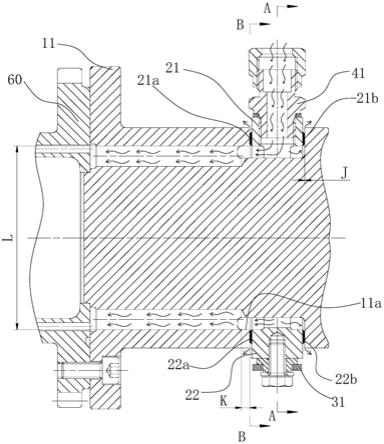
1.本发明涉及一种供油环,特别是用于给工作在高转速下的同步自动离合器供油。
背景技术:
2.同步自动离合器作为机械系统中的连接设备,有着广泛的应用,离合器本身结构复杂,其内部的传扭齿、棘轮棘爪机构必须工作在润滑条件在才能保证长期可靠的运行,由于同步自动离合器的结构特点,棘轮棘爪一般布置的离合器的最内层,供油结构必须能够将润滑油供到棘轮棘爪所在的位置,供油结构若不能将油供至离合器的内部深处,则需要改变离合器棘轮棘爪的位置来适应离合器的供油结构,从而使离合器的径向设计尺寸过大,造成设计浪费,并会对离合器所在轴系的动力学特性造成不利影响。
3.同步自动离合器一般安装在齿轮箱内部或直接串接在设备轴系中,安装在齿轮箱内部时,离合器所在的齿轮箱内部轴系一般存在自由端,此自由端不连接其他设备,可在该轴端的中心位置加工轴向油路孔,孔的一段连接离合器,另一端与供油管连接,这种供油方式可将润滑油供至离合器的最深处。
4.但当离合器直接串接在设备轴系中时,没有自由端安装润滑油管,目前采用图1所示的供油结构,在离合器输入轴的支撑轴承处开设润滑流道,润滑油通过输入轴上的径向油孔进入同步自动离合器,高转速工况时,输入轴处于旋转状态,受离心力的影响,润滑油供入离合器过程中需要克服输入轴油孔中r1至r2段内流体在径向油孔入口处的产生离心压力pω。
5.其中pω=1/2*ρ*(ω/60*2*pi)^2*(r1^2-r2^2)/1000000,式中,
6.r1,进油孔半外径,m
7.r2,进油孔内半径,m
8.ρ,油密度,kg/m^3
9.ω,转速,r/min
10.因此实现离合器供油要求r1处的最小供油压力>pω,转速越高,轴径越大,pω值越高。供油困难的问题限制了同步自动离合器在高转速串接轴系中的应用,亟需解决。
技术实现要素:
11.本发明目的是为了解决现有同步自动离合器在高速串接轴系中供油苦难的问题,提供了一种供油滑环。
12.本发明专利解决其技术问题所采用的技术方案是:
13.本发明专利的有益效果是,对于串接式高转速同步自动离合器,这种供油滑环结构简单,转动件上的流道以轴向流道为主,降低了同步自动离合器对供油压力的要求,使同步自动离合器应用机组的润滑系统更加简单。
附图说明
14.下面结合附图和实施例对本发明专利进一步说明。
15.图1为现有离合器供油结构图;
16.图2为供油滑环的轴向截面图;
17.图3为供油滑环的垂直轴线的剖面图ⅰ(图2中a-a截面);
18.图4为供油滑环的垂直轴线的剖面图ⅱ(图2中b-b截面);
19.图5为去除连接轴后的滑环组件外形图。
20.图中100.滑动轴承,200.输入轴,210.径向油孔,300.同步自动离合器,11.连接轴, 11a.集油环槽,21.滑环基体ⅰ,21a.基体ⅰ铸造合金层ⅰ,21b.基体ⅰ铸造合金层ⅱ,21c. 基体ⅰ铸造合金层ⅲ,22.滑环基体ⅱ,22a.基体ⅱ铸造合金层ⅰ,22b.基体ⅱ铸造合金层ⅱ, 22c.基体ⅱ铸造合金层ⅲ,31.限位杆,32.连接套ⅰ,33.连接套ⅱ,41.供油接头,51.固定架,60.同步自动离合器。
具体实施方式
21.下面结合附图与具体实施方式对本发明作进一步详细描述。
22.图2中,供油滑环包含两部分,滑环组件及滑环安装槽,滑环安装槽位于同步自动离合器 60的连接轴11上,其余零件组成滑环组件。离合器的连接轴(11)上开设环槽和轴向油孔,润滑油从供油接头41供入,流经连接轴11上的润滑油孔,最终进入同步自动离合器60。工作状态下同步自动离合器60及其连接轴11高速转动,会导致流体在连接轴11上的径向流动变得困难,为保证润滑油更够有效供入连接轴11上的轴向油孔,在环槽和轴向油孔的交接处设置有一定宽度的集油环槽11a,集油环槽11a宽度k大于3mm,且集油环槽11a的最大外径尺寸、轴向油孔的径向外侧尺寸、供油滑环内部油槽的径向外侧尺寸均为l,三者保持一致,用以保证滑油的轴向流通。高转速工况下,图2所示结构中连接轴11上的油孔为轴向,相比图1中结构给离合器供油不需要克服pω,图2中给离合器供油所需在直径l处的最小压力p
l>0
即可。
23.图2、图4、图5滑环组件与连接轴11上的环槽存在三个配合面,一个径向配合面,两个轴向配合面,径向配合面d处直径间隙/轴直颈比值为1.5-2
‰
,连接轴11高速运转状态下,连接轴11与滑环径向配合面呈流体动压润滑状态,避免了摩擦面之间的直接接触,提高了滑环组件的使用寿命。轴向配合j处间隙典型值为0.1-0.3mm,工作间隙用于满足工作面的润滑需求,避免连接轴11高速旋转时造成配合面损坏,同时间隙不宜过大,以免造成润滑油通过间隙的泄漏量过大,其中滑环基体21上的基体ⅰ铸造合金层ⅰ21a、基体ⅱ铸造合金层ⅱ22b、基体ⅰ铸造合金层ⅲ21c,滑环基体22上的基体ⅱ铸造合金层ⅰ22a、基体ⅱ铸造合金层ⅱ22b、基体ⅱ铸造合金层ⅲ22c采用铸造锡青铜材料或其他减摩材料,减摩材料可以提高滑环组件与连接轴11接触面的磨合性,减小接触面的摩擦及磨损,提高滑环的使用寿命。配合面通过供油接头供入的滑油进行润滑。在滑环基体ⅰ21和滑环基体ⅱ22在供油滑环的内部开设有4-8处圆周均布的流道,流道截面形状为圆弧形,其中一个流道与供油接头41的油路连通,流道用于保证配合面得到有效润滑以及足够的润滑油进入轴向油孔。
24.图4、图5中,滑环组件采用中分面剖分式机构,滑环基体ⅰ21与滑环基体ⅱ22通过螺栓和定位销连接,滑环组件外侧上设置有供油接头41和限位结构,限位结构通过限位杆
31 实现,限位杆31一侧通过间隙配合套在连接套ⅰ32上,通过螺栓连接将连接套ⅰ32固定在滑环基体ⅱ22上,限位杆31另一侧通过间隙配合套在连接套ⅱ33上,通过螺栓连接将连接套ⅱ33固定在固定架51上,限位杆31与连接套ⅰ32、限位杆31与连接套ⅱ33在h处的间隙大于1mm,使限位杆31能起到滑环转动,但不承担供油滑环质量,供油滑环质量由连接轴11承担,避免滑环出现过定位的情况,使滑环对连接轴11产生过大的附加力。
25.本发明包含滑环本体、滑环安装槽、限位结构等部分构成,其特征是滑环安装槽位于同步自动离合的连接轴上,连接轴上开设轴向油孔,通过集油环槽与滑环安装槽连通,滑环本体浮动安装在滑环安装槽内,通过外部限位机构限制滑环本体随连接轴转动。在环槽和轴向油孔的交接处设置有一定深度的集油环槽,集油环槽深度大于3mm,且集油环槽的最大外径尺寸、轴向油孔的径向外侧尺寸、滑环组件内部油槽的径向外侧尺寸三者保持一致,用以保证滑油的轴向有效流通。供油滑环与连接轴上的滑环安装槽存在三个配合面,一个径向配合面,两个轴向配合面,径向配合面处直径间隙/轴直颈比值为1.5-2
‰
,轴向配合间隙典型值 0.1-0.3mm,其中供油滑环侧的工作面材料为锡青铜或其他减摩材料。在供油滑环的内部开设有4-8处圆周均布的流道,流道截面形状为圆弧形,其中一个流道与供油接头的油路连通。限位结构通过限位杆实现,限位杆两侧分别连接供油滑环和离合器所在箱体,限位杆与供油滑环和离合器所在箱体的连接副间存在一定的安装间隙,使限位杆能能起到限制供油滑环转动,但不限制承担供油滑环质量,使供油滑环处于浮动状态,滑环质量由连接轴承担。
26.一种适用于高转速的同步自动离合器供油滑环。其由供油滑环和滑环安装槽两部分构成,滑环安装槽位于同步自动离合的连接轴上,连接轴上开设轴向油孔,通过一定宽度的集油环槽与滑环安装槽连通,滑环组件采用剖分式结构,滑环组件外侧上设置有供油接头和限位结构,其与滑环安装槽配合部分的表面浇铸有锡青铜材料,滑环内表面开设均布的轴向流道用于润滑配合表面,滑环组件浮动安装在滑环安装槽内,并通过与固定架连接的限位杆限制浮动滑环跟随转动的连接轴转动。本发明专利适用于串接在机组轴系中的高转速同步自动离合器,这种供油滑环结构简单,转动连接轴上的流道以轴向流道为主,降低了同步自动离合器对供油压力的要求,使机组的润滑系统更加简单。
再多了解一些
本文用于企业家、创业者技术爱好者查询,结果仅供参考。