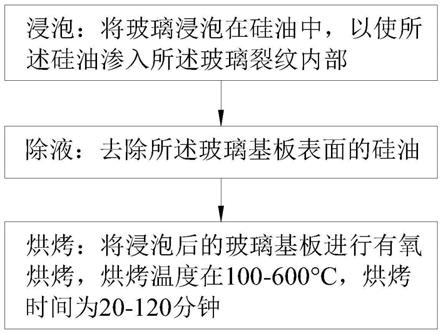
1.本发明属于玻璃加工领域,尤其涉及一种玻璃修复方法和玻璃修复设备。
背景技术:
2.近年来,随着信息技术的飞速发展,诸如平板电脑、笔记本、手机等显示终端不断在我们生活中成为不可或缺的工具,用户对显示终端的显示性能也越来越高。柔性基板具有良好的弯曲特性,在曲面显示领域占据很大优势。由于玻璃材质具有透光率高、性能稳定的特点,而作为显示屏的基板材料。不过玻璃基板,尤其异形玻璃基板,在切割磨削过程中极易产生微微裂纹,强度变弱,易崩边破裂。
3.传统玻璃基板增强的方法是氢氟酸处理,此方法虽然除去了表面的微微裂纹,但氢氟酸会残留在产品表面造成污染,并且在后制成过程中加热、冷却会吸收大气中水分,其表面又会被侵蚀,还会产生新微裂纹,强度有所削减。
技术实现要素:
4.本发明的目的在于克服上述现有技术的不足,提供了一种玻璃修复方法和玻璃修复设备,其旨在对玻璃基板切割过程中产生的微微裂纹进行修补,以提高玻璃基板的强度。
5.一种玻璃修复方法,包括:
6.浸泡:将玻璃基板浸泡在硅油中,以使所述硅油渗入所述玻璃基板微裂纹内部;
7.烘烤:将浸泡后的玻璃基板进行有氧烘烤,烘烤温度在100-600℃,烘烤时间为20-120分钟。
8.可选的,在所述烘烤步骤中,对浸泡后的玻璃基板进行连续升温加热,待温度达到烘烤温度时,恒温烘烤20-120分钟。
9.可选的,在所述烘烤步骤中,烘烤温度在180-210℃,烘烤时间为25-32分钟。
10.可选的,所述硅油粘度不大于1000cs。
11.可选的,所述浸泡步骤中,将玻璃基板浸泡在硅油中,且浸泡时间不小于30分钟。
12.可选的,在所述浸泡步骤之后并于所述烘烤步骤之前,还包括除液:去除所述玻璃基板表面的硅油。
13.可选的,在去除所述玻璃基板表面的硅油之前或之后,将所述玻璃基板静置10分钟以上。
14.可选的,所述硅油为甲基硅油。
15.可选的,所述硅油为羟基硅油或二乙烯基硅油,并混有含氢硅油。
16.一种玻璃修复设备,包括:
17.浸泡池,装载有硅油并能够供玻璃基板置入;
18.烘炉,可为半封闭式式烘炉,也可为高温化学熔盐等其他高温条件炉,用于对经浸泡后的所述玻璃基板进行烘烤。
19.本技术提供的玻璃修复方法和玻璃修复设备利用硅油在有氧加热环境下共价键
和并能够生成有机硅氧膜的特性,通过浸泡的方式使得硅油渗入玻璃基板微裂纹内部,再进行烘烤,玻璃基板微裂纹内的硅油受热发生共价键合成线性大分子链并附着在玻璃基板微裂纹断面上,并进一步交联而形成三维网状结构,从而形成具有高强度的有机硅氧膜。首先,玻璃基板裂缝处,由有机硅氧膜填充。有机硅氧膜具有很好的抗擦伤性和抗磨损性,大大提高了玻璃基板的强度。其次,有机硅氧膜包覆各微裂纹处以对玻璃基板进行保护,并能够防止了新微裂纹的产生。再而,由于硅油表面张力小,硅油能够覆盖玻璃各微裂纹处而不容易产生气泡等情况,从而保证了修复的效果,增强了玻璃强度。最后,这种修复方法不会污染玻璃基板,最大限度得保护玻璃基板。
附图说明
20.为了更清楚地说明本发明实施例中的技术方案,下面将对实施例中所需要使用的附图作简单地介绍,显而易见地,下面描述中的附图仅仅是本发明的一些实施例,对于本领域普通技术人员来讲,在不付出创造性劳动的前提下,还可以根据这些附图获得其他的附图。
21.图1为本技术实施例提供的玻璃修复方法的示意图;
22.图2为本技术实施例中甲基硅油的分子式;
23.图3为本技术实施例中甲基硅油在玻璃基板微缝隙内共价键合的示意图;
24.图4为本技术实施例中甲基硅油在玻璃基板微缝隙内交联的示意图;
25.图5为本技术实施例中甲基硅油在玻璃基板形成有机硅氧膜的效果图。
26.其中,图中各附图标记:
27.1、玻璃基板;2、有机硅氧膜。
具体实施方式
28.为了使本发明的目的、技术方案及优点更加清楚明白,以下结合附图及实施例,对本发明进行进一步详细说明。应当理解,此处所描述的具体实施例仅用以解释本发明,并不用于限定本发明。
29.本实施例提供一种玻璃修复方法和对应的玻璃修复设备,用于对玻璃基板进行修复、强化。玻璃基板可以是有功能层的玻璃也可以是裸玻璃;可以磨边,也可以不磨边;可以是经过钢化处理或未经过刚化的玻璃基板。
30.请参照图1至图5,玻璃修复方法包括:
31.浸泡:将玻璃基板1浸泡在硅油中,以使硅油渗入玻璃基板1微裂纹内部;
32.烘烤:将浸泡后的玻璃基板1进行有氧烘烤,烘烤温度在100-600℃,烘烤时间为20-120分钟。
33.将玻璃基板1浸泡在硅油中,硅油为液体,利用毛细作用而渗入玻璃基板1的微裂纹内部。而后在烘烤中,硅油高温下产生共价键合并覆盖玻璃基板1的微裂纹断面位置(图3),同时在有氧加热环境下,硅油上的有机官能团会发生氧化而分解成二氧化碳,并产生自交联而形成有机硅氧膜2,以填充覆盖玻璃基板1微裂纹(图4)。
34.对应的,玻璃修复设备,包括浸泡池和烘炉。浸泡池装载有硅油并能够供玻璃基板1置入。换言之,玻璃基板1的浸泡在浸泡池中进行。烘炉为半封闭式式烘炉,用于对经浸泡
后的玻璃基板1进行烘烤。
35.本实施例提供的玻璃修复方法和玻璃修复设备利用硅油在有氧加热环境下共价键和并能够生成有机硅氧膜2的特性,通过浸泡的方式使得硅油渗入玻璃基板1微裂纹内部,再进行烘烤,玻璃基板1微裂纹内的硅油受热发生共价键合成线性大分子链并附着在玻璃基板1微裂纹断面上,而后进一步交联而形成三维网状结构,从而形成具有高强度的有机硅氧膜2。首先,玻璃基板1裂缝处,由有机硅氧膜2填充。有机硅氧膜2具有很好的抗擦伤性和抗磨损性,大大提高了玻璃基板1的强度。其次,有机硅氧膜2包覆各微裂纹处以对玻璃基板1进行保护,并能够防止了新微裂纹的产生。再而,由于硅油表面张力小,硅油能够覆盖玻璃各微裂纹处而不容易产生气泡等情况,从而保证了修复的效果,增强了玻璃强度。最后,这种修复方法不会污染玻璃基板1,最大限度得保护玻璃基板1。
36.对硅油的反应条件进行控制,以确保生成的有机硅氧膜2的质量。经多次实验,在温度低于100℃下,硅油自交联效果较弱,而在温度高于230℃后,硅油容易产生进一步的氧化反应而影响有机硅氧膜2的生成。经浸泡后的玻璃基板1在100-600℃的温度下烘烤20-120分钟,能够获得良好的修复强化效果。
37.需要说明的是,烘烤时间为达到设计烘烤温度后持续时间,不包括前期预热时间。
38.优选的,在烘烤步骤中,对浸泡后的玻璃基板1进行连续升温加热,待温度达到烘烤温度时,恒温烘烤20-120分钟。本领域技术人员可以采用持续升温的模式,对浸泡后的玻璃基板1进行预热。比如,将浸泡后的玻璃基板1置于烘炉中,将烘炉加热温度设为30℃,加热0.5分钟;而后将加热温度设为50℃,加热0.5分钟;再将加热温度设为80℃,加热0.5分钟。。。直至温度达到烘烤温度,完成对玻璃基板1的预热。而后恒温烘烤20-120分钟。本领域技术人员可以根据实际情况调整分段加热的时间和温度,在此不作限定。采用持续升温的方式对玻璃基板1进行预热,再进行恒温烘烤,有利于硅油的充分反应,从而提高有机硅氧膜2的成型质量。
39.对烘烤条件进一步优化选择为:烘烤温度在180-210℃,烘烤时间为25-32分钟。该设计能够进一步提高有机硅氧膜2的成型质量。本领域技术人员可以将烘烤温度进一步选择为180℃、182℃、185℃、188℃、190℃、192℃、196℃、198℃、200℃、202℃、205℃、206℃、208℃、210℃等,在此不作唯一限定。本领域技术人员可以将烘烤时间进一步选择为25min、26min、27min、28min、28.5min、29min、30min、30.5min、31min、32min等,在此不作唯一限定。
40.在本技术另一实施例中,硅油粘度不大于1000cs。硅油粘度的控制能够提高硅油在玻璃基板1缝隙的渗入效果。一般说来,硅油粘度越小,则渗入效果越好。经多次实验,硅油粘度不大于1000cs,能够确保硅油的渗入效果从而提高玻璃基板1的修复效果。本领域技术人员可以将硅油的粘度进一步控制在800cs、600cs、500cs、400cs、300cs以下。
41.在本技术另一实施例中,浸泡步骤中,将玻璃基板1浸泡在硅油中,浸泡时间不小于30分钟。一般说来,玻璃基板1浸泡在硅油中的时间越长,则硅油渗入玻璃基板1的微裂纹的深度越深,而有利于最终的修复效果。经多次实验,浸泡时间不小于30分钟,能够确保硅油的渗入效果。本领域技术人员可以将浸泡时间进一步优选为30min、35min、38min、40min、45min、50min、60min等,在此不作限定。
42.在本技术另一实施例中,请参照图1,在浸泡步骤之后并于烘烤步骤之前,还包括除液:去除玻璃基板1表面的硅油。
43.在未做除液处理时,浸泡后的玻璃基板1周侧表面均附着有硅油,进入烘炉中烘烤而在玻璃基板1周侧表面形成有机硅氧膜层。则需要在烘烤之后对玻璃基板1周侧表面的有机硅氧膜层进行去除处理。
44.本实施例中,在烘烤步骤之前,对多余的硅油进行去除,从而免除烘烤后对玻璃基板1周侧表面的有机硅氧膜层的处理。相比之下,硅油为液态,对硅油的去除处理比对成型的有机硅氧膜的处理更为方便。且不会对置于玻璃基板1缝隙中的有机硅氧膜2造成影响。
45.对玻璃基板1表面的硅油的去除,可以通过擦除、吸附、吹除或挤压的方式实现,本领域技术人员根据实际情况选择合适的去除方式,在此不作限定。
46.在本技术另一实施例中,在除液步骤并在去除玻璃基板1表面的硅油之前或之后,将玻璃基板1静置10分钟以上。玻璃基板1的静置,有利于硅油进一步的渗入玻璃基板1的内部。一般说来,玻璃基板1在浸泡池中浸泡的时间越长,则硅油渗入玻璃基板1的效果越好。不过,玻璃基板1占用浸泡池的时间太长,不利于实际作业效率。将玻璃基板1静置的空间从浸泡池转移,在去除玻璃基板1表面的硅油之前或之后,对玻璃基板1进行静置处理,能够延长硅油渗入的时间,并减少玻璃基板1占用浸泡池的时间,从而有利于生产作业效率。本领域技术人员可以将玻璃基板1静置时间设为10mim、15mim、20mim等,在此不作唯一限定。
47.本技术另一实施例中,硅油为甲基硅油。甲基硅油无色、无味、不易挥发,甲基硅油具有卓越的耐候性、疏水性和较小的表面张力,还具有低的黏温系数。为最常用的硅油制品。此外,甲基硅油在有氧高温环境下(比如200℃)能够自交联生成有机硅氧膜2,无需交联剂等其它材料的辅助。
48.在本技术另一实施例中,硅油为羟基硅油或二乙烯基硅油,并混有含氢硅油。含氢硅油可以作为交联剂加入羟基硅油或二乙烯基硅油中,以提高有机硅氧膜2的成型质量。
49.下面对采用本技术实施例提供的玻璃修复方法修复效果进行示例说明。
50.示例1:对经过钢化处理并带有功能层且经过磨边处理的康宁玻璃基板1进行修复。
51.将该玻璃基板1浸泡在甲基硅油中,静置30分钟;而后将玻璃基板1取出,去除表面多余硅油后,放置10分钟。最后将玻璃基板1放入烘炉200℃烘烤30min。
52.修复前后的弯曲强度对比如下:
[0053][0054]
示例2:对经过钢化处理并带有功能层且经过磨边处理的苏打玻璃基板1进行修复。
[0055]
将该玻璃基板1浸泡在甲基硅油中,静置30分钟;而后将玻璃基板1取出,去除表面多余硅油后,放置10分钟。最后将玻璃基板1放入烘炉200℃烘烤30min。
[0056]
修复前后的弯曲强度对比如下:
[0057]
苏打基板实验前后抗弯强度对比
[0058][0059]
有上述两示例的数据可知,本技术实施例提供的玻璃修复方法能够大幅度提高玻璃基板1的抗弯曲强度。
[0060]
以上所述仅为本发明的较佳实施例而已,并不用以限制本发明,凡在本发明的精神和原则之内所作的任何修改、等同替换或改进等,均应包含在本发明的保护范围之内。
再多了解一些
本文用于企业家、创业者技术爱好者查询,结果仅供参考。