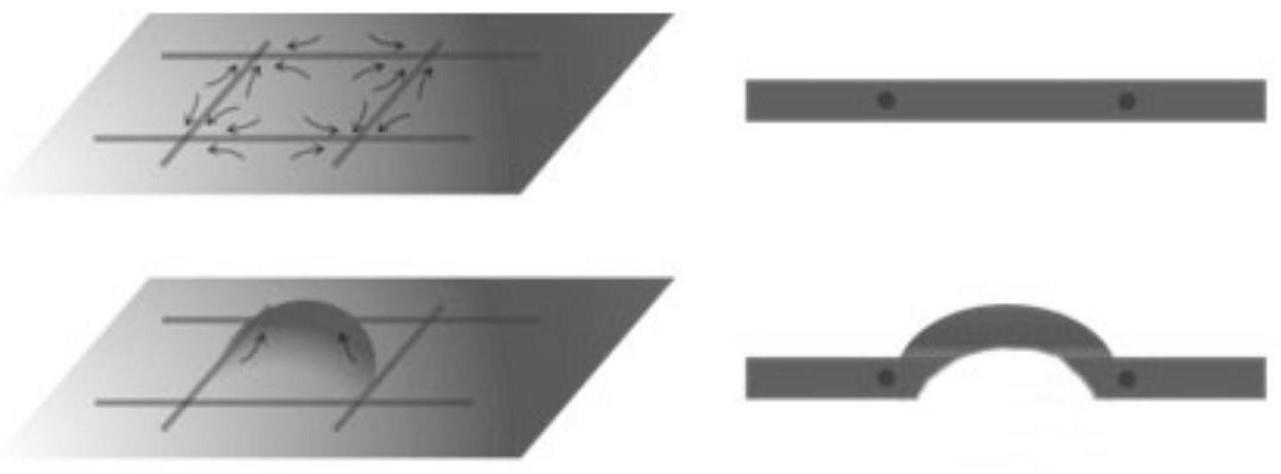
1.本发明涉及一种氯碱离子膜内部增强纤维松弛度测试方法,该方法通过简单的器具和操作,实现了对氯碱离子膜内部增强纤维松弛程度的数据化分析,填补了纤维复合进膜材料内部后,其实际松弛程度测定的技术空白,为进一步分析膜内部结构和溶胀状态、预测膜水解后表观情况提供了有力支持,属于氯碱离子交换膜技术领域。
技术背景
2.氯碱离子膜在生产加工过程中,氯碱膜前驱体会因为发生水解反应而出现尺寸溶胀现象,而膜内部存在纵横交织的增强纤维,膜的溶胀实际会分为两步:第一步,膜基体溶胀,将有一定松弛度的增强纤维拉直;第二步,增强纤维拉直后,膜继续溶胀。由于增强纤维松弛度有限,且纤维本身尺寸较稳定,不易发生溶胀,膜基体在发生第二步溶胀时势必会受到周围增强纤维的束缚作用,转而在没有增强纤维的部分沿z方向(垂直于膜基体方向)溶胀凸起,形成“麻点”(如图1所示)。可能会造成膜面与电极网接触摩擦,产生机械损伤,也会影响外观。
3.由上可知,膜内部增强纤维的松弛程度是膜表观是否出现麻点,以及麻点是否严重的重要影响因素。当膜内部增强纤维松弛度比较高时,膜一般更不容易起麻点,或者麻点更浅,当膜内部增强纤维松弛度比较低,纤维比较紧绷时,膜则更容易起麻点,麻点也更深。
4.然而目前现有的方法仅是利用生产过程中设备的运行张力间接估计膜内部增强纤维的松紧程度,并不能直观、准确地体现纤维的真实状态。不能准确在膜水解前测定膜内增强纤维的松弛度,就无法预测在现有生产参数下膜在水解后是否会产生麻点,无法在水解前对生产设备张力等参数进行调整,加大后期麻点产生的几率。因此,为了降低麻点的产生几率,研究膜内部增强纤维的松弛程度具有非常重要的意义。
技术实现要素:
5.本发明的目的是提供一种氯碱离子膜内部增强纤维松弛度测试方法,其能够实现对增强纤维在膜材料内部实际松弛情况的检测、分析及膜水解后表观情况(主要是麻点)的预测,解决了纤维复合入膜内部后其松弛度无法直接测定的难题。利用本发明方法测定出纤维松弛度后,可及时调整设备张力等参数,实现降低麻点产生几率的目的,为氯碱离子膜的后续生产提供指导。
6.为了实现上述目的,本发明采用以下技术方案:
7.一种氯碱离子膜内部增强纤维松弛度的测试方法,其特征在于,包括以下步骤:
8.(1)测定不包含增强纤维的氯碱离子膜前驱体的水解溶胀率,溶胀率(td或md)=100%
×
(膜水解后尺寸-膜水解前尺寸)/膜水解前尺寸;
9.(2)计算含增强纤维的氯碱离子膜前驱体待测样品的极限位移,并通过拉伸曲线得出极限位移处的拉伸力,
10.极限位移=拉伸样品有效长度
×
溶胀率;
11.(3)计算含增强纤维的氯碱离子膜前驱体待测样品中纤维松弛度,
12.纤维松弛度=(1/极限位移处拉伸力)
×
100%。
13.本发明中所述氯碱离子膜前驱体指未水解的全氟磺酸树脂薄膜、全氟羧酸树脂薄膜或者全氟磺酸树脂和全氟羧酸树脂的复合薄膜。所述前驱体包括含有增强纤维或者不包含增强纤维的氟树脂薄膜。本发明的上述测试方法适用于在氯碱离子膜制备过程中,尤其是添加增强纤维后,全氟磺酸树脂层内的增强纤维的松弛度的测试。氯碱离子膜制备过程为本领域常规手段,为了更好地理解本发明方法,可参照中国专利文献cn102978654a(cn201210545793.6)中氯碱离子膜的制备过程。
14.氯碱离子膜前驱体的水解工艺为常规手段,可参照中国专利文献cn102978654a(cn201210545793.6)中增强离子膜的水解工艺。
15.拉伸样品有效长度即拉伸时实际被拉长的部分,例如标准哑铃型样品,其两头被固定夹住,在拉伸过程中不会受力拉长,所以不算有效长度。
16.步骤(2)中,拉伸曲线的横坐标为拉伸力(n),纵坐标为拉伸位移(mm)。
17.步骤(2)中,所述极限位移,是指当氯碱离子膜前驱体在水解过程中溶胀到最大程度时,其尺寸对应的膜样品拉伸位移。认为在理想状态下,增强纤维在极限位移处的拉伸力最能反映其在膜内部的松弛程度。
18.优选的,步骤(1)中所述td向溶胀率为膜垂直于机器生产方向的溶胀率,md向溶胀率为平行于机器生产方向的溶胀率。
19.优选的,步骤(2)中含增强纤维的氯碱离子膜前驱体待测样品的尺寸为长100~300mm,宽10~50mm的长条形,或者哑铃型标准式样。优选的,所述哑铃型标准式样为按照gb/t 1040.2-2006《塑料拉伸性能的测定》中哑铃型标准式样裁切。进一步优选的,步骤(2)中所述长条形或哑铃型标准式样为1条或多条,优选2~20条。
20.优选的,步骤(2)中所述含增强纤维的氯碱离子膜前驱体的待测样品的取样方法为:在氯碱离子膜前驱体膜卷md方向,选取长度为100~1000mm,在氯碱离子膜前驱体膜卷td方向,选取完整一横幅或某一宽度,然后进行进一步裁切,得到待测样品。优选的,长度为150~500mm,更优选的,长度为250~300mm;优选的,宽度为100~2000mm,更优选的,宽度为200~500mm。
21.进一步优选的,步骤(2)中所述含增强纤维的氯碱离子膜前驱体的样品在进行进一步裁切处理前进行前处理。前处理进一步可确保所有待测样品处于同一种初始状态。前处理使样品达到平衡状态,即样品吸水或吸收平衡液达到饱和状态,比如可根据样品尺寸及质量不再随时间变化来确定。
22.前处理的方法为:将含增强纤维的氯碱离子膜前驱体(下简称“膜”)样品浸泡在室温纯水或平衡溶液中平衡处理,平衡后取出擦干,或用室温鼓风吹干。更进一步优选的,所述平衡溶液是一种中性溶液,包括质量浓度为0.1~50.0%的醇、醛、酮、氯化盐或硫酸盐的水溶液中的一种或几种。更进一步优选的,所述氯化盐为licl、nacl或kcl中的一种;所述硫酸盐包括li2so4、na2so4或k2so4中的一种。
23.优选的,步骤(2)的拉伸曲线是利用万能试验机对膜样品进行拉伸曲线的测定。
24.完成样品在极限位移处拉伸力与纤维松弛度的数据转换,并作图分析不同样品的拉伸曲线斜率情况。斜率代表膜在拉伸过程中单位位移受力大小,膜内纤维松弛度越小,斜
率越大。
25.本发明还提供一种防止氯碱离子膜产生麻点的方法,其特征在于,控制膜中纤维的松弛度》7%。
26.在实际生产薄膜的过程中,可通过调小设备运行张力来提高纤维松弛度。
27.本发明的原理为,氯碱离子膜生产加工过程中,前驱体膜中复合的td、md方向增强纤维的松弛度越低,张紧程度越紧,膜在水解过程中第一步溶胀的程度越小,第二步在z方向上自体溶胀的程度越大,越容易产生麻点,即,理想状态下,膜在水解过程中表观是否会产生麻点的关键,在于膜基体(全氟离子交换树脂基膜)溶胀至极限时受到的增强纤维的束缚力是否过大。在膜样品拉伸过程中,可以以膜拉伸到与基体溶胀率相对应的极限位移时拉伸力大小来间接反映膜内部增强纤维的松紧度。松弛度较低、即张紧程度较紧的增强纤维反映在拉伸曲线图中,则体现为曲线斜率越大,极限位移处拉伸力越大。
28.本发明的有益效果:
29.与传统的仅利用生产过程中设备的运行张力来大体估计膜中增强纤维的松弛程度的方式相比,本发明的优点在于:(1)能够更加明确地数据化膜中纤维的松弛度;(2)得到的相对数据与膜中增强纤维的相对松弛程度更加贴近;(3)本发明方法所使用的器具简单,成本低廉,操作简易,涉及人员少,仅需一人操作即可完成测试。(4)本发明方法解决了纤维复合入膜内部后其松弛度无法直接测定的难题。利用本发明方法测定出纤维松弛度后,可及时调整设备张力等参数,实现降低麻点产生几率的目的,为氯碱离子膜的后续生产提供指导,本发明方法的准确率可达80%以上。
附图说明
30.图1是氯碱离子膜溶胀并产生麻点的过程示意图(图内直线为膜内部增强纤维示意图,箭头为溶胀方向);
31.图2是实施例1的氯碱离子膜a的td向和md向拉伸曲线;
32.图3是实施例2的氯碱离子膜b的td向和md向拉伸曲线;
33.图4是实施例1的氯碱离子膜a水解后表观图片;
34.图5是实施例2的氯碱离子膜b水解后表观图片;
35.图6是实施例3的氯碱离子膜c的td向和md向拉伸曲线。
具体实施方式
36.通过下面的实施例可以对本发明进行进一步地描述,然而,本发明的范围并不限于下述实施例。本领域的专业人员能够理解,在不背离本发明的精神和范围的前提下,可以对本发明进行各种变化和修饰。
37.本发明实施例所用的全氟离子交换膜均来自山东东岳氟硅科技集团生产的氯碱离子交换膜df2807及其相关产品。但是本发明提供的处理方法的适用对象不限于该膜。
38.实施例1
39.一种氯碱离子膜内部增强纤维松弛度的测试方法,包括以下步骤:
40.(1)测定型号为df2807的某一批次氯碱离子膜a在制备过程中,其未添加增强纤维的前驱体(全氟离子交换树脂基膜),在水解过程中的基体溶胀率,取样10
×
10cm无纤维膜
水解前驱体,溶胀率为td:11.03%,md:9.87%。
41.(2)在该批次含增强纤维的氯碱离子膜a前驱体(增强离子膜)的膜卷上取长度150mm,中间区域宽度为200mm的膜样品,浸泡在纯水中16h,干燥后,用gb/t1040.2-2006《塑料拉伸性能的测定》中哑铃型标准式样模具分别沿td、md向对样品进行裁切,每个方向裁切5条样品条。
42.通过公式:极限位移=拉伸样品有效长度(115mm)
×
溶胀率,计算得到对应的标准哑铃型拉伸样品极限位移为td:5.5mm,md:4.9mm。
43.再将裁切后的样品条固定在万能试验机上进行拉伸测试,测试软件为material test v4.3,测试条件为:夹具间距离115mm;压力传感器200n,拉伸速率25mm/min。拉伸至样品条断裂,得到拉伸曲线如图2所示:
44.从拉伸曲线中得到膜样品在td方向极限位移处(5.5mm)的拉伸力为12.78
±
0.49n,md方向极限位移处(4.9mm)的拉伸力为9.34
±
0.35n。
45.(3)根据公式纤维松弛度=(1/极限位移处拉伸力)
×
100%,计算得到该膜样品td方向纤维松弛度为7.82%,md方向纤维松弛度为10.71%。由此可知,在该膜样品中,md方向增强纤维比td方向更松弛。
46.实施例2
47.一种氯碱离子膜内部增强纤维松弛度的测试方法,包括以下步骤:
48.(1)测定型号为df2807的某一批次氯碱离子膜b在制备过程中,其未添加增强纤维的前驱体(全氟离子交换树脂基膜),在水解过程中的基体溶胀率,取样10
×
10cm无纤维膜水解前驱体,溶胀率为td:10.82%,md:8.56%。
49.(2)在该批次含增强纤维的氯碱离子膜b前驱体(增强离子膜)的膜卷上取长度300mm,中间区域宽度为400mm的膜样品,浸泡在纯水中16h,干燥后,用gb/t1040.2-2006《塑料拉伸性能的测定》中哑铃型标准式样模具分别沿td、md向对样品进行裁切,每个方向裁切5条样品条。
50.通过公式:极限位移=拉伸样品有效长度(115mm)
×
溶胀率,计算得到对应的标准哑铃型拉伸样品极限位移为td:5.4mm,md:4.7mm。
51.将裁切后的样品条固定在万能试验机上进行拉伸测试,测试软件为material test v4.3,测试条件为:夹具间距离115mm;压力传感器200n,拉伸速率25mm/min。拉伸至样品条断裂,得到拉伸曲线如图3所示:
52.从拉伸曲线中得到膜样品在td方向极限位移处(5.4mm)的拉伸力为21.22
±
0.96n,md方向极限位移处(4.7mm)的拉伸力为26.47
±
1.43n。
53.(3)计算得到该膜样品td方向纤维松弛度为4.71%,md方向纤维松弛度为3.78%。由此可知,在该膜样品中,td方向增强纤维比md方向更松弛。
54.由于样品处理方法相同,比较实施例1和实施例2,还可以得知,氯碱离子膜a内部增强纤维的松弛度较氯碱离子膜b大,即a膜内部纤维更松弛。对应生产实际情况,膜b在水解过后表观出现麻点(图5),而a膜表观无麻点(图4)。
55.实施例3
56.一种氯碱离子膜内部增强纤维松弛度的测试方法,包括以下步骤:
57.(1)测定型号为df2807的某一批次氯碱离子膜c在制备过程中,其未添加增强纤维
的前驱体(全氟离子交换树脂基膜),在水解过程中的基体溶胀率,取样10
×
10cm无纤维膜水解前驱体,溶胀率为td:12.52%,md:10.98%。
58.(2)在该批次含增强纤维的氯碱离子膜c前驱体(增强离子膜)的膜卷上取长度250mm,中间区域宽度为300mm的膜样品,浸泡在纯水中16h,干燥后,
59.按照长250mm,宽10mm尺寸分别沿td、md向将样品裁切成长条装,每个方向裁切5条样品条。
60.通过公式:极限位移=拉伸样品有效长度(200mm)
×
溶胀率,计算得到对应的标准哑铃型拉伸样品极限位移为:td:6.3mm,md:4.7mm。
61.将裁切后的样品条固定在万能试验机上进行拉伸测试,测试软件为material test v4.3,测试条件为:夹具间距离200mm;压力传感器200n,拉伸速率25mm/min。拉伸至样品条断裂,得到拉伸曲线如图6所示:
62.从拉伸曲线中得到膜样品在td方向极限位移处(6.3mm)的拉伸力为22.82
±
0.81n,md方向极限位移处(4.7mm)的拉伸力为26.75
±
1.03n。
63.(3)计算得到该膜样品td方向纤维松弛度为4.38%,md方向纤维松弛度为3.74%。由此可知,在该膜样品中,td方向增强纤维比md方向更松弛。对应生产实际情况,膜c在水解过后表观出现麻点。
64.实施例1~3所述氯碱离子膜a、b、c的纤维松弛度具有一定差异的原因是,生产过程中设备张力的不稳定造成的。而通过本发明方法可以准确测试纤维松弛度,对后续批次生产过程的张力等参数进行调整,从而解决松弛度不稳定、易产生麻点的问题,经过多次验证,松弛度越大越不容易产生麻点。
再多了解一些
本文用于企业家、创业者技术爱好者查询,结果仅供参考。