明的优选方式中,所述加热炉能够在所述原衬底和所述原料体之间形成温度梯度。通过采用这样的结构,本发明可以在原衬底和原料体之间实现将原衬底和原料体之间的温度梯度作为驱动力的原料输送。
在本发明的优选方式中,还具有分离装置,能够分离具有所述生长层的所述原衬底的一部分。通过采用这样的结构,本发明可以将高质量的半导体衬底从包括生长层的衬底分离。
在本发明的优选方式中,所述分离装置具有:引入装置,能够向具有所述生长层的所述原衬底照射激光束并将损伤层引入到具有所述生长层的所述原衬底中;以及剥离装置,能够剥离具有所述生长层的所述原衬底的一部分。通过采用这样的结构,本发明可以将损伤层引入到距原衬底的表面的期望深度,并可以制造高质量的半导体衬底。
在本发明的优选方式中,所述原衬底和所述原料体包括SiC材料。通过采用这样的结构,本发明可以提供一种能够生长高质量的SiC半导体衬底的新技术。
发明的效果
根据所公开的技术,可以提供一种能够生长高质量的半导体衬底的新技术。
其他所要解决的技术问题、特征和优点将通过阅读以下记载的具体实施方式并结合附图和权利要求书而变得显而易见。
附图说明
图1是本发明的一实施方式的半导体衬底的制造方法的说明图。
图2是本发明的一实施方式的半导体衬底的制造方法的说明图。
图3是本发明的一实施方式的半导体衬底的制造方法的说明图。
图4是本发明的一实施方式的半导体衬底的制造装置的说明图。
图5是本发明的一实施方式的半导体衬底的制造装置的说明图。
图6是本发明的一实施方式的半导体衬底的制造装置的说明图。
图7是本发明的一实施方式的半导体衬底的制造装置的说明图。
图8是本发明的一实施方式的半导体衬底的制造装置的说明图。
图9是与参考例1中的BPD数量的评价相关的说明图。
图10是参考例2中的衬底表面的SEM像。
图11是参考例2中的衬底表面的SEM像。
图12是参考例3中的半导体衬底的生长速度与加热温度的相关图。
具体实施方式
以下,参照附图对本发明的一实施方式进行详细说明。本发明的技术范围不限于附图所示的实施方式,能够在权利要求书中所记载的范围内进行适当的改变。
《半导体衬底的制造方法》
以下,对本发明的一实施方式的衬底的制造方法(以下简称为制造方法)进行详细说明。
尽管本说明书例示了使用SiC材料进行SiC晶体生长的情况,但是在GaN(氮化镓)或Ga2O3(氧化镓)材料等半导体材料中也可以起到相同的作用效果。因此,原衬底11和原料体12是SiC、GaN和Ga2O3等半导体材料。
本发明可以理解为一种制造方法,其包括:设置步骤S1,交替设置原衬底11和原料体12;加热步骤S2,加热原衬底11和原料体12而在原衬底11上形成生长层111;以及分离步骤S3,分离由加热步骤S2加热的原衬底11的一部分。
<设置步骤S1>
根据本发明的一实施方式的设置步骤S1交替设置原衬底11和原料体12。此时,原衬底11和原料体12设置成大致平行。此时,对由设置步骤S1设置的原衬底11和原料体12各自的数量没有限制。
设置步骤S1将原衬底11和原料体12设置在准封闭空间中。
另外,本说明书中的说明中的“准封闭空间”是指虽然能够进行空间内部的抽真空,但能够将在空间内部产生的蒸气的至少一部分封闭的空间。
设置步骤S1将原衬底11和原料体12设置成紧密结合。
本说明书的说明中的“紧密结合”是指不同的部件等靠近并形成预定的隔开距离。
在设置步骤S1中,在包括原衬底11和原料体12的单位处理体1X之间设置用于防止后述的原衬底11和原料体12之间的原料输送的原料输送防止体28。本说明书中的说明中的“单位处理体1X”例如可以理解为分别由一个原衬底11和原料体12构成,并且例如,也可以理解为分别由多个原衬底11和原料体12构成。另外,根据本发明的一实施方式的设置步骤S1可以理解为设置一个以上的单位处理体1X。
<原衬底11和原料体12>
原衬底11可以例示从通过升华法等制造的晶锭切成圆盘状而获得的SiC晶片、和将SiC单晶加工成薄板状而获得的SiC衬底。另外,作为SiC单晶的晶体多晶型,可以采用任何多晶型。
原料体12优选具有与原衬底11相同的材料,并且至少包括构成原衬底11的原子物种。原料体12与原衬底11一样,可以采用从通过升华法等制造的晶锭切成圆盘状而获得的SiC晶片等、并且既可以是单晶衬底,也可以是多晶衬底。此外,原料体12也可以是包括SiC多晶的烧结体等加工品。
根据本发明的一实施方式的SiC单晶衬底表面可以例示从(0001)晶面或(000-1)晶面设置数度(例如,0.4至8.0°)的偏离角的表面(另外,在本说明书中,在米勒指数的标记中,横号“-”表示紧随其后为指数)。
在平坦化后的SiC单晶衬底表面处,可以确认台阶-平台结构。该台阶-平台结构为作为一分子层以上的台阶部位的台阶和作为{0001}晶面露出的平坦部位的平台交替排列而成的阶梯结构。在平坦化后的SiC单晶衬底表面上的台阶中,一分子层(0.25nm)为最小高度(最小单位),通过该一分子层重叠多层而形成各种台阶高度。
在本说明书中的说明中,台阶束化(聚束,bunching)而巨大化,并且将具有超过各多晶型的一晶胞的高度的称为宏观台阶聚束(Macro Step Bunching:MSB)。
即,MSB在4H-SiC的情况下是超过4分子层(5分子层以上)聚束而成的台阶,在6H-SiC的情况下是超过6分子层(7分子层以上)聚束而成的台阶。
另外,由于MSB是生长层形成时的表面处的缺陷发生、或SiC半导体器件中的氧化膜可靠性的阻碍等主要原因之一,因而期望的是,在衬底表面上不形成该MSB。
原衬底11和原料体12可以例示从数厘米见方的芯片尺寸至6英寸(约15.24厘米)以上的晶片尺寸,并且其尺寸没有限制。
原衬底11具有主表面113(未图示)和背表面114。此外,原料体12具有主表面123和背表面124(未图示)。
本说明书中的说明中的“表面”是指主表面和背表面的双方。此外,本说明书中的说明中的“一个表面”是指主表面和背表面中的任一个,另一表面是指与一个表面相对的同一衬底的表面。
此外,在本说明书的说明中,生长层111是指通过原料输送在原衬底11上形成的生长层。
此外,在本说明书的说明中,生长层121是指通过原料输送在原料体12上形成的生长层。
形成在原衬底11上的生长层的表面优选的是基底表位错(Basal Plane Dislocation:BPD)密度被无限降低。此外,在生长层111等的形成中,优选的是BPD转变为包含贯通刃型位错(Threading Edge Dislocation:TED)的其他缺陷/位错。
<加热步骤S2>
在加热步骤S2中,加热原衬底11和原料体12,使得在原衬底11和原料体12之间形成温度差,使原衬底11进行晶体生长,在原衬底11的表面处形成生长层111。
如图1所示,在加热步骤S2中,通过将原衬底11设置在低温侧,同时进行原衬底11(背表面114)中的生长层111的形成和原料体12(主表面123)的蚀刻。
在加热步骤S2中,将原衬底11和原料体12在准封闭空间内进行加热。
如图2所示,可以理解为,在原衬底11和原料体12中,持续地进行基于以下的1)至5)的反应的原料输送,并且例如在原料体12上形成生长层121。这即使在原衬底11上形成生长层111的情况下也是同样的。
另外,尽管根据本发明的一实施方式的原衬底11和原料体12紧密结合,但即使在该情况下,也可以理解为,原衬底11和原料体12之间的微小空隙成为原料输送空间。
1)SiC(s)→Si(v) C(s)
2)2C(s) Si(v)→SiC2(v)
3)C(s) 2Si(v)→Si2C(v)
4)Si(v) SiC2(v)→2SiC(s)
5)Si2C(v)→Si(v) SiC(s)
1)的说明:由于原衬底11的背表面114被热分解,因而Si原子(Si(v))从背表面114脱离。
2)和3)的说明:由于Si原子(Si(v))脱离而残留在背表面114处的C原子(C(s))与原料输送空间内的Si蒸气(Si(v))反应而成为Si2C或SiC2等并在原料输送空间内升华。
4)和5)的说明:所升华的Si2C或SiC2等由于温度梯度而到达/扩散到原料体12的主表面123的平台,并且到达台阶,由此延续主表面123的多型而使生长层121生长/形成(台阶流动生长)。
加热步骤S2包括:Si原子升华步骤S21,使Si原子从原衬底11或原料体12的表面热升华;以及C原子升华步骤S22,使残留在原衬底11或原料体12的表面处的C原子与原料输送空间内的Si原子键合而使其升华。
此外,加热步骤S2包括:蚀刻步骤S23,基于Si原子升华步骤S21和C原子升华步骤S22对原衬底11或原料体12的表面进行蚀刻。例如,加热步骤S2包括:生长步骤S24,对原料体12的表面进行蚀刻,另一方面在原衬底11的表面中,基于上述的台阶流动生长形成生长层111。依次进行加热步骤S2中包括的各步骤。另外,由于所输送的Si2C或SiC2等过饱和而凝结,从而形成生长层111,因而可以理解为,生长步骤S24是基于PVT(物理气相输送)的步骤。
此外,可以理解为,加热步骤S2包括分解SiC单晶衬底表面上的MSB的聚束分解步骤。
可以理解为,加热步骤S2中的原料输送的驱动力是由所形成的温度梯度引起的原衬底11和原料体12之间的蒸气压差。因此,可以理解为,不仅原衬底11和原料体12各自的表面处的温度差,而且由原衬底11和原料体12之间的晶体结构引起的蒸气压差或化学势差也可以成为原料输送的驱动力。
另外,可以理解为,在加热步骤S2中,在将原衬底11、原料体12、原料输送防止体28、原衬底11和原料体12依次层叠的情况下,仅在原衬底11的主表面或背表面形成生长层111。
作为在加热步骤S2中用于形成准封闭空间的装置的一部分的SiC材料可以适当地成为原料体12。
在加热步骤S2中的原料输送中,通过使用掺杂气体供给装置将掺杂气体供给到准封闭空间内,可以调整生长层111的掺杂浓度。可以理解为,在未通过掺杂气体供给装置向准封闭空间内供给掺杂气体的情况下,生长层111延续准封闭空间内的掺杂浓度。
加热步骤S2中的原料输送优选在具有包含Si元素的气相物种和包含C元素的气相物种的环境下进行,更优选在SiC-Si平衡蒸气压环境下进行,进一步优选在SiC-C平衡蒸气压环境下进行。
本说明书中的说明中的“SiC-Si蒸气压环境”是指当SiC(固体)和Si(液相)通过气相成为相平衡状态时的蒸气压环境。
此外,本说明书中的说明中的“SiC-C平衡蒸气压环境”是指当SiC(固相)和C(固相)通过气相成为相平衡状态时的蒸气压环境。
SiC-Si平衡蒸气压环境是通过对Si/C原子数比超过1的准封闭空间进行加热而形成的。
SiC-C平衡蒸气压环境是通过对Si/C原子数比为1以下的准封闭空间进行加热而形成的。
加热步骤S2中的加热温度优选设定在1400至2300℃的范围内,更优选设定在1600至2000℃的范围内。
加热步骤S2中的加热时间可以设定为能够达到期望的蚀刻量的任意时间。
例如,当蚀刻速度为1.0μm/min时,在想要将蚀刻量设定为1.0μm的情况下,加热时间为1min(1分钟)。
期望的是,加热步骤S2中的温度梯度例如设定在0.1至5.0℃/mm的范围内,并且在原料输送空间中是一样的。
加热步骤S2中的蚀刻量和生长量例如在0.1至20μm的范围内,但可以根据需要适当改变。此外,可以理解为,蚀刻量和生长量是相同的。
加热步骤S2中的蚀刻速度和生长层111的生长速度可以通过上述温度范围来进行控制,并且例如可以设定在0.001至2.0μm/min的范围内。
可以理解为,在加热步骤S2中被蚀刻的SiC单晶衬底上的表面层例如是经过机械加工(例如,切片、研磨/抛光)、激光加工等被引入的划痕、潜在划痕、应变等的损伤层300等。
<分离步骤S3>
作为分离步骤S3中的分离衬底13的方法,可以例示以下方法:通过使多根金属丝往复运动来进行切断的多金属丝锯切断,断续地产生等离子放电而进行切断的放电加工法,在晶体中照射/会聚激光束并使用形成成为切断的基点的层的激光束来进行切断的方法。分离步骤S3在采用使用激光束来进行切断的方法的情况下,可以减少衬底13的分离中的材料损失。
分离步骤S3将具有生长层111的原衬底11的一部分分离,并获得具有生长层111的衬底13。
此外,分离步骤S3至少包括:引入步骤31,将损伤层300引入到原衬底11中;和剥离步骤S32,以损伤层300为起点剥离衬底13。
如图3所示,引入步骤S31将对原衬底11具有透射性的波长的激光束的会聚点作为相当于应从上表面分离的衬底13的厚度的深度,使其位于原衬底11的内部,并对原衬底11照射激光束来形成损伤层300。
如图3所示,在剥离步骤S32中,沿损伤层300从原衬底11剥离具有生长层111的衬底13。剥离步骤S32可以例示将原衬底11的正表面和背表面吸附到基座等上并将它们分离的方法。此外,剥离步骤S32通过使细金属丝沿损伤层300往复运动或产生超声波振动等来将常规机械振动赋予给原衬底11,并以损伤层300为起点从原衬底11剥离衬底13。
引入步骤S31和剥离步骤S32可以适当采用例如日本特开2013-49161号公报、日本特开2018-207034号公报、日本特表2017-500725号公报、日本特开2017-526161号公报等中记载的方法等的公知技术的至少一部分。
此外,引入步骤S31和剥离步骤S32可以适当采用例如日本特表2017-526161号公报、日本特表2017-500725号公报、日本特开2018-152582号公报、日本特表2019-500220号公报以及日本特表2019-511122号公报等专利文献中记载的方法等的公知技术的至少一部分。
如上所述,原衬底11经过设置步骤S1、加热步骤S2以及分离步骤S3,从而制造具有生长层111的衬底13。通过重复进行该步骤组,可以重复制造具有生长层111的衬底13。此外,可以将所制造的具有生长层111的衬底13作为原衬底11,再次进行该步骤组。
经过设置步骤S1、加热步骤S2以及分离步骤S3获得的原衬底11和衬底13分别具有残留的损伤层300。因此,在本发明的一实施方式中,也可以采用这样的结构:通过对分离步骤S3之后的原衬底11和衬底13实施包括蚀刻步骤S23的加热步骤S2,从而去除在原衬底11和衬底13中残留的损伤层300。
本发明的一实施方式可以依次进行设置步骤S1、加热步骤S2、设置步骤S1a、加热步骤S2a以及分离步骤S3。此时,设置步骤S1a沿原衬底11和原料体12的厚度方向设置原衬底11和原料体12,以使由设置步骤S1设置的原衬底11和原料体12的设置顺序反转。此外,此时,加热步骤S2a与加热步骤S2一样地对原衬底11和原料体12进行加热。
此外,本发明的一实施方式可以依次进行设置步骤S1、加热步骤S2、加热步骤S2a以及分离步骤S3。此时,加热步骤S2b对原衬底11和原料体12进行加热,以使沿原衬底11和原料体12的厚度方向形成的温度梯度反转。此外,此时,加热步骤S2b在与加热步骤S2相同的温度条件、气氛下,基于原料输送机构,对原衬底11和原料体12进行加热。
《半导体衬底的制造装置》
以下,本说明书对本发明的一实施方式的半导体衬底的制造装置(以下,简称为制造装置)进行详细说明。另外,对于与上述制造方法中所示的结构基本相同的结构要素,标注相同的附图标记并简化其说明。
如图4所示,制造装置具有主体容器20、加热炉30、高熔点容器40以及分离装置50。
可以理解为,原衬底11和原料体12以形成预定的隔开距离1112的方式交替设置。
隔开距离1112优选为10mm以下,更优选为7.0mm以下,更优选为5.0mm以下,更优选为4.0mm以下,更优选为3.0mm以下,更优选为2.0mm以下,更优选为1.7mm以下,更优选为1.5mm以下,更优选为1.2mm以下,更优选为1.0mm以下,更优选为700μm以下,更优选为500μm以下,更优选为200μm以下,更优选为100μm以下,更优选为70μm以下,更优选为50μm以下,更优选为20μm以下,更优选为10μm以下,更优选为7.0μm以下,更优选为5.0μm以下,更优选为2.0μm以下,更优选为1.0μm以下,更优选为0.7μm以下,更优选为0.5μm以下,更优选为0.2μm以下。
此外,隔开距离1112优选为0.1μm以上,更优选为0.2μm以上,更优选为0.5μm以上,更优选为0.7μm以上,更优选为1.0μm以上,更优选为2.0μm以上,更优选为5.0μm以上,更优选为7.0μm以上,更优选为10μm以上,更优选为20μm以上,更优选为50μm以上,更优选为70μm以上,更优选为100μm以上,更优选为200μm以上,更优选为500μm以上,更优选为700μm以上,更优选为1.0mm以上,更优选为1.2mm以上,更优选为1.5mm以上,更优选为1.7mm以上,更优选为2.0mm以上,更优选为3.0mm以上,更优选为4.0mm以上,更优选为5.0mm以上,更优选为7.0mm以上。
主体容器20也可以包括用于调整隔开距离1112的间隔件等常规的距离调整装置27。距离调整装置27由与原衬底11和原料体12相同的原子物种构成。
<主体容器20>
如图5所示,主体容器20是能够交替设置原衬底11和原料体12的容器。此时,原衬底11和原料体12设置成紧密结合。此时,主体容器20在内部具有准封闭空间。此外,主体容器20在被加热时在内部产生包含构成原衬底11的原子物种的气相物种的蒸气压。此时,对由主体容器20设置的原衬底11和原料体12各自的数量没有限制。另外,原衬底11和原料体12既可以按原衬底11、原料体12和原衬底11的顺序交替设置,也可以按原料体12、原衬底11和原料体12的顺序交替设置。
如图6所示,主体容器20是能够交替设置原衬底11和原料体12的容器。此时,原衬底11和原料体12通过距离调整装置27以分离隔开距离1112的方式交替设置。另外,原衬底11和原料体12既可以按原衬底11、原料体12和原衬底11的顺序交替设置,也可以按原料体12、原衬底11和原料体12的顺序交替设置。
此外,主体容器20在内部具有准封闭空间。此时,主体容器20在被加热时在内部产生包含构成原衬底11的原子物种的气相物种的蒸气压。此时,对由主体容器20设置的原衬底11和原料体12各自的数量没有限制。
如图7所示,主体容器20是能够在包括原衬底11和原料体12的单位处理体1X之间设置原料输送防止体28的容器,该原料输送防止体28防止在不同的单位处理体1X之间的、原衬底11和原料体12之间的原料输送。此时,对由主体容器20设置的单位处理体1X和原料输送防止体28各自的数量没有限制。另外,原衬底11和原料体12既可以按原衬底11、原料体12和原衬底11的顺序交替设置,也可以按原料体12、原衬底11和原料体12的顺序交替设置。
原料输送防止体28优选为不成为上述的原衬底11和原料体12之间的原料输送中的输送目的地或输送源的W、Re、Os、Ta、Mo等高熔点金属、Ta9C8、HfC、TaC、NbC、ZrC、Ta2C、TiC、WC、MoC等碳化物、HfB2、TaB2、ZrB2、NB2、TiB2等硼化物等。
如图8所示,多个主体容器20分别收纳一个原衬底11。此时,多个主体容器20分别能够相互嵌合。此时,主体容器20在内部具有准封闭空间。此时,主体容器20在被加热时在内部产生包含构成原衬底11的原子物种的气相物种的蒸气压。此时,对收纳一个原衬底11的主体容器20的数量没有限制。另外,多个主体容器20也可以构成为分别收纳原衬底11和原料体12。
主体容器20例如由包含SiC多晶的SiC材料构成。因此,主体容器20的至少一部分作为原料体12可以成为原料输送中的输送目的地或输送源。
在本发明的一实施方式中,也可以通过适当组合图5至图8各自中的结构的至少一部分,实现至少能够交替设置原衬底11和原料体12的主体容器。
期望的是,加热后的主体容器20内的环境例如成为包含Si元素的气相物种和包含C元素的气相物种的混合体系的蒸气压环境。作为包含该Si元素的气相物种,可以例示Si、Si2、Si3、Si2C、SiC2、SiC等。此外,作为包含C元素的气相物种,可以例示Si2C、SiC2、SiC、C等。
主体容器20的掺杂剂和掺杂浓度可以根据想要形成的生长层111或121的掺杂剂和掺杂浓度来选择。作为掺杂剂,可以例示N元素。
此外,只要是在主体容器20的加热处理时在内部空间中产生包含Si元素的气相物种和包含C元素的气相物种的蒸气压的结构,就可以采用该结构。例如,可以示出在内表面的一部分处露出SiC多晶的结构、或在主体容器20内单独设置SiC多晶的结构等。
例如,主体容器20是包括能够相互嵌合的上容器23和下容器24的嵌合容器。在上容器23和下容器24的嵌合部处形成有微小的间隙25,构成为能够从该间隙25进行主体容器20内的排气(抽真空)。
<Si蒸气供给源26>
主体容器20具有Si蒸气供给源26(在图4中未图示,在图5中图示)。Si蒸气供给源26是以将主体容器20内的准封闭空间的Si/C原子数比调整为超过1为目的而使用的。作为Si蒸气供给源,可以例示固体的Si(Si片或Si粉末等的Si颗粒)或Si化合物。
例如,如本发明的一实施方式那样,在主体容器20整体由SiC多晶构成的情况下,通过设置Si蒸气供给源26,主体容器20内的Si/C原子数比超过1。具体地,当在满足化学计量比1:1的SiC多晶的主体容器20内设置了满足化学计量比1:1的原衬底11和原料体12以及Si蒸气供给源26的情况下,主体容器20内的Si/C原子数比超过1。
根据本发明的一实施方式的SiC-Si平衡蒸气压环境是通过对Si/C原子数比超过1的准封闭空间进行加热而形成的。此外,根据本发明的一实施方式的SiC-C平衡蒸气压环境是通过对Si/C原子数比为1以下的准封闭空间进行加热而形成的。根据本发明的一实施方式的主体容器20也可以构成为适当收纳预定部件,使得分别成为SiC-Si平衡蒸气压环境或SiC-C平衡蒸气压环境。
<加热炉30>
加热炉30构成为进行加热以形成温度梯度,使得温度从主体容器20的上容器23朝向下容器24下降/上升。由此,在原衬底11的厚度方向上形成温度梯度。
如图4所示,加热炉30包括:主加热室31,能够将被处理物(原衬底11或主体容器20、高熔点容器40等)加热到1000℃以上且2300℃以下的温度;预备室32,能够将被处理物预热到500℃以上的温度;高熔点容器40,能够收纳主体容器20;以及移动装置33(移动台),能够将该高熔点容器40从预备室32移动到主加热室31。
主加热室31在平面剖视图中形成为正六边形,并且在其内侧设置有高熔点容器40。主加热室31内设置有加热器34(网状加热器)。此外,在主加热室31的侧壁或顶部处固定有多层热反射金属板(未图示)。多层热反射金属板构成为使加热器34的热量朝向主加热室31的大致中央部反射。
加热器34设置成在主加热室31内围绕收纳被处理物的高熔点容器40。此时,通过在加热器34的外侧设置多层热反射金属板,能够实现在1000℃以上且2300℃以下的温度范围内的升温。
加热器34例如可以采用电阻加热式的加热器或高频感应加热式的加热器。
加热器34也可以采用能够在高熔点容器40内形成温度梯度的结构。
加热器34例如也可以构成为在上侧(或下侧)设置多个加热器。此外,加热器34也可以构成为使宽度随着朝向上侧(或下侧)而变大。或者,加热器34也可以构成为能够随着朝向上侧(或下侧)而增大所供给的电力。此外,加热器34也可以能够使温度梯度的形成方向反转。
在主加热室31连接有:真空形成用阀35,进行主加热室31内的排气;惰性气体注入用阀36,将惰性气体导入到主加热室31内;以及真空计37,测量主加热室31内的真空度。
真空形成用阀35与对主加热室31内进行排气而抽真空的抽真空泵连接(未图示)。通过该真空形成用阀35和抽真空泵,可以将主加热室31内的真空度调整为优选10Pa以下,更优选1.0Pa以下,最优选10-3Pa以下。作为该抽真空泵,可以例示涡轮分子泵。
惰性气体注入用阀36与惰性气体供给源连接(未图示)。通过该惰性气体注入用阀36和惰性气体供给源,可以在10-5至104Pa的范围内将惰性气体导入主加热室31内。作为该惰性气体,可以选择Ar等。
惰性气体注入用阀36是能够向主体容器20内供给掺杂气体的掺杂气体供给装置。即,通过选择掺杂气体(例如,N2等)作为惰性气体,可以提高生长层111的掺杂浓度。
预备室32与主加热室31连接,并且构成为能够通过移动装置33移动高熔点容器40。另外,本实施方式的预备室32构成为能够利用主加热室31的加热器34的余热来升温。例如,在将主加热室31升温到2000℃的情况下,预备室32被升温到1000℃左右,可以进行被处理物的脱气处理。
移动装置33构成为能够载置高熔点容器40并在主加热室31和预备室32之间移动。
由于利用移动装置33进行的主加热室31与预备室32之间的输送最短在1分钟左右完成,因而可以实现1.0至1000℃/min的升温/降温。由此,由于可以进行急速升温和急速降温,因而能够观察不具有升温中和降温中的低温生长历史的表面形状。此外,在图4中,预备室32设置在主加热室31的下方,但不限于此,预备室32也可以设置在任何方向上。
根据本实施方式的移动装置33是用于载置高熔点容器40的移动台。该移动台和高熔点容器40的接触部成为热量的传播路径。由此,可以在高熔点容器40内形成温度梯度,使得移动台和高熔点容器40的接触部侧成为低温侧。
在本实施方式的加热炉30中,由于高熔点容器40的底部与移动台接触,因而温度梯度被设置成使温度从高熔点容器40的上容器41朝向下容器42下降。
通过改变移动台和高熔点容器40的接触部的位置,可以将温度梯度的方向设定为任意方向。例如,在移动台采用悬挂式等并且将接触部设置在高熔点容器40的顶部处的情况下,热量向上方向逸出。因此,温度梯度设置成使温度从高熔点容器40的上容器41朝向下容器42上升。另外,期望的是,该温度梯度沿原衬底11和原料体12的厚度方向形成。此外,如上所述,也可以根据加热器34的结构形成温度梯度。
<高熔点容器40>
根据本实施方式的加热炉30内的包含Si元素的气相物种的蒸气压环境是使用高熔点容器40和Si蒸气供给材料44来形成的。例如,只要是能够在主体容器20的周围形成包含Si元素的气相物种的蒸气压环境的方法,就可以在本发明的半导体衬底的制造装置中采用。
高熔点容器40优选的是构成为包括具有与构成主体容器20的材料的熔点相同或其以上的熔点的高熔点材料。
高熔点容器40例如可以例示:作为通用耐热部件的C,作为高熔点金属的W、Re、Os、Ta、Mo,作为碳化物的Ta9C8、HfC、TaC、NbC、ZrC、Ta2C、TiC、WC、MoC,作为氮化物的HfN、TaN、BN、Ta2N、ZrN、TiN,作为硼化物的HfB2、TaB2、ZrB2、NB2、TiB2,SiC多晶等。
如图5所示,高熔点容器40与主体容器20一样,是包括能够相互嵌合的上容器41和下容器42的嵌合容器,并且构成为能够收纳主体容器20。在上容器41和下容器42的嵌合部处形成有微小的间隙43,构成为能够从该间隙43进行高熔点容器40内的排气(抽真空)。
高熔点容器40具有能够向高熔点容器40内供给包含Si元素的气相物种的蒸气压的Si蒸气供给材料44。
<Si蒸气供给材料44>
Si蒸气供给材料44只要是在加热处理时在高熔点容器40内产生Si蒸气的结构即可,例如可以例示固体的Si(Si片或Si粉末等的Si颗粒)或Si化合物。
Si蒸气供给材料44例如是包覆高熔点容器40的内壁的薄膜。
在高熔点容器40是TaC等的金属化合物的情况下,Si蒸气供给材料44例如是构成高熔点容器40的金属原子和Si原子的硅化物材料。
<分离装置>
分离装置50分离具有生长层111的原衬底11的一部分,并获得具有生长层111的衬底13。
此外,分离装置50至少包括:引入装置51,将损伤层300引入到原衬底11中;和剥离装置52,以损伤层300为起点剥离衬底13。
如图3所示,引入装置51将对生长层111和原衬底11具有透射性的波长的激光束的会聚点作为相当于应从上表面分离的衬底13的厚度的深度,使其位于原衬底11的内部,并对原衬底11照射激光束来形成损伤层300。
引入装置51例如包括:保持装置(未图示),能够基于吸附卡盘等常规方法保持原衬底11和原料体12;振荡装置511,能够照射进行脉冲振荡的激光束的光源;以及透镜等常规会聚装置512,能够会聚该激光束,并且引入装置51能够扫描振荡装置511和会聚装置512中的至少一部分。
此外,在引入装置51中,构成引入装置51的各装置的至少一部分具有能够在任意的轴方向上对准的常规调整装置。另外,对该激光束的波长、时间宽度、输出以及光斑直径等没有限制。
如图3所示,剥离装置52沿损伤层300从原衬底11剥离具有生长层111的衬底13。
此外,剥离装置52可以例示将原衬底11的正表面和背表面吸附到基座等上并将它们分离的方法。
此外,剥离装置52通过使细金属丝沿损伤层300往复运动或产生超声波振动等来将常规机械振动赋予给原衬底11,并以损伤层300为起点从原衬底11剥离衬底13。
剥离装置52具有:剥离用高熔点容器,能够收纳原衬底11;和保持装置,能够基于吸附卡盘等常规方法保持原衬底11。
此外,剥离装置52具有:振动装置,能够产生包括超声波振动的常规机械振动并将该机械振动赋予给原衬底11;和液体供给装置,能够供给纯水等液体并且基于常规方法。
引入装置51和剥离装置52可以适当采用用于实现公知技术的装置等。
引入装置51和剥离装置52分别可以适当采用例如日本特开2013-49161号公报、日本特开2018-207034号公报、日本特表2017-500725号公报、日本特开2017-526161号公报等中记载的装置等的至少一部分。
此外,引入装置51和剥离装置52分别可以适当采用例如日本特表2017-526161号公报、日本特表2017-500725号公报、日本特开2018-152582号公报、日本特表2019-500220号公报以及日本特表2019-511122号公报等专利文献中记载的装置等的至少一部分。
如上所述,原衬底11经过利用主体容器20、加热炉30以及分离装置50进行的处理,从而制造具有生长层111的衬底13。通过重复进行该处理,可以重复制造具有生长层111的衬底13。此外,也可以将具有生长层111的衬底13作为新的原衬底11来进行该处理。
本说明书结合参考例1至3来说明根据本发明的作用效果。
《参考例1》
在以下条件下,将SiC单晶衬底E10收纳在主体容器20中,并且将主体容器20收纳在高熔点容器40中。
<SiC单晶衬底E10>
多晶型:4H-SiC
衬底尺寸:横宽(10mm)、纵宽(10mm)、厚度(0.3mm)
偏离方向和偏离角:<11-20>方向4°偏离
生长表面:(0001)晶面
MSB的有无:无
损伤层:无
<主体容器>
材料:SiC多晶
容器尺寸:直径(60mm)、高度(4.0mm)
SiC单晶衬底E10与SiC材料的距离:2.0mm
容器内的Si/C原子数比:1以下
<高熔点容器>
材料:TaC
容器尺寸:直径(160mm)、高度(60mm)
Si蒸气供给材料44(Si化合物):TaSi2
在以下条件下对在上述条件下设置的SiC单晶衬底E10进行了加热处理。
加热温度:1700℃
加热时间:300min
温度梯度:1.0℃/mm
生长速度:5.0nm/min
主加热室31的真空度:10-5Pa
图9是求出在生长层E11中从BPD转变为其他缺陷/位错(TED等)的转变率的方法的说明图。
图9中的(a)示出了通过加热步骤使生长层E11生长的状况。在该加热步骤中,存在于SiC单晶衬底E10处的BPD以一定概率转变为TED。因此,除非进行100%转变,否则TED和BPD会混合存在于生长层E11的表面处。
图9中的(b)示出了使用KOH溶解蚀刻法确认了生长层E11中的缺陷的状况。该KOH溶解蚀刻法是这样的方法:将SiC单晶衬底E10浸入加热到约500℃的溶解盐(KOH等)中,在位错或缺陷部分处形成蚀刻坑,并且根据该蚀刻坑的尺寸/形状来判别位错的种类。通过该方法,评价存在于生长层E11表面处的BPD数量。
图9中的(c)示出了在KOH溶解蚀刻之后去除生长层E11的状况。
在该方法中,在通过机械抛光、CMP等平坦化到蚀刻坑深度之后,通过热蚀刻去除生长层E11,从而使SiC单晶衬底E10的表面露出。
图9中的(d)示出了针对去除了生长层E11的SiC单晶衬底E10使用KOH溶解蚀刻法确认了SiC单晶衬底E10中的缺陷的状况。通过该方法,评价存在于SiC单晶衬底E10表面处的BPD数量。
根据图9所示的一系列顺序,将存在于生长层E11表面处的BPD数量(参照图9中的(b))和存在于SiC单晶衬底E10表面处的BPD数量(图9中的(d))进行比较,从而可以获得在加热步骤S2中从BPD转变为其他缺陷/位错的BPD转变率。
参考例1的存在于生长层E11表面处的BPD数量约为0/cm-2,存在于SiC单晶衬底E10表面处的BPD数量为1000个cm-2。即,可以理解为,通过将表面处不存在MSB的SiC单晶衬底E10设置在Si/C原子数比为1以下的准封闭空间并进行加热来减少/去除BPD。
在参考例1中,在主体容器20内形成SiC-C平衡蒸气压环境,使得主体容器20内的Si/C原子数比为1以下。可以理解为,由于上述方法中的包括蚀刻步骤S23的加热步骤S2和根据本发明的一实施方式的包括蚀刻步骤的加热步骤S2基于同一反应过程,因而即使在根据本发明的一实施方式的蚀刻步骤中也可以减少/去除BPD。
《参考例2》
在以下条件下,将SiC单晶衬底E10收纳在主体容器20中,并且将主体容器20收纳在高熔点容器40中。
<SiC单晶衬底E10>
多晶型:4H-SiC
衬底尺寸:横宽(10mm)、纵宽(10mm)、厚度(0.3mm)
偏离方向和偏离角:<11-20>方向4°偏离
生长表面:(0001)晶面
MSB的有无:有
<主体容器>
材料:SiC多晶
容器尺寸:直径(60mm)、高度(4.0mm)
SiC单晶衬底E10与SiC材料的距离:2.0mm
Si蒸气供给源26:Si片
容器内的Si/C原子数比:超过1
通过将Si片与SiC单晶衬底一起收纳在主体容器20内,容器内的Si/C原子数比超过1。
<高熔点容器>
材料:TaC
容器尺寸:直径160mm×高度60mm
Si蒸气供给材料44(Si化合物):TaSi2
在以下条件下对在上述条件下设置的SiC单晶衬底E10进行了加热处理。
加热温度:1800℃
加热时间:60min
温度梯度:1.0℃/mm
生长速度:68nm/min
主加热室31的真空度:10-5Pa
图10是生长层E11的生长前的SiC单晶衬底E10表面的SEM像。图10中的(a)是以倍率×1000观察到的SEM像,图10中的(b)是以倍率×100000观察到的SEM像。可以理解为,在该生长层E11的生长前的SiC单晶衬底E10表面处形成有MSB,并且高度3.0nm以上的台阶以平均42nm的平台宽度排列。另外,通过AFM测量了台阶高度。
图11是生长层E11的生长后的SiC单晶衬底E10表面的SEM像。图11中的(a)是以倍率×1000观察到的SEM像,图11中的(b)是以倍率×100000观察到的SEM像。
可以理解为,在参考例2的生长层E11表面处未形成MSB,并且1.0nm(全晶胞)的台阶以14nm的平台宽度有规则地排列。另外,通过AFM测量了台阶高度。
因此,可以理解为,通过将表面处存在MSB的SiC单晶衬底E10设置在Si/C原子数比超过1的准封闭空间中并进行加热来形成MSB被分解的生长层E11。
在参考例2中,由于将Si蒸气供给源26设置成使主体容器20内的Si/C原子数比超过1,因而在主体容器20内形成SiC-Si平衡蒸气压环境。
可以理解为,由于上述方法中的包括蚀刻步骤S23的加热步骤S2和根据本发明的一实施方式的包括蚀刻步骤的加热步骤基于同一反应过程,因而即使在根据本发明的一实施方式的蚀刻步骤中也可以分解SiC单晶衬底表面上的MSB。
《参考例3》
图12是示出通过根据本发明的SiC单晶衬底的制造方法进行生长得到的加热温度与生长速度之间的关系的曲线图。该曲线图的横轴是温度的倒数,并且该曲线图的纵轴以对数表示生长速度。将SiC单晶衬底E10设置在Si/C原子数比超过1的空间(主体容器20内)中并在SiC单晶衬底E10上使生长层E11进行生长得到的结果用○标记表示。此外,将SiC单晶衬底E10设置在Si/C原子数比为1以下的空间(主体容器20内)中并在SiC单晶衬底E10上使生长层E11进行生长得到的结果用×标记表示。
此外,在图12的曲线图中,将SiC-Si平衡蒸气压环境中的SiC衬底生长的热力学计算结果用虚线(阿伦尼乌斯图)表示,并且将SiC-C平衡蒸气压环境中的SiC衬底生长的热力学计算结果用双点划线(阿伦尼乌斯图)表示。
在本方法中,在SiC原料与SiC衬底之间的蒸气压环境成为SiC-C平衡蒸气压环境或SiC-C平衡蒸气压环境的条件下,将化学势差或温度梯度作为生长驱动力,使SiC单晶衬底E10生长。该化学势差可以例示在SiC多晶和SiC单晶的表面产生的气相物种的分压差。
在此,在将从SiC原料(输送源)和SiC衬底(输送目的地)产生的蒸气的分压差作为生长量的情况下,通过以下的式1求出SiC生长速度。
[式1]
在此,T为SiC原料侧的温度,mi为气相物种(SixCy)的分子量,k为玻尔兹曼常数。此外,P输送源i-P输送目的地i是原料气体成为过饱和状态而作为SiC析出的生长量,并且作为原料气体,可以设想SiC、Si2C、SiC2。
因此,虚线是在SiC(固体)和Si(液相)通过气相成为相平衡状态时的蒸气压环境中以SiC多晶为原料使SiC单晶生长时的热力学计算结果。具体地,该结果是使用式1在以下的条件(i)~(iv)下进行了热力学计算而得到的。
(i)是体积恒定的SiC-Si平衡蒸气压环境;
(ii)生长驱动力是主体容器20内的温度梯度和SiC多晶与SiC单晶之间的蒸气压差(化学势差);
(iii)原料气体为SiC、Si2C、SiC2;
(iv)原料吸附到SiC单晶衬底E10的台阶的吸附系数为0.001。
此外,双点划线是在SiC(固相)和C(固相)通过气相成为相平衡状态时的蒸气压环境中以SiC多晶为原料使SiC单晶生长时的热力学计算结果。具体地,该结果是使用式1在以下的条件(i)~(iv)下进行热力学计算而得到的。
(i)是体积恒定的SiC-C平衡蒸气压环境;
(ii)生长驱动力是主体容器20内的温度梯度和SiC多晶与SiC单晶之间的蒸气压差(化学势差);
(iii)原料气体为SiC、Si2C、SiC2;
(iv)原料吸附到SiC单晶衬底E10的台阶的吸附系数为0.001。
另外,在热力学计算中使用的各化学物种的数据采用了JANAF热化学表的值。
根据该图12的曲线图,可以理解为,将SiC单晶衬底E10设置在Si/C原子数比超过1的空间(主体容器20内)中并在SiC单晶衬底E10上使生长层E11进行生长得到的结果(○标记)与SiC-Si平衡蒸气压环境中的SiC生长的热力学计算结果倾向一致。此外,可以理解为,将SiC单晶衬底E10设置在Si/C原子数比为1以下的空间(主体容器20内)中并在SiC单晶衬底E10上使生长层E11进行生长得到的结果(×标记)与SiC-C平衡蒸气压环境中的SiC生长的热力学计算结果倾向一致。
可以理解为,在SiC-Si平衡蒸气压环境下,在1960℃的加热温度下实现1.0μm/min以上的生长速度。此外,可以理解为,在2000℃以上的加热温度下实现2.0μm/min以上的生长速度。另一方面,可以理解为,在SiC-C平衡蒸气压环境下,在2000℃的加热温度下实现1.0μm/min以上的生长速度。此外,可以理解为,在2030℃以上的加热温度下实现2.0μm/min以上的生长速度。
根据本发明,可以提供一种在多个原衬底各自中同时实现期望的生长条件的、能够生长高质量的半导体衬底的新技术。
附图标记说明
1X 单位处理体
11 原衬底
12 原料体
13 衬底
20 主体容器
27 距离调整装置
28 原料输送防止体
30 加热炉
40 高熔点容器
50 分离装置
51 引入装置
52 剥离装置
111 生长层
300 损伤层
511 振荡装置
512 会聚装置
1112 隔开距离
S1 设置步骤
S2 加热步骤
S21 Si原子升华步骤
S22 C原子升华步骤
S23 蚀刻步骤
S24 生长步骤
S3 分离步骤
S31 引入步骤
S32 剥离步骤
本文用于企业家、创业者技术爱好者查询,结果仅供参考。