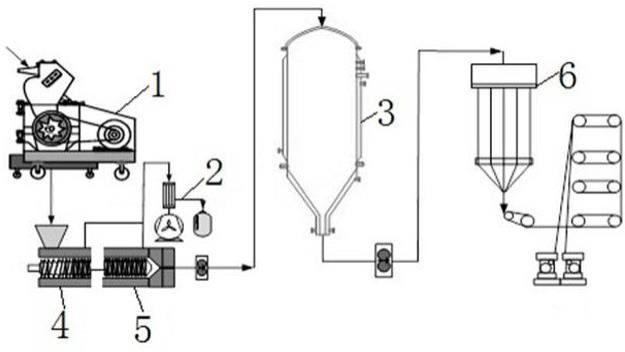
1.本发明涉及一种涤纶工业丝生产方法,具体涉及一种废旧聚酯再生熔体直纺涤纶工业丝生产方法。
背景技术:
2.我国是世界纺织品生产和消费大国,而聚酯(pet)作为化纤纺织品的主要原料之一,2020年聚酯化纤总产量达到4100万吨,占到全球化纤总产量的69.4%,占绝对主导地位。然而,随着聚酯化纤行业快速发展的同时,随之而来的废旧聚酯制品处理问题也越来越迫切。废旧聚酯(纺织品)主要指以聚酯化纤为原材料进行加工生产过程中产生的各类下脚料、废料,包括化纤制备过程中产生的废丝废块,以及各种消费后产生的废旧纺织品。据统计,每年废旧聚酯(纺织品)产生量约达3200万吨以上。
3.虽然我国目前再生聚酯产能已经达到世界第一,但是再生聚酯特性黏度不高,产品品质普遍偏低,再生产品仅能降级回收被用于填充及包覆等低端领域,距离真正意义的循环再利用还有很大差距。例如中国公开专利cn102605454a:由回收pet瓶片料规模化生产涤纶工业长丝的方法,将回收的pet瓶粉碎成片状,清洗后烘干,然后送入结晶床体内,在进入结晶床体的热风的作用下,进行结晶,在瓶片料表面形成结晶层,然后将结晶的瓶片料送入干燥塔,干燥后的瓶片料进入螺杆挤压机进行熔融挤压,将所得的熔体送入由粗过滤器、精过滤器以及两者之间的加压泵组成的两级过滤装置进行过滤,除去熔体中的杂质和对纺丝有害的凝聚物,经过两级过滤的熔体进入液相增粘釜,在真空度为40
‑
71pa、温度为279
‑
281℃的条件下并在搅拌下,在液相增粘釜内进行缩聚反应,使熔体的粘度数值增加至0.820
±
0.001dl/g,经过液相增粘后的熔体进入纺丝箱,采用高速纺丝工艺进行纺丝,制得涤纶工业长丝。这种方法中关键的液相增黏步骤,采用带搅拌的鼠笼卧式反应釜,由于结构的缺陷,在制备0.820 dl/g以上高黏度的熔体时会造成搅拌电流过大、成膜效果差以及死区过多等问题,因此无法生产高强度、品质均匀的涤纶工业丝,且生产成本高,品种单一。
技术实现要素:
4.发明目的:本发明的目的是为了克服现有技术中的不足,提供一种废旧聚酯物理化学法再生技术,采用立式降膜熔融缩聚反应器,能够实现脱挥、聚合增黏一体化,特性黏度可提升达到工业丝级,填补了熔体直纺高强度再生聚酯工业丝制备的行业空白,从而实现废旧聚酯的高效率、高品质和高值化再利用,采用多点柔性在线添加技术,可以形成原位配色制备有色再生聚酯工业丝和阻燃、抗老化等多功能复合差别化再生聚酯工业丝,进一步提高废旧聚酯再生制品附加值的废旧聚酯再生熔体直纺高强涤纶工业丝生产方法。
5.技术方案:为了解决上述技术问题,本发明所述的一种废旧聚酯再生熔体直纺高强涤纶工业丝生产方法,它包括以下步骤,(1)将废旧聚酯经分拣、破断装置处理,得到外观形态一致,长度不大于80cm的破断废旧聚酯原料;
(2)将经过步骤(1)处理后的物料进行螺杆熔融,在螺杆熔融时通过真空系统进行多级抽真空处理,去除水分和低分子挥发物;(3)将经过步骤(2)处理后的物料粗过滤后,进入立式、无动力、竖管外降膜液相增黏反应器,使熔体的特性黏度数值增加至0.9~1.2dl/g以上;(4)将经过步骤(3)处理后的物料精密过滤后,经过水下切粒机造粒得到高黏度再生聚酯切片或通过熔体管道输送进行熔体直接纺丝,制得断裂强度大于8.0cn/dtex的再生涤纶工业长丝。
6.进一步地,废旧聚酯经过步骤(1)后通过致密化处理,再进行步骤(2)真空螺杆熔融,所述致密化处理的温度为230℃~255℃,致密化后的破断聚酯废料堆积密度达到400kg/m3以上。
7.进一步地,螺杆熔融由两级真空螺杆组成,第一级是输送螺杆,为带有真空脱气的单螺杆,进料口上方设有致密化装置,物料在260℃~280℃温度下经过软化真空脱除大部分水分后,固熔混合形态物料以稳定的进料压力进入第二级真空单螺杆或双螺杆,在280℃~320℃温度条件下进行挤压熔融、压缩和计量,并继续通过设置的两处真空脱气口进一步脱除水分和小分子挥发物;两级真空螺杆真空脱气与真空系统连接,真空系统为机械真空泵组,极限真空度小于1000pa。
8.进一步地,步骤(3)中,所述降膜液相增黏反应器采用立式结构、无机械搅拌装置,优选已授权发明专利zl201610302101.3结构,物料全部依靠重力作用完成从进料端到出料端的转移;再生聚酯熔体在竖直管外降膜流动,反应器内物料温度控制在275℃~282℃,反应器内压力0.01mpa~0.04 mpa,反应器内熔体停留时间在30min~60min。
9.进一步地,步骤(4)中,所述熔体直接纺丝包括出料增压泵输出的高黏再生聚酯熔体经过熔体管道输送到纺丝箱体内计量泵,计量泵精确计量后进入纺丝组件,经纺丝组件内喷丝板喷丝孔挤出形成纤维,纤维经过缓冷、风冷、上油、预网、多级拉伸定型和终网打结后高速卷绕成高强再生涤纶工业丝;所述增压泵和熔体管道,采用液相热媒保温,温度280℃~290℃,增压泵压力12mpa~24mpa;所述纺丝箱体,采用气相热媒保温,温度290℃~310℃;所述多级拉伸定型,拉伸倍率为4.0~6.2,松弛比为3%~12%,拉伸定型温度为80℃~250℃。
10.进一步地,在步骤(2)中螺杆熔融、步骤(3)中降膜液相增粘反应器(3)、步骤(4)中熔体管道处设置多点柔性在线添加装置,添加着色剂、阻燃剂或抗菌剂等一种或多种功能助剂,以原液着色为基础功能,原位制备多重复合功能再生高强涤纶工业长丝;其中,在步骤(2)阶段添加着色剂,所述着色剂包括色粉,该色粉包括炭黑、铁红、偶氮黄、钛菁蓝中的一种或多种,色粉与聚酯熔体的质量比为0.1~1%;在步骤(3)、(4)阶段添加阻燃剂、抗菌剂等一种或多种功能助剂,其中阻燃剂包括二乙基次磷酸铝、氢氧化镁、氢氧化铝、硅系等一种或几种复配物,阻燃剂与聚酯熔体的质量比为0.5~5.0%;抗菌剂包括纳米银、纳米铜、纳米锌中一种或多种合金,抗菌剂与聚酯熔体的质量比0.1~0.5%。
11.进一步地,步骤(1)中,废旧聚酯包括聚酯民用丝、聚酯工业丝纺丝及其以聚酯工业丝为原料的工业织带生产过程的废丝、废块、边角料等废料和消费后回收的废旧工业织带等。
12.有益效果:本发明与现有技术相比,其显著优点是:本发明采用物理化学法再生技术,立式降膜熔融缩聚反应器,使再生聚酯熔体“脱挥
‑
增黏”一体化完成,特性黏度可提升达到工业丝级,再生聚酯液相增黏可以达到更高的黏度0.9~1.2dl/g,反应效率高,在40min左右,可以实现高强度大于8.0cn/dtex再生涤纶工业丝熔体直纺生产,填补了熔体直纺高强度再生聚酯工业丝制备的行业空白,从而实现废旧聚酯的高效率、高品质和高值化再利用,开创性地应用多点在线添加技术制备高性能再生聚酯工业丝,在螺杆挤出、降膜式液相增黏以及熔体输送管道等多点柔性在线添加技术,相对于现有技术,本发明多点柔性添加制备原位有色和阻燃、抗菌等多功能复合再生涤纶工业丝具有明显技术优势,省去功能母粒制备工序,避免了低黏度、母粒载体带入对涤纶工业丝强度的影响,低含量色粉在聚酯熔体中分散性好,经螺杆挤出、液相增黏和熔体输送多环节混合保证颜色均匀性,可以形成原位配色制备有色再生聚酯工业丝和阻燃、抗菌等多功能复合差别化再生聚酯工业丝技术,进一步提高废旧聚酯再生制品附加值,采用聚酯民用丝、聚酯工业丝纺丝及其以聚酯工业丝为原料的工业织带生产过程的废丝、废块、边角料等废料和消费后回收的废旧工业织带循环再生制备高性能化纤,建立真正的从“聚酯纺丝(废料)—工业织带(边角废料)—市场废旧工业织带(回收)—聚酯纺丝(差别化高性能化纤)—再生工业织带(grs认证)”过程的聚酯b2b“(织)带到(织)带(belt to belt)”循环再生利用生产体系,将聚酯产品全生命周期中产生的废旧品高效再生,实现废旧聚酯资源的高值化利用,本发明也能在pc、pbt、ptt等废旧聚酯的资源回收利用上推广应用。
附图说明
13.图1 是本发明的流程示意图。
具体实施方式
14.下面结合附图和实施例对本发明作进一步的说明。
15.实施例1如图1所示,一种废旧聚酯再生熔体直纺高强涤纶工业丝生产方法,它包括以下步骤,(1)将废旧聚酯经分拣、破断装置1处理,得到外观形态一致,长度不大于80cm的破断废旧聚酯原料;(2)将经过步骤(1)处理后的物料进行螺杆熔融,在螺杆熔融时通过真空系统2进行多级抽真空处理,去除水分和低分子挥发物;(3)将经过步骤(2)处理后的物料粗过滤后,进入立式、无动力、竖管外降膜液相增黏反应器3,使熔体的特性黏度数值增加至1.06dl/g;(4)将经过步骤(3)处理后的物料精密过滤后,经过水下切粒机造粒得到高黏度再生聚酯切片或通过熔体管道输送进行熔体直接纺丝,制得断裂强度大于8.0cn/dtex的涤纶工业长丝。
16.废旧聚酯经过步骤(1)后通过致密化处理,再进行步骤(2)真空螺杆熔融,所述致密化处理的温度为235℃,致密化后的破断聚酯废料堆积密度达到400kg/m3以上。
17.螺杆熔融由两级真空螺杆组成,第一级是输送螺杆4,为带有真空脱气的单螺杆,
进料口上方设有致密化装置,物料在275℃温度下经过软化真空脱除大部分水分后,固熔混合形态物料以稳定的进料压力进入第二级真空单螺杆或双螺杆5,在310℃温度条件下进行挤压熔融、压缩和计量,并继续通过设置的两处真空脱气口进一步脱除水分和小分子挥发物;两级真空螺杆真空脱气与真空系统2连接,真空系统2为机械真空泵组,极限真空度小于1000pa。
18.步骤(3)中,所述降膜液相增黏反应器3采用立式结构、无机械搅拌装置,反应器内物料全部依靠重力作用完成从进料端到出料端的转移;再生聚酯熔体在竖直管外降膜流动,反应器内物料温度控制在278℃,反应器内压力0.03 mpa,反应器内熔体停留时间在40min,得到特性黏度1.06dl/g的再生聚酯熔体。
19.步骤(4)中,所述熔体直接纺丝包括出料增压泵输出的高黏再生聚酯熔体经过熔体管道输送到纺丝箱体内计量泵,计量泵精确计量后进入纺丝组件6,经纺丝组件6内喷丝板喷丝孔挤出形成纤维,纤维经过缓冷、风冷、上油、预网、多级拉伸定型和终网打结后高速卷绕成高强再生涤纶工业丝;所述增压泵和熔体管道,采用液相热媒保温,温度285℃,增压泵压力18mpa;所述纺丝箱体,采用气相热媒保温,温度295℃;所述多级拉伸定型,预拉伸倍率为1.003,一级拉伸倍率为1.4,拉伸温度为95℃,第二级拉伸倍率为4.2,拉伸定型温度为180℃,松弛比为5%,得到纤度1110dtex,断裂强度为8.1cn/dtex,断裂伸长为11%的再生高强低伸涤纶工业丝,适合在土工织物材料应用。
20.实施例2如图1所示,一种废旧聚酯再生熔体直纺高强涤纶工业丝生产方法,它包括以下步骤,(1)将废旧聚酯经分拣、破断装置1处理,得到外观形态一致,长度不大于80cm的破断废旧聚酯原料;(2)将经过步骤(1)处理后的物料进行螺杆熔融,在螺杆熔融时通过真空系统2进行多级抽真空处理,去除水分和低分子挥发物;(3)将经过步骤(2)处理后的物料粗过滤后,进入立式、无动力、竖管外降膜液相增黏反应器3,使熔体的特性黏度数值增加至1.12dl/g;(4)将经过步骤(3)处理后的物料精密过滤后,经过水下切粒机造粒得到高黏度再生聚酯切片或通过熔体管道输送进行熔体直接纺丝,制得断裂强度大于8.0cn/dtex的涤纶工业长丝。
21.废旧聚酯经过步骤(1)后通过致密化处理,再进行步骤(2)真空螺杆熔融,所述致密化处理的温度为245℃,致密化后的破断聚酯废料堆积密度达500kg/m3以上。
22.螺杆熔融由两级真空螺杆组成,第一级是输送螺杆4,为带有真空脱气的单螺杆,进料口上方设有致密化装置,物料在265℃温度下经过软化真空脱除大部分水分后,固熔混合形态物料以稳定的进料压力进入第二级真空单螺杆或双螺杆5,在290℃温度条件下进行挤压熔融、压缩和计量,并继续通过设置的两处真空脱气口进一步脱除水分和小分子挥发物;两级真空螺杆真空脱气与真空系统2连接,真空系统2为机械真空泵组,极限真空度小于1000pa。
23.步骤(3)中,所述降膜液相增黏反应器3采用立式结构、无机械搅拌装置,反应器内
物料全部依靠重力作用完成从进料端到出料端的转移;再生聚酯熔体在竖直管外降膜流动,反应器内物料温度控制在280℃,反应器内压力0.02 mpa,反应器内熔体停留时间在50min,得到特性黏度1.12dl/g的再生聚酯熔体。
24.步骤(4)中,所述熔体直接纺丝包括出料增压泵输出的高黏再生聚酯熔体经过熔体管道输送到纺丝箱体内计量泵,计量泵精确计量后进入纺丝组件6,经纺丝组件6内喷丝板喷丝孔挤出形成纤维,纤维经过缓冷、风冷、上油、预网、多级拉伸定型和终网打结后高速卷绕成高强再生涤纶工业丝;所述增压泵和熔体管道,采用液相热媒保温,温度289℃,增压泵压力22mpa;所述纺丝箱体,采用气相热媒保温,温度305℃;所述多级拉伸定型,预拉伸倍率为1.003,一级拉伸倍率为1.43,拉伸温度为110℃,第二级拉伸倍率为4.25,拉伸定型温度为220℃,松弛比为3%。
25.在步骤(2)阶段添加着色剂,所述着色剂包括色粉,该色粉包括炭黑、铁红、偶氮黄、钛菁蓝中的一种或多种,色粉与聚酯熔体的质量比为0.3%。
26.步骤(1)中,废旧聚酯包括聚酯民用丝、聚酯工业丝纺丝及其以聚酯工业丝为原料的工业织带生产过程的废丝、废块、边角料等废料和消费后回收的废旧工业织带等。
27.实施例3如图1所示,一种废旧聚酯再生熔体直纺高强涤纶工业丝生产方法,它包括以下步骤,(1)将废旧聚酯经分拣、破断装置1处理,得到外观形态一致,长度不大于80cm的破断废旧聚酯原料;(2)将经过步骤(1)处理后的物料进行螺杆熔融,在螺杆熔融时通过真空系统2进行多级抽真空处理,去除水分和低分子挥发物;(3)将经过步骤(2)处理后的物料粗过滤后,进入立式、无动力、竖管外降膜液相增黏反应器3,使熔体的特性黏度数值增加至1.15dl/g;(4)将经过步骤(3)处理后的物料精密过滤后,经过水下切粒机造粒得到高黏度再生聚酯切片或通过熔体管道输送进行熔体直接纺丝,制得断裂强度大于8.0cn/dtex的涤纶工业长丝。
28.废旧聚酯经过步骤(1)后通过致密化处理,再进行步骤(2)真空螺杆熔融,所述致密化处理的温度为250℃,致密化后的破断聚酯废料堆积密度达500kg/m3以上。
29.螺杆熔融由两级真空螺杆组成,第一级是输送螺杆4,为带有真空脱气的单螺杆,进料口上方设有致密化装置,物料在270℃温度下经过软化真空脱除大部分水分后,固熔混合形态物料以稳定的进料压力进入第二级真空单螺杆或双螺杆5,在300℃温度条件下进行挤压熔融、压缩和计量,并继续通过设置的两处真空脱气口进一步脱除水分和小分子挥发物;两级真空螺杆真空脱气与真空系统2连接,真空系统2为机械真空泵组,极限真空度小于1000pa。
30.步骤(3)中,所述降膜液相增黏反应器3采用立式结构、无机械搅拌装置,反应器内物料全部依靠重力作用完成从进料端到出料端的转移;再生聚酯熔体在竖直管外降膜流动,反应器内物料温度控制在279℃,反应器内压力0.02 mpa,反应器内熔体停留时间在45min,得到特性黏度1.15dl/g的再生聚酯熔体。
31.步骤(4)中,所述熔体直接纺丝包括出料增压泵输出的高黏再生聚酯熔体经过熔体管道输送到纺丝箱体内计量泵,计量泵精确计量后进入纺丝组件6,经纺丝组件6内喷丝板喷丝孔挤出形成纤维,纤维经过缓冷、风冷、上油、预网、多级拉伸定型和终网打结后高速卷绕成高强再生涤纶工业丝;所述增压泵和熔体管道,采用液相热媒保温,温度288℃,增压泵压力20mpa;所述纺丝箱体,采用气相热媒保温,温度300℃;所述多级拉伸定型,预拉伸倍率为1.004,一级拉伸倍率为1.44,拉伸温度为120℃℃,第二级拉伸倍率为4.24,拉伸定型温度为230℃,松弛比为6%。
32.在步骤(2)阶段添加着色剂,所述着色剂包括色粉,该色粉包括炭黑、铁红、偶氮黄、钛菁蓝中的一种或多种,色粉与聚酯熔体的质量比为0.5%;在步骤(3)、(4)阶段添加阻燃剂、抗菌剂等一种或多种功能助剂,其中阻燃剂包括二乙基次磷酸铝、氢氧化镁、氢氧化铝、硅系等一种或几种复配物,阻燃剂与聚酯熔体的质量比为2.0%;抗菌剂包括纳米银、纳米铜、纳米锌中一种或多种合金,抗菌剂与聚酯熔体的质量比0.3%。
33.步骤(1)中,废旧聚酯包括聚酯民用丝、聚酯工业丝纺丝及其以聚酯工业丝为原料的工业织带生产过程的废丝、废块、边角料等废料和消费后回收的废旧工业织带等。
34.本发明采用物理化学法再生技术,立式降膜熔融缩聚反应器,使再生聚酯熔体“脱挥
‑
增黏”一体化完成,特性黏度可提升达到工业丝级,再生聚酯液相增黏可以达到更高的黏度0.9~1.2dl/g,反应效率高,在40min左右,可以实现高强度大于8.0cn/dtex再生涤纶工业丝熔体直纺生产,填补了熔体直纺高强度再生聚酯工业丝制备的行业空白,从而实现废旧聚酯的高效率、高品质和高值化再利用,开创性地应用多点在线添加技术制备高性能再生聚酯工业丝,在螺杆挤出、降膜式液相增黏以及熔体输送管道等多点柔性在线添加技术,相对于现有技术,本发明多点柔性添加制备原位有色和阻燃、抗菌等多功能复合再生涤纶工业丝具有明显技术优势,省去功能母粒制备工序,避免了低黏度、母粒载体带入对涤纶工业丝强度的影响,低含量色粉在聚酯熔体中分散性好,经螺杆挤出、液相增黏和熔体输送多环节混合保证颜色均匀性,可以形成原位配色制备有色再生聚酯工业丝和阻燃、抗菌等多功能复合差别化再生聚酯工业丝技术,进一步提高废旧聚酯再生制品附加值,采用聚酯民用丝、聚酯工业丝纺丝及其以聚酯工业丝为原料的工业织带生产过程的废丝、废块、边角料等废料和消费后回收的废旧工业织带循环再生制备高性能化纤,建立真正的从“聚酯纺丝(废料)—工业织带(边角废料)—市场废旧工业织带(回收)—聚酯纺丝(差别化高性能化纤)—再生工业织带(grs认证)”过程的聚酯b2b“(织)带到(织)带(belt to belt)”循环再生利用生产体系,将聚酯产品全生命周期中产生的废旧品高效再生,实现废旧聚酯资源的高值化利用,本发明也能在pc、pbt、ptt等废旧聚酯的资源回收利用上推广应用。
35.本发明提供了一种思路及方法,具体实现该技术方案的方法和途径很多,以上所述仅是本发明的优选实施方式,应当指出,对于本技术领域的普通技术人员来说,在不脱离本发明原理的前提下,还可以做出若干改进和润饰,这些改进和润饰也应视为本发明的保护范围,本实施例中未明确的各组成部分均可用现有技术加以实现。
再多了解一些
本文用于企业家、创业者技术爱好者查询,结果仅供参考。