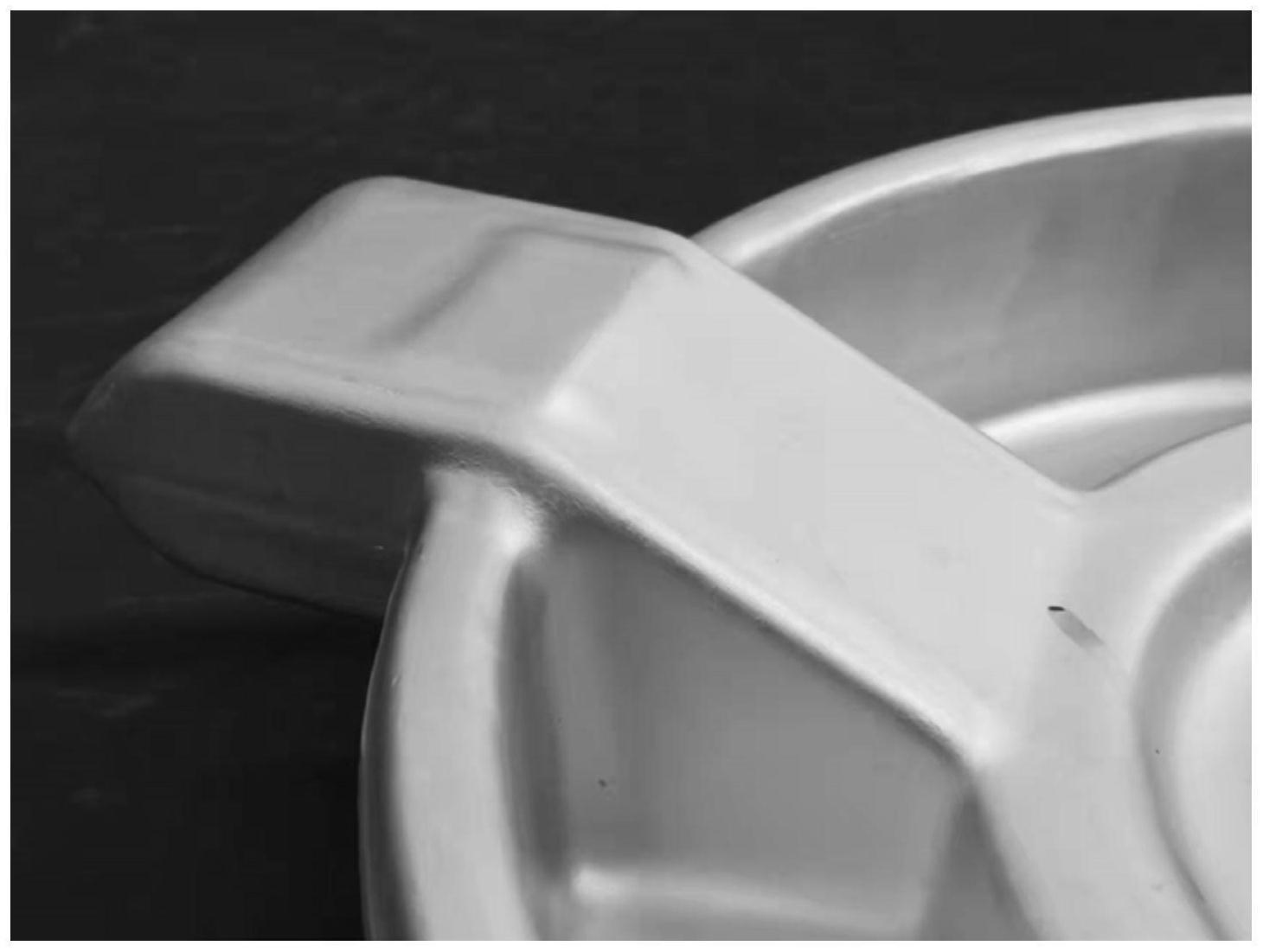
1.本发明涉及一种铝合金环形锻件控制折叠的成形方法。
背景技术:
2.铝合金具有密度低,比强度高,耐腐蚀性好等特点,是航空航天及武器系统领域追求轻量化的首选材料。铝合金环形件作为承载构件目前广泛应用于飞机上,一种不均匀分布四枝杈铝合金环形锻件直径为420mm,盘边形似汽车轮毂,沿盘边依次排布3个凸耳,间隔为90
°
,凸出部分长75mm,宽80mm,厚度50mm。另外存在一个与其中一个凸耳成30
°
夹角的梯形摇臂,摇臂长130mm,根宽120mm,顶宽80mm,厚度20mm。该环形锻件用在直升机升力系统,是承载结构件。该环形锻件的环壁厚度和凸耳厚度差较大,整体呈非对称结构使用常规模锻锤、模锻机和水压机很难成形,即使能成形的话成品率也很低。此类环形锻件对流线和疲劳寿命也有很高的要求。采用普通热模锻成形,模具温度远低于坯料温度,两者接触时坯料温度有一定程度下降,造成模锻变形抗力增大,锻件精度难以保证。这种复杂结构的环形锻件只能采用等温模锻方法才能保证锻件的成形几何尺寸和内部的组织及性能要求。由于存在3个凸耳和1个长摇臂的特殊结构,铝合金环形锻件在等温成形过程中难以控制金属流动,极易出现中心部位排料困难和锻件边缘凸耳和摇臂充不满的问题,若直接增大坯料体积会造成原材料的大量浪费,导致生产成本大幅增加。即使大料能成形,由于锻件的凸耳与环壁连接处没有过渡区,锻件凸耳很厚,环壁较薄(20mm左右),薄厚差距很大,成形时会产生金属对流折叠,折叠严重时,导致锻件无法使用,甚至报废。如何避免此类形状复杂锻件成形过程中产生折叠损伤是一个关键技术问题,目前此类具有流线要求和使用性能要求的复杂铝合金环形模锻件在研制生产过程中仍然存在很大难度。
技术实现要素:
3.本发明是要解决目前不均匀分布四枝杈铝合金环形锻件成形时会产生金属对流折叠的技术问题,而提供一种不均匀分布四枝杈铝合金环形锻件控制折叠的成形方法。
4.本发明的不均匀分布四枝杈铝合金环形锻件控制折叠的成形方法是按以下步骤进行的:
5.一、自由锻制坯:选用直径220mm和高365mm的铝合金挤压棒料,棒材的成形性能好,且成形后的锻件流线好,然后经过自由锻制坯,大变形镦粗后获得470mm
×
330mm
×
90mm的毛坯,如图1和图2所示,坯料的两个相对的侧面为竖直平面,另外两个相对的侧面有向外的弧形鼓度,留有弧形鼓度的目的是方便后续模锻过程中锻件摇臂和凸耳部位的填充;
6.二、预锻精确分料:在5000t液压机上通过预锻模具对坯料进行预锻精确分料,为后续等温模锻做准备;预锻的目的不仅是分料后使各个部位都有足够的坯料来充填模膛,更重要的是控制锻件终锻过程中折叠缺陷的形成,保证后续的等温模锻成形;预锻模具分为预锻上模和预锻下模,预锻上模如图3所示,预锻下模如图4所示;
7.通过预锻分料控制折叠缺陷的机理如下:
8.若不采用预锻分料,直接选择较大尺寸坯料进行终锻,由于铝合金环锻件的凸耳很厚,锻件的环壁较薄,薄厚差距很大且凸耳与环壁连接处没有过渡区,在终锻成形时,锻件折叠缺陷形成的示意图如图5(正视图)所示:上模1下压,环壁4处和凸耳3处的金属首先沿轴向向上流动,当金属充满较薄的环壁4后,此时凸耳3并没有充满,环壁4处多余的金属会发生环向和径向流动,环向金属流动示意图如图6所示(正视图),径向金属流动示意图如图7(俯视图)所示,最终在凸耳3处形成环向和径向折叠。锻件整体的实物图如图8所示,若没有采用预锻分料,终锻后锻件凸耳处产生严重折叠,如图9所示,圈1处为金属环向流动产生的折叠缺陷,圈2处为金属径向流动产生的折叠缺陷。对锻件折叠缺陷进行手工切除过程中发现,折叠缺陷很深,如图10所示;
9.采用预锻分料后,锻件的凸耳处会预先储料,终锻过程中,开始时环壁处和凸耳处金属同时沿轴向流动,金属流动示意图如图11所示;随着终锻的进行,上模下压,虽然锻件的环壁和凸耳处薄厚差距较大,但是预锻分料使锻件凸耳处预先储料,所以锻件的环壁和凸耳会同时充满型腔,金属流动示意图如图12所示,这样通过预锻精确分料成功的控制了锻件凸耳处折叠缺陷的产生;
10.对预锻精确分料过程进行说明:
11.采用预锻上模对自由锻大变形后的厚板470mm
×
330mm
×
90mm坯料进行轴向加压,使中心坯料减薄的同时,外缘凸耳的位置也进行加压减薄,在预锻上模加压的过程中,坯料中心部位金属沿着轴向流动,受预锻模具模膛的结构限制多余的坯料沿着径向有序的向着锻件凸耳和摇臂的方向流动,预锻过程中坯料的金属流动正视示意图如图13所示,图14为预锻过程坯料金属流动的俯视示意图(1为上模,2为下模,3为坯料);后续模锻使凸耳和摇臂处需要很多金属填充,通过使用预锻模具对坯料进行加压预锻,将坯料金属有序分流到位,实现环形锻件凸耳和摇臂处的预先储料,解决了模锻等温模锻过程中铝合金环锻件凸耳和摇臂处极容易出现的充不满和折叠问题;
12.预锻精确过程中具体工艺如下:
13.将预锻上模、预锻下模和自由锻制坯后的坯料放入电阻炉加热,预锻时坯料和预锻模具温度控制在430℃~450℃,预锻加压前坯料的厚度为90mm,预锻加压后上模下行,进行坯料减薄,精确分料,坯料减薄至厚度为70mm~75mm,上模下行的速度为3mm/s~5mm/s,经过预锻精确分料后坯料示意图如图15和图16所示,预锻精确分料后的坯料实物图如图17所示;
14.三、多道次等温模锻成形:
15.为了保证铝合金环形锻件的成形几何尺寸和成形后锻件的内部组织性能,在预锻精准分料后对在5000t液压机上对坯料进行多道次等温模锻成形,共进行3道次等温模锻;模锻后的不均匀分布四枝杈铝合金环形锻件实物图如图18所示,锻件各部位充填良好,且没有折叠缺陷产生,锻件凸耳局部实物图如图19所示;
16.在多道次等温模锻过程中,通过控制模锻件和锻模的温度,控制液压机每道次的加压速度,变形量(每道次上下模的合模间隙),最终得到的不均匀分布四枝杈铝合金环形锻件几何形状符合锻件图纸要求;环形锻件进行热处理后对锻件进行超声检测,表面荧光检测,金相检测,机械性能测试和疲劳性能测试,最终获得的铝合金环形模锻件完全满足使用要求。
17.本发明的有益效果是:
18.本发明提出一种不均匀分布四枝杈铝合金环形锻件控制折叠的成形方法,在等温锻造前对铝合金挤压棒材进行自由锻制坯和预锻精确分料,在铝合金环形锻件难以成形的凸耳和摇臂部位提前储料,解决了后续等温模锻过程中极容易出现的锻件充不满和折叠缺陷问题;通过多道次等温成形,控制环形模锻件和锻模的温度,控制液压机每道次的加压速度和变形量,获得几何形状和使用性能满足要求的不均匀分布四枝杈铝合金环形模锻件,为解决目前此类形状复杂的铝合金环形模锻件等温模锻过程中由于难以控制金属流动造成的成形困难及成形缺陷问题提供了理论依据和相关方法。
附图说明
19.图1为具体实施方式一的步骤一中大变形镦粗后获得的毛坯的俯视图;
20.图2为图1的左视图;
21.图3为具体实施方式一的步骤二中的预锻上模的示意图;
22.图4为具体实施方式一的步骤二中的预锻下模的示意图;
23.图5为具体实施方式一的步骤二中不采用预锻分料锻件凸耳处折叠形成正视示意图(环壁和凸耳未充满);
24.图6为具体实施方式一的步骤二中不采用预锻分料锻件凸耳处环向折叠形成示意图(环壁充满,凸耳未充满);
25.图7为具体实施方式一的步骤二中不采用预锻分料锻件凸耳处径向折叠形成示意图(环壁充满,凸耳未充满);
26.图8为具体实施方式一的步骤二中不采用预锻分料锻件的实物图;
27.图9为具体实施方式一的步骤二中不采用预锻分料锻件凸耳处折叠缺陷的实物图;
28.图10为具体实施方式一的步骤二中不采用预锻分料手工切除锻件折叠缺陷后的实物图;
29.图11为具体实施方式一的步骤二中采用预锻分料后锻件凸耳处金属流动的示意图(环壁和凸耳未充满);
30.图12为具体实施方式一的步骤二中采用预锻分料后锻件凸耳处金属流动的示意图(环壁和凸耳同时充满);
31.图13为具体实施方式一的步骤二中预锻过程坯料金属流动的正视示意图;
32.图14为具体实施方式一的步骤二中预锻过程坯料金属流动的俯视示意图;
33.图15为具体实施方式一的步骤二中采用预锻分料后坯料的示意图;
34.图16为图15的左视图;
35.图17为具体实施方式一的步骤二中采用预锻分料后坯料的实物图;
36.图18为具体实施方式一的步骤三中多道次等温模锻成形后锻件的实物图;
37.图19为具体实施方式一的步骤三中多道次等温模锻成形后锻件局部凸耳的实物图。
具体实施方式
38.具体实施方式一:本实施方式为一种不均匀分布四枝杈铝合金环形锻件控制折叠的成形方法,如图1-图19所示,具体是按以下步骤进行的:
39.一、自由锻制坯:选用直径220mm和高365mm的铝合金挤压棒料,棒材的成形性能好,且成形后的锻件流线好,然后经过自由锻制坯,大变形镦粗后获得470mm
×
330mm
×
90mm的毛坯,如图1和图2所示,坯料的两个相对的侧面为竖直平面,另外两个相对的侧面有向外的弧形鼓度,留有弧形鼓度的目的是方便后续模锻过程中锻件摇臂和凸耳部位的填充;
40.二、预锻精确分料:在5000t液压机上通过预锻模具对坯料进行预锻精确分料,为后续等温模锻做准备;预锻的目的不仅是分料后使各个部位都有足够的坯料来充填模膛,更重要的是控制锻件终锻过程中折叠缺陷的形成,保证后续的等温模锻成形;预锻模具分为预锻上模和预锻下模,预锻上模如图3所示,预锻下模如图4所示;
41.通过预锻分料控制折叠缺陷的机理如下:
42.若不采用预锻分料,直接选择较大尺寸坯料进行终锻,由于铝合金环锻件的凸耳很厚,锻件的环壁较薄,薄厚差距很大且凸耳与环壁连接处没有过渡区,在终锻成形时,锻件折叠缺陷形成的示意图如图5(正视图)所示:上模1下压,环壁4处和凸耳3处的金属首先沿轴向向上流动,当金属充满较薄的环壁4后,此时凸耳3并没有充满,环壁4处多余的金属会发生环向和径向流动,环向金属流动示意图如图6所示(正视图),径向金属流动示意图如图7(俯视图)所示,最终在凸耳3处形成环向和径向折叠。锻件整体的实物图如图8所示,若没有采用预锻分料,终锻后锻件凸耳处产生严重折叠,如图9所示,圈1处为金属环向流动产生的折叠缺陷,圈2处为金属径向流动产生的折叠缺陷。对锻件折叠缺陷进行手工切除过程中发现,折叠缺陷很深,如图10所示;
43.采用预锻分料后,锻件的凸耳处会预先储料,终锻过程中,开始时环壁处和凸耳处金属同时沿轴向流动,金属流动示意图如图11所示;随着终锻的进行,上模下压,虽然锻件的环壁和凸耳处薄厚差距较大,但是预锻分料使锻件凸耳处预先储料,所以锻件的环壁和凸耳会同时充满型腔,金属流动示意图如图12所示,这样通过预锻精确分料成功的控制了锻件凸耳处折叠缺陷的产生;
44.对预锻精确分料过程进行说明:
45.采用预锻上模对自由锻大变形后的厚板470mm
×
330mm
×
90mm坯料进行轴向加压,使中心坯料减薄的同时,外缘凸耳的位置也进行加压减薄,在预锻上模加压的过程中,坯料中心部位金属沿着轴向流动,受预锻模具模膛的结构限制多余的坯料沿着径向有序的向着锻件凸耳和摇臂的方向流动,预锻过程中坯料的金属流动正视示意图如图13所示,图14为预锻过程坯料金属流动的俯视示意图(1为上模,2为下模,3为坯料);后续模锻使凸耳和摇臂处需要很多金属填充,通过使用预锻模具对坯料进行加压预锻,将坯料金属有序分流到位,实现环形锻件凸耳和摇臂处的预先储料,解决了模锻等温模锻过程中铝合金环锻件凸耳和摇臂处极容易出现的充不满和折叠问题;
46.预锻精确过程中具体工艺如下:
47.将预锻上模、预锻下模和自由锻制坯后的坯料放入电阻炉加热,预锻时坯料和预锻模具温度控制在430℃~450℃,预锻加压前坯料的厚度为90mm,预锻加压后上模下行,进行坯料减薄,精确分料,坯料减薄至厚度为70mm~75mm,上模下行的速度为3mm/s~5mm/s,
经过预锻精确分料后坯料示意图如图15和图16所示,预锻精确分料后的坯料实物图如图17所示;
48.三、多道次等温模锻成形:
49.为了保证铝合金环形锻件的成形几何尺寸和成形后锻件的内部组织性能,在预锻精准分料后对在5000t液压机上对坯料进行多道次等温模锻成形,共进行3道次等温模锻;模锻后的不均匀分布四枝杈铝合金环形锻件实物图如图18所示,锻件各部位充填良好,且没有折叠缺陷产生,锻件凸耳局部实物图如图19所示;
50.在多道次等温模锻过程中,通过控制模锻件和锻模的温度,控制液压机每道次的加压速度,变形量(每道次上下模的合模间隙),最终得到的不均匀分布四枝杈铝合金环形锻件几何形状符合锻件图纸要求;环形锻件进行热处理后对锻件进行超声检测,表面荧光检测,金相检测,机械性能测试和疲劳性能测试,最终获得的铝合金环形模锻件完全满足使用要求。
51.具体实施方式二:本实施方式与具体实施方式一不同的是:步骤一中所述的铝合金挤压棒料的材质为lc9铝合金。其他与具体实施方式一相同。
52.具体实施方式三:本实施方式与具体实施方式一或二不同的是:步骤二中预锻时坯料和预锻模具温度控制在430℃。其他与具体实施方式一或二相同。
53.具体实施方式四:本实施方式与具体实施方式一至三之一不同的是:步骤二中预锻时坯料和预锻模具温度控制在440℃。其他与具体实施方式一至三之一相同。
54.具体实施方式五:本实施方式与具体实施方式四不同的是:步骤二中预锻时坯料和预锻模具温度控制在450℃。其他与具体实施方式四相同。
55.具体实施方式六:本实施方式与具体实施方式一不同的是:步骤二中坯料减薄至厚度为70mm。其他与具体实施方式一相同。
56.具体实施方式七:本实施方式与具体实施方式一不同的是:步骤二中坯料减薄至厚度为73mm。其他与具体实施方式一相同。
57.具体实施方式八:本实施方式与具体实施方式一不同的是:步骤二中坯料减薄至厚度为75mm。其他与具体实施方式一相同。
58.具体实施方式九:本实施方式与具体实施方式一不同的是:步骤二中上模下行的速度为4mm/s。其他与具体实施方式一相同。
59.具体实施方式十:本实施方式与具体实施方式一不同的是:步骤二中上模下行的速度为5mm/s。其他与具体实施方式一相同。
60.用以下试验对本发明进行验证:
61.试验一:本试验为一种不均匀分布四枝杈铝合金环形锻件控制折叠的成形方法,如图1-图19所示,具体是按以下步骤进行的:
62.一、自由锻制坯:选用直径220mm和高365mm的lc9铝合金挤压棒料,棒材的成形性能好,且成形后的锻件流线好,然后经过自由锻制坯,大变形镦粗后获得470mm
×
330mm
×
90mm的毛坯,如图1和图2所示,坯料的两个相对的侧面为竖直平面,另外两个相对的侧面有向外的弧形鼓度,留有弧形鼓度的目的是方便后续模锻过程中锻件摇臂和凸耳部位的填充;
63.二、预锻精确分料:在5000t液压机上通过预锻模具对坯料进行预锻精确分料,为
后续等温模锻做准备;预锻的目的不仅是分料后使各个部位都有足够的坯料来充填模膛,更重要的是控制锻件终锻过程中折叠缺陷的形成,保证后续的等温模锻成形;预锻模具分为预锻上模和预锻下模,预锻上模如图3所示,预锻下模如图4所示;
64.通过预锻分料控制折叠缺陷的机理如下:
65.若不采用预锻分料,直接选择较大尺寸坯料进行终锻,由于铝合金环锻件的凸耳很厚,锻件的环壁较薄,薄厚差距很大且凸耳与环壁连接处没有过渡区,在终锻成形时,锻件折叠缺陷形成的示意图如图5(正视图)所示:上模1下压,环壁4处和凸耳3处的金属首先沿轴向向上流动,当金属充满较薄的环壁4后,此时凸耳3并没有充满,环壁4处多余的金属会发生环向和径向流动,环向金属流动示意图如图6所示(正视图),径向金属流动示意图如图7(俯视图)所示,最终在凸耳3处形成环向和径向折叠。锻件整体的实物图如图8所示,若没有采用预锻分料,终锻后锻件凸耳处产生严重折叠,如图9所示,圈1处为金属环向流动产生的折叠缺陷,圈2处为金属径向流动产生的折叠缺陷。对锻件折叠缺陷进行手工切除过程中发现,折叠缺陷很深,如图10所示;
66.采用预锻分料后,锻件的凸耳处会预先储料,终锻过程中,开始时环壁处和凸耳处金属同时沿轴向流动,金属流动示意图如图11所示;随着终锻的进行,上模下压,虽然锻件的环壁和凸耳处薄厚差距较大,但是预锻分料使锻件凸耳处预先储料,所以锻件的环壁和凸耳会同时充满型腔,金属流动示意图如图12所示,这样通过预锻精确分料成功的控制了锻件凸耳处折叠缺陷的产生;
67.对预锻精确分料过程进行说明:
68.采用预锻上模对自由锻大变形后的厚板470mm
×
330mm
×
90mm坯料进行轴向加压,使中心坯料减薄的同时,外缘凸耳的位置也进行加压减薄,在预锻上模加压的过程中,坯料中心部位金属沿着轴向流动,受预锻模具模膛的结构限制多余的坯料沿着径向有序的向着锻件凸耳和摇臂的方向流动,预锻过程中坯料的金属流动正视示意图如图13所示,图14为预锻过程坯料金属流动的俯视示意图(1为上模,2为下模,3为坯料);后续模锻使凸耳和摇臂处需要很多金属填充,通过使用预锻模具对坯料进行加压预锻,将坯料金属有序分流到位,实现环形锻件凸耳和摇臂处的预先储料,解决了模锻等温模锻过程中铝合金环锻件凸耳和摇臂处极容易出现的充不满和折叠问题;
69.预锻精确过程中具体工艺如下:
70.将预锻上模、预锻下模和自由锻制坯后的坯料放入电阻炉加热,预锻时坯料和预锻模具温度控制在430℃,预锻加压前坯料的厚度为90mm,预锻加压后上模下行,进行坯料减薄,精确分料,坯料减薄至厚度为73mm,上模下行的速度为5mm/s,经过预锻精确分料后坯料示意图如图15和图16所示,预锻精确分料后的坯料实物图如图17所示;
71.三、多道次等温模锻成形:
72.为了保证铝合金环形锻件的成形几何尺寸和成形后锻件的内部组织性能,在预锻精准分料后对在5000t液压机上对坯料进行多道次等温模锻成形,共进行3道次等温模锻;模锻后的不均匀分布四枝杈铝合金环形锻件实物图如图18所示,锻件各部位充填良好,且没有折叠缺陷产生,锻件凸耳局部实物图如图19所示;
73.在多道次等温模锻过程中,通过控制模锻件和锻模的温度,控制液压机每道次的加压速度,变形量(每道次上下模的合模间隙),最终得到的不均匀分布四枝杈铝合金环形
锻件几何形状符合锻件图纸要求;环形锻件进行热处理后对锻件进行超声检测,表面荧光检测,金相检测,机械性能测试和疲劳性能测试,最终获得的铝合金环形模锻件完全满足使用要求;具体工艺如下:
74.第一道次等温模锻:坯料和模具温度控制在450℃,上模和下模的合模间隙控制在15mm,上模的下行位移速度在前半程控制在15mm/s,后半程控制在8mm/s,5000t液压机最大加压至2500t;第一次等温模锻后,将固定环锻件中心孔机加去掉直径为140mm的坯料;
75.第二道次等温模锻:锻件和模具温度控制在450℃,上模和下模的合模间隙控制在5mm,上模的下行位移速度控制在5mm/s,压力机最大加压至3200t;
76.第三道次等温模锻:为保证锻件力学性能,锻件温度控制在420℃,模具温度控制在450℃,上模和下模的合模间隙控制在0.1mm,上模的下行位移速度控制在2mm/s,压力机最大加压至4200t,随后保压3min,得到的铝合金环形模锻件如图18和图19所示。
77.本试验的有益效果是:
78.本试验提出一种不均匀分布四枝杈铝合金环形锻件控制折叠的成形方法,在等温锻造前对铝合金挤压棒材进行自由锻制坯和预锻精确分料,在铝合金环形锻件难以成形的凸耳和摇臂部位提前储料,解决了后续等温模锻过程中极容易出现的锻件充不满和折叠缺陷问题;通过多道次等温成形,控制环形模锻件和锻模的温度,控制液压机每道次的加压速度和变形量,获得几何形状和使用性能满足要求的不均匀分布四枝杈铝合金环形模锻件,为解决目前此类形状复杂的铝合金环形模锻件等温模锻过程中由于难以控制金属流动造成的成形困难及成形缺陷问题提供了理论依据和相关方法。
再多了解一些
本文用于企业家、创业者技术爱好者查询,结果仅供参考。