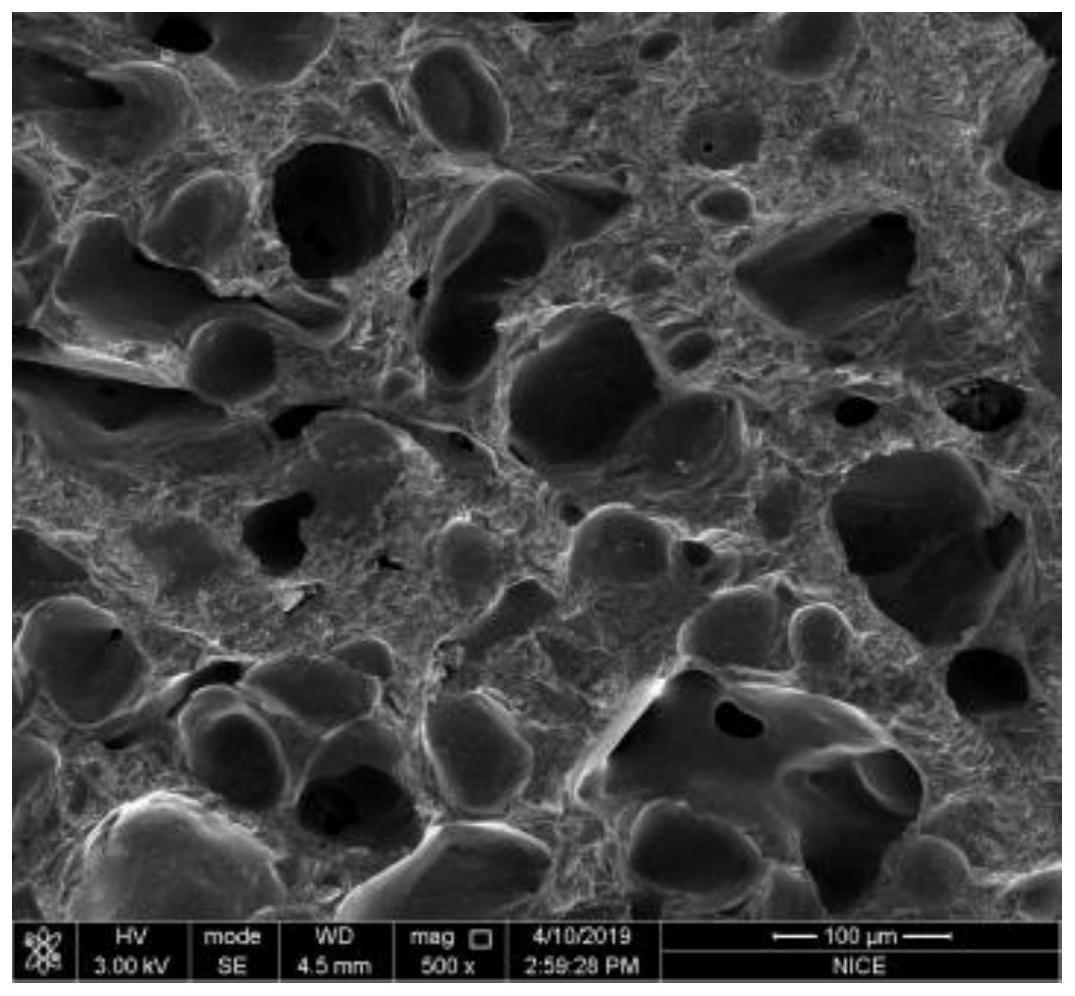
1.本发明涉及炭材料技术领域,具体涉及一种泡沫炭材料及其制备方法。
背景技术:
2.泡沫炭是由孔泡和相互连接的孔泡壁组成的具有三维网状结构的轻质多孔材料,由于结构的独特性,泡沫炭在声学、电学及热学等领域具有特殊的性能。近年来,炭泡沫材料的研究在国内外得到高度关注。
3.cn106698415a公开了一种高强度炭泡沫材料及其制备方法,该方法以糖类物质为碳源材料,与水凝胶剂材料溶于水中,得到混合液;向得到的混合液中加入发泡剂,在惰性气体保护下发泡得到发泡体,然后将发泡体凝胶固化,得到泡沫凝胶体;将得到的泡沫凝胶体进行碳化处理,得到炭泡沫材料。但该制备方法需要加入发泡剂,且发泡和炭化操作不连续,增加了工艺复杂度。
4.cn108584909a公开了一种采用改性沥青制备高强度泡沫炭的方法,该方法包括煤沥青的改性处理,改性沥青制备中间相沥青,中间相沥青发泡以及炭化步骤;本发明可以通过硼酸和苯丙烯醛对煤沥青进行改性,调节煤沥青的软化点、残炭率、甲苯不溶物用量和喹啉不溶物用量等性质,从而对中间相沥青的性质和结构进行有效调控;可以通过对泡孔结构的调节,获得高强度泡沫炭。但该制备方法采用高温高压的反应条件,对设备要求高,操作复杂,存在安全隐患。
5.cn108584942a公开了一种石墨烯泡沫炭复合材料的制备方法,该方法包括通过超声分散使石墨烯和泡沫炭前驱体混合均匀,然后再进行发泡、炭化和石墨化,实现石墨烯在泡沫炭基体中的均匀分散,从而获得具有优良综合性能的泡沫炭复合材料。但该制备方法中发泡和炭化操作不连续,增加了工艺复杂度。
6.因此,有必要提供一种新的泡沫炭材料的制备方法。
技术实现要素:
7.本发明的目的是为了解决现有制备泡沫炭的方法中存在的高温高压对设备要求高,且不能实现发泡和炭化连续操作的问题,提供了一种泡沫炭材料及其制备方法,该方法对设备要求低,安全性能好,并且发泡和炭化可连续进行,工艺简单。
8.为了实现上述目的,本发明第一方面提供了一种泡沫炭材料的制备方法,该方法包括:
9.(1)将沥青与树脂、导热添加剂混合,得到的混合物进行固化处理;
10.(2)在惰性气体下,将步骤(1)得到的产物进行热处理,得到泡沫炭材料。
11.本发明第二方面提供了一种由本发明第一方面所述的制备方法制得的泡沫炭材料,所述泡沫炭材料的孔隙率为60-95%,压缩强度为10-40mpa,热导率为5-150w/mk,无定型炭峰与石墨峰的峰值比为10-90%。
12.通过上述技术方案,本发明通过将沥青与树脂、导热添加剂混合后进行固化处理,
然后在高温常压下发泡、炭化能够制备得到导热性能好、压缩强度高的泡沫炭材料,且该方法对设备要求低,安全性能好,发泡和炭化可连续进行,简化工艺流程。
附图说明
13.图1为本发明实施例8制备得到的泡沫炭材料的sem图。
14.图2为本发明实施例8制备得到的泡沫炭材料的xrd图。
15.图3为本发明实施例8制备得到的泡沫炭材料的xrd图谱分峰图。
具体实施方式
16.在本文中所披露的范围的端点和任何值都不限于该精确的范围或值,这些范围或值应当理解为包含接近这些范围或值的值。对于数值范围来说,各个范围的端点值之间、各个范围的端点值和单独的点值之间,以及单独的点值之间可以彼此组合而得到一个或多个新的数值范围,这些数值范围应被视为在本文中具体公开。
17.传统泡沫炭材料的制备工艺中,多采用高温高压或添加发泡剂等方法制备泡沫炭,即原料在高温高压(例如3mpa)环境中发泡得到泡沫炭生料,然后将泡沫炭生料炭化得到泡沫炭。高温高压对设备要求高,操作复杂,存在安全隐患,且上述方法不能实现发泡和炭化连续操作,增加了工艺复杂度。为了解决上述问题,本发明的发明人在研究中发现,通过将沥青与树脂、导热添加剂混合后进行固化处理,然后在高温常压下发泡、炭化的制备工艺能够获得导热性能好、压缩强度高的泡沫炭材料,该方法对设备要求低,安全性能好,且发泡和炭化可连续进行,简化工艺流程。
18.如前所述,本发明第一方面提供了一种泡沫炭材料的制备方法,该方法包括:
19.(1)将沥青与树脂、导热添加剂混合,得到的混合物进行固化处理;
20.(2)在惰性气体下,将步骤(1)得到的产物进行热处理,得到泡沫炭材料。
21.在本发明的一些实施例中,为了更好的使反应原料混合均匀,可将沥青粉碎、筛分得到50-600目的颗粒,优选地,将沥青粉碎、筛分得到100-300目的颗粒。本发明对所述粉碎、筛分的方式没有特别的限定,可以采用任何现有的粉碎、筛分方式。
22.在本发明的一些实施例中,优选地,步骤(1)中,所述沥青与树脂、导热添加剂的重量百分比为(10-80):(20-90):(0-20)。更优选情况下,所述沥青与树脂、导热添加剂的重量百分比为(30-60):(40-70):(0-10),这样有利于获得压缩强度更高、导热性能更好的泡沫炭材料。
23.在本发明的一些实施例中,为了提高泡沫炭材料的导热性能,优选地,所述树脂的含碳量为30-60wt%,所述树脂在900℃下的残炭含量为5-20wt%。更优选情况下,所述树脂的含碳量为30-45wt%,所述树脂在900℃下的残炭含量为5-10wt%,用于进一步提高泡沫炭材料的导热性能。
24.在本发明的一些实施例中,可以通过添加树脂辅助泡沫炭成型,优选地,所述树脂选自聚氯乙烯、聚苯乙烯、聚偏氟乙烯、聚丙烯、聚乙烯、环氧树脂、聚碳酸酯、聚酰胺、酚醛树脂和不饱和树脂中的至少一种。
25.在本发明的一些实施例中,优选地,所述沥青的中间相含量>60%,软化点为150-400℃。更优选情况下,所述沥青的中间相含量为80-100%,软化点为200-400℃。
26.在本发明的一些实施例中,对所述导热添加剂的选择范围较宽,优选地,所述导热添加剂选自石墨烯、碳纳米管、天然石墨、膨胀石墨、碳化硅和氮化硼中的至少一种。
27.在本发明的一些实施例中,优选地,步骤(1)中,所述固化处理的条件包括:固化温度为30-200℃,固化时间为10-300min。更优选情况下,固化温度为50-150℃,固化时间为150-270min。本发明通过固化处理有利于泡沫炭成型以及压缩强度的提高。
28.在本发明的一些实施例中,为了提高泡沫炭的孔隙率和热导率,对经固化处理后的产物进行热处理,优选地,步骤(2)中,所述热处理的条件包括:温度为400-3200℃,更优选为1800-3200℃;压力为常压。本发明所述常压即一个大气压,也就是我们平常生活的这个大气层产生的气体压力。一个标准大气压为101325pa(即0.1mpa),这里的常压可以近似认为是一个标准大气压。本发明所述热处理的时间为10-120min。
29.在本发明的一些实施例中,对所述惰性气体没有特别的限定,采用本领域现有的惰性气体即可,例如包括但不限于氮气和/或氩气。
30.为了清楚地描述本发明的泡沫炭材料的制备方法,以下提供一种优选的具体实施方式进行说明:
31.(1)将沥青粉碎、筛分为50-600目的颗粒,与树脂、导热添加剂按照重量百分比为(10-80):(20-90):(0-20)混合,得到的混合物在30-200℃下固化处理10-300min;
32.(2)在惰性气体下,将步骤(1)得到的产物在400-3200℃、0.1mpa下热处理10-120min,得到泡沫炭材料。
33.本发明第二方面提供了一种由本发明第一方面所述的制备方法制得的泡沫炭材料,所述泡沫炭材料的孔隙率为60-95%,压缩强度为10-40mpa,热导率为5-150w/mk,无定型炭峰与石墨峰的峰值比为10-90%。满足上述限定条件的泡沫炭材料具有压缩强度高、导热性能好的特点,满足高级碳材料的需求。
34.在本发明的一些实施例中,优选地,所述泡沫炭材料的孔隙率为70-95%,压缩强度为20-40mpa,热导率为50-150w/mk,无定型炭峰与石墨峰的峰值比为10-40%。满足上述限定条件的泡沫炭材料具有更高的压缩强度和更好的导热性能。
35.在没有特别说明的情况下,本发明所述的压力均表示表压。
36.以下将通过实例对本发明进行详细描述。以下实例中,在没有特别说明的情况下,使用的各种原料均可从商业渠道获得。
37.沥青i:中间相含量为80%、软化点为300℃,购自济宁科能新型碳材料科技有限公司。
38.沥青ii:中间相含量为70%、软化点为180℃,购自济宁科能新型碳材料科技有限公司。
39.天然石墨:购自信达矿产品有限公司。
40.环氧树脂:含碳量为40wt%、900℃下的残炭含量为8wt%,购自中旷化工公司。
41.以下实例中,孔隙率根据公式:(1-ρb/ρ
t
)
×
100计算得到;
42.其中ρb为体积密度,通过质量除以体积计算得到,质量通过天平测定,体积通过将样品切割为规则的立方体,测量长宽高测定;
43.ρ
t
为真密度,通过真密度仪(micromeritics accupycⅱ1340)测定。
44.压缩强度通过压力试验机(因斯特朗6800系列)测定。
45.热导率根据公式κ=αρc
p
计算得到;
46.其中α为热扩散系数,通过激光热导仪(耐驰lfa467)测定;
47.ρ为体积密度,通过质量除以体积计算得到,质量通过天平测定,体积通过将样品切割为规则的立方体,测量长宽高测定;
48.c
p
为比热,通过差式扫描量热仪(ta q2000)测定。
49.无定型炭峰与石墨峰的峰值比通过xrd测定并计算得到。
50.实施例1
51.本实施例用于说明本发明的泡沫炭材料的制备方法。
52.(1)将沥青i粉碎、筛分为200目的颗粒,与环氧树脂按照重量百分比为50:50混合,得到的混合物在150℃下固化处理150min;
53.(2)在氮气气氛下,将步骤(1)得到的产物在1800℃、0.1mpa下热处理20min,得到泡沫炭材料。
54.实施例2
55.本实施例用于说明本发明的泡沫炭材料的制备方法。
56.(1)将沥青i粉碎、筛分为100目的颗粒,与环氧树脂按照重量百分比为60:40混合,得到的混合物在50℃下固化处理270min;
57.(2)在氮气气氛下,将步骤(1)得到的产物在3200℃、0.1mpa下热处理60min,得到泡沫炭材料。
58.实施例3
59.本实施例用于说明本发明的泡沫炭材料的制备方法。
60.(1)将沥青i粉碎、筛分为300目的颗粒,与环氧树脂、天然石墨按照重量百分比为30:60:10混合,得到的混合物在100℃下固化处理200min;
61.(2)在氮气气氛下,将步骤(1)得到的产物在2000℃、0.1mpa下热处理100min,得到泡沫炭材料。
62.实施例4
63.按照与实施例1相同的方法制备泡沫炭材料,不同的是,步骤(1)中,将200目的沥青i颗粒与环氧树脂的重量百分比改变为66.6:33.3,得到泡沫炭材料。
64.实施例5
65.按照与实施例1相同的方法制备泡沫炭材料,不同的是,用相同用量的沥青ii代替沥青i,得到泡沫炭材料。
66.实施例6
67.按照与实施例1相同的方法制备泡沫炭材料,不同的是,用相同用量的聚乙烯(含碳量为50wt%、900℃下的残炭含量为20wt%、购自中旷化工公司)代替环氧树脂,得到泡沫炭材料。
68.实施例7
69.按照与实施例1相同的方法制备泡沫炭材料,不同的是,步骤(1)中,固化温度改变为200℃,固化时间改变为10min,得到泡沫炭材料。
70.实施例8
71.按照与实施例1相同的方法制备泡沫炭材料,不同的是,步骤(2)中,热处理的温度
改变为700℃,得到泡沫炭材料。
72.将得到的泡沫炭材料进行sem测试,结果如图1所示,从图1中可以看出,该泡沫炭材料为三维网状结构,有孔洞,测量孔径为30-80μm。
73.将得到的泡沫炭材料进行xrd测试,得到2θ角从20
°
到30
°
的衍射峰值,如图2所示。将2θ角从20
°
到30
°
的不对称宽峰进行分峰处理,得到2θ=23.4
°
的宽无定型炭峰和2θ=25.3
°
的尖石墨峰的xrd衍射图,如图3所示,分析图3可知,2θ=23.4
°
的无定型炭峰峰值为0.507,2θ=25.3
°
的石墨峰峰值为0.813,计算可得xrd图谱下无定型炭峰与石墨峰的峰值比为62.4%,结果见表1。
74.对比例1
75.采用与实施例1相似的方法制备泡沫炭材料,不同的是,步骤(1)中,仅将沥青i粉碎、筛分为200目的颗粒,不与环氧树脂混合,具体为:
76.(1)将沥青i粉碎、筛分为200目的颗粒,然后在150℃下固化处理150min;
77.(2)在氮气气氛下,将步骤(1)得到的产物在1800℃、0.1mpa下热处理20min,得到泡沫炭材料。
78.将实施例1-7和对比例1中制备得到的泡沫炭材料分别进行sem测试,得到与图1相似的图像,泡沫炭材料均为三维网状结构,有孔洞。
79.将实施例1-7和对比例1中制备得到的泡沫炭材料分别进行xrd测试,得到与图2、3相似的谱图,并按照实施例1的方法计算得到xrd图谱下无定型炭峰与石墨峰的峰值比,结果见表1。
80.将上述实施例1-8和对比例1中制备得到的泡沫炭材料进行孔隙率、压缩强度和热导率的测试,测试结果见表1。
81.表1
[0082][0083]
注:
“-”
表示制备得到的泡沫炭材料破碎成粉末、不成型,无法测试其孔隙率和压缩强度。
[0084]
从表1的结果可以看出,本发明通过将沥青与树脂、导热添加剂混合,不需要添加发泡剂,在高温常压下发泡、炭化制备得到泡沫炭材料的孔隙率为60-95%,压缩强度为10-40mpa,热导率为5-150w/mk,无定型炭峰与石墨峰的峰值比为10-90%,表明该泡沫炭材料
具有压缩强度高、导热性能好的特点,满足高级碳材料的需求。进一步地,通过将沥青、树脂和导热添加剂的用量、参数指标和反应条件调整到本技术限定的优选范围内,能够控制泡沫炭材料的孔隙率在70-95%的范围内,压缩强度在20-40mpa的范围内,热导率在50-150w/mk的范围内,无定型炭峰与石墨峰的峰值比在10-40%的范围内,从而获得压缩强度更高、导热性能更好的泡沫炭材料。而对比例不添加树脂制备得到的泡沫炭材料的压缩强度和导热性能均较差。
[0085]
以上详细描述了本发明的优选实施方式,但是,本发明并不限于此。在本发明的技术构思范围内,可以对本发明的技术方案进行多种简单变型,包括各个技术特征以任何其它的合适方式进行组合,这些简单变型和组合同样应当视为本发明所公开的内容,均属于本发明的保护范围。
再多了解一些
本文用于企业家、创业者技术爱好者查询,结果仅供参考。