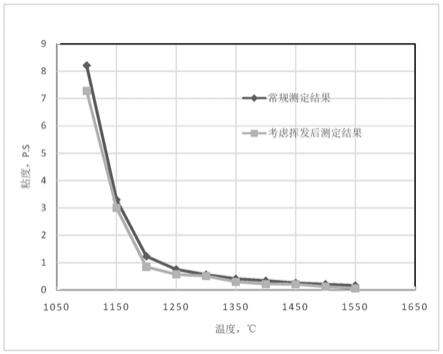
1.本发明属于冶金工程技术领域,具体涉及一种含易挥发组元炉渣挥发对粘度影响的评价方法。
背景技术:
2.我国钢铁和有色金属生产大国,2020年的钢产量达到了10.53亿吨,有色金属铅产量达到664.3万吨,锌产量达到642.5万吨。这些大宗金属的生产主要采用火法冶金,而对火法冶金过程,熔体的组成、物化性能不仅是冶金工艺控制的重要依据,也是后续利用的关键基础数据。以冶金炉渣为例,其成分及物理化学性能对熔炼过程的温度控制、界面反应特性、夹杂物去除、甚至是熔炼过程顺行均息息相关。炉渣性能主要包括熔点、粘度、结晶性能和表面张力等,其中粘度是性能控制中的关键参数之一,反映着炉渣的流动性能和动力学反应性能。
3.为保证炉渣性能,经常需要添加一些具有挥发性的熔剂,如黑色金属冶炼过程尤以含氟炉渣、含钾钠氧化物炉渣等;也有部分炉渣中本身就带有挥发性组元,如有色金属冶炼过程中的铅锌冶炼炉渣等。
4.在利用传统方法进行粘度测定时,升温和保温往往需要数个小时,也就是说需要在高温下停留较长时间,造成炉渣中的易挥发组元的大量挥发,部分炉渣中的氟化物挥发量可达30%以上;铅及其化合物的挥发量可达40%以上,这种挥发量对炉渣成分及性能的影响是很大的,导致炉渣粘度测定结果会出现较大偏差。这类问题在含易挥发组元渣性能测定中普遍存在,也就是说现行的粘度测定方法已经不适合挥发性影响较大的炉渣的粘度测定,而目前尚缺乏就挥发对炉渣粘度影响的评价及有效的解决办法。
5.因为未考虑测定过程的挥发而会出现很大偏差,导致部分冶炼过程缺乏准确的炉渣基础性能参数,其冶炼条件的确定仍然要靠经验确定,严重制约着进一步的工艺优化和新工艺开发,如直接炼铅工艺中炉渣中铅含量会经历60%左右逐步降低到1%左右的炉渣性能参数。
6.为此,如何对火法冶金用含易挥发组元炉渣中挥发的影响进行评价,进而获得更准确的粘度值具有重要的理论意义和实际应用价值。
技术实现要素:
7.本发明的目的在于提供一种含易挥发组元炉渣挥发对粘度影响的评价方法,以解决火法冶金过程中使用含易挥发组元炉渣导致粘度测定不准确技术问题,从而获得更加准确的粘度值,为涉及含有易挥发组元炉渣的火法冶金工艺控制及优化提供支撑。
8.为实现上述目的,本发明采用如下技术方案:
9.一种含易挥发组元炉渣挥发对粘度影响的评价方法,包括以下步骤:
10.保持挥发性炉渣比例不变以传统方法测定挥发性炉渣的粘度与温度关系;
11.测定不同温度下对应的炉渣粘度及炉渣成分;
12.将多组初始比例相同的炉渣在不同温度下对应的炉渣粘度及炉渣成分进行多元回归分析,得到实际的炉渣成分、粘度和温度的对应关系;
13.基于实际的炉渣成分、粘度和温度的对应关系,与保持挥发性炉渣比例不变以传统方法测定挥发性炉渣的粘度与温度关系进行比较,在初始炉渣成分相同的情况下二者相同温度下不同粘度的差值为挥发性炉渣挥发对炉渣粘度的影响。
14.本发明的进一步改进在于:所述传统方法为旋转柱体测定法。
15.本发明的进一步改进在于:所述测定不同温度下对应的炉渣粘度及炉渣成分采用热重分析或烧渣试验。
16.本发明的进一步改进在于:采用热重分析测定不同温度下对应的炉渣粘度及炉渣成分,具体包括以下步骤:
17.在相同条件下对热重及挥发物连续检测得到炉渣的tg曲线和炉渣挥发物气体分子强度随时间变化曲线;
18.根据炉渣的tg曲线和炉渣挥发物气体分子强度随时间变化曲线建立挥发反应动力学模型;
19.将tg曲线与挥发反应动力学模型进行拟合得到温度对应粘度与该粘度下炉渣实际成分。
20.本发明的进一步改进在于:采用烧渣试验测定不同温度下的炉渣粘度及炉渣成分,具体包括以下步骤:
21.在相同条件下设置若干反应炉;
22.选择若干温度对应粘度测定节点,在每个节点从一个反应炉中取出待测炉渣;
23.对待测炉渣进行急冷和化学分析得到该温度对应粘度测定节点的炉渣成分。
24.本发明的进一步改进在于:所述相同条件包括相同的原料,配制相同的炉渣,依照粘度测定过程的气氛、升温速率、保持温度和保温时间。
25.本发明的进一步改进在于:采用烧渣试验测定不同温度下的炉渣粘度及炉渣成分时,采用的反应炉数量大于等于5个。
26.本发明的进一步改进在于:测定炉渣的数据样本量有限时,基于同一炉渣试样,在同一温度,不同保温时间下进行粘度测定,测定的保温时间点大于等于4个,根据挥发情况对粘度的影响进行评价;测试粘度前后进行对炉渣进行失重测定,进而基于挥发情况对粘度的影响,对测定的粘度值进行修正,通过外推,得到失重量为零时对应的粘度值。
27.本发明的进一步改进在于:所有粘度测定前后都对待测炉渣进行称重,采用炉渣、坩埚或测定用旋转柱体总重推算的方法。
28.与现有技术相比,本发明至少包括以下有益效果:
29.1、充分考虑炉渣挥发组元对炉渣粘度的影响,获得更准确的粘度值,实现对炉渣挥发性的影响测定与评价。
30.2、可以利用现行的火法冶金用含易挥发组元炉渣粘度测定装置及测定方法,可以最大限度地利用已有的相关测定结果。
31.3、基于同一炉渣试样,在同一温度,不同保温时间下进行粘度测定,使炉渣的样本量不足时能够获得准确的粘度值。
附图说明
32.构成本发明的一部分的说明书附图用来提供对本发明的进一步理解,本发明的示意性实施例及其说明用于解释本发明,并不构成对本发明的不当限定。在附图中:
33.图1为含氟炉渣炼钢时通过常规粘度测定方法获得的表观粘度与温度关系图;
34.图2为使用含氟炉渣炼钢时不同温度对应的炉渣焙烧成分变化图;
35.图3为测定的含氟炉渣tg曲线图;
36.图4为含氟炉渣高温质谱测定挥发物气体分子强度随时间变化曲线图;
37.图5为含氟炉渣挥发对炉渣成分影响的动力学模型与tg曲线拟合情况;
38.图6为挥发对炼钢用含氟炉渣粘度影响评价及理论粘度值测算示意图;
39.图7为炼钢用含氟炉渣小样本量条件下的挥发影响及理论粘度值测算示意图;
40.图8为炼铅过程中含铅炉渣通过常规粘度测定方法获得的表观粘度与温度关系图;
41.图9为炼铅过程中含铅炉渣不同温度对应的炉渣焙烧成分变化图;
42.图10为测定的含铅炉渣tg曲线图;
43.图11为含铅炉渣高温质谱测定挥发物气体分子强度随时间变化曲线图;
44.图12为含铅炉渣挥发对炉渣成分影响的动力学模型与tg曲线拟合情况;
45.图13为挥发对含铅炉渣粘度影响评价及理论粘度值测算示意图;
46.图14为含铅炉渣小样本条件下的会发影响及理论粘度值测算示意图。
具体实施方式
47.下面将参考附图并结合实施例来详细说明本发明。需要说明的是,在不冲突的情况下,本发明中的实施例及实施例中的特征可以相互组合。
48.以下详细说明均是示例性的说明,旨在对本发明提供进一步的详细说明。除非另有指明,本发明所采用的所有技术术语与本发明所属领域的一般技术人员的通常理解的含义相同。本发明所使用的术语仅是为了描述具体实施方式,而并非意图限制根据本发明的示例性实施方式。
49.本发明一种含易挥发组元炉渣挥发对粘度影响的评价方法,包括:
50.以炼钢用含氟炉渣的相关测定数据为例进行说明,其中氟化物为挥发组元,其它挥发性炉渣的实施方案与此类似。
51.测定方法及数据提取:粘度测定仍然采用传统的旋转柱体测定法,可得到η-t关系图,可称为挥发性炉渣的表观粘度与温度关系,如图1所示。在进行粘度测定的同时,进行炉渣试样相同条件下的热重或烧样试验,即与粘度测定时的升温、保温、气氛等条件一致情况下的热重和挥发机制研究或烧样,以取得不同温度及保持时间的炉渣适时成分,以此适时成分与瞬时粘度对应,如图2所示。如图1中常规旋转柱体法测定炉渣粘度在t1点即1200℃,测得的粘度值为1.51pa
·
s,这一粘度对应的适时炉渣成分应该为图2中1200℃对应的炉渣成分,而不是炉渣的初始成分。同理,可提取其它不同温度点对应的炉渣粘度及炉渣成分。
52.热重和挥发机制包括:采用相同的原料,配制相同的炉渣,依照粘度测定过程的气氛、升温速率、保持温度、保温时间,通过对热重及挥发物连续检测,如图3-4所示,可建立挥发反应动力学模型,如图5所示,进而和挥发物检测结合,可测算得到粘度测定对应瞬时时
间的炉渣实际组成,因为炉渣在加热及保温过程会持续挥发,导致炉渣成分变化,进而引起粘度的变化。以此瞬时炉渣成分与瞬时测定的炉渣粘度对应将更加符合实际。因此,当温度发生变化时,测定得到的将是不同炉渣成分的渣子,因挥发成分发生变化的渣子,与不同温度条件下的粘度值。而传统的方法是认为炉渣成分由配渣决定,配好后就一成不变,得到的η-t关系是初始确定组成的炉渣的粘度随温度变化关系。
53.烧渣试验步骤包括:采用相同的原料,配制相同的炉渣,依照粘度测定过程的气氛、升温速率、保持温度、保温时间,利用其它炉子模拟粘度测定过程的炉渣反应,在对应的粘度测定节点,将炉渣试样取出急冷、化学分析,得到瞬时的炉渣化学组成,如图2所示,以便与适时的粘度测定值对应。为了全程模拟炉渣的反应状态,需要同时焙烧多个试样,一般应不少于5个,在不同的对应时间节点取出分析。焙烧试样越多,分析得到的粘度测定过程炉渣成分变化规律越准确。
54.测定数据的处理:传统方法认为炉渣性能不变,可直接测定得到炉渣表观粘度与温度的对应关系,即η-t关系。本实施例提出炉渣由于挥发炉渣成分将处于不断的变化之中,因此不同温度下测定的粘度将对应不同的炉渣成分值。以同类炉渣不同原始试样(炉渣体系)的测定结果进行多元回归分析,可得到更加符合实际的炉渣成分、粘度和温度的对应关系。
55.挥发影响的评价及粘度值求取:基于回归分析结果,测算与初始炉渣成分相同的炉渣在不同温度的η-t关系,并与常规方法测定的η-t关系比较,二者的差值就是挥发的影响,据此可对挥发的影响进行评价,如图6所示,可以看出,任一温度下,挥发利用本方法测得的粘度值都低于常规方法,说明挥发物的挥发导致了炉渣粘度测定值的升高。
56.如果测定的数据样本量有限,可以直接基于同一原始渣样、在同一温度下、不同保温时间的粘度测定,就挥发对粘度的影响进行评价。测定的保温时间应取4个点以上,测试前后进行失重测定。进而基于对挥发影响的估算,对测定的粘度值进行修正,通过外推,得到失重量为零的点对应的粘度值,即为粘度测定的近似理论粘度值,如图7所示,可以看出外推到失重为零时,即b点对应的粘度外推值为1.40pa
·
s。
57.对挥发量的评价:所有粘度测定前后进行炉渣试样称重,可以利用炉渣、坩埚、测定用旋转柱体总重推算,可以估算炉渣中挥发组元的含量变化,进而为挥发影响机制研究及挥发影响评价提供依据。
58.对挥发性较强的冶金炉渣,应适当提高升温速率,减少保温时间,并采用预熔渣等措施有利于获得更接近熔点“真值”的炉渣粘度测定值。
59.实施例2
60.电渣重熔用渣粘度测定过程数据提取及挥发影响评价
61.基本情况:
62.电渣重熔用渣的原始组成如表1所示。
63.表1电渣成分
64.组成al2o3mgosio2caf2cao含量/%29.332.579.1530.1228.83
65.按照常规粘度测定方法,可得到炉渣粘度与温度的关系如图1所示。另经测定,该炉渣在粘度测定过程的高温失重,高温为800℃以上的失重可达8.2%。
66.应用方式:
67.采用常规粘度测定的气氛、升温速率和保温时间,进行炉渣焙烧试验,得到过程的炉渣成分变化如图2所示,进而将挥发引起的适时成分变化和测得的粘度值耦合,得到粘度和炉渣成分关系。采用常规方法测得温度1200℃时粘度为1.51pa
·
s,即认为是表1中所示的炉渣在1200℃的粘度;利用实施例1的方法,得到挥发后的该适时炉渣成分如表2所示,以此炉渣成分与测得的粘度值耦合对应,也就是说1.51pa
·
s是这个新炉渣成分1200℃的粘度值,而不是表1中炉渣对应的粘度值。
68.表2挥发后电渣成分
[0069][0070][0071]
结果评价与分析:
[0072]
由于挥发引起的炉渣成分变化较大,利用实施例1所述方法得到的炉渣粘度值已与常规测定方法测定值已有明显差异。可以预测,表1中的炉渣caf2含量明显高于挥发后的炉渣成分,其粘度应明显低于1.51pa
·
s。也就是说常规测定方法测定的粘度值明显偏高,实施例1中所述方法的到的炉渣粘度值应低于常规测定法测定值。
[0073]
实施例3
[0074]
一种铁水预处理渣粘度测定过程数据提取及挥发影响评价
[0075]
基本情况:
[0076]
炼钢炉渣成分如表3所示。
[0077]
表3含氟炼钢炉渣成分(质量分数)
[0078]
组成caf2al2o3mgosio2caona2co3含量17.63.83.027.227.221.2
[0079]
按照常规粘度测定方法,可得到粘度与温度的关系如图6中所示曲线。另经测定,该渣在粘度测定过程的高温失重(800℃以上的失重)可达11.6%。
[0080]
应用方式:
[0081]
采用常规粘度测定的气氛、升温速率和保温时间,进行炉渣焙烧试验,得到过程的炉渣成分变化如图2所示,进而将挥发引起的适时成分变化和测得的粘度值耦合,得到表所示的粘度和炉渣成分关系。进一步对该渣系碱度和氧化镁含量不变的情况下,其它组元含量变化对粘度的影响采用上述方法进行了系统的测定,并经回归得到了粘度—炉渣成分—温度的对应关系。
[0082]
应用结果:
[0083]
基于得到的粘度—炉渣成分—温度的对应关系,计算得到炼钢炉渣的粘度随温度变化曲线如图3所示。两条曲线之间的区域就是挥发影响区,两条曲线间的垂直距离可以反映在同一温度下,挥发对粘度测定值的影响。取1200℃和1400℃,常规测定法测得的粘度值分别为1.23pa
·
s和0.34pa
·
s;而本发明方法测得的粘度值分别为0.84pa
·
s和0.22pa
·
s。本发明测定明显低于常规测定结果就,符合挥发使得粘度升高规律。随着温度的升高,差
别不断减小,但其影响仍然较大。
[0084]
实施例4
[0085]
高氟电渣重熔渣粘度测定过程数据提取及挥发影响评价
[0086]
基本情况:
[0087]
基于基础研究,已经得到高氟电渣重熔用渣的挥发动力学模型如图5所示,现在拟对炉渣成分如表4所示的高氟渣提取其适时炉渣成分变化,以便与测定的粘度-温度关系曲线耦合提取新炉渣成分-温度-粘度的对应数据。
[0088]
表4高氟炉渣成分(质量分数)
[0089]
组成caf2al2o3mgosio2cao含量502496.510.5
[0090]
应用方式:
[0091]
利用动力学模型可以预测某时刻/温度的炉渣失重量。另据高温质谱测定结果,如图4所示),炉渣的主要挥发组元是caf2、mgf2,按照质谱测定结果,可以得到两种挥发物的挥发质量之比即caf2:mgf2=2:1,与测算得到的失重对应,可以折算炉渣的适时成分变化。
[0092]
应用结果:
[0093]
利用得到的适时成分变化,可与常规粘度测定结果耦合,得到新炉渣成分-温度-粘度的对应。
[0094]
实施例5
[0095]
anf-6渣粘度测定过程数据提取及挥发影响评价
[0096]
基本情况:
[0097]
拟对炉渣质量组成为70%caf2-30%al2o3的高氟渣,拟评价在1500℃炉渣挥发对粘度测定结果的影响,常规测定方法测定的粘度值为,表观粘度值0.21pa
·
s。
[0098]
应用方式:
[0099]
基于热重测定,挥发主要发生在高温条件下,可近似按照线型关系处理。在1500℃连续测定了4个不同保温时间的粘度,并依照挥发动力学模型,测算得到炉渣在不同保温时间对应的炉渣重量变化,过程中温度在800℃以上,外推可得到失重为零的对应点b,再以不同保温时间测得的粘度测定结果外推,与失重为零的点对应的粘度外推值a点即为更接近理论粘度值的粘度值0.14pa
·
s。
[0100]
应用结果:
[0101]
可以看出,二者的差值可达0.07pa
·
s,差别可达33%。利用本发明测定值符合挥发组元挥发导致测定常规方法测定结果粘度偏高的基本判断,与利用实例3的方法的理论粘度推算值基本一致,也就是说本实例外推得到的粘度值0.14pa
·
s更接近理论粘度值。
[0102]
实施例6
[0103]
中铅渣粘度测定过程数据提取及挥发影响评价
[0104]
基本情况:
[0105]
铅直接还原中的中等含量含铅渣原始组成如表5所示。
[0106]
表5中等含量含铅渣的成分,wt%
[0107]
组成pboznocaofeosio2含量20.0010.0012.3537.0620.59
[0108]
按照常规粘度测定方法,可得到粘度与温度的关系如图8所示。另经测定,该渣在粘度测定过程的高温失重,即800℃以上的失重可达18.58%。
[0109]
应用方式:
[0110]
采用常规粘度测定的气氛、升温速率和保温时间,进行含铅渣焙烧试验,得到过程的含铅渣成分变化如图9所示,进而将挥发引起的适时成分变化和测得的粘度值耦合,得到粘度和含铅渣组成关系。采用常规方法测得温度1200℃时粘度为0.22pa
·
s,即认为是表5中所示的含铅渣在1200℃的粘度;得到该适时含铅渣成分挥发后如表6所示,以此含铅渣成分与测得的粘度值耦合对应,也就是说0.22pa
·
s是这个新含铅渣组成1200℃的粘度值,而不是表5中含铅渣的粘度值。
[0111]
表6挥发后中等含量含铅渣的成分,wt%
[0112]
组成pboznocaofeosio2含量7.46.5615.1845.5525.31
[0113]
结果评价与分析:
[0114]
由于挥发引起的含铅渣成分变化较大,利用本发明得到的含铅渣粘度值已与常规测定方法测定值已有明显差异。可以预测,表5中的含铅渣pbo含量明显高于表6的含铅渣组成,其粘度应明显低于0.22pa
·
s。也就是说常规测定方法测定的粘度值明显偏高,粘度的理论粘度值应低于常规测定法测定值。
[0115]
实施例7一种中铅渣粘度测定过程数据提取
[0116]
基本情况
[0117]
基于基础研究,已经得到某中铅渣的挥发动力学模型如图12所示,拟对含铅渣组成如表7所示的铅渣提取其适时含铅渣组成变化,以便与测定的粘度-温度关系曲线耦合提取新含铅渣组成-温度-粘度的对应数据。
[0118]
表7中铅含量炉渣的成分,wt%
[0119]
组成pboznocaofeosio2含量201012.3537.0620.59
[0120]
应用方式:
[0121]
利用如图10所示的动力学模型可以预测某时刻/温度的含铅渣失重量。另据高温质谱测定结果如图11所示,含铅渣的主要挥发组元是pbo、zno,按照质谱测定结果,可以得到两种挥发物的挥发质量之比即pbo:zno=3:1,与测算得到的失重对应,可以折算含铅渣的适时成分变化。
[0122]
应用结果:
[0123]
利用得到的适时成分变化,可与常规粘度测定结果耦合,结果如图13所示,得到新含铅渣组成-温度-粘度的对应关系。
[0124]
实施例8含铅渣粘度测定过程数据修正及挥发影响评价
[0125]
基本情况:
[0126]
拟评价含铅渣组成如表7所示的中铅渣在1050℃含铅渣挥发对粘度测定结果的影响,常规测定方法测定的表观粘度值为3.02pa
·
s。
[0127]
应用方式:
[0128]
基于热重测定,挥发主要发生在高温条件下。如图14所示按照本发明小样本量处
置方法,在1050℃连续测定了7个不同保温时间的粘度,并依照挥发动力学模型,测算得到含铅渣在不同保温时间对应的含铅渣重量变化,皆为800℃以上,外推可得到失重为零的对应b点,再以不同保温时间测得的粘度测定结果外推,与失重为零的点对应的粘度外推值a点即为更接近理论粘度值的粘度值2.80pa
·
s。
[0129]
应用结果:
[0130]
可以看出,二者的差值可达0.22pa
·
s,差别可达8%。利用本发明测定值符合挥发组元挥发导致测定常规方法测定结果粘度偏高的基本判断,与利用实例3的方法的推算值2.75pa
·
s基本一致,也就是说本实例外推得到的粘度值2.80pa
·
s更接近理论粘度值。
[0131]
由技术常识可知,本发明可以通过其它的不脱离其精神实质或必要特征的实施方案来实现。因此,上述公开的实施方案,就各方面而言,都只是举例说明,并不是仅有的。所有在本发明范围内或在等同于本发明的范围内的改变均被本发明包含。
[0132]
最后应当说明的是:以上实施例仅用以说明本发明的技术方案而非对其限制,尽管参照上述实施例对本发明进行了详细的说明,所属领域的普通技术人员应当理解:依然可以对本发明的具体实施方式进行修改或者等同替换,而未脱离本发明精神和范围的任何修改或者等同替换,其均应涵盖在本发明的权利要求保护范围之内。
再多了解一些
本文用于企业家、创业者技术爱好者查询,结果仅供参考。