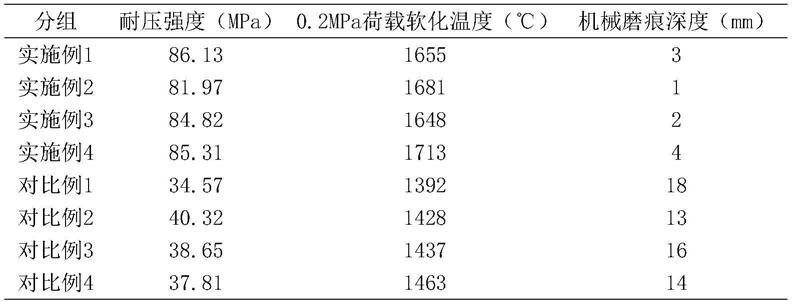
1.本发明涉及耐火材料技术领域,尤其是一种石灰窑用的内衬耐火材料及其制备方法。
背景技术:
2.近年来,随着锑矿开采和利用,每年产生大量的锑尾渣,锑尾渣中锑含量极低(≤0.1%),且含有大量的硅质资源,使得锑尾渣堆放时,不仅容易造成土地资源的占用和污染元素(例如:)污染环境,而且还导致了大量的有益资源消耗。因此,将锑尾渣应用于建材产品的制备受到了相关研究者的关注,例如:专利号为2014107504714公开了采用锑矿尾砂、粉煤灰、生石灰、石膏、水泥、铝粉作为发气剂制备成蒸压加气混凝土砌块,达到充分利用锑尾渣资源,制备的砌块具有放射性较低,表观密度低,导热系数优异,且锑、砷、汞、镉等重金属浸出率大幅度下降,提高锑尾矿应用安全性的技术方案。但是,将锑尾渣应用于耐火材料制备领域的应用研究相对较少。
3.耐火材料是具有适用于作高温应用中耐热性屏障性质的材料,该材料可作用炉底、反应室或槽等装置设备内,通过诸如浇注、喷洒、喷补,再经凝固-干燥-加热的工艺,将材料应用于装置或设备内作内衬。耐火材料往往由骨料和粘合剂组合而成,其中粘合剂包括用于制备成含水泥的耐火材料型的水泥和其他水合性氧化铝;还包括用于制备成不含水泥的耐火材料型的氧化铝溶胶粘合剂、水合性氧化铝源和氧化镁组成的无氧化钙粘合剂等。而其中用于制备不含水泥的耐火材料的粘合剂优于用于制备含水泥的耐火材料的粘合剂,得到本领域技术人员的重点关注和研究青睐,继而研究形成并开发了无水泥浇注料,但其仍有诸多问题需要解决,例如:凝固时间长、凝固行为复杂、坯强度不足、耐火性以及热机械受力行为不足等。因此,有研究者就该技术问题作出了研究,例如:专利号为201680073913.3公开了包含沸石型微结构的可浇注耐火材料组合物及其用途,采用骨料、硅灰、水合性氧化铝、钙源、分散剂等原料制备而成,骨料是氧化铝、铝硅酸盐、氧化锆、锆石、氧化镁、橄榄石、氧化铬或铬矿、尖晶石、碳化硅或其混合物;钙源铝酸钙水泥、硫酸钙、氯化钙等,所述水合性氧化铝是ρ-氧化铝等。
4.石灰窑内衬结构基本上采用以耐火砖为主,辅以隔热砖和耐火纤维制备成保温层,因此,在保温层制备过程中,耐火材料的内衬利用必不可少,目前,对于石灰窑内衬用耐火材料的研究相对较少,但也出现了相关文献,例如:专利申请号为2019103822195和专利申请号为2020104497540等文献中所公开的技术方案。
5.然而,以锑尾渣用于制备石灰窑耐火材料的研究还未见报道;因此,以锑尾渣为原料开发石灰窑用耐火材料,有助于消纳锑尾渣堆存量,充分利用锑尾渣资源,实现变废为宝,同时,保障石灰窑用内衬材料的技术需求得以改善。
技术实现要素:
6.为了解决现有技术中存在的上述技术问题,本发明提供一种石灰窑用的内衬耐火
材料及其制备方法,采用锑尾渣作为主要原料制备,充分利用锑尾渣资源,降低锑尾渣堆存量,提高资源化利用率,降低石灰窑用耐火材料制备成本,同时,保障石灰窑用内衬耐火材料各项技术指标,使得耐磨、耐热、耐压等性能得到大幅度的改善。
7.具体是通过以下技术方案得以实现的:
8.本发明创造的目的之一在于提供一种石灰窑用的内衬耐火材料,原料成分按照质量比计为细骨料:粗骨料:锑尾渣粉=1:0.3-1:4-9混合成混合物,且添加占混合物质量0.01-1%硅微粉;其中,所述细骨料粒径≤0.04cm,且d50为0.005-0.03cm;所述粗骨料粒径≤0.5cm,且d50为0.27-0.38cm。
9.为了能够提高锑尾渣粉中硅质成分以及其他有益成分能够有效的裸露利用,改善耐火材料的性能,优选,所述的锑尾渣粉是将锑尾渣送入球磨机球磨过至少200目筛而得的粉末。更优选,所述的锑尾渣粉过300目筛的筛余>5%,且所述锑尾渣粉过400目筛的筛余≤15%。
10.为了提高制备耐火材料性能,优选,所述的电解铝灰中氧化铝含量≥70%,且中粒径d
50
为0.10-0.22μm。
11.为了充分利用锑尾渣资源,保障骨料颗粒的性能,优选,所述的粗骨料是采用锑尾渣粉与粉煤灰、普通硅酸盐水泥按照质量比为1:0.2-1:0.05-0.1混合,浇水至湿润后,造粒,煅烧而成。更优选,所述的细骨料是采用电解铝灰与锑尾渣粉按照质量比为1-3:1混合,浇水至湿润后,造粒,煅烧而成。
12.在本发明创造中,所述的普通硅酸盐水泥选自但不仅限于po.42.5,该限定主要是对实际实施例操作中采用的水泥引入,而对于采用其他具有相同特性的水泥也是本发明创造的可选择范围。为了提高制备耐火材料性能,优选,所述的粉煤灰bet表面积介于12-20m2/g。
13.为了提高制备耐火材料性能,优选,所述的硅微粉中硅含量≥97%。
14.本发明创造的目的之二在于提供上述石灰窑用的内衬耐火材料制备方法,包括以下步骤:
15.(1)将锑尾渣送入球磨机中球磨过至少200目筛制成锑尾渣粉;
16.(2)取锑尾渣粉与粉煤灰、普通硅酸盐水泥混合,浇水至混合物湿润后,制备成颗粒,煅烧,得到粗骨料;
17.(3)取锑尾渣粉与电解铝灰混合,浇水至混合物湿润后,制备成颗粒,煅烧,得到细骨料;
18.(4)取细骨料、粗骨料、锑尾渣粉混合成混合物,拌匀,再加入硅微粉,得到干拌物料,加水至干拌物料湿润后,挤压成型,得到初坯;
19.(5)将初坯养护,煅烧制备,即得。
20.经锑尾渣球磨制备锑尾渣粉,降低锑尾渣中颗粒粒径较大的颗粒存在,避免影响硅质成分与其他成分相互作用效能的缺陷,提高硅质成分与其他成分胶凝相互形成胶凝成分的胶凝联结作用,增强制备的强度;再结合锑尾渣粉制备粗骨料、细骨料以及利用锑尾渣粉对细骨料、粗骨料拌合胶结作用,再利用硅微粉补充硅,使得硅铝比合适,提高挤压-养护-烧结而成的耐火材料的耐高温、耐机械摩擦、耐压等性能,且充分利用废弃物锑尾渣做原料制备,极大程度降低了石灰窑内衬耐火材料制备成本,有助于降低锑尾渣堆存量,降低
环境污染。
21.在本发明创造中,所述的煅烧,其温度≥900℃。例如:在步骤(2)中制备粗骨料煅烧时,可以采用900℃,950℃,1000℃,1100℃,1300℃进行煅烧;同理,对于步骤(3)中制备细骨料时,也可以采用类似的温度进行煅烧制备而成;煅烧时间均控制在至少4h。再例如:在步骤(5)中煅烧制备时,采用900℃煅烧10h,采用1000℃煅烧9h,采用1200℃煅烧6h,采用1300℃煅烧7h等。
22.与现有技术相比,本发明创造的技术效果体现在:
23.本发明创造涉及适合用作石灰窑用的内衬耐火材料,用于铺设在石灰窑内形成保温层、隔热层内衬材料,其具有抗压强度高、耐机械摩擦强度强、荷载耐火性能优异。
24.本发明创造利用锑尾渣为主要原料,辅以粉煤灰、普通硅酸盐水泥(po.42.5)、电解铝灰、少量的硅微粉制备而成,极大程度的降低了高成本原料的利用,将锑尾渣变废为宝,不仅解决了大量锑尾渣堆存污染环境和占用土地资源的危害,而且还实现了锑尾渣的资源化利用,同时更解决了传统石灰窑用内衬材料制备时选用的铝矾土、铝土矿、纳米硅等成本较高所导致的内衬材料成本较高的缺陷。
25.本发明创造经过将锑尾渣球磨制备成锑尾渣粉,再分别选用锑尾渣粉制备粗骨料、细骨料;再将粗骨料、细骨料、锑尾渣粉复合,补充少量硅微粉浇水润湿之后,注模挤压成型,养护煅烧制备而成,使得所得的石灰窑用的内衬耐火材料的耐压强度达到81mpa以上,0.2mpa荷载软化温度达到1630℃以上,经机械摩擦磨痕大幅度的降低;极大程度增强了内衬耐火材料的耐高温、抗机械摩擦和抗碰撞挤压能力。
具体实施方式
26.下面结合具体的实施方式来对本发明的技术方案做进一步的限定,但要求保护的范围不仅局限于所作的描述。
27.在该实施例中,石灰窑用的内衬耐火材料制备方法,包括以下步骤:
28.(1)将锑尾渣送入球磨机中球磨过至少200目筛制成锑尾渣粉;
29.(2)取锑尾渣粉与粉煤灰、普通硅酸盐水泥按照质量比为1:0.2-1:0.05-0.1混合,例如选自但不仅限于:1:0.2:0.05,1:1:0.1,1:0.5:0.08,1:0.4:0.06,1:0.8:0.09等,浇水至混合物料湿润,制备成粒径≤0.5cm的颗粒,且d
50
为0.27-0.38cm,例如选自但不仅限于0.27cm,0.32cm,0.33cm,0.38cm等,煅烧,例如煅烧时选自但不仅限于900℃煅烧处理10h,1000℃煅烧处理8h,1200℃煅烧处理6h,1100℃煅烧处理7h,1300℃煅烧处理9h等,得到粗骨料;
30.(3)取锑尾渣粉与电解铝灰按照质量比为1:1-3混合,例如选自但不仅限于:1:1,1:2,1:3等,浇水至混合物料湿润,制备成粒径≤0.04cm的颗粒,且d
50
为0.005-0.03cm,例如选自但不仅限于0.005cm,0.015cm,0.02cm,0.025cm,0.030cm等,煅烧,例如煅烧时选自但不仅限于950℃煅烧处理9h,1080℃煅烧处理8h,1100℃煅烧处理6h,1200℃煅烧处理7h,1300℃煅烧处理8h等,得到细骨料;
31.(4)取细骨料、粗骨料、锑尾渣粉按照质量比为1:0.3-1:4-9混合成混合物,例如选自但不仅限于1:0.3:4,1:1:8,1:0.7:6,1:0.8:5等,拌匀,加入占混合物质量0.01-1%硅微粉,例如选自但不仅限于:0.01%,0.05%,0.09%,0.1%,0.5%,0.7%,0.8%,1%等,加水
至混合物料湿润后,挤压成型,挤压成型时,例如采用15mpa的挤压压力挤压而成,得到初坯;
32.(5)将初坯养护,煅烧制备,例如煅烧时选自但不仅限于900℃煅烧10h,采用1000℃煅烧9h,采用1200℃煅烧6h,采用1300℃煅烧7h等,即得。
33.该法充分利用锑尾渣粉制备成粗骨料、细骨料,并利用锑尾渣粉与粗骨料、细骨料拌合成混合物后,补充硅微粉,提高了锑尾渣粉与粗骨料、细骨料之间的胶结强度,增强了抗压强度和耐机械摩擦强度,避免作为内衬材料时出现碰撞、摩擦而出现破裂的现象,提高内衬效果;同时,使得所得耐火材料的荷载软化温度大幅度的提升,达到1600℃以上,提高了耐火材料的耐火性能。
34.在该实施例中,所述的锑尾渣粉过200目筛的筛余≤0.1%,例如可以选自但不仅限于筛余0.1%,0.08%,0.05%,0.01%等。极大程度的使得锑尾渣能够被研磨成更细的粉末,促使锑尾渣粉中的有益成分大量裸露,保障后续胶结成型效果。
35.在该实施例中,所述的锑尾渣粉过400目筛的筛余≤15%,例如可以选自过200目筛的筛余≤0.1%的前提下,将锑尾渣粉过400目时的筛余控制为15%,14%,13%,12%,11%,10%等,能够极大程度降低锑尾渣粉的颗粒粒径,提高锑尾渣粉应用效果。同时也可以直接将锑尾渣粉过400目筛的筛余≤15%的范围内选择,以达到极大程度降低锑尾渣粉的颗粒粒径。
36.在该实施例中,所述的锑尾渣粉过300目筛的筛余>5%,该锑尾渣粉的粒径范围是在锑尾渣粉过400目筛的筛余≤15%的基础上,再过300目筛的筛余>5%,这样能够使得锑尾渣粉颗粒粒径介于200-300目之间具有足够的成分,提高锑尾渣粉的颗粒级配性,保障所得产品的强度。
37.在本发明创造的实施例中,所述的普通硅酸盐水泥为po.42.5。所述的粉煤灰bet表面积介于12-20m2/g。所述的电解铝灰中氧化铝含量≥70%,且中粒径d
50
为0.10-0.22μm。所述的硅微粉中硅含量≥97%。能够极大程度保障耐火材料的抗压强度,提高荷载软化温度,增强耐火性能。
38.本发明创造其他未尽事宜参照现有技术或者本领域技术人员所熟知的公知常识,常规技术手段加以实现,即可。为了能够更好的验证本发明创造的技术效果,本研究者在研究过程中,开展了如下试验研究。
39.在以下实施例中采用的粉煤灰bet表面积介于12m2/g。采用的硅微粉中硅含量98%。采用的普通硅酸盐水泥为po.42.5。采用的电解铝灰中氧化铝含量80%,且中粒径d
50
为0.10μm。
40.实施例1
41.石灰窑用的内衬耐火材料制备方法,包括以下步骤:
42.(1)将锑尾渣送入球磨机中球磨过200目筛,且筛余为0.1%,制成锑尾渣粉;
43.(2)取锑尾渣粉与粉煤灰、普通硅酸盐水泥按照质量比为1:0.2:0.05混合,浇水湿润,制备成粒径介于0.1-0.5cm之间,且d
50
为0.38cm的颗粒,以10℃min升温至900℃恒温煅烧10h,得到粗骨料;
44.(3)取锑尾渣粉与电解铝灰按照质量比为1:1混合,浇水湿润,制备成粒径介于0.01-0.04cm之间,且d
50
为0.02cm的颗粒,以升温速度为50℃升温至900℃恒温煅烧10h,得
到细骨料;
45.(4)取细骨料、粗骨料、锑尾渣粉按照质量比为1:0.3:4混合成混合物,拌匀,加入占混合物质量0.01%硅微粉,加水,拌匀,浇注,以15mpa挤压压力挤压成型,得到初坯;
46.(5)将初坯自然环境下堆存养护5d,以20℃/min的升温速度升温至1000℃恒温煅烧9h制备,即得。
47.对比例1:
48.将实施例1至所得锑尾渣粉与粉煤灰、普通硅酸盐水泥、电解铝灰按照质量比计为6:0.2:0.05:1混合成混合物,拌匀,再加入占混合物质量0.01%硅微粉,加水,拌匀,浇注,以15mpa挤压压力挤压成型,得到初坯;再将初坯自然环境下堆存养护5d,以20℃/min的升温速度升温至1000℃恒温煅烧9h制备,再将初坯自然环境下堆存养护5d,即得。
49.实施例2
50.石灰窑用的内衬耐火材料制备方法,包括以下步骤:
51.(1)将锑尾渣送入球磨机中球磨过200目筛,且筛余为0.08%,制成锑尾渣粉;
52.(2)取锑尾渣粉与粉煤灰、普通硅酸盐水泥按照质量比为1:1:0.1混合,浇水湿润,制备成粒径介于0.1-0.5cm之间,且d
50
为0.35cm的颗粒,以20℃min升温至1000℃恒温煅烧8h,得到粗骨料;
53.(3)取锑尾渣粉与电解铝灰按照质量比为1:3混合,浇水湿润,制备成粒径介于0.01-0.04cm之间,且d
50
为0.03cm的颗粒,以升温速度为40℃升温至1100℃恒温煅烧9h,得到细骨料;
54.(4)取细骨料、粗骨料、锑尾渣粉按照质量比为1:1:9混合成混合物,拌匀,加入占混合物质量1%硅微粉,加水,拌匀,浇注,以15mpa挤压压力挤压成型,得到初坯;
55.(5)将初坯自然环境下养护5d,以30℃/min的升温速度升温至1200℃恒温煅烧7h制备,即得。
56.对比例2:
57.将实施例2至所得锑尾渣粉与粉煤灰、普通硅酸盐水泥、电解铝灰按照质量比计为11:1:0.1:3混合成混合物,拌匀,再加入占混合物质量1%硅微粉,加水,拌匀,浇注,以15mpa挤压压力挤压成型,得到初坯;再将初坯自然环境下养护5d,以30℃/min的升温速度升温至1200℃恒温煅烧7h制备,即得。
58.实施例3
59.石灰窑用的内衬耐火材料制备方法,包括以下步骤:
60.(1)将锑尾渣送入球磨机中球磨过200目筛,且筛余为0.07%,制成锑尾渣粉;
61.(2)取锑尾渣粉与粉煤灰、普通硅酸盐水泥按照质量比为1:0.5:0.07混合,浇水湿润,制备成粒径介于0.1-0.5cm之间,且d
50
为0.27cm的颗粒,以40℃min升温至1200℃恒温煅烧9h,得到粗骨料;
62.(3)取锑尾渣粉与电解铝灰按照质量比为1:2混合,浇水湿润,制备成粒径介于0.01-0.04cm之间,且d
50
为0.03cm的颗粒,以升温速度为30℃升温至1000℃恒温煅烧8h,得到细骨料;
63.(4)取细骨料、粗骨料、锑尾渣粉按照质量比为1:0.9:6混合成混合物,拌匀,加入占混合物质量0.05%硅微粉,加水,拌匀,浇注,以15mpa挤压压力挤压成型,得到初坯;
64.(5)将初坯自然环境下养护5d,以40℃/min的升温速度升温至1100℃恒温煅烧9h制备,即得。
65.对比例3:
66.将实施例3至所得锑尾渣粉与粉煤灰、普通硅酸盐水泥、电解铝灰按照质量比计为8:0.5:0.07:2混合成混合物,拌匀,再加入占混合物质量0.05%硅微粉,加水,拌匀,浇注,以15mpa挤压压力挤压成型,得到初坯;再将初坯自然环境下养护5d,以40℃/min的升温速度升温至1100℃恒温煅烧9h制备,即得。
67.实施例4
68.石灰窑用的内衬耐火材料制备方法,包括以下步骤:
69.(1)将锑尾渣送入球磨机中球磨过200目筛,且筛余为0.1%,制成锑尾渣粉;
70.(2)取锑尾渣粉与粉煤灰、普通硅酸盐水泥按照质量比为1:0.3:0.09混合,浇水湿润,制备成粒径介于0.1-0.5cm之间,且d
50
为0.30cm的颗粒,以50℃min升温至1300℃恒温煅烧7h,得到粗骨料;
71.(3)取锑尾渣粉与电解铝灰按照质量比为1:3混合,浇水湿润,制备成粒径介于0.01-0.04cm之间,且d
50
为0.03cm的颗粒,以升温速度为30℃升温至1200℃恒温煅烧9h,得到细骨料;
72.(4)取细骨料、粗骨料、锑尾渣粉按照质量比为1:0.3:8混合成混合物,拌匀,加入占混合物质量0.09%硅微粉,加水,拌匀,浇注,以15mpa挤压压力挤压成型,得到初坯;
73.(5)将初坯自然环境下养护5d,以50℃/min的升温速度升温至1200℃恒温煅烧8h制备,即得。
74.对比例4:
75.将实施例4至所得锑尾渣粉与粉煤灰、普通硅酸盐水泥、电解铝灰按照质量比计为10:0.3:0.09:3混合成混合物,拌匀,再加入占混合物质量0.09%硅微粉,加水,拌匀,浇注,以15mpa挤压压力挤压成型,得到初坯;再将初坯自然环境下养护5d,以50℃/min的升温速度升温至1200℃恒温煅烧8h制备,即得。
76.将实施例1-4和对比例1-4制备所得的耐火材料进行耐压强度、0.2mpa荷载软化温度、机械磨痕情况测试统计,其结果如下表1所示:
77.表1:各组耐火材料的性能检测表
[0078][0079]
备注:机械磨痕深度是采用钢筋在制备的样品表面来回摩擦3min,测试磨痕摩擦深度情况。
[0080]
在以下实施例中采用的粉煤灰bet表面积介于20m2/g。采用的硅微粉中硅含量98%。采用的普通硅酸盐水泥为po.42.5。采用的电解铝灰中氧化铝含量80%,且中粒径d
50
为0.22μm。
[0081]
实施例5
[0082]
在实施例1的基础上,锑尾渣粉过200目筛的筛余为0.1%,且过400目筛的筛余为15%,其他按照实施例1制备方法制备。
[0083]
实施例6
[0084]
在实施例1的基础上,锑尾渣粉过200目筛的筛余为0.08%,且过400目筛的筛余为8%,其他按照实施例1制备方法制备。
[0085]
实施例7
[0086]
在实施例1基础上,锑尾渣粉过200目筛的筛余为0.09%,且过400目筛的筛余为10%,过300目筛的筛余为6%,其他按照实施例1制备方法制备。
[0087]
实施例8
[0088]
在实施例1的基础上,锑尾渣粉过200目筛的筛余为0.04%,且过400目筛的筛余为12%,过300目筛的筛余为8%,其他按照实施例1制备方法制备。
[0089]
将实施例5-8制备的耐火材料进行耐压强度、0.2mpa荷载软化温度、机械磨痕情况测试统计,其结果如下表2所示:
[0090]
表2实施例5-8制备的耐火材料指标检测结果
[0091][0092]
备注:机械磨痕深度是采用钢筋在制备的样品表面来回摩擦3min,测试磨痕摩擦深度情况。
[0093]
经上述表1,表2数据可知,本发明创造利用锑尾渣经合理的工艺处理之后,使得锑尾渣经颗粒级配之后,增强其力学性能,提高了耐火材料的耐火性能;实现了将锑尾渣应用于石灰窑用耐火材料制备领域,有助于降低锑尾渣堆存,实现锑尾渣变废为宝,同时丰富了石灰窑等类似装置设备用内衬耐火材料的生产原料来源,降低了耐火材料制备成本。
[0094]
以上所述,仅为本发明较佳的具体实施方式,但本发明的保护范围并不局限于此,任何熟悉本技术领域的技术人员在本发明揭露的技术范围内,根据本发明的技术方案及其发明构思加以等同替换或改变,都应涵盖在本发明的保护范围之内。
再多了解一些
本文用于企业家、创业者技术爱好者查询,结果仅供参考。