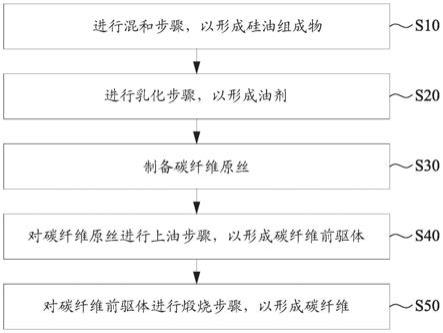
1.本
技术实现要素:
是有关于一种碳纤维的制造方法。
背景技术:
2.近年来,随着环保意识抬头以及节能高效的概念逐渐形成,碳纤维的需求越来越高。由于碳纤维具有耐疲劳性佳、热传导率高、摩擦系数小、润滑性佳、热膨胀系数小、耐腐蚀性佳、x射线穿透率高以及比热与导电性介于非金属和金属之间等优点,因此常广泛地应用于例如是工业、运动、土木建筑、交通运输、能源、航天以及军事等领域。然而,在碳纤维的制造过程中,基于前驱物、工艺以及碳化条件的不同,所制成的碳纤维的机械强度及其他物性与化性也不相同。
3.在碳纤维的制造过程中,几乎都是在加热的环境下对纤维原丝进行牵伸,且纤维原丝的煅烧也是在高温的环境下进行,而高温易导致纤维原丝软化,甚至进一步发生单纤粘着的情形。此外,纤维原丝在输送的过程中会与滚轮表面接触摩擦,导致毛羽及其他缺陷的产生而使碳纤维的质量降低。为防止上述情形发生,目前最常使用的方式是将油剂附着在纤维原丝的表面以形成保护膜。然而,由于一般常用的油剂难以承受高温,因此便逐渐发展出改质的油剂。然而,经改质后的油剂仍存在着成膜性差、耐热性差、安定性差、亲水性差、工艺复杂等的问题。基于上述,如何提供一种可克服上述问题的油剂,是本领域业者积极研究的重要课题。
发明内容
4.根据本发明一些实施方式,一种碳纤维的制造方法包括以下步骤。进行乳化步骤,将硅油组成物及乳化剂均匀混和,以形成油剂,其中硅油组成物包括γ-二乙烯三氨丙基甲基二甲氧基硅烷以及n-(β-氨乙基)-γ-氨丙基甲基二甲氧基硅烷。进行上油步骤,将碳纤维原丝浸泡于油剂中,使油剂附着于碳纤维原丝的表面,以形成碳纤维前驱体。对该碳纤维前驱体进行煅烧步骤,以形成碳纤维。
5.在本发明一些实施方式中,γ-二乙烯三氨丙基甲基二甲氧基硅烷与n-(β-氨乙基)-γ-氨丙基甲基二甲氧基硅烷的重量比介于7:3至8:2之间。
6.在本发明一些实施方式中,在空气中对油剂进行热重分析,在温度为273℃至277℃时,油剂的重量大于油剂的原重量的90%至95%。
7.在本发明一些实施方式中,在温度为428℃至432℃时,油剂的重量大于油剂的原重量的80%至85%。
8.在本发明一些实施方式中,在上油步骤中,油剂的附油率介于0.5%至0.8%之间。
9.在本发明一些实施方式中,碳纤维的制造方法还包括以下步骤。进行混和步骤,在300rpm至1000rpm的转速下将γ-二乙烯三氨丙基甲基二甲氧基硅烷以及n-(β-氨乙基)-γ-氨丙基甲基二甲氧基硅烷均匀地混和,以形成硅油组成物。
10.在本发明一些实施方式中,混和步骤在50℃至65℃的温度下进行。
11.在本发明一些实施方式中,乳化步骤还包括以下步骤。将硅油组成物、乳化剂以及去离子水均匀地混和,以形成油剂,其中硅油组成物、乳化剂以及去离子水的重量比为(12~40):(3~15):(45~85)。
12.在本发明一些实施方式中,乳化剂包括非离子界面活性剂、阳离子界面活性剂、阴离子界面活性剂或其组合。
13.在本发明一些实施方式中,非离子界面活性剂包括聚氧乙烯醚与聚氧丙烯醚嵌段共聚物、三苯乙烯苯基醚与环氧乙烷/环氧丙烷嵌段共聚物或其组合。
14.根据本发明上述实施方式,本发明的油剂用于制造碳纤维,且包括γ-二乙烯三氨丙基甲基二甲氧基硅烷及n-(β-氨乙基)-γ-氨丙基甲基二甲氧基硅烷,由于γ-二乙烯三氨丙基甲基二甲氧基硅烷及n-(β-氨乙基)-γ-氨丙基甲基二甲氧基硅烷皆为经胺基改质的硅烷,故两者的兼容性佳,有助于提升油剂的安定性,且可提供工艺上的便利性,并可使硅油组成物具有较佳的亲水性。另一方面,由于本发明的油剂可具有良好的成膜性及耐热性,因此其可在具有很小的附油率的前提下达到良好的保护效果。
附图说明
15.为让本发明的上述和其他目的、特征、优点与实施例能更明显易懂,所附图式的说明如下:
16.图1绘示根据本发明一些实施方式的碳纤维的制造方法的流程图;以及
17.图2绘示根据本发明一些实施方式的油剂的热重分析结果。
具体实施方式
18.以下将以图式公开本发明的复数个实施方式,为明确地说明起见,许多实务上的细节将在以下叙述中一并说明。然而,应了解到,这些实务上的细节不应用以限制本发明。也就是说,在本发明部分实施方式中,这些实务上的细节是非必要的,因此不应用以限制本发明。
19.请参阅图1,其绘示根据本发明一些实施方式的碳纤维的制造方法的流程图。本发明的碳纤维的制造方法包括步骤s10至步骤s50。在步骤s10中,进行混和步骤,以形成硅油组成物。在步骤s20中,进行乳化步骤,以形成油剂。在步骤s30中,制备碳纤维原丝。在步骤s40中,对碳纤维原丝进行上油步骤,以形成碳纤维前驱体。在步骤s50中,对碳纤维前驱体进行煅烧步骤,以形成碳纤维。在以下的叙述中,将进一步说明上述各个步骤。
20.首先,在步骤s10中,进行混和步骤,将第一胺基改质硅油以及第二胺基改质硅油均匀地混和,以形成硅油组成物。第一胺基改质硅油包括γ-二乙烯三氨丙基甲基二甲氧基硅烷,且第二胺基改质硅油包括n-(β-氨乙基)-γ-氨丙基甲基二甲氧基硅烷。由于γ-二乙烯三氨丙基甲基二甲氧基硅烷以及n-(β-氨乙基)-γ-氨丙基甲基二甲氧基硅烷皆为经胺基改质的硅烷,故两者的兼容性佳,有助于提升硅油组成物整体的安定性,且可提供工艺上的便利性(例如,在以硅油组成物形成油剂时,在乳化剂的选择上较为多元,此将于后文进一步说明)。此外,由于γ-二乙烯三氨丙基甲基二甲氧基硅烷以及n-(β-氨乙基)-γ-氨丙基甲基二甲氧基硅烷皆为经胺基改质的硅烷,因此可使硅油组成物具有较佳的亲水性,以便于以乳化的方式形成油剂后,再使油剂附着于碳纤维原丝的表面,而不须使用挥发性强
且可燃性高的有机溶剂来溶解硅油组成物以将其成型在碳纤维原丝的表面,如此可提升工艺的安全性。
21.在一些实施方式中,第一胺基改质硅油与第二胺基改质硅油的重量比可介于7:3至8:2之间,从而提升后续所形成的油剂的成膜性以及热稳定性。详细而言,若上述重量比小于7:3(例如6:4),可能导致油剂的热稳定性较差,不利于保护碳纤维原丝;若上述重量比大于8:2(例如9:1),可能导致油剂的成膜性差,不利于附着于碳纤维原丝的表面。在一些实施方式中,可使用300rpm至1000rpm的转速对第一胺基改质硅油以及第二胺基改质硅油进行搅拌,以使第一胺基改质硅油及第二胺基改质硅油均匀地混和。详细而言,若上述转速小于300rpm,可能导致混和不均匀,进而影响油剂的保护能力;若上述转速大于1000rpm,可能导致不必要的热生成,造成第一胺基改质硅油及第二胺基改质硅油变质。在一些实施方式中,可使用50℃至65℃的温度进行混和步骤,并持续60分钟至90分钟的时间,从而确保第一胺基改质硅油及第二胺基改质硅油彻底地混和。
22.接着,在步骤s20中,进行乳化步骤,将在步骤s10所形成的硅油组成物、乳化剂以及去离子水均匀地混和,以形成油剂。乳化剂的添加可提升硅油组成物的亲水性,使硅油组成物与去离子水可充分混和。在一些实施方式中,硅油组成物、乳化剂以及去离子水的重量比可为(12~40):(3~15):(45~85),从而达到较佳的混合/乳化效果。在一些实施方式中,乳化剂可包括非离子界面活性剂、阳离子界面活性剂、阴离子界面活性剂或其组合。在较佳的实施方式中,乳化剂可包括非离子界面活性剂。本发明所使用的非离子界面活性剂包括聚氧乙烯醚与聚氧丙烯醚嵌段共聚物、三苯乙烯苯基醚与环氧乙烷/环氧丙烷嵌段共聚物或其组合,上述非离子界面活性剂可较佳地将包括有经胺基改质的硅烷的硅油组成物与去离子水乳化。在完成步骤s20后,便可得到本发明的油剂。在一些实施方式中,可进一步于油剂中加入醋酸、柠檬酸或其组合,以将油剂的酸碱值(ph值)控制在7以下,从而确保油剂的安定性。
23.随后,在步骤s30中,制备碳纤维原丝,其可包括步骤s32至步骤s36。首先,在步骤s32中,将第一单体及第二单体溶于溶剂中,并进行聚合反应,以得到共聚高分子。在一些实施方式中,第一单体包括丙烯腈,而第二单体具有不饱和键结。具体而言,第二单体可例如是丙烯酸、甲基丙烯酸、丙烯酰胺、丙烯酸甲酯、甲基丙烯酸甲酯、丙烯酸乙酯、丙烯酸正丁酯、丙烯酸异丁酯、乙酸乙烯酯、甲基丙烯酸乙酯、甲基丙烯酸异丙酯、丙烯酸异丁酯、甲基丙烯酸正丁酯、甲基甲基丙烯酸正己酯、甲基丙烯酸环己酯、甲基丙烯酸-2-羟基乙酯、溴化乙烯、衣康酸、柠檬酸、马来酸、中康酸、巴豆酸、苯乙烯、氯乙烯、氟乙烯、偏二氯乙烯、偏二氟乙烯、乙烯基甲苯、烯丙基磺酸、苯乙烯磺酸、上述任意化合物的胺盐或酯类衍生物。在一些实施方式中,考虑到共聚高分子于溶剂中的溶解性、对纤维的致密性以及稳定化工艺中促进氧化反应的功能,第二单体较佳可例如是衣康酸。
24.在一些实施方式中,以100wt%的第一单体与第二单体的总和计,第一单体的含量可介于95wt%至100wt%之间,即,第二单体的含量可小于5wt%。在上述含量范围中,第一单体具有高含有率,因此可使后续所形成的碳纤维前驱体免于在后续的煅烧步骤期间产生缺陷,以提升碳纤维的机械强度。详细而言,当第一单体的含量小于95wt%,可能导致碳纤维前驱体在煅烧步骤期间损失过多的质量,并容易导致缺陷的产生。在较佳实施方式中,以100wt%的第一单体与第二单体的总和计,第一单体的含量可介于99wt%至100wt%之间,
即,第二单体的含量可小于1wt%,从而较佳地实现上述效果,使得碳纤维具有更佳的机械强度。
25.接着,在步骤s34中,进行纺丝步骤,以形成初生碳纤维。具体而言,纺丝步骤可依序包括抽丝步骤及凝丝步骤。首先,可先将共聚高分子以合适的浓度溶于溶剂中,以形成纺丝原液,并对纺丝原液进行抽丝步骤,从而形成丝状共聚高分子。在此步骤中,溶剂可为二甲基甲酰胺、二甲基乙酰胺、二甲基亚砜等有机溶剂或其组合。在其他实施方式中,溶剂可例如是二氯化锌、硫氰酸钠等无机盐类水溶液或其组合。为避免金属的残留而影响碳纤维的物性,溶剂较佳为二甲基亚砜。在一些实施方式中,共聚高分子在溶剂中的重量百分浓度可介于18%至25%之间,从而利于经抽丝步骤以形成具有适当致密性的丝状共聚高分子。详细而言,当共聚高分子在溶剂中的重量百分浓度小于18%时,纺丝原液无法承受高倍率的延伸,且经抽丝所得的丝状共聚高分子结构疏松,导致碳纤维的机械强度偏低;当共聚高分子在溶剂中的重量百分浓度大于15%时,溶剂对共聚高分子溶解能力不足,导致纺丝原液的均匀性差且粘度过高,造成纺丝原液的流动性低,不利于纺丝工艺的稳定性。
26.随后,可采用干喷湿纺或湿喷湿纺对丝状共聚高分子进行凝丝步骤,以形成初生碳纤维。具体而言,可使用凝丝槽对丝状共聚高分子进行凝丝步骤,以于凝丝槽中吐出初生碳纤维。借由调整凝丝槽中凝丝液的浓度、凝丝步骤的温度(凝丝液的温度)、凝丝槽出口的牵引张力及延伸倍数等条件,可控制初生碳纤维的孔洞尺寸。在一些实施方式中,凝丝液可包括溶有二甲基亚砜的水溶液,且以100wt%的凝丝液计,二甲基亚砜的含量介于20wt%至50wt%之间。详细而言,当二甲基亚砜的含量小于20wt%时,可能导致丝状共聚高分子由凝丝液中析出以及凝固的速度过快,造成初生碳纤维的结构疏松且表面孔洞尺寸较大;当二甲基亚砜的含量大于50wt%时,可能导致丝状共聚高分子由凝丝液中凝固的速度过慢,造成初生碳纤维无法完全凝丝,使得初生碳纤维于后续的水洗、延伸等步骤期间产生单纤粘着。在一些实施方式中,凝丝步骤的温度可介于0℃至40℃之间,以利于提升初生碳纤维的致密性,并且使初生碳纤维的孔洞尺寸得以被控制在合适的范围中。详细而言,当凝丝温度小于0℃时,可能导致初生碳纤维的孔洞尺寸小于目标范围;当凝丝温度大于40℃时,可能导致初生碳纤维的结构过于松散,不利于形成高机械强度的碳纤维。
27.接着,在步骤s36中,可使用水洗槽对初生碳纤维进行水洗步骤。借由调整水洗槽中水洗液的浓度、水洗步骤的温度(水洗液的温度)等条件,可避免单纤粘着,并可控制初生碳纤维的孔洞尺寸。在一些实施方式中,水洗槽可包括溶有二甲基亚砜的水溶液(也称水洗液),且以100wt%的水洗液计,二甲基亚砜的含量可介于0wt%至25wt%之间。在一些实施方式中,水洗步骤的温度可介于70℃至90℃之间,而若为多段水洗步骤,最后一段水洗步骤的温度可进一步提升至90℃至95℃之间。在较佳的实施方式中,为较佳地避免溶剂残留而于初生碳纤维中形成不必要的孔洞,水洗步骤的温度较佳为100℃(即水洗液处于沸腾状态)。在一些实施方式中,在进行水洗步骤前,可对初生碳纤维进行延伸步骤,以使用2倍至5倍的延伸倍率对初生碳纤维进行拉伸。具体而言,延伸步骤可使用高温热滚轮、高温热板或于高温高压蒸汽内拉伸等方式进行。在较佳的实施方式中,可进行多段延伸步骤及多段水洗步骤,且延伸步骤以及水洗步骤可例如是交替进行。在完成步骤s30(包括步骤s32至s36)后,便可得到碳纤维原丝。
28.接着,在步骤s40中,将碳纤维原丝浸泡于油剂中,使得油剂附着于碳纤维原丝的
表面,以形成碳纤维前驱体。在一些实施方式中,在将碳纤维原丝浸泡于油剂中并取出后,油剂可完全包覆碳纤维原丝,也就是说,碳纤维原丝的所有表面可完全免于裸露出来。在一些实施方式中,可将油剂以水稀释,且稀释后油剂的浓度可介于20wt%至35wt%之间,以使油剂具有合适的流动性。在一些实施方式中,油剂的附油率可介于0.5%至0.8%之间,从而确保油剂充分覆盖碳纤维原丝的表面,并可避免油剂的浪费。详细而言,当油剂的附油率小于0.5%时,可能无法确保油剂充分覆盖碳纤维原丝的表面,导致油剂对碳纤维原丝的保护力不足;当油剂的附油率大于0.8%,可能因油剂的量过多而影响后续的工艺,且也造成油剂的浪费。另一方面,由于本发明的油剂可具有良好的成膜性及耐热性,因此其可在具有很小(介于0.5%至0.8%之间)的附油率的前提下达到良好的保护效果。在完成步骤s40后,便可得到碳纤维前驱体。
29.请参阅图2,其绘示根据本发明一些实施方式的油剂的热重分析结果。更详细而言,油剂的热重分析结果是使用mettler stare system tga2测量仪在空气中进行的,且是由温度为25℃以10℃/min的速率升温至250℃后停留半小时,再以10℃/min的速率升温至455℃。由图2的热重分析结果可以看出在温度为273℃至277℃(例如275℃)时,油剂的重量大于油剂的原重量的90%至95%(例如93.8%);而在温度为428℃至432℃(例如430℃)时,油剂的重量大于油剂的原重量的80%至82%。换句话说,由本发明的制造方法所制造而成的油剂在高温下可具有优异的耐热性,以对碳纤维原丝形成良好的保护,从而进行后续的煅烧、延伸等步骤。
30.随后,在步骤s50中,对碳纤维前驱体进行煅烧步骤,以形成碳纤维。煅烧步骤可采用业界公知的方式来进行,例如依序包括稳定化、碳化、表面处理以及上浆等四段步骤。具体而言,稳定化步骤是使碳纤维前驱体在适当的张力及温度为200℃至300℃的空气中进行反应,而经稳定化步骤后的碳纤维前驱体的纤维密度可介于1.3g/cm3至1.4g/cm3之间;碳化步骤是将碳纤维前驱体在高温的惰性气体中进行高温碳化,而为提高碳纤维的机械强度,碳化温度可介于1000℃至2000℃之间,若有必要,可进一步将碳化温度提升为介于2000℃至2500℃之间,以进行石墨化;表面处理步骤可提升碳纤维与树脂的结合能力,其包括化学接枝、等离子体、电解、臭氧处理等方式,较佳为采用等离子体处理;上浆步骤是将表面处理后的碳纤维前驱体进行水洗并干燥,再以含浸的方式使浆液附着于碳纤维前驱体的表面,从而使碳纤维具有良好的耐磨性、集束性等保护效果。在完成步骤s50后,即可得到本发明的具有高机械强度的碳纤维。
31.下文将参照各实施例及各比较例的碳纤维,更具体地描述本发明的特征及功效。应了解到,在不逾越本发明范畴的情况下,可适当地改变所用材料、其量及比率、处理细节以及处理流程等等。因此,不应由下文所述的各实施例对本发明作出限制性的解释。各实施例及各比较例的详细说明如下文所述。
32.各实施例及各比较例的碳纤维的制造方法包括以下步骤。以98wt%的丙烯腈为第一单体,以2wt%的衣康酸为第二单体,以于二甲基亚砜溶剂中进行聚合反应,从而形成共聚高分子。将包括22wt%的共聚高分子的溶液(纺丝原液)由纺丝嘴于空气中吐出后,以35wt%的二甲基亚砜的水溶液于凝丝槽中形成初生碳纤维。在对初生碳纤维进行水洗步骤后,于沸水中分二段进行总延伸倍率为3.5倍的延伸步骤,以形成碳纤维原丝。以油剂于油剂槽中对碳纤维原丝进行上油步骤。以温度为175℃的热滚轮对上油后的碳纤维原丝进行
干燥致密步骤。在高压蒸汽中对碳纤维原丝进行延伸倍率为3.5倍的延伸步骤,从而形成碳纤维前驱体。将碳纤维前驱体于空气中由240℃逐步升温至300℃,并控制前后牵引滚轮的速度比为1.0以在维持碳纤维前驱体的张力的条件下进行稳定化步骤,且稳定化后的碳纤维前驱体的纤维密度为1.35g/cm3。将稳定化后的碳纤维前驱体于氮气中由300℃逐步升温至800℃,并控制前后牵引滚轮的速度比为0.9的条件下进行低温碳化,再将温度由900℃逐步升温至1800℃,并且控制前后牵引滚轮的速度比为0.95的条件进行高温碳化。对碳化后的碳纤维前驱体进行电解表面处理。对表面处理后的碳纤维前驱体进行水洗、干燥以及上浆步骤,以得到最终的碳纤维。有关于油剂中的详细成分如下文述。
33.各实施例的油剂中的第一胺基改质硅油为γ-二乙烯三氨丙基甲基二甲氧基硅烷,第二胺基改质硅油为n-(β-氨乙基)-γ-氨丙基甲基二甲氧基硅烷,且乳化剂为三苯乙烯苯基醚与环氧乙烷/环氧丙烷嵌段共聚物;各比较例是将氨基改性聚二甲基硅氧烷为聚[3-((2-氨基乙基)氨基)丙基]二甲基硅氧烷(简称第一硅氧烷)以及环氧改质聚二甲基硅氧烷为1,2环氧环己基改质聚二甲基硅氧烷(简称第二硅氧烷)混合以作为硅油组成物,且乳化剂为脂肪醇聚氧乙烯醚。各成分的含量如表一所示。
[0034]
表一
[0035][0036]
注1:实施例及比较例的油剂皆为稀释后的油剂,其浓度范围为30~40wt%。
[0037]
《实验例1:油剂的附油率及残留重量测试》
[0038]
在本实验例中,使用索式蒸馏器对碳纤维原丝进行萃取,每次取10g含油剂的碳纤维原丝,将丙酮加热至沸腾溶剂进行萃取,萃取时间为4小时。计算瓶内剩余的残留重量,即可求得附油率。油剂残留重量使用tga(热重损失仪器)由系统纪录得到数据,其中油剂为升温至275℃及430℃后的状态,测试结果如表二所示。
[0039]
表二
[0040][0041]
由测试结果可知,本发明的油剂的附油率可维持在0.5%至0.8%的范围内,以确保油剂充分覆盖碳纤维原丝的表面,并在低复由绿的情况,可降低油剂的使用量及成本。
[0042]
《实验例2:碳纤维的机械强度测试》
[0043]
在本实验例中,使用标准方法astm d4018-99对各实施例及各比较例的进行碳纤维的强度测试,测试结果如表三所示。
[0044]
表三
[0045][0046]
综合实验例1及实验例2的测试结果可知,本发明的油剂在较低的附油率下可对碳纤维原丝达到较佳的保护效果,使最终制造出的碳纤维具有较高的机械强度,可有效降低油剂的成本。
[0047]
根据本发明上述实施方式,本发明的油剂用于制造碳纤维,且包括γ-二乙烯三氨丙基甲基二甲氧基硅烷及n-(β-氨乙基)-γ-氨丙基甲基二甲氧基硅烷,由于γ-二乙烯三氨丙基甲基二甲氧基硅烷及n-(β-氨乙基)-γ-氨丙基甲基二甲氧基硅烷皆为经胺基改质的硅烷,故两者的兼容性佳,有助于提升油剂的安定性,且可提供工艺上的便利性,并可使硅油组成物具有较佳的亲水性。另一方面,由于本发明的油剂可具有良好的成膜性及耐热性,因此其可在具有很小的附油率的前提下达到良好的保护效果。
[0048]
虽然本发明已以实施方式公开如上,然其并非用以限定本发明,本领域技术人员,在不脱离本发明的精神和范围内,当可作各种的更动与润饰,因此本发明的保护范围当视权利要求书所界定者为准。
[0049]
【符号说明】
[0050]
s10~s50:步骤。
再多了解一些
本文用于企业家、创业者技术爱好者查询,结果仅供参考。