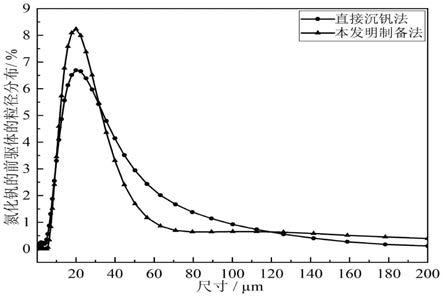
1.本发明属于氮化钒的前驱体技术领域。具体涉及一种氮化钒的前驱体及其制备方法。
背景技术:
2.氮化钒是一种新型的合金添加剂,在钢中通过细化晶粒和强化析出提高钢的韧性、强度、延展性及耐磨性等综合机械性能,并能有效改善钢的焊接性能。与钒铁相比,氮化钒的添加可节约钒的加入量,从而降低成本。氮化钒的前驱体作为制备氮化钒的中间产物,其制备过程引起极大关注,良好的前驱体能有效优化氮化钒的制备过程并提高氮化钒的综合性能。
3.现有制备氮化钒的前驱体大多是用氧化钒作钒源,与碳质还原剂共磨混匀,加入粘结剂造块,存在原料混合不均的问题。改进技术中将钒酸铵溶于去离子水中并加入碳质还原剂,制得前驱体,制备过程复杂;还将碳质还原剂加入含钒溶液中,通过沉钒的方法制得前驱体,该方法存在沉钒时间长、前驱体粒径不均匀和比表面积小等问题。
[0004]“一种简易的氮化钒生产方法”(cn102173395a)专利技术,以v2o5粉和石墨按4∶1的质量比在干混机充分混合,按100∶15的质量比在混合粉中加4%聚乙烯醇水溶液,在湿混机混合,压球制得前驱体;然后将前驱体在800℃预还原5h,升温至1350℃深度还原6h,再升温至1600℃经过6~10h氮化烧结,冷却,得到氮化钒。该工艺前驱体制备经过两次混匀过程,混匀流程复杂,且混合不均匀。
[0005]“前驱体碳化/氮化法制备纳米氮化钒粉末”(中国陶瓷[j].2009,45(11):59-61.doi:10.16521/j.cnki.issn.1001-9642.2009.11.010),将粉状偏钒酸铵和纳米碳黑溶于去离子水中,搅拌制备混合液,将混合液加热、干燥得到前驱体粉末。所得前驱体经过碳化/氮化得到纳米氮化钒粉末。该工艺前驱体制备是将粉状偏钒酸铵和纳米碳黑溶于去离子水,搅拌制备混合液,将混合液再加热、干燥得到,制备过程复杂,制备成本高。
[0006]“a novel method to synthesize vanadium nitride nanopowders by ammonia reduction from combustion precursors”(journal of alloys and compounds.2019,772,808-813.https://doi.org/10.1016/j.jallcom.2018.09.112),以偏钒酸铵为钒源,硝酸铵为氧化剂,甘氨酸为燃料,采用超快scs法制备vo2前驱体,再经过还原氮化反应制备氮化钒。该方法制备vo2前驱体的时候需加入氧化剂和燃料燃烧产生热量,工艺复杂,同时使制备成本增高。
[0007]“一种用含钒溶液制备钒氮合金的方法”(cn107058855a)专利技术,以含钒溶液为钒源,将碳质还原剂加入含钒溶液中沉钒1h,将沉钒产物烘干,得到前驱体;然后经过高温还原氮化,冷却出炉,破碎磨细,压块,制得钒氮合金。该工艺制备前驱体的过程中的沉钒时间较长,制备的颗粒粒径较大且颗粒分布范围广,比表面积较小。
[0008]
综上所述,现有制备氮化钒的前驱体需多次混合后仍存在混合不均匀的问题,通过沉钒的方法制备前驱体时存在沉钒时间长、粒径不均匀和比表面积小的问题。
技术实现要素:
[0009]
本发明旨在克服现有技术缺陷,目的在于提供一种制备时间短和制备工艺简单的氮化钒的前驱体的制备方法,用该方法制备的氮化钒的前驱体中钒与碳混合充分、粒径均匀和比表面积大,所制备的氮化钒的氮含量高。
[0010]
为实现上述目的,本发明采用的技术方案的具体步骤是:
[0011]
步骤一、按含钒溶液中的v∶碳质还原剂中的c的质量比为1∶(0.2~1),在搅拌条件下,向含钒溶液中加入碳质还原剂,得到浆体i。
[0012]
所述含钒溶液为五价钒溶液,v离子浓度≥5.0g/l,其它杂质离子和的浓度≤5.5mol/l;
[0013]
步骤二、按含钒溶液中的v∶沉淀剂中的nh3的摩尔比为1∶(3~9),在搅拌条件下,向所述浆体i中加入所述沉淀剂,得到浆体ii。
[0014]
步骤三、将所述浆体ii的ph值调至1.5~3.0,得到浆体iii;将所述浆体iii置于微波化学反应器中,在微波功率为250~600w、搅拌转速为100~600r/min和温度为80~100℃的条件下搅拌10~50min,固液分离,得到滤渣。
[0015]
步骤四、将所述滤渣在80~150℃条件下烘干0.5~6h,制得氮化钒的前驱体。
[0016]
所述碳质还原剂的c含量≥94wt%。
[0017]
所述沉淀剂为氨水、碳酸氢铵、氯化铵和硫酸铵中的一种以上。
[0018]
由于采用上述技术方案,本发明与现有技术相比具有如下积极效果:
[0019]
(1)本发明在含钒溶液中加入碳质还原剂,快速搅拌,碳质还原剂分散在溶液中形成浆体,浆体中钒与碳混合均匀,再将浆体在微波化学反应器中沉钒,制得组分均匀的氮化钒的前驱体,制备工艺简单,钒与碳混合充分。
[0020]
(2)本发明在微波化学反应器中沉钒,制备前驱体的时间为10~50min,使本发明制备的氮化钒的前驱体的时间为直接沉钒制备前驱体时间的17~83%,制备时间短。
[0021]
(3)本发明在微波化学反应器中进行沉钒,制备的氮化钒的前驱体颗粒细小而均匀,对比直接沉钒法制备的氮化钒的前驱体颗粒,平均粒径减小了13~35%。表面形貌为层状和多孔状混合存在,比表面积增加了36~47%,比表面积大。
[0022]
(4)本发明制备的氮化钒的前驱体经过还原氮化反应,制得的氮化钒的氮含量与直接沉钒法制得的氮化钒的前驱体制备的氮化钒的氮含量相比增加了0.5~1.4wt%,所制备的氮化钒的氮含量高。
[0023]
因此,本发明制备时间短和制备工艺简单;所制备的氮化钒的前驱体具有钒与碳充分混合、颗粒粒径均匀和比表面积大的特点,所制备的氮化钒的氮含量高。
附图说明
[0024]
图1为本发明制备的一种氮化钒的前驱体与直接沉钒法制备的氮化钒的前驱体的粒径分布对比图;
[0025]
图2为图1所示的本发明制备的一种氮化钒的前驱体sem图;
[0026]
图3为图2中a的局部放大图;
[0027]
图4为图1所示的直接沉钒法制备的氮化钒的前驱体sem图;
[0028]
图5为图4中b的局部放大图。
具体实施方式
[0029]
下面结合附图和具体实施方式对本发明做进一步描述,并非对其保护范围的限制。
[0030]
本具体实施方式中:
[0031]
所述碳质还原剂的c含量≥94wt%。
[0032]
实施例中不再赘述。
[0033]
实施例1
[0034]
一种氮化钒的前驱体及其制备方法。本实施例所述方法的具体步骤是:
[0035]
步骤一、按含钒溶液中的v∶碳质还原剂中的c的质量比为1∶(0.2~0.5),在搅拌条件下,向含钒溶液中加入碳质还原剂,得到浆体i。
[0036]
所述含钒溶液为五价钒溶液,v离子浓度≥5.0g/l,其它杂质离子和的浓度≤5.5mol/l。
[0037]
步骤二、按含钒溶液中的v∶沉淀剂中的nh3的摩尔比为1∶(3~5),在搅拌条件下,向所述浆体i中加入所述沉淀剂,得到浆体ii。
[0038]
步骤三、将所述浆体ii的ph值调至1.5~2.0,得到浆体iii;将所述浆体iii置于微波化学反应器中,在微波功率为250~300w、搅拌转速为100~300r/min和温度为80~850℃的条件下搅拌10~20min,固液分离,得到滤渣。
[0039]
步骤四、将所述滤渣在80~100℃条件下烘干4.5~6h,制得氮化钒的前驱体。
[0040]
所述沉淀剂为氨水、碳酸氢铵、氯化铵和硫酸铵中的一种。
[0041]
本实施例制备的氮化钒的前驱体与直接沉钒法制备的氮化钒的前驱体相比:平均粒径减小了24~35%;比表面积增加了40~47%;分别制得的氮化钒的氮含量增加了0.8~1.4wt%。
[0042]
实施例2
[0043]
一种氮化钒的前驱体及其制备方法。本实施例所述方法的具体步骤是:
[0044]
步骤一、按含钒溶液中的v∶碳质还原剂中的c的质量比为1∶(0.5~0.6),在搅拌条件下,向含钒溶液中加入碳质还原剂,得到浆体i。
[0045]
所述含钒溶液为五价钒溶液,v离子浓度≥5.0g/l,其它杂质离子和的浓度≤5.5mol/l。
[0046]
步骤二、按含钒溶液中的v∶沉淀剂中的nh3的摩尔比为1∶(5~6),在搅拌条件下,向所述浆体i中加入所述沉淀剂,得到浆体ii。
[0047]
步骤三、将所述浆体ii的ph值调至1.8~2.3,得到浆体iii;将所述浆体iii置于微波化学反应器中,在微波功率为300~400w、搅拌转速为200~400r/min和温度为85~90℃的条件下搅拌20~30min,固液分离,得到滤渣。
[0048]
步骤四、将所述滤渣在100~120℃条件下烘干3.0~4.5h,制得氮化钒的前驱体。
[0049]
所述沉淀剂为氨水、碳酸氢铵、氯化铵和硫酸铵中的任意两种的混合物。
[0050]
本实施例制备的氮化钒的前驱体与直接沉钒法制备的氮化钒的前驱体相比:平均粒径减小了20~30%;比表面积增加了39~47%;分别制得的氮化钒的氮含量增加了0.7~1.3wt%。
[0051]
实施例3
[0052]
一种氮化钒的前驱体及其制备方法。本实施例所述方法的具体步骤是:
[0053]
步骤一、按含钒溶液中的v∶碳质还原剂中的c的质量比为1∶(0.6~0.8),在搅拌条件下,向含钒溶液中加入碳质还原剂,得到浆体i。
[0054]
所述含钒溶液为五价钒溶液,v离子浓度≥5.0g/l,其它杂质离子和的浓度≤5.5mol/l。
[0055]
步骤二、按含钒溶液中的v∶沉淀剂中的nh3的摩尔比为1∶(6~8),在搅拌条件下,向所述浆体i中加入所述沉淀剂,得到浆体ii。
[0056]
步骤三、将所述浆体ii的ph值调至2.2~2.8,得到浆体iii;将所述浆体iii置于微波化学反应器中,在微波功率为400~500w、搅拌转速为3000~500r/min和温度为90~95℃的条件下搅拌30~40min,固液分离,得到滤渣。
[0057]
步骤四、将所述滤渣在120~140℃条件下烘干1.5~3.0h,制得氮化钒的前驱体。
[0058]
所述沉淀剂为氨水、碳酸氢铵、氯化铵和硫酸铵中任意三种的混合物。
[0059]
本实施例制备的氮化钒的前驱体与直接沉钒法制备的氮化钒的前驱体相比:平均粒径减小了17~25%;比表面积增加了37~44%;分别制得的氮化钒的氮含量增加了0.7~1.2wt%。
[0060]
实施例4
[0061]
一种氮化钒的前驱体及其制备方法。本实施例所述方法的具体步骤是:
[0062]
步骤一、按含钒溶液中的v∶碳质还原剂中的c的质量比为1∶(0.8~1),在搅拌条件下,向含钒溶液中加入碳质还原剂,得到浆体i。
[0063]
所述含钒溶液为五价钒溶液,v离子浓度≥5.0g/l,其它杂质离子和的浓度≤5.5mol/l。
[0064]
步骤二、按含钒溶液中的v∶沉淀剂中的nh3的摩尔比为1∶(8~9),在搅拌条件下,向所述浆体i中加入所述沉淀剂,得到浆体ii。
[0065]
步骤三、将所述浆体ii的ph值调至2.5~3.0,得到浆体iii;将所述浆体iii置于微波化学反应器中,在微波功率为500~600w、搅拌转速为400~600r/min和温度为95~100℃的条件下搅拌40~50min,固液分离,得到滤渣。
[0066]
步骤四、将所述滤渣在140~150℃条件下烘干0.5~1.5h,制得氮化钒的前驱体。
[0067]
所述沉淀剂为氨水、碳酸氢铵、氯化铵和硫酸铵的混合物。
[0068]
本实施例制备的氮化钒的前驱体与直接沉钒法制备的氮化钒的前驱体相比:平均粒径减小了13~21%;比表面积增加了36~41%;分别制得的氮化钒的氮含量增加了0.5~1.0wt%。
[0069]
本具体实施方式与现有技术相比具有如下积极效果:
[0070]
(1)本具体实施方式在含钒溶液中加入碳质还原剂,快速搅拌,碳质还原剂分散在溶液中形成浆体,浆体中钒与碳混合均匀,再将浆体在微波化学反应器中沉钒,制得组分均匀的氮化钒的前驱体,制备工艺简单,钒与碳混合充分。
[0071]
(2)本具体实施方式在微波化学反应器中沉钒,制备前驱体的时间为10~50min,使本具体实施方式制备的氮化钒的前驱体的时间为直接沉钒制备前驱体时间的17~83%,制备时间短。
[0072]
(3)本具体实施方式制备的氮化钒的前驱体的粒径分布如附图所示,图1为实施例
1制备的一种氮化钒的前驱体与直接沉钒法制备的氮化钒的前驱体的粒径分布对比图;图2为图1所示的实施例1制备的一种氮化钒的前驱体sem图;图3为图2中a的局部放大图;图4为图1所示的直接沉钒法制备的氮化钒的前驱体sem图;图5为图4中b的局部放大图。分析图1可知,平均粒径减小了14.86%;对比图4,从图2可以看出,实施例1制备的氮化钒的前驱体颗粒粒径明显减小且更加均匀,前驱体颗粒没有明显的团聚现象;对比图5,从图3可以看出实施例1制备的氮化钒的前驱体结构中出现了多孔状结构,比表面积增加了37.58%;,该前驱体经过还原氮化过程制备的氮化钒的氮含量增加了0.55%。
[0073]
本具体实施方式在微波化学反应器中进行沉钒,制备的氮化钒的前驱体颗粒细小而均匀,对比直接沉钒法制备的氮化钒的前驱体颗粒,平均粒径减小了13~35%。表面形貌为层状和多孔状混合存在,比表面积增加了36~47%,比表面积大。
[0074]
(4)本具体实施方式制备的氮化钒的前驱体经过还原氮化反应,制得的氮化钒的氮含量与直接沉钒法制得的前驱体制备的氮化钒的氮含量相比增加了0.5~1.4wt%,使用效果好。
[0075]
因此,本具体实施方式制备时间短和制备工艺简单;所制备的氮化钒的前驱体具有钒与碳充分混合、颗粒粒径均匀和比表面积大的特点,所制备的氮化钒的氮含量高。
再多了解一些
本文用于企业家、创业者技术爱好者查询,结果仅供参考。