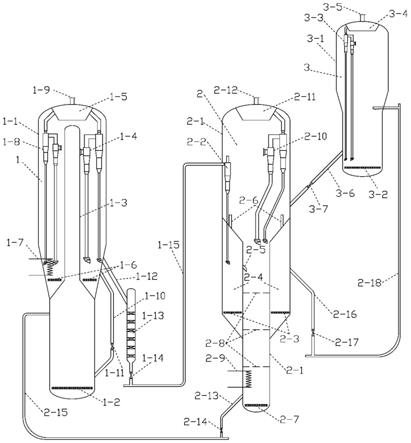
1.本技术涉及一种再生装置、制备低碳烯烃的装置及其应用,属于化工催化领域。
背景技术:
2.甲醇制烯烃技术(mto)主要有中国科学院大连化学物理研究所的dmto技术和美国uop公司的mto技术。2010年,采用dmto技术的神华包头甲醇制烯烃工厂建成投产,此为mto技术的全球首次工业化应用,截至2019年底,已有14套dmto工业装置投产,低碳烯烃产能共计约800万吨/年。
3.最近几年,dmto技术进一步发展,性能更加优良的新一代dmto催化剂逐渐开始工业化应用,为dmto工厂创造了更高的效益。新一代dmto催化剂具有更高的甲醇处理能力和低碳烯烃选择性。
4.甲醇制烯烃技术一般采用sapo-34分子筛催化剂,甲醇制烯烃过程低碳烯烃的高选择性是通过分子筛的酸性催化作用结合分子筛骨架结构中的孔口的限制作用共同实现的。甲醇转化过程同时伴随着酸性分子筛催化剂的结焦过程。现有的甲醇制烯烃工厂的甲醇结焦率为1.5-2.5wt%,即,甲醇中的3.3-5.5%的c原子转化为催化剂中的焦,焦在再生器中燃烧生成co、co2和h2o等物质后排放,c原子利用率仅为94.5-96.7%。随着技术的进步,甲醇制烯烃过程的低碳烯烃选择性大幅度提高,甲醇结焦率高、c原子利用率低已经成为抑制技术进步的瓶颈,因此,需要开发新的甲醇制烯烃技术,提高c原子利用率,提高技术的原子经济性。
技术实现要素:
5.甲醇制烯烃过程同时伴随着酸性分子筛催化剂的结焦过程,在分子筛笼内形成焦物种,引发甲醇制烯烃的催化过程。催化剂结焦覆盖了分子筛的活性位,降低了催化剂的活性,但分子筛中的焦进一步限制了分子筛骨架结构中的孔口,提高了低碳烯烃的选择性。
6.本技术中所述的低碳烯烃是指乙烯和丙烯。申请人研究发现,影响dmto催化剂的活性和低碳烯烃选择性的主要因素是催化剂中的焦含量、焦含量分布和焦物种。催化剂的平均焦含量相同时,焦含量分布窄,则低碳烯烃选择性高、活性高。催化剂中的焦物种包含多甲基芳烃和多甲基环烷烃等,其中,多甲基苯和多甲基萘能促进乙烯的生成。因此,控制催化剂中的焦含量、焦含量分布以及焦物种是控制dmto催化剂的操作窗口、提高低碳烯烃选择性的关键。
7.甲醇制烯烃待生催化剂中的焦含量一般为7-13wt%,当焦含量高时,催化剂的活性大幅度下降。当前甲醇制烯烃工厂一般采用空气再生的方法恢复催化剂的活性,从而循环利用催化剂,在这个过程中,焦在再生器中燃烧生成co、co2和h2o等物质后排放。实际上,待生催化剂中的焦可以分为两类,一类是分子量较大、石墨化程度高、没有催化活性的焦,可称之为非活性焦,一类是分子量较小、具有催化活性的多甲基芳烃和多甲基环烷烃,可称之为活性焦。采用空气作为再生介质时,由于空气具有强氧化性,非活性焦、活性焦和氧气
发生深度氧化反应,主要生成co、co2和h2o等物质,很难实现焦的可控转化,难以控制催化剂中的焦含量、焦含量分布以及焦物种,因此,以空气为再生介质,催化剂中的焦含量《3wt%时,即,大部分的焦被氧化消除,催化剂才能恢复足够的催化活性。采用此种再生方案获得的再生催化剂的低碳烯烃选择性低、甲醇结焦率高、甲醇单耗高。采用水作为再生介质时,活性焦和水发生反应,大分子物种向小分子物种转化,在合适的条件下,活性焦可以转化为以多甲基苯和多甲基萘为主的物种。采用水和氧气共同作为再生介质时,非活性焦和活性焦在氧气和水的作用下,转化为分子量较小的含氧烃类物种和不含氧烃类物种,其中含氧烃类物种没有催化活性。含氧烃类物种在水蒸气、氢气、甲烷、乙烷、丙烷等物质的作用下可转化为具有催化活性的不含氧烃类物种。
8.因此,本技术提供了一种待生催化剂转化为再生催化剂的可控活化方法,并且所获得的再生催化剂具有高活性、高低碳烯烃选择性等特性,能够降低甲醇单耗、降低甲醇结焦率,提高甲醇制烯烃技术的原子经济性。
9.根据本技术的一个方面,提供了一种用于活化含氧化合物制备低碳烯烃的催化剂的再生装置。
10.一种用于活化含氧化合物制备低碳烯烃的催化剂的再生装置,所述再生装置包括第一再生器和第二再生器;
11.所述第一再生器由下至上包括第二活化区、第一活化区和气固分离区;
12.所述第二活化区和气固分离区轴向连通;
13.所述第一活化区设置在所述第二活化区与气固分离区连接处的外周,且所述第一活化区与所述第二活化区连通;
14.所述第一活化区为环形腔体;
15.所述第一活化区中沿径向设有n个挡板,所述n个挡板将所述第一活化区分割为n个第一活化区子区;
16.其中,n-1个所述挡板上开设有催化剂流通孔,以使进入所述第一活化区的催化剂沿着环形方向流动;
17.所述第一再生器的第一活化区与所述第二再生器管路连接,用于将所述第一活化区中的催化剂通入所述第二再生器中;
18.所述第二再生器与所述第一再生器的气固分离区管路连接,用于将第二再生器中的催化剂通入所述气固分离区中。
19.可选地,所述再生装置包括第二再生斜管、第二再生剂输送管、第三再生斜管;
20.第一再生器的第一活化区、第二再生斜管、第二再生剂输送管、第二再生器的中部依次连通;
21.第二再生器的底部、第三再生斜管、第一再生器的气固分离区依次连通。
22.可选地,所述第二再生斜管、第二再生剂输送管通过第二再生滑阀连通。
23.可选地,所述第三再生斜管设置有第三再生滑阀。
24.具体地,第二再生斜管的入口连接于第一活化区,第二再生滑阀的入口连接于第二再生斜管的出口,第二再生滑阀的出口经管道连接于第二再生剂输送管的入口,第二再生剂输送管的出口连接于第二再生器的中部。
25.具体地,第三再生斜管的入口连接于第二再生器的下部,第三再生斜管中设置第
三再生滑阀,第三再生斜管的出口连接于第一再生器的气固分离区。
26.可选地,在所述第一活化区中,所述n个挡板包括第1挡板、第2挡板至第n挡板;
27.所述第1挡板上未开设有所述催化剂流通孔;
28.所述第2至第n挡板上开设有所述催化剂流通孔;
29.所述第1挡板与所述第2挡板分割而成的第1活化区子区设有待生催化剂进口;
30.所述第1挡板与所述第n挡板分割而成的第n活化区子区设有第一活化区催化剂输送管,所述第一活化区催化剂输送管将所述第一活化区和所述第二活化区连通;
31.所述第一活化区子区的下方设有第一活化区分布器;
32.所述第一活化区子区的顶部设有第一活化区气体输送管。
33.具体地,挡板上开设的催化剂流通孔可以为1个,或者也可以为多个,本技术不做严格限定。当设置多个催化剂流通孔时,催化剂流通孔彼此的相对位置本技术也不做严格限定,例如,多个催化剂流通孔可以平行设置,或者也可以无规则设置。
34.优选地,在每一个第一活化区子区的下方均设有第一活化区分布器。这样可以实现第一活化区原料的整体均匀进入第一活化区子区。
35.优选地,每一个第一活化区子区的顶部均设有第一活化区气体输送管。
36.具体地,所述第一活化区原料通过第一活化区分布器和待生催化剂接触反应。
37.可选地,所述第一活化区上部设置有第一再生器第一气固分离设备;
38.所述第一再生器第一气固分离设备通过所述待生催化剂进口与所述第一活化区连通。
39.具体地,所述待生催化剂经过第一再生器第一气固分离设备进入第一活化区。
40.具体地,所述第一活化区设置第一活化区催化剂输送管,所述的第一活化区催化剂输送管的入口连接于第n第一活化区子区,第一活化区催化剂输送管的出口位于第二活化区。
41.可选地,第一再生器第一气固分离设备采用气固旋风分离器。
42.可选地,所述n的取值范围为:2≤n≤10。
43.可选地,所述第一活化区子区的横截面是扇环形。
44.可选地,所述第二活化区中沿水平方向设置有m块多孔板;
45.其中,1≤m≤10。
46.可选地,所述多孔板的开孔率为5-50%。
47.本技术中,第二活化区采用多孔板抑制催化剂在床层内的反混,提高催化剂中的焦分布的均匀性。
48.可选地,所述第二活化区的底部设置有第二活化区分布器。
49.可选地,所述第一再生器包括第一再生器集气室、第一再生器取热器;
50.所述第一再生器集气室位于所述第一再生器的顶部;
51.所述第一再生器集气室的顶部设置有第一再生器产品气输送管;
52.所述气固分离区设置第一再生器第二气固分离设备;
53.所述第一再生器集气室连接于第一再生器第二气固分离设备的气体出口;
54.所述第一再生器取热器位于所述第二活化区的下部。
55.具体地,第二活化区和气固分离区的连接处的内径由小至大。
56.具体地,第一再生器的下壳体和上壳体的连接处的内径由小至大。
57.可选地,所述第一再生器第一气固分离设备采用气固旋风分离器或气固快速分离器。
58.可选地,所述第一再生器第二气固分离设备采用一组或多组气固旋风分离器。
59.优选地,每组气固旋风分离器包含一个第一级气固旋风分离器和一个第二级气固旋风分离器。
60.可选地,所述第二再生器包括第二再生器壳体、第二再生器分布器、第二再生器气固分离设备、第二再生器集气室;
61.所述第二再生器分布器位于第二再生器的底部;
62.所述第二再生器气固分离设备位于第二再生器的上部;
63.所述第二再生器集气室位于第二再生器的顶部;
64.所述第二再生器气固分离设备的气体出口连接于第二再生器集气室;所述第二再生器气固分离设备的催化剂出口位于第二再生器的下部。
65.可选地,所述第二再生器集气室的顶部设置有烟气输送管。
66.作为一个优选的实施方式,所述再生装置包含第一再生器和第二再生器;
67.所述第一再生器由下至上分为第二活化区、第一活化区和气固分离区;
68.所述第一再生器包含:第一再生器壳体,第一再生器第一气固分离设备,第一活化区分布器,挡板,第一活化区催化剂输送管,第一活化区气体输送管,第二活化区分布器,多孔板,第一再生器取热器,第一再生器第二气固分离设备,第一再生器集气室,第一再生器产品气输送管,第一再生斜管,第一再生滑阀,第一再生剂输送管,第二再生斜管,第二再生滑阀和第二再生剂输送管;
69.第一活化区位于第二活化区上方的环形区域,第一活化区内设置n个挡板,挡板将第一活化区分割为n个第一活化区子区,2≤n≤10,每个第一活化区子区的底部都独立设置第一活化区分布器,第一活化区的横截面是环形,第一活化区子区的横截面是扇环形,第1-n第一活化区子区同心依序排列,挡板中含有催化剂流通孔,但第1第一活化区子区和第n第一活化区子区间的挡板不含催化剂流通孔;第一再生器第一气固分离设备位于第一再生器的气固分离区,第一再生器第一气固分离设备的入口连接于待生剂输送管的出口,第一再生器第一气固分离设备的气体出口位于气固分离区,第一再生器第一气固分离设备的催化剂出口位于第1第一活化区子区;第一活化区催化剂输送管的入口连接于第n第一活化区子区,第一活化区催化剂输送管的出口位于第二活化区;每个第一活化区子区的顶部都独立设置第一活化区气体输送管,第一活化区气体输送管的出口位于气固分离区;第二活化区分布器位于第一再生器的第二活化区的底部,第二活化区中设置m块多孔板,1≤m≤10,第一再生器取热器位于第二活化区;第一再生器第二气固分离设备和第一再生器集气室位于第一再生器的气固分离区,第一再生器第二气固分离设备的入口位于第一再生器的气固分离区,第一再生器第二气固分离设备的气体出口连接于第一再生器集气室,第一再生器第二气固分离设备的催化剂出口位于第二活化区,第一再生器产品气输送管连接于第一再生器集气室的顶部;第一再生斜管的入口连接于第二活化区的下部,第一再生滑阀的入口连接于第一再生斜管的出口,第一再生滑阀的出口经管道连接于第一再生剂输送管的入口,第一再生剂输送管的出口连接于流化床反应器的反应区;第二再生斜管的入口连接于第一
活化区,第二再生滑阀的入口连接于第二再生斜管的出口,第二再生滑阀的出口经管道连接于第二再生剂输送管的入口,第二再生剂输送管的出口连接于第二再生器的中部;
70.所述第二再生器包含:第二再生器壳体,第二再生器分布器,第二再生器气固分离设备,第二再生器集气室,烟气输送管,第三再生斜管和第三再生滑阀;
71.第二再生器分布器位于第二再生器的底部,第二再生器气固分离设备位于第二再生器的上部,第二再生器气固分离设备的入口位于第二再生器的上部,第二再生器气固分离设备的气体出口连接于第二再生器集气室,第二再生器气固分离设备的催化剂出口位于第二再生器的下部,第二再生器集气室位于第二再生器的顶部,烟气输送管连接于第二再生器集气室的顶部,第三再生斜管的入口连接于第二再生器的下部,第三再生斜管中设置第三再生滑阀,第三再生斜管的出口连接于第一再生器的气固分离区。
72.可选地,第二再生器气固分离设备采用一组或多组气固旋风分离器。
73.优选地,每组气固旋风分离器包含一个第一级气固旋风分离器和一个第二级气固旋风分离器。
74.根据本技术的第二个方面,提供了一种用于含氧化合物制备低碳烯烃的装置。该装置为包含流化床反应器和再生装置的含氧化合物制低碳烯烃(dmto)装置。
75.一种用于含氧化合物制备低碳烯烃的装置,包括流化床反应器和上述所述的再生装置。
76.可选地,所述装置包括待生斜管、流化床反应器汽提器、待生剂输送管、第一再生斜管和第一再生剂输送管;
77.待生剂区、待生斜管、流化床反应器汽提器、待生剂输送管、第一再生器第一气固分离设备依次连通;
78.第二活化区、第一再生斜管、第一再生剂输送管、流化床反应器的反应区依次连通。
79.具体地,待生斜管、流化床反应器汽提器、待生剂输送管依次相连;
80.第一再生斜管和第一再生剂输送管依次相连;
81.第一再生斜管的入口连接于第二活化区的下部;
82.在流化床反应器反应后的待生催化剂进入待生斜管,经待生剂输送管进入第一再生器;
83.经第一再生器再生后的再生催化剂进入第一再生斜管,经第一再生剂输送管进入流化床反应器。
84.可选地,所述流化床反应器汽提器、待生剂输送管通过待生滑阀相连。
85.可选地,所述第一再生斜管、第一再生剂输送管通过再生滑阀相连。
86.可选地,所述流化床反应器包括下壳体、输送管和上壳体;
87.所述下壳体围合成反应区;
88.所述输送管位于所述反应区的上方且与所述反应区连通;
89.所述输送管的外周设有上壳体;
90.所述上壳体与所述输送管围合形成空腔;
91.所述空腔自下至上分为待生剂区和气固分离区。
92.具体地,流化床反应器的反应区和输送管的连接处的内径由大至小。
93.具体地,流化床反应器的下壳体和上壳体的连接处的内径由小至大。
94.可选地,所述反应区属于快速流态化区。
95.可选地,所述待生剂区属于鼓泡流态化区。
96.本技术中,对反应区的流态化类型不作严格限定,优选反应区属于快速流态化区。反应区的气体表观线速度可以达到7.0m/s,具有较高的甲醇通量,设备单位体积的甲醇处理量大,甲醇质量空速可以达到20h-1
。本技术中,对待生剂区的流态化类型不作严格限定,优选待生剂区属于鼓泡流态化区。待生剂区用于取热、降低待生催化剂的温度,并向反应区输送低温的待生催化剂,提高反应区的床层密度、控制反应区的床层温度,当气体表观线速度为0.5-7.0m/s时,相对应的床层密度为500-100kg/m3。
97.可选地,所述气固分离区设置有流化床反应器第一气固分离设备;
98.所述输送管的上部连接于流化床反应器第一气固分离设备的入口。
99.可选地,所述流化床反应器包括流化床反应器分布器,流化床反应器取热器,待生剂区气体分布器,流化床反应器集气室,流化床反应器第二气固分离设备;
100.所述流化床反应器分布器位于反应区的底部;
101.所述流化床反应器取热器位于待生剂区的下部;
102.所述待生剂区气体分布器位于待生剂区的下部;
103.流化床反应器第二气固分离设备和流化床反应器第一气固分离设备的气体出口和流化床反应器集气室相连;
104.所述流化床反应器集气室设置有产品气输送管;
105.流化床反应器第一气固分离设备和流化床反应器第二气固分离设备的催化剂出口和待生剂区相连。
106.具体地,所述含有含氧化合物的原料通过流化床反应器分布器和再生催化剂接触反应。
107.具体地,所述待生剂区流化气体通过待生剂区气体分布器和待生催化剂接触。
108.可选地,所述反应区和待生剂区之间通过待生剂循环管连通。
109.具体地,所述待生剂循环管的入口连接与待生区;
110.所述待生剂循环管的出口连接与反应区的底部。
111.可选地,所述待生剂循环管设置有待生剂循环滑阀。
112.可选地,所述流化床反应器第一气固分离设备采用一组或多组气固旋风分离器。
113.优选地,每组气固旋风分离器包含一个第一级气固旋风分离器和一个第二级气固旋风分离器。
114.可选地,所述流化床反应器第二气固分离设备采用一组或多组气固旋风分离器。
115.优选地,每组气固旋风分离器包含一个第一级气固旋风分离器和一个第二级气固旋风分离器。
116.作为一种优选的实施方式,所述流化床反应器包含:流化床反应器壳体,流化床反应器分布器,输送管,流化床反应器第一气固分离设备,流化床反应器集气室,待生剂区气体分布器,流化床反应器取热器,流化床反应器第二气固分离设备,产品气输送管,待生剂循环管,待生剂循环滑阀,待生斜管,流化床反应器汽提器,待生滑阀和待生剂输送管;
117.所述流化床反应器的下部是反应区,中部是待生剂区,上部是气固分离区;
118.所述流化床反应器分布器位于流化床反应器的反应区的底部,输送管位于流化床反应器中部和上部的中心区域,输送管的底端连接于反应区的顶端,输送管的上部连接于流化床反应器第一气固分离设备的入口,流化床反应器第一气固分离设备位于流化床反应器的气固分离区,流化床反应器第一气固分离设备的气体出口连接于流化床反应器集气室,流化床反应器第一气固分离设备的催化剂出口位于待生剂区,待生剂区气体分布器位于待生剂区的底部,流化床反应器取热器位于待生剂区,流化床反应器第二气固分离设备位于流化床反应器的气固分离区,流化床反应器第二气固分离设备的入口位于流化床反应器的气固分离区,流化床反应器第二气固分离设备的气体出口连接于流化床反应器集气室,流化床反应器第二气固分离设备的催化剂出口位于待生剂区,流化床反应器集气室位于流化床反应器的顶部,产品气输送管连接于流化床反应器集气室的顶部,待生剂循环管的入口连接于待生剂区,待生剂循环管的出口连接于流化床反应器的反应区的底部,待生剂循环管中设置待生剂循环滑阀,待生斜管的入口连接于待生剂区,待生斜管的出口连接于流化床反应器汽提器的上部,流化床反应器汽提器置于流化床反应器壳体之外,待生滑阀的入口经管道连接于流化床反应器汽提器的底部,待生滑阀的出口经管道连接于待生剂输送管的入口,待生剂输送管的出口连接于第一再生器。
119.根据本技术的第三方面,提供一种活化含氧化合物制备低碳烯烃的催化剂的方法。
120.一种活化含氧化合物制备低碳烯烃的催化剂的方法,采用上述所述的再生装置。
121.可选地,所述方法包括:
122.将第一活化区原料与待生催化剂通入第一活化区中,所述待生催化剂沿着所述第一活化区子区以环形方向流动的同时,与第一活化区原料发生化学反应,生成催化剂a;
123.将所述催化剂a的一部分催化剂a1与第二再生器原料通入第二再生器中,发生化学反应,生成催化剂a3;
124.将所述催化剂a的另一部分催化剂a2、催化剂a3和第二活化区原料通入第二活化区中,发生化学反应,生成再生催化剂;
125.所述催化剂a中的焦的组成中含有含氧烃类物种和不含氧烃类物种。
126.可选地,第一活化区原料通过第一活化区分布器进入第一活化区,与催化剂中的焦发生反应。
127.可选地,第二活化区原料通过第二活化区分布器进入第二活化区,与催化剂中的焦发生反应。
128.可选地,第二再生器原料通过第二再生器分布器进入第二活化区,与催化剂中的焦发生反应。
129.具体地,待生催化剂沿着设置在挡板上的催化剂流通孔以环形方向流动的同时,第一活化区原料由位于下方的第一活化区分布器进入第一活化区子区,与待生催化剂接触,将待生催化剂中的非活性焦和活性焦转化为分子量较小的含氧烃类物种和不含氧烃类物种,气相(包括未反应的第一活化区原料)由第一活化区上方的第一活化区气体输送管输送至气固分离区。
130.具体地,催化剂通过第一活化区催化剂输送管进入第二活化区,第二活化区原料由位于下方的第二活化区分布器进入第二活化区,与催化剂接触,将催化剂中的焦中所含
的没有催化活性的含氧烃类物种转化为具有催化活性的不含氧烃类物种,气相(包括未反应的第二活化区原料)进入气固分离区。
131.具体地,催化剂通过第二再生剂输送管进入第二再生器,第二再生器原料由位于下方的第二再生器分布器进入第二再生器,与催化剂接触,催化剂中的焦被燃烧消除,空气转化为烟气,气相(包括未反应的第二再生器原料)进入气固分离区。
132.可选地,所述待生催化剂中的焦与第一活化区原料发生化学反应,生成第一活化区产品气。
133.可选地,所述催化剂a的另一部分催化剂a2、催化剂a3中的焦与第二活化区原料发生化学反应,生成第二活化区产品气。
134.可选地,第一活化区产品气和第二活化区产品气在气固分离区中混合形成再生器产品气。
135.可选地,再生器产品气携带催化剂进入第一再生器第二气固分离设备,经第一再生器第二气固分离设备分离得到再生器产品气和催化剂;
136.所述再生器产品气进入第一再生器集气室;
137.所述催化剂返回第一再生器的第二活化区。
138.具体地,所述催化剂a的部分a1中的焦与第二再生器原料发生化学反应,催化剂中的焦被燃烧消除,空气转化为烟气。
139.具体地,所述烟气携带催化剂进入第二再生器气固分离设备,气固分离后,烟气进入第二再生器集气室,催化剂返回第二再生器的底部。
140.可选地,所述第一活化区原料含有氧气和水蒸气;
141.其中,氧气的质量分数0-10wt%;
142.水蒸气的质量分数90-100wt%。
143.可选地,所述第一活化区原料为氧气和水蒸气。
144.可选地,所述第二活化区原料选自水蒸气、烃类混合物中的至少一种;
145.其中,所述烃类混合物包含甲烷、乙烷、丙烷和c
4-c6烃类,所述c
4-c6烃类包含丁烯、丁烷、戊烯、戊烷、己烯和己烷。
146.具体地,所述烃类混合物来自于用本技术的装置生产的除乙烯和丙烯之外的其他产物,包含甲烷、乙烷、丙烷和c
4-c6烃类,所述c
4-c6烃类包含丁烯、丁烷、戊烯、戊烷、己烯和己烷。
147.具体地,所述烃类混合物来自于含氧化合物在流化床反应器中转化生成的除乙烯和丙烯之外的副产物。
148.可选地,所述第二再生器原料含有空气。
149.可选地,所述第二再生器原料为空气。
150.可选地,所述催化剂a3的焦含量为0-0.5wt%。
151.可选地,所述待生催化剂中的焦含量为9-13wt%。
152.优选地,所述待生催化剂中的焦含量为10-12wt%。
153.可选地,所述再生催化剂中的焦含量为5-11wt%;
154.所述再生催化剂中的焦含量分布的四分位差小于等于1.5wt%。
155.可选地,所述再生催化剂中,焦物种中包含多甲基苯和多甲基萘;
156.多甲基苯和多甲基萘的质量和在焦总质量中的含量为≥60wt%;
157.分子量》184的焦物种的质量在焦总质量中的含量为≤30wt%;
158.其中,所述焦总质量是指焦物种的总质量。
159.本技术中,焦物种的类型,以及焦物种的含量非常重要,通过控制催化剂在第一活化区和第二活化区中的平均停留时间和停留时间分布控制催化剂中的焦含量及焦含量分布,实现了多甲基苯和多甲基萘在焦总质量中的含量≥60wt%的效果,提高了催化剂的活性,以及低碳烯烃选择性。
160.可选地,第二再生器进入第一再生器的催化剂的质量流量是第一再生器进入流化床反应器的催化剂的质量流量的1-20wt%。
161.具体地,所述经由第三再生斜管和第三再生滑阀进入第一再生器的催化剂的质量流量为经由第一再生斜管、第一再生滑阀和第一再生剂输送管进入流化床反应器的催化剂的质量流量的1-20wt%。
162.可选地,所述待生催化剂含有sapo-34分子筛。
163.本技术中,催化剂中的活性组分是sapo-34分子筛。
164.可选地,所述第一再生器的第一活化区的工艺操作条件为:气体表观线速度为0.1-0.5m/s,温度为650-750℃,压力为100-500kpa,床层密度为400-700kg/m3。
165.可选地,所述第一再生器的第二活化区的工艺操作条件为:气体表观线速度为0.1-0.5m/s,温度为550-700℃,压力为100-500kpa,床层密度为400-700kg/m3。
166.可选地,所述第二再生器的工艺操作条件为:气体表观线速度为0.5-2.0m/s,温度为650-750℃,压力为100-500kpa,床层密度为150-700kg/m3。
167.本技术中的第一再生器的第一活化区包含n个第一活化区子区,催化剂仅能通过第一活化区中的挡板中的催化剂流通孔从上游子区依序流向下游子区,其有益效果包含:
①
可以通过改变工艺操作条件控制催化剂在第一活化区中的平均停留时间,因此,可以控制催化剂中的焦含量;
②
采用n个第一活化区子区的结构控制催化剂的停留时间分布,其停留时间分布近似于n个串联的全混釜反应器,因此,可以获得焦含量分布窄的再生催化剂。
168.本技术中,由于催化剂为粉体,所以催化剂的焦含量是指每个催化剂颗粒焦含量的均值,但是每个催化剂颗粒中的焦含量实际上是不一样的。本技术中,可以将再生催化剂中的焦含量分布的四分位差控制在小于1.5wt%的范围内,使得催化剂整体焦含量分布窄,从而提高催化剂的活性、以及低碳烯烃选择性。
169.本技术中,催化剂的活化过程包含三个步骤:
①
以水蒸气和少量氧气为活化气体将待生催化剂中的非活性焦和活性焦转化为分子量较小的含氧烃类物种和不含氧烃类物种,其中含氧烃类物种没有催化活性,此步骤在第一再生器的第一活化区完成;
②
以空气为活化气体将一部分催化剂的焦含量降低至≤0.5wt%,此步骤在第二再生器中完成;
③
以水蒸气、甲烷、乙烷、丙烷和c
4-c6烃类等非氧化性气体为活化气体,一方面将来自第一活化区的催化剂中所含的没有催化活性的含氧烃类物种转化为具有催化活性的不含氧烃类物种,另一方面甲烷、乙烷、丙烷和c
4-c6烃类在来自第二再生器的焦含量≤0.5wt%的催化剂的作用下,转化为乙烯和丙烯,此步骤在第一再生器的第二活化区完成。第一步采用弱氧化性的活化气体将非活性焦分解,但分解速率较慢,很难将非活性焦完全分解,并且不完全分解导致生成一部分没有催化活性的含氧烃类物种;第二步采用强氧化性的空气将一部分催化剂
中的焦几乎完全分解,获得一部分具有高活性的催化剂,此部分催化剂可以用于将甲烷、乙烷、丙烷和c
4-c6烃类转化为乙烯和丙烯;第三步采用非氧化性的活化气体进一步将没有催化活性的含氧烃类物种转化为具有催化活性的不含氧烃类物种,并且同时增产乙烯和丙烯。经过三步活化之后,再生催化剂中的焦的物种以多甲基苯和多甲基萘为主,乙烯选择性高。
170.本技术中,第一再生器和第二再生器为放热反应和吸热反应的耦合,第一活化区原料和催化剂中的焦在第一活化区中发生反应,生成co和h2等物质,释放热量将催化剂的温度升高,空气和催化剂中的焦在第二再生器中发生反应,释放热量将催化剂的温度进一步升高,第二活化区原料和催化剂中的焦在第二活化区中发生反应,此反应是吸热反应,反应所需热量由第一活化区和第二再生器中的放热反应供给。
171.本技术的第一再生器中,在活化待生催化剂的同时将副产品转化为乙烯和丙烯,提高了乙烯和丙烯的收率。
172.本技术的第一再生器中,在活化待生催化剂的同时将待生催化剂中的焦转化为co和h2,co和h2可以作为制备甲醇的原料循环利用。
173.本技术的第二再生器中,以强氧化性的空气为再生介质将催化剂中的非活性焦和活性焦几乎完全消除,达到焦含量≤0.5wt%。
174.作为一种优选的实施方式,将第一活化区原料从第一活化区分布器通入第一再生器的第一活化区,将待生催化剂从待生剂输送管通入第一再生器第一气固分离设备,气固分离后,气体由第一再生器第一气固分离设备的气体出口排入第一再生器的气固分离区,待生催化剂由第一再生器第一气固分离设备的催化剂出口排入第一再生器的第一活化区;第一活化区原料和待生催化剂在第一活化区接触、发生化学反应,待生催化剂中的非活性焦和活性焦转化为分子量较小的含氧烃类物种和不含氧烃类物种,并生成第一活化区产品气;第一活化区中的催化剂经由挡板中的催化剂流通孔依序通过第1-n第一活化区子区;一部分催化剂经由第一活化区催化剂输送管进入第一再生器的第二活化区,另一部分催化剂经由第二再生斜管、第二再生滑阀和第二再生剂输送管进入第二再生器的中部;第一活化区产品气经由第一活化区气体输送管进入第一再生器的气固分离区;将第二活化区原料从第二活化区分布器通入第一再生器的第二活化区,与来自第一活化区和第二再生器的催化剂接触、发生化学反应,焦中所含的没有催化活性的含氧烃类物种转化为具有催化活性的不含氧烃类物种,与此同时,焦的分子量进一步变小,即,催化剂中的焦转化为以多甲基苯和多甲基萘为主的物种,经过第二活化区后,催化剂被称之为再生催化剂,在第二活化区中,第二活化区原料转化为第二活化区产品气,然后进入第一再生器的气固分离区;第一活化区产品气和第二活化区产品气在气固分离区中混合形成再生器产品气,再生器产品气携带催化剂进入第一再生器第二气固分离设备,气固分离后,分为再生器产品气和催化剂,再生器产品气进入第一再生器集气室,然后再经由第一再生器产品气输送管进入下游工段,催化剂返回第一再生器的第二活化区;第二活化区的再生催化剂在取热、降温之后经由第一再生斜管、第一再生滑阀和第一再生剂输送管进入流化床反应器;
175.将空气从第二再生器分布器通入第二再生器的底部,在第二再生器中,空气和来自第一再生器的催化剂接触,发生化学反应,催化剂中的焦被燃烧消除,空气转化为烟气,烟气携带催化剂进入第二再生器气固分离设备,气固分离后,烟气进入第二再生器集气室,
再经由烟气输送管进入下游的烟气处理系统,催化剂返回第二再生器的底部,第二再生器中的催化剂经由第三再生斜管和第三再生滑阀进入第一再生器的气固分离区。
176.根据本技术的第四方面,提供一种含氧化合物制备低碳烯烃的方法。
177.一种含氧化合物制备低碳烯烃的方法,采用上述所述的装置。
178.可选地,所述方法包括:
179.将含有含氧化合物的原料与再生催化剂通入反应区,反应,得到含有低碳烯烃和待生催化剂的物流a;
180.将所述物流a气固分离后,将所述待生催化剂通入待生剂区;
181.待生剂区的一部分待生催化剂返回流化床反应区,另一部分待生催化剂进入第一再生器。
182.具体地,待生剂区的一部分待生催化剂通过待生剂循环管返回流化床反应区,另一部分待生催化剂通过待生斜管、流化床反应器汽提器和待生剂输送管进入第一再生器。
183.可选地,所述待生催化剂经再生装置再生后得到的再生催化剂,通过第一再生剂输送管进入流化床反应器的反应区。
184.可选地,再生催化剂进入流化床反应器的反应区的同时,含有含氧化合物的原料通过流化床反应器分布器进入流化床反应器的反应区,反应,得到含有低碳烯烃和待生催化剂的物流a。
185.可选地,含有低碳烯烃和待生催化剂的物流a经过输送管进入流化床反应器第一气固分离设备,分离得到含有低碳烯烃的气体和待生催化剂。
186.可选地,所述含有低碳烯烃的气体进入流化床反应器集气室。
187.可选地,所述待生催化剂经汽提后进入第一再生器。
188.可选地,所述待生剂区流化气体选自氮气、水蒸气中的至少一种。
189.可选地,所述含氧化合物的原料选自甲醇、二甲醚中的至少一种。
190.可选地,所述再生催化剂的质量流量和所述含氧化合物的进料量的比值为0.3~1.0吨催化剂/吨甲醇。
191.优选地,所述再生催化剂的质量流量和所述含氧化合物的进料量的比值为0.5~1.0吨催化剂/吨甲醇。
192.可选地,所述流化床反应器的反应区的工艺操作条件为:气体表观线速度为0.5-7.0m/s,反应温度为350-550℃,反应压力为100-500kpa,床层密度为100-500kg/m3。
193.可选地,所述流化床反应器的待生剂区的工艺操作条件为:气体表观线速度为0.1-1.0m/s,反应温度为350-550℃,反应压力为100-500kpa,床层密度为200-800kg/m3。
194.可选地,含有含氧化合物的原料与再生催化剂在流化床反应器的反应区反应后获得含有低碳烯烃和待生催化剂的物流a,经过输送管进入流化床反应器第一气固分离设备,气固分离后,分为气相物流b和固相物流c,固相物流c进入待生剂区,待生剂区流化气体和固相物流c形成物流d,物流d进入流化床反应器第二气固分离设备,气固分离后,分为气相物流e和固相物流f,固相物流f返回待生剂区,待生剂区的待生催化剂经汽提后进入第一再生器,经再生装置再生后的再生催化剂经第一再生剂输送管进入流化床反应器的反应区。
195.可选地,待生剂区的一部分待生催化剂经过待生剂循环管返回流化床反应器的反应区的底部。
196.可选地,所述固相物流c、固相物流f含有待生催化剂。
197.可选地,气相物流b和气相物流e在流化床反应器集气室中混合形成产品气;
198.所述气相物流b含有低碳烯烃。
199.本技术中,反应区属于快速流态化区,反应区的气体表观线速度可以达到7.0m/s,具有较高的甲醇通量,设备单位体积的甲醇处理量大,甲醇质量空速可以达到20h-1
;待生剂区属于鼓泡流态化区,待生剂区用于取热、降低待生催化剂的温度,并向反应区输送低温的待生催化剂,提高反应区的床层密度、控制反应区的床层温度,当气体表观线速度为0.5-7.0m/s时,相对应的床层密度为500-100kg/m3。
200.本技术中,流化床反应器第一气固分离设备直接连接于输送管的结构,实现了物流a中含有低碳烯烃的气体和待生催化剂的快速分离,避免了低碳烯烃在待生催化剂的作用下进一步反应生成具有更大分子量的烃类副产品。
201.作为一种优选的实施方式,将含有含氧化合物的原料从流化床反应器分布器通入流化床反应器的反应区,与来自第一再生剂输送管的再生催化剂接触,生成含有低碳烯烃和待生催化剂的物流a,物流a经过输送管进入流化床反应器第一气固分离设备,气固分离后,分为气相物流b和固相物流c,气相物流b是含有低碳烯烃的气体,固相物流c是待生催化剂,气相物流b进入流化床反应器集气室,固相物流c进入待生剂区;将待生剂区流化气体从待生剂区气体分布器通入待生剂区,和待生催化剂接触,待生剂区流化气体和其携带的待生催化剂形成物流d,物流d进入流化床反应器第二气固分离设备,气固分离后,分为气相物流e和固相物流f,气相物流e是待生剂区流化气体,固相物流f是待生催化剂,气相物流e进入流化床反应器集气室,固相物流f返回待生剂区;气相物流b和气相物流e在流化床反应器集气室中混合形成产品气,产品气经由产品气输送管进入下游工段;待生剂区的一部分待生催化剂经过待生剂循环管和待生剂循环滑阀返回流化床反应器的反应区的底部,另一部分待生催化剂经由待生斜管进入流化床反应器汽提器,汽提之后,待生催化剂再经由待生滑阀和待生剂输送管进入第一再生器。
202.本技术中,“剂醇比”,是指再生催化剂的质量流量/含氧化合物的进料量,本技术表述剂醇比时,将含氧化合物中的二甲醚质量依据c元素质量等同折算为甲醇质量计。
203.本技术所述的方法中,含氧化合物在流化床反应器中转化为乙烯、丙烯和副产物,副产物在第一再生器中进一步转化为乙烯和丙烯,因此,乙烯和丙烯的总产量包含这两部分的产量。本技术所述的方法中,乙烯的收率为39-56wt%,丙烯的收率为37-53wt%,c
4-c6烃类的收率为≤5wt%,其他组分的收率为≤4wt%,其他组分是甲烷、乙烷、丙烷、氢气、co和co2等,并且乙烯和丙烯的总收率为92-96wt%。
204.本技术表述生产单耗时,将含氧化合物中的二甲醚质量依据c元素质量等同折算为甲醇质量计,生产单耗的单位为吨甲醇/吨低碳烯烃。
205.本技术所述的方法中,生产单耗为2.4-2.5吨甲醇/吨低碳烯烃。
206.本技术能产生的有益效果包括:
207.(1)再生催化剂中的焦的物种以多甲基苯和多甲基萘为主,乙烯选择性高;
208.(2)通过控制催化剂在第一活化区和第二活化区中的平均停留时间和停留时间分布控制催化剂中的焦含量及焦含量分布;
209.(3)采用多孔板抑制催化剂在床层内的反混,提高催化剂中的焦分布的均匀性;
210.(4)在活化待生催化剂的同时将待生催化剂中的焦转化为co和h2,co和h2可以作为制备甲醇的原料循环利用;
211.(5)分别以弱氧化性气体、强氧化性气体和非氧化性气体为再生介质,分步活化待生催化剂,在活化待生催化剂、获得高的低碳烯烃选择性的同时实现了副产物转化增产乙烯和丙烯;
212.(6)由于待生催化剂中的大部分的焦被转化为co和h2后循环利用,全过程中c原子利用率≥98.5%。
附图说明
213.图1为本技术根据本技术一个实施方案的含氧化合物制备低碳烯烃(dmto)的装置的示意图。
214.图2为图1中第一活化区的横截面的示意图。
215.附图1和2中的附图标记说明如下:
216.1-流化床反应器;1-1-流化床反应器壳体;1-2-流化床反应器分布器;1-3-输送管;1-4-流化床反应器第一气固分离设备;1-5-流化床反应器集气室;1-6-待生剂区气体分布器;1-7-流化床反应器取热器;1-8-流化床反应器第二气固分离设备;1-9-产品气输送管;1-10-待生剂循环管;1-11-待生剂循环滑阀;1-12-待生斜管;1-13-流化床反应器汽提器;1-14-待生滑阀;1-15-待生剂输送管;
217.2-第一再生器;2-1-第一再生器壳体;2-2-第一再生器第一气固分离设备;2-3-第一活化区分布器;2-4-挡板;2-5-第一活化区催化剂输送管;2-6-第一活化区气体输送管;2-7-第二活化区分布器;2-8-多孔板;2-9-第一再生器取热器;2-10-第一再生器第二气固分离设备;2-11-第一再生器集气室;2-12-第一再生器产品气输送管;2-13-第一再生斜管;2-14-第一再生滑阀;2-15-第一再生剂输送管;2-16-第二再生斜管;2-17-第二再生滑阀;2-18第二再生剂输送管;
218.3-第二再生器;3-1-第二再生器壳体;3-2-第二再生器分布器;3-3-第二再生器气固分离设备;3-4-第二再生器集气室;3-5-烟气输送管;3-6-第三再生斜管;3-7-第三再生滑阀。
具体实施方式
219.下面结合实施例详述本技术,但本技术并不局限于这些实施例。
220.如无特别说明,本技术的实施例中的原料和催化剂均通过商业途径购买。
221.作为本技术的一种实施方式,含氧化合物制低碳烯烃(dmto)装置的示意图如图1和图2所示,该装置包含流化床反应器(1)、第一再生器(2)和第二再生器(3),分述如下:
222.如图1所示,a.流化床反应器(1)包含:流化床反应器壳体(1-1),流化床反应器分布器(1-2),输送管(1-3),流化床反应器第一气固分离设备(1-4),流化床反应器集气室(1-5),待生剂区气体分布器(1-6),流化床反应器取热器(1-7),流化床反应器第二气固分离设备(1-8),产品气输送管(1-9),待生剂循环管(1-10),待生剂循环滑阀(1-11),待生斜管(1-12),流化床反应器汽提器(1-13),待生滑阀(1-14)和待生剂输送管(1-15)。流化床反应器(1)的下部是反应区,中部是待生剂区,上部是气固分离区。流化床反应器分布器(1-2)位于
流化床反应器(1)的反应区的底部,输送管(1-3)位于流化床反应器(1)中部和上部的中心区域,输送管(1-3)的底端连接于反应区的顶端,输送管(1-3)的上部连接于流化床反应器第一气固分离设备(1-4)的入口,流化床反应器第一气固分离设备(1-4)位于流化床反应器(1)的气固分离区,流化床反应器第一气固分离设备(1-4)的气体出口连接于流化床反应器集气室(1-5),流化床反应器第一气固分离设备(1-4)的催化剂出口位于待生剂区,待生剂区气体分布器(1-6)位于待生剂区的底部,流化床反应器取热器(1-7)位于待生剂区,流化床反应器第二气固分离设备(1-8)位于流化床反应器(1)的气固分离区,流化床反应器第二气固分离设备(1-8)的入口位于流化床反应器(1)的气固分离区,流化床反应器第二气固分离设备(1-8)的气体出口连接于流化床反应器集气室(1-5),流化床反应器第二气固分离设备(1-8)的催化剂出口位于待生剂区,流化床反应器集气室(1-5)位于流化床反应器(1)的顶部,产品气输送管(1-9)连接于流化床反应器集气室(1-5)的顶部,待生剂循环管(1-10)的入口连接于待生剂区,待生剂循环管(1-10)的出口连接于流化床反应器(1)的反应区的底部,待生剂循环管(1-10)中设置待生剂循环滑阀(1-11),待生斜管(1-12)的入口连接于待生剂区,待生斜管(1-12)的出口连接于流化床反应器汽提器(1-13)的上部,流化床反应器汽提器(1-13)置于流化床反应器壳体(1-1)之外,待生滑阀(1-14)的入口经管道连接于流化床反应器汽提器(1-13)的底部,待生滑阀(1-14)的出口经管道连接于待生剂输送管(1-15)的入口,待生剂输送管(1-15)的出口连接于第一再生器(2)。流化床反应器第一气固分离设备(1-4)采用多组气固旋风分离器,每组气固旋风分离器包含一个第一级气固旋风分离器和一个第二级气固旋风分离器;流化床反应器第二气固分离设备(1-8)采用多组气固旋风分离器,每组气固旋风分离器包含一个第一级气固旋风分离器和一个第二级气固旋风分离器。
223.如图1所示,第一再生器(2)包含:第一再生器壳体(2-1),第一再生器第一气固分离设备(2-2),第一活化区分布器(2-3),挡板(2-4),第一活化区催化剂输送管(2-5),第一活化区气体输送管(2-6),第二活化区分布器(2-7),多孔板(2-8),第一再生器取热器(2-9),第一再生器第二气固分离设备(2-10),第一再生器集气室(2-11),第一再生器产品气输送管(2-12),第一再生斜管(2-13),第一再生滑阀(2-14),第一再生剂输送管(2-15),第二再生斜管(2-16),第二再生滑阀(2-17)和第二再生剂输送管(2-18)。第一再生器(2)由下至上分为第二活化区、第一活化区和气固分离区。第一活化区位于第二活化区上方的环形区域,第一活化区内设置n个挡板(2-4),挡板(2-4)将第一活化区分割为n个第一活化区子区,每个第一活化区子区的底部都独立设置第一活化区分布器(2-3),第一活化区的横截面是环形,第一活化区子区的横截面是扇环形,第1-n第一活化区子区同心依序排列,挡板(2-4)中含有催化剂流通孔,但第1第一活化区子区和第n第一活化区子区间的挡板不含催化剂流通孔;第一再生器第一气固分离设备(2-2)位于第一再生器(2)的气固分离区,第一再生器第一气固分离设备(2-2)的入口连接于待生剂输送管(1-15)的出口,第一再生器第一气固分离设备(2-2)的气体出口位于气固分离区,第一再生器第一气固分离设备(2-2)的催化剂出口位于第1第一活化区子区;第一活化区催化剂输送管(2-5)的入口连接于第n第一活化区子区,第一活化区催化剂输送管(2-5)的出口位于第二活化区;每个第一活化区子区的顶部都独立设置第一活化区气体输送管(2-6),第一活化区气体输送管(2-6)的出口位于气固分离区;第二活化区分布器(2-7)位于第一再生器(2)的第二活化区的底部,第二活化区中
设置m块多孔板(2-8),第一再生器取热器(2-9)位于第二活化区;第一再生器第二气固分离设备(2-10)和第一再生器集气室(2-11)位于第一再生器(2)的气固分离区,第一再生器第二气固分离设备(2-10)的入口位于第一再生器(2)的气固分离区,第一再生器第二气固分离设备(2-10)的气体出口连接于第一再生器集气室(2-11),第一再生器第二气固分离设备(2-10)的催化剂出口位于第二活化区,第一再生器产品气输送管(2-12)连接于第一再生器集气室(2-11)的顶部;第一再生斜管(2-13)的入口连接于第二活化区的下部,第一再生滑阀(2-14)的入口连接于第一再生斜管(2-13)的出口,第一再生滑阀(2-14)的出口经管道连接于第一再生剂输送管(2-15)的入口,第一再生剂输送管(2-15)的出口连接于流化床反应器(1)的反应区;第二再生斜管(2-16)的入口连接于第一活化区,第二再生滑阀(2-17)的入口连接于第二再生斜管(2-16)的出口,第二再生滑阀(2-17)的出口经管道连接于第二再生剂输送管(2-18)的入口,第二再生剂输送管(2-18)的出口连接于第二再生器(3)的中部。第一再生器第二气固分离设备(2-10)采用多组气固旋风分离器,每组气固旋风分离器包含一个第一级气固旋风分离器和一个第二级气固旋风分离器。
224.如图1所示,第二再生器(3)包含:第二再生器壳体(3-1),第二再生器分布器(3-2),第二再生器气固分离设备(3-3),第二再生器集气室(3-4),烟气输送管(3-5),第三再生斜管(3-6)和第三再生滑阀(3-7)。第二再生器分布器(3-2)位于第二再生器(3)的底部,第二再生器气固分离设备(3-3)位于第二再生器(3)的上部,第二再生器气固分离设备(3-3)的入口位于第二再生器(3)的上部,第二再生器气固分离设备(3-3)的气体出口连接于第二再生器集气室(3-4),第二再生器气固分离设备(3-3)的催化剂出口位于第二再生器(3)的下部,第二再生器集气室(3-4)位于第二再生器(3)的顶部,烟气输送管(3-5)连接于第二再生器集气室(3-4)的顶部,第三再生斜管(3-6)的入口连接于第二再生器(3)的下部,第三再生斜管(3-6)中设置第三再生滑阀(3-7),第三再生斜管(3-6)的出口连接于第一再生器(2)的气固分离区。第二再生器气固分离设备(3-3)采用多组气固旋风分离器,每组气固旋风分离器包含一个第一级气固旋风分离器和一个第二级气固旋风分离器。
225.作为本技术的一个具体实施方案中,本技术所述的由含氧化合物制备低碳烯烃的方法包括:
226.将含有含氧化合物的原料从流化床反应器分布器(1-2)通入流化床反应器(1)的反应区,与来自第一再生剂输送管(2-15)的再生催化剂接触,生成含有低碳烯烃和待生催化剂的物流a,物流a经过输送管(1-3)进入流化床反应器第一气固分离设备(1-4),气固分离后,分为气相物流b和固相物流c,气相物流b是含有低碳烯烃的气体,固相物流c是待生催化剂,气相物流b进入流化床反应器集气室(1-5),固相物流c进入待生剂区;将待生剂区流化气体从待生剂区气体分布器(1-6)通入待生剂区,和待生催化剂接触,待生剂区流化气体和其携带的待生催化剂形成物流d,物流d进入流化床反应器第二气固分离设备(1-8),气固分离后,分为气相物流e和固相物流f,气相物流e是待生剂区流化气体,固相物流f是待生催化剂,气相物流e进入流化床反应器集气室(1-5),固相物流f返回待生剂区;气相物流b和气相物流e在流化床反应器集气室(1-5)中混合形成产品气,产品气经由产品气输送管(1-9)进入下游工段;待生剂区的一部分待生催化剂经过待生剂循环管(1-10)和待生剂循环滑阀(1-11)返回流化床反应器(1)的反应区的底部,另一部分待生催化剂经由待生斜管(1-12)进入流化床反应器汽提器(1-13),汽提之后,待生催化剂再经由待生滑阀(1-14)和待生剂
输送管(1-15)进入第一再生器(2);
227.将第一活化区原料从第一活化区分布器(2-3)通入第一再生器(2)的第一活化区,将待生催化剂从待生剂输送管(1-15)通入第一再生器第一气固分离设备(2-2),气固分离后,气体由第一再生器第一气固分离设备(2-2)的气体出口排入第一再生器(2)的气固分离区,待生催化剂由第一再生器第一气固分离设备(2-2)的催化剂出口排入第一再生器(2)的第一活化区;第一活化区原料和待生催化剂在第一活化区接触、发生化学反应,待生催化剂中的非活性焦和活性焦转化为分子量较小的含氧烃类物种和不含氧烃类物种,并生成第一活化区产品气;第一活化区中的催化剂经由挡板(2-4)中的催化剂流通孔依序通过第1-n第一活化区子区;一部分催化剂经由第一活化区催化剂输送管(2-5)进入第一再生器(2)的第二活化区,另一部分催化剂经由第二再生斜管(2-16)、第二再生滑阀(2-17)和第二再生剂输送管(2-18)进入第二再生器(3)的中部;第一活化区产品气经由第一活化区气体输送管(2-6)进入第一再生器(2)的气固分离区;将第二活化区原料从第二活化区分布器(2-7)通入第一再生器(2)的第二活化区,与来自第一活化区和第二再生器(3)的催化剂接触、发生化学反应,焦中所含的没有催化活性的含氧烃类物种转化为具有催化活性的不含氧烃类物种,与此同时,焦的分子量进一步变小,即,催化剂中的焦转化为以多甲基苯和多甲基萘为主的物种,经过第二活化区后,催化剂被称之为再生催化剂,在第二活化区中,第二活化区原料转化为第二活化区产品气,然后进入第一再生器(2)的气固分离区;第一活化区产品气和第二活化区产品气在气固分离区中混合形成再生器产品气,再生器产品气携带催化剂进入第一再生器第二气固分离设备(2-10),气固分离后,分为再生器产品气和催化剂,再生器产品气进入第一再生器集气室(2-11),然后再经由第一再生器产品气输送管(2-12)进入下游工段,催化剂返回第一再生器(2)的第二活化区;第二活化区的再生催化剂在取热、降温之后经由第一再生斜管(2-13)、第一再生滑阀(2-14)和第一再生剂输送管(2-15)进入流化床反应器(1)。
228.将空气从第二再生器分布器(3-2)通入第二再生器(3)的底部,在第二再生器中,空气和来自第一再生器(2)的催化剂接触,发生化学反应,催化剂中的焦被燃烧消除,空气转化为烟气,烟气携带催化剂进入第二再生器气固分离设备(3-3),气固分离后,烟气进入第二再生器集气室(3-4),再经由烟气输送管(3-5)进入下游的烟气处理系统,催化剂返回第二再生器(3)的底部,第二再生器(3)中的催化剂经由第三再生斜管(3-6)和第三再生滑阀(3-7)进入第一再生器(2)的气固分离区。
229.为更好地说明本技术,便于理解本技术的技术方案,本技术的典型但非限制性的实施例如下:
230.实施例1
231.本实施方案采用图1和图2所示的装置,第一再生器第一气固分离设备(2-2)采用气固旋风分离器,第一再生器(2)的第一活化区内设置2个挡板(2-4),即,n=2,挡板(2-4)将第一活化区分割为2个第一活化区子区,第一再生器(2)的第二活化区内设置10块多孔板(2-8),即,m=10,多孔板(2-8)的开孔率为50%。
232.本实施方案中,含氧化合物是甲醇;待生剂区流化气体是氮气;第一活化区原料是10wt%氧气和90wt%水蒸气;第二活化区原料是水蒸气;催化剂中的活性组分是sapo-34分子筛;经由第三再生斜管和第三再生滑阀进入第一再生器的催化剂中的焦含量约为
0.5wt%;再生催化剂中的焦含量约为5wt%,焦物种中包含多甲基苯和多甲基萘,多甲基苯和多甲基萘的质量在焦总质量中的含量约为70wt%,分子量》184的焦物种的质量在焦总质量中的含量约为17wt%;再生催化剂中的焦含量分布的四分位差约为0.5wt%;待生催化剂中的焦含量约为9wt%;经由第三再生斜管和第三再生滑阀进入第一再生器的催化剂的质量流量为经由第一再生斜管、第一再生滑阀和第一再生剂输送管进入流化床反应器的催化剂的质量流量的1wt%;流化床反应器(1)的反应区属于快速流态化区,流化床反应器(1)的反应区的工艺操作条件为:气体表观线速度约为7.0m/s,反应温度约为550℃,反应压力约为100kpa,床层密度约为100kg/m3;流化床反应器(1)的待生剂区的工艺操作条件为:气体表观线速度约为1.0m/s,反应温度约为550℃,反应压力约为100kpa,床层密度约为200kg/m3;第一再生器(2)的第一活化区的工艺操作条件为:气体表观线速度为0.5m/s,温度为750℃,压力为100kpa,床层密度为400kg/m3;第一再生器(2)的第二活化区的工艺操作条件为:气体表观线速度为0.5m/s,温度为700℃,压力为100kpa,床层密度为400kg/m3;第二再生器(3)的工艺操作条件为:气体表观线速度为0.5m/s,温度为750℃,压力为100kpa,床层密度为700kg/m3。
233.本实施方案中,剂醇比约为0.3吨催化剂/吨甲醇;乙烯的收率约为56wt%,丙烯的收率约为37wt%,c
4-c6烃类的收率约为3wt%,其他组分的收率约为4wt%,其他组分是甲烷、乙烷、丙烷、氢气、co和co2等;生产单耗为2.48吨甲醇/吨低碳烯烃。全过程中c原子利用率是99.5%。
234.实施例2
235.本实施方案采用图1和图2所示的装置,第一再生器第一气固分离设备(2-2)采用气固旋风分离器,第一再生器(2)的第一活化区内设置10个挡板(2-4),即,n=10,挡板(2-4)将第一活化区分割为10个第一活化区子区,第一再生器(2)的第二活化区内设置1块多孔板(2-8),即,m=1,多孔板(2-8)的开孔率为5%。
236.本实施方案中,含氧化合物是82wt%甲醇和18wt%二甲醚;待生剂区流化气体是水蒸气;第一活化区原料是5wt%氧气和95wt%水蒸气;第二活化区原料是水蒸气;催化剂中的活性组分是sapo-34分子筛;经由第三再生斜管和第三再生滑阀进入第一再生器的催化剂中的焦含量约为0.3wt%;再生催化剂中的焦含量约为7wt%,焦物种中包含多甲基苯和多甲基萘,多甲基苯和多甲基萘的质量在焦总质量中的含量约为62wt%,分子量》184的焦物种的质量在焦总质量中的含量约为24wt%;再生催化剂中的焦含量分布的四分位差约为0.2wt%;待生催化剂中的焦含量约为11wt%;经由第三再生斜管和第三再生滑阀进入第一再生器的催化剂的质量流量为经由第一再生斜管、第一再生滑阀和第一再生剂输送管进入流化床反应器的催化剂的质量流量的5wt%;流化床反应器(1)的反应区的工艺操作条件为:气体表观线速度约为0.5m/s,反应温度约为350℃,反应压力约为500kpa,床层密度约为500kg/m3;流化床反应器(1)的待生剂区属于鼓泡流态化区,流化床反应器(1)的待生剂区的工艺操作条件为:气体表观线速度约为0.1m/s,反应温度约为350℃,反应压力约为500kpa,床层密度约为800kg/m3;第一再生器(2)的第一活化区的工艺操作条件为:气体表观线速度为0.3m/s,温度为700℃,压力为500kpa,床层密度为510kg/m3;第一再生器(2)的第二活化区的工艺操作条件为:气体表观线速度为0.3m/s,温度为550℃,压力为500kpa,床层密度为510kg/m3;第二再生器(3)的工艺操作条件为:气体表观线速度为2.0m/s,温度为
700℃,压力为500kpa,床层密度为150kg/m3。
237.本实施方案中,剂醇比约为0.5吨催化剂/吨甲醇;乙烯的收率约为39wt%,丙烯的收率约为53wt%,c
4-c6烃类的收率约为5wt%,其他组分的收率约为3wt%,其他组分是甲烷、乙烷、丙烷、氢气、co和co2等;生产单耗为2.50吨甲醇/吨低碳烯烃。全过程中c原子利用率是99.3%。
238.实施例3
239.本实施方案采用图1和图2所示的装置,第一再生器第一气固分离设备(2-2)采用气固快速分离器,第一再生器(2)的第一活化区内设置4个挡板(2-4),即,n=4,挡板(2-4)将第一活化区分割为4个第一活化区子区,第一再生器(2)的第二活化区内设置6块多孔板(2-8),即,m=6,多孔板(2-8)的开孔率为30%。
240.本实施方案中,含氧化合物是二甲醚;待生剂区流化气体是5wt%氮气和95wt%水蒸气;第一活化区原料是1wt%氧气和99wt%水蒸气;第二活化区原料是水蒸气和副产物的混合物,副产物指本实施方案生产的除乙烯和丙烯之外的其他产物,包含氢气、甲烷、乙烷、丙烷和c4-c6烃类等;催化剂中的活性组分是sapo-34分子筛;经由第三再生斜管和第三再生滑阀进入第一再生器的催化剂中的焦含量约为0.2wt%;再生催化剂中的焦含量约为8wt%,焦物种中包含多甲基苯和多甲基萘,多甲基苯和多甲基萘的质量在焦总质量中的含量约为81wt%,分子量》184的焦物种的质量在焦总质量中的含量约为9wt%;再生催化剂中的焦含量分布的四分位差约为1.5wt%;待生催化剂中的焦含量约为12wt%;经由第三再生斜管和第三再生滑阀进入第一再生器的催化剂的质量流量为经由第一再生斜管、第一再生滑阀和第一再生剂输送管进入流化床反应器的催化剂的质量流量的20wt%;流化床反应器(1)的反应区的工艺操作条件为:气体表观线速度约为3.0m/s,反应温度约为450℃,反应压力约为300kpa,床层密度约为230kg/m3;流化床反应器(1)的待生剂区的工艺操作条件为:气体表观线速度约为0.2m/s,反应温度约为450℃,反应压力约为300kpa,床层密度约为600kg/m3;第一再生器(2)的第一活化区的工艺操作条件为:气体表观线速度为0.2m/s,温度为680℃,压力为300kpa,床层密度为580kg/m3;第一再生器(2)的第二活化区的工艺操作条件为:气体表观线速度为0.2m/s,温度为630℃,压力为300kpa,床层密度为580kg/m3;第二再生器(3)的工艺操作条件为:气体表观线速度为1.5m/s,温度为690℃,压力为300kpa,床层密度为250kg/m3。
241.本实施方案中,剂醇比约为0.8吨催化剂/吨甲醇;乙烯的收率约为46wt%,丙烯的收率约为48wt%,c
4-c6烃类的收率约为4wt%,其他组分的收率约为2wt%,其他组分是甲烷、乙烷、丙烷、氢气、co和co2等;生产单耗为2.45吨甲醇/吨低碳烯烃。全过程中c原子利用率是98.5%。
242.实施例4
243.本实施方案采用图1和图2所示的装置,第一再生器第一气固分离设备(2-2)采用气固快速分离器,第一再生器(2)的第一活化区内设置8个挡板(2-4),即,n=8,挡板(2-4)将第一活化区分割为8个第一活化区子区,第一再生器(2)的第二活化区内设置4块多孔板(2-8),即,m=4,多孔板(2-8)的开孔率为20%。
244.本实施方案中,含氧化合物是甲醇;待生剂区流化气体是水蒸气;第一活化区原料是1wt%氧气和99wt%水蒸气;第二活化区原料是水蒸气和副产物的混合物,副产物指本实
施方案生产的除乙烯和丙烯之外的其他产物,包含氢气、甲烷、乙烷、丙烷和c4-c6烃类等;催化剂中的活性组分是sapo-34分子筛;经由第三再生斜管和第三再生滑阀进入第一再生器的催化剂中的焦含量约为0.2wt%;再生催化剂中的焦含量约为11wt%,焦物种中包含多甲基苯和多甲基萘,多甲基苯和多甲基萘的质量在焦总质量中的含量约为82wt%,分子量》184的焦物种的质量在焦总质量中的含量约为7wt%;再生催化剂中的焦含量分布的四分位差约为1.1wt%;待生催化剂中的焦含量约为13wt%;经由第三再生斜管和第三再生滑阀进入第一再生器的催化剂的质量流量为经由第一再生斜管、第一再生滑阀和第一再生剂输送管进入流化床反应器的催化剂的质量流量的15wt%;流化床反应器(1)的反应区的工艺操作条件为:气体表观线速度约为4.0m/s,反应温度约为500℃,反应压力约为200kpa,床层密度约为160kg/m3;流化床反应器(1)的待生剂区的工艺操作条件为:气体表观线速度约为0.5m/s,反应温度约为500℃,反应压力约为200kpa,床层密度约为300kg/m3;第一再生器(2)的第一活化区的工艺操作条件为:气体表观线速度为0.1m/s,温度为650℃,压力为200kpa,床层密度为700kg/m3;第一再生器(2)的第二活化区的工艺操作条件为:气体表观线速度为0.1m/s,温度为600℃,压力为200kpa,床层密度为700kg/m3;第二再生器(3)的工艺操作条件为:气体表观线速度为1.0m/s,温度为650℃,压力为200kpa,床层密度为400kg/m3。
245.本实施方案中,剂醇比约为1.0吨催化剂/吨甲醇;乙烯的收率约为50wt%,丙烯的收率约为46wt%,c
4-c6烃类的收率约为2wt%,其他组分的收率约为2wt%,其他组分是甲烷、乙烷、丙烷、氢气、co和co2等;生产单耗为2.40吨甲醇/吨低碳烯烃。全过程中c原子利用率是99.0%。
246.以上所述,仅是本技术的几个实施例,并非对本技术做任何形式的限制,虽然本技术以较佳实施例揭示如上,然而并非用以限制本技术,任何熟悉本专业的技术人员,在不脱离本技术技术方案的范围内,利用上述揭示的技术内容做出些许的变动或修饰均等同于等效实施案例,均属于技术方案范围内。
再多了解一些
本文用于企业家、创业者技术爱好者查询,结果仅供参考。