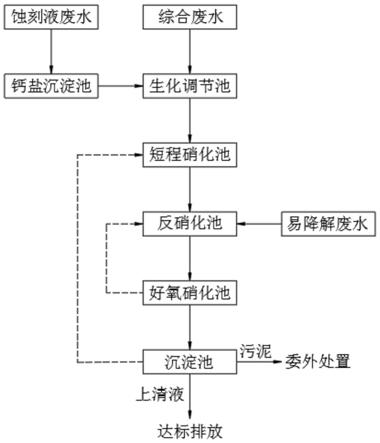
1.本发明属于废水生物处理技术领域,特别是涉及一种基于短程硝化反硝化的电子行业废水处理方法。
背景技术:
2.近几年,我国电子工业得到快速发展,其中蚀刻工艺为印刷线路板、玻璃镜片等生产过程中的关键步骤之一,玻璃化学蚀刻工艺中主要包括光面蚀刻和毛面蚀刻,其中光面蚀刻主要是利用氢氟酸与玻璃表面进行反应,形成可溶性盐类;而毛面蚀刻则需要加入氟化铵(nh4f),在与玻璃和氢氟酸的反应中生成硅氟化铵微晶。由于玻璃蚀刻技术会大量使用氢氟酸和氟化铵(nh4f),造成蚀刻废水中含有高浓度的氟化物和超高浓度的氨氮,增加了废水处理的难度。针对该类废水,现有的处理方法通常采用化学沉淀法,吹脱汽提等,使得污水厂废水处理成本耗费高,出水达标难,容易产生二次污染。
技术实现要素:
3.本发明主要解决的技术问题是提供一种基于短程硝化反硝化的电子行业废水处理方法,能够大大降低高氟高氨氮废水出水时氟化物和氨氮的浓度,实现高氟高氨氮废水深度除氟、脱氮的目的。
4.为解决上述技术问题,本发明采用的一个技术方案是:一种基于短程硝化反硝化的电子行业废水处理方法,包括以下步骤:
5.s1、将待处理蚀刻液废水输送至钙盐沉淀池进行除氟预处理;
6.s2、将除氟预处理后的废水以及综合废水输送至生化调节池,调节ph为7
‑
8;
7.s3、调节ph后的废水流至短程硝化池进行短程硝化反应,功能性菌群为氨氧化菌,氨氮被氧化成亚硝氮,短程硝化池内悬挂生物填料,池内补充碳酸氢钠维持系统碱度>70mg/l,ph为7
‑
8;
8.s4、经步骤s3处理后的废水输送至反硝化池,反硝化池补加碳源,维持c/n比为3
‑
4;
9.s5、经步骤s4处理后的废水输送至好氧硝化池,进行进一步碳氧化反应和硝化反应,好氧硝化池废水回流至反硝化池,回流比为1~4:1;
10.s6、处理后的废水输送至沉淀池沉淀分离,上清液排入标准排放口,下部污泥委外处置。
11.进一步地说,所述沉淀池中的污泥可通过回流管回流至短程硝化池。
12.进一步地说,所述好氧硝化池中的废水可通过回流管回流至所述反硝化池。
13.进一步地说,所述步骤s1中的除氟预处理为:首先在钙盐沉淀池内添加石灰乳调节ph为9
‑
10,再添加钙盐溶液并沉淀1
‑
2h,钙盐溶液和氟离子的投放比例为1.5:1。
14.进一步地说,所述钙盐溶液为氧化钙溶液、碳酸钙溶液和氯化钙溶液中的至少一种。
15.进一步地说,在生化调节池内投入絮凝剂进行絮凝沉淀。
16.进一步地说,所述综合废水为厂区生活污水和未含氟生产废水。
17.进一步地说,所述反硝化池内的有机碳源为易降解废水。
18.本发明的有益效果至少具有以下几点:
19.1、本发明采用化学沉淀法进行除氟预处理,即向高氟废水中投加钙盐,使钙盐与氟离子形成氟化钙沉淀并固液分离以达到除氟效果;
20.2、本发明采用短程硝化反硝化生物脱氮过程,除了具备生物脱氮过程的一系列优点外,与全程硝化反硝化相比,还具备特有的一些优点:
①
硝化阶段可减少25%左右的好氧量,降低了能耗;
②
反应时间短,构筑物占地面积小;
③
较高的反硝化速率,no
2-
‑
n的反硝化速率通常比no
3-
‑
n高63%左右。
附图说明
21.图1是本发明的工艺流程图;
22.图2是本发明的生物脱氮效果图。
具体实施方式
23.下面结合附图对本发明的较佳实施例进行详细阐述,以使本发明的优点和特征能更易于被本领域技术人员理解,从而对本发明的保护范围做出更为清楚明确的界定。
24.本发明实施例中涉及的氨氧化菌包括革兰氏染色阴性的美丽盐单胞菌(halomonas venusta),保藏号为cgmcc no.17273;反硝化菌包括脱氮副球菌(paracoccus denitrificans)dn
‑
3,保藏号为cgmcc no.3658;硝化菌包括欧洲亚硝化单胞菌,购自bncc菌种库,货号atcc19718;好氧菌包括法式柠檬酸杆菌citrobacter freundii,菌种购买自美国模式菌种收集中心,保藏号为atcc 8090。以上菌种均可通过公开途径(向实验室索取或市场购买)获得,无需另行专利保藏。
25.实施例1:一种基于短程硝化反硝化的电子行业废水处理方法,如图1所示,包括以下步骤:
26.s1、将待处理蚀刻液废水输送至钙盐沉淀池进行除氟预处理,预处理后取上清液测定废水中氟离子浓度(氟离子浓度按照《水质氟化物的测定离子选择电极法》(gb 7484-87)规定测定);
27.s2、将除氟预处理后的废水以及综合废水输送至生化调节池,用盐酸或氢氧化钠调节ph为7;
28.s3、调节ph后的废水流至短程硝化池进行短程硝化反应,功能性菌群为氨氧化菌,氨氮被氧化成亚硝氮(通常全程硝化是氧化成硝态氮,即这一步可以减省药剂投加、曝气量和池体占地面积),短程硝化池内悬挂生物填料,生物填料选用的是辫带式仿生水草生物绳填料,这一过程需要控制的条件为:投加碳酸氢钠或碳酸钠维持系统碱度>70mg/l,ph在7,废水温度在25℃,溶解氧浓度在2mg/l,废水有机负荷在0.05kgbod/(kg mlss
·
d),总氮负荷<0.35kgtn/(m3·
d);
29.本发明的生物脱氮过程的主要反应过程为:
30.[0031][0032]
而通常全程反硝化过程的主要反应过程为:
[0033][0034][0035]
因此,本发明的生物脱氮过程具有较高的硝化速率,no
2-
‑
n的反硝化速率通常比no
3-
‑
n高63%左右。
[0036]
s4、经步骤s3处理后的废水输送至反硝化池,反硝化菌是异养微生物,利用有机碳源将废水中的亚硝氮和硝氮还原成氮气,实现氨氮的有效去除。这一过程需要控制的条件:投加有机碳源(乙酸钠、葡萄糖等和易降解废水b/c>0.45)维持系统内c/n比在3,ph在7,溶解氧维持在2mg/l,温度在25℃之间,orp在
‑
160mv;
[0037]
s5、经步骤s4处理后的废水输送至好氧硝化池,好氧硝化池内是硝化菌和好氧菌的混合体系,在该池中前端未反应完全的氨氮可以进一步被氧化成亚硝态氮或硝态氮,然后回流至反硝化池进行反硝化脱氮。同时,反硝化池中未降解完全的有机物也可以进一步被降解。这一过程需要控制的条件:ph在7,溶解氧在2mg/l,温度在25℃,回流比在1:1;
[0038]
s6、处理后的废水输送至沉淀池沉淀分离,上清液排入标准排放口,下部污泥委外处置。
[0039]
所述沉淀池中的污泥可通过回流管回流至短程硝化池。
[0040]
所述好氧硝化池中的废水可通过回流管回流至所述反硝化池。
[0041]
所述步骤s1中的除氟预处理为:首先在钙盐沉淀池内添加石灰乳调节ph为9,再添加钙盐溶液并沉淀1h,钙盐溶液和氟离子的投放比例为1.5:1。
[0042]
所述钙盐溶液为氧化钙溶液、碳酸钙溶液和氯化钙溶液中的至少一种。本实施例的钙盐溶液选用的是质量浓度为30%wt的氯化钙溶液。
[0043]
在生化调节池内投入絮凝剂进行絮凝沉淀。所述絮凝剂为pac和pam,pac的浓度为400mg/l,pam的浓度为0.05mg/l。
[0044]
所述综合废水为厂区生活污水和未含氟生产废水。
[0045]
所述反硝化池内的有机碳源为b/c>0.45的易降解废水,易降解废水的生化性较好。
[0046]
采用本发明实施例1的处理方法对某印刷电路板生产蚀刻液废水进行处理,结果表明:原始废水中的氟化物为12471mg/l,cod为457mg/l,tn为528mg/l,氨氮为400.2mg/l,tp为5.3mg/l,经过“短程硝化(hrt 2.5d) 反硝化(hrt 20h) 好氧硝化(hrt 1.5d)”生化处理后,最终出水中的氟化物为9.9mg/l,cod为133mg/l,tn为46.2mg/l,氨氮为39.5mg/l,tp为4.0mg/l,达到废水排放标准。
[0047]
实施例2:一种基于短程硝化反硝化的电子行业废水处理方法,如图1所示,包括以下步骤:
[0048]
s1、将待处理蚀刻液废水输送至钙盐沉淀池进行除氟预处理,预处理后取上清液测定废水中氟离子浓度(氟离子浓度按照《水质氟化物的测定离子选择电极法》(gb 7484-87)规定测定);
[0049]
s2、将除氟预处理后的废水以及综合废水输送至生化调节池,用盐酸或氢氧化钠调节ph为8;
[0050]
s3、调节ph后的废水流至短程硝化池进行短程硝化反应,功能性菌群为氨氧化菌,氨氮被氧化成亚硝氮(通常全程硝化是氧化成硝态氮,即这一步可以减省药剂投加、曝气量和池体占地面积),短程硝化池内悬挂生物填料,生物填料选用的是辫带式仿生水草生物绳填料,这一过程需要控制的条件为:投加碳酸氢钠或碳酸钠维持系统碱度>70mg/l,ph在8,废水温度在35℃,溶解氧浓度在3mg/l,废水有机负荷在0.15kgbod/(kg mlss
·
d),总氮负荷<0.35kgtn/(m3·
d);
[0051]
s4、经步骤s3处理后的废水输送至反硝化池,反硝化菌是异养微生物,利用有机碳源将废水中的亚硝氮和硝氮还原成氮气,实现氨氮的有效去除。这一过程需要控制的条件:投加有机碳源(乙酸钠、葡萄糖等和易降解废水b/c>0.45)维持系统内c/n比在4,ph在7.5,溶解氧维持在4mg/l,温度在35℃,orp在
‑
200mv;
[0052]
s5、经步骤s4处理后的废水输送至好氧硝化池,好氧硝化池内是硝化菌和好氧菌的混合体系,在该池中前端未反应完全的氨氮可以进一步被氧化成亚硝态氮或硝态氮,然后回流至反硝化池进行反硝化脱氮。同时,反硝化池中未降解完全的有机物也可以进一步被降解。这一过程需要控制的条件:ph在8,溶解氧在4mg/l,温度在35℃,回流比在4:1;
[0053]
s6、处理后的废水输送至沉淀池沉淀分离,上清液排入标准排放口,下部污泥委外处置。
[0054]
所述沉淀池中的污泥可通过回流管回流至短程硝化池。
[0055]
所述好氧硝化池中的废水可通过回流管回流至所述反硝化池。
[0056]
所述步骤s1中的除氟预处理为:首先在钙盐沉淀池内添加石灰乳调节ph为10再添加钙盐溶液并沉淀2h,钙盐溶液和氟离子的投放比例为1.5:1。
[0057]
所述钙盐溶液为氧化钙溶液、碳酸钙溶液和氯化钙溶液中的至少一种。本实施例的钙盐溶液选用的是质量浓度为30%wt的碳酸钙溶液。
[0058]
在生化调节池内投入絮凝剂进行絮凝沉淀。所述絮凝剂为pac和pam,pac的浓度为200g/l,pam的浓度为0.02mg/l。
[0059]
所述综合废水为厂区生活污水和未含氟生产废水。
[0060]
所述反硝化池内的有机碳源为b/c>0.45的易降解废水,易降解废水的生化性较好。
[0061]
采用本发明实施例2的处理方法对某摄像头镜片和玻璃盖板生产蚀刻液和切削液废水进行处理,结果如图2所示,结果表明:原始废水中的氟化物为10672mg/l,cod为432mg/l,tn为505mg/l,氨氮为389.6mg/l,tp为4.6mg/l,经过“短程硝化(hrt 2.5d) 反硝化(hrt 20h) 好氧硝化(hrt 1.5d)”生化处理后,最终出水中的氟化物为9.8mg/l,cod为124mg/l,tn为43.7mg/l,氨氮为37.8mg/l,tp为3.7mg/l,达到园区排放标准。
[0062]
以上所述仅为本发明的实施例,并非因此限制本发明的专利范围,凡是利用本发明说明书及附图内容所作的等效结构变换,或直接或间接运用在其他相关的技术领域,均同理包括在本发明的专利保护范围内。
再多了解一些
本文用于企业家、创业者技术爱好者查询,结果仅供参考。