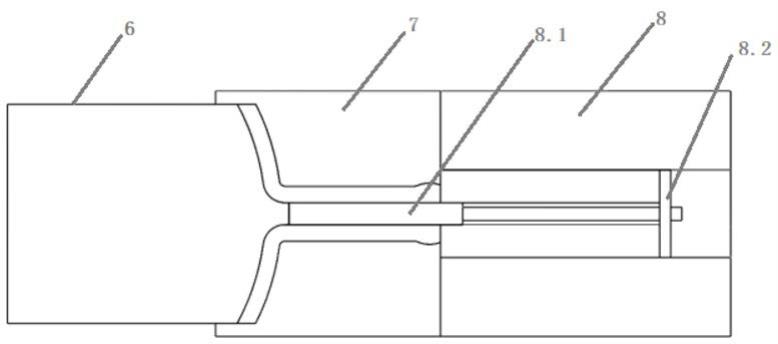
1.本发明属于碳化硅管制备技术领域,特别涉及一种异形半导体管芯非导电保护管的制备方法。
背景技术:
2.半导体管芯的尺寸规格超长和局部结构差异比严重,造成产品细微结构成型缺陷明显,通过尺寸(外形)观察到明显的变径突兀,薄弱环节造成的产品在坯料制作环节废品率过高,通过研究分析发现造成该产品结构失败的原因是脱模管径太长,脱模时局部细微衔接处应力过大,存在严重的成型尺寸不达标的相关问题。
技术实现要素:
3.本发明的目的在于克服现有技术中异形半导体管芯非导电保护管制备过程废品率过高的缺陷,提供一种异形半导体管芯非导电保护管的制备方法。
4.本发明的第一方面,提供了一种粘接剂,各组分及重量配比为:基料70~90%,辅料8~24%,外加剂2~6%;所述基料为碳化硅粉;所述辅料为酚醛树脂或呋喃树脂;所述外加剂为二叔丁基、羟基苄基、硫醚、丙酮的至少一种;进一步的方案为,各组分及重量配比为:基料80%,辅料16%,外加剂4%。
5.进一步的方案为,所述粘接剂的制备方法包括以下步骤:s1:基料拣选,挑选高纯度的碳化硅粉;s2:对步骤1中所得的基料进行破碎、磨粉;粉状碳化硅粒径为0.4μm-1.0μm;s3:将粉状基料、辅料和外加剂依次置入搅拌机,搅拌10~30min,混合均匀得粘接剂。
6.本发明的第二方面,提供了一种异形半导体管芯非导电保护管的制备方法,包括以下步骤:步骤1、将异形半导体管芯非导电保护管分成圆头管、第一导气管、第二导气管、第一直管和第二直管五部分;步骤2、制作圆头管和第一导气管的模具,得到圆头管模具和第一导气管模具;步骤3、利用圆管模具压铸第二导气管、第一直管和第二直管;步骤4、分别利用圆头管模具和第一导气管模具制备圆头管和第一导气管;步骤5、利用上述的粘接剂将圆头管、第一导气管、第二导气管、第一直管和第二直管分别粘接,既得异形半导体管芯非导电保护管。
7.进一步的方案为,所述步骤2中,第一导气管模具包括导气管压铸型腔、型腔包覆臂和复动腔;所述导气管压铸型腔的右端为弧形,所述弧形中心位置开设有空心管;
所述型腔包覆臂包括左侧包覆臂和右侧包覆臂;所述左侧包覆臂和右侧包覆臂的底端通过转轴连接;所述复动腔内部设置有滑动板,所述滑动板向左侧延伸设置有芯棒;使用状态时,导气管压铸型腔嵌入所述型腔包覆臂内部,芯棒穿过空心管内部进入压铸型腔。
8.进一步的方案为,所述步骤2中,圆头管模具包括圆头管压铸型腔和双联动型腔;所述圆头管压铸型腔为u形管状结构,所述u形管状结构右端中心位置设置有第一顶杆,所述u形管状结构的右端一侧设置有第二顶杆;所述双联动型腔内部设置有与所述u形管状结构相适应的u形槽,所述u形槽右端设置有与所述第一顶杆相适应的第一通孔和与所述第二顶杆相适应的第二通孔;使用状态时,圆头管压铸型腔嵌入所述型双联动型腔内部,第一顶杆插入第一通孔,第二顶杆插入第二通孔。
9.进一步的方案为,所述步骤3中,第二导气管、第一直管和第二直管的压铸方法包括:步骤3.1、在实心棒和圆管模具内腔涂抹脱模剂,将实心棒插入圆管模具中,碳化硅粉填充到圆管模具和实心棒的中间;步骤3.2、将模具放到冷等静压机内,加压至10-22mpa,保持50-60min后将模具取下,得到碳化硅管生胚;步骤3.3、将胚放入到高温烧结炉中烧结;取出后冷却,得到碳化硅管毛胚;步骤3.4、将碳化硅管毛胚研磨抛光,得到碳化硅管成品;优选的,所述步骤3.3中,烧结温度为1300℃-1500℃,稳定控温,保温4-6小时。
10.进一步的方案为,所述步骤4中,第一导气管的制备方法包括以下步骤:步骤4.1、在导气管压铸型腔的外壁、型腔包覆臂内壁以及芯棒表面均涂抹脱模剂,将碳化硅粉填充到型腔包覆臂内;步骤4.2、将导气管压铸型腔推入到型腔包覆臂内部,通过滑动板带动芯棒穿过空心管内部进入压铸型腔;步骤4.3、将模具放到冷等静压机内,加压至10-22mpa保持时间为50分钟,芯棒退回,压铸型腔退回;型腔包覆臂左右打开,得到第一导气管生胚;步骤4.4、将第一导气管生胚放入到高温烧结炉中烧结,烧结温度1300℃-1500℃,稳定控温,保温4-6小时;取出后冷却,得到第一导气管毛胚;步骤4.5、将第一导气管毛胚研磨抛光,得到第一导气管。
11.进一步的方案为,所述步骤4中,圆头管的制备方法包括以下步骤:步骤4.11、在圆头管压铸型腔的外壁、双联动型腔的内壁均涂抹脱模剂,将碳化硅粉填充到双联动型腔内;步骤4.22、将圆头管压铸型腔推入到双联动型腔内部,第一顶杆插入第一通孔,第二顶杆插入第二通孔;步骤4.33、将模具放到冷等静压机内,加压至10-22mpa保持时间为50分钟,取下模具,得到圆头管生胚;步骤4.44、将圆头管生胚放入到高温烧结炉中烧结,烧结温度1300℃-1500℃,稳
定控温,保温4-6小时;取出后冷却,得到圆头管毛胚;步骤4.55、将圆头管毛胚研磨抛光,得到圆头管。
12.进一步的方案为,所述步骤5包括以下步骤:步骤5.1、对第二导气管进行切割,将待粘接的一端切至与所述第二顶杆与圆头管压铸型腔的接触端相适应;步骤5.2、先将圆头管1固定,然后使用粘接剂依次粘接第一导气管、第二导气管、第一直管和第二直管;步骤5.3、使用打磨工具将溢流的粘接剂清理干净后静置,进行整体烘烤,烘烤温度为60-100℃,控温2-4小时,即得异形半导体管芯非导电保护管。
13.应当理解的,上述异形半导体管芯非导电保护管的制备方法,仅适用于以下结构的半导体管芯:包括一端为圆头的长直管(类似于试管的形状),在圆头端设置有第一导气管和第二导气管,其中,第二导气管为直管,第一导气管包括弧面个直管两部分,弧面与圆头管相适应;第一导气管和第二导气管均与长直管连通。
14.与现有技术相比,本发明的有益效果在于:本发明提供了一种半导体管芯的生产工艺的改进。从提高产品的合格率,降低产品制造的加工难度和降低产品对生产设备的包容性上,对产品设计中的薄弱环节提高良品率,降低制造风险。
15.本发明通过将异形半导体管芯非导电保护管进行分割,再使用通用型模具制造出坯料,通过专用粘接剂粘结的工艺将分段制造的碳化硅坯料粘接在一起,通过这种方式可以大幅提高产品的制造效率。
附图说明
16.以下附图仅对本发明作示意性的说明和解释,并不用于限定本发明的范围,其中:图1:第一导气管制备模具;图2:圆头管制备模具;图3:第一导气管结构示意图;图4:第二导气管结构示意图;图5:圆头管结构示意图;图6:第一直管和第二直管粘接示意图;图7:第一透气管、第二透气管与圆头管粘接示意图;图8:粘接成型后的异形半导体管芯非导电保护管结构示意图。
具体实施方式
17.为了使本发明的目的、技术方案、设计方法及优点更加清楚明了,以下结合附图通过具体实施例对本发明进一步详细说明。应当理解,此处所描述的具体实施例仅用于解释本发明,并不用于限定本发明。
18.本发明的第一方面,提供了一种粘接剂,各组分及重量配比为:基料70~90%,辅料8~24%,外加剂2~6%;所述基料为碳化硅粉;所述辅料为酚醛树脂或呋喃树脂;
所述外加剂为二叔丁基、羟基苄基、硫醚、丙酮的至少一种;进一步的方案为,各组分及重量配比为:基料80%, 辅料16%,外加剂4%。
19.进一步的方案为,所述粘接剂的制备方法包括以下步骤:s1:基料拣选,挑选高纯度(99.999%)的碳化硅粉;s2:对步骤1中所得的基料进行破碎、磨粉;粉状碳化硅粒径为0.5μm;s3:将粉状基料、辅料和外加剂依次置入搅拌机,搅拌30min,混合均匀得粘接剂。
20.如图1-8所示,本发明的第二方面,提供了一种异形半导体管芯非导电保护管的制备方法,包括以下步骤:步骤1、将异形半导体管芯非导电保护管分成圆头管1、第一导气管2、第二导气管3、第一直管4和第二直管5五部分;步骤2、制作圆头管1和第一导气管2的模具,得到圆头管模具和第一导气管模具;步骤3、利用圆管模具压铸第二导气管3、第一直管4和第二直管5;步骤4、分别利用圆头管模具和第一导气管模具制备圆头管和第一导气管;步骤5、利用上述的粘接剂将圆头管、第一导气管、第二导气管、第一直管和第二直管分别粘接,既得异形半导体管芯非导电保护管。
21.在上述中,如图1所示,所述步骤2中,第一导气管模具包括导气管压铸型腔6、型腔包覆臂7和复动腔8;所述导气管压铸型腔的右端为弧形,所述弧形中心位置开设有空心管;所述型腔包覆臂包括左侧包覆臂和右侧包覆臂;所述左侧包覆臂和右侧包覆臂的底端通过转轴连接;所述复动腔8内部设置有滑动板8.2,所述滑动板8.2向左侧延伸设置有芯棒8.1;使用状态时,导气管压铸型腔6嵌入所述型腔包覆臂7内部,芯棒8.1穿过空心管内部进入压铸型腔。
22.如图2所示,圆头管模具包括圆头管压铸型腔9和双联动型腔10;所述圆头管压铸型腔9为u形管状结构,所述u形管状结构右端中心位置设置有第一顶杆10.1,所述u形管状结构的右端一侧设置有第二顶杆10.2;所述双联动型腔10内部设置有与所述u形管状结构相适应的u形槽10.5,所述u形槽10.5右端设置有与所述第一顶杆10.1相适应的第一通孔10.3和与所述第二顶杆10.2相适应的第二通孔10.4;使用状态时,圆头管压铸型腔9嵌入所述型双联动型腔10内部,第一顶杆10.1插入第一通孔10.3,第二顶杆10.2插入第二通孔10.4。
23.在上述中,所述步骤3中,第二导气管3、第一直管4和第二直管5的压铸方法包括:步骤3.1、在实心棒和圆管模具内腔涂抹脱模剂,将实心棒插入圆管模具中,碳化硅粉填充到圆管模具和实心棒的中间;步骤3.2、将模具放到冷等静压机内,加压至10-22mpa,保持50-60min后将模具取下,得到碳化硅管生胚;步骤3.3、将胚放入到高温烧结炉中烧结;取出后冷却,得到碳化硅管毛胚;步骤3.4、将碳化硅管毛胚研磨抛光,得到碳化硅管成品;在上述中,所述步骤3.3中,烧结温度为1400℃,稳定控温,保温5小时。
24.应当理解的,第二导气管3、第一直管4和第二直管5均为普通圆管,因此,在步骤3中,所使用的圆管模具为本领域的普通圆管模具。
25.在上述中,所述步骤4中,第一导气管2的制备方法包括以下步骤:
步骤4.1、在导气管压铸型腔6的外壁、型腔包覆臂7内壁以及芯棒8.1表面均涂抹脱模剂,将碳化硅粉填充到型腔包覆臂7内;步骤4.2、将导气管压铸型腔6推入到型腔包覆臂7内部,通过滑动板8.2带动芯棒8.1穿过空心管内部进入压铸型腔;步骤4.3、将模具放到冷等静压机内,加压至18mpa保持时间为50分钟,芯棒8.1退回,压铸型腔退回;型腔包覆臂7左右打开,得到第一导气管生胚;步骤4.4、将第一导气管生胚放入到高温烧结炉中烧结,烧结温度1300℃-1500℃,稳定控温,保温4-6小时;取出后冷却,得到第一导气管毛胚;步骤4.5、将第一导气管毛胚研磨抛光,得到第一导气管2。
26.在上述中,所述步骤4中,圆头管1的制备方法包括以下步骤:步骤4.11、在圆头管压铸型腔9的外壁、双联动型腔10的内壁均涂抹脱模剂,将碳化硅粉填充到双联动型腔10内;步骤4.22、将圆头管压铸型腔9推入到双联动型腔10内部,第一顶杆10.1插入第一通孔10.3,第二顶杆10.2插入第二通孔10.4;步骤4.33、将模具放到冷等静压机内,加压至10-22mpa保持时间为50分钟,取下模具,得到圆头管生胚;步骤4.44、将圆头管生胚放入到高温烧结炉中烧结,烧结温度1300℃-1500℃,稳定控温,保温4-6小时;取出后冷却,得到圆头管毛胚;步骤4.55、将圆头管毛胚研磨抛光,得到圆头管1。
27.在上述中,所述步骤5包括以下步骤:步骤5.1、对第二导气管3进行切割,将待粘接的一端切至与所述第二顶杆与圆头管压铸型腔9的接触端相适应;步骤5.2、先将圆头管1固定,然后使用粘接剂依次粘接第一导气管2、第二导气管3、第一直管4和第二直管5;步骤5.3、使用打磨工具将溢流的粘接剂清理干净后静置,进行整体烘烤,烘烤温度为60-100℃,控温2-4小时,即得异形半导体管芯非导电保护管。
28.以上已经描述了本发明的各实施例,上述说明是示例性的,并非穷尽性的,并且也不限于所披露的各实施例。在不偏离所说明的各实施例的范围和精神的情况下,对于本技术领域的普通技术人员来说许多修改和变更都是显而易见的。本文中所用术语的选择,旨在最好地解释各实施例的原理、实际应用或对市场中的技术改进,或者使本技术领域的其它普通技术人员能理解本文披露的各实施例。
再多了解一些
本文用于企业家、创业者技术爱好者查询,结果仅供参考。